Теплофизика высоких температур, 2019, T. 57, № 2, стр. 278-283
Комплексное математическое моделирование теплозащиты из высоконаполненных эластомеров
В. Л. Страхов 1, *, И. А. Кузьмин 1, В. Н. Бакулин 2
1 АО “Центральный научно-исследовательский институт специального машиностроения”,
Московской обл.,
г., Хотьково, Россия
2 Институт прикладной механики РАН,
Москва, Россия
3 Московский авиационный институт (национальный исследовательский университет)
Москва, Россия
* E-mail: strakhovvl@gmail.com
Поступила в редакцию 05.02.2018
После доработки 13.03.2018
Принята к публикации 01.03.2018
Аннотация
На основании анализа и обобщения результатов теоретических и экспериментальных исследований сформулированы математическая и компьютерная модели поведения теплозащиты из высоконаполненных эластомеров. Результаты численных исследований находятся в удовлетворительном согласии с экспериментальными данными.
ВВЕДЕНИЕ
Высоконаполненные эластомеры – резиноподобные теплозащитные материалы (ТЗМ), широко применяются для теплозащиты современных изделий, работающих при высоких температурах [1]. Для обеспечения требуемых технологических и эксплуатационных качеств ТЗМ в состав резиновых смесей вводят порошковые и волокнистые наполнители [2–4].
Необходимые для оценки качества изготовления теплозащиты и расчета требуемых толщин теплозащитного покрытия (ТЗП) теплофизические и физико-механические характеристики ТЗМ зависят от технологических режимов изготовления ТЗП. Поэтому в данной работе предпринята попытка комплексного математического моделирования процесса основной работы теплозащиты с учетом изменения состава, структуры, основных характеристик материала на всех этапах жизненного цикла теплозащиты: от изготовления до основной работы в горячем газовом потоке.
Математическая модель построена на основе общего аппарата теории теплозащиты, разработанного ранее, с доработками, выходящими за пределы того круга научных проблем, на которые была ориентирована теория [5, 6]. При этом использованы результаты экспериментальных и теоретических исследований, выполненных в последующие годы авторами работ [7–12] и др. Составной частью комплексной математической модели функционирования теплозащиты из высоконаполненных эластомеров является математическая модель высокотемпературных теплофизических характеристик резиноподобных ТЗМ [11], дополненная эмпирической зависимостью от степени вулканизации теплофизических характеристик материала [12].
МАТЕМАТИЧЕСКАЯ МОДЕЛЬ
На основе результатов экспериментальных исследований методами дифференциальной сканирующей калориметрии и динамического механического анализа разработана математическая модель процесса вулканизации резиновых смесей с порошковыми и волокнистыми наполнителями и программно-методическое обеспечение для оптимизации технологического режима термообработки теплозащиты.
В состав модели входят уравнение сохранения энергии в объеме изделия, уравнение кинетики процесса вулканизации резиновой смеси и замыкающие соотношения
(1)
$\begin{gathered} с \left( {T,\beta } \right)\rho \left( \beta \right)\frac{{\partial T}}{{\partial t}} = div\left( {\lambda \left( {T,\beta } \right)gradT} \right) + \rho Q{{\mu }_{п }}\frac{{d\beta }}{{dt}}, \\ t = 0,\,\,\,\,T = {{T}_{0}}; \\ - \frac{{d\beta }}{{dt}} = A\exp \left( { - \frac{E}{{RT}}} \right){{\left( {1 - \beta } \right)}^{n}}{{\beta }^{a}},\,\,\,\,t = 0,\,\,\,\,\beta = {{\beta }_{0}}; \\ \lambda \frac{{\partial T}}{{\partial {{n}_{e}}}} = {{\alpha }_{e}}({{T}_{{ce}}} - {{T}_{{we}}}); \\ \lambda \frac{{\partial T}}{{\partial {{n}_{i}}}} = {{\alpha }_{i}}({{T}_{{ci}}} - {{T}_{{wi}}}). \\ \end{gathered} $Здесь Т – температура; t – время; λ, с, ρ – теплопроводность, теплоемкость и плотность материала; Q – теплота, выделяющаяся при вулканизации; ${{\mu }_{n}}$ – массовая доля полимерной части в материале; β – степень вулканизации; А, Е – предэкспонента и энергия активации процесса вулканизации; ne,i – нормаль к поверхности; αe,i – коэффициент конвективной теплоотдачи; индексы: e –наружный, i – внутренний, c – окружающая среда, w – поверхность.
Экспериментальные зависимости теплофизических характеристик ТЗМ от степени вулканизации резиновой смеси [12] представлена в табл. 1. Коэффициенты теплоотдачи от газа к поверхности формы с вулканизуемым ТЗП определены экспериментально применительно к натурному автоклаву, используемому при производстве крупногабаритных изделий. Результаты экспериментальных исследований обобщены в виде критериальных формул
(2)
$\begin{gathered} Nu = C{{\operatorname{Re} }^{n}}{{\Pr }^{m}},\,\,\,\,Nu = {{\alpha d} \mathord{\left/ {\vphantom {{\alpha d} \lambda }} \right. \kern-0em} \lambda },\,\,\,\,\operatorname{Re} = {{\rho wd} \mathord{\left/ {\vphantom {{\rho wd} \mu }} \right. \kern-0em} \mu }, \\ n = 0.8,\,\,\,\,m = 0.37, \\ \end{gathered} $Таблица 1.
Зависимость от степени вулканизации резиновой смеси теплофизических характеристик типичного ТЗМ на основе этиленпропиленового каучука с наполнителем в виде порошка технического углерода
Характеристики | Значения характеристик при степени вулканизации, % | |||
---|---|---|---|---|
60 | 88 | 94 | 97 | |
Плотность, кг/м3 | 1000 ± 0.005 | 1099 ± 0.002 | 1097 ± 0.003 | 1101 ± 0.002 |
Теплоемкость, кДж/(кг К) | 1.70 ± 0.02 | 1.72 ± 0.10 | 1.80 ± 0.08 | 1.90 ± 0.10 |
Теплопроводность, Вт/(м К) | 0.26 ± 0.04 | 0.25 ± 0.02 | 0.28 ± 0.02 | 0.29 ± 0.03 |
Температуропроводность, мм2/с | 0.141 ± 0.005 | 0.135 ± 0.003 | 0.140 ± 0.003 | 0.141 ± 0.005 |
Значения коэффициента С для различных участков поверхности формы, обозначенных соответствующими цифрами на рис. 1, приведены в табл. 2.
Таблица 2.
Значения коэффициента С в формуле (2)
Обогреваемые поверхности формы | Значения коэффициента С для характерных сечений формы в местах установки датчиков (рис. 1) | |||
---|---|---|---|---|
1, 5 | 2, 6 | 4, 8 | 3, 7 | |
Наружная поверхность | 0.078 | 0.074 | 0.028 | 0.025 |
Внутренняя поверхность | 0.028 | 0.038 | 0.060 | 0.062 |
Введение в состав модели эмпирических формул, связывающих основную характеристику качества ТЗМ – относительное удлинение при разрыве со степенью вулканизации и с температурой термообработки, позволило учесть влияние на качество изготовления ТЗП всех этапов его термообработки после вулканизации резиновой смеси в автоклаве:
– термообработку совместно с силовой оболочкой корпуса;
– термообработку при заполнении корпуса и отверждении наполнителя;
– изменения температуры при длительном хранении, транспортировке и эксплуатации корпуса в составе изделия.
Зависимость относительного удлинения при разрыве ε от степени вулканизации типичного ТЗМ на основе этиленпропиленового каучука описывается формулой
Зависимость относительного удлинения ТЗМ при разрыве от температуры (после полной вулканизации):
Обоснование оптимального режима вулканизации резиновых смесей проводится при параметрических расчетах с использованием разработанной математической модели с учетом:
а) инерционности системы нагрева и охлаждения потока азота в автоклаве;
б) тепловой инерционности стальной формы с вулканизуемой резиновой смесью;
в) установленного ограничения по эластичности (предельному удлинению) ТЗМ после всех этапов термообработки.
Последнее ограничение определено на основе моделирования основной работы ТЗП в деформированном состоянии (в зоне соединения металлического фланца с оболочкой корпуса из полимерного композита).
Уточненная математическая модель работы ТЗП в потоке продуктов сгорания разработана на основе математической модели, рассмотренной в работах [7–10], с учетом результатов исследований, приведенных в [11, 12].
Основные положения математической модели заключаются в следующем.
Механизм работы в высокотемпературном газовом потоке разлагающейся при нагреве с поглощением теплоты и выделением газообразных продуктов теплозащиты характеризуется схемой, показанной на рис. 2. Здесь qк, qл – конвективный и лучистый тепловой поток от потока продуктов сгорания к рабочей поверхности ТЗП; $\dot {m}{\text{''}}$ – массовая скорость вдува газов пиролиза в пограничный слой потока продуктов сгорания; ${{\dot {m}}_{y}},$ ${{\dot {m}}_{и }}$ – массовая скорость поверхностного уноса углерода и массовая скорость испарения минерального наполнителя; Qу – теплота испарения углерода; Qи – теплота испарения минерального наполнителя. Под рабочей поверхностью ТЗП образуется пористый обугленный слой, каркас которого в общем случае состоит из пиролитического углерода и перечисленных наполнителей. В результате химического взаимодействия углерода обугленного слоя с активными компонентами продуктов сгорания (O, O2, CO2, H2O, N, N2) происходит химико-механический унос массы теплозащиты. Кроме того, при повышенных температурах возможно испарение: вначале минеральных наполнителей, а затем (при сверхвысоких температурах) и углерода.
Рис. 2.
Схема подповерхностного слоя ТЗП, работающего при высоких температурах газового потока: 1 – углеродный слой, 2 – обугленный слой (кокс), 3 – слой пластичного материала (зона пластичности), 4 – зона термического разложения, 5 – неразложившийся материал покрытия.
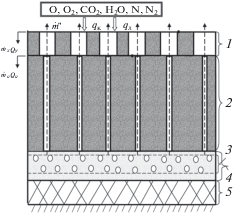
На рис. 3 приведена расчетная схема, где T – температура; T(x, t) – распределение температуры по координате x в момент времени t; p, u, ε – давление, скорость и степень черноты; индексы: f, w, и, кр, нр, кп, нп, о, доп – газовый поток, рабочая поверхность, испарение минерального наполнителя, конец и начало термического разложения, конец и начало пластичности, защищаемая оболочка, допускаемый соответственно. Для расчетной области, представленной в системе координат 0х, начало которой совпадает с начальным положением рабочей поверхности внутреннего ТЗП11, уравнение сохранения энергии в теплозащите принято в виде
Рис. 3.
Расчетная схема к задаче прогрева и уноса массы ТЗП, работающего в высокотемпературном газовом потоке: штрихпунктир – начальное положение рабочей поверхности ТЗП; 1–5 соответствуют обозначениям слоев на рис. 2.
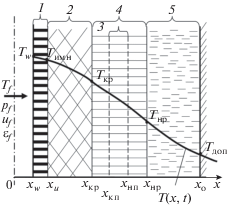
Краевые условия к уравнению (1) включают:
а) начальное условие T(x, 0) = T0= сonst;
б) условие на рабочей поверхности ТЗП (внутренней поверхности корпуса) с температурой Tw(t)
при Tw(t) ≤ Тимн: ${{\dot {m}}_{у }}{{Q}_{у }} = {{\dot {m}}_{х }}{{Q}_{х }} + {{\dot {m}}_{{{\text{и м н }}}}}{{Q}_{{{\text{и м н }}}}},$
при Tw(t) ≥ Тимн: ${{\dot {m}}_{y}}{{Q}_{y}} = {{\dot {m}}_{x}}{{Q}_{x}} + {{\dot {m}}_{{uC}}}{{Q}_{{uC}}};$
в) условие на фронте испарения минеральных наполнителей c температурой Tимн = const (при Tw(t) ≥ Тимн)
г) условия на границе между слоями из различных материалов
д) условие на правой границе расчетной области при справедливости допущения “термически толстой стенки”
е) условие на наружной поверхности корпуса, если допущение о “термически толстой стенке” не проходит:
Выражения для эффективной функции радиационных параметров продуктов сгорания и рабочей поверхности ТЗП имеют вид
Принятые обозначения: I – энтальпия; t – время; х – поперечная координата; ρо – исходное значение объемной плотности материала; λΣ – эффективная (суммарная) теплопроводность; φ – пористость; $\rho {\text{'}}$ – плотность каркаса пористого прогретого слоя ТЗП; $c{\text{'}}$ – теплоемкость каркаса пористого прогретого слоя ТЗП; ср – теплоемкость; χ – степень завершенности процесса термического разложения; K – массовая доля конденсированного остатка в продуктах полного термического разложения;
– массовая скорость фильтрации газообразных продуктов термического разложения; $c_{p}^{{{\text{''}}}}$ – теплоемкость газообразных продуктов термического разложения; QΣ – суммарный тепловой эффект процесса термического разложения; ${{\text{v}}_{y}}$ – скорость уноса массы с рабочей поверхности ТЗП; ${{\varepsilon }_{\text{v}}}$ – относительная деформация вспучивания (плюс) или усадки (минус); Тf, Tw – температуры газовой среды и рабочей поверхности ТЗП; рf – давление в камере сгорания; uf – скорость в ядре потока продуктов сгорания; αf – коэффициент конвективной теплоотдачи от газовой среды к рабочей поверхности ТЗП;
η – коэффициент вдува; Аf – коэффициент лучистого теплообмена между газовой средой и рабочей поверхностью ТЗП;
σ – постоянная Стефана–Больцмана; ${{\dot {m}}_{e}},$ ${{Q}_{e}}$ – массовая скорость и тепловой эффект поверхностного уноса массы обугленного слоя
за счет химического взаимодействия углерода с активными компонентами потока продуктов
сгорания и сублимации компонентов обугленного слоя; qл – лучистый тепловой поток; Тх, Те – температуры наружной поверхности корпуса и окружающей среды вблизи нее; εf – интегральная излучательная способность газовой среды; εw, εх – степень черноты нагреваемой и ненагреваемой (или второй нагреваемой) поверхности;
Аe – коэффициент лучистого теплообмена между ненагреваемой поверхностью и окружающей
средой; αe – коэффициент конвективного теплообмена между ненагреваемой поверхностью и окружающей
средой; xw, xгр – координаты нагреваемой поверхности теплозащиты и границы между слоями из материалов
с различными теплофизическими характеристиками; xнп, xкп – координаты зоны пластичности; xи – координата фронта испарения минерального наполнителя; Тимн – температура на фронте испарения минерального наполнителя; Qимн – теплота испарения минерального наполнителя; Тдоп – допускаемая из условия прочности температура на защищаемой поверхности оболочки
корпуса.
Алгоритм расчета параметров, входящих в граничные условия к уравнению сохранения энергии в теплозащите, рассмотрен в работе [10], методика расчета высокотемпературных теплофизических характеристик резиноподобных ТЗМ с учетом динамики образования пористого обугленного слоя под рабочей поверхностью ТЗП дана в 11].
К числу отличительных особенностей современного варианта модели относятся:
– учет влияния на теплофизические характеристики ТЗМ изменения степени полимеризации связующего на различных этапах термообработки ТЗП;
– описание динамики образования пористого обугленного слоя под рабочей поверхностью ТЗП с учетом усадки при рабочем давлении и вспучивания при спаде давления;
– учет изменения контактного термического сопротивления между частицами неразлагающегося наполнителя и разлагающейся при нагреве полимерной матрицей ТЗМ;
– учет кинетики химического взаимодействия углерода с активными компонентами продуктов сгорания N, N2 (наряду с известными реакциями углерода с O, O2, CO2, H2O);
– учет кинетики сублимации при повышенных температурах основных компонентов обугленного слоя (углерода и окислов SiO2, MgO).
Разработанная математическая модель высокотемпературных теплофизических свойств внутренней теплозащиты выбранного состава и структуры позволяет учитывать в явном виде изменение состава и структуры ТЗМ в процессе термического разложения и при дальнейшем повышении температуры [11]. Ведение в модель зависимости теплофизических характеристик ТЗМ от степени вулканизации (табл. 1) позволяет учитывать влияние режима термообработки на теплозащитную эффективность ТЗМ.
На этой основе разработаны алгоритм и компьютерная программа для моделирования функционирования теплозащиты с учетом изменения состава, структуры, основных характеристик материала на всех этапах жизненного цикла изделия: от изготовления до основной работы в горячем газовом потоке.
РЕЗУЛЬТАТЫ ЧИСЛЕННОГО АНАЛИЗА
Численные исследования выполнены для типичного резиноподобного ТЗМ на основе этиленпропиленового каучука с плотностью в исходном состоянии 1100 кг/м3, наполненного порошком технического углерода.
Плотность наполнителя – 1600 кг/м3. Плотность монолитного (без пор) связующего – 960 кг/м3. Теплопроводность связующего – 0.2 Вт/(м К). Массовая доля неразлагающегося наполнителя, входящего в состав материала покрытия, – 0.28. Плотность кокса связующего в зависимости от температуры изменяется в пределах от 1100 до 1900 кг/м3. Коксовое число материала – 0.34.
Результаты оптимизационных расчетов технологического режима термообработки данного ТЗМ, обеспечивающего максимальное качество теплозащиты, приведены на рис. 4. Основные результаты расчетов высокотемпературных теплофизических характеристик этого материала по методике [10] представлены на рис. 5, 6.
Рис. 4.
Оптимальный температурный режим термообработки в автоклаве типичного резиноподобного ТЗМ на основе этиленпропиленового каучука, наполненного порошком технического углерода: 1 – давление; 2 – температура в автоклаве; 3, 4 – температура снаружи и внутри слоя ТЗМ; 5, 6 – степень вулканизации снаружи и внутри слоя ТЗМ.
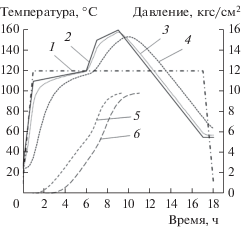
Рис. 5.
Зависимость от температуры теплопроводности кокса (1), теплопроводности матрицы (2) и эффективной теплопроводности ТЗМ (3).
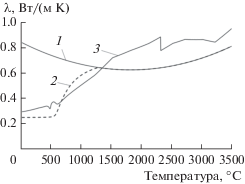
Рис. 6.
Зависимость от температуры теплоемкостей кокса (1), матрицы (2), наполнителя (3) и каркаса (4).
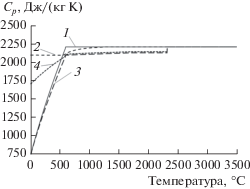
На рис. 5 дана зависимость от температуры теплопроводности матрицы, которая представляет собой связующее, преобразующееся в зоне пиролиза в кокс, а также эффективной теплопроводности ТЗМ. Эффективная теплопроводность материала уменьшается в зоне термического разложения и усадки вследствие изменения состава и структуры материала. Ее дальнейший рост обусловлен ростом теплопроводности наполнителя и увеличением лучистого теплопереноса в порах при повышенных температурах.
Рис. 6 иллюстрирует зависимость от температуры теплоемкости разлагающейся при нагреве матрицы, наполнителя и каркаса, состоящего из переходящей в кокс матрицы и неразлагающегося наполнителя. Резкое падение в зоне пиролиза и последующий рост теплоемкости каркаса ТЗМ обусловлены соответствующим изменением состава материала и теплоемкости его компонентов. Резкий скачок теплоемкости при температуре 2400°С связан с испарением наполнителя, имеющего относительно невысокую теплоемкость.
С целью обоснования возможности практического применения разработанной компьютерной модели были проведены расчеты глубины деструкции натурного ТЗП в условиях камеры сгорания двигателя, работающего при высоких температурах. Их результаты представлены на рис. 7. На этом же рисунке показаны значения глубины деструкции, определенные по результатам дефектации целого ряда корпусов после огневых стендовых испытаний двигателя.
Рис. 7.
Сравнение результатов расчета (сплошная кривая) с экспериментальным распределением средних значений глубины деструкции ТЗП (точки).
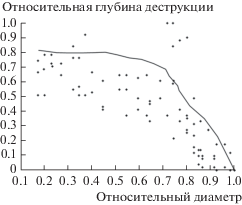
Сопоставление результатов расчетов и экспериментов показывает, что теоретические и экспериментальные значения глубины деструкции удовлетворительно согласуются между собой. На этом основании можно сделать вывод о правомерности допущений, принятых при разработке математической модели и компьютерной программы расчета высокотемпературных теплофизических характеристик резиноподобных ТЗМ.
ЗАКЛЮЧЕНИЕ
На основании анализа и обобщения результатов теоретических и экспериментальных исследований сформулированы математическая и компьютерная модели поведения теплозащиты из высоконаполненных эластомеров. Отличительной особенностью моделей является учет изменения состава, структуры и основных характеристик материала на всех этапах жизненного цикла теплозащиты: от изготовления до основной работы в горячем газовом потоке. Полученные результаты содержат новую информацию, которая не только характеризует индивидуальный материал, но и служит основой для построения и развития моделей целого класса материалов внутренней теплозащиты.
Удовлетворительное согласие результатов теоретического моделирования и опытных данных подтверждает справедливость принципов и гипотез, использованных при построении описанных в данной работе моделей. Полученные результаты свидетельствуют о перспективности развиваемого подхода для описания поведения теплозащиты в условиях интенсивного теплового воздействия.
Список литературы
Газодинамические и теплофизические процессы в ракетных двигателях твердого топлива / Под ред. Коротеева А.С. М.: Машиностроение, 2004. 512 с.
Михайлин Ю.А. Специальные полимерные композиционные материалы. СПб.: Научные основы и технологии, 2008. 660 с.
Ahmed A.F., Hoa S.V. Thermal Insulation by Heat Resistant Polymers for Solid Rocket Motor Insulation // J. Composite Mater. 2012. V. 46. № 13. P. 1544.
Singh Sangita, Guchhait P.K., Singha N.K., Chaki T.K. EPDM Nanocomposites Using Polyimide as Ablator: Morphology and Thermophysical Properties // Am. J. Macromol. Sci. 2014. V. 1. № 1. P. 1.
Полежаев Ю.В., Юревич Ф.Б. Тепловая защита. М.: Энергия, 1976. 392 с.
Панкратов Б.М., Полежаев Ю.В., Рудько А.К. Взаимодействие материалов с газовыми потоками. М.: Машиностроение, 1976. 224 с.
Страхов В.Л., Гаращенко А.Н., Кузнецов Г.В., Рудзинский В.П. Тепломассообмен в тепло- и огнезащите с учетом процессов термического разложения, испарения-конденсации, уноса массы и вспучивания-усадки // Матем. моделирование. 2000. Т. 11. № 5. С. 107.
Страхов В.Л., Гаращенко А.Н., Кузнецов Г.В., Рудзинский В.П. Высокотемпературный тепломассоперенос в слое влагосодержащего огнезащитного материала // ТВТ. 2000. Т. 38. № 6. С. 958.
Страхов В.Л., Кузьмин И.А. Математическое моделирование физико-химических свойств внутренней теплозащиты // Матер. 44 Всерос. симп. по механике и процессам управления. Т. 1. Механика и процессы управления. М.: РАН, 2014. С. 87.
Страхов В.Л., Кульков А.А., Кузьмин И.А. Система компьютерного моделирования работы внутренней теплозащиты // Мат. ХII Всерос. конф., посвященной 70-летию Победы. Т. 1. Новые технологии. М.: РАН, 2015. С. 3.
Страхов В.Л., Атаманов Ю.М., Кузьмин И.А., Бакулин В.Н. Математическое моделирование высокотемпературных теплофизических характеристик резиноподобных теплозащитных материалов // ТВТ. 2017. Т. 55. № 4. С. 528.
Малахо А.П., Шорникова О.Н., Страхов В.Л., Кульков А.А. Экспериментальное исследование комплекса термохимических, теплофизических свойств и кинетики вулканизации резиноподобных теплозащитных материалов // Вопр. оборон. техники. Сер. 15. 2016. Вып. 3–4 (182–183). С. 93.
Дополнительные материалы отсутствуют.
Инструменты
Теплофизика высоких температур