Теоретические основы химической технологии, 2019, T. 53, № 3, стр. 290-301
Оценка характеристик конверсии продуктов газификации органического топлива в синтез-газ методом парциального окисления
С. В. Глазов *
Институт проблем химической физики РАН
Черноголовка, Россия
* E-mail: glazov@icp.ac.ru
Поступила в редакцию 24.01.2018
После доработки 02.04.2018
Принята к публикации 10.04.2018
Аннотация
Оценки характеристик конверсии продуктов газификации твердого органического топлива в бессмольный синтез-газ методом парциального окисления выполнены на основе предложенной ранее стационарной термодинамической модели. Проведены расчеты температуры горения, состава синтез-газа, а также энергетических характеристик для конверсии в синтез-газ продуктов газификации древесины в случае использования кислорода и обогащенного кислородом воздуха. Изучено влияние количества пиролизных смол и их элементного состава на характеристики конверсии.
ВВЕДЕНИЕ
В последние годы резко увеличился интерес к процессам газификации биомассы, которая рассматривается в качестве перспективного возобновляемого источника получения энергии, а также в качестве источника синтез-газа для химической промышленности. Однако из-за высокого содержания пиролизных смол проблема прямого использования продуктов газификации топлив органического происхождения остается нерешенной [1–6]. Различные методы использования синтез-газа допускают присутствие определенного количества смол. Например, для выработки электроэнергии с помощью газовых моторов содержание смол не должно превышать ~100 мг/м3 [1]; еще более строгие требования предъявляются для современных топливных ячеек, особенно с протонообменными мембранами (менее 100 млн–1); а широко известный синтез Фишера–Тропша требует еще меньшего количества пиролизных смол – не более 1 млн–1. И только низкоэффективное сжигание в топке паровых котлов допускает высокое содержание смол, но при соблюдении условия отсутствия их конденсации.
Содержание смол в продуктах газификации может меняться в очень широких пределах и зависит не только от вида сырья, но и от условий, при которых происходит процесс термического воздействия, т.е. от метода газификации [1–5, 7]. Так, например, обращенный процесс газификации в плотном слое характеризуется относительно низким содержанием смол (0.02–2.0 г/м3), а для прямого процесса типично довольно большое их количество (30–200 г/м3). Причем, наши прямые измерения показали еще более высокие значения – до 500 г/м3 [8, 9], что связано с особенностями используемого метода газификации.
Такой широкий диапазон возможного содержания смол пиролиза обусловливает и разнообразие методов борьбы с ними [3, 4]: от простейших механических методов удаления смол (фильтры, центрифуги, скрубберы и т.д.) до термической или каталитической конверсии смол в газ (паровой или окислительной конверсии). Разумеется, для увеличения эффективности можно использовать сочетание вышеперечисленных методов.
Понятно, что при низком содержании смол выбор методов значительно шире. А при высоком содержании смол приходится учитывать не только стоимость и эффективность того или иного метода, но и энергетическую ценность самих пиролизных смол. В частности, при газификации древесины в прямом процессе плотного слоя смол пиролиза так много, что при их удалении энергетическая ценность газа может снизиться вдвое или даже втрое [8, 9]. Такие потери нельзя не учитывать, тем более, сами по себе смолы являются проблемным токсичным отходом, не представляющим высокой ценности с химической точки зрения. Естественно, что в этом случае целесообразно использовать именно методы конверсии пиролизных смол в синтез-газ. Причем каталитическая конверсия при таком количестве смол также будет весьма проблематичной.
Исходя из вышесказанного, весьма актуальным представляется поиск оптимальных методов, которые позволили бы конвертировать низкокачественный продукт-газ с высоким содержанием пиролизных смол в бессмольный синтез-газ, который далее может быть использован как для выработки электрической энергии (например, с помощью газопоршневых двигателей), так и в качестве сырья для синтеза химических продуктов.
Настоящая работа является продолжением исследований процесса некаталитического парциального окисления воздухом продукт-газа с высоким содержанием смол. По нашему мнению, это наиболее простой и очевидный путь преобразования смол в синтез-газ без потери их энергетической ценности.
Предварительные оценки возможности метода парциального окисления для конверсии продукт-газа [10] были сделаны нами с помощью математической модели на основе термодинамического приближения. При достаточно высоких температурах лимитирующим процессом становится поступление реагентов в зону химических реакций. В этом случае химические реакции можно считать быстрыми и вместо кинетических данных использовать условие термодинамического равновесия в продуктах при температуре горения, что практикуется для оценок параметров газификации [11–13]. В работе [10] была представлена математическая модель и выполнены расчеты температуры горения и состава синтез-газа в зависимости от расхода воздуха для процессов конверсии продуктов газификации четырех типов твердого топлива: древесины, торфа, отходов угля и горючих сланцев. Настоящая работа является продолжением этих исследований. Далее, в частности, представлены оценки кислородной конверсии продукт-газа, а также исследовано влияние количества и состава пиролизных смол на характеристики конверсии.
ОПИСАНИЕ МОДЕЛИ
Подробно схема конверсии продукт-газа в бессмольный синтез-газ методом парциального окисления и основные допущения модели описаны в [10]. Будем полагать, что количество пиролизных смол и их элементный состав (C1HxNyOz) известны.
Напомним систему уравнений, описывающих режим конверсии. В нее входят уравнения сохранения элементов в зоне реакции:
(1)
$\begin{gathered} {\text{к и с л о р о д :}}\quad\quad\quad\quad2{{d}_{0}} + {{m}_{0}} + {{w}_{0}} + 2{{o}_{a}} + \hfill \\ \,\,\,\,\,\,\,\,\,\,\,\,\,\,\,\,\,\,\,\,\,\,\, + \,\,z{{t}_{0}} = 2d + m + w, \hfill \\ \end{gathered} $(4)
${\text{а з о т :}}\,\,\,\,\,\,\,\,\,\,\,\,\,\,\,\,2{{n}_{0}} + 2{{\eta }_{n}}{{o}_{a}} + y{{t}_{0}} = 2n.$Закон сохранения энергии может быть записан в виде сохранения суммы полных энтальпий компонентов:
(5)
$\begin{gathered} {{d}_{0}}{{H}_{d}}({{T}_{g}}) + {{m}_{0}}{{H}_{m}}({{T}_{g}}) + {{w}_{0}}{{H}_{w}}({{T}_{g}}) + {{h}_{0}}{{H}_{h}}({{T}_{g}}) + \\ + \,\,{{n}_{0}}{{H}_{n}}({{T}_{g}}) + {{t}_{0}}{{H}_{t}}({{T}_{g}}) + {{n}_{a}}{{H}_{n}}({{T}_{0}}) + {{o}_{a}}{{H}_{o}}({{T}_{0}}) = \\ = d{{H}_{d}}({{T}_{b}}) + m{{H}_{m}}({{T}_{b}}) + w{{H}_{w}}({{T}_{b}}) + \\ + \,\,h{{H}_{h}}({{T}_{b}}) + n{{H}_{n}}({{T}_{b}}), \\ \end{gathered} $(6)
$\kappa = \kappa (T) = \frac{{{{P}_{{{\text{CO}}}}}{{P}_{{{{{\text{H}}}_{{\text{2}}}}{\text{O}}}}}}}{{{{P}_{{{\text{C}}{{{\text{O}}}_{{\text{2}}}}}}}{{P}_{{{{{\text{H}}}_{{\text{2}}}}}}}}} = \frac{{mw}}{{dh}},$Зависимости констант диссоциации от температуры известны с достаточно высокой точностью. Мы использовали значения из справочника [17]. Для энтальпии образования пиролизных смол использовали оценку по формуле Д.И. Менделеева, исходя из их элементного состава [18].
Получение численного решения описанной системы уравнений (1)–(6) не представляет существенных трудностей. Несмотря на то, что искомая температура не может быть выражена в аналитических функциях из уравнений (5) и (6), явное решение, связывающее конечный результат с исходными данными, может быть получено из обратной задачи, в которой заданной считается температура горения, а одно из исходных данных, например, расход воздуха, полагается неизвестной величиной, т.е. можно прямо рассчитать, какой расход воздуха необходимо задать, чтобы обеспечить установление заданной температуры горения. Таким образом, указанное приближение позволяет описать зависимость режимов конверсии от начальных условий без использования данных о детальном кинетическом механизме протекающих реакций.
Границы области применимости модели тоже понятны. С одной стороны, когда расход газа окислителя (воздуха или кислорода) недостаточен для конверсии того количества пиролизных смол, которое присутствует в продукт-газе, расчет становится некорректным. Кроме того, условие достижения равновесия в продуктах может выполняться лишь при достаточно высокой температуре. Точного температурного критерия нет, но мы придерживались мнения, что при температурах ниже 1000 К достоверность результатов расчета становится сомнительной. При малом расходе газа может иметь место сажеобразование, условие которого можно также рассчитать по равновесию:
Но, как правило, выполнение этого условия полностью перекрывается вышеназванным недостаточным расходом газа-окислителя для конверсии пиролизных смол. C другой стороны, мы ограничены полным окислением продукт-газа при избыточном расходе газа-окислителя. Впрочем, это уже малоинтересная область, где конверсия, как таковая, заканчивается.
ВЛИЯНИЕ ДОЛИ КИСЛОРОДА
Как показали предыдущие результаты расчетов по предложенной модели [10], перспективность воздушной конверсии продуктов газификации невысока. Даже идеальные (без теплопотерь) системы не позволят полностью преобразовать химическую энергию пиролизных смол в энергию синтез-газа. Получение синтез-газа с относительно высоким значением отношения R, необходимого для химического синтеза, также затруднительно. Имеет смысл оценить зависимость параметров процесса от содержания кислорода в подаваемом газообразном окислителе, а также возможности кислородной конверсии. С этой целью выполнили серию расчетов с варьированием содержания кислорода в газообразном окислителе, представляющем собой смесь азота с кислородом. В качестве сырья выбрали продукт-газ, соответствующий продуктам газификации древесины [19] (см. табл. 1).
Таблица 1.
Исходные характеристики продуктов газификации древесины, используемые для расчетов
Xd, об. % | Xn, об. % | Xm, об. % | Xh, об. % | W, г/м3 | S, г/м3 | x | y | z |
---|---|---|---|---|---|---|---|---|
17.5 | 61.9 | 17.5 | 3.1 | 210 | 500 | 1.48 | 0.00 | 0.58 |
При расчетах воздушной конверсии продуктов пиролиза древесины было установлено, что оптимальное отношение объема подаваемого воздуха к объему продукт-газа составляет приблизительно 1.4 [10]. В связи с этим отношение объемов воздуха и продукт-газа было зафиксировано именно на этом значении, т.е. в этой серии расчетов полагали, что в конвертор подается 1.4 л газообразного окислителя на каждый литр продукт-газа. Долю кислорода в газообразном окислителе варьировали в широких пределах при фиксированном значении общего расхода окислителя. Понятно, что при заданных параметрах оптимальный режим конверсии должен располагаться близко к значению 21 об. % кислорода (как в воздухе).
Результаты расчетов показывают, что по составу синтез-газа действительно существует некоторый оптимум в районе 21–22 об. % кислорода. Оптимум заключается в максимальном содержании CO при минимальном содержании CO2 (см. рис. 1а). Остальные параметры монотонно ухудшаются при увеличении доли кислорода в окислителе, т.е. снижается содержание водорода и, соответственно, отношение R = [H2]/[CO], характеризующее качество синтез-газа, а также все энергетические характеристики (см. рис. 1б). Для оценки процесса конверсии мы выбрали три энергетические характеристики:
Рис. 1.
Зависимость параметров процесса от содержания кислорода в газообразном окислителе при фиксированном расходе (A = 1.4): (а) – температура и состав синтез-газа (1 – CO; 2 – CO2; 3 – H2, 4 – H2O; 5 – температура); (б) – энергетические характеристики и отношение R = [H2]/[CO] (1 – Eq; 2 – Ew; 3 – ε; 4 – R).
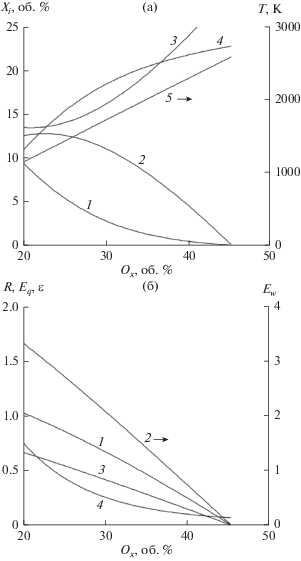
Eq – отношение теплоты сгорания синтез-газа к теплоте сгорания исходного газа. Этот коэффициент характеризует увеличение удельной теплоты сгорания.
Ew – отношение общего теплосодержания газа после и до конверсии. Этот коэффициент учитывает не только теплоту сгорания, но и объем газа, таким образом, характеризует общую энергию, которая может быть получена при сжигании газа.
ε – химический КПД конверсии, который учитывает теплосодержание не только газа, но смол в исходном газе. Этот коэффициент характеризует общую энергетическую эффективность процесса конверсии.
При содержании кислорода 45.2 об. % осуществляется режим полного сгорания (λ = 1), а при содержании кислорода менее 15.5 мы попадаем в область сажеобразования в соответствии с формулой (7).
Вышеописанные зависимости параметров конверсии от содержания кислорода в окислителе рассчитаны при фиксированном значении общего расхода газа. Представляет интерес рассмотрение этих же зависимостей при значении фиксированного стехиометрического коэффициента. Выбор значения коэффициента (λ = 0.463) также был сделан на основании оптимального режима для воздушной конверсии продуктов газификации древесины [10]. Таким образом, в следующей серии расчетов полагали, что количество кислорода, подаваемого в конвертор, остается неизменным, а количество азота варьируется в широких пределах.
Результаты расчетов показали, что зависимости параметров конверсии от содержания кислорода в газообразном окислителе при фиксированном стехиометрическом коэффициенте имеют иной характер (см. рис. 2). В основном, повышение кислорода дает положительный эффект. В частности, увеличивается содержание основных компонентов синтез-газа (водород и CO), в то же время увеличивается и содержание воды и диоксида углерода, что ухудшает качество синтез-газа (см. рис. 2а). Отношение R, являющееся важным параметром синтез-газа, также снижается при увеличении количества кислорода в окислителе (см. рис. 2б), что делает этот газ малопригодным для химического синтеза.
Рис. 2.
Зависимость параметров процесса от содержания кислорода в газообразном окислителе при фиксированном стехиометрическом коэффициенте (λ = = 0.463): (а) – температура конверсии и состав синтез-газа (1 – CO; 2 – CO2; 3 – H2; 4 – H2O; 5 – температура); (б) – энергетические характеристики и отношение [H2]/[CO] (1 – Eq; 2 – Ew; 3 – ε; 4 – R).
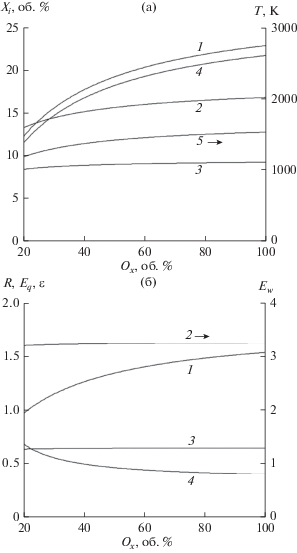
При увеличении количества кислорода в окислителе энергетические показатели конверсии немного улучшаются (см. рис. 2б), но не настолько, чтобы считать этот путь перспективным. По крайней мере, повышение доли кислорода выше 50% становится малоэффективным и почти не сказывается на характеристиках. Это связано с тем, что продукты воздушной газификации биомассы уже разбавлены азотом, и снижение количества азота, подаваемого на конверсию этих продуктов, не может исправить этот недостаток.
КИСЛОРОДНАЯ КОНВЕРСИЯ
Представляет интерес сопоставление результатов расчета воздушной конверсии продуктов газификации [10] с конверсией чистым кислородом. Для этого были выполнены расчеты основных параметров кислородной конверсии продуктов пиролиза древесины. Для уверенного сопоставления результатов в качестве исходного сырья брали тот же состав продуктов, что и при расчете воздушной конверсии (см. табл. 1). Кислородная конверсия не позволит избавиться от азота в продуктах, поскольку большое количество азота исходно содержится в продуктах воздушной газификации биомассы, которые мы выбрали в качестве исходного сырья. Однако можно рассчитывать на значительное снижение количества азота в синтез-газе, а также на увеличение температуры конверсии, от которой зависит и состав образующегося синтез-газа.
На рис. 3 представлены результаты расчетов основных параметров кислородной конверсии (сплошные линии). Для сравнения пунктирными линиями показаны те же параметры для воздушной конверсии. Рис. 3а показывает зависимость содержания основных компонентов синтез-газа от стехиометрического коэффициента λ. Из рисунка видно, что по сравнению с воздушной газификацией наиболее значимым изменением является увеличение содержания CO почти вдвое. Увеличение диоксида углерода не столь большое, в связи с чем появилась область, в которой содержание CO значительно превышает содержание CO2, чего не наблюдалось для воздушной газификации. В то же время увеличение содержания водорода заметно лишь в области малых значений коэффициента λ (менее 0.5). В результате отношение R, характеризующее качество синтез-газа, оказалось ниже, чем при воздушной газификации во всем диапазоне расчетов (см. рис. 3б). При этом температура выше во всем диапазоне, особенно при больших значениях коэффициента λ.
Рис. 3.
Результаты расчетов основных параметров кислородной конверсии продуктов газификации древесины (сплошные линии). Для сравнения пунктирными линиями (нумерация со штрихом) показаны те же параметры для воздушной конверсии. (а) – состав синтез-газа (1 – CO; 2 – CO2; 3 – H2; 4 – H2O); (б) – отношение [H2]/[CO] и температура конверсии (1 – R; 2 – T); (в) – энергетические характеристики (1 – Eq; 2 – Ew; 3 – ε).
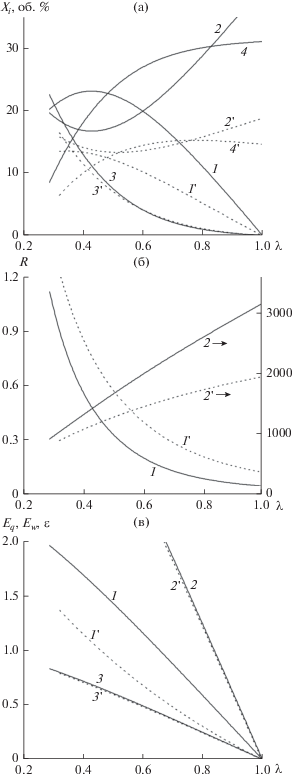
Из энергетических показателей можно отметить существенное увеличение теплоты сгорания газа (см. рис. 3б) по сравнению с воздушной газификацией, связанное в первую очередь со снижением количества азота. Однако, с учетом уменьшения объема, общее теплосодержание синтез-газа, как и энергетическая эффективность конверсии ε, остались такими же, как при воздушной газификации.
Результаты расчетов показывают, что кислородная конверсия продуктов газификации биомассы не дает значительных преимуществ перед воздушной конверсией. В частности, несмотря на снижение количества азота в продуктах, качество синтез-газа остается невысоким из-за недостаточно высокого содержания водорода. Для увеличения содержания водорода можно включить в процесс дополнительные стадии, например, реализующие реакцию водяного сдвига.
Необходимо учитывать, что сопоставление воздушной и кислородной газификации проводили по стехиометрическому коэффициенту λ. При этом в абсолютных единицах расход кислорода в 5 раз меньше расхода воздуха.
ВЛИЯНИЕ КОЛИЧЕСТВА СМОЛ
Как было отмечено выше, процесс окислительной конверсии требует точной регулировки количества подаваемого воздуха, которое рассчитывается на основе предварительных данных о составе продукт-газа. Количество необходимого воздуха в первую очередь определяется количеством пиролизных смол в продукт-газе.
Рассмотрим, как зависят основные характеристики конверсии от количества пиролизных смол. Будем полагать, что состав продукт-газа и состав смол соответствует продукт-газу от древесины (см. табл. 1).
На рис. 4 представлено расчетное содержание основных компонентов синтез-газа после конверсии в зависимости от количества пиролизных смол при фиксированном расходе воздуха для процесса конверсии (A = 1.4 л/л). Из рисунка видно, что чем больше пиролизных смол в исходном газе, тем выше содержание основных компонентов (водорода и CO). Содержание углекислого газа, напротив, снижается с увеличением количества смол. На этом же графике изображено отношение R, характеризующее синтез-газ как сырье для производства химических продуктов. В указанном диапазоне параметров это отношение не превышает значения 0.35, что свидетельствует о низком качестве синтез-газа. Естественно, что при малом количестве смол такой расход воздуха становится избыточным. Поэтому кривые слева обрываются. С другой стороны, при слишком высоком содержании смол модель также становится некорректной из-за недостатка кислорода и неучета сажеобразования. Однако диапазон возможного содержания смол остается довольно широким. Напомним, что при газификации древесины в сверхадиабатическом режиме содержание смол в продукт-газе составляло ~500 г/м3 (см. табл. 1).
Рис. 4.
Состав синтез-газа (1 – CO; 2 – CO2; 3 – H2; 4 – H2O; 5 – R) в зависимости от количества смол (S), присутствующих в исходном продукт-газе, при фиксированной подаче воздуха для процесса конверсии.

На рис. 5 представлена зависимость температуры от количества смол, присутствующих в исходном продукт-газе при том же фиксированном расходе воздуха. Энергетические характеристики процесса конверсии изображены на рис. 6. Представлены те же три характеристики, что и выше (Eq – отношение теплоты сгорания газа после и до конверсии; Ew – отношение общего теплосодержания газа после и до конверсии; ε – химический КПД).
Рис. 5.
Зависимость отношения R (1) и температуры (2) от содержания смол при фиксированной подаче воздуха.
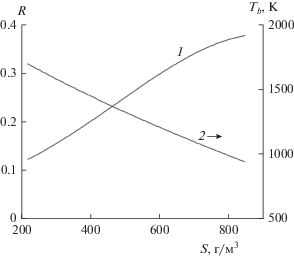
Рис. 6.
Расчетные энергетические характеристики конверсии (1 – Eq; 2 – Ew; 3 – ε) при различном содержании пиролизных смол и фиксированной подаче воздуха.
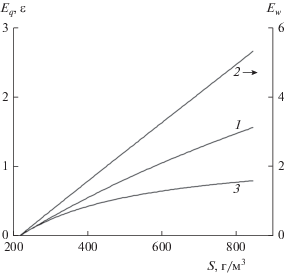
Понятно, что в рамках вышеописанной модели все смолы преобразуются в горючие компоненты, поэтому, чем больше смол в исходном сырье, тем выше энергетическая эффективность. Однако энергетическая целесообразность проведения процесса конверсии наблюдается, только начиная с содержания смол S = 335 г/м3. При меньшем содержании смол процесс конверсии снижает общее теплосодержание газа. Это объясняется тем, что при низком содержании смол выбранный нами фиксированный расход воздуха (A = 1.4 л/л) становится избыточным. Теплота сгорания конвертированного газа сравнивается с теплотой сгорания исходного газа лишь при содержании смол 580 г/м3.
ВЛИЯНИЕ СОСТАВА СМОЛ
Если влияние содержания пиролизных смол в исходном продукт-газе вполне понятно и предсказуемо, то влияние качественного состава смол является более сложной задачей. В состав смол входит огромное количество самых разных углеводородов [20, 21], поэтому характеризовать их можно лишь по усредненным характеристикам. Однако при термодинамическом рассмотрении важен лишь элементный состав и энтальпия образования. Поскольку содержание азота в смолах, как правило, незначительное, мы будем характеризовать состав смолы двумя параметрами, отражающими ее элементный состав – соотношениями водород–углерод и кислород–углерод. Такие характеристики часто используют при изучении керогенов – органических компонентов углей, сланцев, нефтей и др. [22]. Чтобы отобразить на графиках зависимость характеристик конверсии сразу от двух указанных параметров, целесообразно использовать широко известную диаграмму Ван Кревелена [23], на которой будем изображать изолинии конкретной характеристики как изолинии высоты на географических картах.
Будем полагать, что состав продукт-газа и количество смол в нем соответствует продукт-газу от древесины, и подача воздуха для процесса конверсии зафиксирована (1.4 л на литр продукт-газа). На рис. 7–10 представлены диаграммы Ван Кревелена с изолиниями рассчитанных характеристик, в частности, температуры конверсии (рис. 7), состава образующегося синтез-газа (рис. 8 и 9) и некоторые энергетические характеристики процесса конверсии (рис. 10).
Рис. 7.
Изолинии температуры конверсии (1 – 900; 2 – 1000; 3 – 1200; 4 – 1400; 5 – 1600 К) на диаграмме Ван Кревелена для различного состава пиролизных смол.
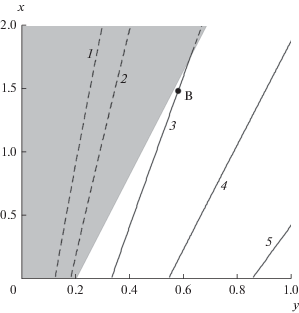
Рис. 8.
Состав синтез-газа. Изолинии на диаграмме Ван Кревелена: (а) – содержание водорода, об. % (1 – 3; 2 – 5; 3 – 7; 4 – 10; 5 – 15), (б) – содержание монооксида углерода, об. % (1 – 5; 2 – 7; 3 – 10; 4 – 15; 5 – 20).
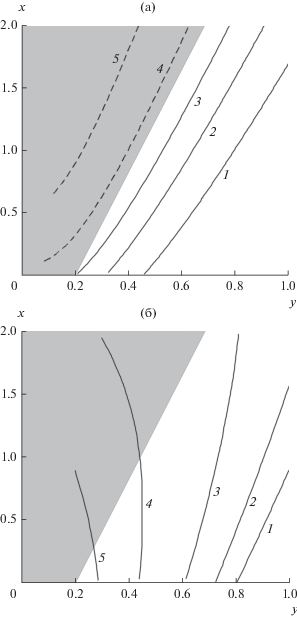
Рис. 9.
Мольное отношение водорода к CO (1 – R = = 0.2; 2 – 0.4; 3 – 0.6; 4 – R = 0.8) для различного состава пиролизных смол.
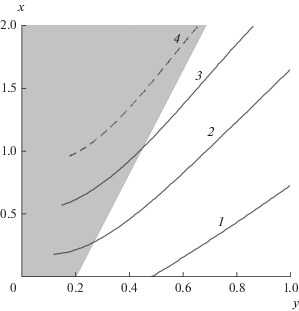
Рис. 10.
Изолинии энергетических характеристик конверсии на диаграмме Ван Кревелена: (а) – отношение теплоты сгорания (1 – Eq = 0.2; 2 – 0.4; 3 – 0.6; 4 – 0.8; 5 – 1.0; 6 – Eq = 1.2); (б) – отношение теплосодержания (1 – Ew = 1.0; 2 – 2.0; 3 – 3.0; 4 – Ew = 4.0); (в) – химический КПД конверсии (1 – ε = 0.2; 2 – 0.3; 3 – 0.4; 4 – 0.5; 5 – 0.6; 6 – ε = 0.7).
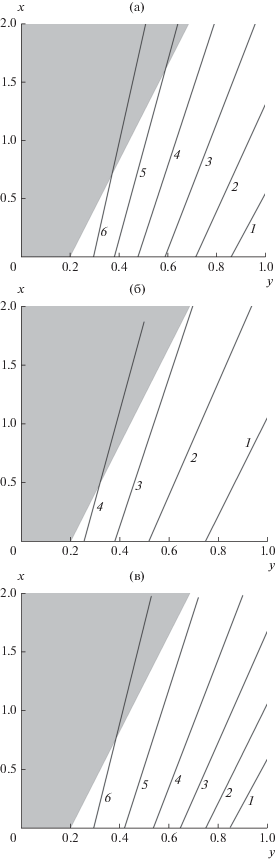
На рисунках закрашенные зоны (слева) соответствуют области, где кислорода недостаточно для конверсии того количества пиролизных смол, которое присутствует в продукт-газе. Поэтому изолинии, рассчитанные для этих областей при зафиксированном значении расхода воздуха, нельзя считать корректными. Эти изолинии всего лишь показывают тенденции соответствующей характеристики. При меньших расходах воздуха закрашенные запретные области будут сдвигаться влево. Область параметров, в которой по термодинамике возможно образование сажи, при вышеуказанных начальных условиях лежит еще левее в кислородонедостаточной области, поэтому не ограничивает область применения модели.
Изолинии температуры показывают, что с увеличением отношения H/C = x температура конверсии снижается, а с увеличением отношения O/C = z – наоборот, возрастает (см. рис. 7). Снижение температуры в данном случае отражает уменьшение потерь энергии на процесс конверсии, т.е. является положительной тенденцией.
Температура конверсии тоже является ограничивающим параметром, поскольку при относительно низких температурах обеспечение условия достижения термодинамического равновесия становится затруднительным. Однако область низких температур почти совпадает с запретной областью нехватки кислорода, и в разрешенном поле диаграммы температуры достаточно высокие (~1000 К и выше). Точка B на рис. 7 характеризует состав исходных пиролизных смол при газификации древесины. Зафиксированный расход воздуха оптимален для конверсии именно продукт-газа от древесины, в котором относительно много пиролизных смол, поэтому точка B расположена вблизи линии недостаточности кислорода, но в разрешенной области.
На рис. 8 представлены расчетные данные по составу продукт газа после процесса конверсии. На графиках изображены изолинии объемного содержания водорода (рис. 8а) и монооксида углерода (рис. 8б). Изолинии состава синтез-газа показывают, что с увеличением отношения x в смолах содержание водорода и СО в синтез-газе возрастают, а увеличение z, т.е. увеличение элементного содержания кислорода в смолах, наоборот, приводит к довольно быстрому снижению содержания этих компонентов в продуктах. Сравнение рис. 8а и 8б показывает, что характер изолиний водорода и СО различен. Вследствие этого элементный состав пиролизных смол существенно влияет на отношение R в синтез-газе. Характер этого влияния демонстрирует рис. 9, на котором изображены изолинии этого параметра. Как видно из рисунка, получение качественного синтез-газа при газификации древесины затруднительно, даже если состав смол окажется более подходящим. Значение отношения R едва превышает 0.6.
Теперь сделаем оценки энергетической эффективности процесса конверсии. Энергетическая ценность синтез-газа определяется как теплотой сгорания газа, так и его количеством. Ясно, что объем газа в процессе конверсии значительно увеличивается, поскольку в конвертор подается воздух, и, кроме того, присутствующие в исходном продукт-газе пиролизные смолы преобразуются в компоненты синтез-газа.
На рис. 10а представлены диаграммы Ван Кревелена с изолиниями отношения теплоты сгорания газа после и до конверсии (Eq), а на рис. 10б – изолинии отношения теплосодержания этих газов (Ew). Изолинии имеют форму прямых. Увеличение содержания кислорода в составе смол значительно снижает теплоту сгорания газа, а увеличение содержания водорода, напротив, несколько повышает теплоту сгорания. Это вполне ожидаемые результаты. Закрашенная область составов смолы также соответствует кислородонедостаточным режимам (для выбранных значений количества смол и расхода воздуха), в которых модель не дает верных результатов.
Из рисунка видно, что существует довольно обширная область, где теплота сгорания образующегося синтез-газа может быть выше теплоты сгорания исходного газа (область левее изолинии, соответствующей единице). Для выбранных значений расчетных параметров отношение теплоты сгорания может быть выше 1.2 (см. рис. 10а). С учетом увеличения количества газа теплосодержание газа в процессе конверсии может возрастать в 4 раза (рис. 10б). При этом химический КПД конверсии ε относительно невысок ~0.7 (см. рис. 10в). В настоящей работе мы ограничились рассмотрением химического КПД. Невысокое значение этой характеристики связано с неизбежным уносом тепла с горячим синтез-газом, которое в данном случае считается потерями. В практическом приложении это тепло может быть использовано, например, для подогрева подаваемого воздуха. C учетом этого КПД реальных процессов конверсии может быть значительно выше.
Относительно надежности и точности выполненных расчетов можно утверждать, что наибольшее отклонение от рассчитанных параметров может быть связано с недостаточно высокой температурой или недостаточным для установления термодинамического равновесия временем пребывания синтез-газа в конверторе. Кроме того, погрешности расчетов могут быть связаны с погрешностью использованной приближенной формулы для расчета теплоты сгорания, которая может давать ошибку в 2–3% [18]. В связи с этим были выполнены оценки погрешности вычислений, связанных с неточностью теплоты сгорания. Оценки показали, что занижение теплоты сгорания смол на 3% величины дает снижение расчетной температуры горения на 0.8–4.4%, уменьшение количества СО в синтез-газе на 0.6–4.2% от расчетной величины и увеличение количества водорода на 4–6%. Максимальные отклонения наблюдаются при минимальных значениях стехиометрического коэффициента (т.е. как раз на оптимальных режимах конверсии), когда ошибка в энтальпии образования выступает на фоне снижающегося общего теплового эффекта конверсии. При этом энергетические параметры процесса меняются не столь значительно. Так, снижение теплоты сгорания газа составляет не более 0.3%, а общий КПД конверсии ε повышается на 2.1–2.3%.
ЗАКЛЮЧЕНИЕ
С помощью предложенной ранее математической модели выполнены расчеты, на основании которых сделаны оценки влияния состава газообразного окислителя на характеристики окислительной конверсии продуктов газификации твердого органического топлива в синтез-газ методом парциального окисления. Показано, что при увеличении количества кислорода в окислителе энергетические показатели конверсии несколько улучшаются, при этом повышение доли кислорода выше 50% становится малоэффективным и почти не влияет на характеристики. Кислородная конверсия продуктов газификации биомассы не дает значительных преимуществ перед воздушной конверсией. В частности, несмотря на значительное снижение количества азота в продуктах кислородной конверсии, получение синтез-газа с относительно высоким значением отношения R, необходимого для химического синтеза, возможно лишь при использовании дополнительной стадии коррекции состава (например, с помощью реакции водяного сдвига).
Выполнены расчеты характеристик конверсии в зависимости от количества пиролизных смол и их элементного состава. Показано, что окислительная конверсия продуктов газификации биомассы может иметь практическое значение, особенно в случае большого количества пиролизных смол в исходных продуктах.
Количество воздуха (или другого окислителя), подаваемого на конверсию, следует рассчитывать, в первую очередь, исходя из количества пиролизных смол в исходных продуктах. Например, при хорошо подобранном количестве воздуха парциальное окисление продуктов газификации древесины может увеличить общее теплосодержание более чем в 2 раза. При этом, как показывают расчеты, значительно увеличить теплоту сгорания газа вряд ли удастся, а все увеличение теплосодержания будет происходить за счет увеличения объема газа.
Элементный состав пиролизных смол также имеет значение, поскольку непосредственно связан с их теплосодержанием. Очевидно, что чем больше водорода и меньше кислорода в составе смол, тем выше энергетические параметры. Однако влияние состава смол на содержание основных компонентов синтез-газа (водорода и монооксида углерода) различно. Количество водорода в продуктах окислительной конверсии остается невысоким, поэтому добиться высокого качества газа, необходимого для химического синтеза (отношение R ≥ 1), без применения дополнительных методов увеличения доли водорода будет затруднительно.
Работа выполнена по теме государственного задания (№ государственной регистрации 01201361842), а также при частичной поддержке Программы фундаментальных исследований Президиума РАН № 31 “Фундаментальные исследования процессов горения и взрыва”.
ОБОЗНАЧЕНИЯ
A | объемное отношение поступающего в конвертор воздуха и продукт-газа |
d, h, m, n, t, w | удельные (на единицу площади сечения конвертора) мольные расходы диоксида углерода, водорода, монооксида углерода, азота, пиролизных смол и водяного пара соответственно, моль/(с м2) |
Eq | отношение теплоты сгорания синтез-газа к теплоте сгорания исходного газа |
Ew | отношение общего теплосодержания синтез-газа к теплосодержанию исходного газа |
Hi = Hi(T) | мольная энтальпия i-го компонента, кДж/моль |
Kc(T) | парциальное давление паров атомарного углерода, Па |
Kd, Kh, Km, Kw | константы диссоциации диоксида углерода, водорода, монооксида углерода и водяного пара соответственно, Па, Па2 |
nа | мольный расход азота, поступающего с окислителем, моль/(с м2) |
Ox | содержание кислорода в газообразном окислителе, % |
oа | мольный расход кислорода, поступающего в конвертор с газообразным окислителем, моль/(с м2) |
P | полное давление в системе, Па |
PCO, ${{P}_{{{\text{C}}{{{\text{O}}}_{2}}}}},$${{P}_{{{{{\text{H}}}_{{\text{2}}}}{\text{O}}}}},$${{P}_{{{{{\text{H}}}_{2}}}}}$ | парциальные давления компонентов газа, Па |
R | мольное отношение водорода к монооксиду углерода в синтез-газе |
S | содержание пиролизных смол в продукт-газе, г/м3 |
T | температура, K |
T0 | температура окружающей среды, K |
Tb | температура горения (конечная температура, установившаяся в системе после завершения конверсии), K |
Tg | температура поступающего в конвертор исходного продукт-газа, K |
W | содержание влаги в продукт-газе, г/м3 |
Xi | объемная доля i-го компонента газа, об. % |
x | отношение H/C в брутто-формуле пиролизных смол |
y | отношение N/C в брутто-формуле пиролизных смол |
z | отношение O/C в брутто-формуле пиролизных смол |
ε | химический КПД конверсии (отношение теплосодержания синтез-газа к общему теплосодержанию исходного газа с учетом смол) |
ηn | мольное отношение азота к кислороду в окислителе |
κ(T) | безразмерная функция равновесия; |
λ | стехиометрический коэффициент (отношение количества поданного газа-окислителя к количеству, необходимому для полного сгорания исходного газа с учетом смол) |
ИНДЕКСЫ
Список литературы
Richardson Y., Blin J., Julbe A. A short overview on purification and conditioning of syngas produced by biomass gasification: Catalytic strategies, process intensification and new concepts // Prog. Energy Combust. Sci. 2012. V. 38. № 6. P. 765.
Shen Y., Yoshikawa K. Recent progresses in catalytic tar elimination during biomass gasification or pyrolysis – A review // Renewable and Sustainable Energy Reviews. 2013. V. 21. P. 371.
Woolcock P.J., Brown R.C. A review of cleaning technologies for biomass-derived syngas // Biomass and Bioenergy. 2013. V. 52. P. 54.
Asadullah M. Biomass gasification gas cleaning for downstream applications: A comparative critical review // Renewable and Sustainable Energy Reviews. 2014. V. 40. P. 118.
Heidenreich S., Foscolo P.U. New concepts in biomass gasification // Progress in Energy and Combustion Science. 2015. V. 46. P. 72.
Sansaniwal S.K., Pal K., Rosen M.A., Tyagi S.K. Recent advances in the development of biomass gasification technology: A comprehensive review // Renewable and Sustainable Energy Reviews. 2017. V. 72. P. 363.
Hasler P., Nussbaumer T. Gas cleaning for IC engine applications from fixed bed biomass gasification // Biomass and Bioenergy. 1999. V. 16. P. 385.
Kislov V.M., Glazov S.V., Chervonnaya N.A., Patronova L.I., Salganskaya M.V., Manelis G.B. Biomass Gasification under Combustion Conditions with Superadiabatic Heating // Solid Fuel Chemistry. V. 42. № 3. P. 135. [Кислов В.М., Глазов С.В., Червонная Н.А., Патронова Л.И., Салганская М.В., Манелис Г.Б. Газификация биомассы в режиме фильтрационного горения со сверхадиабатическим разогревом // Химия твердого топлива. 2008. № 3. С. 9.]
Salganskii E.A., Kislov V.M., Glazov S.V., Zholudev A.F., Manelis G.B. Specific Features of Filtration Combustion of a Pyrolized Solid Fuel // Combustion Explosion and Shock Waves. 2010. V. 46. № 5. P. 528. [Салганский Е.А., Кислов В.М., Глазов С.В., Жолудев А.Ф., Манелис Г.Б. Особенности фильтрационного горения пиролизующегося твердого топлива // Физика горения и взрыва. 2010. Т. 46. № 5. С. 42.]
Глазов С.В. Термодинамическая оценка конверсии в синтез-газ продуктов газификации низкосортных топлив методом неполного окисления // Теорет. основы хим. технологии. 2019. Т. 53. № 1. С. 1.
Higman C., van der Burgt M. Gasification. Amsterdam: Elsevier, 2003.
Shabbar S., Janajreh I. Thermodynamic equilibrium analysis of coal gasification using Gibbs energy minimization method // Energy Conversion and Management. 2013. V. 65. P. 755.
Jarungthammachote S., Dutta A. Equilibrium modeling of gasification: Gibbs free energy minimization approach and its application to spouted bed and spout-fluid bed gasifiers // Energy Conversion and Management. 2008. V. 49. P. 1345.
Polianczyk E.V., Glazov S.V. Model for filtration combustion of carbon: Approximation of a thermodynamically equilibrium composition of combustion products // Combust., Explos., Shock Waves. 2014. V. 50. № 3. P. 251. [Полианчик Е.В., Глазов С.В. Модель горения углерода в фильтрационном режиме в приближении термодинамически равновесного состава продуктов // Физика горения и взрыва. 2014. Т. 50. № 3. С. 9.]
Glazov S.V., Polianczyk E.V. Filtration combustion of carbon in the presence of endothermic oxidizers // Combust., Explos., Shock Waves. 2015. V. 51. № 5. P. 540. [Глазов С.В., Полианчик Е.В. Фильтрационное горение углерода в присутствии эндотермических окислителей // Физика горения и взрыва. 2015. Т. 51. № 5. С. 34.]
Dorofeenko S.O., Polianczyk E.V. Conversion of hydrocarbon gases to synthesis gas in a reversed-flow filtration combustion reactor // Chemical Engineering Journal. 2016. V. 292. P.183.
Термодинамические свойства индивидуальных веществ. Справочное издание в четырех томах / Под ред. Глушко В.П., Гуревич Л.В. 3-е изд. М.: Наука, 1981.
Равич М.Б. Эффективность использования топлива. М.: Наука, 1977.
Salgansky E.A., Kislov V.M., Glazov S.V., Salganskaya M.V. Formation of Liquid Products at the Filtration Combustion of Solid Fuels // J. Combustion. 2016. Article no. 9637082.
Anis S., Zainal Z.A. Tar reduction in biomass producer gas via mechanical, catalytic and thermal methods: A review // Renewable and Sustainable Energy Reviews. 2011. V. 15. № 5. P. 2355.
Wu W.G., Luo Y.H., Chen Y., Su Y., Zhang Y.L., Zhao S.H., Wang Y. Experimental investigation of tar conversion under inert and partial oxidation conditions in a continuous reactor // Energy Fuels. 2011. V. 25. № 6. P. 2721.
Kerogen: Insoluble Organic Matter from Sedimentary Rocks / Ed. Durand B. Paris: Editions Technip, 1980.
Van Krevelen D.W. Graphical-statistical method for the study of structure and reaction processes of coal // Fuel. 1950. V. 29. № 12. P. 269.
Дополнительные материалы отсутствуют.
Инструменты
Теоретические основы химической технологии