Теоретические основы химической технологии, 2021, T. 55, № 1, стр. 116-125
Синтез и вспенивание фосфатных стекломатриц для комплексных микроудобрений
Б. М. Гольцман a, *, Е. А. Яценко a
a Южно-Российский государственный политехнический университет (НПИ) им. М.И. Платова
Новочеркасск, Россия
* E-mail: boriuspost@gmail.com
Поступила в редакцию 18.05.2020
После доработки 01.10.2020
Принята к публикации 05.10.2020
Аннотация
Рассмотрена возможность вспенивания фосфатных стекломатриц для синтеза комплексных микроудобрений пролонгированного действия. Изучена область стеклообразования в системе K2O–CaO–P2O5, выбран оптимальный состав исходного стекла. Проведено вспенивание исходных смесей по одностадийной и двухстадийной технологии, изучена их внутренняя структура, фазовый состав и стойкость к воздействию воды. Установлено, что вспенивание по двухстадийной технологии позволяет получить материал со стабильной структурой и свойствами, что важно при использовании в качестве удобрений пролонгированного действия.
ВВЕДЕНИЕ
Одной из главных причин слабого роста российского сельского хозяйства является очень низкий уровень потребления удобрений. При этом для получения высококачественных урожаев необходимо использовать не только основные элементы минерального питания растений, но и пополнять запасы микроэлементов в почве с помощью микроудобрений – особой группы удобрений, в которых, наряду с прочими компонентами, имеются необходимые растениям микроэлементы. У существующих на данный момент микроудобрений есть ряд существенных недостатков, мешающих их масштабному использованию. Минеральные микроудобрения [1, 2] малорастворимы, вызывают засаливание почв и т.д., тогда как хелатные микроудобрения [3, 4] требуют дополнительной корневой подкормки, а также регулярного внесения (2–4 раза за вегетационный период) при определенных погодных условиях.
Новым и малоизученным видом микроудобрений являются комплексные микроудобрения на основе фосфатных стекол. Стеклообразные фосфаты из-за низкой химической устойчивости характеризуются высокой биохимической активностью, что позволяет крайне эффективно использовать их в качестве удобрений. Кроме того, стеклянные удобрения не выветриваются, медленно растворяются в почве и обеспечивают питание растений в течение 3–5 лет. Важной особенностью стекловидной фазы здесь является возможность ее модифицирования одним или несколькими элементами [5, 6]. При взаимодействии с водой и компонентами почвы происходит удаление оксидов микроэлементов. Остающийся после удаления фосфор-кислородный каркас разрушается с образованием растворимых в воде гидратов оксидов фосфора, также потребляемых растениями. Однако существенным недостатком таких порошкообразных удобрений является их вымывание грунтовыми водами, что снижает эффективность их использования.
Данная проблема может быть решена путем синтеза мелкопористых стеклогранул, причем за счет развитой пористой поверхности стекла будет увеличиваться площадь взаимодействия с водой и достигаться больший эффект. Кроме того, за счет пористой структуры удобрения повысится равномерность насыщения почвы микроэлементами во времени, что позволит получать удобрения с заданным сроком действия. Также использование крупных (3–5 мм) высокопористых гранул вместо традиционных порошковых удобрений позволит обеспечить стабильный уровень залегания в почве без вымывания. Таким образом, целью данной работы была разработка технологии синтеза и вспенивания фосфатных стекломатриц для получения комплексных микроудобрений.
ТЕОРЕТИЧЕСКИЙ АНАЛИЗ
Разработка фосфатных стеклоудобрений, а также способов их модификации различными микроэлементами является одним из современных направлений, развивающихся как на территории Российской Федерации, так и на мировом уровне. В области биоразлагаемых стеклоудобрений работают коллективы исследователей из Сербии, Польши, Индии, Южной Кореи и др. [5–10]. На территории РФ разработкой стеклоудобрений пролонгированного действия наиболее активно занимается научная школа под руководством Г.О. Карапетяна [11, 12]. Более того, в России существует промышленное производство фосфатных стеклоудобрений [13], что подтверждает их экономическую эффективность.
Методологической основой всех описанных исследований является синтез удобрений по традиционной стекольной технологии, включающей смешение шихт, их варку, выработку стекла и его измельчение с получением конечного продукта – порошкообразных стеклянных удобрений. Однако существенным недостатком таких удобрений являются изменения в кинетике пролонгированного действия, обусловленные замедлением разрушения стеклянных гранул с течением времени за счет формирования на их поверхности низкореакционного слоя гидроксидов, образовавшегося при контакте с водой. Это ведет к снижению эффективности удобрения и необходимости досрочного введения новых порций. Кроме того, как указывалось выше, удобрения в виде порошков вымываются грунтовыми водами, что также снижает их эффективность.
Для увеличения стабильности залегания удобрений в почве при сохранении большой поверхности контакта между удобрением и почвой, целесообразно применение высокопористых гранул с развитой поверхностью. По аналогии с пористыми силикатными материалами была рассмотрена применимость двух технологий синтеза пористых стекломатериалов – одностадийной (напрямую из шихты) и двухстадийной (варка промежуточного стекла и его дальнейшее вспенивание). В качестве исходной была выбрана трехкомпонентная система K2O–CaO–P2O5, применяемая при синтезе различных видов биоактивных стекол [14–17]. На основании проведенных ранее исследований [14–19] была выбрана область стеклообразования, представленная на рис. 1.
Вспенивание по одностадийной технологии осуществлялось по так называемому гидратному механизму за счет взаимодействия исходных компонентов шихты (мел, поташ, ортофосфорная кислота) по реакции (1) и последующей поризации размягченной фосфатной массы парами воды, что можно изобразить схемой (2) :
(1)
$\begin{gathered} {{{\text{K}}}_{{\text{2}}}}{\text{C}}{{{\text{O}}}_{3}} + 2{\text{CaC}}{{{\text{O}}}_{3}} + 2{{{\text{H}}}_{{\text{3}}}}{\text{P}}{{{\text{O}}}_{4}} \to \\ \to \,\,2\left( {{\text{K}},{\text{ Ca}}} \right){\text{P}}{{{\text{O}}}_{{\text{4}}}}~ \cdot \,3{{{\text{H}}}_{{\text{2}}}}{\text{O}} + 3{\text{C}}{{{\text{O}}}_{2}}, \\ \end{gathered} $(2)
$\left( {{\text{K}},{\text{ Ca}}} \right){\text{P}}{{{\text{O}}}_{4}} \cdot 3{{{\text{H}}}_{{\text{2}}}}{\text{O}} \to \left( {{\text{K}},{\text{ Ca}}} \right){\text{P}}{{{\text{O}}}_{4}} + 3{{{\text{H}}}_{{\text{2}}}}{\text{O}}{\kern 1pt} \uparrow {\kern 1pt} .$Для вспенивания по двухстадийной технологии предварительно осуществлялась варка стекла из исходной шихты, его охлаждение, измельчение и вспенивание. Для вспенивания фосфатной массы был выбран порообразователь, применяемый на реальных производствах пеностекла – глицерин [20, 21]. При этом протекает каскад следующих реакций [22, 24]:
(3)
$\begin{gathered} {{{\text{C}}}_{{\text{3}}}}{{{\text{H}}}_{{\text{5}}}}{{{\text{(OH}})}_{3}} + x{{{\text{O}}}_{2}} \to a{\text{C}}{{{\text{O}}}_{2}} + b{\text{CO}} + \\ + \,\,c{{{\text{H}}}_{{\text{2}}}}{\text{O}} + d{{{\text{H}}}_{2}} + e{\text{C}} + d{\text{C}}{{{\text{H}}}_{4}} + \ldots . \\ \end{gathered} $(4)
${\text{Стекло}}{\kern 1pt} --{\kern 1pt} {\text{S}}{{{\text{O}}}_{3}} + 2{\text{C}} \to {\text{стекло}}{\kern 1pt} --{\kern 1pt} {{{\text{S}}}^{{2--}}} + {\text{C}}{{{\text{O}}}_{2}} + {\text{CO}},$Основным преимуществом разработанной технологии является использование смеси порообразующих компонентов, позволяющих вести вспенивание в интервале температур от 250°С, что является превосходным показателем в сравнении с традиционными порообразователями, где температуры вспенивания составляют 700–900°С. Фактическая температура вспенивания будет равна температуре размягчения стекломассы, которая для легкоплавких фосфатных стекол составляет от 400°С. Кроме того, микропоры в межпоровых стенках в процессе взаимодействия с окружающей средой будут быстро разрушаться, открывая доступ к веществу внутренних слоев материала до разрушения всей межпоровой стенки и повышая равномерность насыщения почвы во времени.
ЭКСПЕРИМЕНТАЛЬНАЯ ЧАСТЬ
В качестве исходного сырья для синтеза фосфатных стекломатриц были использованы реагенты марок “ХЧ”, “ЧДА”, а именно ортофосфорная кислота H3PO4, карбонат кальция (мел) CaCO3, карбонат калия (поташ) K2CO3. Процесс подготовки шихты включал следующие стадии: расчет и отвешивание заданного количества компонентов, смешение компонентов в барабанной мельнице в течение 30 мин.
При одностадийной технологии из полученной шихты формовались полуфабрикаты-гранулы, которые подвергались термической обработке (вспениванию), описанной ниже. При двухстадийной технологии предварительная варка стекла осуществлялась по стекольной технологии и включала следующие стадии: загрузка шихты в шамотный тигель, установка тигля в электрическую муфельную печь при комнатной температуре, нагрев печи до заданной температуры варки со скоростью 5°С/мин, выдержка при температуре варки в течение 1 ч, сухая грануляция (выливание расплава стекла на металлическую гофру). Провар стекла определялся методом “проба на нить” путем опускания огнеупорного стержня из нержавеющей стали в стекломассу и последующего вытягивания нити. При полном проваре получаемая нить должна быть прозрачной, гладкой и не должна содержать гетерогенных включений.
Далее остывшее стекло размалывали до размера частиц менее 250 мкм (прохождение через стандартное сито № 60, что соответствует удельной поверхности 3000 см2/г), добавляли порообразующие и модифицирующие добавки, формовали полуфабрикаты-гранулы, которые подвергали термической обработке – вспениванию. В качестве порообразующей добавки применяли глицерин C3H5(OH)3, а в качестве модифицирующей добавки – техническую контактную серную кислоту H2SO4. Вспенивание гранул осуществлялось согласно графику, представленному на рис. 2 [25, 26].
Рис. 2.
Температурно-временной режим вспенивания: a – одностадийное вспенивание; b – двухстадийное вспенивание; 1 – нагрев; 2 – вспенивание; 3 – резкое охлаждение; 4 – отжиг.
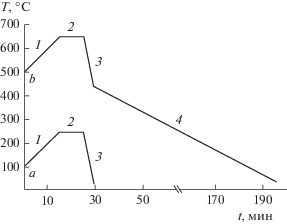
Отличия в режиме вспенивания по одностадийной и двухстадийной технологии заключались в следующем. При вспенивании по одностадийной технологии температура стадии 2 не превышала 300°С, вследствие чего необходимость в отжиге (стадия 4) отсутствовала. Также в зависимости от технологии температура загрузки образцов и температура стадии 2 варьировалась таким образом, чтобы обеспечить разницу между ними 150°С и обеспечение температурой вспенивания вязкости в диапазоне 106–104 Па с.
После извлечения гранул из печи они подвергались исследованию внутренней структуры с использованием оптического микроскопа Bresser Duolux 20x-1280x. Определение кажущейся плотности образцов проводили согласно ГОСТ 9758-2012. Определение химической стойкости к воде проводили согласно методике ВНИИС, основанной на определении количества (мл) 0.01 н. раствора HCl, использованного на титрование 50 мл Н2О, воздействовавшей на 2 г стекла за 1 ч при 100°С [27, с. 321]. Каждая приведенная величина является средним значением пяти параллельных измерений.
Фазовый состав синтезированных образцов определяли с помощью порошкового рентгенофазового анализа. Образцы измельчали и исследовали с помощью рентгеновского порошкового дифрактометра ARL (Thermo Fisher Scientific). Интерпретация данных проводилась с использованием базы данных ICDD (Международный центр дифракционных данных).
РЕЗУЛЬТАТЫ И ИХ ОБСУЖДЕНИЕ
На основе выделенной области стеклования (рис. 1) был разработан ряд составов, представленный в табл. 1. Лимитирующим фактором в целях повышения энергоэффективности технологии была выбрана температура варки, которая должна быть ниже 1000°С. Результаты обжига разработанных составов при данной температуре также представлены в табл. 1 и на рис. 3.
Таблица 1.
Исходные составы фосфатных стекломатриц
Оксид | Содержание оксида, мас. %, в составе № | ||||||||||
---|---|---|---|---|---|---|---|---|---|---|---|
1 | 2 | 3 | 4 | 5 | 6 | 7 | 8 | 9 | 10 | 11 | |
K2O | 18 | 6 | 10 | 18 | 20 | 25 | 35 | 15 | 25 | 25 | 20 |
CaO | 42 | 41 | 30 | 32 | 20 | 22 | 10 | 15 | 15 | 10 | 10 |
P2O5 | 40 | 53 | 60 | 50 | 60 | 53 | 55 | 70 | 60 | 65 | 70 |
Рис. 3.
Динамика плавления фосфатных шихт: 1 – неспеченный порошок; 2 – спек; 3 – пена; 4 – начало плавления; 5 – расплав.

Из таблицы и рисунка видно, что основное влияние на плавкостные свойства стекла оказывают оксиды кальция и фосфора. Так, при соотношении P2O5 : CaO < 1.5 отсутствует даже спекание шихты. При смещении соотношения в сторону P2O5 процессы спекания и плавления интенсифицируются. При соотношении P2O5 : CaO > 3 наблюдается появление расплава, а при соотношении P2O5 : CaO > 6 полное расплавление шихты обеспечивается уже при температуре ниже 800°C. Оксид калия снижает температуру плавления шихты.
Важным является тот факт, что в процессе термической обработки по достижении определенной вязкости шихта всех составов начинала вспениваться. Это подтверждает возможность формирования пористых материалов по одностадийной технологии. Оптимальным среди исследованных составов был выбран состав № 9, на основе которого и проводились дальнейшие исследования. Данный состав, с одной стороны, обладает широким диапазоном стабильности пены при обработке шихты, а с другой стороны, имеет достаточно низкую температуру варки, что обеспечивает повышение энергоэффективности технологии в случае двухстадийного вспенивания.
Была исследована возможность синтеза пористых стекломатриц по одностадийной технологии напрямую из шихты состава № 9. Анализ изменения вязкостных свойств позволил установить интервал размягчения шихты, составивший 200–300°С. Выше данной температуры вязкость стекломассы слишком низка, и пена оседает под собственным весом. Была проведена термическая обработка шихты состава № 9 в данном температурном интервале согласно рис. 2 и исследована плотность и внутренняя структура полученных образцов, представленная на рис. 4.
При различных температурах вспенивания плотность материала составляла: 200°С – 1310 кг/м3; 225°С – 1270 кг/м3; 250°С – 1260 кг/м3; 275°С – 1210 кг/м3; 300°С – 520 кг/м3. Таким образом, плотность материала меняется нелинейно, уменьшаясь за 25°С более чем в 2 раза. Дальнейшее увеличение температуры на 25°С ведет к полному оседанию образца, вследствие чего структуру образцов при температуре выше 300°С изучить практически невозможно. Диагональные трещины на внешней части образцов обусловлены неравномерным распределением давления прессования, что предъявляет особые требования к формованию гранул.
Анализируя изменения внутренней структуры материала, можно обозначить основные этапы формирования пор. При температуре 200°С в материале начинаются процессы твердофазового спекания, завершающиеся при 225°С. При этом возрастает плотность и прочность материала, что усложняет его механическую обработку. При этой же температуре начинается жидкофазовое спекание, что ведет к началу деформации образца. Процессы жидкофазового спекания интенсифицируются с дальнейшим ростом температуры, вязкость материала при этом продолжает снижаться. При температуре 275°С вязкость достигает значений, позволяющих заключенным внутри материала водяным парам образовать зародыши пор, из которых при дальнейшем повышении температуры образуются макропоры. Формирование макропор обеспечивается двумя процессами: увеличение объема отдельных пор, что обусловлено ростом давления паров внутри пор, и коалесценция отдельных пор. Как видно из рисунка, пористая структура крайне неоднородна, размер пор колеблется от 120 до 700 мкм. Подобный тип структуры характерен для пористых материалов, полученных по гидратному механизму, и объясняется высоким сродством порообразователя к стекломассе [23, 28].
Была исследована возможность синтеза пористых стекломатриц по двухстадийной технологии с предварительной варкой стекла. Для этого шихта состава 10 подвергалась варке и выработке согласно описанному выше режиму, после чего на основе полученного стеклопорошка формировались гранулы, содержащие порообразующие и модифицирующие добавки в различных соотношениях, представленных в табл. 2. Синтез полученных образцов проводился согласно рис. 2, плотность синтезированных составов представлена в табл. 2, а их структура – на рис. 5.
Таблица 2.
Шихтовые составы и плотность образцов, синтезированных по двухстадийной технологии
№ | Содержание компонента, мас. % | Плотность образцов, кг/м3, при Т, °С | |||||
---|---|---|---|---|---|---|---|
cтекло | глицерин | серная кислота | 550 | 600 | 650 | 700 | |
9.1 | 95.0 | 5.0 | – | 1221 | 1205 | 1244 | 1315 |
9.2 | 95.0 | 4.5 | 0.5 | 831 | 756 | 714 | 384 |
9.3 | 95.0 | 4.0 | 1.0 | 425 | 312 | 225 | 253 |
Из рис. 5 видно, что введение порообразующей добавки (глицерина) в состав шихты не приводит к вспениванию массы. Более того, цвет исходного бесцветного (белого) стекла меняется на коричнево-черный. Это объясняется термическим разложением глицерина по реакции (3), в результате которой остатки разложения оседают в виде тонкодисперсной сажи, меняя цвет образца. Введение 0.5 мас. % серной кислоты существенно изменяет процессы, протекающие в стекле. При повышении температуры до 600°С в образце появляются белые вспененные участки, что можно объяснить взаимодействием глицерина и серной кислоты.
Газообразование при использовании глицерина происходит за счет его испарения, а также за счет окислительно-восстановительной реакции между углеродным остатком и сульфат-ионами (обычно содержащимися в стекле) по реакции (4). При этом углерод окисляется до CO и CO2, а сульфат-ионы восстанавливаются до сульфидов. Поскольку углерод большей частью окисляется, то он практически не окрашивает стекломассу, и она остается белого цвета. В случае недостатка сульфатной серы (состав 9.2) в результате окислительно-восстановительной реакции углерод частично окисляется, и в таких зонах стекло представляет собой вспененную массу белого цвета. В остальной части образца вспенивание отсутствует, а цвет материала коричневый.
Из рис. 5 видно, что 0.5 мас. % серной кислоты (0.41 мас. % SO3) недостаточно для полного окисления углерода. В структуре образцов четко прослеживаются прореагировавшие и непрореагировавшие участки, отличающиеся по цвету и структуре. При повышении количества серной кислоты до 1 мас. % (0.82 мас. % SO3) в материале исчезают коричневые невспененные участки, что указывает на полное окисление углерода и равномерное вспенивание всего объема образца. Следует также отметить, что сульфат-ионы можно вводить в состав исходной шихты в виде, к примеру, сульфата натрия в количестве 1.5 мас. % (0.84 мас. % SO3). Это позволит упростить технологию смешения смеси и обеспечить равномерное распределение сульфат-ионов в стекломассе.
Поскольку порообразующие и модифицирующие добавки не оказывают влияния на вязкость стекла, то ее изменение в образцах всех трех составов происходит одинаково. В рассмотренном интервале температур 550–700°С стекло находится в вязкопластичном состоянии, вследствие чего материал способен изменять свою форму и размеры. При отсутствии порообразователя образец при нагревании уменьшается в размерах и, в дальнейшем, начинает оседать под собственным весом. При добавлении порообразователя вязкая масса раздувается газами от его разложения и существенно увеличивается в объеме. Однако по достижении температуры 700°С пена также начинает самопроизвольно оседать, поскольку вязкость массы достигла величины ниже 104 Па с [29]. Для исследования внутренней структуры синтезированных образцов состава № 9.3 был проведен микроскопический анализ, представленный на рис. 6.
Из рис. 6 видно, что с повышением температуры размер пор закономерно увеличивается с 70–400 мкм при 600°С до 1–3 мм при 750°С, что обусловлено описанными выше процессами уменьшения вязкости стекломассы и увеличением давления газов внутри пор. Кроме того, в структуре стекла видны темные вкрапления, представляющие собой частицы сажи, вплавленные в межпоровые перегородки. Эти вкрапления повышают стабильность пены, так как углерод обладает малым химическим сродством к стекломассе и выступает в качестве поверхностно-активного вещества [28]. По результатам изучения плотности и структуры материалов оптимальной температурой вспенивания была выбрана температура 650°С, обеспечивающая максимальное вспенивание образцов без оседания пены.
С применением рентгенофазового анализа был исследован фазовый состав фосфатных стекломатриц, синтезированных по одностадийной и двухстадийной технологии. Результаты рентгенофазового анализа представлены на рис. 7.
Рис. 7.
Результаты рентгенофазового анализа синтезированных образцов: a – одностадийное вспенивание; b – двухстадийное вспенивание; 1 – арчерит KH2PO4; 2 – монетит CaHPO4; 3 – KPO3; 4 – KCaP3O9.
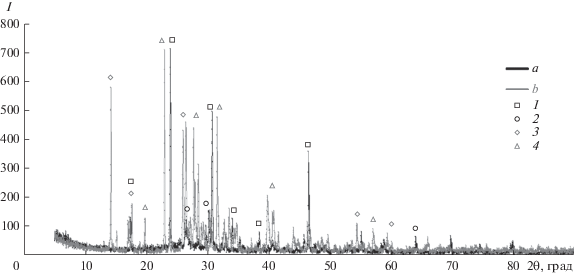
Как видно из рентгенограммы, интенсивность пиков менее 800 ед., высокий фон и аморфное “гало” в области 20°–30° у обоих составов указывают на преобладание в них рентгеноаморфной стеклофазы, причем у стекломатрицы, полученной по двухстадийной технологии, “гало” выше, что ожидаемо указывает на большее количество стеклофазы. При этом фазовый состав материалов, синтезированных по одностадийной и двухстадийной технологии, существенно отличается. При одностадийном низкотемпературном вспенивании кристаллические фазы представлены гидрофосфатами калия и кальция. Это подтверждает гипотезу о вспенивании за счет удаления гидратной воды, а также указывает на ее неполное удаление.
Материал на основе предварительно сваренного стекла представлен кристаллическими фазами фосфата калия и двойного фосфата калия-кальция, причем в обоих случаях фосфаты представлены мета-формой. Это указывает на полное удаление молекул воды при термической обработке. Наличие значительного количества кристаллической фазы после вспенивания довольно необычно, так как исходное стекло было полностью прозрачным, при выработке обладало вязкостью, сопоставимой с вязкостью воды (исходя из динамики выработки), а тест “проба на нить” не выявил никаких гетерогенных включений. Вероятно, формирование кристаллической фазы обусловлено отличиями в изменении вязкости и кристаллизационной способности фосфатных стекол в сравнении с силикатными. Следовательно, необходимо более тщательно исследовать взаимозависимости скорости образования центров кристаллизации, линейной скорости роста кристаллов и вязкости, а также доработать температурно-временные режимы вспенивания, что будет являться целью дальнейших исследований.
Далее была исследована химическая стойкость разработанных материалов к воздействию воды, результаты определения представлены в табл. 3. Показатель количества раствора HCl, пошедшего на титрование, указывает на количество K2O, перешедшего из материала в воду, что, в свою очередь, характеризует скорость выделения нутриентов в почву при внесении удобрения.
Таблица 3.
Результаты определения стойкости материалов к воде
Способ синтеза | Количество раствора HCl на титрование, мл | Гидролитический класс |
---|---|---|
Одностадийное вспенивание | 61.8 | V (неудовлетворительное стекло, более 6.5 мл) |
Двухстадийное вспенивание | 24.8 | V (неудовлетворительное стекло, более 6.5 мл) |
Из табл. 3 видно, что оба вида фосфатных стекломатриц обладают крайне низкой стойкостью к воде и принадлежат к V гидролитическому классу (неудовлетворительные стекла), причем количество перешедшего в раствор K2O многократно превышает нижний предел класса. При этом стойкость материала, синтезированного по одностадийной технологии, в 2.5 раза ниже, чем для стекла, вспененного по двухстадийной технологии. Это, вероятно, объясняется наличием во вспененной шихте фосфатов калия, не вошедших в структуру стекла и потому легко переходящих в раствор. Это может оказывать негативный эффект на свойства получаемых удобрений, поскольку полноту реакции структурообразования в таких шихтах контролировать достаточно проблематично.
Вклад проделанной работы в достижение поставленной цели, а именно в разработку технологии синтеза и вспенивания фосфатных стекломатриц для получения комплексных микроудобрений, заключается в установлении оптимальной области вспенивания исходных шихт, определении наиболее легкоплавкого состава шихты, исследовании особенностей вспенивания фосфатных стекломатриц по одностадийной и двухстадийной технологии, определении их структуры, фазового состава и химической стойкости, а также выработке рекомендаций для получения высокопористых фосфатных стекломатриц.
ЗАКЛЮЧЕНИЕ
Фосфатные стеклоудобрения являются новым перспективным типом удобрений пролонгированного действия. В данной работе рассмотрена возможность увеличения стабильности действия удобрения путем синтеза пористых фосфатных стекломатриц по одностадийной (напрямую из шихты) и двухстадийной (вспенивание предварительно сваренного стекла) технологии. На основе трехкомпонентной системы K2O–CaO–P2O5 была выбрана область стеклообразования, разработаны исходные составы и проведена их термическая обработка. На основе полученных результатов выбран оптимальный состав шихты, пригодный для вспенивания согласно обеим технологиям.
Результаты синтеза по одностадийной технологии показали, что вспенивание шихты происходит весьма интенсивно, уменьшаясь за 25°С более чем в 2 раза, а дальнейшее увеличение температуры на 25°С ведет к полному оседанию образца. При этом пористая структура крайне неоднородна, размер пор колеблется в пределах 120–700 мкм. Подобный тип структуры объясняется высоким сродством порообразователя к стекломассе.
Вспенивание по двухстадийной технологии включало предварительную варку стекла, составление шихты, состоящей из стекла и модифицирующих добавок, и ее вспенивание. Установлено, что введение порообразующей добавки в состав шихты не приводит к вспениванию массы, а цвет меняется на коричнево-черный, что объясняется оседанием остатков от термического разложения глицерина. Дополнительное введение модифицирующей добавки серной кислоты ведет к формированию белых вспененных участков за счет окислительно-восстановительной реакции между углеродным остатком и сульфат-ионами. При этом углерод окисляется до CO и CO2, формируя порообразующие газы и потому не изменяя окраску стекла. Установлено, что для полного окисления порообразователя достаточно 1 мас. % H2SO4. Микроскопический анализ образцов показал, что с повышением температуры размер пор закономерно увеличивается с повышением температуры. Также в структуре стекла выявлены темные вкрапления, представляющие собой частицы сажи, вплавленные в межпоровые перегородки и повышающие стабильность пены.
С применением рентгенофазового анализа был исследован фазовый состав фосфатных стекломатриц, синтезированных по одностадийной и двухстадийной технологии. Выявлено, что у обоих составов преобладает рентгеноаморфная стеклофаза, на что указывает низкая интенсивность пиков, высокий фон и аморфное “гало” в области 20°–30°. Фазовый состав материалов существенно отличается: при одностадийном низкотемпературном вспенивании кристаллические фазы представлены гидрофосфатами калия и кальция за счет неполного удаления гидратной воды, а материал на основе предварительно сваренного стекла представлен кристаллическими фазами фосфата калия и двойного фосфата калия-кальция, причем в мета-форме, что указывает на полное удаление молекул воды при термической обработке.
Результаты исследования химической стойкости разработанных материалов к воздействию воды показали, что оба вида фосфатных стекломатриц обладают крайне низкой стойкостью к воде и принадлежат к V гидролитическому классу (неудовлетворительные стекла). Стойкость материала, синтезированного по одностадийной технологии, в 2.5 раза ниже, чем для стекла, полученного по двухстадийной технологии, что объясняется наличием во вспененной шихте фосфатов калия, не вошедших в структуру стекла и потому легко переходящих в раствор.
Таким образом, на основании спектра проведенных исследований можно заключить, что более пригодной для синтеза фосфатных стекломатриц является двухстадийная технология, позволяющая получить стеклообразный материал с контролируемой скоростью выхода нутриентов и возможностью в широких пределах варьировать размер пор. Вклад проделанной работы в достижение цели исследования заключается в установлении склонности фосфатных шихт к вспениванию и плавлению, исследовании особенностей их вспенивания по одностадийной и двухстадийной технологии, определении структуры, состава и свойств полученных пористых материалов, а также выработке рекомендаций для получения высокопористых фосфатных стекломатриц.
Работа выполнена при финансовой поддержке Российского научного фонда (проект № 19-79-00015).
ОБОЗНАЧЕНИЯ
Список литературы
Sigurnjak I., Michels E., Crappé S. Utilization of derivatives from nutrient recovery processes as alternatives for fossil-based mineral fertilizers in commercial greenhouse production of Lactuca sativa L. // Sci. Hortic. (Amsterdam, Neth.). 2016. V. 198. P. 267.
Li X., Lei Z., Qu J. et al. Synthesizing slow-release fertilizers via mechanochemical processing for potentially recycling the waste ferrous sulfate from titanium dioxide production // J. Environ. Manage. 2017. V. 186. Part 1. P. 120.
İpek M., Aras S., Arıkan Ş. et al. Root plant growth promoting rhizobacteria inoculations increase ferric chelate reductase (FC-R) activity and Fe nutrition in pear under calcareous soil conditions // Sci. Hortic. (Amsterdam, Neth.). 2017. V. 219. P. 144.
Ghasemi S., Khoshgoftarmanesh A., Afyuni M., Hadadzadeh H. Iron(II)–amino acid chelates alleviate salt-stress induced oxidative damages on tomato grown in nutrient solution culture // Sci. Hortic. (Amsterdam, Neth.). 2014. V. 165. P. 91.
Nikolić J.D., Živanović V.D., Matijašević S.D. et al. Crystallization and sintering behaviors of the polyphosphate glass doped with Zn and Mn // J. Therm. Anal. Calorim. 2016. V. 124. P. 585.
Wacławska I., Szumera M., Stoch P., Sitarz M. Structural role of Fe in the soil active glasses // Spectrochim. Acta, Part A. 2011. V. 79. P. 728.
Hazra G., Das T. A Review on Controlled Release Advanced Glassy Fertilizer // Global J. Sci. Front. Res., B: Chem. 2014. V. 14. № 4. P. 33.
Szumera M., Wacławska I., Olejniczak Z. Influence of B2O3 on the structure and crystallization of soil active glasses // J. Therm. Anal. Calorim. 2010. V. 99. P. 879.
Lee H., Hwang S., Kang W. Preparation of K2O–CaO–P2O5 eco-glass fertilizers and effect in crops // Mater. Sci. Forum. 2005. V. 486–487. P. 407.
Vujošević A., Matijašević S., Smiljanić S. et al. Polyphosphate glass as fertilizer for plant seedlings // Zast. Mater. 2019. V. 60. № 1. P. 96.
Kosareva I.A., Tkachenko K.G., Karapetjan G.O. et al. Comparative analysis of impact of the complex vitreous fertilizers with microelements on the microflora of sod-podzolic and peat soils // J. Plant Nutr. 2006. V. 29. № 5. P. 933.
Kogan V.E., Karapetyan K.G. Theoretical Analysis of the Influence of Particle Size Distribution on the Kinetics of the Dissolution of Phosphorus-Containing Vitreous Fertilizers // Glass Phys. Chem. 2018. V. 44. № 5. P. 394.
ООО “Вита-АВА” (2020) Удобрения AVA от производителя. https://avamarket.com. Дата обращения: 17.05.2020.
Vujošević A., Matijašević S., Smiljanić S. et al. Polyphosphate glass as fertilizer for plant seedlings // Zast. Mater. 2019. V. 60. № 1. P. 96.
Tošić M.B., Nikolić J.D., Grujić S.R. et al. Dissolution behavior of a polyphosphate glass into an aqueous solution under static leaching conditions // J. Non-Cryst. Solids. 2013. V. 362. P. 185.
Petropavlovskii I.A., Pochitalkina I.A., Ryashko A.I. Graphic Study of the Dihydrate–Hemihydrate Process for the Synthesis of Phosphoric Acid According to the Diagram of the CаO–P2O5–SO3–H2O System // Theor. Found. Chem. Eng. 2019. V. 53. № 3. P. 364. [Петропавловский И.А., Почиталкина И.А., Ряшко А.И. Графическое исследование дигидратно-полугидратного процесса получения фосфорной кислоты по диаграмме системы CаO–P2O5–SO3–H2O // Теор. осн. хим. технол. 2019. Т. 53. № 3. С. 276.]
Zhang Y., Santos J.D. Crystallization and microstructure analysis of calcium phosphatebased glass ceramics for biomedical applications // J. Non-Cryst. Solids. 2000. V. 272. P. 14.
Амосов А.В., Джураев Н.Д., Дуботовко О.Е. и др. Стеклообразное гранулированное удобрение пролонгированного действия на основе фосфатного стекла. Пат. 1742276 РФ. 1992.
Докукина А.Ф., Карапетян Г.О., Карапетян К.Г. и др. Комплексное стеклянное удобрение пролонгированного действия и способ его получения. Пат. 2206552 РФ. 2001.
Лазарев Е.В. Способ получения пеностекла. Пат. 2701951 РФ. 2019.
Фефелов А.Б., Никулин М.Л. Фракционный утеплитель из вспененного стекла для железнодорожного строительства. Пат. 2681157 РФ. 2019.
Демидович Б.К. Пеностекло. Минск: Наука и техника, 1975.
Шилл Ф. Пеностекло. М.: Стройиздат, 1965.
Yatsenko E.A., Gol’tsman B.M., Kosarev A.S. et al. Synthesis of Foamed Glass Based on Slag and a Glycerol Pore-Forming Mixture // Glass Phys. Chem. 2018. V. 44. № 2. P. 152. [Яценко Е.А., Гольцман Б.М., Косарев А.С. и др. Синтез пеностекла с использованием шлаков и глицериновой порообразующей смеси // Физ. хим. стекла. 2018. Т. 44. № 2. С. 199.]
Goltsman B.M., Yatsenko L.A., Goltsman N.S. Production of foam glass materials from silicate raw materials by hydrate mechanism // Solid State Phenom. 2020. V. 299. P. 293.
Yatsenko E.A., Ryabova A.V., Goltsman B.M. Development of fiber-glass composite coatings for protection of steel oil pipelines from internal and external corrosion // Chern. Met. 2019. № 12. P. 46. [Яценко Е.А., Рябова А.В., Гольцман Б.М. Разработка стеклокомпозиционных покрытий для защиты стальных нефтепроводов от внутренней и внешней коррозии // Черн. мет. 2019. № 12. С. 46.]
Справочник химика. Т. 5. Л.: Химия, 1966.
Жабрев В.А., Чуппина С.В., Катенев Е.В. Межфазные реакции силикатной матрицы с фосфатными составляющими при формировании пеностекла // Изв. С.-Петерб. гос. технол. инст. (тех. унив.). 2016. № 33. С. 8.
Sarkisov P.D., Vinokurov E.G., Gradova N.B., Babusenko E.S., Bondar’ V.V. Bioengineering of glass surface // Theor. Found. Chem. Eng. 2013. V. 47. № 1. P. 14. [Саркисов П.Д., Винокуров Е.Г., Градова Н.Б., Бабусенко Е.С., Бондарь В.В. Инженерная биотехнология поверхности стекла // Теор. осн. хим. технол. 2013. Т. 47. № 1. С. 18.]
Дополнительные материалы отсутствуют.
Инструменты
Теоретические основы химической технологии