Теоретические основы химической технологии, 2020, T. 54, № 3, стр. 376-382
Получение чистых изобутана и изобутилена в технологической системе с рециркуляционными узлами
Ч. Ш. Ибрагимов a, С. Н. Гулиева a, *
a Азербайджанский государственный университет нефти и промышленности
Баку, Азербайджанская Республика
* E-mail: raoztun@mail.ru
Поступила в редакцию 05.06.2018
После доработки 15.10.2019
Принята к публикации 22.10.2019
Аннотация
Приведены результаты разработки теоретических основ получения высокочистых изобутана и изобутилена из изобутан-изобутиленовой фракции пиролизного газа. В экспериментальной части предложен метод повышения чистоты фракций изобутана и изобутилена, выделенных с помощью серной кислоты из изобутан-изобутиленовой фракции пиролизного газа. При этом предложено добавить две адсорбционные установки в заводскую технологическую схему выделения изобутана и изобутилена из фракции С4 пиролизного газа. Разработана математическая модель процессов получения чистых изобутилена и изобутана с учетом принципов теории рециркуляции.
ВВЕДЕНИЕ
Производство и потребление изобутилена, изобутана, н-бутиленов, ароматических углеводородов непрерывно возрастает [1]. Изобутан, изобутилен, ароматические углеводороды являются важнейшими источниками сырья для химической и нефтехимической промышленности. Чистота этих продуктов требуется в производстве других продуктов, получаемых на их основе. Например, высокая чистота изобутилена требуется в производстве бутилкаучука, в том числе на основе бензола вырабатываются полупродукты для получения каучуков, пластмасс, полиэфирных смол, присадок к смазочным маслам. Основное количество бензола потребляется в производстве стирола, фенола, циклогексана [2–9].
Извлечение изобутана и изобутилена из смеси углеводородов фракции С4 пиролизного газа осуществляется серной кислотой с последующей доочисткой изобутановой фракции от изобутилена адсорбцией активированным углем АР-3, а изобутиленовой фракции доочисткой от н-бутиленов адсорбцией с помощью цеолита марки СаА. Эти процессы осуществляются на установке, содержащей последовательно расположенные две поглотительные системы 11 и 12, установленные соответственно на выходе изобутановой и изобутиленовой фракций (рис. 1) [3].
Рис. 1.
Технологическая схема модифицированной установки получения изобутана и изобутилена высокой чистоты: 1 – склад изобутан-изобутиленовой фракции; 2, 3, 10, 14 – насосы; 4, 5 – реакторы-отстойники; 6, 7 – холодильники; 8 – сборник; 9 – емкость; 11, 12 – адсорберы; 13, 15, 18 – колонны; 16 – конденсатор; 17 – отстойник; 19 – емкость изобутановой фракции; 20 – емкость изобутиленовой фракции.
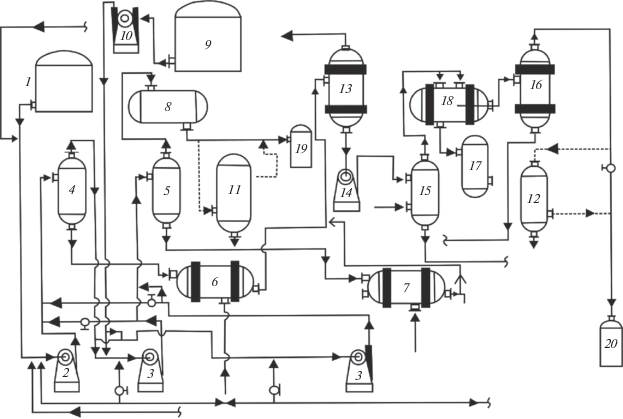
Состав изобутан-изобутиленовой фракции С4 пирогаза, поступающей на выделение изобутилена и изобутана, приведен в табл. 1.
Таблица 1.
Состав изобутан-изобутиленовой фракции пирогаза
Наименование | Молекулярный вес | Количество, кг/ч |
Концентрация, мас. % | Количество, моль/ч |
Концентрация, мол. % |
---|---|---|---|---|---|
С3 | 44 | 40 | 0.4 | 0.91 | 0.5 |
Изобутилен | 56 | 4713 | 44.1 | 84.2 | 44.8 |
Н-бутилены | 56 | 383 | 3.6 | 6.84 | 3.7 |
Изобутан | 58 | 5339 | 49.9 | 92.9 | 49.1 |
Н-бутан | 58 | 189 | 1.8 | 3.26 | 1.7 |
С5 и выше | 72 | 21 | 0.2 | 0.29 | 0.2 |
Из емкости 1 изобутан-изобутиленовая фракция и серная кислота из колонны 15 подаются через насос 2 в отстойник-реактор 4, из него в отстойник-реактор 5, а оттуда в сборник 8. Свежая серная кислота из емкости 9 подается в отстойник-реактор 5. Изобутановая фракция из сборника 8 подается в емкость 19. Чтобы получить изобутан высокой чистоты, на выходе сборника 8 изобутановой фракции установлен блок адсорбции 11 для очистки изобутановой фракции от изобутилена. Насыщенная изобутиленом серная кислота направляется в колонну 13 для выделения содержащегося в ней изобутилена-рецикла. Из колонны 13 отдувка возвращается в виде рецикла в смесительный насос 2 на поглощение серной кислотой изобутилена. Остальную часть отдувки составляют н-бутилены. Из куба колонны 13 насыщенная серная кислота после дегазации подается на гидролиз в колонну 15. Сверху этой колонны отгоняется изобутилен, триметилкарбинол, полимеры и часть воды, а из куба выводятся разбавленная до 40% серная кислота и вода. Отгоняемые сверху пары поступают в конденсатор 16, охлаждаемый водой, где конденсируются триметилкарбинол, полимеры и вода. Конденсат поступает в отстойник 17, а нескоденсировавшийся изобутилен поступает в компрессор. Компримированный изобутилен подается в колонну 18, предназначенную для получения изобутилена-ректификата. Изобутиленовая фракция из колонны 18 собирается в емкость 20. Кубовая жидкость из колонны 18, содержащая изобутилен и полимеры, возвращается в виде рецикла в смесительный насос 2 на поглощение серной кислотой.
Сущность разработанного метода заключается в очистке адсорбцией изобутановой фракции от изобутилена активированным углем АР-3, а изобутиленовой фракции от н-бутиленов цеолитом СаА с использованием блоков адсорбции 11 и 12, установленных соответственно на выходе аппаратов, для получения изобутановой и изобутиленовой фракций. Это позволяет увеличить степень извлечения изобутана и изобутилена из смеси углеводородов фракции С4 пиролизного газа до 99.9%.
Непрореагировавшая часть сырья выделяется из продукта реакции и направляется в поток свежей загрузки, которая идет в реакторы. Процессы рециркуляции идут в колоннах 13, 15, 18. Рециркуляты поступают через насосы 2 и 3 к свежему составу сырья на повторное поглощение серной кислотой, в результате чего достигается максимальное превращение реагирующих веществ [8].
Основной целью работы является исследование процессов, осуществляемых в рециркуляционных узлах данной системы. При этом используются принципы теории рециркуляции, поскольку, как видно из технологической схемы, процессы осложняются многочисленными рециркуляционными потоками.
Поскольку процессы извлечения целевых компонентов связаны многочисленными рециркуляционными потоками, то при разработке модели всей системы применены также принципы теории рециркуляции [4–6].
ОСНОВНАЯ ЧАСТЬ
Загрузка реактора материальными потоками каждого компонента $j$ фракции пирогаза, вступающими в реакцию, определяется формулами, выведенными с учетом следующих условий.
В период пуска или изменения режима работы системы, работающей с обратной связью рециркуляции непрерывной части сырья, в течение определенного времени она работает в неустановившемся режиме, поскольку количество рециркуляции непрореагировавшей части изобутана и изобутилена меняется.
Загрузка реактора, когда расход свежего сырья (${{g}_{{oj}}}$) по компоненту $j$ является постоянным и к нему добавляется непрореагировавшая часть сырья в виде рециркулята, определяется по формуле
(1)
$\frac{{{{g}_{{ij}}}}}{t} = \frac{{1 - a_{j}^{i}}}{{1 - {{a}_{j}}}}{{g}_{{oj}}}\,\,\,\,\left[ {{\text{кг/с}}} \right],$При установившемся состоянии, т.е. при $i \to \infty ,$ загрузка реактора по компоненту $j$ свежим сырьем и собственным рециркулятом имеет вид
(2)
${{g}_{j}} = \frac{{{{g}_{{ij}}}}}{t} = \frac{1}{{1 - {{\alpha }_{i}}}}{{g}_{{oj}}}\,\,\left[ {{{{\text{кг}}} \mathord{\left/ {\vphantom {{{\text{кг}}} {\text{c}}}} \right. \kern-0em} {\text{c}}}} \right].$Здесь ${1 \mathord{\left/ {\vphantom {1 {\left( {1 - {{\alpha }_{i}}} \right)}}} \right. \kern-0em} {\left( {1 - {{\alpha }_{i}}} \right)}} = {{K}_{{Rj}}}$ – коэффициент рециркуляции, который характеризует степень превращения целевого компонента (физически означает кратность пребывания всех частей данной порции сырья в зоне реакции).
В общем случае загрузка (2) величина переменная, так как ${{\alpha }_{j}}\left( t \right)$ в зависимости от скорости реакции меняется, т.е. является функцией кинетики процесса. Для упрощения решения сложных задач часто применяется $\alpha = {\text{const}}{\text{.}}$
Надо отметить, что разделение собственного рециркулята от продукта реакции может осуществляться по частям в разных аппаратах и разными методами (экстракцией, гидролизом, адсорбцией, ректификацией). В этом случае
где $n$ – номер аппарата, откуда рециркулируется целевой компонент.Очевидно, что выход реактора по целевому компоненту состоит из двух слагаемых
где ${{g}_{{{\alpha }j}}}$ – количество продукта реакции, кг/с; ${{g}_{{Rj}}}$ – количество рециркулята, кг/с.Количества ${{g}_{{aj}}}$ и ${{g}_{{Rj}}}$ зависят от физико-химических условий реактора, которые отражаются на коэффициенте разделения ${{\alpha }_{j}}$ и коэффициенте рециркуляции ${{K}_{{Rj}}}.$
Если ${{g}_{{aj}}}$ и ${{g}_{{Rj}}}$ выразить через параметры реактора, то при установившемся состоянии получим
(5)
${{g}_{{aj}}} = {{g}_{{oj}}},\,\,\,\,{{g}_{{Rj}}} = \frac{{{{\alpha }_{j}}}}{{1 - {{\alpha }_{j}}}}{{g}_{{oj}}}.$С другой стороны, чтобы непрореагировавшая часть сырья стала рециркулятом, она должна пройти через аппараты разделения продукта реакции от рециркулята. Следовательно, рециркулят зависит также и от параметров разделительного аппарата. Учитывая это, для рециркулята получена следующая формула [7]:
(6)
${{g}_{{Rj}}} = \frac{{{{g}_{{0j}}}}}{{1 - {{\alpha }_{j}}}}\left( {C_{j}^{0} - {{C}_{j}}} \right)\,\,\,\,\left[ {{\text{кг/с}}} \right],$Тогда для общего материального выхода реактора получим уравнение, которое включает параметры и реактора, и разделительного аппарата:
(7)
${{g}_{j}} = {{g}_{{0j}}} + {{g}_{{Rj}}} = \left( {1 + \frac{{C_{j}^{0} - {{C}_{j}}}}{{1 - {{\alpha }_{j}}}}} \right){{g}_{{oj}}}\,\,\,\,\left[ {{\text{кг/с}}} \right].$Формулы (1)–(7) выведены для тех случаев, когда в реактор поступает свежая загрузка и собственный рециркулят. В более общем виде материальная загрузка реактора состоит из свежей загрузки, собственного рециркулята и свежей загрузки вещества $j,$ поступающего из других аппаратов, и выражается уравнением вида
(8)
${{g}_{{{\nu }j}}} = \left( {1 + \frac{{C_{{R{\nu }j}}^{0} - {{C}_{{R{\nu }j}}}}}{{1 - {{a}_{{R{\nu }j}}}}}} \right)\left( {{{g}_{{{\nu }oj}}} + \sum\limits_k {{{g}_{{k{\nu }}}}} } \right)\,\,\,\,\left[ {{\text{кг/с}}} \right],$Прежде чем войти в назначенные аппараты (разделительные, реакторные и т.д.) материальные потоки проходят через теплообменники, где приобретают температуру аппарата, куда направляется поток. В этом случае формулы обменного количества тепла будут следующими:
1) для общей загрузки
(9)
$\begin{gathered} {{q}_{{{\nu }j}}} = \left( {1 + \frac{{C_{{R{\nu }j}}^{0} - {{C}_{{R{\nu }j}}}}}{{1 - {{\alpha }_{{R{\nu }}}}}}} \right)\left( {{{g}_{{{\nu }oj}}} + \sum\limits_k {{{g}_{{k{\nu }}}}} } \right) \times \\ \times \,\,{{c}_{j}}\left( {{{T}_{{\delta }}} - {{T}_{M}}} \right)\,\,\left[ {{\text{ккал/с}}} \right]; \\ \end{gathered} $2) для рециркулята
(10)
${{q}_{{Rj}}} = \frac{{{{g}_{{oj}}}}}{{1 - {{\alpha }_{j}}}}\left( {C_{j}^{0} - {{C}_{j}}} \right){{c}_{j}}\left( {{{T}_{{\delta }}} - {{T}_{M}}} \right)\,\,\left[ {{\text{ккал/с}}} \right];$3) для продукта реакции
(11)
${{q}_{{aj}}} = {{g}_{{aj}}}{{c}_{j}}\left( {{{T}_{{\delta }}} - {{T}_{M}}} \right)\,\,\left[ {{\text{ккал/с}}} \right];$4) для общего выхода реактора
(12)
${{q}_{j}} = \left( {1 + \frac{{C_{j}^{0} - {{C}_{j}}}}{{1 - {{\alpha }_{j}}}}} \right){{g}_{{oj}}}{{c}_{j}}\left( {{{T}_{{\delta }}} - {{T}_{M}}} \right)\,\,\left[ {{\text{ккал/с}}} \right],$Количество тепла, привнесенное в реактор потоком общей загрузки, имеет формулу
Количество второго реагента определяется экспериментально с учетом стехиометрии реагирующих веществ.
Загрузка реактора вторым реагентом определяется следующими формулами:
1) при общей загрузке реактора всеми потоками компонента $j$
2) в частном случае при загрузке реактора свежим сырьем и собственным рециркулятом компонента $j$
3) при загрузке реактора за счет рециркулята компонента $j$
Коэффициент $\gamma $ может быть больше, меньше или равен единице, который определяется экспериментально.
Прежде чем войти в назначенный аппарат потоки второго реагента, так же как и первого, проходят через теплообменники, где приобретают температуру аппарата, куда направляется поток. Тогда формулы обменного количества тепла будут следующими:
1) для общей загрузки реактора вторым реагентом
(17)
$q_{{{\nu }j}}^{'} = g_{{{\nu }j}}^{'}c_{j}^{'}\left( {{{T}_{{\delta }}} - {{T}_{M}}} \right)\,\,\left[ {{\text{ккал/с}}} \right],$2) для загрузки реактора вторым реагентом в том случае, когда реактор загружается свежим сырьем и собственным рециркулятом первого реагента
(18)
$q_{j}^{'} = g_{j}^{'}c_{j}^{'}\left( {{{T}_{{\delta }}} - {{T}_{M}}} \right)\,\,\left[ {{\text{ккал/с}}} \right],$3) для загрузки реактора рециркулятом второго реагента в том случае, когда реактор загружается рециркулятом первого реагента
(19)
$q_{{Rj}}^{'} = g_{{Rj}}^{'}c_{j}^{'}\left( {{{T}_{{\delta }}} - {{T}_{M}}} \right)\,\,\left[ {{\text{ккал/с}}} \right],$В разделительных колоннах продукт реакции отделяется от непрореагировавшей части целевого компонента фракции пирогаза, т.е. от рециркулята, который рециркулируется в реактор с целью повторного участия его в процессе реакции.
Разумеется, что в разделительную колонну поступает поток смеси продукта реакции с непрореагировавшей частью (рециркулятом) целевого компонента $j$ фракции пирогаза.
Следовательно, загрузка разделительной колонны материальным потоком целевого компонента будет иметь формулу, подобную или (1), или (7), или (8) (т.е. для конкретного процесса). Более общая формула загрузки разделительной колонны будет иметь следующий вид:
(20)
${{g}_{{{\nu }j}}} = \left( {1 + \frac{{C_{{R{\nu }j}}^{0} + {{C}_{{R{\nu }j}}}}}{{1 - {{\alpha }_{{R{\nu }j}}}}}} \right)\left( {{{g}_{{{\nu }oj}}} + \sum\limits_k {{{g}_{{k{\nu }}}}} } \right)\,\,\left[ {{\text{кг/с}}} \right].$Формулы обменного количества тепла будут соответственно в виде (9)–(12).
Количество поглотителя (или растворителя), необходимое для выделения рециркулята целевого компонента от продукта реакции, можно определить следующим образом (например, для абсорбционных, экстракционных, ионообменных и адсорбционных методов разделения).
Очевидно, что
(21)
${{g}_{{Rj}}} = {{G}_{j}}\left( {{{\alpha }_{j}} - {{\alpha }_{{nj}}}} \right)\,\,\left[ {{{{\text{кг}}} \mathord{\left/ {\vphantom {{{\text{кг}}} {\text{c}}}} \right. \kern-0em} {\text{c}}}} \right],$Учитывая (6), из (21) для количества поглотителя (растворителя) получим
(22)
${{G}_{j}} = \frac{{{{g}_{{oj}}}\left( {C_{j}^{0} - {{C}_{j}}} \right)}}{{(1 - {{\alpha }_{j}})({{\alpha }_{j}} - {{\alpha }_{{nj}}})}}\,\,\left[ {{{{\text{кг}}} \mathord{\left/ {\vphantom {{{\text{кг}}} {\text{c}}}} \right. \kern-0em} {\text{c}}}} \right].$Как видно, количество поглотителя рециркулята зависит от параметров как реакторного, так и поглотительного аппаратов.
Загрузка теплом аппарата разделения рециркулята от продукта реакции определяется нижеследующим образом.
В аппарат разделения рециркулята от продукта реакции поступают поглотитель, продукт реакции и рециркулят. Необходимо довести их температуру до требуемого для разделения уровня.
Следовательно, нагрев аппарата разделения продукта от рециркулята можно определить по следующему уравнению:
(23)
$\begin{gathered} {{q}_{{{\text{раз}}}}} = \left( {{{G}_{j}}{{G}_{o}} + \left( {{{g}_{{{\nu }aj}}} + {{g}_{{Rj}}}} \right){{c}_{j}}} \right) \times \\ \times \,\,\left( {{{T}_{{\delta }}} - {{T}_{M}}} \right)\,\,\left[ {{{{\text{ккал}}} \mathord{\left/ {\vphantom {{{\text{ккал}}} {\text{c}}}} \right. \kern-0em} {\text{c}}}} \right], \\ \end{gathered} $На основании полученных результатов составлена модель отдельных узлов системы разделения компонентов фракций пиролиза нефтяных углеводородов: загрузки реактора материальными и тепловыми потоками извлекаемого целевого компонента из фракции пирогаза, загрузки разделительной колонны материальными и тепловыми потоками, в том числе поглотителя рециркулята, процессов в реакторе и разделительной колонне, а также всего комплекса разделения компонентов фракций пиролиза нефтепродуктов.
В результате исследований процессов адсорбции из пиролизного газа остатков изобутилена, н-бутиленов и высших углеводородов решены следующие задачи для этих процессов: выбор адсорбентов, моделирование процессов, анализ экспериментального материала, расчеты параметров, определение оптимальных режимов.
В табл. 2 и 3 приведены экспериментальные и расчетные данные изотермы, кинетики, выхода адсорбции н-бутиленов на цеолите СаА и расчеты кинетических, диффузионных и изотермических параметров.
Таблица 2.
Изотермические, кинетические и выходные экспериментальные данные адсорбции н-бутиленов на цеолите СаА из смеси с изобутиленом при температуре 25°С
Ср, м3/м3 | ар, кг/100 кг | t, с | акин, кг/100 кг | Свых, м3/м3 |
---|---|---|---|---|
0.1 | 11.66 | 20 | 6.10 | 0.013 |
0.3 | 12.89 | 40 | 7.16 | 0.038 |
0.5 | 13.58 | 60 | 7.30 | 0.071 |
0.7 | 13.98 | 80 | 8.25 | 0.108 |
0.8 | 14.35 | 100 | 10.83 | 0.200 |
0.9 | 14.70 | 120 | 11.75 | 0.314 |
1.0 | 14.95 | 160 | 13.20 | 0.430 |
– | – | 180 | 13.50 | 0.602 |
– | – | 200 | 13.95 | 0.615 |
Таблица 3.
Результаты расчетов равновесных кинетических и диффузионных параметров процесса адсорбции н-бутиленов на цеолите СаА
t, с | βкин ×103, с–1 | ${{D}_{c}}$, м2/ч | ${{a}_{\infty }}$, кг/100 кг |
b, м3/м3 |
---|---|---|---|---|
40 | 6.80 | 2.90 | 15.01 | 80.97 |
60 | 5.95 | 2.02 | – | – |
80 | 3.00 | 1.40 | – | – |
85 | 2.95 | 0.99 | – | – |
90 | 2.70 | 0.65 | – | – |
95 | 3.55 | 0.58 | – | – |
105 | 2.91 | 0.42 | – | – |
115 | 2.01 | 0.35 | – | – |
125 | 1.97 | 0.28 | – | – |
135 | 1.50 | 0.15 | – | – |
145 | 1.20 | 0.14 | – | – |
155 | 1.20 | 0.14 | – | – |
В табл. 4 приведен экспериментальный материал изотермических, кинетических и выходных показателей адсорбции изобутилена на активированном угле АР-3. Максимальная адсорбция активированного угля марки АР-3 составляет 16 г на 100 г угля.
Таблица 4.
Экспериментальные данные адсорбции изобутилена на активированном угле марки АР-3 из смеси с изобутаном при температуре 25°С (равновесные, кинетические и выходные данные)
Изотерма адсорбции | t, с | акин, кг/100 кг | Свых, м3/м3 | |
---|---|---|---|---|
Ср, м3/м3 | ар, кг/100 кг | |||
0.1 | 14.52 | 20 | 8.15 | 0.015 |
0.2 | 15.75 | 40 | 9.22 | 0.040 |
0.4 | 14.60 | 60 | 9.55 | 0.075 |
0.6 | 15.35 | 80 | 10.46 | 0.115 |
0.8 | 15.90 | 100 | 12.65 | 0.210 |
0.9 | 16.15 | 120 | 13.36 | 0.350 |
1.0 | 16.05 | 160 | 13.50 | 0.460 |
Результаты расчетов параметров процесса адсорбции изобутилена приведены в табл. 5.
Таблица 5.
Результаты расчетов равновесных, кинетических и диффузионных параметров процесса адсорбции изобутилена на активированном угле марки АР-3
t, с | βкин ×103, с–1 | ${{D}_{c}}$, м2/ч | ${{a}_{\infty }}$, кг/100 кг |
b, м3/м3 |
---|---|---|---|---|
40 | 14.05 | 1.85 | 15.95 | 85.40 |
60 | 13.10 | 1.40 | – | – |
80 | 11.90 | 1.10 | – | – |
85 | 10.70 | 1.05 | – | – |
90 | 8.40 | 0.95 | – | – |
95 | 8.35 | 0.60 | – | – |
105 | 7.35 | 0.42 | – | – |
115 | 6.10 | 0.35 | – | – |
125 | 4.50 | 0.30 | – | – |
135 | 4.75 | 0.23 | – | – |
145 | 4.85 | 0.15 | – | – |
155 | 5.00 | – | – | – |
Из табл. 5 видно, что активированный уголь проявляет высокую активность по отношению к изобутилену. Он насыщается в течение 160 с. Выходные данные адсорбции изобутилена на угле АР-3 позволяют рассчитать время цикла адсорбции, т.е. время повторного использования угля АР-3, а это используется при проектировании адсорбера и в расчетах экономической эффективности адсорбции изобутилена из смеси с изобутаном.
ЗАКЛЮЧЕНИЕ
В настоящей работе разработана комплексная математическая модель всех процессов, происходящих в системе выделения серной кислотой из пирогаза фракции С4 изобутана и изобутилена и доочистки их адсорбционным методом, с учетом принципов теории рециркуляции, с помощью которой рассчитаны параметры процессов.
ОБОЗНАЧЕНИЯ
${{a}_{{R{\nu }j}}}$ | массовая доля рециркулята от общей загрузки |
$C_{j}^{0},$${{C}_{j}}$ | концентрация рециркулята на входе и выходе разделительного аппарата, кг/кг |
Ср | равновесная концентрация в газовой фазе, м3/м3 |
ар | равновесная концентрация на твёрдой фазе, кг/100 кг |
акин | кинетические данные адсорбции |
Свых | выходные данные адсорбции |
t | время адсорбции, c |
$C_{{R{\nu }j}}^{0},$${{C}_{{R{\nu }j}}}$ | концентрации компонента $j,$ кг/кг |
${{c}_{G}}$ | теплоемкость поглотителя (растворителя), ккал/(кг °С) |
${{c}_{j}}$ | теплоемкость, ккал/(кг °С) |
$c_{J}^{'}$ | теплоемкость второго реагента, ккал/(кг °С) |
${{G}_{j}}$ | количество поглотителя, кг/с |
${{g}_{{ij}}}$ | общая загрузка компонента, кг |
${{g}_{{k{\nu }}}}$ | количество вещества $j,$ поступающего в реактор $\nu $ из аппарата k, кг/с |
${{g}_{{oj}}}$ | расход свежего сырья по компоненту, кг/с |
${{g}_{{{\nu }oj}}}$ | свежая загрузка, поступающая со склада, кг/с |
${{g}_{{Rj}}}$ | количество рециркулята, кг/с |
${{g}_{{{\alpha }j}}}$ | количество продукта реакции, кг/с |
$i$ | число циклов |
$j$ | номер целевого компонента |
$n$ | номер аппарата, откуда рециркулируется целевой компонент |
${{T}_{M}}$ | температура теплоносителя, у которого температура меньше, °С |
${{T}_{{\delta }}}$ | температура теплоносителя, у которого температура больше, °С |
${{\alpha }_{j}},$${{\alpha }_{{nj}}}$ | текущая и начальная активности поглотителя по целевому компоненту, кг/кг |
Список литературы
Юрченко И.Е., Максименко А.М., Чаплин Д.Н. Состояние и перспективы производства высококонцентрированного изобутилена // Пром-сть синт. кауч. 1980. № 10. С. 2.
Юсубов Ф.В. Исследование промышленных адсорберов с использованием комбинированных моделей // Экоэнергетика. 2009. № 2. С. 13.
Гулиева С.Н. Исследования получения изобутана и изобутилена высокой чистоты // 69-я Международная молодежная научная конференция “Нефть и газ-2015”. М.: Российский государственный университет нефти и газа им. И.М. Губкина, 2015. С. 140.
Нагиев М.Ф. Теория рециркуляции и повышение оптимальности химических процессов. М.: Наука, 1970.
Шахтахтинский Т.Н., Кузнецов В.И., Зайцева З.А. Создание и развитие учения о рециркуляционных процессах в химической технологии. Баку: Элм, 1979.
Ibragimov Ch.Sh., Nurmamedov E.B. Liquid-phase adsorption and isomerization of C5–C8n-paraffins // Theor. Found. Chem. Eng. 2012. V. 46. № 2. P. 135. [Ибрагимов Ч.Ш., Нурмамедов Э.Б. Исследование процессов жидкофазной адсорбции смесей и изомеризации н-парафиновых углеводородов С5–С8 // Теор. осн. хим. технол. 2012. Т. 46. № 2. С. 169.]
Ибрагимов Ч.Ш. К методам проектирования и управления адсорбционными процессами. Баку: Элм, 1989.
Келбалиев Г.И., Расулов С.Р. Гидродинамика и массоперенос в дисперсных средах. СПб.: Химиздат, 2014.
Ибрагимов Ч.Ш., Бабаев А.И. Научные основы и практические задачи химической кибернетики. Баку: АГНА, 2012.
Дополнительные материалы отсутствуют.
Инструменты
Теоретические основы химической технологии