Теоретические основы химической технологии, 2020, T. 54, № 2, стр. 244-256
Оптимизация пиролизных печей типа SRT-VI крупнотоннажной этиленовой установки
Д. В. Арапов *
Воронежский государственный университет инженерных технологий
Воронеж, Россия
* E-mail: arapovdv@gmail.com
Поступила в редакцию 22.02.2019
После доработки 22.07.2019
Принята к публикации 28.09.2019
Аннотация
Рассмотрены вопросы разработки и решения оптимизационной модели для управления в реальном времени процессом пиролиза прямогонного бензина, учитывающей ограничения, накладываемые последующими узлами крупнотоннажного производства на процесс пиролиза: узлом первичного фракционирования пирогаза, его компримирования и сепарации, этиленовым и пропиленовым холодильными циклами, реакторами гидрирования ацетиленистых соединений, разделительными колоннами. Оптимизация реализована на основе математической модели, состоящей из трех частей: расчета физико-химических характеристик прямогонного бензина на основе измеренной плотности и разгонки по Энглеру, расчета кинетических параметров процесса и определения выходов 14 основных продуктов пиролиза. Погрешность моделирования составляет, в отн. %: по этилену ±1.5; пропилену ±2.8; бутадиену ±3.3; бензолу ±3.1. При оптимизации исследовали “легкий” (плотность 0.706 кг/л) и “тяжелый” (0.72 кг/л) прямогонный бензин. Для обоих видов сырья при заданном выходе этилена 10.45 т ч–1/1 печь при заданных ограничениях максимизировалась прибыль и минимизировалась расходная норма по бензину. Полученные результаты сравнивались с пиролизом по регламенту, при котором задание на выход этилена не выполнялось для обоих видов сырья и составило соответственно 10.32 и 9.68 т ч–1/1 печь. При оптимизации максимальная прибыль соответственно составила 1143 и 935 у.е. ч–1/1 печь. При минимизации расходной нормы получили 1.79 т/т для легкого бензина и 1.84 т/т для тяжелого. Ограничения и задание на выход этилена были выполнены. Получен вывод о неэффективности пиролиза прямогонного бензина непосредственно из “трубы” поставщика и необходимости подготовки сырья в промежуточных емкостях с перемешиванием и регламентным анализом плотности бензина и разгонки по Энглеру, которые затем используются при оптимизации.
ВВЕДЕНИЕ
В объеме вырабатываемых в мире пластических масс первое место занимают полиолефины – полиэтилен и полипропилен. Непрерывно растет мировое производство сополимеров этилена и пропилена с другими органическими веществами, например с винилацетатом и бутиленом. Кроме того, низшие алкены являются важнейшим сырьем для получения спиртов, оксидов этилена и пропилена, нитрила акриловой кислоты, винилацетата, стирола, винилхлорида, синтетических каучуков и т.п. Этилен занимает первое место по объему производства среди всех продуктов нефтехимической промышленности. В 2018 году мировое потребление этилена составило 164 млн т, а в РФ было произведено всего 3.5 млн т [1].
Основным способом получения этилена и пропилена служит высокотемпературный пиролиз жидкого и газообразного сырья. При этом образуются побочные продукты: водород, бутилены, бутадиен, ароматические углеводороды, включая бензол, которые повышают технико-экономические показатели этиленовых установок.
С увеличением общего объема выпуска низших алкенов и числа заводов для их производства на порядок возросла мощность отдельных установок, достигнув 400–600 тыс. т. этилена в год, а на некоторых заводах – 1 млн т/год. Большое внимание уделяется созданию новых высокоселективных многопоточных пиролизных печей большой единичной мощности для пиролиза жидкого и газообразного сырья. Это печи USC фирмы Stone and Webster, Millisecond фирмы Kellog, SRT-VI фирмы ABB−Lummus, печи LSCC совместной разработки фирм Linde и Selas, GK-VII фирмы Technip. На отечественных нефтехимических заводах наибольшее распространение получили печи SRT фирмы ABB−Lummus. Возросшие требования к чистоте целевых и побочных продуктов, снижению потерь ценных продуктов и утилизации энергетических потоков привели к существенному усложнению технологической схемы производства этилена и широкому использованию ЭВМ и микроконтроллеров для оптимизации и управления процессами пиролиза и выделения готовых продуктов [2–10]. Оптимальное управление современными крупнотоннажными нефтехимическими установками, включая производство низших алкенов и бензола типа ЭП-300, 450, 600 методом высокотемпературного пиролиза (800–860°C), базируется на использовании информационно-моделирующих систем (ИМС), позволяющих проигрывать на ЭВМ различные производственно-экономические ситуации и выбирать оптимальные решения. На установке ЭП-300 (г. Томск) [2, 3] используется ИМС, позволяющая исследовать влияние различного углеводородного сырья на выходы продуктов пиролиза. Система в информационно-советующем режиме выдает рекомендации по компоновке сырья, планированию и оптимизации режима пиролизных печей. Ядром ИМС служат детерминированные модели кинетики пиролиза газообразного и жидкого сырья и модели печей разной конструкции. На производстве ЭП-300 завода “Мономер” предприятия ПАО “Газпром” “Салаватнефтеоргсинтез” планируется [4] использовать ИМС SPIRO Suite 7, разработанную фирмой Technip. Экономическая выгода внедрения программного продукта заключается в реализации планирования качества и количества продуктов при постоянно изменяющемся составе сырья печей пиролиза. Конечной стадией внедрения будет оснащение этиленовой установки поточными анализаторами состава сырья и адаптация ИМС для оптимального управления пиролизными печами в реальном времени. Примеры использования глобальной системы GPROMS для моделирования и оптимизации процесса пиролиза рассмотрены в [5, 6]. Оптимизировались подача газообразного и жидкого сырья в узел пиролиза, температурный режим и соотношение пар/сырье для каждой печи на основе критерия экономической прибыли с учетом ограничений на суммарный расход сырья, выработку этилена, пропилена, этана и пропана, расхода топливного газа. Для оптимизации использовался метод последовательного квадратичного программирования (SQR). В [7] настройка реализованной в GPROMS кинетики процесса пиролиза в промышленной печи осуществлялась путем добавления новых компонентов и новых схем реакций. В [8] для используемого бензинового сырья заданного состава выполнено моделирование и оптимизация температурного режима крупнотоннажной промышленной печи на основе критерия максимизации получения целевого продукта. Выход этилена рассчитывался по упрощенной модели, полученной на основе заводских экспериментальных данных при изменении температуры процесса. Оптимальная температура, соответствующая максимальному выходу этилена, составила 855°C. Детальное моделирование и оптимизация схемы этиленового завода по переработке пропана описаны в [9]. В разработанной технологической схеме используются пропиленовый и этиленовый холодильные циклы. Пропилен конденсируется холодной водой, а этилен – жидким пропиленом. Оптимизации подверглись ключевые узлы разработанной технологии: пиролиз пропана, ректификационные колонны, холодильные циклы. Итогом проведенной в [9] работы явилось уменьшение эксплуатационных затрат этиленового завода на 42%. Основой алгоритма оптимального управления процессом пиролиза углеводородов [10] служат методы термодинамики смеси с хаосом систем химического состава. В модели установлена зависимость параметров функции нормального распределения продуктов пиролиза по стандартным температурам кипения от режимных параметров процесса. Однако оценка адекватности разработанной модели не приводится. При оптимизации ищется максимум выхода целевых продуктов. Результаты оптимизации смеси этана и бутан-изобутиленовой фракции в пиролизной печи SRT-I установки ЭП-300 ПО “Азерихимия” SOCAR г. Сумгаит (Азербайджан) приведены в [11]. Математическая модель основана на молекулярно-кинетическом механизме пиролиза этана, пропана, бутана и изобутилена. Оптимальные значения параметров составили: температура 850°C, соотношение пар/сырье 1.0. Расчетная прибыль от оптимизации составила 2.4 млн долл./год. В [12–15] реализовано детальное моделирование пиролиза соответственно гудрона, бензиновой и этановой фракций, в [16] исследован процесс пиролиза нафты в присутствии диоксида углерода (ДУ) вместо водяного пара. Отмечается увеличение длины пробега реактора на 25% и выхода целевых продуктов по сравнению с паровым крекингом. Также снижается температура стенки змеевика. Однако вопросы получения больших количеств ДУ и их последующего удаления из пирогаза не рассмотрены.
Общим недостатком опубликованных работ является: 1) оптимизация режима пиролизных печей осуществляется без учета возможности переработки полученной в печах (или печи) парогазовой смеси последующими узлами этиленовой установки, например, при соотношении пар/сырье, равном 1, могут возникнуть проблемы в узле первичного фракционирования по отделению воды от пирогаза и его охлаждению; 2) в подавляющем большинстве в расчетах используются математические модели, основанные на знании химического состава сырья покомпонентного или группового, что связано с большими аналитическими и вычислительными трудностями, значительными финансовыми затратами, невысокой надежностью поточных оптических анализаторов состава сырья при реализации оптимизационных задач в реальном времени, особенно при переработке жидкого сырья.
Для оптимального управления в [17, 18] разработаны упрощенные модели соответственно процессов пиролиза и охлаждения оборотной воды в производстве этилена.
Экономическая эффективность производства этилена определяется как разность стоимости продукции и производственных расходов [5, 19]:
(1)
${\text{Э}} = \sum\limits_{i = 1}^I {{{k}_{i}}{{{\text{Ц}}}_{i}}{{G}_{i}} - \sum\limits_{j = 1}^J {{{Z}_{j}}} } .$Основным видом производственных расходов Zj в (1) на отечественных установках низших алкенов являются [20, 21] затраты на сырье, так как топливный газ для печей получается при пиролизе, а электрическая энергия вырабатывается, как правило, на собственных заводских ТЭЦ. Полнота превращения сырья характеризуется его расходом на получение 1 т целевых продуктов, в качестве которых принимают этилен и пропилен, либо этилен, пропилен, бутадиен и бензол. Расходная норма бензина на 1 т алкенов – это основной критерий [21], характеризующий работу отечественной крупнотоннажной этиленовой установки. Он учитывает выработку олефинов в цехе пиролиза и их потери в цехе газоразделения, выражаемые коэффициентом извлечения:
(2)
${{R}_{{{\text{RN}}}}} = \frac{{{{F}_{{\text{S}}}}}}{{\sum\limits_{l = 1}^L {{{k}_{l}}{{G}_{l}}} }}.$Описание процесса. Основные узлы структуры производства этилена термическим крекингом углеводородного сырья изображены на рис. 1. Прямогонный бензин из узла его подготовки и хранения подается в трубы конвекционных секций пиролизных печей SRT-VI, предварительно разбавленный водяным паром. Подаваемая паросырьевая смесь нагревается до температуры термического разложения углеводородного сырья. В результате реакций пиролиза парогазовая смесь расширяется в несколько раз. Во время работы давление на выходе из печей поддерживается на заданном уровне посредством регулирования давления на входе пирогазового компрессора.
Рис. 1.
Принципиальная схема крупнотоннажной этиленовой установки: 1 – узел подготовки и хранения сырья; 2 – отделение пиролиза; 3 – узел первичного фракционирования пирогаза; 4, 5 – отделение компрессии и сепарации пирогаза; 6 – отделение низкотемпературной ректификации; 7 – узел выделения фракции С4 и разделения жидких продуктов
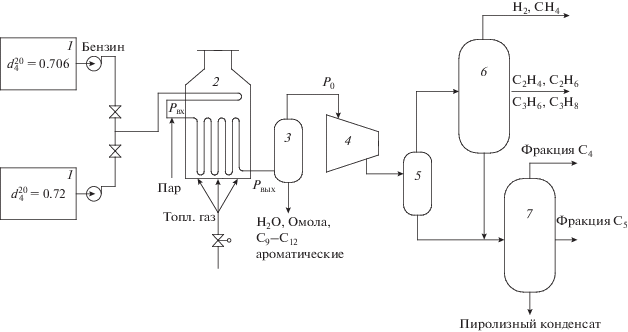
В узле первичного фракционирования (УПФ) пирогаз охлаждается, промывается, из него выделяется пиролизная смола и большая часть воды и ароматических углеводородов ${{С}_{9}}{\kern 1pt} - {\kern 1pt} {{С}_{{12}}}$. В отделении компримирования и сепарации пирогаз сжимается, охлаждается, отделяется от жидких продуктов пиролиза и поступает в отделение низкотемпературной ректификации. Здесь для дальнейшего разделения оставшихся паров используются два холодильных цикла – этиленовый и пропиленовый. Для удобства моделирования предполагается, что разделение водорода и метана реализуется с помощью этиленового цикла, а разделение этилена, этана, пропилена и пропана – посредством пропиленового цикла. Перед разделением на продукты из этан-этиленовой и пропан-пропиленовой фракций удаляются ацетилен (${{{\text{С}}}_{{\text{2}}}}{{{\text{H}}}_{{\text{2}}}}$), пропин с пропадиеном (${{{\text{C}}}_{{\text{3}}}}{{{\text{H}}}_{4}}$) путем гидрирования водородной фракцией в соответствующих реакторах (на рис. 1 не показаны).
Жидкие продукты из отделений компримирования и ректификации подаются в узел выделения фракции ${{{\text{C}}}_{4}}$ и разделения сконденсировавшихся жидкостей.
Ключевым процессом этиленовой установки является высокотемпературный пиролиз углеводородного сырья. Здесь образуются как целевые (этилен, пропилен, бутадиен и бензол), так и побочные продукты (водород, метан, ацетилен, пропин и пропадиен, этан, пропан, изобутилены, бутан, неароматические углеводороды C5–C8, толуол, ксилолы, этилбензол, стирол, ароматические углеводороды C9–C12, пиролизная смола). Остальные процессы являются вспомогательными, служащими для выделения полученных при пиролизе продуктов. От эффективности работы отделения пиролиза зависит эффективность функционирования производства этилена в целом. Объем перерабатываемого сырья на современных крупнотоннажных установках превышает 1 млн т в год. В этой связи даже небольшое усовершенствование режима пиролиза в сторону экономии сырья или повышения селективности процесса экономически выгодно. Кинетика процесса является сложной функцией состава сырья, температуры, пребывания сырья в реакционной зоне, парциального давления, жесткости процесса и т.д. [13, 20]. Однако специалист, следящий за процессом, может регулировать только несколько рабочих переменных: давление на всасе компрессора, расходы сырья и пара в печи, топлива в горелки при постоянно изменяющихся условиях, связанных с изменением свойств сырья, закоксовыванием труб пирозмеевиков и закалочно-испарительных аппаратов (ЗИА), изменением экономической конъюнктуры. Эти колебания требуют частой корректировки значений управляющих воздействий, что не под силу человеку. В этой связи работа актуальна, так как посвящена оптимизации режима пиролизных печей с учетом возможности по переработке парогазовой смеси последующими узлами крупнотоннажной этиленовой установки и без аналитического контроля химического состава бензинового сырья.
ТЕОРЕТИЧЕСКИЙ АНАЛИЗ
Модель процесса. Полная математическая модель процесса пиролиза в трубчатых печах [13] служит для имитации и исследования процесса. Для реализации управления разработана математическая модель, косвенно учитывающая состав сырья и состоящая из трех частей: расчета свойств реакционного бензина, расчета кинетических параметров процесса и определения выходов 14 основных продуктов пиролиза. В реальных производственных условиях каждую смену анализируется плотность жидкого сырья, подаваемого на пиролиз и его фракционный состав (температурная разгонка по Энглеру). По этим анализам в модели рассчитываются физико-химические свойства сырья: индекс ароматичности, показатель парафинистости, молекулярная масса, массовое содержание водорода, углеродные и водородные числа и их отношение, суммарная концентрация атомов водорода, связанных с третичными атомами углерода в разветвленных молекулах сырья, фактор состава сырья по Расторгуеву.
Кинетические параметры основаны на 4 независимых переменных процесса: расходе сырья (${{F}_{{\text{S}}}},$ т/ч), соотношении пар/сырье ($f$), температуре пирогаза на выходе из печи ($T$, K), давлении на линии всасывания пирогазового компрессора (${{P}_{0}}$, МПа). Температура пирогаза на входе в реакционную зону принята равной 650°С, так как при этой температуре начинают заметно протекать реакции пиролиза.
Моделирование свойств бензинового сырья. Исходная ежесменная информация, получаемая в заводской лаборатории в течение 15–20 мин:
$d_{4}^{{20}}$− относительная плотность бензина при 20°С;
${{t}_{{{\text{NK}}}}}$− температура начала кипения бензина, °С;
${{t}_{{10}}}$ − температура, при которой выкипает 10 об. % бензина, °С;
${{t}_{{30}}}$ − температура, при которой выкипает 30 об. % бензина, °С;
${{t}_{{50}}}$ − температура, при которой выкипает 50 об. % бензина, °С;
${{t}_{{70}}}$ − температура, при которой выкипает 70 об. % бензина, °С;
${{t}_{{90}}}$ − температура, при которой выкипает 90 об. % бензина, °С;
${{t}_{{{\text{KK}}}}}$ − температура, при которой выкипает 100 об. % бензина, °С.
1) Индекс ароматичности сырья [22] рассчитывается по формуле
(3)
${\text{BMCI}} = {{87\,552} \mathord{\left/ {\vphantom {{87\,552} {{{A}_{{\text{R}}}}}}} \right. \kern-0em} {{{A}_{{\text{R}}}}}} + 473.7d_{{15.6}}^{{15.6}} - 456.6,$(4)
$\begin{gathered} d_{{15.6}}^{{15.6}} = \left( {d_{4}^{{20}} + 4.4\left( {0.23573 + 0.2229d_{4}^{{20}}} \right.} \right. - \\ - \,\,0.46029 \times {{10}^{{ - 1}}}{{\left( {d_{4}^{{20}}} \right)}^{2}} - {{0.14544 \times {{{10}}^{{ - 2}}}} \mathord{\left/ {\vphantom {{0.14544 \times {{{10}}^{{ - 2}}}} {d_{4}^{{20}}}}} \right. \kern-0em} {d_{4}^{{20}}}} + \\ + \,\,0.53387 \times {{10}^{{ - 1}}}\ln \left( {d_{4}^{{20}}} \right) - 0.41796{{\left( {d_{4}^{{20}}} \right)}^{{0.5}}} + \\ {{ + \,\,\left. {\left. {0.73273 \times {{{10}}^{{ - 2}}}{{{\left( {d_{4}^{{20}}} \right)}}^{3}}} \right)} \right)} \mathord{\left/ {\vphantom {{ + \,\,\left. {\left. {0.73273 \times {{{10}}^{{ - 2}}}{{{\left( {d_{4}^{{20}}} \right)}}^{3}}} \right)} \right)} {0.99903}}} \right. \kern-0em} {0.99903}}; \\ \end{gathered} $(5)
$\begin{gathered} {{A}_{{\text{R}}}} = 1.8{{t}_{{519}}} + 461.69; \\ {{t}_{{519}}} = 0.5\left( {{{t}_{{50}}} + 0.5\left( {{{t}_{{10}}} + {{t}_{{90}}}} \right)} \right). \\ \end{gathered} $2) Показатель парафинистости бензинового сырья (фактор Уотсона) [21–23] равен
(6)
$\begin{gathered} {{{\text{K}}}_{{\text{W}}}} = 1.216{{{{{\left( {{{t}_{{\text{M}}}} + 273.15} \right)}}^{{1/3}}}} \mathord{\left/ {\vphantom {{{{{\left( {{{t}_{{\text{M}}}} + 273.15} \right)}}^{{1/3}}}} {d_{{15.6}}^{{15.6}}}}} \right. \kern-0em} {d_{{15.6}}^{{15.6}}}},\,\,\,\,{\text{где}} \\ {{t}_{{\text{M}}}} = {{t}_{{\text{V}}}} - \left( { - 246.87152 - 403.47302\Delta A} \right. + \\ + \,\,75.6376{{\left( {\Delta A} \right)}^{2}} - 8.7978{{\left( {\Delta A} \right)}^{3}} + \\ \left. { + \,\,587.93994{{{\left( {\Delta A} \right)}}^{{0.5}}} - 0.6429 \times {{{10}}^{{ - 1}}}{{{\left( {\Delta A} \right)}}^{5}}} \right);{\text{ }} \\ \Delta A = {{\left( {{{t}_{{90}}} - {{t}_{{10}}}} \right)} \mathord{\left/ {\vphantom {{\left( {{{t}_{{90}}} - {{t}_{{10}}}} \right)} {80}}} \right. \kern-0em} {80}}; \\ \end{gathered} $(7)
${{t}_{V}} = {{\left( {{{t}_{{10}}} + {{t}_{{30}}} + {{t}_{{50}}} + {{t}_{{70}}} + {{t}_{{90}}}} \right)} \mathord{\left/ {\vphantom {{\left( {{{t}_{{10}}} + {{t}_{{30}}} + {{t}_{{50}}} + {{t}_{{70}}} + {{t}_{{90}}}} \right)} 5}} \right. \kern-0em} 5}.$3) Средняя молекулярная масса бензина рассчитывается по формулам [24]
(8)
$\begin{gathered} {{М}_{{\text{M}}}} = {{\left( {5{{М}_{{{\text{M}}1}}} + {{М}_{{{\text{M}}2}}} + {{М}_{{{\text{M}}3}}}} \right)} \mathord{\left/ {\vphantom {{\left( {5{{М}_{{{\text{M}}1}}} + {{М}_{{{\text{M}}2}}} + {{М}_{{{\text{M}}3}}}} \right)} 7}} \right. \kern-0em} 7},\,\,\,\,{\text{где}} \\ {{М}_{{{\text{M}}1}}} = A + B{{t}_{{\text{М}}}} + Сt_{{\text{M}}}^{2}; \\ \end{gathered} $(9)
$\begin{gathered} A = 204\,324.33 + 9372.8389{{\operatorname{K} }_{W}}\,\, - \\ - \,\,136.1243{\text{K}}_{{\text{W}}}^{2} - {{397\,591.07} \mathord{\left/ {\vphantom {{397\,591.07} {{{{\text{K}}}_{{\text{W}}}}}}} \right. \kern-0em} {{{{\text{K}}}_{{\text{W}}}}}} - \\ - \,\,106\,239.37\ln \left( {{{{\text{K}}}_{{\text{W}}}}} \right); \\ \end{gathered} $(10)
$\begin{gathered} B = 2560.0619 + 131.49387{{{\text{K}}}_{{\text{W}}}} - \\ - \,\,2.09186{\text{K}}_{{\text{W}}}^{2} - {{4850.543} \mathord{\left/ {\vphantom {{4850.543} {{{{\text{K}}}_{{\text{W}}}}}}} \right. \kern-0em} {{{{\text{K}}}_{{\text{W}}}}}} - \\ - \,\,1381.2868\ln \left( {{{{\text{K}}}_{{\text{W}}}}} \right); \\ \end{gathered} $(11)
$\begin{gathered} C = - 1.73893 - 0.122947{{{\text{K}}}_{{\text{W}}}} + \\ + \,\,0.2302 \times {{10}^{{ - 2}}}{\text{K}}_{{\text{W}}}^{2} + {{2.91525} \mathord{\left/ {\vphantom {{2.91525} {{{{\text{K}}}_{{\text{W}}}}}}} \right. \kern-0em} {{{{\text{K}}}_{{\text{W}}}}}} + \\ + \,\,1.0629\ln \left( {{{{\text{K}}}_{{\text{W}}}}} \right); \\ \end{gathered} $(13)
$\begin{gathered} {{М}_{{{\text{M}}3}}} = \left( {40.28{{{\text{K}}}_{{\text{W}}}} - 411.6} \right) + \\ + \,\,\left( {2.0977 - 0.2038{{{\text{K}}}_{{\text{W}}}}} \right)\left( {{{t}_{{\text{M}}}} + 273.15} \right) + \\ + \,\,\left( {0.0003{{{\text{K}}}_{{\text{W}}}} - 0.00245} \right){{\left( {{{t}_{{\text{M}}}} + 273.15} \right)}^{2}}. \\ \end{gathered} $Формулы (9)–(11) получены математической обработкой справочных [24] данных.
4) Фактор состава сырья по Расторгуеву равен [23]
(14)
${{\psi }_{{{\text{RS}}}}} = d_{4}^{{20}} + {{200} \mathord{\left/ {\vphantom {{200} {\left( {{{t}_{{{\text{NK}}}}} + {{t}_{{{\text{KK}}}}} + 546.3} \right)}}} \right. \kern-0em} {\left( {{{t}_{{{\text{NK}}}}} + {{t}_{{{\text{KK}}}}} + 546.3} \right)}}.$5) Содержание водорода в бензине [17]: ${{C}_{{{{{\text{H}}}_{2}}}}} = 2.54{{{\text{K}}}_{{\text{W}}}} - 16.35$, мас. %.
6) Отношение атомов углерода к атомам водорода получено [17] для широкой углеводородной фракции, включая бензиновую, керосиновую и газойлевую:
(15)
$\begin{gathered} \eta = - 6665.5313 + 11\,349.755d_{4}^{{20}} - \\ - \,\,2440.7932{{\left( {d_{4}^{{20}}} \right)}^{2}} - {{2238.1585} \mathord{\left/ {\vphantom {{2238.1585} {d_{4}^{{20}}}}} \right. \kern-0em} {d_{4}^{{20}}}} - \\ - \,\,8746.1899\ln \left( {d_{4}^{{20}}} \right). \\ \end{gathered} $7) Для расчета суммарной концентрации атомов водорода, связанных в молекуле бензина с вторичными и третичными атомами углерода [19], в пиролизном бензине используется формула [17]
(16)
${{C}_{{\sum {{{{\text{H}}}_{2}}} }}} = {{\left( {0.07{{C}_{{{{{\text{H}}}_{2}}}}} - 1} \right)} \mathord{\left/ {\vphantom {{\left( {0.07{{C}_{{{{{\text{H}}}_{2}}}}} - 1} \right)} {0.06}}} \right. \kern-0em} {0.06}},\,\,\,\,{\text{мас}}.\,\,\% ,$8) Углеродное NC и водородное ${{N}_{{{{{\text{H}}}_{{\text{2}}}}}}}$ числа пиролизного сырья равны
(17)
${{N}_{{\text{C}}}} = 0.001{{M}_{{\text{M}}}}{{\left( {100 - {{C}_{{{{{\text{H}}}_{{\text{2}}}}}}}} \right)} \mathord{\left/ {\vphantom {{\left( {100 - {{C}_{{{{{\text{H}}}_{{\text{2}}}}}}}} \right)} {12}}} \right. \kern-0em} {12}};$(18)
${{N}_{{{{{\text{H}}}_{{\text{2}}}}}}} = 0.01{{M}_{{\text{M}}}}{{C}_{{{{{\text{H}}}_{{\text{2}}}}}}}.$Расчет кинетических параметров. 1) Конверсия бензина X является функцией [17, 19] кинетического фактора жесткости процесса:
(20)
$\begin{gathered} {\text{KSF}} = \exp ({{ - 32\,710} \mathord{\left/ {\vphantom {{ - 32\,710} T}} \right. \kern-0em} T} + \ln \left( {0.2{{\psi }_{{{\text{QQ}}}}}} \right) + \\ + \,\,32.2362 - \ln \left( {{{N}_{{\text{C}}}} - 2} \right)). \\ \end{gathered} $Среднее время контакта обратно пропорционально объемному расходу газа. Следовательно, время контакта для среднего зафиксированного объемного расхода может быть определено как среднее значение времени псевдопребывания на входе и выходе радиантной части пирозмеевика:
(21)
${{\psi }_{{{\text{QN}}}}} = \frac{{{{k}_{{\text{Q}}}}\left( {{{P}_{{{\text{вых}}}}} + {{\psi }_{{{\text{DP}}}}}} \right)}}{{923.15\left( {\frac{F}{{6{{M}_{{\text{M}}}}}} + \frac{{{{F}_{{\text{S}}}}f}}{{108}}} \right)}};$(22)
${{\psi }_{{{\text{QK}}}}} = \frac{{{{k}_{{\text{Q}}}}{{P}_{{{\text{вых}}}}}}}{{T\left( {\frac{{{{F}_{{\text{S}}}}{{k}_{{{\text{RAS}}}}}}}{{6{{M}_{{\text{M}}}}}} + \frac{{{{F}_{{\text{S}}}}f}}{{18}}} \right)}};$(23)
${{\psi }_{{{\text{QQ}}}}} = {{\left( {{{\psi }_{{{\text{QN}}}}} - {{\psi }_{{{\text{QK}}}}}} \right)} \mathord{\left/ {\vphantom {{\left( {{{\psi }_{{{\text{QN}}}}} - {{\psi }_{{{\text{QK}}}}}} \right)} {\ln \left( {{{{{\psi }_{{{\text{QN}}}}}} \mathord{\left/ {\vphantom {{{{\psi }_{{{\text{QN}}}}}} {{{\psi }_{{{\text{QK}}}}}}}} \right. \kern-0em} {{{\psi }_{{{\text{QK}}}}}}}} \right)}}} \right. \kern-0em} {\ln \left( {{{{{\psi }_{{{\text{QN}}}}}} \mathord{\left/ {\vphantom {{{{\psi }_{{{\text{QN}}}}}} {{{\psi }_{{{\text{QK}}}}}}}} \right. \kern-0em} {{{\psi }_{{{\text{QK}}}}}}}} \right)}},$при моделировании принято: kQ = 26.5; kRAS = 3.5.
2) Перепад давления в радиантной секции пиролизного змеевика пропорционален квадрату мольного расхода:
(24)
${{\psi }_{{{\text{DP}}}}} = {{k}_{{{\text{DP}}}}}{{\left( {\frac{{{{F}_{{\text{S}}}}}}{{6{{M}_{{\text{M}}}}}} + \frac{{{{F}_{{\text{S}}}}f}}{{108}}} \right)}^{2}},$3) Функция парциального давления углеводородов на выходе из печи равна
(25)
${{\psi }_{{{\text{PP}}}}} = {{P}_{{{\text{вых}}}}}\left( {\frac{{{{F}_{{\text{S}}}}{{k}_{{{\text{RAS}}}}}}}{{6{{M}_{{\text{M}}}}}} + \frac{{{{F}_{{\text{S}}}}f}}{{108}}} \right).$Число 6 в формулах (21), (22) и (24), (25) означает количество разветвленных пирозмеевиков в печи SRT-VI.
4) Параметр молекулярных столкновений [17, 20, 21] объединяет три других важнейших параметра пиролиза – температуру, время контакта и парциальное давление углеводородов:
(26)
${\text{PMS}} = \frac{{\psi _{{{\text{PP}}}}^{2}{{\psi }_{{{\text{QQ}}}}}}}{{\Delta T_{1}^{{1.5}}}},$5) Параметр, характеризующий отношение скорости отрыва третичного атома водорода к скорости отрыва первичного атома в углеводородном сырье, равен [17]
(27)
$\begin{gathered} {{k}_{{{\text{TRE}}}}} = - 1422.0031 + 2211.7921\Delta T - \\ - \,\,962.87658\Delta {{T}^{2}} + 191.01314\Delta {{T}^{3}} - \\ - \,\,894.24911\ln \left( {\Delta T} \right) - {{10.339855} \mathord{\left/ {\vphantom {{10.339855} {\Delta {{T}^{2}}}}} \right. \kern-0em} {\Delta {{T}^{2}}}}; \\ \Delta T = {{\left( {t + 273.15} \right)} \mathord{\left/ {\vphantom {{\left( {t + 273.15} \right)} {1000}}} \right. \kern-0em} {1000}}. \\ \end{gathered} $6) Давление пирогаза Pвых на выходе из печи, с одной стороны, равно
С другой стороны, выход печи связан с входом в пирогазовый компрессор через ЗИА и УПФ:
(29)
${{P}_{{{\text{вых}}}}} - \Delta {{P}_{{{\text{ЗИА}}}}} - \Delta {{P}_{{{\text{PF}}}}} = {{P}_{0}}.$Объединяя (28) и (29), получим выражение для расчета давления на входе в компрессор: ${{P}_{0}} = {{P}_{{{\text{вх}}}}} - {{\psi }_{{{\text{DP}}}}} - \Delta {{P}_{{{\text{ЗИА}}}}} - \Delta {{P}_{{{\text{PF}}}}}.$
Давление Pвх для свежей, незакоксованной печи SRT-VI составляет Pвх = 0.38–0.4 МПа и Pвх = = 0.4–0.43 МПа для печи с пробегом 60 сут. Перепад давления на свежем ЗИА равен $\Delta {{P}_{{{\text{ЗИА}}}}}$ = = 0.021–0.022 МПа, а на ЗИА с пробегом 60 сут $\Delta {{P}_{{{\text{ЗИА}}}}}$ = 0.027–0.029 МПа. Перепад давления на УПФ находится в пределах $\Delta {{P}_{{{\text{PF}}}}}$ = 0.02–0.025 МПа в зависимости от состояния этого узла и связывающих трубопроводов. Таким образом, давление на входе в компрессор для свежих и закоксованных аппаратов: печи, ЗИА и УПФ соответственно равно
(30)
${{P}_{0}} = 0.339 - {{\psi }_{{{\text{DP}}}}};\,\,\,\,{{P}_{0}} = 0.376 - {{\psi }_{{{\text{DP}}}}}.$Расчет выходов продуктов. Для расчета выходов продуктов пиролиза получены 14 регрессионных уравнений, основанных на лабораторных значениях плотности и фракционного состава бензина, экспериментальных данных о режиме процесса в печи SRT-VI, хроматографическом анализе состава газообразных и жидких продуктов пиролиза. В общем виде полученные математические формулы записываются в виде функции
(31)
${{B}_{i}} = \psi \left( {{\text{BMCI}},{{{\text{K}}}_{{\text{W}}}},{{M}_{{\text{M}}}},{{C}_{{{{{\text{H}}}_{2}}}}},\eta ,{{\psi }_{{{\text{RS}}}}},X,{{\psi }_{{{\text{DP}}}}},{{\psi }_{{{\text{QQ}}}}},{{\psi }_{{{\text{PP}}}}},{\text{PMS}},{{k}_{{{\text{TRE}}}}},\Delta T,f} \right).$Фактор состава сырья по Расторгуеву (14) используется только при расчете выходов жидких продуктов i = 10–14. Ниже приведены полученные регрессии для расчета выходов (мас. %) четырех основных продуктов пиролиза – этилена, пропилена, бутадиена и бензола:
(32)
$\begin{gathered} {{B}_{4}} = {{a}_{1}}{{X}^{{{{a}_{2}}}}} + {{a}_{3}}\Delta T + {{a}_{4}}\psi _{{{\text{PP}}}}^{{{{a}_{5}}}} + {{a}_{6}}{\text{PMS}} + {{a}_{7}}{{{\text{K}}}_{{\text{W}}}} + \\ + \,\,{{{{a}_{8}}{{C}_{{{{{\text{H}}}_{{\text{2}}}}}}}} \mathord{\left/ {\vphantom {{{{a}_{8}}{{C}_{{{{{\text{H}}}_{{\text{2}}}}}}}} {{{M}_{{\text{M}}}}}}} \right. \kern-0em} {{{M}_{{\text{M}}}}}} + {{a}_{9}}{{{\text{K}}}_{{\text{W}}}}{{{{C}_{{{{{\text{H}}}_{{\text{2}}}}}}}} \mathord{\left/ {\vphantom {{{{C}_{{{{{\text{H}}}_{{\text{2}}}}}}}} {{\text{BMCI}}}}} \right. \kern-0em} {{\text{BMCI}}}} + {{{{a}_{{10}}}\Delta T} \mathord{\left/ {\vphantom {{{{a}_{{10}}}\Delta T} {{{\eta }_{{c/н}}}}}} \right. \kern-0em} {{{\eta }_{{c/н}}}}} + \\ + \,\,{{a}_{{11}}}{{\left( {100 - {\text{BMCI}}} \right)} \mathord{\left/ {\vphantom {{\left( {100 - {\text{BMCI}}} \right)} {{\text{BMCI}}}}} \right. \kern-0em} {{\text{BMCI}}}} + {{a}_{{12}}}f, \\ \end{gathered} $(33)
$\begin{gathered} {{B}_{7}} = {{{{a}_{1}}} \mathord{\left/ {\vphantom {{{{a}_{1}}} {{{X}^{{{{a}_{2}}}}}}}} \right. \kern-0em} {{{X}^{{{{a}_{2}}}}}}} + {{{{a}_{3}}f} \mathord{\left/ {\vphantom {{{{a}_{3}}f} {{{\psi }_{{{\text{QQ}}}}}}}} \right. \kern-0em} {{{\psi }_{{{\text{QQ}}}}}}} + {{a}_{4}}\Delta T + {{{{a}_{5}}} \mathord{\left/ {\vphantom {{{{a}_{5}}} {\psi _{{{\text{PP}}}}^{{{{a}_{6}}}}}}} \right. \kern-0em} {\psi _{{{\text{PP}}}}^{{{{a}_{6}}}}}} + \\ + \,\,{{a}_{7}}{\text{PMS}} + {{a}_{8}}\left( {100 - {\text{BMCI}}} \right){{M}_{{\text{M}}}} + {{{{a}_{9}}{{{\text{K}}}_{{\text{W}}}}} \mathord{\left/ {\vphantom {{{{a}_{9}}{{{\text{K}}}_{{\text{W}}}}} {{{k}_{{{\text{TRE}}}}}}}} \right. \kern-0em} {{{k}_{{{\text{TRE}}}}}}} + \\ + \,\,{{{{a}_{{10}}}{{C}_{{{{{\text{H}}}_{{\text{2}}}}}}}} \mathord{\left/ {\vphantom {{{{a}_{{10}}}{{C}_{{{{{\text{H}}}_{{\text{2}}}}}}}} {{{M}_{{\text{M}}}}}}} \right. \kern-0em} {{{M}_{{\text{M}}}}}} + {{a}_{{11}}}{{{\text{K}}}_{{\text{W}}}}{{{{C}_{{{{{\text{H}}}_{{\text{2}}}}}}}} \mathord{\left/ {\vphantom {{{{C}_{{{{{\text{H}}}_{{\text{2}}}}}}}} {{\text{BMCI}}}}} \right. \kern-0em} {{\text{BMCI}}}} + {{{{a}_{{12}}}} \mathord{\left/ {\vphantom {{{{a}_{{12}}}} X}} \right. \kern-0em} X} \\ + \,\,{{a}_{{13}}}f + + {{a}_{{14}}}{{M}_{{\text{M}}}}{{\left( {0.07{{C}_{{{{{\text{H}}}_{{\text{2}}}}}}} - 1} \right)} \mathord{\left/ {\vphantom {{\left( {0.07{{C}_{{{{{\text{H}}}_{{\text{2}}}}}}} - 1} \right)} {{{C}_{{{{{\text{H}}}_{{\text{2}}}}}}}}}} \right. \kern-0em} {{{C}_{{{{{\text{H}}}_{{\text{2}}}}}}}}}; \\ \end{gathered} $(34)
$\begin{gathered} {{B}_{8}} = {{{{a}_{1}}{{X}^{{{{a}_{2}}}}}{{\psi }_{{{\text{QQ}}}}}} \mathord{\left/ {\vphantom {{{{a}_{1}}{{X}^{{{{a}_{2}}}}}{{\psi }_{{{\text{QQ}}}}}} {\psi _{{{\text{PP}}}}^{{2.5}}}}} \right. \kern-0em} {\psi _{{{\text{PP}}}}^{{2.5}}}} + {{{{a}_{3}}f} \mathord{\left/ {\vphantom {{{{a}_{3}}f} {{{\psi }_{{{\text{QQ}}}}}}}} \right. \kern-0em} {{{\psi }_{{{\text{QQ}}}}}}} + {{a}_{4}}\Delta T + \\ + \,\,{{a}_{5}}\psi _{{PP}}^{{{{a}_{6}}}} + {{a}_{7}}{\text{PMS}} + {{a}_{8}}{{{{\left( {100 - {\text{BMCI}}} \right)} \mathord{\left/ {\vphantom {{\left( {100 - {\text{BMCI}}} \right)} {{{M}_{{\text{M}}}}}}} \right. \kern-0em} {{{M}_{{\text{M}}}}}}} \mathord{\left/ {\vphantom {{{{\left( {100 - {\text{BMCI}}} \right)} \mathord{\left/ {\vphantom {{\left( {100 - {\text{BMCI}}} \right)} {{{M}_{{\text{M}}}}}}} \right. \kern-0em} {{{M}_{{\text{M}}}}}}} {{{{\text{K}}}_{{\text{W}}}}}}} \right. \kern-0em} {{{{\text{K}}}_{{\text{W}}}}}} + \\ + \,\,{{a}_{9}}{{{\text{K}}}_{{\text{W}}}}{{M}_{{\text{M}}}}{{\left( {0.07{{C}_{{{{{\text{H}}}_{{\text{2}}}}}}} - 1} \right)} \mathord{\left/ {\vphantom {{\left( {0.07{{C}_{{{{{\text{H}}}_{{\text{2}}}}}}} - 1} \right)} {{{k}_{{{\text{TRE}}}}}}}} \right. \kern-0em} {{{k}_{{{\text{TRE}}}}}}} + {{{{a}_{{10}}}{{C}_{{{{{\text{H}}}_{{\text{2}}}}}}}} \mathord{\left/ {\vphantom {{{{a}_{{10}}}{{C}_{{{{{\text{H}}}_{{\text{2}}}}}}}} {{{M}_{{\text{M}}}}}}} \right. \kern-0em} {{{M}_{{\text{M}}}}}} + \\ + \,\,{{a}_{{11}}}{{{\text{K}}}_{{\text{W}}}}{{{{C}_{{{{{\text{H}}}_{{\text{2}}}}}}}} \mathord{\left/ {\vphantom {{{{C}_{{{{{\text{H}}}_{{\text{2}}}}}}}} {{\text{BMCI}}}}} \right. \kern-0em} {{\text{BMCI}}}} + {{{{{{a}_{{12}}}{{C}_{{{{{\text{H}}}_{{\text{2}}}}}}}} \mathord{\left/ {\vphantom {{{{a}_{{12}}}{{C}_{{{{{\text{H}}}_{{\text{2}}}}}}}} {{{k}_{{{\text{TRE}}}}}}}} \right. \kern-0em} {{{k}_{{{\text{TRE}}}}}}}} \mathord{\left/ {\vphantom {{{{{{a}_{{12}}}{{C}_{{{{{\text{H}}}_{{\text{2}}}}}}}} \mathord{\left/ {\vphantom {{{{a}_{{12}}}{{C}_{{{{{\text{H}}}_{{\text{2}}}}}}}} {{{k}_{{{\text{TRE}}}}}}}} \right. \kern-0em} {{{k}_{{{\text{TRE}}}}}}}} {{{M}_{{\text{M}}}}}}} \right. \kern-0em} {{{M}_{{\text{M}}}}}} + \\ + \,\,{{a}_{{13}}}f + {{a}_{{14}}}{{M}_{{\text{M}}}}{{\left( {0.07{{C}_{{{{{\text{H}}}_{{\text{2}}}}}}} - 1} \right)} \mathord{\left/ {\vphantom {{\left( {0.07{{C}_{{{{{\text{H}}}_{{\text{2}}}}}}} - 1} \right)} {{{C}_{{{{{\text{H}}}_{{\text{2}}}}}}}}}} \right. \kern-0em} {{{C}_{{{{{\text{H}}}_{{\text{2}}}}}}}}} + \\ + \,\,{{a}_{{15}}}\left( {0.07{{C}_{{{{{\text{H}}}_{{\text{2}}}}}}} - 1} \right){{{{k}_{{{\text{TRE}}}}}} \mathord{\left/ {\vphantom {{{{k}_{{{\text{TRE}}}}}} {{{M}_{{\text{M}}}}}}} \right. \kern-0em} {{{M}_{{\text{M}}}}}} + {{a}_{{16}}}{{\psi }_{{{\text{QQ}}}}}; \\ \end{gathered} $(35)
$\begin{gathered} {{B}_{{11}}} = {{{{a}_{1}}} \mathord{\left/ {\vphantom {{{{a}_{1}}} {{{X}^{{{{a}_{2}}}}}}}} \right. \kern-0em} {{{X}^{{{{a}_{2}}}}}}}{{\psi }_{{{\text{QQ}}}}}\psi _{{{\text{PP}}}}^{{2.5}} + {{a}_{3}}{{\psi }_{{{\text{DP}}}}} + {{{{a}_{4}}} \mathord{\left/ {\vphantom {{{{a}_{4}}} {\psi _{{{\text{PP}}}}^{{{{a}_{5}}}}}}} \right. \kern-0em} {\psi _{{{\text{PP}}}}^{{{{a}_{5}}}}}} + \\ + \,\,{{a}_{6}}{\text{PMS}}{{C}_{{{{{\text{H}}}_{{\text{2}}}}}}} + {{{{a}_{7}}} \mathord{\left/ {\vphantom {{{{a}_{7}}} {{{C}_{{{{{\text{H}}}_{{\text{2}}}}}}}}}} \right. \kern-0em} {{{C}_{{{{{\text{H}}}_{{\text{2}}}}}}}}} + {{{{a}_{8}}{\text{BMCI}}} \mathord{\left/ {\vphantom {{{{a}_{8}}{\text{BMCI}}} {\left( {{{{\text{K}}}_{{\text{W}}}}{{C}_{{{{{\text{H}}}_{{\text{2}}}}}}}} \right)}}} \right. \kern-0em} {\left( {{{{\text{K}}}_{{\text{W}}}}{{C}_{{{{{\text{H}}}_{{\text{2}}}}}}}} \right)}} + \\ + \,\,{{a}_{9}}\Delta T\eta + {{{{a}_{{10}}}{{\psi }_{{{\text{QQ}}}}}} \mathord{\left/ {\vphantom {{{{a}_{{10}}}{{\psi }_{{{\text{QQ}}}}}} f}} \right. \kern-0em} f} + {{a}_{{11}}}{{\psi }_{{QQ}}} + \\ + \,\,{{a}_{{12}}}{{{X \mathord{\left/ {\vphantom {X {\left( {0.07{{C}_{{{{{\text{H}}}_{{\text{2}}}}}}} - 1} \right)}}} \right. \kern-0em} {\left( {0.07{{C}_{{{{{\text{H}}}_{{\text{2}}}}}}} - 1} \right)}}} \mathord{\left/ {\vphantom {{{X \mathord{\left/ {\vphantom {X {\left( {0.07{{C}_{{{{{\text{H}}}_{{\text{2}}}}}}} - 1} \right)}}} \right. \kern-0em} {\left( {0.07{{C}_{{{{{\text{H}}}_{{\text{2}}}}}}} - 1} \right)}}} {{{C}_{{{{{\text{H}}}_{{\text{2}}}}}}}}}} \right. \kern-0em} {{{C}_{{{{{\text{H}}}_{{\text{2}}}}}}}}} + {{{{a}_{{13}}}} \mathord{\left/ {\vphantom {{{{a}_{{13}}}} {{{\psi }_{{{\text{RS}}}}}}}} \right. \kern-0em} {{{\psi }_{{{\text{RS}}}}}}}. \\ \end{gathered} $Критерии оптимизации. Выработка i-го продукта в процессе пиролиза равна
Подставляя (36) в (1) и (2), получим значения критериев оптимизации этиленовой установки – прибыли (37) или нормы расхода сырья (38):
(37)
$\begin{gathered} {\text{Э}} = 0.01{{F}_{{\text{S}}}}\left( {{{k}_{1}}{{B}_{1}}{{{\text{Ц}}}_{1}} + } \right.{{k}_{2}}{{B}_{2}}{{{\text{Ц}}}_{2}} + {{k}_{4}}{{B}_{4}}{{{\text{Ц}}}_{4}} + \\ + \,\,{{k}_{5}}{{B}_{5}}{{{\text{Ц}}}_{5}} + {{k}_{7}}{{B}_{7}}{{{\text{Ц}}}_{7}} + {{k}_{8}}{{B}_{8}}{{{\text{Ц}}}_{8}} + {{k}_{9}}{{B}_{9}}{{{\text{Ц}}}_{9}} + \\ + \,\,{{k}_{{10}}}{{B}_{{10}}}{{{\text{Ц}}}_{{10}}} + {{k}_{{11}}}{{B}_{{11}}}{{{\text{Ц}}}_{{11}}} + {{k}_{{12}}}{{B}_{{12}}}{{{\text{Ц}}}_{{12}}} + \\ \left. { + \,\,{{k}_{{13}}}{{B}_{{13}}}{{{\text{Ц}}}_{{13}}} + {{k}_{{14}}}{{B}_{{14}}}{{{\text{Ц}}}_{{14}}}} \right) - {{F}_{{\text{S}}}}{{{\text{Ц}}}_{{\text{S}}}}; \\ \end{gathered} $(38)
${{R}_{{{\text{RN}}}}} = \frac{{100\% }}{{{{k}_{4}}{{B}_{4}} + {{k}_{7}}{{B}_{7}} + {{k}_{8}}{{B}_{8}} + {{k}_{{11}}}{{B}_{{11}}}}}.$Ограничения. В зависимости от конструкции блока пиролизных печей и этиленовой установки в целом на принятый критерий оптимизации (37) или (38) накладываются ограничения в виде неравенств и равенства.
Ограничения на независимые переменные – расход сырья и пара в печь, температуру пирогаза на выходе из печи, давление на входе в пирогазовый компрессор записываются в виде
Ограничения (39)–(41) определяются технологическим регламентом, а (42) – безопасностью работы пирогазового компрессора и всего производства этилена для предотвращения подсоса атмосферного воздуха.
Ограничения на выработку целевых и побочных продуктов пиролиза, накладываемые со стороны последующих узлов и отделений этиленовой установки для потока пирогаза из одной печи SRT-VI:
(43)
${{R}_{g}} = 0.01{{F}_{{\text{S}}}}\sum\limits_{i = 1}^{{{N}_{g}}} {{{\alpha }_{{ig}}}{{B}_{i}} \leqslant R_{g}^{{\max }}} .$Ограничения $R_{g}^{{\max }}$ определяются из анализа паспортных характеристик основного оборудования g узла, материального баланса и технологического регламента с учетом текущего состояния аппаратуры (насосов, теплообменников, сепараторов, колонн и т.п.), арматуры, трубопроводов. Чаще всего эти ограничения накладываются со стороны УПФ, пирогазового компрессора, этиленового и пропиленового холодильных циклов, реакторов гидрирования ацетиленистых соединений, ряда разделительных колонн, например, выделения этана и этилена, пропана и пропилена, разделения фракции C4 и жидких продуктов пиролиза и т.д.
В проведенном исследовании приняли:
1) УПФ может переработать не более $R_{{{\text{PF}}}}^{*},$ $\frac{{{\text{т/ч}}}}{{{\text{1 печь}}}}$ жидких углеводородов и воды:
(44)
$\begin{gathered} {{R}_{{{\text{PF}}}}} = 0.01{{F}_{{\text{S}}}}\left( {0.15{{B}_{{10}}} + 0.55{{B}_{{13}}} + {{B}_{{14}}}} \right) + \\ + \,\,0.999{{F}_{{\text{S}}}}f \leqslant R_{{{\text{PF}}}}^{*}. \\ \end{gathered} $2) Нагрузка на пирогазовый компрессор ограничена минимальным и максимальным мольным расходом паров на его входе $R_{{{\text{PC}}}}^{{\min }}$ и $R_{{{\text{PC}}}}^{{\max }},$ $\frac{{{\text{т - моль/ч}}}}{{{\text{1 печь}}}}$. Минимальное значение обуславливается защитой компрессора от помпажа с заданным запасом устойчивости и определяется из паспортной газодинамической характеристики его первой ступени [25], максимальное – производительностью компрессора:
(45)
$\begin{gathered} R_{{{\text{PC}}}}^{{\min }} \leqslant {{R}_{{{\text{PC}}}}} = 0.01{{F}_{{\text{S}}}}\left( {\frac{{{{B}_{1}}}}{{{{M}_{{{{B}_{1}}}}}}} + \frac{{{{B}_{2}}}}{{{{M}_{{{{B}_{2}}}}}}} + \frac{{{{B}_{3}}}}{{{{M}_{{{{B}_{3}}}}}}} + } \right. \\ + \,\,\frac{{{{B}_{4}}}}{{{{M}_{{{{B}_{4}}}}}}} + \frac{{{{B}_{5}}}}{{{{M}_{{{{B}_{5}}}}}}} + \frac{{{{B}_{6}}}}{{{{M}_{{{{B}_{6}}}}}}} + \frac{{{{B}_{7}}}}{{{{M}_{{{{B}_{7}}}}}}} + \frac{{{{B}_{8}}}}{{{{M}_{{{{B}_{8}}}}}}} + \frac{{{{B}_{9}}}}{{{{M}_{{{{B}_{9}}}}}}} + \\ \left. { + \,\,\frac{{0.85{{B}_{{10}}}}}{{{{M}_{{{{B}_{{10}}}}}}}} + \frac{{0.95{{B}_{{11}}}}}{{{{M}_{{{{B}_{{11}}}}}}}} + \frac{{0.95{{B}_{{12}}}}}{{{{M}_{{{{B}_{{12}}}}}}}} + \frac{{0.45{{B}_{{13}}}}}{{{{M}_{{{{B}_{{13}}}}}}}}} \right) \leqslant R_{{{\text{PC}}}}^{{\max }}. \\ \end{gathered} $3) Нагрузка на этиленовый холодильный цикл ограничена его возможностью охлаждения определенной массы водорода и метана $R_{{\text{E}}}^{*},$ $\frac{{{\text{т/ч}}}}{{{\text{1 печь}}}}$:
(46)
${{R}_{{\text{E}}}} = 0.01{{F}_{{\text{S}}}}\left( {{{B}_{1}} + {{B}_{2}}} \right) \leqslant R_{{\text{E}}}^{*}.$4) Нагрузка на пропиленовый холодильный цикл ограничена его возможностью охлаждения до необходимой температуры определенной массы этилена, этана, пропилена и пропана $R_{{\text{P}}}^{*},$ $\frac{{{\text{т/ч}}}}{{{\text{1 печь}}}}$:
(47)
${{R}_{{\text{P}}}} = 0.01{{F}_{{\text{S}}}}\left( {{{B}_{4}} + {{B}_{5}} + {{B}_{7}} + 0.33{{B}_{5}}} \right) \leqslant R_{{\text{P}}}^{*},$5) Реакторы гидрирования ацетилена в ЭЭФ и пропина с пропадиеном в ППФ могут переработать $R_{{{\text{AC}}}}^{*}$ $\frac{{{\text{т/ч}}}}{{{\text{1 печь}}}}$ ацетилена и $R_{{{\text{MAC}}}}^{*}$ $\frac{{{\text{т/ч}}}}{{{\text{1 печь}}}}$ пропина с пропадиеном соответственно:
6) Пропускная способность этан-этиленовой и пропан-пропиленовой колонн ограничена величинами $R_{{{\text{EE}}}}^{*},$ $\frac{{{\text{т/ч}}}}{{{\text{1 печь}}}}$ и $R_{{{\text{PP}}}}^{*},$ $\frac{{{\text{т/ч}}}}{{{\text{1 печь}}}}$ соответственно:
(50)
${{R}_{{{\text{EE}}}}} = 0.01{{F}_{{\text{S}}}}\left( {{{B}_{4}} + {{B}_{5}}} \right) \leqslant R_{{{\text{EE}}}}^{*};$(51)
${{R}_{{{\text{PP}}}}} = 0.01{{F}_{{\text{S}}}}\left( {{{B}_{7}} + {{{{B}_{5}}} \mathord{\left/ {\vphantom {{{{B}_{5}}} 3}} \right. \kern-0em} 3}} \right) \leqslant R_{{{\text{PP}}}}^{*}.$Ограничение – равенство обычно накладывается заданием на выпуск главного целевого продукта – этилена:
Задача оптимизации крупнотоннажной пиролизной печи заключается в максимизации критерия (37) (или минимизации критерия (38)) в условиях действующих ограничений на независимые и зависимые переменные и выполнении задания по выпуску этилена, в общем случае (39)–(43), (52), а в исследованном варианте (39)–(42), (44)–(52).
РЕЗУЛЬТАТЫ И ИХ ОБСУЖДЕНИЕ
Программные пакеты, реализующие идентификацию моделей (31)–(35) и оптимизацию этиленовой установки (37), (38), (39)–(42), (44)–(52), разработаны на языке C# в среде MS Visual Studio 2010. Параметрическая идентификация моделей (31)–(35), а также оптимизация установки реализована методом конфигураций Хука–Дживса. При идентификации искомыми константами служат коэффициенты aqi, рассчитанные для каждого i-го продукта. В качестве функции цели используется квадратичный критерий отклонения расчетных значений выходов продуктов от экспериментальных:
(53)
${{\sum\limits_{n = 1}^{26} {\left( {1 - \frac{{{{B}_{{{\text{in}}}}}\left( {\mathbf{A}} \right)}}{{B_{{{\text{in}}}}^{{{\text{ex}}}}}}} \right)} }^{2}}\xrightarrow[{\mathbf{А}}]{}\min .$Поиск реализуется по коэффициентам ${\mathbf{А}}$. Погрешность моделирования составила: по этилену ±1.5 отн. %, пропилену ±2.8 отн. %, бутадиену ±3.3 отн. %, бензолу ±3.1 отн. %. Максимальные ошибки, равные ±7.6, ±8.9, ±19.1 отн. %, получены соответственно для пиролизной смолы, ацетилена и суммы пропина с пропадиеном, выход которой составляет 0.5–0.7 мас. %. В табл. 1 приведены полученные коэффициенты aqi моделей для целевых продуктов пиролиза – этилена, пропилена, бутадиена и бензола.
Таблица 1.
Коэффициенты математической модели выхода основных продуктов
Этилен | |||
a1 = 20.3810 | a2 = 1.6239 | a3 = 178.3526 | a4 = –31.6989 |
a5 = 7.7732 | a6 = 111.3322 | a7 = –10.5657 | a8 = 1182.0275 |
a9 = –7.5857 | a10 = –428.5813 | a11 = 14.8222 | a12 = –199.3399 |
Пропилен | |||
a1 = 255.8471 | a2 = 1.6153 | a3 = 78.6966 | a4 = –32.7128 |
a5 = 6.6845 | a6 = 10.0 | a7 = 2244.8213 | a8 = –102.5539 |
a9 = 34.6640 | a10 = –682.6153 | a11 = 0.2483 | a12 = –453.2543 |
a13 = –55.9916 | a14 = 21.2514 | ||
Бутадиен | |||
a1 = -555.2265 | a2 = 0.02158 | a3 = 78.5815 | a4 = –336.0991 |
a5 = 177.7355 | a6 = –1.4691 | a7 = 3613.8265 | a8 = –976.4193 |
a9 = –0.5831 | a10 = –5274.3245 | a11 = 0.1338 | a12 = 19111.308 |
a13 = 250.4853 | a14 = 4.1395 | a15 = 7737.2557 | a16 = 232.3183 |
Бензол | |||
a1 = –11.9139 | a2 = 10.0 | a3 = 32.2360 | a4 = –419.2141 |
a5 = 0.06217 | a6 = –1.6853 | a7 = –1415.9462 | a8 = 50.1048 |
a9 = 16.0764 | a10 = 53.577 | a11 = 1178.2109 | a12 = 0.4785 |
a13 = 67.7981 |
При оптимизации режима печи были исследованы 2 вида прямогонного бензина, поступающего на пиролиз: относительно легкий и более тяжелый, имеющие следующие физические характеристики, зафиксированные на действующем крупнотоннажном производстве в разные моменты времени:
1) “Легкий” бензин: $d_{4}^{{20}}$ = 0.706; tNK = 45°С; t10 = 64°С; t30 = 80°С; t50 = 95°С; t70 = 110°С; t90 = = 130°С; tKK = 162°С.
2) “Тяжелый” бензин: $d_{4}^{{20}}$ = 0,72; tNK = 45°С; t10 = = 72°С; t30 = 95°С; t50 = 113°С; t70 = 131°С; t90 = = 155°С; tKK = 180°С.
Коэффициенты извлечения товарных продуктов в отделении их разделения определяются из материального баланса производства [20, 21] и приняты равными: k1 = 0.33; k2 = 0.98; k4 = 1; k5 = 1.01; k7 = = 0.98; k8 = 0.93; k9 = 0.94; k10 = 0.95; k11 = 0.95; k12 = 0.95; k13 = 0.95; k14 = 0.99. Коэффициент извлечения для водорода равный 0.33 показывает, что только третья часть водорода выпускается в виде товарной продукции. Остальные 2/3 расходуется на собственные нужды в реакторах гидрирования и в виде топлива в печах. Коэффициент k5 для этана больше 1 потому, что часть его образуется из этилена при гидрировании этан-этиленовой фракции (ЭЭФ). Потери этилена при гидрировании ЭЭФ и разделении этана и этилена приняты равными его приросту при гидрировании ацетилена.
Принятые условные цены товарных продуктов:
Ц1 = 450 у.е./т; Ц2 = 70 у.е./т; Ц4 = 330 у.е./т; Ц5 = 150 у.е./т; Ц7 = 180 у.е./т; Ц8 = 170 у.е./т; Ц9 = 150 у.е./т; Ц10 = 150 у.е./т; Ц11 = 210 у.е./т; Ц12 = 210 у.е./т; Ц13 = 210 у.е./т; Ц14 = 70 у.е./т; ЦS = 140 у.е./т.
Ограничения на независимые переменные:
$F_{{\text{S}}}^{{\min }}$ = 36 т/ч; $F_{{\text{S}}}^{{\max }}$ = 38 т/ч; f min = 0.58; f max = = 0.62; T min = 820°С; T max = 862°С; $P_{0}^{{\min }}$ ≥ 0.15 МПа.
Ограничения, накладываемые последующими технологическими узлами:$R_{{{\text{PF}}}}^{*} = 30.22$ $\frac{{{\text{т/ч}}}}{{{\text{1 печь}}}}$; $R_{{{\text{PC}}}}^{{\max }}$ = 1.335 $\frac{{{\text{т - моль/ч}}}}{{{\text{1 печь}}}}$; $R_{{{\text{PC}}}}^{{\min }}$ = 0.95 $\frac{{{\text{т - моль/ч}}}}{{{\text{1 печь}}}}$; $R_{{\text{Е}}}^{*} = 7.25$ $\frac{{{\text{т/ч}}}}{{{\text{1 печь}}}}$; $R_{{\text{P}}}^{*}$ = 18.0 $\frac{{{\text{т/ч}}}}{{{\text{1 печь}}}}$; $R_{{{\text{AC}}}}^{*}$ = 0.55 $\frac{{{\text{т/ч}}}}{{{\text{1 печь}}}}$; $R_{{{\text{MAC}}}}^{*} = 0.55$ $\frac{{{\text{т/ч}}}}{{{\text{1 печь}}}}$; $R_{{{\text{EE}}}}^{*} = 12.5$ $\frac{{{\text{т/ч}}}}{{{\text{1 печь}}}}$; $R_{{{\text{PP}}}}^{*}$ = = 30.22 $\frac{{{\text{т/ч}}}}{{{\text{1 печь}}}}$.
Задание на выработку этилена одной печью равно $G_{4}^{*} = 10.45$ и 9.68 $\frac{{{\text{т/ч}}}}{{{\text{1 печь}}}}$.
Решение оптимизационных задач было реализовано на ПЭВМ с процессором Intel i3-3110m, время расчета варьировалось в пределах от 30 до 60 с в зависимости от постановки задачи и заданных начальных значений управляющих воздействий. Критерием окончания поиска служило отсутствие изменения величины целевой функции при размере шага 10–6. Целевая функция формировалась в виде суммы критерия и штрафных функций, накладываемых ограничениями типа равенства и неравенств. В методе Хука–Дживса реализована автоматическая генерация направления поиска и увеличение размера шага при положительной тенденции уменьшения целевой функции.
В табл. 2 и 3 представлены сравнительные результаты оптимизации этиленовой установки при работе соответственно на “легком” (табл. 2) и “тяжелом” бензине (табл. 3). При работе печи по технологическому регламенту (табл. 2) прибыль равна 1092.75 $\frac{{{\text{у}}{\text{.е}}{\text{./ч}}}}{{{\text{1 печь}}}}$, расходная норма по сырью 1.791, не выполняется задание, равное 10.45 $\frac{{{\text{т/ч}}}}{{{\text{1 печь}}}}$, на выпуск этилена, не обеспечивается в должной мере безопасность компрессора по давлению на его входе. При оптимизации процесса таких проблем не возникает. Полученная прибыль, равная 1143.07 $\frac{{{\text{у}}{\text{.е}}{\text{./ч}}}}{{{\text{1 печь}}}}$, больше “регламентной”, а расходная норма 1.787 по бензину меньше. При работе по технологическому регламенту на более тяжелом бензине (табл. 3) не выполняется ограничение на выработку этилена (вырабатывается только 9.68 $\frac{{{\text{т/ч}}}}{{{\text{1 печь}}}}$ вместо задания 10.45 $\frac{{{\text{т/ч}}}}{{{\text{1 печь}}}}$). При оптимизации печи показатели по прибыли и расходной норме сравнимы с регламентными показателями (оптимальные 935.02 $\frac{{{\text{у}}{\text{.е}}{\text{./ч}}}}{{{\text{1 печь}}}}$ и 1.8362; регламентные 937.85 $\frac{{{\text{у}}{\text{.е}}{\text{./ч}}}}{{{\text{1 печь}}}}$ и 1.74), задание на выпуск этилена, равное 10.45 $\frac{{{\text{т/ч}}}}{{{\text{1 печь}}}}$, выполняется. В двух последних колонках табл. 3 показаны результаты оптимизации печи при задании на выпуск этилена 9.68 $\frac{{{\text{т/ч}}}}{{{\text{1 печь}}}}$. При обоих критериях оптимизации ее результаты превышают показатели пиролиза по регламенту, особенно по прибыли: 974.63 $\frac{{{\text{у}}{\text{.е}}{\text{./ч}}}}{{{\text{1 печь}}}}$ против 937.85 и 1.737 против 1.74.
Таблица 2.
Результаты оптимизации этиленовой установки, сырье – “легкий бензин"
Наименование | Пиролиз по технологическому регламенту |
Оптимизация по критерию | |
---|---|---|---|
Прибыль | Расходная норма | ||
Температура на выходе печи, °C | 850 | 861.8 | 860.4 |
Расход сырья в печь, т/ч | 37 | 36 | 36.11 |
Соотношение пар/бензин, т/т | 0.6 | 0.607 | 0.604 |
Состав пирогаза, мас. %: | |||
H2 | 1.22 | 1.24 | 1.24 |
CH4 | 15.16 | 16.04 | 16.05 |
C2H4 | 27.88 | 29.03 | 28.94 |
C2H6 | 4.06 | 4.13 | 4.12 |
C3H6 | 13.63 | 12.03 | 12.13 |
C4H6 | 4.74 | 4.96 | 4.82 |
C4H8 | 2.47 | 2.04 | 2.07 |
C6H6 | 11.05 | 11.00 | 10.9 |
C7H8 | 3.54 | 3.10 | 3.19 |
C5–C9 | 4.71 | 4.05 | 3.95 |
C8H10 | 4.53 | 3.99 | 4.09 |
C200 | 4.76 | 6.18 | 6.05 |
C2H2 | 0.8 | 1.04 | 1.01 |
C3H4 | 0.74 | 0.7 | 0.73 |
P0, МПа | 0.14 | 0.15 | 0.15 |
Полученная прибыль, ${\text{у}}{\text{.е}}{\text{.}} \times {{{{{\text{ч}}}^{{ - 1}}}} \mathord{\left/ {\vphantom {{{{{\text{ч}}}^{{ - 1}}}} {\text{1}}}} \right. \kern-0em} {\text{1}}}{\text{ печь}}$ | 1092.75 | 1143.07 | – |
Расходная норма по сырью, т/т | 1.791 | – | 1.7869 |
Выработка этилена, ${\text{т}} \times {{{{{\text{ч}}}^{{ - 1}}}} \mathord{\left/ {\vphantom {{{{{\text{ч}}}^{{ - 1}}}} {\text{1}}}} \right. \kern-0em} {\text{1}}}{\text{ печь}}$ | 10.32 | 10.45 | 10.45 |
Таблица 3.
Результаты оптимизации этиленовой установки, сырье – “тяжелый бензин”
Наименование | Пиролиз по технологи-ческому регламенту |
Задание по этилену
10.45 т × ч–1/1 печь. Оптимизация по критерию |
Задание по этилену
9.68 т × ч–1/1 печь. Оптимизация по критерию |
||
---|---|---|---|---|---|
прибыль | расходная норма | прибыль | расходная норма | ||
Температура на выходе печи, °C | 850 | 862 | 862 | 862 | 859.92 |
Расход сырья в печь, т/ч | 37 | 37.61 | 37.61 | 36.19 | 36.287 |
Соотношение пар/бензин, т/т | 0.6 | 0.583 | 0.583 | 0.612 | 0.61 |
Состав пирогаза, мас. %: | |||||
H2 | 1.13 | 1.04 | 1.04 | 1.12 | 1.13 |
CH4 | 14.1 | 16.76 | 16.76 | 14.69 | 14.65 |
C2H4 | 26.17 | 27.79 | 27.79 | 26.75 | 26.68 |
C2H6 | 4.18 | 4.09 | 4.09 | 4.24 | 4.23 |
C3H6 | 14.91 | 12.43 | 12.43 | 13.94 | 14.07 |
C4H6 | 5.43 | 4.14 | 4.14 | 5.64 | 5.56 |
C4H8 | 3.07 | 1.9 | 1.9 | 2.72 | 2.78 |
C6H6 | 12.26 | 11.2 | 11.2 | 12.64 | 12.56 |
C7H8 | 3.34 | 3.58 | 3.58 | 2.86 | 2.94 |
C5-C9 | 5.6 | 3.38 | 3.38 | 6.11 | 5.96 |
C8H10 | 2.9 | 3.08 | 3.08 | 1.92 | 2.11 |
C200 | 5.07 | 6.15 | 6.15 | 6.15 | 5.99 |
C2H2 | 1.1 | 1.32 | 1.32 | 1.34 | 1.3 |
C3H4 | 0.59 | 0.78 | 0.78 | 0.47 | 0.5 |
P0, МПа | 0.148 | 0.15 | 0.15 | 0.15 | 0.15 |
Полученная прибыль, у.е. × ч–1/1 печь | 937.85 | 935.02 | – | 974.63 | – |
Расходная норма по сырью, т/т | 1.7399 | – | 1.8362 | – | 1.737 |
Выработка этилена, т × ч–1/1 печь | 9.68 | 10.45 | 10.45 | 9.68 | 9.68 |
Полученные результаты доказывают эффективность и целесообразность оптимизации процесса пиролиза и необходимость учитывать физические свойства прямогонного бензина при управлении процессом пиролиза на крупнотоннажных этиленовых установках, что позволяет сделать разработанная оптимизационная модель, так как составы пирогаза при крекинге этих бензинов ощутимо отличаются друг от друга.
ЗАКЛЮЧЕНИЕ
Разработана математическая модель для управления в реальном времени процессом пиролиза бензинового сырья в печи большой единичной мощности, учитывающая физические характеристики пиролизуемого сырья. На основе модели поставлена и решена задача оптимизации крупнотоннажной пиролизной печи, в которой учитываются ограничения, накладываемые на пиролиз последующими узлами производства. Предложенный подход к оптимизации печей SRT-VI может быть использован при управлении аналогичными производствами с другими печами, работающими на бензиновом сырье. При этом формулы (3)–(20), (26)–(29) остаются без изменений, а (21)–(25), (30) корректируются исходя из конструкции, состояния и количества змеевиков в печи. Структура моделей (31)–(35) остается без изменений, а параметры A подлежат корректировке. Оптимизационная модель реализуется в составе АСУТП и срабатывает 1 раз в смену после обновления информации о физических свойствах перерабатываемого бензина. Из проведенного исследования следует вывод о неэффективности пиролиза прямогонного бензина непосредственно из “трубы” поставщика и необходимости подготовки сырья в промежуточных емкостях (рис. 1) с перемешиванием и регламентным анализом плотности бензина и разгонки по Энглеру, которые затем используются для расчета химических характеристик сырья.
ОБОЗНАЧЕНИЯ
A | температура выкипания 50 об. % бензина, ° Ренкина |
A | вектор коэффициентов модели |
a | регрессионные коэффициенты, полученные для каждого из 14 продуктов |
B | выход продукта пиролиза, мас. % |
BMCI | индекс ароматичности бензина |
C | концентрация, масс. % |
d | относительная плотность бензина |
F | расход, т/ч |
f | соотношение пар/бензин, т/т |
G | выработка продукта, т |
I | количество извлекаемых продуктов пиролиза |
J | количество затрат |
Kw | показатель парафинистости сырья (фактор Уотсона) |
KSF | кинетический фактор жесткости |
k | коэффициент |
L | количество целевых продуктов |
M | средняя молекулярная масса бензина |
N | количество продуктов, атомов углерода |
Ng | количество продуктов, поступающих на переработку в g-й узел |
P | среднее значение абсолютного давления пирогаза, МПа |
ΔP | потери давления, МПа |
PMS | параметр молекулярных столкновений |
R | нагрузка, $\frac{{{\text{т - моль/ч}}}}{{{\text{1 печь}}}}$ или $\frac{{{\text{т/ч}}}}{{{\text{1 печь}}}}$ |
T | температура на выходе из печи, K |
t | температура пирогаза на выходе из печи, °C |
X | конверсия бензина |
Z | производственные затраты |
Ц | цена продукта или сырья, у.е./т |
Э | экономический эффект, руб. |
$\eta $ | отношение чисел атомов углерода и водорода в бензине |
$\psi $ | функция |
ИНДЕКСЫ
0 | вход пирогазового компрессора |
4; 15,6; 20 | индексы, указывающие на температуру при расчете плотности |
AC | гидрирование ацетилена |
C | атомы углерода |
DP | перепад давления |
E | этиленовый холодильный цикл |
EE | этан-этиленовая колонна |
ex | экспериментальное значение |
g | узел цеха разделения продуктов |
H2 | водород |
i | продукт пиролиза: |
i = 1 | водород |
i = 2 | метан |
i = 3 | ацетилен |
i = 4 | этилен |
i = 5 | этан |
i = 6 | пропин с пропадиеном |
i = 7 | пропилен |
i = 8 | бутадиен |
i = 9 | изобутилены |
i = 10 | сумма неароматических углеводородов C5–C8 |
i = 11 | бензол |
i = 12 | толуол |
i = 1 | сумма этилбензола, стирола, ксилолов и ароматических углеводородов C9–C12 |
i = 14 | пиролизная смола |
j | вид производственных затрат |
KK | конец кипения |
l | целевой продукт |
M | формула расчета молекулярной массы |
MAC | гидрирование пропина и пропадиена |
max | максимальное значение |
min | минимальное значение |
NK | начало кипения |
n | номер эксперимента критерии идентификации модели; |
P | пропиленовый холодильный цикл |
PC | пирогазовый компрессор |
PF | первичное фракционирование пирогаза |
PP | парциальное давление |
PP | пропан-пропиленовая колонна |
Q | приведение размерностей при расчете времени контакта |
QK | время контакта на выходе из радиантной зоны |
QN | время контакта на входе в радиантную зону |
среднее время пребывания сырья в реакционной зоне | |
q | номер коэффициента aq в модели выхода i-го продукта, q = 1–16 |
R | градусы Ренкина, °R |
RAS | расширение сырья |
RN | расходная норма |
RS | фактор состава сырья по Расторгуеву |
S | сырье |
TRE | отношение скоростей отрыва третичного и первичного атомов водорода в молекуле сырья |
V | среднее значение |
w | фактор Уотсона |
вх | вход в радиантную часть змеевика |
вых | на выходе печи |
ЗИА | закалочно-испарительный аппарат |
$\sum {{{{\text{H}}}_{2}}} $ | суммарная концентрация атомов водорода |
* | заданное значение |
Список литературы
Жагфаров Ф.Г., Геяси П.А.Ф. Современное состояние производства этилена // Булатовские чтения. Материалы II Международной научно-практической конференции (31 марта 2018 г.): в 7 т. Т. 5: Химическая технология и экология в нефтяной и газовой промышленности: сборник статей / Под общ. ред. О.В. Савенок. Краснодар: Изд. Дом-Юг, 2018. С. 88.
Шевченко И.Ю. Управление сложным нефтехимическим промышленным производством на основе математического моделирования и современных информационных технологий // Вестн. Алтай. гос. аграр. унив. 2014. Т. 122. № 12. С. 146.
Зеленко И.Ю. Разработка моделирующей системы процесса пиролиза углеводородов. Автореф. дис. … канд. техн. наук. Томск: Томский политехнический университет, 1999.
Прозорова О.Б. Совершенствование производства этилена в ОАО “Салаватнефтеоргсинтез”. Автореф. дис. … канд. техн. наук. Уфа: Уфимский государственный нефтяной технический университет, 2011.
Jarullah A.T., Hameed S.A., Hameed Z.A., Mujtaba I.M. Optimal operation of a pyrolysis reactor // Proc. 12th International Symposium on Process Systems Engineering and 25th European Symposium on Computer Aided Process Engineering (Elsevier Series in Computer Aided Chemical Engineering. V. 37) / Eds. Gernaey K.V., Huusom J.K., Gani R. Amsterdam: Elsevier, 2015. P. 827.
Berreni M., Wang M. Modelling and dynamic optimization of thermal cracking of propane for ethylene manufacturing // Comput. Chem. Eng. 2011. V. 35. № 14. P. 2876.
Marcos J.M.M. Modelling of naphtha cracking for olefins production. MS Thesis. Tecnico Lisboa, 2016.
Ziarifar E., Fakhrhoseini S.M., Chiassi M. Optimization of Coil Outlet Temperature for Producing Maximum Products in an Olefin Furnace // Pet. Sci. Technol. 2013. V. 31. P. 596. https://doi.org/10.1080/10916466.2011.586957
Borralho F.J.O. Detailed modeling and optimization of an ethylene plant. MS Thesis. Tecnico Lisboa, 2013.
Журавлева И.А., Кутуева А.В., Доломатов М.Ю., Быстров А.И. Алгоритм программы оптимизации технологического процесса пиролиза многокомпонентных углеводородных систем с целью достижения максимального выхода целевого // Электротех. инф. комплексы сист. 2017. Т. 13. № 3. С. 56.
Мамедов З.А. Оптимизация безрециркуляционного процесса пиролиза этана с бутан-изобутиленовой фракцией в промышленной печи // Вестн. Пермск. нац. исслед. политех. унив. Хим. технол. биотехнол. 2018. № 1. С. 77.
Гартман Т.Н., Советин Ф.С., Подсекина Ю.И., Швец В.Ф., Козловский Р.А., Сапунов В.Н. Кинетическое моделирование процесса инициированного крекинга гудрона // Теор. осн. хим. технол. 2018. Т. 52. № 1. С. 60.
Арапов Д.В., Тихомиров С.Г., Подвальный С.Л., Курицын В.А., Карманова О.В. Математическое моделирование промышленных процессов пиролиза бензина в трубчатых печах // Теор. осн. хим. технол. 2018. Т. 52. № 6. С. 649.
Cowperthwaite E.V. Mathematical model for ethane pyrolysis in an industrial furnace. MS Thesis. Kingston, Canada: Queen’s University, 2014.
Yan M. Simulation and optimization of an ethylene plant. MS Thesis. Texas Tech University, 2000.
Haghighi S.S., Rahimpour M.R., Raeissi S., Dehghani O. Investigation of ethylene production in naphtha thermal cracking plant in presence of steam and carbon dioxide // Chem. Eng. J. 2013. V. 228. P. 1158.
Kuritsyn V.A., Arapov D.V., Ekimova A.M., Yakupov A.A. Modeling of pyrolysis of straight-run naphtha in a large-capacity type SRT-VI furnace // Chem. Technol. Fuels Oils. 2008. V. 44. № 3. P. 180. [Курицын В.А., Арапов Д.В., Екимова А.М., Якупов А.А. Моделирование процесса пиролиза прямогонного бензина в крупнотоннажной печи типа SRT-VISIT // Хим. технол. топл. масел. 2008. № 3. С. 37.]
Kuritsyn V.A., Arapov D.V., Gorilchenko R.L. Optimization of circulation water cooling process in forced-draft towers // Chem. Technol. Fuels Oils. 2012. V. 48. № 2. P. 97. [Курицын В.А., Арапов Д.В., Горильченко Р.Л. Оптимизация процесса охлаждения циркуляционной воды в градирнях с искусственной тягой // Хим. технол. топл. масел. 2012. № 2. С. 12.]
Степанов А.В. Производство низших олефинов. Киев: Наукова думка, 1978.
Тучинский М.Р., Родных Ю.В. Автоматизированные системы управления производством олефинов. М.: Химия, 1985.
Мухина Т.Н., Барабанов Н.Л., Бабаш С.Е., Меньщиков В.А., Аврех Г.Л. Пиролиз углеводородного сырья. М.: Химия, 1987.
Гориславец С.П., Тменов Д.Н., Майоров В.И. Пиролиз углеводородного сырья. Киев: Наукова думка, 1977.
Расчеты основных процессов и аппаратов нефтепереработки: справочник / Под ред. Судакова Е.Н. М.: Химия, 1979.
Рудин М.Г., Драбкин А.Е. Краткий справочник нефтепереработчика. Л.: Химия, 1980.
Arapov D.V., Tikhomirov S.G., Chertov E.D., Khaustov I.A., Kudryashov V.S., Saiko D.S. Determination of parameters assigned to an anti-surge controller in a turbocompressor automation system // Chem. Pet. Eng. 2018. V. 53. № 9–10. P. 653. [Арапов Д.В., Тихомиров С.Г., Чертов Е.Д., Хаустов И.А., Кудряшов В.С., Сайко Д.С. Определение параметров, задаваемых антипомпажному регулятору в системе автоматизации турбокомпрессора // Хим. нефтегазов. машиностр. 2017. № 10. С. 13.]
Дополнительные материалы отсутствуют.
Инструменты
Теоретические основы химической технологии