Теплоэнергетика, 2023, № 2, стр. 47-59
Моделирование режимов пуска котла энергоблока 660 МВт Троицкой ГРЭС без пускового циркуляционного насоса и оценка температурного режима НРЧ и ВРЧ
В. М. Супранов a, *, К. А. Плешанов a, **, М. Н. Зайченко a, К. В. Стерхов a, Д. А. Хохлов a, Д. С. Ткаченко b
a Национальный исследовательский университет “Московский энергетический институт”
111250 Москва, Красноказарменная ул., д. 14, Россия
b Филиал ПАО ОГК-2 Троицкая ГРЭС
457100 Челябинская обл., г. Троицк, Россия
* E-mail: svm-mpei@mail.ru
** E-mail: pleshanovka@mpei.ru
Поступила в редакцию 20.05.2022
После доработки 17.08.2022
Принята к публикации 30.08.2022
Аннотация
Котел HG-2100/25,4-YM16, изготовленный Харбинским котельным заводом, работает в составе энергоблока 660 МВт Троицкой ГРЭС. Анализ конструкции показал, что использование многих технических решений не характерно для отечественных производителей. Цель данного исследования – моделирование и оптимизация технологии пуска котла без циркуляционного насоса (ЦН), но при обеспечении надежной работы элементов котла. Для достижения этой цели необходимо решить следующие основные задачи: обосновать критерии надежной работы элементов котла во время пуска, разработать адаптированную статическую (СМ) и адаптированную динамическую (ДМ) расчетные модели котла; исследовать возможность пуска котла без ЦН. Основные критерии надежности нижней (НРЧ) и верхней (ВРЧ) радиационных частей котла – отсутствие процесса окалинообразования (расчетная температура наружной поверхности металла должна быть меньше допускаемой) и устойчивость движения среды. Однако результаты расчета температуры металла пароперегревательных поверхностей нагрева в динамическом режиме не являются точными. Поэтому для них критерием надежности был расход пара за сепаратором, значения которого в режимах пуска котла с насосом и без него должны быть близкими. Критерием надежной работы выходной ступени пароперегревателя низкого давления (ППНД2) является температура газов на выходе из топки, которая не должна увеличиться при пуске без ЦН. Для расчетов использовалась программа Boiler Designer. Адаптированная статическая модель котла создавалась с учетом предыдущих работ авторов статьи в сопоставлении с результатами заводских расчетов. Затем на основе статической модели была создана адаптированная динамическая модель котла. Для этого использовались тренды реальных пусков с циркуляционным насосом, предоставленные специалистами Троицкой ГРЭС. Эти данные, а также опыт прошлых расчетов и экспертные оценки авторов статьи позволили провести настройку динамической модели. Детально были исследованы три режима пуска котла из холодного состояния: один с насосом (при температуре питательной воды tп.в = 104°С) и два без него (при tп.в = 104 и 150°С). Во всех случаях рассматривались следующие этапы пуска: горячая промывка, толчок турбины, конец толчка, выход котла на прямоточный режим. Последнему этапу соответствовала нагрузка 30% BMCR (boiler maximum continuous rating – режим максимальной длительной нагрузки). Анализ полученных результатов показал, что принятые критерии надежности выполняются для всех режимов и этапов работы котла.
Котел HG-2100/25.4-YM16 (рис. 1) – прямоточный с промежуточным перегревом на сверхкритические параметры пара, работающий и в режиме скользящего давления. В режиме BMCR (номинальная нагрузка) температура свежего (перегретого) пара за котлом составляет 571°C, давление 25.4 МПа; эти же параметры для пара вторичного перегрева равны 570°C и 4.448 МПа.
Рис. 1.
Схема котла HG-2100/25.4-YM16: 1, 6 – нижняя и верхняя радиационные части котла; 2 – сопла горелок; 3, 4 – воздуховоды горелок и сопл OFA; 5 – разъем между НРЧ и ВРЧ; 7 – радиационные ширмы; 8, 11 – выходная и первая ступени пароперегревателя СКД; 9, 10 – выходная и первая ступени промежуточного пароперегревателя; 12 – экономайзер; 13 – разделительный экран; 14 – шиберы для регулирования расхода газов; 15 – регенеративные воздухоподогреватели
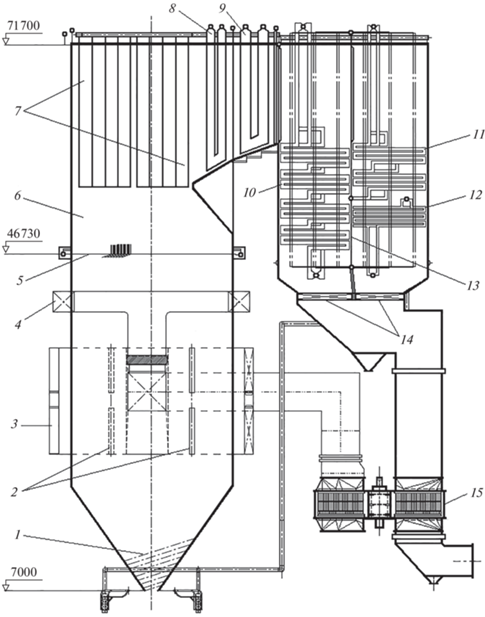
Котел однокорпусный, П-образный, газоплотный, предназначен для работы с уравновешенной тягой в режиме твердого шлакоудаления. Основным видом топлива является высокореакционный каменный уголь, растопочное топливо – мазут марки M100.
Топка котла сечением в плане 19.082 × 19.082 м оборудована прямоточными горелками с тангенциальной компоновкой. Для размола топлива используются шесть пылесистем с прямым вдуванием и воздушной сушкой, укомплектованных среднеходными мельницами, работающими под давлением. При работе котла на проектном топливе пять мельниц находятся в действии, одна – в резерве. Над основными горелками расположены сопла OFA (over-fire air). Примененная схема сжигания твердого топлива позволяет рассредоточить тепловыделение по высоте топки, избежать шлакования экранов и одновременно снизить выбросы оксидов азота NOx.
Образовавшиеся при горении дымовые газы поднимаются в верхнюю часть топки, где расположены радиационные ширмовые пароперегреватели (ШПП). По ширине котла установлено шесть рядов ШПП, по восемь ширм в каждом ряду. В отечественных котлах, как правило, используется одна ступень U-образных топочных ширм. Ширмовые пароперегреватели занимают почти всю глубину топки, а на выходе из нее установлена выходная ступень пароперегревателя высокого давления (ППВД2), выполненная в виде полурадиационных ширм. В ППВД2 располагаются 34 ширмы по ширине соединительного газохода.
Далее продукты сгорания через подвесную систему заднего экрана топки попадают в выходную ступень ППНД2. На выходе из соединительного газохода предусмотрен двухрядный фестон, представляющий собой разводку труб нижнего экрана этого газохода, а за ним – подвесная система фронтового экрана конвективной шахты (КШ). Пройдя через эти поверхности нагрева, дымовые газы разворачиваются на 90° в поворотной камере и попадают в КШ.
Конвективная шахта выполнена по схеме “расщепленный хвост”, которая не нашла широкого применения в России, но довольно часто используется зарубежными производителями [1]. В котле конвективная шахта делится на два параллельных газохода: передний (глубиной 8.618 м) и задний (глубиной 9.098 м). В переднем газоходе расположена горизонтальная часть первой ступени пароперегревателя низкого давления (ППНД1), а в заднем газоходе –последовательно по ходу газов горизонтальная часть первой ступени пароперегревателя высокого давления (ППВД1) и экономайзер (ЭК). Все эти поверхности нагрева размещены на подвесных трубах. Подвесные трубы проходят через поворотную камеру и через систему тяг передают весовую нагрузку на каркас котла. Помимо подвесных труб, в поворотной камере расположены вертикальные части ППНД1 и ППВД1, а также подвесная система разделительного экрана КШ.
В нижней части конвективной шахты предусмотрены шиберы, позволяющие изменять расходы газов через передний и задний газоходы и тем самым регулировать температуру вторичного пара.
После КШ дымовые газы перемешиваются и поступают в два регенеративных воздухоподогревателя (РВП). В режиме BMCR температура газов за РВП составляет 124°C, а расчетный КПД котла (по низшей теплоте сгорания) – 93.67%. Если температура воздуха опускается ниже 20°C, то его предварительно подогревают в калориферах.
В режиме BMCR 6% питательной воды отбирается на впрыски, а остальная ее часть подается в коридорный противоточный ЭК с поперечным оребрением. После этого рабочее тело попадает в нижнюю радиационную часть, выполненную в виде спирально-ленточной навивки Рамзина газоплотного исполнения, которая начинается в холодной воронке котла, переходит на вертикальные стены топки и поднимается по ним до отметки 46 730 мм. Между трубами НРЧ, как и во всех остальных экранах котла, вварена стальная полоса толщиной 6 мм. После нижней радиационной части среда поступает в коллектор, где она перемешивается и распределяется по экранам верхней радиационной части.
Верхняя радиационная часть сделана в виде параллельно включенных мембранных панелей из вертикальных труб в один ход. Схема с переходом газоплотной навивки Рамзина через промежуточный коллектор в вертикальные подъемные одноходовые экраны также до текущего времени не освоена отечественным энергетическим машиностроением. Рабочее тело протекает параллельно четырьмя потоками по переднему, боковым и заднему экранам топки, а после заднего экрана еще и по его обогреваемой подвесной системе. Затем среда проходит экраны ограждения соединительного газохода и попадает в четыре вертикальных полнопроходных сепаратора. На нагрузках ниже 30% BMCR они работают в режиме отделения влаги.
После сепараторов пар совершает четыре хода по экранам ограждений и подвесным трубам и затем перемешивается в коллекторе, расположенном в средней части разделительного экрана КШ, который является входным коллектором ППВД1. Первая ступень пароперегревателя высокого давления выполнена коридорной, противоточной. Далее по ходу пара происходит первый впрыск питательной воды, а затем он поступает в ШПП.
За ШПП происходит второй впрыск, и пар направляется в ППВД2 – коридорную, прямоточную ступень. Температура перегретого пара регулируется путем поддержания на нужном уровне соотношения вода – топливо. Впрыски питательной воды предусмотрены для динамической подрегулировки температуры перегретого пара и повышения надежности работы металла наиболее теплонапряженных ступеней пароперегревателя.
Ступень ППНД1 коридорная, противоточная. После нее предусмотрен аварийный впрыск в тракт низкого давления. Выходная ступень ППНД2 выполнена коридорной, прямоточной.
Пусковая схема котла HG-2100/25.4-YM16 с циркуляционным насосом в упрощенном виде показана на рис. 2, а. Ее основа была разработана фирмой Babcock&Wilcox [1] в 60-е годы XX в. Схема предусматривает пуск на скользящих параметрах, что позволяет уменьшить затраты электроэнергии на собственные нужды. В России данная схема не получила широкого применения. Главная причина этого – отсутствие локализации производства циркуляционных насосов в стране. Между тем, ЦН подвержены частым поломкам, что подтверждается данными [2].
Рис. 2.
Упрощенные пусковые схемы котла HG-2100/25.4-YM16 с циркуляционным насосом (а) и без него (б)
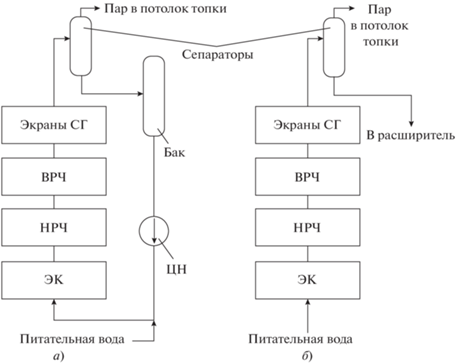
Цель настоящего исследования – изучение возможности пуска HG-2100/25.4-YM16 без циркуляционного насоса (рис. 2, б) при обеспечении надежной работы элементов котла и минимальных изменениях в конструкции. Для достижения этой цели необходимо решить следующие задачи:
определить критерии надежности элементов котла во время пуска;
разработать адаптированные статическую и динамическую расчетные модели котла;
провести расчетное моделирование пусков котла без ЦН и убедиться в выполнении критериев надежной работы.
Для организации пуска HG-2100/25.4-YM16 без использования ЦН предлагается направлять воду из сепаратора в расширитель, предусмотренный пусковой схемой. Надежность элементов котла зависит в том числе от температурного режима металла его элементов, эффективности охлаждения труб поверхностей нагрева и свойств их материала. Требуемый температурный режим металла труб с малой толщиной стенки определяется температурой окалинообразования или температурой изменения структуры металла [3]. Поэтому основным критерием надежности элементов котла является выполнение условия, при котором температура металла труб tст не должна превышать допускаемых значений [tст]. Однако расчет температуры металла пароперегревательных поверхностей нагрева в динамическом режиме, в том числе при пуске, дает неточные результаты. Исходя их этого, в качестве критерия надежной работы пароперегревательных поверхностей нагрева первичного тракта приняли расход пара за сепаратором. Если расход генерируемого пара при пуске котла без ЦН будет иметь значения, близкие к значениям при пуске с насосом, то надежность пароперегревательных поверхностей будет обеспечена. Критерием надежной работы ППНД2 является температура газов на выходе из топки, которая не должна увеличиться при пуске без ЦН.
При существующей пусковой схеме расход воды на входе в ЭК составляет 800–1000 т/ч, при этом температура воды будет иметь промежуточное значение между температурами питательной воды и насыщения при давлении в сепараторе в зависимости от кратности циркуляции в контуре. При пуске без ЦН на вход в ЭК будет поступать питательная вода с меньшей температурой, что приведет к увеличению доли тепла, расходуемого на подогрев воды до кипения, и снижению количества тепла, затрачиваемого на испарение при одинаковой тепловой нагрузке котла. При пуске без ЦН для обеспечения паропроизводительности котла, близкой к таковой при пуске с ЦН, необходимо либо увеличивать расход топлива, что приведет к росту температур по пароперегревательному тракту, либо уменьшать расход воды на входе в ЭК. В итоге организовать пуск котла без ЦН и существенных изменений в конструкции можно, только разработав и обосновав технические решения, при которых расход пара и уровень температур газов в пароперегревательном тракте не будут существенно отличаться от таковых при пуске с ЦН.
Адаптированная статическая модель котла разрабатывалась для режима BMCR. Для создания этой модели использовались программа Boiler Designer [4] и расчетная методика [5]. Такой подход уже неоднократно и успешно применялся, например в [6, 7]. При создании СМ использовались чертежи котла и его поверхностей нагрева, гидравлическая схема и описание котла. Первоначально в файл исходных данных были введены значения коэффициентов тепловой эффективности ψ, загрязнения ε, использования ξ и относительного тепловосприятия Qотн радиационных поверхностей топки, определенные с учетом рекомендаций [5].
После этого был выполнен расчет по Boiler Designer, полученные результаты проанализированы и сопоставлены с результатами заводского расчета (ЗР) котла. Было обнаружено, что в целом наблюдается соответствие данных, но его можно улучшить путем настройки модели.
Эта настройка проводилась путем изменения только коэффициентов ψ, ξ и Qотн для отдельных поверхностей нагрева, а именно ППВД2, ППНД2, горячей части РВП и ШПП. При этом указанные коэффициенты изменялись в разумных пределах так, чтобы их изменение не противоречило физическому смыслу. Также учитывалось, что ППВД2 и ППНД2 – выходные ступени, а ШПП – весьма теплонапряженная ступень пароперегревателя, поэтому приращение энтальпии пара в них должно быть в определенных пределах.
В табл. 1 приводятся результаты расчета по настроенной модели и их сопоставление с заводскими данными. В качестве критерия соответствия каждого параметра в таблице использована относительная погрешность, вычисленная по формуле
Таблица 1.
Основные параметры котла, определенные по статистической модели и по результатам заводского расчета для режима BMCR
Параметр | Расчет | ΔП, % | |
---|---|---|---|
заводской | по СМ | ||
Расход, т/ ч: | |||
свежего пара D | 2100 | 2100 | 0.00 |
пара промежуточного перегрева Dвт | 1780 | 1780 | 0.00 |
воды на: | |||
первый впрыск Dвпр1 | 63 | 63 | 0.00 |
второй впрыск DвпрР2 | 63 | 63 | 0.00 |
впрыск в промежуточный пароперегреватель Dвпр.вт | 0 | 0 | 0.00 |
воздуха на котел (до РВП) Gвоз | 2420 | 2486 | 2.73 |
газов: | |||
на выходе из топки Gг.т | 2637 | 2644 | 0.27 |
через ППНД11 Gг.ППНД11 | 1187 | 1351 | 13.82 |
через ППВД1 и ЭК Gг.ЭК | 1450 | 1293 | 10.83 |
перед РВП Gг.РВП | 2637 | 2644 | 0.27 |
Давление, МПа: | |||
свежего (перегретого) пара на выходе из котла pпе | 25.400 | 25.400 | 0.00 |
пара на входе в промежуточный пароперегреватель $p_{{вт}}^{'}$ | 4.668 | 4.659 | 0.19 |
питательной воды pп.в | 29.000 | 29.001 | Приблизи- тельно 0 |
Температура, °C: | |||
свежего пара на выходе из котла tпе | 571.0 | 571.0 | 0.00 |
питательной воды tп.в | 286.4 | 286.4 | 0.00 |
пара промежуточного перегрева в котле: | |||
на входе $t_{{вт}}^{'}$ | 324.3 | 324.3 | 0.00 |
на выходе ![]() |
570.0 | 570.0 | 0.00 |
газов на выходе из топки ![]() |
981.0 | 981.0 | 0.00 |
газов: | |||
за ППНД2 ![]() |
830.0 | 783.0 | 5.66 |
за ППНД12* ![]() |
534.0 | 523.0 | 2.03 |
за ППНД11* ![]() |
369.0 | 371.0 | 0.54 |
за ЭК ![]() |
347.0 | 374.0 | 7.78 |
перед РВП $\vartheta _{{{\text{РВП}}}}^{'}$ | 357.0 | 372.0 | 4.20 |
уходящих газов ϑух | 124.0 | 124.0 | 0.00 |
горячего воздуха за РВП tг.в | 329.0 | 326.0 | 0.91 |
среды за: | |||
ЭК ![]() |
316.0 | 308.0 | 2.53 |
сепаратором ![]() |
424.0 | 426.0 | 0.47 |
ППВД1 ![]() |
466.0 | 477.0 | 2.36 |
первым впрыском ![]() |
456.0 | 465.0 | 1.97 |
ШПП ![]() |
540.0 | 560.0 | 3.70 |
вторым впрыском ![]() |
521.0 | 541.0 | 3.84 |
пара за ППНД12 ![]() |
462.0 | 470.0 | 1.73 |
КПД котла (по низшей теплоте сгорания) ηкот, % | 93.67 | 93.63 | 0.04 |
Коэффициент избытка воздуха на выходе из топки αт | 1.2 | 1.2 | 0.00 |
Анализ табл. 1 показывает, что для 20 параметров из 34 приведенных в ней ΔП не превышает 1%, для 4 – находится в диапазоне от 5 до 14%, а для остальных 10 – занимает промежуточное положение.
В целом можно сделать вывод, что статическая модель хорошо описывает работу котла.
Адаптированная динамическая модель котла разрабатывалась на основе статической. Учитывалось, что на начальном этапе пуска в топку подается только мазут марки М100. В расчетную схему были включены новые элементы: паровая турбина, быстродействующие редукционно-охладительные установки высокого и низкого давления (БРОУ ВД и БРОУ НД), конденсатор и др. После этого было проведено замыкание тракта первичного и вторичного пара через БРОУ ВД или паровую турбину (в зависимости от этапа пуска). Далее были заданы параметры, зависящие от нагрузки N. К ним относятся: параметр M, учитывающий характер распределения температуры по высоте топки, коэффициент тепловой эффективности экранов ψэкр, относительное тепловосприятие топочных ширм Qш.отн, температура воды на входе в экономайзер $t_{{ЭК}}^{'}$ и некоторые другие.
Формирование этого блока данных является непростой задачей, особенно для этапа пуска, который заканчивается на нагрузке 30% номинальной. Указаний по этому поводу в [5] нет, а публикаций в открытой печати мало. Поэтому использовались материалы, предоставленные станцией, опыт проведенных ранее расчетов [8, 9] и экспертные оценки авторов.
По рекомендациям [5], коэффициент тепловой эффективности экранов топки ψэкр при сжигании угля должен быть равен 0.45, а для мазута – 0.55. Начальный этап пуска котла на мазуте – кратковременное мероприятие. Поэтому все коэффициенты тепловой эффективности и загрязнения следовало бы принимать, как при сжигании угля. Однако на этапе пуска экраны “холодные”, поэтому математическая модель для топки, представленная в [5], работает плохо. Проще всего скомпенсировать это с помощью ψэкр. В результате собственно для этапа пуска (N = 0–30%) было принято ψэкр = 0.8. В диапазоне нагрузок от 30 до 40% ψэкр линейно снижался до 0.45, так как на этом этапе происходит переход на сжигание угольной пыли, и дальше не менялся. Здесь и далее описано, как менялся параметр во всем диапазоне N от 0 до 100%, поскольку это необходимо задать для первоначальной отладки динамической модели.
Выбор параметра М для динамической модели котла осложнялся тем, что по ходу пуска котла сначала включаются две мазутные форсунки, а затем их число постепенно увеличивается. Примерно через 1.5 ч начинают подавать пыль в основные горелки, а в режиме BMCR (при N = = 100%) работают большая часть горелок и сопла OFA. В конечном счете, в ДМ в диапазоне нагрузки от 0 до 100% параметр М менялся на 0.048, но собственно для этапа пуска (N = 0–30%) он не изменялся.
Относительное тепловосприятие топочных ширм вычисляется по формуле
где qш – плотность теплового потока, воспринятого ШПП, кВт/м2; qт – средняя плотность теплового потока, воспринятого всеми поверхностями нагрева топки, кВт/м2.При разработке статической модели было определено, что Qш.отн = 0.5. В динамической модели было принято, что в диапазоне N = 0–30% Qш.отн линейно возрастает от 0.05 до 0.50 и остается постоянным при N > 30%. Такая зависимость Qш.отн от нагрузки вполне логична, потому что на начальном этапе факелы двух форсунок занимают лишь малую часть топки и ширмы плохо освещены.
Зависимость $t_{{ЭК}}^{'}$ = f(N) задавалась вариативно, так как на станции существует возможность поддерживать различное давление в деаэраторе путем подачи в него стороннего пара. Поэтому в начале пуска температура питательной воды tп.в может составлять 104°C при давлении в деаэраторе 0.1 МПа или 150°C при 0.47 МПа. При исследовании пусков с циркуляционным насосом рассматривали только вариант с tп.в = 104°C, а зависимость $t_{{ЭК}}^{'}$ = f(N) задавали по данным станции с реальных пусков. При расчетах пусков без ЦН рассматривали оба варианта. В первом случае в диапазоне N = 0–18% температура воды на входе в экономайзер была равна $t_{{ЭК}}^{'}$ = tп.в = 104°C, а затем она начинала постепенно возрастать и в режиме BMCR достигала значения 286.4°C, как в статической модели. Во втором случае в диапазоне N = 0–20% принимали $t_{{ЭК}}^{'}$ = tп.в = 150°C, и далее следовало постепенное увеличение $t_{{ЭК}}^{'}$ до 286.4°C. Рост $t_{{ЭК}}^{'}$ происходит вследствие регенеративного подогрева питательной воды.
Основными возмущающими воздействиями для динамической модели котла являются расходы топлива и воздуха. Дополнительными воздействиями служат степени открытия различных регулирующих органов (задвижек и клапанов). Поэтому важно было правильно задать в ДМ график изменения коэффициента избытка воздуха на выходе из топки αт = f(N). Для этого использовали инструкцию по эксплуатации котла и тренды изменения концентрации кислорода за экономайзером, полученные во время реальных пусков. В результате анализа этих материалов была получена упрощенная зависимость αт = f(N): в диапазоне нагрузок от 0 до 10% αт = 3, при N = = 10–30% αт линейно уменьшается до 1.5 и при дальнейшем увеличении N до 100% линейно снижается до 1.2.
Моделирование пуска котла в ДМ из различных тепловых состояний проводилось с учетом графика-задания, взятого из инструкции по эксплуатации котла. Для всех динамических расчетов за начало пуска был принят момент подачи топлива в котел. Скорость нагружения выбирали с учетом выполнения критериев надежности работы. Время выдержки на различных этапах пуска определяли, исходя из условий прогрева элементов котла, которые описаны в инструкции по эксплуатации. После завершения динамического моделирования критерии надежности работы проверяли детально, о чем будет сказано далее. Основные этапы пуска, учтенные в ДМ, представлены в табл. 2.
Таблица 2.
Основные этапы пуска котла
Этап | Время пуска, мин, при исходном состоянии котла | |||
---|---|---|---|---|
холодном | неостывшем | горячем | предельно горячем | |
Горячая промывка | 0–70* | – | – | – |
Набор толчковых параметров | 70–105 | 0–65 | 0–65 | 0–65 |
Толчок паровой турбины | 115–135 | 100–115 | 100–115 | 100–115 |
Окончание толчка паровой турбины (открытие регулирующего клапана) | 150–185 | 165–185 | 115–150 | 115–150 |
Выход на прямоточный режим (прямоток) | 185–215 | 185–215 | 165–185 | 165–185 |
По окончании настройки динамической модели были получены результаты, которые хорошо совпадали с экспериментальными данными по пуску котла с циркуляционным насосом. После этого были выполнены все необходимые динамические расчеты. В итоге были получены графики изменения всех параметров по времени Пi = f(τ). Количество графиков, которые в действительности были проанализированы, очень велико, и они относятся в том числе к различным элементам оборудования. Далее речь пойдет только о результатах, относящихся к пуску из холодного состояния.
Наиболее значимые зависимости Пi = f(τ) приведены на рис. 3, 4.
Рис. 3.
Изменение основных параметров тракта высокого давления во время пуска котла из холодного состояния с использованием ЦН. 1, 2, 3 – расход, температура и давление питательной воды; 4, 5, 6 – расход, температура и давление перегретого пара за котлом; 7, 8 – расход мазута и угля
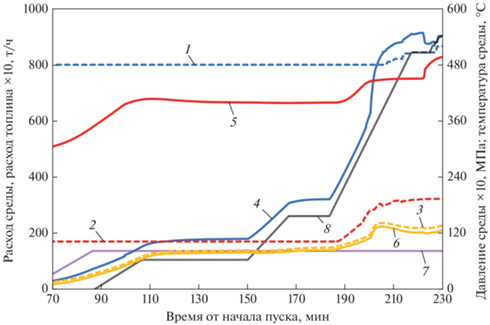
Рис. 4.
Изменение основных параметров тракта высокого давления во время пуска котла из холодного состояния без использования ЦН при температуре питательной воды tп.в = 104°C (а) и tп.в = 150°C (б). Обозначения см. рис. 3
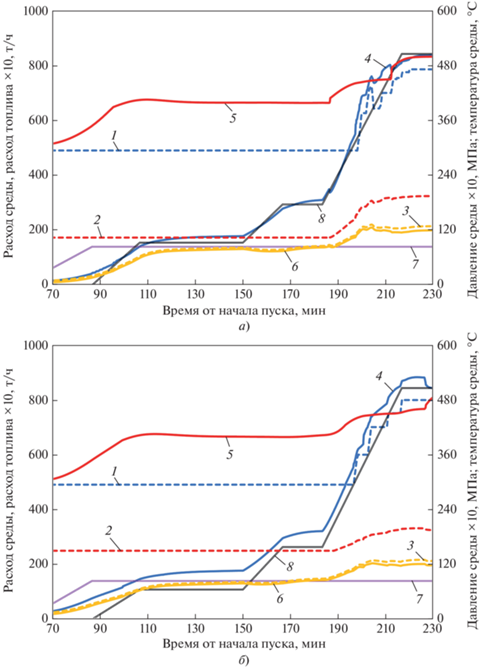
Необходимо отметить, что на начальном этапе времени (τ близко к нулю) динамическая модель ведет себя нестабильно. Поэтому графики, представленные на рис. 3, 4, начинаются с 70-й минуты после подачи топлива в котел, т.е. на них отсутствует этап горячей промывки.
В качестве объектов для расчета температурного режима рассматривались спирально-ленточная навивка НРЧ и передний экран ВРЧ топки. Выбор переднего экрана обусловлен тем, что он имеет самую большую из всех экранов ВРЧ топки площадь поверхности нагрева и, как следствие, максимальное тепловосприятие. Температуры металла определялись по методике [5] в расчетных сечениях на выходе из указанных радиационных поверхностей нагрева.
Для каждого из этапов рассмотренных режимов пуска с ЦН и без него в этих расчетных сечениях определялись четыре значения температуры металла в соответствии со схемой, представленной на рис. 5. Наружная температура стенки tст. н в лобовой точке трубы, обращенной в топку, используется для оценки возможности протекания процесса окалинообразования на поверхности трубы. Средняя температура по толщине стенки в лобовой части трубы tст нужна для проведения прочностных расчетов. Температуры tк и tв в методике [5] называются температурами в корне и в вершине плавника.
Рис. 5.
Схема расположения точек для определения температуры в расчетном сечении. s – шаг труб в экране
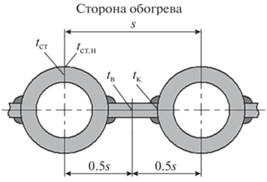
В данном случае все экраны топки выполнены мембранными, а не из плавниковых труб, т.е. tк и tв – это температуры металла по оси экрана в корне и в середине мембраны.
Обычно из четырех перечисленных расчетных значений температур tк – самая низкая, а tст.н или tв – максимальная. Какая из температур – tст.н или tв – больше, зависит от толщины мембраны, соотношения ширины мембраны (высоты плавника) и диаметра труб, размера сварных швов. По методике [5] последовательно рассчитывают значения tст, tст.н, tк и tв. Следует отметить, что температуру металла в середине мембраны на наружной поверхности, обращенной в топку, по [5] не определяют, но ее значение ненамного выше tв. Поэтому tв можно применять для оценки возможности протекания процесса окалинообразования на поверхности мембраны.
Окалинообразование не происходит, если tст.н или tв не превышает некоторого допускаемого значения [tст.н], известного для каждой марки стали. Экраны топки изготовлены из стали SA-213T12, отечественным аналогом которой является сталь марки 12Х1МФ, для которой [tст.н] = 585°C. Оценка надежности работы экранов по условиям прочности сводится к проверке выполнения условия σ ≤ [σ], где σ – расчетное значение напряжения в стенке трубы, Па, а [σ] – его допускаемое значение, Па, которое определяется при расчетном значении tст исходя из свойств материала. Поскольку σ зависит от давления внутри труб, а давление в пусковых режимах значительно меньше, чем в режиме BMCR, то в данном случае проверка выполнения условия прочности не проводилась.
Расчеты температуры металла выполняли в программе Excel. Окончательные данные по всем этапам пуска сведены в табл. 3 и округлены до целых чисел.
Таблица 3.
Расчетные значения температуры стенки для этапов разных режимов пуска
Этап пуска котла | Температура, °C | |||||||
---|---|---|---|---|---|---|---|---|
НРЧ | ВРЧ топки (передний экран) | |||||||
tст | tст.н | tк | tв | tст | tст.н | tк | tв | |
Без циркуляционного насоса: | ||||||||
при tп.в = 104°C: | ||||||||
горячая промывка | 169 | 170 | 169 | 169 | 174 | 174 | 174 | 174 |
толчок | 302 | 306 | 301 | 304 | 297 | 299 | 297 | 300 |
окончание толчка | 306 | 310 | 304 | 308 | 300 | 302 | 300 | 303 |
прямоток | 310 | 319 | 306 | 314 | 547 | 550 | 545 | 551 |
при tп.в = 150°C: | ||||||||
горячая промывка | 200 | 201 | 199 | 200 | 194 | 194 | 193 | 194 |
толчок | 301 | 304 | 299 | 302 | 297 | 298 | 297 | 299 |
окончание толчка | 308 | 312 | 306 | 309 | 302 | 304 | 302 | 305 |
прямоток | 307 | 315 | 304 | 310 | 524 | 526 | 522 | 528 |
С циркуляционным насосом при tп.в = 104°C: | ||||||||
горячая промывка | 203 | 204 | 203 | 203 | 199 | 199 | 199 | 199 |
толчок | 303 | 307 | 302 | 305 | 299 | 300 | 299 | 301 |
окончание толчка | 309 | 313 | 307 | 311 | 303 | 305 | 303 | 306 |
прямоток | 349 | 361 | 345 | 355 | 493 | 497 | 490 | 499 |
При проведении расчетов учитывались не только все конструктивные особенности экранов, но и индивидуальные показатели для отдельных этапов каждого режима пуска: расход среды через экран, начальные параметры среды, тепловосприятие экрана, среднее удельное тепловосприятие лучевоспринимающих поверхностей нагрева топки, фазовое состояние среды в расчетном сечении. Значения всех этих параметров принимались по результатам расчетов по программе Boiler Designer, иногда с учетом рекомендаций [5].
Отдельно необходимо отметить, что в котле HG-2100/25.4-YM16 массовая скорость потока рабочей среды ρw внутри труб экранов топки существенно выше рекомендованных в [3] значений. Так, на номинальной нагрузке в НРЧ ρw = = 2770 кг/(м2 ⋅ с) вместо 2000 кг/(м2 ⋅ с) из [3]. Это привело к тому, что на этапах растопки котла она составляла 690 кг/(м2 ⋅ с), что превышает минимальный уровень массовой скорости 500–600 кг/(м2 ⋅ с) и позволяет надежно охлаждать все трубы НРЧ.
Анализируя данные табл. 3, можно отметить, что для этапа “горячая промывка” всех рассмотренных режимов пуска температуры металла не превышают 204°C. Это связано с тем, что в НРЧ во всех случаях протекает еще не кипящая вода, а на выходе из ВРЧ массовое паросодержание x не превышает 5%. При этом среднее удельное тепловосприятие лучевоспринимающих поверхностей нагрева топки qл очень мало – от 3.023 до 3.489 кВт/м2. Для режима с циркуляционным насосом температура металла даже несколько выше, так как начальная температура воды на входе в НРЧ возрастает, поскольку в контуре циркулирует нагретая среда.
Для этапов “толчок” и “окончание толчка” всех режимов аналогичные температуры различаются всего на несколько градусов и нигде не превышают 313°C. Общий рост температуры связан с тем, что повышается уровень тепловосприятия qл, которое в данном случае находится в диапазоне 17.458–23.260 кВт/м2. Малое различие всех температур (297–313°C) обусловлено тем, что в расчетных сечениях разверенных труб во всех случаях находится кипящая вода. Поэтому превышение температуры среды в расчетной точке над средней составляет Δtт = 0 и температуры металла для разных режимов различаются лишь из-за давления среды на входе в НРЧ (от которого зависит температура насыщения) и из-за qл. Для этих этапов пуска температуры металла незначительно (на 1–3°C) выше в режиме с ЦН, потому что выше давление среды и температура насыщения.
Для этапа “прямоток” удельное тепловосприятие лучевоспринимающих поверхностей нагрева топки qл существенно возрастает. Для режимов без ЦН qл = 44.977 и 42.438 кВт/м2 при начальной температуре питательной воды 104 и 150°C соответственно. Для режима с ЦН расходы воды и топлива больше, поэтому qл = 62.432 кВт/м2. Во всех случаях на выходе из НРЧ – кипящая вода с массовым паросодержанием x = 53–54%, а на выходе из переднего экрана ВРЧ топки – пар. Температуры металла на выходе из НРЧ в режимах без ЦН меньше и составляют 304–319°C. В режиме с ЦН из-за большего давления температура насыщения выше и qл больше, поэтому и температуры металла выше и составляют 345–361°C.
Но в ВРЧ, где на выходе – перегретый пар, ситуация другая. Здесь температуры металла для режима с ЦН меньше и находятся в диапазоне 490–499°C. Это связано с тем, что данном случае Δtт ≈ 99°С, тогда как для режимов без ЦН перепад температур в 1.5 раза больше. Кроме того, коэффициент теплоотдачи от трубы к среде в расчетном сечении для режима с ЦН из-за большего расхода и скорости пара получается выше. Для режимов без ЦН на этапе “прямоток” температура металла разверенных труб на выходе из ВРЧ топки составляет 545–551°C и 522–528°C при начальной температуре питательной воды 104 и 150°C соответственно. Это объясняется тем, что в первом случае приращение энтальпии среды Δh в ВРЧ несколько выше, поэтому Δtт получается больше.
Примечательно, что для всех случаев (см. табл. 3) в НРЧ максимальной получается наружная температура стенки трубы tст.н, а в ВРЧ – температура в вершине плавника tв. Это связано с тем, что при меньшем диаметре трубы ширина мембраны в ВРЧ больше, поэтому металл мембраны хуже охлаждается.
В заключение стоит отметить, что во всех рассмотренных случаях температура металла меньше, чем допускаемое значение [tст.н] = 585°C, следовательно, протекание окалинообразования не ожидается. Если же сравнивать рассмотренные пусковые режимы без ЦН, то предпочтительнее будет вариант с большим начальным значением температуры питательной воды (150°C), потому что температуры метала в конце ВРЧ на этапе “прямоток” в этом случае получаются ниже.
В ходе исследований было зафиксировано некоторое уменьшение крутизны гидравлической характеристики, которое, однако, не привело к снижению надежного охлаждения экранов топки в рабочих областях. Дополнительно следует упомянуть, что могут возникнуть проблемы с осуществлением слива воды из сепаратора в расширитель. Проведенные расчеты показали, что расход слива существенно возрастает, из-за чего может потребоваться увеличение внутреннего диаметра трубы за регулирующим клапаном с 149 до 224 мм. Окончательный вывод о достаточности пропускной способности слива из встроенного сепаратора можно будет сделать по итогам проведения экспериментального пуска.
Возвращаясь к другим критериям надежности, нужно отметить, что и они во всех случаях выполнялись. Так, например, про расход пара, охлаждающего пароперегревательный тракт, при пуске из холодного состояния (худший случай) можно сказать следующее: при атмосферном давлении в деаэраторе в начале пуска при tп.в = = 104°C он несколько ниже, чем при пуске с ЦН. На этапе горячей промывки расход пара при пуске без насоса ниже на 20–50%, чем при пуске с ЦН. Однако температура газов по тракту на этом этапе не превышает 450°C, поэтому снижение расхода пара не окажет влияния на надежность работы пароперегревательных поверхностей нагрева. На этапах толчка паровой турбины и выхода котла на прямоточный режим расход пара при пуске без насоса ниже на 3–11%, чем при пуске с ЦН. Такое снижение расхода пара не приведет к значительному ухудшению работы пароперегревательных поверхностей нагрева, расход воды на впрыски увеличивается незначительно. При пуске котла с tп.в = 150°C разница в расходах пара после сепараторов в режимах с ЦН и без него укладывается в расчетную погрешность.
Что касается температуры газов на выходе из топки, то в режимах пуска котла без циркуляционного насоса она на всех этапах заметно ниже, чем при пуске с ЦН. Это обусловлено уменьшением расхода топлива, о чем говорилось ранее. В результате условия надежной работы ППНД2 должны быть обеспечены.
Таким образом, проведенные исследования показали, что при использовании упрощенной схемы пуска без циркуляционного насоса все критерии надежной работы выполняются. Поэтому не исключено внедрение такой схемы на котле HG-2100/25.4-YM16.
ВЫВОДЫ
1. Разработанная адаптированная динамическая модель котла HG-2100/25.4-YM16 позволяет в первом приближении рассматривать различные режимы пуска и проводить их оптимизацию.
2. С использованием динамической модели исследованы режимы пуска котла с использованием циркуляционного насоса и без него. Выполнена оценка температурного режима НРЧ и ВРЧ для всех рассмотренных режимов и этапов пуска. Она дала положительные результаты, что не исключает применения пусковой схемы без циркуляционного насоса.
3. Надежность работы ступеней пароперегревателя при использовании такой схемы обеспечивается за счет поддержания расхода пара и температуры газов по тракту котла на уровне близком к значениям, полученным при пусках с циркуляционным насосом.
Список литературы
Kitto J.B., Stuits S.C. Steam: its generation and use. 41st ed. Barberton: The Babcock & Wilcox Company, 2005. [Ohio, USA.]
Yuxin W.U., Shijie L. Start-up program and analysis of 660 MW ultra supercritical unit without boiler circulating pump // Electr. Power Constr. 2011. V. 1. P. 83–85.
Гидравлический расчет котельных агрегатов. Нормативный метод / О.М. Балдина, В.А. Локшин, Д.Ф. Петерсон, И.Е. Семеновкер, А.Л. Шварц. М.: Энергия, 1978.
Расчет котельных агрегатов с использованием современных программных продуктов / Г.И. Доверман, Б.Л. Шелыгин, А.В. Мошкарин, Ю.В. Мельников. Иваново: ИГЭУ, 2007.
Тепловой расчет котельных агрегатов. Нормативный метод. М.: Энергия, 1973.
Супранов В.М., Изюмов М.А., Росляков П.В. Исследование возможности работы котла ТПЕ-208 энергоблока № 1 Смоленской ГРЭС на непроектных углях // Теплоэнергетика. 2011. № 1. С. 44–54.
Супранов В.М., Штегман А.В., Фоменко Е.А. Оценка возможности перевода котлов ТП-14А Кумертауской ТЭЦ на сжигание угля марки Б3 Верхне-Сокурского месторождения // Теплоэнергетика. 2016. № 4. С. 50–59. https://doi.org/10.1134/S0040363616040081
Плешанов К.А., Стерхов К.В., Зайченко М.Н. Расчет динамических характеристик котла-утилизатора Новогорьковской ТЭЦ // Электрические станции. 2015. № 4. С. 10–15.
Разработка и исследование технологии пуска твердотопливного котла Е-240-13.8-560 АО “ЗиО” / К.А. Плешанов, К.В. Стерхов, В.П. Князьков, А.Р. Квривишвили // Электрические станции. 2018. № 4. С. 15–23.
Дополнительные материалы отсутствуют.
Инструменты
Теплоэнергетика