Теоретические основы химической технологии, 2020, T. 54, № 3, стр. 276-285
Применение схем с частично связанными тепловыми и материальными потоками и тепловых насосов для снижения энергетических затрат на экстрактивную ректификацию смеси изобутиловый спирт–изобутилацетат с диметилформамидом
П. С. Клаузнер a, *, Д. Г. Рудаков a, Е. А. Анохина a, А. В. Тимошенко a
a МИРЭА – Российский технологический университет
Москва, Россия
* E-mail: paulklausner@mail.ru
Поступила в редакцию 26.12.2019
После доработки 30.12.2019
Принята к публикации 13.01.2020
Аннотация
Исследован процесс экстрактивной ректификации смеси изобутиловый спирт–изобутилацетат с диметилформамидом. В сравнении с традиционной схемой рассмотрены схемы с применением тепловых насосов открытого типа и комплексы с частично связанными тепловыми и материальными потоками – как без, так и с применением теплового насоса. Показано, что применение тепловых насосов в данном процессе позволяет значительно снизить энергетические и полные годовые затраты.
ВВЕДЕНИЕ
Ректификация является одним из основных промышленных процессов очистки и разделения смесей различной природы. Она характеризуется высокими удельными затратами энергии [1]. Низкий термодинамический коэффициент полезного действия этого процесса заставляет исследователей вести постоянный поиск путей уменьшения энергопотребления. В настоящее время основными направлениями совершенствования отдельных процессов и технологических схем являются: внутренняя [2] и внешняя теплоинтеграция [3], а также применение тепловых насосов [4, 5].
Экстрактивная ректификация (ЭР) – процесс, основанный на применении специального вещества, изменяющего (увеличивающего, обращающего) относительную летучесть компонентов исходной смеси, используется как метод разделения азеотропных смесей и смесей компонентов с относительной летучестью, близкой к 1. В промышленности она применяется для выделения бензола из фракций пиролиза и риформинга [6], а также бутадиена и изопрена из продуктов пиролиза, и дегидрирования С4–С5 фракций [7]. Несмотря на то, что ЭР в ряде случаев характеризуется существенно меньшим энергопотреблением, чем азеотропная ректификация [8, 9] и метод разделения, основанный на варьировании давления [10–12], снижение энергетических затрат на ее проведение является актуальной задачей вследствие многотоннажности технологий основного органического и нефтехимического синтеза, где она главным образом применяется [13].
Так же как и в обычной ректификации, при совершенствовании этого процесса используются вышеуказанные подходы. Существенным отличием является то, что если для обычной ректификации они, в части использования внешних тепловых насосов, уже широко распространены, и примером такой технологией является ректификация пропан-пропиленовой фракции, то для экстрактивной ректификации разработка только начинается [14].
В качестве объекта исследования выбраны технологические схемы экстрактивной ректификации азеотропной смеси изобутиловый спирт (ИБС)–изобутилацетат (ИБА) с диметилформамидом (ДМФА) в качестве экстрактивного агента (ЭА). Применение ДМФА для разделения этой смеси предложено авторами [15].
В качестве метода исследования используется математическое моделирование химико-технологических процессов, которое является мощным современным методом разработки новых и совершенствования традиционных технологий [16].
РАСЧЕТНАЯ ЧАСТЬ
Все расчеты проводили в программном комплексе Aspen Plus v.9. Для моделирования парожидкостного равновесия использовали модель UNIQUAC, параметры которой приведены в табл. 1. Использовали доступные в базе данных (БД) Aspen Plus параметры бинарного взаимодействия для системы ИБС–ИБА и данные [11] для систем ИБС–ЭА и ИБА–ЭА, поскольку в базе данных программного комплекса параметры для них отсутствуют. Следует отметить, что для системы ИБС–ИБА параметры модели UNIQUAC из базы данных Aspen Plus обеспечивают более точное описание парожидкостного равновесия (ПЖР). Средние относительные ошибки для каждой бинарной пары при описании параметрами из разных источников приведены в табл. 2. Так как принцип работы тепловых насосов подразумевает сжатие паров, для учета неидеальности паровой фазы было применено уравнение состояния Редлиха–Квонга.
Таблица 1.
Параметры бинарного взаимодействия модели UNIQUAC
Источник | Лит. | БД | Лит. | Лит. |
---|---|---|---|---|
Компонент i | ИБС | ИБС | ИБС | ИБА |
Компонент j | ИБА | ИБА | ДМФА | ДМФА |
aij | 0.26671 | 0 | 0 | 0 |
aji | 0.22675 | 0 | 0 | 0 |
bij | –58.459 | 1.3501 | –28.484 | –277.43 |
bji | –182.11 | –45.3251 | 78.462 | 141.51 |
Таблица 2.
Средние относительные ошибки описания ПЖР
Источ-ник | Компонент i | Компонент j | ΔY*, % | ΔТ*, % |
---|---|---|---|---|
Лит. | ИБС | ИБА | 1.58 | 0.44 |
БД | ИБС | ИБС | 1.37 | 0.36 |
Лит. | ИБС | ДМФА | 1.94 | 0.19 |
Лит. | ИБА | ДМФА | 3.27 | 0.29 |
Для разделения рассматриваемой смеси можно использовать традиционную схему экстрактивной ректификации с тяжелокипящим ЭА и схемы, использующие тепловые насосы открытого типа. Поскольку система экстрактивной ректификации бинарной смеси представляет собой двухколонный комплекс, то тепловые насосы могут быть применены как по отдельности для каждой из колонн, так и для обеих колоннах одновременно.
Для всех вариантов схем рассматривали разделение исходной смеси с концентрацией изобутилового спирта 41 мас. %, скоростью подачи – 1500 кг/ч, температурой 73°C, давлением – 26 кПа. Концентрацию ИБС и ИБА в продуктовых потоках поддерживали постоянной и равной 99.5 мас. %.
Для традиционного варианта организации экстрактивной ректификации (рис. 1) по алгоритму, предложенному в [17], были определены оптимальные рабочие параметры.
Рис. 1.
Традиционная схема экстрактивной ректификации смеси ИБС–ИБА с разделяющим агентом ДМФА: ЭК – колонна экстрактивной ректификации; РК – колонна регенерации разделяющего агента; 1 – исходная смесь ИБС и ИБА; 2 – разделяющий агент ДМФА; 3 – ИБА; 4 – ИБС.
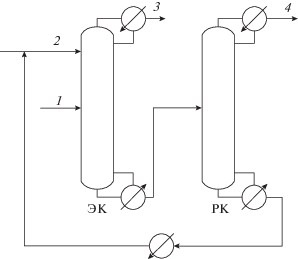
Давление вверху колонн было выбрано равным 20 кПа [15], рассматривались теоретические тарелки с перепадом давления на тарелке, равным 0.1013 кПа. Расчеты выполнялись в проектно-поверочном режиме с закрепленным качеством продуктовых потоков. В процессе оптимизации определяли общее число тарелок в обеих колоннах, тарелки подачи питания в экстрактивную колонну (ЭК) и колонну регенерации ЭА (РК), тарелку подачи экстрактивного агента в ЭК, количество потока ЭА и его температуру. Критерием оптимизации являлась суммарная тепловая нагрузка на кипятильники Qsum. Для оптимизации использовали встроенные инструменты программного комплекса Aspen Plus, такие как NQ Curve, Sensitivity Analysis и SQP Optimization. В целом процедура оптимизации включала следующие этапы.
На первом этапе при помощи инструмента NQ Curve при закрепленном количестве потока разделяющего агента (S), равном [15] 3000 кг/ч, было определено общее число теоретических тарелок в колоннах – 64 и 35 в колоннах ЭК и РК соответственно.
Далее была исследована зависимость тепловых нагрузок на кипятильник и конденсатор и флегмового числа первой колонны от температуры разделяющего агента. Данные приведены в табл. 3.
Таблица 3.
Зависимость параметров ЭК от температуры подачи ЭА
T, °С | Qreb, кВт | Qcond, кВт | R |
---|---|---|---|
70 | 639.2 | –586.7 | 6.08 |
79 | 638.3 | –602.5 | 6.27 |
87 | 638.3 | –571.3 | 5.89 |
96 | 638.2 | –618.6 | 6.46 |
102 | 638.2 | –630.2 | 6.60 |
Видно, что нагрузка на кипятильник колонны практически не зависит от температуры подачи ЭА. Поскольку большой паровой поток вверху колонны благоприятен для применения теплового насоса, то была выбрана температура подачи ЭА, равная 102°C. Такая температура позволяет также не осложнять систему установкой дополнительного теплообменника на линии рецикла разделяющего агента.
Затем были установлены пределы варьирования количества разделяющего агента. Для этого для ряда положений тарелок подачи питания NF и агента NS определено минимальное необходимое количество разделяющего агента, а также значений, при котором $Q_{{reb}}^{{{\text{ЭК}}}}$ достигает минимального значения. Результаты представлены в табл. 4.
Таблица 4.
Минимальный и оптимальный (для ЭК) расход разделяющего агента в зависимости от положения NS/Nf
NS/NF | Smin, кг/ч | Sopt, кг/ч | Qreb при Smin, кВт | Qreb при Sopt, кВт |
---|---|---|---|---|
12/39 | 2380 | 3100 | 705.4 | 635.2 |
12/40 | 2400 | 3030 | 714.1 | 635.0 |
12/41 | 2410 | 3010 | 722.4 | 637.6 |
13/39 | 2490 | 3070 | 705.5 | 640.1 |
13/40 | 2410 | 3000 | 719.4 | 639.3 |
13/41 | 2380 | 2980 | 729.9 | 642.7 |
14/39 | 2500 | 3080 | 700.3 | 636.6 |
14/40 | 2430 | 3020 | 712.3 | 635.6 |
14/41 | 2410 | 3000 | 724.6 | 637.8 |
15/39 | 2540 | 3110 | 708.2 | 638.4 |
15/40 | 2480 | 3070 | 728.1 | 638.2 |
15/41 | 2440 | 3050 | 722.2 | 640.3 |
Видно, что минимальный расход ЭА достаточно сильно зависит от NF, таким образом, для оптимизации расхода ЭА при различных NF имеет смысл установить различные границы варьирования. Для 12-й тарелки подачи агента были выбраны пределы от 2410 до 3100 кг/ч, для 13-й – от 2490 до 3070 кг/ч, для 14-й – от 2500 до 3080 кг/ч, для 15-й – от 2540 до 3110 кг/ч.
Далее для пределов варьирования расхода ЭА от 2500 до 3200 кг/ч проверено отсутствие влияния на оптимальное положение тарелки питания в РК. Результат проверки представлен в табл. 5.
Таблица 5.
Оптимальное положение тарелки питания в колонне регенерации при варьировании расхода ЭА
S, кг/ч | NF | Qreb, кВт | Qcond, кВт | R |
---|---|---|---|---|
2500 | 11 | 421.1 | –427.6 | 3.0 |
2600 | 11 | 434.0 | –440.8 | 3.12 |
2800 | 11 | 460.1 | –467.3 | 3.37 |
3000 | 11 | 486.2 | –493.9 | 3.62 |
3200 | 11 | 512.2 | –520.3 | 3.87 |
При одновременном использовании инструментов Sensitivity Analysis и SQP Optimization было установлено оптимальное положение тарелок подачи питания и агента в ЭК и оптимальное количество потока разделяющего агента. При этом инструментом Sensitivity Analysis варьировались положения тарелок подачи питания и ЭА, а при помощи SQP для каждого положения подбирался оптимальный расход разделяющего агента, при котором суммарная нагрузка на кипятильники колонн Qsum = $Q_{{reb}}^{{{\text{ЭК}}}}$ + $Q_{{reb}}^{{{\text{РК}}}}$ достигает минимального значения. Результаты представлены в табл. 6.
Таблица 6.
Определение оптимального расхода ЭА, положения тарелки питания и подачи ЭА
NS | NF | S, кг/ч | $Q_{{reb}}^{{{\text{ЭК}}}}$ | $Q_{{{\text{cond}}}}^{{{\text{ЭК}}}}$ | RЭК | $Q_{{reb}}^{{{\text{РК}}}}$ | $Q_{{{\text{cond}}}}^{{{\text{РК}}}}$ | RРК | Qsum |
---|---|---|---|---|---|---|---|---|---|
12 | 39 | 2617 | 652.3 | –645.8 | 6.79 | 436.4 | –443.2 | 3.14 | 1089 |
40 | 2602 | 649.9 | –643.5 | 6.76 | 434.4 | –441.2 | 3.12 | 1084 | |
41 | 2602 | 649.7 | –643.3 | 6.76 | 434.3 | –441.1 | 3.12 | 1084 | |
42 | 2476 | 668.1 | –662.2 | 6.99 | 418.0 | –424.5 | 2.96 | 1086 | |
13 | 39 | 2698 | 643.1 | –636.3 | 6.68 | 446.7 | –453.7 | 3.24 | 1090 |
40 | 2610 | 648.3 | –641.9 | 6.74 | 435.3 | –442.1 | 3.13 | 1084 | |
41 | 2541 | 654.5 | –648.3 | 6.82 | 426.3 | –432.9 | 3.05 | 1081 | |
42 | 2498 | 663.4 | –657.5 | 6.93 | 420.8 | –427.3 | 2.99 | 1084 | |
14 | 39 | 2635 | 655.2 | –648.7 | 6.82 | 438.5 | –445.4 | 3.16 | 1094 |
40 | 2627 | 649.9 | –643.4 | 6.76 | 437.5 | –444.3 | 3.15 | 1087 | |
41 | 2627 | 649.7 | –643.2 | 6.76 | 437.6 | –444.4 | 3.16 | 1087 | |
42 | 2535 | 662.7 | –656.6 | 6.92 | 425.5 | –432.2 | 3.04 | 1088 | |
15 | 39 | 2740 | 652.0 | –645.0 | 6.78 | 452.2 | –459.3 | 3.30 | 1104 |
40 | 2638 | 658.6 | –652.1 | 6.87 | 438.9 | –445.8 | 3.17 | 1098 | |
41 | 2644 | 654.8 | –648.2 | 6.82 | 439.7 | –446.6 | 3.18 | 1094 | |
42 | 2576 | 664.7 | –658.4 | 6.94 | 430.9 | –437.6 | 3.09 | 1096 |
Итоговые рабочие параметры традиционной схемы экстрактивной ректификации представлены в табл. 7. Оптимальное количество подаваемого ЭА: 2541 кг/ч, температура ЭА: 102°C.
Таблица 7.
Рабочие параметры традиционной схемы экстрактивной ректификации
Колонны | ЭК | РК |
---|---|---|
Nsum | 64 | 35 |
NF | 41 | 11 |
NS | 13 | |
Qreb, кВт | 656.2 | 426.3 |
Qcond, кВт | –650.1 | –432.9 |
R | 6.8 | 3.05 |
Tcond, °C | 69.7 | 69.6 |
Treb, °C | 99.6 | 104.5 |
Pcond, кПа | 20.0 | 20.0 |
Preb, кПа | 26.4 | 23.4 |
Авторы [18] предложили метод для предварительной оценки целесообразности применения тепловых насосов в ректификации на основе коэффициента эффективности Cef:
На основе традиционной схемы экстрактивной ректификации и приведенных предположений об эффективности тепловых насосов были смоделированы три варианта схем, содержащих тепловые насосы открытого типа (рис. 2). Во всех случаях введенный в схему тепловой насос полностью использует паровой поток, выходящий сверху колонны, на которой он установлен. После сжатия в компрессоре с потребляемой мощностью Wcomp до давления Pcomp и адиабатического нагрева паровой поток направляется в теплообменник, обеспечивая частичный обогрев куба колонны – количество переданного в этом теплообменнике тепла обозначено QHE. Далее паровой поток направляется в дроссель, где давление сбрасывается до 20 кПа. Для полной конденсации потока используется вспомогательный конденсатор, после которого поток разделяется на продуктовый и флегмовый.
Рис. 2.
Варианты организации процесса ректификации с внешним тепловым насосом открытого типа. Установка компрессора: (а) – на паровом потоке ЭК, (б) – на паровом потоке РК, (в) – на паровых потоках обеих колонн. ЭК – колонна экстрактивной ректификации; РК – колонна регенерации разделяющего агента; 1 – исходная смесь ИБС и ИБА; 2 – разделяющий агент ДМФА; 3 – ИБА; 4 – ИБС.
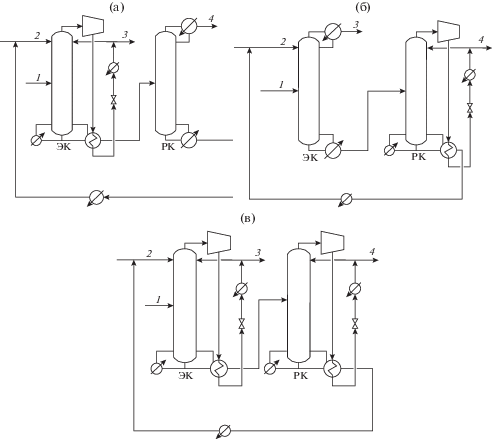
Так как в рассматриваемых схемах замена стандартного теплообменного оборудования ректификационных колонн на обвязку, включающую тепловой насос, не вносит значительных изменений в тепло-массообменные процессы внутри колонн, повторная оптимизация конструкционных параметров колонн не требуется. Следует отметить, что во всех трех вариантах организации процесса у колонн с тепловыми насосами применяются вспомогательные кубовые кипятильники, нагрузка на которые обозначена Qreb, а также вспомогательные конденсаторы, нагрузка на которые обозначена Qcond. Это связано с тем, что в рассматриваемых схемах не удалось полностью отказаться от дополнительного подвода и отвода тепла, несмотря на то, что соответствующие тепловые нагрузки, а следовательно, расходы греющего пара и охлаждающей воды, как будет показано ниже, значительно снижаются по сравнению с традиционной схемой.
Рассчитанные оптимальные рабочие параметры трех вариантов схем с тепловыми насосами приведены в табл. 8.
Таблица 8.
Параметры схем с тепловыми насосами открытого типа
Тепловой насос на колонне экстрактивной ректификации (рис. 2а) | ||
Колонны | ЭК | РК |
Qreb, кВт | 93.3 | 426.3 |
QHE, кВт | 563.9 | |
Qcond, кВт | –194.6 | –432.9 |
Оборудование | ||
Wcomp, кВт | 116.3 | |
Pcomp, кПа | 119.2 | |
Тепловой насос на колонне регенерации разделяющего агента (рис. 2б) | ||
Колонны | ЭК | РК |
Qreb, кВт | 656.2 | 17.5 |
QHE, кВт | 410.5 | |
Qcond, кВт | –650.1 | –98.7 |
Оборудование | ||
Wcomp, кВт | 90.1 | |
Pcomp, кПа | 181.1 | |
Схема с двумя тепловыми насосами (рис. 2в) | ||
Колонны | ЭК | РК |
Qreb, кВт | 93.3 | 17.5 |
QHE, кВт | 563.9 | 410.5 |
Qcond, кВт | –194.6 | –98.7 |
Оборудование | ||
Wcomp, кВт | 116.3 | 90.1 |
Pcomp, кПа | 119.2 | 181.1 |
В технологические схемы с тепловыми насосами (рис. 2) по сравнению с традиционной схемой вносятся существенные изменения части дополнительного технологического оборудования за счет включения в их состав “горячих” компрессоров. Для обогрева кипятильников используется как греющий пар, так и тепло, полученное при компримировании дистиллятных паровых потоков, потребляется электроэнергия для привода компрессоров. Эти энергетические ресурсы имеют различную цену, поэтому использование критерия энергетических затрат для выбора оптимальной технологической схемы с разнородным технологическим оборудованием становится некорректным. В то же время для процесса оптимизации каждой индивидуальной технологической схемы применение этого критерия допустимо и целесообразно. Для сравнения вариантов организации процесса, включающего разнородное технологическое оборудование, принято использовать критерий полных годовых затрат (ТАС):
где ET – срок эксплуатации установки в годах, СС – капитальные затраты, долл. США, ОС – эксплуатационные затраты, долл. США/годПоскольку изменение сроков эксплуатации существенно влияет на величину ТАС, то были проведены расчеты критерия для 10- и 20-летнего периодов.
Для вычисления капитальных и эксплуатационных затрат использованы средства Aspen Process Economic Analyzer. Основные экономические параметры приведены в табл. 9 и 10, а результаты экономической оценки − в табл. 11.
Таблица 9.
Цены на энергоносители в долл. США
Электричество, кВт | 0.0775 |
Оборотная вода, т | 0.03 |
Греющий пар, кг | 0.017 |
Таблица 10.
Стоимость оборудования в долл. США
Общие | Традиционная схема | |||
Колонна | Флегмовый насос | Осн. конденсатор | Осн. кипятильник | |
ЭК | 687 800 | 5200 | 25 400 | 14 700 |
РК | 195 500 | 4500 | 26 500 | 13 600 |
Стоимость оборудования теплового насоса | ||||
Компрессор | Теплообменник | Вспом. конденсатор | Вспом. кипятильник | |
ЭК | 707 400 | 15 100 | 8600 | 11 300 |
РК | 721 100 | 13 100 | 9900 | 12 300 |
Таблица 11.
Экономическая оценка
Экономические показатели | Традицион-ная схема | Схема с тепловым насосом на ЭК (рис. 2а) | Схема с тепловым насосом на РК (рис. 2б) | Схема с двумя тепловыми насосами (рис. 2в) |
---|---|---|---|---|
Затраты на энергоносители, долл. США/год | 357 434 | 273 461 | 3003 75 | 216 461 |
Снижение затрат на энергоносители, % | 0 | 23.5 | 16.0 | 39.4 |
Цена оборудования, долл. США | 973 500 | 1 690 800 | 1 709 800 | 2 427 100 |
TAC (10 лет) | 454 784 | 442 541 | 471 355 | 459 171 |
ТАС (20 лет) | 406 109 | 358 001 | 385 865 | 337 816 |
Снижение ТАС (10 лет), % | 0 | 2.7 | –3.6 | –1 |
Снижение ТАС (20 лет), % | 0 | 11.9 | 5 | 16.8 |
Видно, что при 10-летнем периоде эксплуатации использование технологических схем с тепловыми насосами приносит очень незначительный экономический эффект и практически эти технологические решения находятся на грани экономической эффективности. Также видно, что для схемы экстрактивной ректификации наибольшей эффективностью обладают технические решения, предусматривающие установку компрессора на паровой поток дистиллята колонны экстрактивной ректификации. Применение теплового насоса только на колонне регенерации экстрактивного агента нецелесообразно. Схема с двумя тепловыми насосами наиболее эффективна энергетически. По критерию ТАС при сроках ET = 10 более выгодной является схема с тепловым насосом на экстрактивной колонне, однако, как уже отмечалось выше, экономический эффект незначителен, а при ET = 20 – схема с двумя тепловыми насосами.
Авторами [15] было показано, что применение комплекса с частично связанными тепловыми и материальными потоками (ЧСТМП) при экстрактивной ректификации смеси ИБС–ИБА с диметилформамидом позволяет значительно снизить энергетические затраты. Применение таких комплексов не исключает возможности оснащения схемы тепловым насосом, поэтому на основе традиционной схемы экстрактивной ректификации была смоделирована схема с ЧСТМП (рис. 3а). Затем на ее основе была получена и подвергнута параметрической оптимизации схема с тепловым насосом открытого типа (рис. 3б).
Рис. 3.
(а) – комплекс с ЧСТМП, (б) – комплекс с ЧСТМП и тепловым насосом. ЭК – колонна экстрактивной ректификации; БУС – боковая укрепляющая секция; 1 – исходная смесь ИБС и ИБА; 2 – разделяющий агент ДМФА; 3 – ИБА; 4 – ИБС.
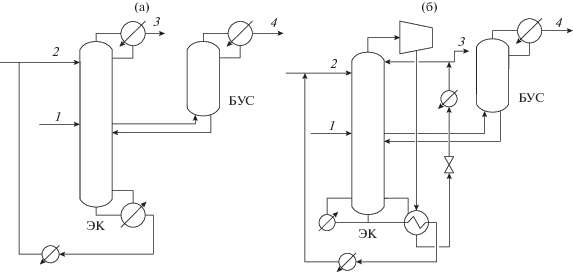
Моделирование и оптимизацию комплекса с ЧСТМП проводили по алгоритму, аналогичному описанному в [17] и состоящему из следующих этапов.
На первом этапе традиционная схема была преобразована в схему, состоящую из одной сложной колонны с боковой укрепляющей секцией (БУС) (рис. 3а) [3, 13]. На втором этапе проводили оптимизацию величины бокового отбора и его положения. Отметим, что, по данным ряда исследований, оптимальные значения других переменных, таких как тарелка подачи питания, тарелка подачи ЭА и поток ЭА, в схемах с ЧСТМП не отличаются или отличаются незначительно от соответствующих параметров традиционной схемы [3, 13], поэтому оптимизация комплексов с ЧСТМП для снижения размерности задачи по этим параметрам может не проводиться. При оптимизации для ряда тарелок бокового отбора при помощи инструмента SQP Optimization определяли величину бокового отбора, соответствующую минимальной нагрузке на кипятильник Qreb. Полученные на этом этапе зависимости приведены в табл. 12.
Таблица 12.
Определение оптимальной тарелки бокового отбора и количества бокового отбора
NV | V, кг/ч | $Q_{{reb}}^{{{\text{ЭК}}}}$ | $Q_{{{\text{cond}}}}^{{{\text{ЭК}}}}$ | RЭК | $Q_{{{\text{cond}}}}^{{{\text{БУС}}}}$ | RБУС |
---|---|---|---|---|---|---|
64 | 1232 | 894.5 | –669.0 | 7.07 | –213.5 | 1.03 |
65 | 1208 | 877.8 | –656.4 | 6.92 | –209.4 | 0.99 |
66 | 1156 | 859.3 | –646.9 | 6.80 | –200.4 | 0.90 |
67 | 1086 | 844.1 | –643.9 | 6.76 | –188.2 | 0.79 |
68 | 1072 | 838.1 | –640.3 | 6.71 | –185.8 | 0.76 |
69 | 1072 | 832.7 | –634.9 | 6.65 | –185.7 | 0.76 |
70 | 1076 | 828.5 | –630.0 | 6.59 | –186.4 | 0.77 |
71 | 1078 | 825.6 | –626.7 | 6.55 | –186.6 | 0.77 |
72 | 1100 | 825.5 | –622.8 | 6.51 | –190.4 | 0.81 |
73 | 1110 | 825.6 | –621.4 | 6.49 | –191.9 | 0.82 |
74 | 1148 | 830.3 | –619.5 | 6.47 | –198.4 | 0.88 |
75 | 1214 | 842.1 | –620.2 | 6.47 | –209.5 | 0.99 |
Результаты моделирования и оптимизации представлены в табл. 13.
Таблица 13.
Параметры комплекса с ЧСТМП
Колонны | ЭК | БУС |
---|---|---|
Nsum | 88 | 11 |
NF | 41 | – |
NV | 71 | – |
NS | 13 | – |
Qreb, кВт | 826.3 | – |
Qcond, кВт | –627.4 | –186.7 |
R | 6.56 | 0.77 |
Tcond, °C | 69.7 | 74.9 |
Treb, °C | 110.4 | – |
Pcond, кПа | 20.0 | 25.9 |
Preb, кПа | 28.8 | – |
На основе этих параметров было проведено моделирование схемы с тепловым насосом открытого типа. В качестве рабочего тела для теплового насоса был выбран поток ИБА, так как нагрузка на конденсатор основной секции выше и флегмовое число больше, чем у конденсатора БУС. Необходимое для обеспечения необходимой разницы температур ΔT = 25 К в теплообменнике теплового насоса давление составляет 121.8 кПа. Результаты моделирования схемы представлены в табл. 14.
Таблица 14.
Параметры комплекса с ЧСТМП и тепловым насосом
Колонны | ЭК | БУС |
Qreb, кВт | 306.2 | – |
QHE, кВт | 495.3 | – |
Qcond, кВт | –175.0 | –186.7 |
Оборудование | ||
Wcomp, кВт | 102.7 | – |
Pcomp, кПа | 121.8 | – |
Для этих схем также была проведена экономическая оценка в Aspen Process Economic Analyzer и определен TAC. Цены на оборудование приведены в табл. 15, а результаты оценки в табл. 16.
Таблица 15.
Стоимость оборудования в долл. США
Колонна | Флегмовый насос | Осн. конденсатор | Осн. кипятильник | |
---|---|---|---|---|
ЭК | 80 100 | 5200 | 25 300 | 17 700 |
БУС | 47 600 | 4500 | 25 400 | – |
Компрессор | Теплообменник | Вспом. конденсатор | ||
ЭК | 704 500 | 14300 | 9800 |
Таблица 16.
Экономическая оценка
Экономические показатели | Традиционная схема | Комплекс с ЧСТМП | Комплекс с ЧСТМП и тепловым насосом |
---|---|---|---|
Затраты на энергоносители, долл. США/год | 357 434 | 281 185 | 200 759 |
Снижение затрат на энергоносители, % | 0 | 21.33 | 55.72 |
Цена оборудования, долл. США | 973 500 | 926 700 | 1 612 300 |
TAC (10 лет) | 454 784 | 373 855 | 361 989 |
ТАС (20 лет) | 406 109 | 327 520 | 281 374 |
Снижение ТАС (10 лет), % | 0 | 17.80 | 20.40 |
Снижение ТАС (20 лет), % | 0 | 19.35 | 30.71 |
Как можно видеть, использование комплекса с ЧСТМП действительно снижает общие энергозатраты на более чем 20%. Схема же с одновременным использованием комплекса с частично связанными тепловыми и материальными потоками и теплового насоса позволяет снизить энергетические затраты на 55.72%, а ТАС за 20 лет – на 30.71%. Схема с одновременным применением комплекса с ЧСТМП и теплового насоса является наиболее эффективной при использовании ДМФА как экстрактивного агента.
ЗАКЛЮЧЕНИЕ
В настоящей работе показано, что применение тепловых насосов в схеме экстрактивной ректификации смеси изобутиловый спирт–изобутилацетат с диметилформамидом в качестве экстрактивного агента может быть экономически оправдано. Среди рассмотренных схем с внешним тепловым насосом открытого типа наибольшую энергетическую эффективность имеет схема, в которой тепловые насосы применяются на обеих колоннах – такая схема обеспечивает снижение затрат на энергоносители на 39.6% по сравнению с традиционной схемой экстрактивной ректификации. По критерию полных годовых затрат при расчете исходя из времени окупаемости установки в 10 лет наименьшее значение ТАС достигается в схеме с тепловым насосом на колонне экстрактивной ректификации. Такая схема обеспечивает снижение десятилетнего ТАС на 2.7% по сравнению с традиционной схемой. При времени функционирования в 20 лет наименьшие полные годовые затраты обеспечивает схема с двумя тепловыми насосами. Применение комплекса с ЧСТМП без теплового насоса позволяет снизить энергетические затраты на 21.33%. Кроме того, в отличие от схем с тепловыми насосами, в ней не происходит изменения рода энергоносителя. Наиболее экономичной из рассмотренных является схема, в которой одновременно применяется и комплекс с ЧСТМП, и тепловой насос. Такая схема обеспечивает снижение затрат на энергоносители на 55.7% и снижение ТАС с окупаемостью в 20 лет на 30.7%.
Работа выполнена при финансовой поддержке Российского фонда фундаментальных исследований (проект № 20-03-00314).
ОБОЗНАЧЕНИЯ
A | термодинамическая работа |
a, b | параметры уравнения UNIQUAC |
С | коэффициент |
СС | капитальные затраты |
ET | срок эксплуатации установки |
N | номер тарелки |
OC | эксплуатационные затраты |
P | абсолютное давление |
Q | тепловая нагрузка |
R | флегмовое число |
S | расход экстрактивного агента |
T | температура |
TAC | полные годовые затраты |
V | поток бокового отбора |
W | потребляемая мощность |
ИНДЕКСЫ
comp | компрессор |
cond | конденсатор |
F | питание |
HE | теплообменник |
i, j | номера компонентов |
min | минимальное значение |
opt | оптимальное значение |
reb | кипятильник |
S | экстрактивный агент |
sum | суммарный |
V | боковой отбор |
СОКРАЩЕНИЯ
БД | данные из базы данных программного комплекса |
БО | боковой отбор |
БУС | боковая укрепляющая секция |
ДМФА | диметилформамид |
ИБА | изобутилацетат |
ИБС | изобутиловый спирт |
Лит. | данные из литературного источника |
ПЖР | парожидкостное равновесие |
РК | колонна регенерации разделяющего агента |
ЧСТМП | частично связанные тепловые и материальные потоки |
ЭА | экстрактивный агент |
ЭК | колонна экстрактивной ректификации |
ЭР | экстрактивная ректификация |
Список литературы
King C.J. Separation processes. Courier Corporation, 2013.
Kiss A.A., Olujić T. A review on process intensification in internally heat-integrated distillation columns // Chem. Eng. Process. 2014. V. 86. P. 125.
Тимошенко А.В., Анохина Е.А., Рудаков Д.Г., Тимофеев В.С., Тациевская Г.И., Матюшенкова Ю.В. Энергосбережение в ректификации с использованием комплексов со связанными потоками // Вестн. МИТХТ. 2011. Т. 6. № 4. С. 28.
Null H.R. Heat pumps in distillation // Chem. Eng. Prog. 1976. V. 72. № 7. P. 58.
Jana A.K. Heat integrated distillation operation // Appl. Energy. 2010. V. 87. № 5. P. 1477.
Гайле А.А., Сомов В.Е. Процессы разделения и очистки продуктов переработки нефти и газа. СПб.: Химиздат, 2012.
Павлов С.Ю. Выделение и очистка мономеров для синтетического каучука. Л.: Химия, 1987.
Meirelles A., Weiss S., Herfurth H. Ethanol Dehydration by Extractive Distillation // J. Chem. Technol. Biotechnol. 1992. V. 53. P. 181.
Arifin S., Chien I.-L. Design and Control of an Isopropyl Alcohol Dehydration Process via Extractive Distillation Using Dimethyl Sulfoxide as an Entrainer // Ind. Eng. Chem. Res. 2008. V. 47. № 3. P. 790.
Luyben W.L. Comparison of Pressure-Swing Distillation and Extractive Distillation Methods for Methanol-Recovery Systems in the TAME Reactive-Distillation Process // Ind. Eng. Chem. Res. 2005. V. 44. № 15. P. 5715.
Luyben W.L. Comparison of Extractive Distillation and Pressure-Swing Distillation for Acetone-Methanol Separation // Ind. Eng. Chem. Res. 2008. V. 47. № 8. P. 2696.
Wang S.-J., Huang H.-P., Yu C.-C. Plantwide Design of Transesterification Reactive Distillation to Co-Generate Ethyl Acetate and n-Butanol // Ind. Eng. Chem. Res. 2010. V. 49. № 2. P. 750.
Анохина Е.А. Энергосбережение в процессах экстрактивной ректификации // Вестн. МИТХТ. 2013. Т. 8. № 5. С. 3.
You X., Rodriguez-Donis I., Gerbaud V. Reducing process cost and CO2 emissions for extractive distillation by double-effect heat integration and mechanical heat pump // Appl. Energy. 2016. V. 166. P. 128.
Анохина Е.А., Рудаков Д.Г., Тимошенко А.В. Экстрактивная ректификация смеси изобутиловый спирт – изобутилацетат с диметилформамидом // Хим. технол. 2011. Т. 12. № 10. С. 627.
Тимошенко А.В., Анохина Е.А. Моделирование и оптимизация как инструмент разработки высокоэффективных технологических схем ректификации // Росс. технол. журн. 2017. Т. 5. № 3. С. 138.
Анохина Е.А., Долматов Б.Б., Тимошенко А.В. Энергетическая эффективность экстрактивной ректификации смеси ацетон–хлоpофоpм в сложной колонне с боковой секцией // Хим. технол. 2008. № 8. С. 402.
Plesu V., Bonet-Ruiz A.E., Bonet J., Llorens J. Simple equation for suitability of heat pump use in distillation // Proc. 24th European Symposium on Computer Aided Process Engineering / Eds. Klemes J.J., Varbanov S.V., Liew P.Y. Amsterdam: Elsevier, 2014. P. 1327.
Дополнительные материалы отсутствуют.
Инструменты
Теоретические основы химической технологии