Теплофизика высоких температур, 2019, T. 57, № 2, стр. 269-277
Термическая деструкция резиноподобных теплозащитных материалов под слоем конденсированной фазы
В. В. Миронов 1, *, М. А. Толкач 1
1 ГНЦ РФ – ФГУП “Исследовательский центр им. М.В. Келдыша” (Центр Келдыша),
Москва, Россия
* E-mail: kerc@elnet.msk.ru
Поступила в редакцию 16.01.2018
После доработки 05.06.2018
Принята к публикации 24.04.2018
Аннотация
На основании анализа результатов экспериментальных исследований прогрева и разрушения резиноподобных материалов под воздействием высокотемпературного двухфазного потока предложен метод уточнения глубин термической деструкции теплозащитного покрытия под слоем осаждающейся конденсированной фазы на момент окончания работы энергетической установки. Учитывается дополнительное коксование и термическое расширение остаточной толщины покрытия в период остывания установки. Предложен новый подход к верификации наличия термического расширения материала теплозащиты в области прогрева ниже температур деструкции.
ВВЕДЕНИЕ
Надежность работы и энергомассовое совершенство современных высокотемпературных энергетических установок, работающих при высоких температурах, во многом определяются правильным выбором теплозащитных материалов (ТЗМ) и конструкцией теплозащитного покрытия (ТЗП) [1].
Для защиты стенок элементов конструкции установок от воздействия высокотемпературного двухфазного потока (газа, содержащего частицы конденсата) широко используются различные резиноподобные материалы, в состав которых наряду с каучуком входят наполнители в виде порошка диоксида кремния (белой сажи), технического углерода, органических и углеродных волокон [2–4]. В таких ТЗП вследствие интенсивных силовых, тепловых, эрозионных и термохимических нагрузок происходят сложные физико-химические и термомеханические процессы. Среди них тепловое расширение и многостадийная термическая деструкция материала с тепловыми эффектами и выделением газообразных продуктов термодеструкции. Теоретические модели таких процессов сложны, достаточно приблизительны и требуют проверки (верификации) на значительном массиве экспериментальных данных.
Одним из факторов, влияющих на скорость деградации ТЗП, является осаждение и накопление на его поверхности конденсированных продуктов из высокотемпературного двухфазного потока, имеющих температуру 3000–4000 К. Например, такая ситуация имеет место в ракетных двигателях твердого топлива в области заднего днища и предсоплового объема, где могут образовываться локальные пленки из жидкого конденсата Al2O3 [1].
Одной из наиболее важных характеристик прогрева и разрушения ТЗП, отражающих газодинамические и тепловые процессы в рабочей камере, является глубина термической деструкции δд покрытия, достигаемая к моменту окончания работы установки. Важность и необходимость знания δд обусловлена ее использованием при определении необходимых толщин теплозащитного покрытия, обеспечивающих надежную работу установки.
Для определения δд изучаются особенности прогрева и разрушения материалов теплозащитного покрытия как в процессе работы установки при воздействии высокотемпературного двухфазного потока и осаждающейся конденсированной фазы, так и после выгорания топлива, т.е. в период остывания установки. Для восстановления δд определяются и используются глубина дополнительного коксования покрытия в период остывания установки и изменение объемных характеристик (расширение или усадка) материалов ТЗП в области ниже зоны термической деструкции, т.е. в области, не претерпевшей разложения.
В настоящей работе проанализированы данные испытаний ряда резиноподобных теплозащитных материалов. Экспериментальные исследования проводились на специальной установке в ГНЦ “Центр Келдыша” с моделированием двухфазного потока и прогнозируемым осаждением конденсированной фазы на поверхность образца резиноподобного теплозащитного материала (рис. 1).
ЗАВИСИМОСТЬ ГЛУБИНЫ ТЕРМИЧЕСКОЙ ДЕСТРУКЦИИ ОТ ПРОДОЛЖИТЕЛЬНОСТИ ИНТЕНСИВНОГО ПРОГРЕВА
Близкие по схеме устройства (рис. 1) для исследования прогрева и разрушения ТЗМ с твердотопливным газогенератором используются давно [1].
Испытываемые образцы ТЗМ 3 и 4 размещены в рабочем отсеке таким образом, что после сепарирующей вставки 2 жидкая конденсированная фаза осаждается на нижний образец 4, образуя слой конденсата 5. При этом верхний образец 3 обтекается газовым потоком со скоростью ≤25 м/с. С помощью теплоизоляторов образцы ТЗМ предохраняются от воздействия газового потока и конденсированной фазы по всем граням, кроме “рабочей” поверхности. Продолжительность работы газогенератора 1, а следовательно, интенсивного прогрева и разрушения образцов ТЗМ 3 и 4 варьировалась от ~5 до ~40 с. Конденсат 5 скапливался на нижнем образце 4 толщиной до ~10 мм (с линейным увеличением толщины по времени).
Испытания проводились в двух режимах. В первом случае для устранения дополнительного коксования, и таким образом прекращения увеличения глубины деструкции в период остывания установки, в рабочий отсек установки непосредственно после окончания работы газогенератора 1 (менее чем через 3 с) подавалась вода. При втором режиме вода в рабочий отсек не подавалась вовсе или подавалась через достаточно длительный промежуток времени (2–15 мин). В отсутствие подачи воды, из-за перетока тепла от слоя конденсата 5 и прогретых элементов конструкции происходит дальнейшее коксование образцов 3 и 4 (дополнительное увеличение глубины деструкции) и термическое расширение в области ниже температур деструкции (утолщение не подвергнутого термодеструкции слоя образца ТЗМ).
Под воздействием теплового потока Q от высокотемпературного двухфазного потока и осаждающихся на поверхность конденсированных продуктов ТЗП прогревается, претерпевает реакции термической деструкции с выделением газообразных продуктов и их фильтрацией через образующийся коксовый слой (рис. 2).
Рис. 2.
Схема термической деструкции покрытия под слоем конденсата (Те – температура нагревающего газового потока).
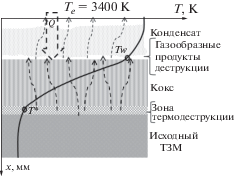
Основная часть физико-химических превращений коксующихся материалов происходит при температурах, которые существенно ниже температуры поверхности Tw покрытия со стороны прогрева. Область термической деструкции для большинства резиноподобных ТЗМ ограничивается достаточно узким температурным интервалом c характерной температурой Т *~300°С, соответствующей максимальной скорости потерь массы, т.е. максимальной скорости газовыделения (рис. 2). Образующиеся газообразные продукты деструкции, фильтруясь через поры коксового остатка, участвуют в реакциях крекинга, а их отдельные компоненты могут вступать в химические реакции с твердой фазой – коксовым слоем [1, 5, 6]. Теплофизические свойства материала по мере его прогрева и разрушения сильно изменяются, зависят от температуры и темпа прогрева.
Рассмотрим результаты исследований глубин термодеструкции двух характерных теплозащитных материалов на основе этиленпропилендиенового каучука: эластичного (мягкого) ТЗМ-1 и жесткого ТЗМ-2. Жесткость ТЗМ-2 обусловлена наличием в его составе наполнителя в виде асбестового волокна. Основные теплофизические (при температуре ниже начала термодеструкции) и теплозащитные характеристики этих материалов приведены в табл. 1.
Таблица 1.
Характеристика ТЗМ | ТЗМ-1 | ТЗМ-2 |
---|---|---|
ρ, кг/м3 | 1040–1080 | 1130–1160 |
λ, Вт/(м К) | 0.23–0.27 | 0.21–0.25 |
с, кДж/(кг К) | 1.53–2.02 | 1.50–2.02 |
ξ, м/с1/2 | 1.0 × 10–3 | 0.85 × 10–3 |
ζ, м | 1.0 × 10–3 | 0.85 × 10–3 |
К, коксовое число | 0.22–0.24 | 0.31–0.32 |
Условия моделирования теплового нагружения образцов: температура газовой смеси ~3400 К; весовая доля конденсированных продуктов, преимущественно Al2O3, ~0.35; давление в отсеке ~5 МПа. Площадь S образцов 3 и 4 (см. рис. 1) со стороны прогрева (со стороны газового потока и конденсированной фазы) составляла 18 см2.
Образцы ТЗМ взвешивались перед их установкой в рабочую камеру и после испытаний с предварительной тщательной очисткой от прококсованного слоя. Далее определялись глубины термодеструкции ТЗМ δдр (в 5–6 сечениях – как разница между начальной и конечной толщинами) и вычислялось их среднее значение ${{\bar {\delta }}_{{{\text{д р }}}}}$. По этим данным определялась начальная масса части образца, претерпевшей физико-химические превращения в режиме коксования – как разность между начальной и конечной массами образца ΔМ.
В результате, используя ${{\bar {\delta }}_{{{\text{д р }}}}}$ и ΔМ, можно вычислить характерную исходную плотность материала ρх0 для части образца, подвергнутой термической деструкции:
Схема процесса коксования приведена на рис. 3.
На рис. 3 приняты следующие обозначения: l0 – измеренная начальная толщина образца в данном сечении; lк, lкр – измеренные конечные толщины образца в данном сечении в отсутствие и при наличии термического расширения непрококсованного слоя; δд, δдр – глубины термической деструкции в отсутствие и при наличии расширения, вычисляемые как (l0 – lк) и (l0 – lкр) соответственно; δр – толщина, на которую увеличивается прогретый, но не прококсованный слой ТЗМ в рассматриваемом сечении.
Из соотношения (1) следует, что, если слой материала, не претерпевший термической деструкции, не изменяет своих размеров (толщины), то значение вычисленной плотности ρх0 должно быть равно плотности исходного материала ρ0.
Если область образца ниже температур деструкции претерпит расширение, то δдр уменьшается (так как lкр увеличится, см. рис. 3), и, следовательно, ρх0, согласно соотношению (1), увеличивается. Значение ρх0, согласно (1), может использоваться для верификации наличия/отсутствия термического расширения/усадки в области образца, не подвергнутой термической деструкции: если ρх0 > ρ0, имеет место термическое расширение; если ρх0 < ρ0, происходит усадка; если ρх0 = ρ0, материал остается в исходном состоянии.
Практически для всех испытаний без гашения получено ρх0 > ρ0 (для верхнего и нижнего образцов). В ~5% от общего количества образцов вычисленные значения ρх0 оказались меньше ρ0. При этом наблюдались следы прогрева и разрушения образцов с боковых граней (из-за нарушения боковой термоизоляции), что, видимо, и привело к увеличению ${{\bar {\delta }}_{{{\text{д р }}}}}$. Данные для этих образцов в анализе не учитывались.
При известных ρх0, ρ0 и ${{\bar {\delta }}_{{{\text{д р }}}}}$ фактическая (т.е. вычисленная с учетом термического расширения) глубина термической деструкции δф для рассматриваемого образца (3 и 4 на рис. 1) может быть определена с использованием соотношения
(2)
${{\delta }_{{\text{ф }}}} = {{\bar {\delta }}_{{{\text{д р }}}}}\frac{{{{\rho }_{{x0}}}}}{{{{\rho }_{0}}}} = \frac{{\Delta M}}{{S{{\rho }_{0}}}}.$На рис. 4 приведены глубины термической деструкции для образцов ТЗМ-1 и ТЗМ-2.
Рис. 4.
Зависимость глубины деструкции от времени для ТЗМ-1 (а), (б) и ТЗМ-2 (в), (г); (а), (в) – при гашении, (б), (г) – без гашения; (a), (б) 5 – δ = $1.0\sqrt \tau - 1,$ (в), (г) 5 – δ = $0.85\sqrt \tau - 0.85.$
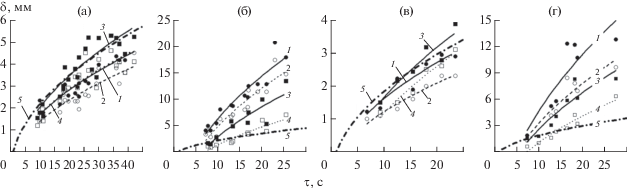
Светлыми значками изображены значения ${{\bar {\delta }}_{{{\text{д р }}}}},$ вычисленные непосредственно по результатам замеров толщин образца. Темными значками – значения δф, вычисленные по (2), т.е. глубины деструкции поправлены с учетом термического расширения области недеструктировавшего материала.
Каждая пара светлый–темный значок является результатом отдельного испытания (всего обработано порядка 40). Пунктирной и сплошной линиями на рисунках изображены зависимости, полученные при обработке методом наименьших квадратов (МНК) данных по ${{\bar {\delta }}_{{{\text{д р }}}}}$ и δф соответственно. При обработке МНК зависимость глубины деструкции от времени принималась в виде стандартного (общепринятого [1]) соотношения
Полученные значения ξ и ζ для каждой из кривых 1–4 приведены в табл. 2.
Таблица 2.
Значение коэффициентов ξ и ζ в (3) для ТЗМ-1 и ТЗМ-2
Марка ТЗМ | Положение образца ТЗМ | Учет термического расширения | С гашением | Без гашения | Обозначение на рис. 4 | ||
---|---|---|---|---|---|---|---|
ξ | ζ | ξ | ζ | ||||
ТЗМ-1 | Верх | Нет | 0.88 | 1.08 | 2.59 | 6.87 | 4 |
Да | 1.10 | 1.48 | 4.36 | 10.96 | 3 | ||
Под конденсатом | Нет | 0.75 | 1.01 | 5.56 | 12.83 | 2 | |
Да | 0.87 | 1.06 | 6.19 | 13.37 | 1 | ||
ТЗМ-2 | Верх | Нет | 1.07 | 2.2 | 2.33 | 6.35 | 4 |
Да | 1.16 | 2.02 | 3.23 | 7.73 | 3 | ||
Под конденсатом | Нет | 0.66 | 0.87 | 3.51 | 7.91 | 2 | |
Да | 0.83 | 1.01 | 4.97 | 11.17 | 1 |
Штрихпунктирной линией на графиках нанесены зависимости глубины деструкции, вычисляемые согласно (3) с ξ и ζ, полученными в исследованиях с использованием термопарных измерений и без осаждения конденсированной фазы. При этом глубина деструкции определялась по положению характерной изотермы 300°С.
Полученные результаты указывают на значительное различие в глубинах термической деструкции обследованных ТЗМ для случаев с гашением и в его отсутствие. Причем отличие имеет место как для случая нахождения ТЗМ под слоем конденсированной фазы, так и для верхних образцов ТЗМ в газовом потоке. Для образца под слоем конденсированной фазы значительное увеличение глубин термической деструкции при отсутствии гашения не удивительно – обусловлено кондуктивной передачей тепла от конденсата в образец. Для образцов, не контактирующих со слоем жидкого конденсата (верхних), значительное увеличение глубин деструкции в период остывания установки (без гашения) обусловлено перетеканием тепла за счет излучения и конвекции как от конденсированной фазы, так и от сильно прогретых деталей (элементов) рабочей камеры установки (см. рис. 1).
В случае испытаний с гашением обращает на себя внимание то, что глубины термической деструкции для ТЗМ-1 и ТЗМ-2 под слоем конденсата несколько меньше, чем для верхнего образца. Отличие в δф (в %) определялось как непосредственно по их величине, так и по полученным значениям коэффициента деструкции ξ (см. табл. 2). Результаты представлены в табл. 3.
Поскольку постоянные ζ в (3) отличаются от полутора для ТЗМ-1 и до двух раз для ТЗМ-2 (табл. 2), постоянные ξ характеризуют не столько глубину деструкции, сколько скорость ее перемещения в фиксированный момент времени прогрева. В силу этого корректными представляются лишь оценки по величине δф. Под слоем конденсата глубина деструкции на ~10–20% может быть меньше, чем в области, где ТЗМ подвержен прогреву лишь от газового потока. Для материала с меньшим коксовым числом (ТЗМ-1) расхождение в глубинах деструкции больше.
Согласно результатам исследований, изложенным в [8], возможным увеличением глубины коксования верхнего образца за счет разрушения (осыпания) коксового остатка с поверхности прогрева в поле массовых сил (n = 1 – только сила тяжести) можно пренебречь. Учитывая это, полагаем, что образующийся на ТЗМ слой конденсата играет роль теплового сопротивления, частично изолируя образец от внешнего теплового потока в процессе работы установки. Кроме этого, при интенсивном разложении материалов покрытия возможно образование газовой прослойки между конденсатом и поверхностью прококсованного слоя (см. рис. 2), что также является дополнительным тепловым сопротивлением.
В табл. 4 приведены результаты оценки среднеквадратичного отклонения s и коэффициента вариации V для глубины термической деструкции, полученные при обработке экспериментальных данных для исследованных материалов в соответствующих условиях. Коэффициент вариации определялся для глубин деструкции с максимальным временем интенсивного прогрева.
Таблица 4.
Среднеквадратичное отклонения s и коэффициента вариации V
ТЗМ | С гашением | Без гашения | Примечание | ||||||
---|---|---|---|---|---|---|---|---|---|
в потоке | под конденсатом | в потоке | под конденсатом | ||||||
s, мм | V, % | s, мм | V, % | s, мм | V, % | s, мм | V, % | ||
ТЗМ-1 | 0.742 | 13.1 | 0.36 | 7.9 | 1.756 | 16.0 | 1.633 | 9.2 | С учетом термического расширения |
0.471 | 10.2 | 0.387 | 10.0 | 0.823 | 13.3 | 1.562 | 10.3 | По данным измерений | |
ТЗМ-2 | 0.29 | 8.0 | 0.234 | 7.7 | 1.037 | 11.2 | 2.04 | 13.7 | С учетом термического расширения |
0.153 | 5.1 | 0.127 | 5.4 | 0.469 | 8.0 | 1.05 | 10.0 | По данным измерений |
Полученные значения s и V указывают на следующее. Наличие термического расширения приводит к увеличению среднеквадратичного отклонения и коэффициента вариации для глубин термической деструкции обоих материалов, прогреваемых без образования слоя конденсата на их поверхности. Для жесткого материала ТЗМ-2 эта закономерность сохраняется и в случае термической деструкции под слоем конденсата. Для более эластичного ТЗМ-1 под слоем конденсата тенденция имеет обратный характер, что, возможно, связано с более стабильным его термическим расширением (распуханием) в области температур, ниже температуры деструкции. Отметим, что эти закономерности сохраняются как при наличии, так и отсутствии гашения/охлаждения образцов материалов после интенсивного прогрева. Значения s для ТЗМ-1 заметно выше (в два и более раза), чем у ТЗМ-2 при прогреве образцов “в потоке”, т.е. без образования слоя конденсата на поверхности. Использование гашения приводит к значительному уменьшению разбросов, что указывает на существенное влияние на величины среднеквадратического отклонения и коэффициента вариации отличий в условиях теплообмена в период остывания установки. Разбросы, получаемые в испытаниях без гашения, лишь частично являются характеристикой материала.
ДОПОЛНИТЕЛЬНОЕ КОКСОВАНИЕ ТЕПЛОЗАЩИТЫ ПРИ ОСТЫВАНИИ УСТАНОВКИ
Как уже отмечалось выше, для обследованных ТЗМ увеличение глубины деструкции в период остывания установки весьма существенно как для образцов под слоем конденсированной фазы, так и образцов, находящихся в потоке. Проведем оценки глубин дополнительного коксования образцов в период их остывания. Для этого сравним глубины термодеструкции δф для случаев с гашением и без него. Используем значения δф при 20-секундном прогреве. Необходимые основные исходные данные и результаты оценок помещены в табл. 5. В силу значительных величин постоянной ζ в (3) (ζ изменяется от ~5 до ~14), использование постоянных ξ для сравнения глубин деструкции некорректно.
Таблица 5.
Отличие в глубине деструкции образцов
Положение образца | Марка ТЗМ | Значение δф, мм | Отличие, % | |
---|---|---|---|---|
с гашением | без гашения | |||
Верх | ТЗМ-1 | 3.5 | 8.6 | 145 |
ТЗМ-2 | 3.17 | 6.7 | 113 | |
Низ (под конденсатом) | ТЗМ-1 | 2.8 | 14.2 | 407 |
ТЗМ-2 | 2.7 | 11.0 | 307 |
Для верхних образцов ТЗМ без осаждения конденсированной фазы отличие составляет ~100% … ~150%. Для нижнего образца разница увеличивается до ~300% … ~400%. Дополнительное коксование не менее чем в два раза выше для ТЗМ под слоем конденсата, чем в материале, на который конденсат не осаждался.
Дополнительное коксование ТЗМ в период остывания установки учитывалось с использованием коэффициента α* – отношения глубины дополнительного коксования к толщине прококсованного слоя (кокса) на момент окончания работы установки. В этом случае справедливо соотношение
где δд – глубина деструкции (толщина прококсованного слоя) с учетом дополнительного коксования; δд0 – глубина термической деструкции на момент завершения работы установки.Для установки, на которой проводились экспериментальные исследования (см. рис. 1), α* существенно отличается от значения для случая, когда дополнительное коксование определяется лишь теплом, накопленным в прококсованном слое покрытия (α* ~ 0.15–0.17 [1]). Согласно результатам, приведенным в табл. 5, оценка величин α* для условий настоящих экспериментальных исследований представлена в табл. 6.
Таблица 6.
Значения α* в отсутствие гашения
Марка ТЗМ | α* | |
---|---|---|
в потоке | под конденсатом | |
ТЗМ-1 | 1.45 | 4.07 |
ТЗМ-2 | 1.13 | 3.07 |
Для эластичного ТЗМ-1 дополнительное коксование заметно выше, чем для жесткого ТЗМ-2.
Эти результаты указывают на необходимость детального анализа экспериментальных данных по глубинам термодеструкции, получаемым из замеров толщин покрытия до и после испытания. При этом требуется предварительное определение глубин дополнительного коксования после окончания работы установки. Ввиду этого очевидна необходимость проведения испытаний материалов с применением гашения установки непосредственно после окончания ее работы.
ТЕРМИЧЕСКОЕ РАСШИРЕНИЕ НЕ ПОДВЕРГНУТОГО КОКСОВАНИЮ СЛОЯ МАТЕРИАЛА
Обратимся теперь к термическому расширению области ТЗМ, прогретой ниже температур деструкции.
Величина термического расширения области прогретого, но не продеструктировавшего слоя (исходного) ТЗМ, вычисляется как δрас = δф – ${{\bar {\delta }}_{{{\text{д р }}}}},$ (см. рис. 3). Массивы полученных значений δрас обрабатывались с помощью МНК в представлении линейной зависимости δрас от δф:
где A и B – постоянные.На рис. 5 представлены как непосредственно вычисленные дискретные значения термического расширения δрас для каждого из ТЗМ, так и соответствующие линейные зависимости согласно полученным МНК постоянным А и В (табл. 7).
Рис. 5.
Зависимость δрас прогретого слоя от глубины термодеструкции (толщины кокса): (а) – при гашении, (б) – без гашения.
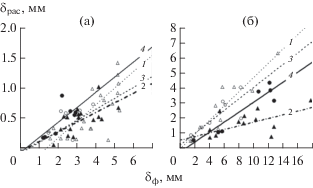
Таблица 7.
Значение постоянных A и B в (5)
Марка ТЗМ | Положение образца ТЗМ | При гашении | Без гашения | Знак на рис. 5 | ||
---|---|---|---|---|---|---|
А | В | А | В | |||
ТЗМ-1 | Верх | 0.28 | 0.34 | 0.47 | 0.01 | 1 |
Под конденсатом | 0.16 | 0.01 | 0.12 | 0.57 | 2 | |
ТЗМ-2 | Верх | 0.18 | 0.04 | 0.38 | 0.25 | 3 |
Под конденсатом | 0.25 | 0.03 | 0.33 | –0.22 | 4 |
Точечная и пунктирная зависимости (для верхнего образца ТЗМ) построены по значениям, отображенным светлыми значками. Сплошная и штрихпунктирная прямые (для нижнего образца, под конденсатом) построены по значениям, отображенным темными значками.
Первое, что следует отметить, для исследованных материалов термическое расширение имеет место как при наличии, так и в отсутствие гашения установки. И второе, в отсутствие гашения термическое расширение значительно превышает величины при гашения. Это указывает на то, что процесс увеличения объема ТЗП в прогретой области образца без термической деструкции происходит и после спада давления, т.е. в период остывания установки.
Для эластичного ТЗМ-1 имеет место значительное отличие в термическом расширении для верхнего и нижнего образцов. Отличие достигает при гашении 70%, без гашения – 290% (см. зависимости 1 и 2 на рис. 5). Для жесткого ТЗМ-2 отличие значительно меньше: при гашении – 40%, без гашения – 15% (3 и 4 на рис. 5).
Имеет ли место термическое расширение в области ТЗМ прогретой ниже температур деструкции во время работы установки, остается под вопросом. Об отсутствии термического расширения материала при интенсивном прогреве и высоком давлении в рабочей камере в некоторой мере свидетельствует близость глубин деструкции, полученных в данном случае через измерение начальных и конечных толщин покрытия для образцов без осаждения конденсированной фазы, и глубин проникновения изотермы с характерной температурой деструкции в 300°С (см. рис. 4а, 4в), линии 5 и 3 в близких условиях прогрева. Естественно, при этом использовались результаты замеров толщин образцов после испытаний с гашением.
Утолщение прогретого до температур ниже температуры деструкции слоя ТЗМ за счет термического расширения при использовании гашения составляет менее 1 мм (с максимальным временем интенсивного прогрева ~25 с и при δф ≈ 3–4 мм – см. рис. 4а, 4в). В то же время, если гашение не использовалось, термическое расширение достигало 3–4 мм (при δф ≈ 15–20 мм, см. рис. 4б, 4г), т.е. дополнительно увеличивалось на 2–3 мм.
Если не учитывать термическое расширение, то ошибки в оценках реальной глубины деструкции на момент окончания работы высокотемпературной установки достигнут аналогичных величин. Такие ошибки в определении глубин деструкции, а впоследствии и потребных толщин покрытия недопустимы (особенно если используются данные эксперимента без гашения).
В силу вышеизложенного, очевидна необходимость восстановления (пересчета) глубин деструкции на момент окончания работы установки, в том числе и с учетом термического расширения прогретого и не деструктировавшего слоя ТЗП. При известной разности начальной и конечной (с удаленным коксом) толщин теплозащитного покрытия δ фактическая глубина термической деструкции δд (поправленная на термическое расширение) может быть вычислена с использованием соотношения (без поправки на дополнительное коксование в период остывания установки):
Здесь α** – коэффициент, учитывающий термическое расширение прогретого, но не деструктировавшего слоя.Согласно результатам экспериментальных исследований оцененные коэффициенты термического расширения α** для исследованных ТЗМ приведены ниже в табл. 8.
Таблица 8.
Значение коэффициента термического расширения α**
Марка ТЗМ | α** | |||
---|---|---|---|---|
с гашением | без гашения | |||
в потоке | под конденсатом | в потоке | под конденсатом | |
ТЗМ-1 | 0.20 | 0.16 | 0.47 | 0.16 |
ТЗМ-2 | 0.17 | 0.25 | 0.39 | 0.31 |
При использовании гашения величина термического расширения прогретого слоя ТЗМ как в потоке, так и под слоем конденсата составляет 15–25% от глубины термодеструкции (толщины прококсованного слоя). При отсутствии гашения термическое расширение может быть существенно выше – до ~50%.
Согласно (4) и (6) толщина прококсованного слоя ТЗМ на конец работы установки (после спада давления) будет составлять
При интенсивном тепловом воздействии продуктов сгорания, в том числе и конденсированной фазы, профиль температуры в покрытии является достаточно крутым (температура резко падает с увеличением глубины). В этом случае слой ТЗМ, прогретый до температур, при которых возможно термическое расширение, достаточно тонок. Предполагая, что удаление прококсованного слоя при тщательной его очистке происходит по конечному положению изотермической поверхности с температурой в 200°С, проведены оценки относительного линейного удлинения для двух случаев: 1 – область термического расширения лежит в диапазоне от 50 до 200°С, 2 – в диапазоне от 100 до 200°С. Необходимые теплозащитные и теплофизические характеристики, использованные при оценках толщин прогретого слоя, приведены в табл. 1.
Результаты оценок толщин прогретого слоя в зависимости от толщины прококсованного слоя покрытия, представлены в табл. 9.
Таблица 9.
Глубина прогрева в заданной области температур
Область температур, °С | Глубина деструкции, мм | Величина прогрева, мм | |
---|---|---|---|
ТЗМ-1 | ТЗМ-2 | ||
50–200 | 2 | 1.05 | 0.92 |
4 | 1.76 | 1.53 | |
6 | 2.47 | 2.14 | |
100–200 | 2 | 0.50 | 0.44 |
4 | 0.84 | 0.73 | |
6 | 1.18 | 1.02 |
Далее оценена величина относительного линейного удлинения в области термического расширения для двух указанных диапазонов температур под слоем конденсированной фазы при использовании гашения. Результаты приведены в табл. 10.
Таблица 10.
Линейное удлинение при термическом расширении в двух диапазонах температур
ТЗМ-1 | ТЗМ-2 | |||||
---|---|---|---|---|---|---|
δк, мм | δрас, мм | ε, % | δрас, мм | ε, % | ||
50–200°С | 100–200°С | 50–200°С | 100–200°С | |||
2 | 0.30 | 30 | 60 | 0.45 | 50 | 102 |
4 | 0.64 | 36 | 76 | 0.90 | 59 | 115 |
6 | 0.95 | 38.5 | 80.5 | 1.40 | 65 | 137 |
$\bar {\varepsilon }$ | 34.8 | 72.2 | 58 | 118 |
Относительное линейное удлинение для более жесткого ТЗМ-2 оказалось почти в два раза выше, чем для эластичного ТЗМ-1.
Согласно приведенным в [9] данным, в отсчете от точки без видимых изменений структуры (т.е. без термической деструкции) материала плотность изменяется по близкому к линейному закону от 0.5ρ0 до ρ0 на глубине в ~2 мм. В [9] изменение плотности объясняется порообразованием вследствие газификации органической составляющей. Оцененная в данной работе относительная деформация (в предположении, что изменение плотности имеет место в области 200–250°С) возрастает по близкому к линейному закону от 0.1 до ~1.1. Учитывая это, нужно отметить, что при смещении поверхности удаления коксового остатка в область изотермической поверхности с более высокой температурой (выше 200°С) термическое расширение частично включает и расширение из-за порообразования.
Отметим, что механизм термического расширения резиноподобных ТЗМ в области температур ниже температур начала термической деструкции остается невыясненным до настоящего времени. Известно, что при каландровании и вулканизации высокомолекулярных соединений имеет место возникновение дополнительных межмолекулярных связей, а также связей с молекулами наполнителя. При этом структура материала становится более упорядоченной и более плотной. Предполагается, что с повышением температуры и при отсутствии внешней нагрузки (внешнего давления) структура упорядоченности нарушается, разрушаются межмолекулярные связи, возникшие при каландровании, в том числе с молекулами наполнителя. Расположение длинных цепочек молекул становится менее упорядоченным, что и приводит к увеличению расстояний между ними и, следовательно, к уменьшению плотности, т.е. к термическому расширению.
ЗАКЛЮЧЕНИЕ
1. Экспериментально подтверждено, что глубина деструкции по завершении интенсивного прогрева под слоем неподвижной конденсированной фазы слабо отличается от достигаемой в открытом потоке. Несколько более низкие значения деструкции под конденсатом могут быть связаны как с теплоизолирующим эффектом этого слоя, так и с механизмом более интенсивного разрушения образца с поверхности прогрева при обтекании потоком без осаждения конденсированной фазы.
2. Наличие конденсата в рабочей камере экспериментальной установки приводит к значительному увеличению как глубины дополнительного коксования образцов в период остывания установки, так и толщины термического расширения в области прогретого, но не прококсованного слоя материала.
3. Зависимость удельного термического расширения от температуры для каждого ТЗМ является индивидуальной характеристикой.
4. Дополнительное коксование и термическое расширение ТЗП необходимо учитывать при анализе результатов дефектации после огневых испытаний материалов теплозащиты: имеет место значительное изменение толщин не подвергнутого термодеструкции образца, достигнутых на момент окончания интенсивного прогрева.
Список литературы
Губертов А.М., Миронов В.В., Волкова Л.И. и др. Газодинамические и теплофизические процессы в ракетных двигателях твердого топлива / Под ред. Коротеева А.С. М.: Машиностроение, 2004. 512 с.
Ho Wai K., Koo Joseph H., Ezekoye Ofodike A. Thermoplastic Polyurethane Elastomer Nanocomposites: Morphology, Thermophysical, and Flammability Properties // J. Nanomater. 2010. V. 2010. http://dx.doi.org/https://doi.org/10.1155/ 2010/583234
Ahmed A.F., Hoa S.V. Thermal Insulation by Heat Resistant Polymers for Solid Rocket Motor Insulation // J. Compos. Mater. 2012. V. 46. № 13. P. 1544.
Sangita S., Guchhait P.K., Singha N.K., Chaki T.K. EPDM Nanocomposites using Polyimide as Ablator: Morphology and Thermophysical Properties // Amer. J. Macromolecular Sci. 2014. V. 1. № 1. P. 1.
Страхов В.Л., Атаманов Ю.М., Кузьмин И.А., Бакулин В.Н. Математическое моделирование высокотемпературных теплофизических характеристик резиноподобных теплозащитных материалов // ТВТ. 2017. Т. 55. № 4. С. 528.
Полежаев Ю.В., Фролов Г.А. Тепловое разрушение материалов / Под ред. Скорохода В.В. Киев: Изд-во ИПМ НАНУ, 2005. 288 с.
Буланов И.М. Технология ракетных и аэрокосмических конструкций из композиционных материалов. Учеб. / Буланов И.М., Воробей В.В. М.: Изд-во МГТУ им. Н.Э. Баумана, 1998. 512 с.
Гаращенко А.Н., Кузнецов Г.В., Ткачев А.И. Механизм высокотемпературного разрушения резиноподобных теплозащитных материалов в поле массовых сил // ТВТ. 1995. Т. 33. № 3. С. 458.
Помин О.В., Лях Ю.А., Королев В.Г., Бескровный И.Б., Льняной В.Н. Опыт предприятия по гашению внутреннего теплозащитного покрытия ракетных двигателей твердого топлива после окончания работы при проведении стендовых испытаний // Авиационно-космическая техника и технология. 2012. № 9(96). С. 180.
Дополнительные материалы отсутствуют.
Инструменты
Теплофизика высоких температур