Теплофизика высоких температур, 2019, T. 57, № 5, стр. 702-712
Взаимодействие металлического расплава двухжидкостного кориума с корпусной сталью
А. А. Сулацкий 1, *, В. Б. Хабенский 1, В. И. Альмяшев 1, В. С. Грановский 1, Е. В. Крушинов 1, С. А. Витоль 1, С. Ю. Котова 1, Е. В. Шевченко 1, Е. К. Каляго 1, Б. О. Раба 1, М. Б. Сулацкая 1
1 ФГУП “Научно-исследовательский технологический институт
им. А.П. Александрова”
г. Сосновый Бор, Россия
* E-mail: andrei314@mail.ru
Поступила в редакцию 09.04.2018
После доработки 02.07.2018
Принята к публикации 27.03.2019
Аннотация
Применительно к задаче удержания расплава в корпусе ВВЭР при тяжелой аварии с плавлением активной зоны выполнено экспериментальное исследование взаимодействия металлического расплава двухжидкостного оксидно-металлического кориума с корпусной сталью. В экспериментах воспроизводились условия поступления расплава непосредственно на внутреннюю поверхность корпуса, до того не контактировавшего с расплавом, и на поверхность, исходно покрытую коркой кориума.
ВВЕДЕНИЕ
Удержание расплава в корпусе реактора (IVR – in-vessel retention) является одним из способов локализации расплава активной зоны (АЗ) при тяжелой аварии АЭС с ВВЭР. Данный способ реализован на АЭС Ловииса с ВВЭР-440 [1], предусмотрен в AP-1000 и в ряде других проектов [2–7]. Обоснование эффективности IVR основывается на доказательстве выполнения ряда условий и критериев, основным из которых является непревышение тепловым потоком, отводимым охлаждающей водой от наружной поверхности корпуса реактора, критического значения. Исследованиям кризиса теплообмена и свободноконвективного теплообмена расплава посвящено большое количество в основном экспериментальных работ, и получены соответствующие обобщающие корреляции.
До недавнего времени обоснования IVR базировались на расчетах, выполненных с использованием стационарных моделей с сосредоточенными параметрами, при этом учитывались исключительно тепловые процессы в ванне расплава при его взаимодействии с корпусом (днищем) реактора, для условий полностью сформировавшейся ванны на днище корпуса. Однако прогресс в области численного моделирования пространственной термогидродинамики, а также результаты исследований физико-химических процессов в расплаве кориума сделали возможным и необходимым, с одной стороны, перейти в анализах IVR к более реалистичным моделям, а с другой стороны, дополнить модели термогидродинамики физико-химическими моделями. При этом моделирование выполняется для всего переходного процесса от начала поступления расплава на днище до достижения стабилизированного (квазистабилизированного) состояния.
Наиболее полно методика анализа IVR, основанная на стационарной постановке и применении точечных моделей ванны расплава, изложена в [8]. В соответствии с этой методикой сформированная на днище корпуса ванна расплава состоит из расположенного снизу, в донной части ванны, оксидного расплава UO2 + ZrO2 и расположенного сверху металлического расплава нержавеющей стали внутрикорпусных устройств, который содержит небольшое количество Zr и отделен от оксидного расплава коркой. Температура по всем границам оксидного расплава одинакова, и распределение теплового потока полностью определяется закономерностями свободноконвективного теплообмена в ванне с равномерным остаточным тепловыделением. Тепловой поток, который через корку передается расплаву металла, в соответствии с закономерностями свободноконвективного теплообмена, развивающегося под действием разности температур расплава и окружающих поверхностей, фокусируется на его границе с корпусом и частично отводится излучением на вышерасположенные конструкции. Как показывают многочисленные расчеты, максимальный тепловой поток и, соответственно, минимальный запас до кризиса пузырькового кипения реализуются в указанной зоне “фокусинга”. Именно в этой зоне неизбежно происходит частичное плавление стенки корпуса, причем чем меньше глубина металлического расплава (до определенного предела), тем больше фокусирующий эффект.
Температура на границе взаимодействия металлического расплава и корпуса в [8] определена экспериментально и составляет ~1300°C (температура эвтектики в системе Fe–Zr при заданном составе), т.е. приблизительно на 200°C меньше температуры плавления корпусной стали. В стационарной постановке при прочих одинаковых условиях чем меньше указанная граничная температура, тем меньше температура металлического расплава, меньше тепловой поток, отводимый излучением, больше фокусирующий эффект, и наоборот.
Наличие неокисленного Zr в ванне расплава подтверждается расчетами деградации и плавления АЗ практически для всех рассматриваемых сценариев тяжелой аварии, характер которых определяет долю Zr. В общем случае чем быстрее происходит осушение реактора (аварии с большой течью), тем больше доля неокисленного Zr в ванне расплава. Таким образом, кориум U–Zr–O, входящий в состав ванны расплава, является субокисленным и вместе с расплавом стали образует двухжидкостную систему, находящуюся в куполе расслаивания. Как показали результаты в программе OECD MASCA [9], в данных условиях происходит такое распределение компонентов между оксидным и металлическим расплавами, в результате которого металлический расплав содержит, наряду с компонентами стали, не только Zr, но также U и небольшое количество кислорода, а оксидный расплав – небольшое количество компонентов стали. При этом в зависимости от характеристик системы (степень окисленности, уран-циркониевое отношение, массовая доля стали) металлический расплав может занимать как донное, так и поверхностное положение.
В результате анализа двухжидкостной системы в куполе расслаивания показано [10], что по всем охлаждаемым границам ванны (обеих расслоенных жидкостей) температура одинакова и равна температуре монотектики. Это происходит в результате формирования на границе между жидкостью и поверхностью теплоотвода корки. Температура на поверхности корки, контактирующей с жидкостью, по условиям термодинамического равновесия должна быть равна температуре ликвидуса (для двухжидкостной системы в куполе расслаивания – температуре монотектики). Применительно к реакторным условиям для системы U–Zr–Fe–O эта температура ≈2300°C, и при стационарном подходе к анализу IVR именно такую температуру логично задавать в качестве граничной для поверхности интерфейса металлического расплава с корпусом реактора. Очевидно, что при такой температуре радикально облегчились бы условия IVR вследствие значительного увеличения доли тепла, отводимого излучением от поверхности металлического расплава, и, соответственно, уменьшения фокусирующего эффекта.
Рассматривая возможность реализации описанной ситуации, прежде всего следует отметить, что с точки зрения обеспечения необходимой для соблюдения теплового баланса толщины оксидной корки на поверхности интерфейса между металлическим расплавом и корпусом реактора запас кислорода в ванне (тем более включая ее оксидную часть), по сравнению с требуемым для образования корки, практически бесконечен. Однако неясным является вопрос о возможности образования оксидной корки в реальном, нестационарном процессе при “выходе” металлического расплава на холодную стенку корпуса. Именно так, в отличие от стационарного подхода, моделируются современными кодами процессы формирования ванны расплава на днище как охлаждаемого, так и неохлаждаемого корпуса реактора. С одной стороны, наличие кислорода в расплаве должно приводить к первичной кристаллизации на поверхности охлаждения тугоплавких оксидов U и Zr. С другой стороны, на этот процесс должна влиять инерционность транспорта кислорода, не поддающаяся расчетной оценке. Следует учесть, что транспорт кислорода из объема расплава конкурирует с тепловым процессом прогрева и возможного плавления поверхностного слоя металла корпуса, который может оказаться менее инерционным, чем транспорт кислорода.
Не менее актуальным, чем выход металлического расплава на “чистую” поверхность корпуса, является выход металлического расплава на поверхность, ранее взаимодействовавшую с оксидным расплавом (в результате инверсии оксидного и металлического расплавов) и вследствие этого исходно покрытую коркой. В этом случае неясно, сохраняется ли корка при взаимодействии с металлическим расплавом, поскольку ее толщина, температура и состав отличаются от аналогичных параметров корки, которая гипотетически может образоваться при поступлении металлического расплава на “чистую” стенку корпуса. Сохранение корки в рассматриваемых условиях обеспечит существенное уменьшение подводимого к корпусу теплового потока, благодаря ее большому термическому сопротивлению.
Из сказанного выше следует, что сохраняющаяся неопределенность в температуре на границе взаимодействия корпусной стали с металлической составляющей расплава кориума ограничивает возможности адекватного расчетного моделирования рассматриваемых процессов IVR.
В настоящей работе изложены результаты экспериментального исследования взаимодействия металлической составляющей расплава кориума как с поверхностью корпусной стали, исходно не контактировавшей с расплавом, так и с поверхностью, ранее бывшей в контакте с оксидной составляющей расплава кориума. Обсуждаются экспериментальные результаты применительно к анализу IVR.
ЭКСПЕРИМЕНТАЛЬНАЯ УСТАНОВКА И ОБРАЗЦЫ КОРПУСНОЙ СТАЛИ
Для корректного моделирования условий поступления металлического расплава кориума на поверхность корпуса необходимо выдержать соотношение площади контакта и объема металлического расплава, который, если не рассматривать оксидный расплав, является непосредственным источником кислорода, затрачиваемого на возможное образование оксидной корки на интерфейсе металлического расплава и стали корпуса.
Форму слоя металла при его верхнем положении в ванне расплава внутри корпуса реактора в первом приближении можно считать цилиндрической с диаметром D, равным внутреннему диаметру корпуса реактора, и высотой H. Тогда площадь контакта этого слоя с корпусной сталью (боковая поверхность цилиндра) и объем металлического слоя соответственно равны $S = \pi DH$ и $V = {{\pi {{D}^{2}}H} \mathord{\left/ {\vphantom {{\pi {{D}^{2}}H} 4}} \right. \kern-0em} 4}.$
Тогда искомое соотношение при $D \approx 4\;{\text{м}}$ равно $\gamma = {S \mathord{\left/ {\vphantom {S V}} \right. \kern-0em} V} = {4 \mathord{\left/ {\vphantom {4 D}} \right. \kern-0em} D} = 1\;{{{\text{м}}}^{{ - 1}}}.$
Учитывая, что внутренний диаметр тигля d, используемого в экспериментах данной работы, составляет 7 × 10–2 м, а толщина слоя металлического расплава h предполагается равной приблизительно $3 \times {{10}^{{ - 2}}}$ м, получим площадь контакта корпусной стали с металлическим расплавом s, соответствующую
Принимая в качестве контактной поверхности торцевую поверхность цилиндрического образца (с противоположной стороны образец охлаждается), можно определить требуемый диаметр образца корпусной стали ${{d}_{s}}{\text{:}}$
Оценим толщину оксидной корки, которая может образоваться на образце. Теплопроводность корки ${{\lambda }_{{{\text{ox}}}}} \approx 2\,\,{{{\text{Вт}}} \mathord{\left/ {\vphantom {{{\text{Вт}}} {\left( {{\text{м К}}} \right)}}} \right. \kern-0em} {\left( {{\text{м К}}} \right)}},$ температура на внешней поверхности оксидной корки – монотектическая температура ${{T}_{{{\text{mon}}}}} \approx 2300^\circ {\text{C}}{\text{.}}$ Примем температуру на поверхности стали равной 800°C, а величину характерного теплового потока (q) оценим в ∼106 Вт/м2. Тогда толщина корки составляет
При допущении, что в состав корки входят диоксиды U и Zr, массовая доля кислорода в корке составит приблизительно 15%. Тогда масса кислорода в корке
Оценим теперь запас кислорода в металлическом расплаве в ходе эксперимента. Массовая доля кислорода в металлическом расплаве по минимальной оценке составляет 0.24–0.30 мас. %. При плотности металлического расплава ρmet ≈ $ \approx 7000\;{{{\text{кг}}} \mathord{\left/ {\vphantom {{{\text{кг}}} {{{{\text{м}}}^{3}}}}} \right. \kern-0em} {{{{\text{м}}}^{3}}}}$ его масса будет соответствовать
Тогда масса кислорода в металлическом расплаве составит
Малая величина диаметра образца по сравнению с диаметром тигля, в котором производится плавление кориума, приводит к необходимости реализации “реверсивной” схемы эксперимента: вместо поступления расплава на поверхность стального образца – погружение образца в расплав.
Для получения двухжидкостного расплава кориума была применена технология индукционной плавки в холодном тигле.
В ходе предварительных исследований (AP1–АР4) была отработана методика проведения экспериментов и выбрана конструкция погружаемого образца. Схемы рабочей ячейки экспериментальной установки и общий вид погружаемого в расплав образца, изготовленного из корпусной стали 15Х2НМФА (Fe – 93.55–96.00, Cr – 1.80–2.30, Ni – 1.00–1.50, Si – 0.17–0.37, прочее – 0.53–1.58 мас. %), представлены на рис. 1, 2 соответственно. Образец корпусной стали вводился в расплав через водоохлаждаемую шахту пирометра (8 на рис. 1), через которую на стадии наплавления ванны расплава производились пирометрирование, видеорегистрация процесса плавки, подача аргона, а также загрузка стали в тигель. Образец представлял собой цилиндр (рис. 2а), на дальнем от расплава конце которого в коническом расширении было организовано водяное охлаждение (на рис. 2 видны подводящая и отводящая воду трубки). Предусмотрена изоляция боковой поверхности цилиндра от теплового излучения с поверхности расплава с помощью кольцевых тепловых экранов (рис. 2б). Кроме того, осуществлено термометрирование образца посредством термопар (тип K), размещенных в каналах, параллельных оси образца (рис. 2а). Такая схема проведения экспериментов с погружаемым в расплав металла образцом корпусной стали реализована в экспериментах AP5 и AP6.
Рис. 1.
Схема рабочей ячейки экспериментальной установки для погружаемых образцов корпусной стали: 1 – секции тигля, 2 – кварцевая обечайка, 3 – донный многосекционный водоохлаждаемый калориметр, 4 – индуктор, 5 – гарнисаж, 6 – расплав оксидно-металлического кориума (металл – сверху, оксиды – снизу), 7 – внутренний объем тигля, 8 – водоохлаждаемая шахта пирометра, 9 – водоохлаждаемая крышка печи, 10 – кварцевое окно в шахте пирометра, 11 – видеокамера, 12 – пирометр.
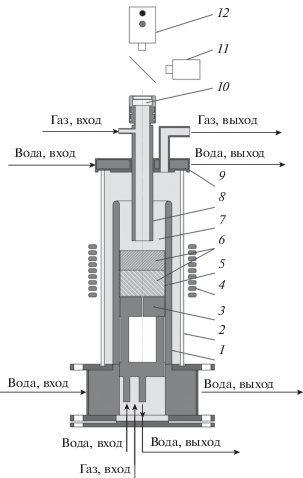
Рис. 2.
Погружаемый образец корпусной стали: (а) – сечение, вид сверху и схема размещения термопар; (б) – образец в сборе.
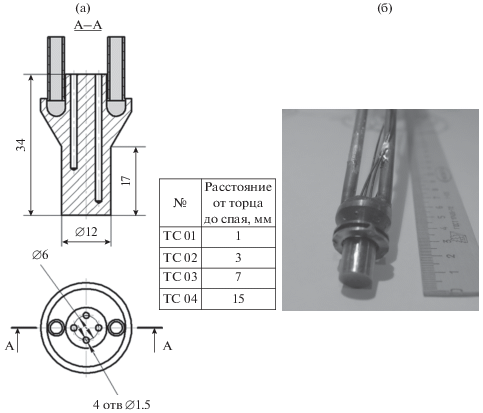
Для исследования взаимодействия металлического расплава двухжидкостной ванны с корпусной сталью, уже взаимодействовавшей с оксидным расплавом, использована методика с донным расположением образца (эксперимент AP7). Схема рабочей ячейки экспериментальной установки для этих условий показана на рис. 3. Донный образец корпусной стали 15Х2НМФА представлял собой цилиндр с диаметром и высотой, равными 70 мм, имеющий донное охлаждение. Боковая поверхность образца корпусной стали была теплоизолирована с помощью порошка ZrO2. На рис. 4 показана схема термометрирования образца корпусной стали термопарами типа K.
Рис. 3.
Схема рабочей ячейки экспериментальной установки с донным положением образца корпусной стали: 1 – образец корпусной стали, 2 – секции тигля, 3 – кварцевая обечайка, 4 – индуктор, 5 – гарнисаж, 6 – расплав (металл – снизу, оксиды – сверху), 7 – водоохлаждаемый электромагнитный экран, 8 – водоохлаждаемая шахта пирометра, 9 – водоохлаждаемая крышка, 10 – кварцевое окно в шахте пирометра, 11 – видеокамера, 12 – пирометр.
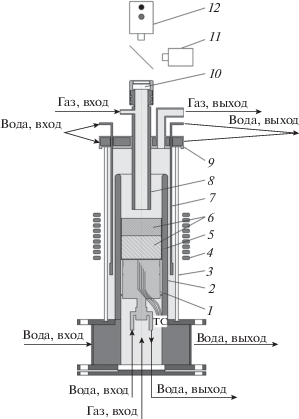
ПРОЦЕДУРЫ ПРОВЕДЕННЫХ ЭКСПЕРИМЕНТОВ
Спецификация проведенных экспериментов была следующей:
– индекс окисленности кориума, обозначающий долю окисленного циркония от его общего количества, для AР5 и AP7 – 0.27 (в общепринятых обозначениях C-27), для AP6 – 0.86 (C-86);
– атомное соотношение ${{\text{U}} \mathord{\left/ {\vphantom {{\text{U}} {{\text{Zr}}}}} \right. \kern-0em} {{\text{Zr}}}} = 1.06;$
– атмосфера над расплавом – сухой аргон высокой чистоты.
Состав загружаемой в тигель шихты представлен в табл. 1. При заданных массовых соотношениях оксидного расплава и вводимой стали в экспериментах AP5 и AP6 металлофаза занимает верхнее положение в ванне расплава, а в эксперименте AP7 – нижнее, донное положение. В качестве металлической составляющей загрузки тигля использовалась нержавеющая сталь 12Х18Н10Т (Fe ≈ 67, Cr – 17–19, Ni – 9–10, Ti – 0.4–1.0, Si до 0.8, Cu до 0.3, Mn до 0.2, C до 0.12, P до 0.035, S до 0.02 мас. %).
Таблица 1.
Составы загрузки тигля для экспериментов AP5–АР7
Эксперимент | AP5 | AP6 | AP7 | |||
---|---|---|---|---|---|---|
Компонент | содержание, мас. % | масса, г | содержание, мас. % | масса, г | содержание, мас. % | масса, г |
UO2 | 48.2 | 976.5 | 49.4 | 814.2 | 66.7 | 1334.4 |
ZrO2 | 5.6 | 113.6 | 18.3 | 301.1 | 7.8 | 155.2 |
Zr | 11.2 | 227.2 | 2.2 | 36.0 | 15.5 | 310.5 |
Шихта без стали | 65.0 | 1317.3 | 69.9 | 1151.3 | 90.0 | 1800.1 |
Сталь марки 12Х18Н10Т | 35.0 | 709.3 | 30.1 | 495.8 | 10.0 | 200.0 |
Полная загрузка | 100.0 | 2026.6 | 100.0 | 1647.1 | 100.0 | 2000.1 |
Доля стали в системе | 0.35 | 0.30 | 0.10 |
В экспериментах AP5 и AP6 после загрузки печи шихтой для удаления сорбированного в порошках воздуха и создания инертной атмосферы печь продувалась аргоном в течение 10 мин с расходом 5 л/мин. После этого включался ВЧ-нагрев, увеличивался расход газа на печь до 10 л/мин и проводилось наплавление ванны расплава. После гомогенизации оксидной ванны расплава и отбора проб расплава на поверхность ванны через шахту пирометра подавалась нержавеющая сталь 12Х18Н10Т (общей массой 709.3 г в эксперименте AP5 и 495.8 г – в AP6) в виде прутков (∅ ≈ 19 мм, длина ≈65 мм) несколькими порциями. Перед вводом первой порции стали температура поверхности расплава составляла приблизительно 2400°C и 2530°C в экспериментах AP5 и AP6 соответственно. После ввода каждой порции стали наблюдалось ее плавление. В случае образования на поверхности расплава оксидной корки она была расплавлена путем увеличения вводимой в расплав мощности и/или перемещения тигля относительно индуктора. После ввода последней порции стали для обеспечения последующего погружения образцов на заданную глубину определялись высотное положение поверхности ванны расплава и ее глубина.
В занимающий верхнее положение металлический расплав на глубину 5 мм вводились образцы корпусной стали № 1 (эксперимент AP5) и № 3 (AP6). Температура поверхности расплава в обоих экспериментах при этом составляла 2620°C. Сразу же после погружения образца он извлекался из расплава. Показания термопар в образцах № 1 и № 3 после погружения в металлический расплав представлены на рис. 5а и 5б соответственно. После извлечения образцов в обоих экспериментах с помощью вольфрамового щупа производился отбор проб расплава.
Рис. 5.
Температурное состояние образцов № 1 (эксперимент AP5) (а) и № 3 (AP6) (б) по данным термопар: 1 – ТС1, 2 – ТС2, 3 – ТС3, 4 – ТС4.
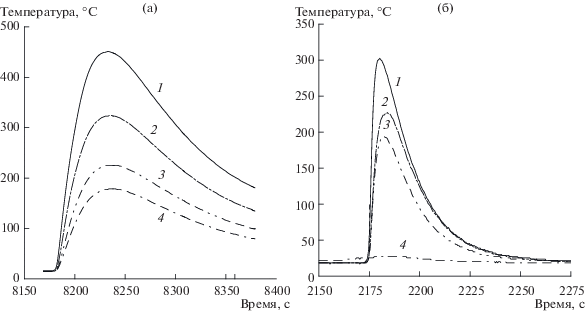
В эксперименте AP5 после извлечения образца № 1 с помощью массивной металлической шуровки удалялась образовавшаяся на поверхности металлического расплава оксидная корочка, повторно измерялись расстояние до поверхности расплава и глубина ванны. После всех проведенных процедур, включая изменение вводимой в расплав мощности, температура его поверхности составила ∼2000°C. Далее в расплав был введен погружаемый образец № 2, и ВЧ-нагрев был сразу же отключен. Заглубление образца в расплав составило 4 мм. Показания термопар в образце № 2 после погружения в металлический расплав представлены на рис. 6. Пунктиром отмечены показания термопар после их контакта с расплавом и образования новых спаев.
После выключения ВЧ-нагрева в эксперименте AP5 была произведена студка слитка с погруженным стальным образцом в инертной атмосфере аргона.
В эксперименте AP6 после извлечения из расплава образца № 3 и отбора пробы расплава был произведен экспресс-анализ пробы металла на рентгеновском спектрометре СПЕКТРОСКАН МАКС-GV. Анализ показал, что содержание урана и циркония в металлическом расплаве составляет всего 3.0 и 2.3 мас. % соответственно. Такие маленькие величины обусловлены высокой степенью окисленности исходного оксидного расплава в совокупности с большой долей введенной стали. Поскольку содержание кислорода в металле коррелирует с содержанием U и Zr, то оно также незначительно и заведомо недостаточно для образования оксидной корки. Поэтому введение в расплав металла очередного образца было признано нецелесообразным и эксперимент прекращен. После отключения ВЧ-нагрева студка слитка проводилась в атмосфере аргона.
Поскольку в эксперименте AP7 применялась методика донного образца корпусной стали, процедура его проведения заметно отличалась от процедур предыдущих экспериментов. Перед началом эксперимента в течение 10 мин с расходом 10 л/мин печь продувалась аргоном с загруженной шихтой. Далее проводились наплавление и гомогенизация ванны расплава. Изменением режима генератора и перемещением водоохлаждаемого экрана стабилизировалась температура образца на основании показаний расположенных в образце наиболее близко к поверхности термопар: ТС-01 – 1450°C и ТС-02 – 1470°C. Далее приблизительно на 3650-й с на поверхность ванны расплава порционно вводилась нержавеющая сталь 12Х18Н10Т. Ввод стали сопровождался падением температуры расплава и образца. По завершении на ∼3760 с ввода стали поверхность расплава покрылась коркой. Для повышения температуры верхнего торца образца два раза перемещался электромагнитный экран вниз (этапами по 5 мм) и увеличивалась мощность генератора. После того как на поверхности образца температура достигла ∼1400°C, в течение ∼15 мин поддерживалось стабильное температурное состояние образца. По истечении указанного времени ВЧ-нагрев был отключен. Студка слитка с образцом производилась в атмосфере аргона.
На рис. 7 представлены показания термопар TC01–ТС07, размещенных на радиусе 10 мм от оси образца. Термопары в легенде упорядочены по степени удаления их от горячей (верхней) поверхности образца. Температура поверхности оксидного расплава (поверхностной оксидной корки) после ввода в расплав нержавеющей стали и инверсии слоев расплава до выключения ВЧ-нагрева, согласно показаниям пирометра, находилась в пределах (2200 ± 100)°C.
РЕЗУЛЬТАТЫ ЭКСПЕРИМЕНТОВ И ПОСТ-ТЕСТ АНАЛИЗОВ
Эксперименты AP5 и AP6. Слитки кориума извлекались из тигля. Слиток эксперимента AP5 был извлечен вместе с “вмороженным” в него образцом № 2 корпусной стали и расколот. Основная часть металла располагалась в верхней части оксидно-металлического слитка (рис. 8). Размеры металлических слитков составили: высота ≈50 мм, диаметр – 50–52 мм (AP5); высота – 43–48 мм, диаметр ≈48 мм (AP6). Нижние части образцов № 1 (AP5 и AP6) и № 2 (AP5) были распилены вдоль оси, и из распилов приготовлены темплеты для проведения SEM/EDX-анализа. На рис. 9а и 9б показаны фотографии осевых сечений образцов № 1 и № 2 (с верхней частью слитка) из эксперимента AP5. Кривизна поверхности металлического слитка обусловлена образованием кольцевой усадочной раковины в процессе студки. На рис. 9в показан образец № 3 эксперимента AP6 после извлечения из расплава.
Рис. 8.
Слиток эксперимента AP5: (a) – после извлечения из тигля (вид сверху), (б) – металлическая часть слитка, (в) – после удаления металлических закраин слитка.
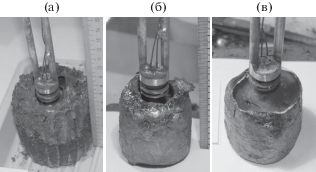
Рис. 9.
Вид погружаемых образцов корпусной стали после экспериментов: (a) – сечение образца № 1 (AP5), (б) – сечение образца № 2 (AP5), (в) – вид образца № 3 (AP6).
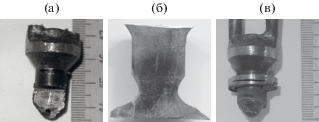
Выполнены рентгеновский спектрофлуоресцентный анализ (РСФА) и SEM/EDX-анализ продуктов плавки экспериментов AP5 и AP6, в том числе погружаемых образцов, оксидной и металлической частей слитков. Результаты анализов, обобщенные по разным исследованным участкам/областям сечений образцов металлических продуктов плавок, приведены в табл. 2. Отметим, что образцы № 1 (AP5) и № 3 (AP6), погружавшиеся в расплав на очень ограниченное время, были существенно оплавлены (рис. 9а), а на их поверхностях, взаимодействовавших с металлическим расплавом, с помощью SEM/EDX-анализа выявлена узкая переходная зона состава, промежуточного между составами корпусной стали и металлического расплава. Толщины этих переходных зон составили 400–500 мкм и 200–300 мкм в экспериментах AP5 и AP6 соответственно. На осевом сечении образца № 2 (AP5), оставленного в расплаве и охлажденного вместе с ним, также наблюдается переходная зона. Толщина этой зоны, естественно, заметно больше, чем в случае образцов, извлеченных из расплава, а именно 5–7 мм, т.е. это фактически вся область “перешейка” между неповрежденной частью образца корпусной стали и металлическим слитком (см. рис. 9б). Средние составы (табл. 2) переходных зон всех трех образцов в обоих экспериментах вне зависимости от времени экспозиции образца в расплаве представляют собой нечто среднее между составом металлического расплава и составом корпусной стали. Видно, что переходные зоны, с одной стороны, обогащены ураном и цирконием, присутствовавшими в металлическом расплаве. С другой стороны, в них наблюдается повышенное содержание основного компонента корпусной стали – железа. Анализ закристаллизованных в переходной зоне фаз показывает, что в ней закристаллизованы те же фазы, что и в металлической составляющей расплава. Таким образом, можно утверждать, что переходная зона представляет собой закристаллизованную смесь металлического расплава и расплавленной стали образца.
Таблица 2.
Составы металлических продуктов плавки в экспериментах AP5 и AP6
Элемент | Содержание, мас. % | |||||
---|---|---|---|---|---|---|
неповрежденная корпусная сталь 15Х2НМФА1) | AP5 | AP6 | ||||
переходная зона2) | металли-ческая часть слитка3) | переходная зона образца № 32) | металли-ческая часть слитка3) | |||
образец № 1 | образец № 2 | |||||
U | – | 13.2 ± 5.2 | 14.0 ± 0.5 | 25.1 ± 0.3 | 3.1 ± 0.4 | 3.0 ± 0.2 |
Zr | – | 7.0 ± 3.0 | 10.4 ± 0.9 | 14.1 ± 0.1 | 1.2 ± 0.3 | 2.3 ± 0.1 |
Fe | 93.55–96.00 | 66.1 ± 11.7 | 63.1 ± 0.6 | 41.5 ± 0.4 | 71.4 ± 2.4 | 68.5 ± 0.7 |
Cr | 1.8–2.3 | 6.9 ± 1.9 | 4.9 ± 0.2 | 8.0 ± 0.1 | 12.4 ± 1.3 | 13.0 ± 0.1 |
Ni | 1.0–1.5 | 5.1 ± 1.5 | 4.5 ± 0.2 | 7.1 ± 0.1 | 10.9 ± 1.9 | 9.5 ± 0.1 |
Si | 0.17–0.37 | 0.4 ± 0.1 | 0.5 ± 0.1 | 0.4 ± 0.1 | 0.6 ± 0.1 | 0.4 ± 0.1 |
Ti | – | 0.2 ± 0.2 | 0.3 ± 0.1 | 0.4 ± 0.1 | – | 0.4 ± 0.1 |
Mo | 0.5–0.7 | 0.1 ± 0.1 | 0.2 ± 0.2 | – | – | – |
C, S, P, Mn, Cu, As, V, Co, Nb | 0.53–1.58 | – | – | 0.3 ± 0.1 | – | – |
O | – | 1.0 ± 1.3 | 2.2 ± 0.4 | 3.1 ± 0.24) | 1.0 ± 0.2 | 2.9 ± 0.14) |
В переходной зоне в случае образца № 2 зафиксировано наличие оксидных глобул с размером ∼5 мкм. Их образование связано с наличием растворенного в металлической фазе кислорода. Однако никакого непрерывного оксидного слоя, отделяющего корпусную сталь от металла слитка, выявлено не было ни в случае образца, оставленного в расплаве, ни тем более в случае образцов, извлеченных из расплава.
Таким образом, результаты анализов подтверждают, что при взаимодействии металлического расплава оксидно-металлической ванны с корпусной сталью, по крайней мере в период до достижения стабилизированного температурного состояния, на поверхности стали образования оксидной корки не происходит. В незначительных количествах оксиды образуются в виде отдельных глобул, не оказывающих влияния на граничную температуру и теплоподвод от металлического расплава к корпусной стали.
Эксперимент AP7. При осмотре извлеченного из тигля слитка обнаружено, что его металлическая часть, как и ожидалось, занимает нижнее положение, т.е. непосредственно над поверхностью образца корпусной стали. Между металлической частью слитка и стальным образцом обнаружена сплошная и достаточно толстая (от 3 до 10 мм) оксидная корка, образовавшаяся на начальном этапе плавки при контакте корпусной стали с оксидным расплавом (до ввода в него нержавеющей стали и ее погружения на дно ванны расплава). Осевое сечение образца корпусной стали и оксидной корки показано на рис. 10 (вышерасположенные металлическая и оксидная части слитка кориума удалены). На рисунке отмечены области оксидной корки и расположенной внутри образца корпусной стали зоны его взаимодействия с расплавом кориума, для которых проведен SEM/EDX-анализ фазового и химического составов (табл. 3). Кроме того, в табл. 3 приведен полученный с помощью РСФА валовой состав металлической и оксидной частей слитка кориума.
Рис. 10.
Корка на поверхности образца корпусной стали (с выделенными областями для SEM/EDX-анализа).
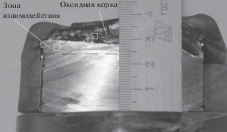
Таблица 3.
Состав основных продуктов плавки эксперимента AP7
Элемент | Содержание, мас. % | |||
---|---|---|---|---|
зона взаимодействия | оксидная корка | металлическая часть слитка | оксидная часть слитка | |
U | 10.2 ± 2.7 | 63.7 ± 7.2 | 37.3 ± 1.6 | 61.1 ± 0.6 |
Zr | 4.1 ± 1.6 | 10.4 ± 2.1 | 24.1 ± 0.4 | 24.2 ± 0.5 |
Fe | 59.2 ± 3.4 | 11.8 ± 6.1 | 26.6 ± 0.8 | 1.3 ± 0.06 |
Cr | 15.5 ± 2.1 | 3.2 ± 2.1 | 6.9 ± 0.3 | 0.5 ± 0.1 |
Ni | 8.4 ± 1.0 | 2.0 ± 1.9 | 3.9 ± 0.1 | 0.25 ± 0.05 |
Si | 0.3 ± 0.1 | – | 0.2 ± 0.0 | <0.1 |
Mn | 1.3 ± 0.9 | – | 0.3 ± 0.0 | <0.1 |
Ti | – | – | 0.2 ± 0.0 | <0.1 |
O | 1.0 ± 0.3 | 8.9 ± 1.3 | 0.1 ± 0.0 | 12.5 ± 0.3 |
Зона взаимодействия, образовавшаяся в поверхностной части образца, аналогична подобным зонам, имевшим место в ранее проведенных экспериментах по исследованию взаимодействия расплава субокисленного кориума с охлаждаемыми стальными образцами [11]. Так же как оксидная и металлическая части слитка, зона взаимодействия сформировалась в результате перераспределения компонентов между расплавом субокисленного кориума и сталью. Данные в табл. 3 показывают, что в оксидной корке содержание железа существенно выше, чем в оксидном слитке, так как через корку происходит указанное перераспределение компонентов. В свою очередь, зона взаимодействия содержит меньшее, чем металлический слиток, но достаточно большое количество урана и циркония.
Для определения температуры на верхнем торце донного образца и плотности теплового потока, подводимого к этой поверхности, выполнен расчет температурного состояния образца в стабилизированном режиме с использованием кода ANSYS. В качестве граничных условий задавались температуры на охлаждаемой водой нижней поверхности образца (1 на рис. 3) и на наружной поверхности боковой теплоизоляции образца. Подводимый тепловой поток варьировался для достижения наилучшего согласования расчетных и измеренных температур. Согласно расчетам, максимальная температура на верхнем торце образца составляет 1400–1450°C. Плотность теплового потока, подводимого к образцу, составила 0.6 МВт/м2.
ОБСУЖДЕНИЕ РЕЗУЛЬТАТОВ ПРИМЕНИТЕЛЬНО К ЗАДАЧЕ УДЕРЖАНИЯ РАСПЛАВА В КОРПУСЕ РЕАКТОРА
Рассмотрим полученные результаты применительно к расчетам удержания расплава в корпусе ВВЭР, выполняемым с использованием кодов, в которых моделируется как термогидродинамика ванны расплава, взаимодействующего с охлаждаемой стенкой корпуса, так и физико-химические процессы в расплаве.
Как показали результаты экспериментов АР5 и АР6, при погружении образца корпусной стали в металлический расплав, содержащий U, Zr и кислород, погруженная часть образца за несколько секунд расплавляется. Это свидетельствует о том, что защитная оксидная корка на поверхности образца не успела образоваться (подтверждается также результатами SEM/EDX-анализа). Поэтому температура на границе образца и расплава равна температуре плавления стали, т.е. ∼1500°C, а не существенно более высокой температуре монотектики (∼2300°C). Нельзя исключить, что при длительной выдержке корка на поверхности образца все же образуется и температура на ее поверхности будет равна температуре монотектики. Однако, учитывая, что максимальная плотность теплового потока и минимальная толщина слоя нерасплавленной корпусной стали достигаются за короткое время (порядка 100 с), процесс возможного образования корки в расчетах температурного состояния корпуса в рассматриваемых условиях не следует принимать во внимание.
Таким образом, при расчетном моделировании формирования ванны расплава на днище корпуса ВВЭР плотность теплового потока, подводимого к внутренней поверхности стенки корпуса при поступлении на нее металлического расплава, следует определять, в отличие от условий поступления оксидного расплава, без учета образования защитной оксидной корки, т.е. принимая температуру поверхности равной температуре плавления стали.
Противоположный вывод следует из результатов эксперимента АР7, в котором воспроизводились условия выхода металлического расплава двухжидкостной ванны на поверхность корпуса, исходно покрытую оксидной коркой. Как показали результаты эксперимента, корка сохранила свою целостность, несмотря на ее проницаемость в процессе перераспределения компонентов между металлическим расплавом и корпусной сталью. Поэтому в рассматриваемых условиях, т.е. после инверсии металлического и оксидного расплавов, в расчетной модели наличие корки необходимо учитывать, что может существенно ограничить плотность подводимого к стенке корпуса теплового потока.
ЗАКЛЮЧЕНИЕ
По результатам проведенного экспериментального исследования взаимодействия металлического расплава оксидно-металлической ванны с охлаждаемой корпусной сталью ВВЭР установлено следующее.
1. Критичным условием с точки зрения максимального теплового потока, подводимого от расплава к корпусу реактора, является поступление металлического расплава непосредственно на внутреннюю поверхность корпуса. При этом вследствие низкой скорости переноса кислорода в расплаве на интерфейсе взаимодействия теплоизолирующая корка тугоплавких оксидов U и Zr образоваться не успевает. Поэтому величина подводимого к внутренней поверхности корпуса теплового потока определяется величиной коэффициента свободноконвективного теплообмена и разностью температур расплава и плавления стали.
2. При поступлении металлического расплава на внутреннюю поверхность корпуса, покрытую коркой тугоплавких оксидов, образовавшейся в предшествующий период контакта поверхности с оксидным расплавом, корка сохраняет целостность и свои теплоизолирующие свойства. Поэтому расчет должен производиться сопряженным моделированием теплопроводности стенки корпуса (с коркой) и свободноконвективного теплообмена с металлическим расплавом.
Список литературы
Kymalainen O., Tuomisto H., Theofanous T.G. In-vessel Retention of Corium at the Loviisa Plant // Nucl. Eng. Des. 1997. V. 169. P. 109.
Theofanous T.G., Lin C., Addition S. et al. In-vessel Coolability and Retention of a Core Melt // Nucl. Eng. Des. 1997. V. 169. P. 1.
Рогов М.Ф., Логвинов С.А., Грановский В.С. и др. Анализ возможности удержания кориума в корпусе реактора ВВЭР-640 при тяжелой аварии с плавлением активной зоны // Теплоэнергетика. 1996. Т. 43. № 11. С. 12.
Fischer M., Levi P. The Severe Accident Control Strategy of the KERENATM BWR // Proc. ICAPP’10. San Diego, USA. 2010. P. 130. Paper 10165.
Oh S.J., Park K.C., Kim H.G. Advanced Design Features of APR 1400 and Realization in Shin Kori Construction Project // Proc. ICAPP’06. Reno, USA. 2006. P. 56. Paper 6172.
Dinh T.N., Tu J.P., Theofanous T.G. Two-phase Natural Circulation Flow in AP-1000 In-vessel Retention-related ULPU-V Facility Experiments // Proc. ICAPP’04. Pittsburgh, USA. 2004. Paper 4242.
Панюшин С.И., Букин Н.В., Быков М.А. и др. Разработка системы удержания расплава и охлаждения корпуса реактора при тяжелых ЗПА для АЭС с РУ ВВЭР-600 и РУ ВВЭР ТОИ // Школа-семинар ИБРАЭ РАН. М., 2011.
Theofanous T.G., Liu C., Additon S. et al. In-vessel Coolability and Retention of a Core Melt. DOE/ID-10460. 1996.
Asmolov V.G., Bechta S.V., Krushinov E.V. et al. Molten Corium Stratification and Component Partitioning // MASCA 2 Seminar. Cadarache, France. 11–12 Oct. 2007.
Seiler J.M., Fouquet A., Froment K., Defort F. Theoretical Analysis for Corium Pool with Miscibility Gap // Nucl. Technol. 2003. V. 141. P. 233.
Bechta S.V., Khabensky V.B., Granovsky V.S. et al. New Experimental Results on the Interaction of Molten Corium with Reactor Vessel Steel // Proc. ICAPP’04. Pittsburgh, PA, USA. 2004. Paper 4114.
Дополнительные материалы отсутствуют.
Инструменты
Теплофизика высоких температур