Теоретические основы химической технологии, 2019, T. 53, № 5, стр. 517-522
Совершенствование технологической схемы выделения бутан-бутиленовой фракции методом хемосорбции с использованием трубчатого турбулентного аппарата
Ф. Б. Шевляков 1, *, Т. Г. Умергалин 1, О. К. Шурупов 1, В. П. Захаров 2, И. Ш. Насыров 3
1 Уфимский государственный нефтяной технический университет
Уфа, Россия
2 Башкирский государственный университет
Уфа, Россия
3 ООО “Управляющая компания "ТАУ НефтеХим”
Стерлитамак, Россия
* E-mail: sfb1980@mail.ru
Поступила в редакцию 07.12.2018
После доработки 04.03.2019
Принята к публикации 02.04.2019
Аннотация
Продуктами разделения бутилен-бутадиеновой фракции методом хемосорбции являются бутадиен и бутан-бутиленовая фракция. Бутадиен является диеновым мономером для производства эластомеров и пластиков. Бутан-бутиленовая фракция используется как сырье для различных нефтехимических процессов, в частности для получения олигомерных продуктов С4 и метилтретбутилового эфира. Остаточное содержание бутадиена в бутан-бутиленовой фракции более 0.5 мас. % оказывает отрицательное влияние при ее использовании в качестве сырья нефтехимических процессов, а также снижает выход бутадиена. В статье рассмотрен способ очистки бутан-бутиленовой фракции от бутадиена путем возврата в виде флегмы части бутан-бутиленовой фракции в смеси с потоком поглотительного медно-аммиачного раствора в колонну хемосорбции. Смешение потоков осуществляется в трубчатом турбулентном аппарате, вмонтированном в флегмовую линию. Организация дополнительного контакта части бутан-бутиленовой фракции с медно-аммиачным раствором позволит повысить сорбционную эффективность колонны.
ВВЕДЕНИЕ
Промышленными способами получения бутадиена-1,3 (бутадиена) являются метод дегидрирования нормального бутана и выделение из фракции С4 пиролиза углеводородов – бутилен-бутадиеновой фракции (ББФ) [1–4]. В ББФ содержание бутадиена составляет в пределах 35–55 мас. %, остальные компоненты – бутан, бутилены, а также примеси легких углеводородов С3–, тяжелых углеводородов С5+, ацетиленовые углеводороды [5].
Для разделения смеси углеводородов ББФ, различающихся ненасыщенностью химических связей, распространена экстрактивная ректификация с использованием таких растворителей, как ацетонитрил, N,N-диметилформамид или N-метилпирролидон [1–4]. Способом разделения фракции ББФ на бутадиеновую (марки А или Б) и бутан-бутиленовую фракции на ОАО “Стерлитамакский нефтехимический завод” является хемосорбция, которая требует использования сырья высокой чистоты. В связи с этим присутствие примесей обусловливает проведение очистки фракции ББФ перед хемосорбцией: методом ректификации от тяжелых углеводородов С5+, легких углеводородов С3–, влаги и метанола, гидрирование на селективном катализаторе [6–12]. Содержание бутадиена в бутан-бутиленовой фракции, получаемой при разделении ББФ методом хемосорбции поглотительным водно-аммиачным раствором ацетата одновалентной меди (МАР), по техническим требованиям должно быть не более 0.5 мас. %. На действующей промышленной технологической схеме отсутствует флегмовая линия возврата бутан-бутиленовой фракции на орошение колонны хемосорбции, что затрудняет регулирование содержания бутадиена в испаряющейся фракции [4].
С целью совершенствования технологической схемы выделения бутан-бутиленовой фракции рассмотрена возможность регулирования состава бутан-бутиленовой фракции путем возврата ее части в виде флегмы в колонну хемосорбции в смеси с раствором МАР через трубчатый турбулентный аппарат (ТТА).
ЭКСПЕРИМЕНТАЛЬНАЯ ЧАСТЬ
В лабораторных условиях проведено смешение МАР с бутан-бутиленовой фракцией. Состав исходного раствора МАР [13] представлен в табл. 1.
Таблица 1.
Компонентный состав МАР
Компонент | C, кг-моль/м3 |
---|---|
Cu2O | 2.75–3.50 |
CuO | 0.18–0.40 |
CH3COOH | 4.0–4.8 |
NH3 | 9.2–12.8 |
Эксперименты по извлечению бутадиена проводили в объемном аппарате смешения и в статическом аппаратах смешения, результаты которых сравнивали с данными эксперимента, моделирующего расслоенное течение углеводородной фракции и сорбента. Время контакта смешиваемых потоков в экспериментах было принято равным одной минуте.
Извлечение бутадиена оценивали по изменению его концентрации в бутан-бутиленовой фракции и в растворе МАР.
Компонентный состав углеводородов бутан-бутиленовой фракции анализировали методом газожидкостной хроматографии с использованием пламенно-ионизационного детектора. Неподвижная фаза – три-н-бутилфосфат на диатомите, жидкая фаза – полиэтиленгликоль ПЭГ-2000, газ-носитель – гелий, температура колонки 15–40°С. Массовую долю фракции углеводородов определяли методом внутренней нормализации.
Компонентный состав поглощенных МАР углеводородов определяли хроматографически методом абсолютной градуировки. Объем пробы, подаваемый на анализ в испаритель, составляет 1–2 мл. В испарителе углеводороды десорбируются из МАР, далее разделяются на фракции в колонке. Условия хроматографирования: колонка с неподвижной фазой – диатомитовый кирпич фракции 0.16–0.25 мм, неподвижная фаза – полиэтиленгликоль ПЭГ-2000, газ-носитель – гелий; температура испарителя 175°С, термостата колонки 70°С.
В медно-аммиачный раствор, отобранный из циркулирующего потока перед его подачей в колонну хемосорбции объемом 100 мл и охлажденный до температуры минус 10°С, вводили бутан-бутиленовую фракцию объемом 20 мл с температурой также минус 10°С. После выдержки в течение 60 с без перемешивания проводился анализ сред (эксперимент 1).
В эксперименте 2 данную смесь в течение 30 с перемешивали лопастной мешалкой в круглодонной колбе, далее выдерживали без перемешивания 30 с и проводили анализ (эксперимент 2).
При температуре и объемных соотношениях перемешиваемых сред, соответствующих условиям экспериментов 1 и 2, смешивание проводили в трубчатом турбулентном аппарате (эксперимент 3). Схема экспериментальной установки представлена на рис. 1.
РЕЗУЛЬТАТЫ И ИХ ОБСУЖДЕНИЯ
Анализ смешения потоков. Из-за различия по плотностям смешиваемых сред, в эксперименте 1 формировалась расслоенная система, и абсорбция бутадиена раствором МАР происходила на поверхности раздела фаз. Углеводородный состав МАР, насыщенного углеводородами С4, и состав бутан-бутиленовой фракции приведены соответственно в табл. 2 и 3. Содержание бутадиена в растворе МАР возросло с 0.095 до 0.12 мас. %, в ББФ уменьшилась с 0.62 до 0.58 мас. %, что свидетельствует о сорбционном неравновесии потоков.
Таблица 2.
Результаты анализа состава поглотительного раствора МАР
Раствор МАР | x, мас. % | |
---|---|---|
ΣC4H8 | C4H6 | |
Исходный | 0.01 | 0.095 |
Эксперимент 1 | 0.057 | 0.12 |
Эксперимент 2 | 0.16 | 0.21 |
Эксперимент 3 | 0.19 | 0.32 |
Таблица 3.
Результаты анализа состава бутан-бутиленовой фракции
Бутан-бутиленовая фракция | x, мас. % | |||||
---|---|---|---|---|---|---|
i-C4H10 | n-C4H10 | α- и i-C4H8 | β-транс-C4H8 | β-цис-C4H8 | C4H6 | |
Исходная | 5.05 | 11.52 | 73.21 | 7.04 | 2.56 | 0.62 |
Эксперимент 1 | 5.09 | 11.55 | 73.34 | 6.99 | 2.45 | 0.58 |
Эксперимент 2 | 5.17 | 11.57 | 73.42 | 6.91 | 2.47 | 0.46 |
Эксперимент 3 | 5.25 | 11.85 | 73.82 | 6.65 | 2.32 | 0.11 |
Использование перемешивающего устройства способствовало увеличению удельной поверхности контакта фаз и абсорбции бутадиена в раствор МАР. Содержание бутадиена в ББФ уменьшилась до 0.46 мас. %, что подтверждает целесообразность использования перемешивающих устройств для очистки бутан-бутиленовой фракции.
Использование объемного аппарата смешения для формирования высокодисперсных систем требует энергетических затрат на работу мешалки и не предотвращает гравитационного расслоения углеводородной среды и МАР. Исходя из этого, в качестве перемешивающего устройства должен использоваться статический аппарат смешения. При получении высокодисперсных систем в нефтехимических отраслях промышленности успешно зарекомендовал себя трубчатый турбулентный аппарат диффузор-конфузорной конструкции [14–18]. В связи с этим дальнейшее исследование по увеличению поверхности раздела фаз было проведено с использованием этого аппарата. При смешивании бутан-бутиленовой фракции и раствора МАР с применением трубчатого турбулентного аппарата остаточное содержание бутадиена в углеводородной фракции уменьшилось до 0.11 мас. % (табл. 3).
Таким образом, организация дополнительного контакта части бутан-бутиленовой фракции с раствором МАР позволит повысить сорбционную эффективность колонны.
Расчет геометрических параметров аппарата. Определение геометрических параметров ТТА проведено для условий промышленной установки хемосорбции с расходом раствора МАР 37–220 м3/ч. При расчете параметров аппарата было учтено, что смешение раствора МАР и углеводородной фракции необходимо проводить при малых перепадах давления, что напрямую связано с затратами энергии для обеспечения требуемой производительности установки. Расчет геометрических параметров и перепада давления в ТТА проводился по методу, представленному в работе [18], где общий перепад давления определяется как сумма перепадов давления в каждой секции аппарата. Расчеты параметров аппарата проводились исходя из условия, что перемешивающее устройство должно быть частью трубопровода с внутренним диаметром 0.2 м и допустимым перепадом давления в трубопроводе ввода раствора МАР в колонну хемосорбции, равным 0.03 МПа.
В табл. 4 представлены рассчитанные геометрические параметры турбулентного аппарата для перемешивания бутан-бутиленовой фракции с раствором МАР, подаваемых в колонну хемосорбции в качестве орошения, при которых перепад давления незначителен и составляет 0.027 МПа.
Таблица 4.
Геометрические параметры трубчатого турбулентного аппарата
Параметр | Значение |
---|---|
dd, м | 0.20 |
dk, м | 0.145 |
Ls, м | 0.40 |
Lin, м | 0.20 |
Lout, м | 0.20 |
LTTA, м | 2.0 |
γ, град | 45 ± 5 |
N | 4 |
∆PTTA, МПа | 0.027 |
Расчет размеров дисперсных включений. Увеличение интенсивности перемешивания приводит к увеличению массопереноса бутадиена в раствор МАР, что достигается увеличением удельной поверхности контакта фаз. Полученные из литературных источников [18] закономерности диспергирования двухфазных потоков позволяют прогнозировать минимальный размер частиц дисперсной фазы по известным физико-химическим свойствам изучаемых сред.
Расчетным методом получены размеры дисперсных частиц бутан-бутиленовой фракции в зависимости от глубины профилирования диффузор-конфузорного канала ТТА в интервале отношения диаметра диффузора dd к диаметру конфузора dk равном 1–3. Результаты представлены в табл. 5.
Таблица 5.
Влияние глубины профилирования канала на размер частиц и удельную поверхность дисперсных включений (GCAS = 110 м3/ч, R = 4.7 м3/ч, dd = 0.2 м)
dd/dk | D, мм | F, м–1 |
---|---|---|
1.0 | 0.52 | 11.5 |
1.38 | 0.17 | 35.3 |
1.60 | 0.11 | 54.5 |
2.0 | 0.07 | 85.7 |
2.5 | 0.06 | 100 |
3.0 | 0.03 | 200 |
При увеличении соотношения dd/dk от 1 до 3 минимальный размер частиц бутан-бутиленовой фракции уменьшается с 0.52 до 0.03 мм, т.е. в 17 раз, удельная поверхность при этом увеличивается с 11.5 до 200 м–1.
Для ТТА с геометрическими параметрами диффузор-конфузорного канала, равными dd/dk = 1.4, и расходом раствора МАР 110 м3/ч минимальный размер частиц составляет 0.17 мм. Снижение расхода раствора МАР приводит к росту размера частиц диспергированной фазы (табл. 6) и, соответственно, к снижению извлечения бутадиена.
Таблица 6.
Влияние расхода потока МАР на размер частиц и удельную поверхность дисперсных включений (R = 4.7 м3/ч, dd/dk = 1.4)
GCAS, м3/ч | D, мм | F, м–1 |
---|---|---|
37 | 0.62 | 9.7 |
73 | 0.27 | 22.2 |
110 | 0.17 | 35.3 |
147 | 0.12 | 50.0 |
183 | 0.09 | 66.7 |
220 | 0.07 | 85.7 |
Изменение расхода бутан-бутиленовой фракции в виде флегмы в интервале 1.8–36.0 м3/ч не приводит к значимым изменениям размера частиц (табл. 7).
Таблица 7.
Влияние расхода флегмы на размер частиц и удельную поверхность дисперсных включений (GCAS = 110 м3/ч, dd/dk = 1.4)
R, м3/ч | D, мм | F, м–1 |
---|---|---|
1.8 | 0.168 | 35.7 |
3.6 | 0.168 | 35.7 |
4.7 | 0.167 | 35.9 |
7.2 | 0.167 | 35.9 |
18 | 0.166 | 36.1 |
36 | 0.164 | 36.6 |
Технологическая схема хемосорбции с использованием трубчатого турбулентного аппарата. В результате вышеприведенного исследования предложена схема смешения углеводородной фракции с раствором МАР, включающая малогабаритный трубчатый турбулентный аппарат диффузор-конфузорной конструкции. На действующей технологической установке ОАО “Стерлитамакский нефтехимический завод” предлагается возвращать часть бутан-бутиленовой фракции в качестве орошения в колонну хемосорбции в смеси с поглотительным раствором МАР через трубчатый турбулентный аппарат. Технологическая схема очистки бутан-бутиленовой фракции по изучаемому способу представлена на рис. 2.
Рис. 2.
Схема выделения бутадиеновой фракции и очистки бутан-бутиленовой фракции: I – сырьевой поток в колонну очистки возвратного растворителя, II – углеводороды фракции С5, III – вода и метанол, IV – водород, V – водно-аммиачный раствор ацетата одновалентной меди, VI – бутадиеновая фракция, VII – бутан-бутиленовая фракция, 1 – колонны ректификации бутилен-бутадиеновой фракции для очистки от тяжелых углеводородов С5, 2 – колонны ректификации бутилен-бутадиеновой фракции для очистки от влаги и метанола, 3 – реактор гидрирования, 4 – колонна абсорбции, 5 – колонна десорбции, 6 – трубчатый турбулентный аппарат.
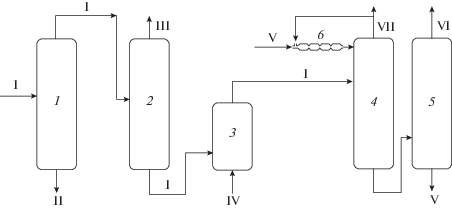
Процесс по предлагаемому способу осуществляется следующим образом. В колонне 1 бутилен-бутадиеновая фракция I очищается от тяжелых углеводородов II методом ректификации. Бутилен-бутадиеновая фракция в колонне азеотропной осушки 2 очищается от влаги и метанола III. На стадии очистки от ацетиленовых углеводородов бутилен-бутадиеновая фракция в реакторе гидрирования подвергается каталитическому гидрированию водородом IV.
На стадии хемосорбции бутилен-бутадиеновая фракция I в присутствии поглотительного водно-аммиачного раствора ацетата одновалентной меди V, охлажденного ниже минус 10°С, делится на бутадиен VI, который выводится из колонны 5 в результате десорбции из раствора МАР при 90–95°С, и бутан-бутиленовую фракцию VII.
Часть потока VII в виде флегмы возвращается в колонну хемосорбции 4, предварительно смешиваясь с МАР V в трубчатом турбулентном аппарате 6.
ЗАКЛЮЧЕНИЕ
В результате исследования показана возможность организации флегмового орошения колонны хемосорбции смесью МАР с бутан-бутиленовой фракцией. Применение трубчатого турбулентного аппарата позволяет получать высокодисперсную систему смешиваемых потоков, повысить сорбционную эффективность колонны.
ОБОЗНАЧЕНИЯ
С | мольная концентрация компонентов в МАР, кг-моль/м3 |
D | размер дисперсных включений, мм |
d | диаметр (внутренний), м |
F | удельная поверхность дисперсных частиц, мм–1 |
G | расход МАР, м3/ч |
L | длина, м |
N | количество диффузор-конфузорных секций |
∆P | перепад давления, МПа |
R | расход бутан-бутиленовой фракции на орошение, м3/ч |
x | содержание компонентов, мас. % |
γ | угол раскрытия диффузора, град |
ИНДЕКСЫ
Список литературы
Платэ Н.А. Основы химии и технологии мономеров. М.: Наука: МАИК “Наука/Интерпериодика”, 2002.
Pavlov O.S., Karsakov S.A., Pavlov S.Yu. Development of processes for C4 hydrocarbons separation and 1,3-butadiene purification // Theor. Found. Chem. Eng. 2011. V. 45. № 6. P. 669. [Павлов О.С., Карсаков С.А., Павлов С.Ю. Развитие процессов разделения C4-углеводородов и очистки 1,3-бутадиена // Теор. осн. хим. технол. 2011. Т. 45. № 6. С. 669.]
Ахмадиев А.Л., Поникаров С.И. Установка вакуумного дегидрирования углеводородов // Вестн. Казан. технол. унив. 2010. № 7. С. 171.
Кирпичников П.А., Береснев В.В., Попова Л.М. Альбом технологических схем основных производств промышленности синтетического каучука. Л.: Химия, 1986.
Насыров И.Ш., Шурупов О.К., Шелудченко В.А., Захаров В.П., Умергалин Т.Г., Шевляков Ф.Б. Оценка влияния состава сырья и технологических параметров отдельных стадий выделения бутадиена-1,3 из бутилен-бутадиеновой фракции методом хемосорбции на расходный коэффициент бутадиена // Башк. хим. ж. 2017. Т. 24. № 4. С. 55.
Касьянова Л.З., Каримов Э.Х., Каримов О.Х. Гидрирование бутадиенсодержащих фракций на поверхности палладиевого катализатора // Приволж. научн. вестн. 2012. № 6 (10). С. 6.
Ламберов А.А., Ильясов И.Р., Егорова С.Р., Назаров М.В., Гильманов Х.Х., Шатилов В.М. Опытные испытания алюмопалладиевых катализаторов селективного гидрирования винилацетилена // Катал. пром-сти. 2008. № 5. С. 49.
Тарарыкин А.Г., Невьянцева Л.Н., Баженов Ю.П., Галиева Ф.А., Касьянова Л.З. Разработка и внедрение в производство катализаторов серии РК220 для селективного гидрирования примесей ацетиленовых углеводородов при очистке бутиленбутадиеновой фракции в процессе получения бутадиена-1,3 // Катал. пром-сти. 2009. № 5. С. 51.
Куттубаев С.Н., Рахимов М.Н., Павлов М.Л., Басимова Р.А., Кутепов Б.И. Исследование эффективности очистки этан-этиленовой фракции пиролиза от ацетиленистых соединений на различных катализаторах // Нефтегазов. дело. 2012. № 4. С. 165.
Nasyrov I.Sh., Shurupov O.K., Zakharov V.P., Shevlyakov F.B., Bakytov N.B. Enhancement of the efficiency of selective hydrogenation of acetylene hydrocarbons in the butylene–butadiene fraction during butadiene-1,3 production // Pet. Chem. 2018. V. 58. № 10. P. 905. [Насыров И.Ш., Шурупов О.К., Захаров В.П., Шевляков Ф.Б., Бакытов Н.Б. Повышение эффективности селективного гидрирования ацетиленовых углеводородов в бутилен-бутадиеновой фракции при производстве бутадиена-1,3 // Нефтехимия. 2018. Т. 58. № 5. С. 618.]
Насыров И.Ш., Шурупов О.К., Захаров В.П., Шевляков Ф.Б., Бакытов Н.Б. Оценка влияния пропускной способности распределительных насадок водорода на эффективность гидрирования ацетиленовых углеводородов в бутилен-бутадиеновой фракции в производстве бутадиена-1,3 // Вестн. технол. унив. 2017. Т. 20. № 24. С. 78.
Захаров В.П., Шевляков Ф.Б., Булатова О.Ф., Путилов Е.Ю., Бакытов Н.Б., Шурупов О.К., Насыров И.Ш. Способ повышения эффективности селективного гидрирования. Патент 2658417 РФ. 2018.
Насыров И.Ш., Шурупов О.К., Шелудченко В.А., Шевляков Ф.Б., Захаров В.П. Исследование влияния окислительно-восстановительного потенциала раствора медноаммиачного на его стабильность в процессе выделения бутадиена из фракции С4 пиролиза углеводородов методом хемосорбции // Хим. пром-сть сегодня. 2017. № 6. С. 16.
Каеем Д.Х., Умергалин Т.Г., Шевляков Ф.Б., Захаров В.П. К уменьшению потерь углеводородных компонентов попутных нефтяных газов // Изв. высш. учебн. завед., хим. хим. технол. 2009. Т. 52. Вып. 12. С. 129.
Данилов Ю.М., Мухаметзянова А.Г., Дьяконов Г.С. Интенсификация процесса перемешивания в малогабаритных трубчатых турбулентных аппаратах // Хим. пром-сть сегодня. 2010. № 9. С. 50.
Захаров В.П., Минскер К.С., Шевляков Ф.Б., Берлин А.А., Алексанян Г.Г., Рытов Б.Л., Коноплев А.А. Интенсификация газожидкостных процессов в трубчатых турбулентных аппаратах // Ж. прикл. хим. 2004. Т. 77. № 11. С. 1822.
Tsadkin M.A., Badikova A.D. Industrial trials of a new-generation contactor for the process of the sulfuric-acid alkylation of isobutane with olefins // Theor. Found. Chem. Eng. 2018. V. 52. № 2. P. 246. [Цадкин М.А., Бадикова А.Д. Промышленные испытания контактора нового поколения для процесса сернокислотного алкилирования изобутана олефинами // Теор. осн. хим. технол. 2018. Т. 52. № 2. С. 225.]
Шевляков Ф.Б., Умергалин Т.Г., Захаров В.П. Использование трубчатого турбулентного аппарата в нефтегазовых и химических процессах. Уфа: Башкирский государственный университет, 2018.
Дополнительные материалы отсутствуют.
Инструменты
Теоретические основы химической технологии