Теоретические основы химической технологии, 2021, T. 55, № 4, стр. 496-505
Термодинамические аспекты использования элементного фтора в качестве фторирующего агента
Д. С. Пашкевич a, *, П. С. Камбур b, В. В. Капустин b, Н. А. Белов b, Ю. И. Алексеев c, Д. А. Мухортов c, В. Б. Петров d
a Санкт-Петербургский политехнический университет Петра Великого
Санкт-Петербург, Россия
b Томский политехнический университет
Томск, Россия
c ООО “Новые химические продукты”
Санкт-Петербург, Россия
d РНЦ “Прикладная химия”
Санкт-Петербург, Россия
* E-mail: pashkevich-ds@yandex.ru
Поступила в редакцию 27.07.2020
После доработки 10.12.2020
Принята к публикации 18.12.2020
Аннотация
Фторирование простых веществ, неорганических и органических соединений элементным фтором сопровождается высоким тепловыделением (порядка сотен килоджоулей на моль фтора), что определяет высокую вероятность их реализации в нестационарном тепловом режиме (режиме горения или теплового взрыва), когда температура продуктов процесса близка к адиабатической и значительную часть выделившегося тепла отводят от полученных веществ вне зоны реакции. Если целевые фториды присутствуют в термодинамически равновесной смеси веществ в системе элементов, содержащей фтор, при температуре, близкой к адиабатической, то фторирование в режиме горения успешно используют в промышленности. В противном случае целесообразно проводить фторирование в стационарном (близком к изотермическому) тепловом режиме, отводя тепло реакции от реагирующей смеси непосредственно в зоне реакции. В статье рассмотрена эффективность применения стационарного и нестационарного теплового режима при фторировании различных веществ элементным фтором.
ВВЕДЕНИЕ
Элементный фтор находит широкое применение в современной химической технологии в качестве фторирующего агента. Его используют для получения целого ряда коммерчески значимых фторсоединений, в том числе: гексафторид урана UF6 для процесса изотопного обогащения природного урана; гексафторид серы SF6, газовый диэлектрик для электротехнического оборудования; трифторид азота NF3, тетрафторид углерода CF4, октафторпропан C3F8, реагенты для травления кремния в промышленности полупроводников; гексафторид вольфрама WF6, газообразный носитель вольфрама для формирования пленок вольфрама; тетрафторид серы SF4, фторирующий агент; гексафториды селена SeF6, теллура TeF6, иридия IrF6, трифторид бора BF3, тетрафторид германия GeF4 и др. для промышленности изотопов; пентафторид фосфора PF5 и полифторид углерода (CFx)n, которые используют при производстве компонентов литиевых источников тока; фториды хлора, йода и брома, которые используют для очистки поверхностей от отложений соединений урана; 5-фторурацил C4H3FN2O2, противоопухолевый препарат; поверхностно модифицированные фтором полимерные изделия с улучшенными эксплуатационными характеристиками.
Процессы фторирования практически всех простых веществ и соединений элементным фтором термодинамически не запрещены, в отличие, например, от наиболее распространенного фторирующего агента фторида водорода, с помощью которого нельзя получить, в том числе из оксидов и фторидов урана, гексафторид урана или заместить водород на фтор в углеводородах. Поэтому фтор, как наиболее электроотрицательный элемент, является универсальным фторирующим агентом. Однако фторирование элементным фтором сопровождается тепловыделением порядка сотен килоджоулей на моль фтора, и процессы с его участием часто протекают в нестационарном тепловом режиме (режиме горения), когда температура в зоне реакции близка к адиабатической и составляет величину порядка 103 К.
Если в термодинамически равновесной смеси веществ для заданной системы элементов, включающей фтор, при температуре, близкой к адиабатической для исследуемой реакции фторирования, целевые фториды присутствуют в технологически приемлемой концентрации, то режим горения исходных веществ во фторе с успехом применяют для производства фторсоединений. В этом случае поток продуктов процесса охлаждают в основном вне зоны реакции, и скорость охлаждения не имеет принципиального значения.
Режим горения также эффективен, если в зоне реакции при достаточно высокой температуре часть целевого фторида подвергается диссоциации с образованием радикала фтора и фторида низшей валентности или радикала фторида
которые рекомбинируют при охлаждении продуктов процесса горения с образованием целевого фторида.
Обычно фториды являются веществами достаточно термостабильными. Например, согласно расчетам, проведенным с использованием программного комплекса “АСТРА.4” [1, 2] (рис. 1), термическая диссоциация фторида водорода становится заметной лишь при температуре выше 2500 К, а при 4000 К HF диссоциирован на 40%, что хорошо согласуется с результатами, приведенными в [3].
Рис. 1.
Зависимость состава веществ в системе элементов H–F и степень диссоциации фторида водорода η в термодинамически равновесной смеси в зависимости от температуры: 1 – CM(HF), 2 – CM(F), 3 – CM(H), 4 – CM(H2), 5 – η(HF).
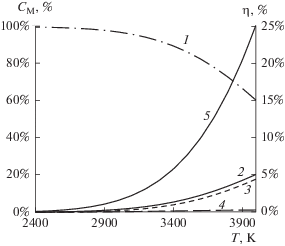
Поэтому в режиме горения получают целый ряд промышленных фторсоединений – UF6, SF6, CF4, WF6, SF4 и др. [4, 5].
Режим горения характеризуется высокой удельной производительностью реакционного объема, так как в зоне реакции достигается температура порядка 2000–3000 К и характерные времена превращения веществ при, например, гомогенном горении (t ∝ u–1 δ, где u – скорость нормального распространения фронта пламени, δ – толщина ламинарного пламени) могут составлять величину порядка 10–3–10–5 с [6]. При диффузионном газофазном и гетерогенном горении скорость реакции расходования фтора определяется скоростью его диффузии ко фторируемому веществу, например, для неподвижного слоя частиц конденсированной фазы (слоевое сжигание) с характерным размером порядка 100–1000 мкм характерное время диффузии (t ∝ l2D–1, где l – характерный размер переноса, D – коэффициент диффузии) может составлять 10–2–10–3 с [7].
Для реакционной системы твердое вещество – фтор слоевое сжигание является наиболее удобным и высокопроизводительным методом фторирования. Однако, если синтезированный фторид может выступать в качестве фторирующего агента по отношению ко фторируемому веществу, то вне зоны фторирования возможно восстановление полученного фторида, и тогда целесообразно применять факельный вид горения, когда оба реагента – и фтор, и фторируемый порошок – подают в зону реакции одновременно в соотношении, близком к стехиометрическому, по аналогии со слоевым и факельным сжиганием углерода в кислороде [8].
Если же при температуре, близкой к адиабатической, целевые вещества в термодинамически равновесной смеси отсутствуют, то фторирование целесообразно проводить в стационарном тепловом режиме, когда скорость теплоотвода из зоны реакции равна скорости тепловыделения и температура существенно ниже адиабатической – получение фторуглеродов из простых веществ [9, 10], трифторида азота [11], 5-фторурацила [12], поверхностная модификация полимерных изделий газообразным фтором [13], развивающийся в последнее время метод фторирования органических соединений раствором фтора в перфторированной жидкости [14–16].
В стационарном тепловом режиме температура в зоне реакции (и, следовательно, скорость фторирования) существенно ниже, чем в режиме горения. Так, в [17] показано, что при недеструктивном водородзаместительном фторировании CF3CFH2 при температуре 373–423 K в режиме, близком к изотермическому, характерное время реакции составляет десятки и сотни секунд, что на 3–4 порядка выше, чем в режиме горения. Поэтому удельная производительность реактора, работающего в стационарном тепловом режиме, существенно ниже, чем работающего в режиме горения.
Для обеспечения высокого значения теплового потока из зоны реакции в реакторе, работающем в стационарном тепловом режиме, обычно для систем с твердой и жидкой фазой используют интенсивное перемешивание так, чтобы обеспечить значения коэффициента теплоотдачи на уровне 102–103 Вт м–2 К–1 [9, 10, 31]. Если же фторируемое вещество является газообразным, то возможно проводить процесс в стационарном тепловом режиме в газожидкостном реакторе с интенсивным перемешиванием, где в качестве жидкой фазы используют перфторированные вещества, достаточно инертные по отношению ко фтору [15].
Возможен также вариант реализации синтеза фторидов в режиме горения во фторе, когда в термодинамически равновесной смеси целевые вещества отсутствуют. Так, предложен метод водородзаместительного фторирования фторэтанов элементным фтором в режиме горения, где, например, из 1,1,1,2-C2F4H2 получают C2F5H и C2F6, хотя в термодинамически равновесной смеси в системе элементов C–H–3F эти вещества отсутствуют [18, 19]. Этого удается достичь, достаточно интенсивно охлаждая поток продуктов и обеспечивая предварительное смешение фтора и CF3CFH2, экспериментально выбирая концентрацию фтора (находящегося в недостатке) в реагирующей смеси таким образом, чтобы температура во фронте пламени была относительно низка и С–С связь практически не подвергалась фторированию.
Целью данной работы является термодинамический анализ фторирования элементным фтором веществ, находящихся в различном фазовом состоянии, на основании которого можно сделать вывод об эффективности использования стационарного и нестационарного теплового режима фторирования при промышленном освоении процесса получения фторидов.
ФТОРИРОВАНИЕ ЭЛЕМЕНТНЫМ ФТОРОМ В НЕСТАЦИОНАРНОМ ТЕПЛОВОМ РЕЖИМЕ
Гексафторид урана. Промышленную технологию получения элементного фтора электролизом фторидов калия разрабатывали для реализации процесса получения UF6 [20]. Гексафторид урана является единственным известным термодинамически стабильным летучим соединением урана, которое применяют в технологиях изотопного обогащения природного урана газодиффузионным и газоцентрифужным методами. Получить UF6 из других соединений урана возможно только с применением фтора, поэтому это вещество является критическим для технологий изотопного обогащения урана.
В настоящее время UF6 получают фторированием порошкообразных октаоксида триурана (Тm = 1423 К) или тетрафторида урана (Тm = 1309 К):
(2)
${{{\text{U}}}_{{\text{3}}}}{{{\text{O}}}_{{{\text{8s}}}}} + 9{{{\text{F}}}_{{{\text{2g}}}}} \to 3{\text{U}}{{{\text{F}}}_{{{\text{6g}}}}} + 4{{{\text{O}}}_{{{\text{2g}}}}}--2871.1\,\,\,{\text{кДж}},$(3)
${\text{U}}{{{\text{F}}}_{{{\text{4s}}}}} + {{{\text{F}}}_{{{\text{2g}}}}} \to {\text{U}}{{{\text{F}}}_{{{\text{6g}}}}}--228.1\,\,\,{\text{кДж}}.$Тепловые эффекты процессов (2) и (3) весьма высоки и адиабатическая температура их продуктов без учета диссоциации может достигать величин более 4000 и порядка 1800 К соответственно.
В табл. 1 приведены составы термодинамически равновесных смесей в системах элементов U–F–O для различной температуры, рассчитанные с использованием программного комплекса “АСТРА.4”.
Таблица 1.
Термодинамически равновесный состав веществ в системах элементов U–F и U–F–O для различной температуры при атмосферном давлении
Соотношение атомов | Т, К | CM, мол. % | ||||||||||
---|---|---|---|---|---|---|---|---|---|---|---|---|
UF6 | UF5 | UF4 | F2 | F | O2 | UO2F | UOF2 | UO2F2 | UOF3 | UOF4 | ||
U–6F | 1000 | 99.7% | 0.2% | – | – | 0.1% | – | – | – | – | – | – |
1500 | 46.7% | 27.1% | – | 0.9% | 25.3% | – | – | – | – | – | – | |
2000 | 0.6% | 49.8% | – | 0.1% | 49.5% | – | – | – | – | – | – | |
U–4F | 1000 | – | – | 100.0% | – | – | – | – | – | – | – | – |
1500 | – | – | 100.0% | – | – | – | – | – | – | – | – | |
2000 | – | 0.2% | 99.8% | – | – | – | – | – | – | – | – | |
U–6F–2O | 1000 | 49.8% | 0.1% | – | – | 0.1% | 49.9% | – | – | – | – | – |
1500 | 22.4% | 18.6% | – | 0.4% | 17.7% | 40.9% | – | – | – | – | – | |
2000 | 0.3% | 33.1% | – | 0.1% | 33.1% | 33.4% | – | – | – | – | – | |
U–5F–2O | 1000 | 0.1% | 49.8% | – | – | – | 50.0% | – | – | – | – | 0.1% |
1500 | 0.1% | 49.9% | – | – | – | 50.0% | – | – | – | – | – | |
2000 | – | 48.4% | 0.7% | – | 1.3% | 49.2% | – | – | – | 0.3% | 0.1% | |
U–4F–2O | 1000 | – | 49.6% | – | – | – | 49.8% | – | – | 0.2% | – | 0.4% |
1500 | – | 32.0% | 0.4% | – | – | 41.6% | 0.1% | – | 7.5% | 16.8% | 1.6% | |
2000 | – | 28.0% | 4.6% | – | 0.1% | 43.0% | 0.5% | 0.3% | 2.9% | 20.0% | 0.6% |
Из результатов расчета следует, что если на 1 атом урана приходится 6 или более атомов фтора, то при температуре порядка 1000 К UF6 является практически единственным урансодержащим веществом. При температуре порядка 2000 К в термодинамически равновесной смеси основным урансодержащим веществом является UF5 и имеет место практически эквимольное количество атомарного фтора. Можно предположить, что при охлаждении термодинамически равновесной смеси ниже 1000 К UF5 и F рекомбинируют с образованием UF6.
Если же количество атомов фтора, приходящихся на 1 атом урана, менее 6, то в термодинамически равновесной смеси присутствуют UF4, UF5, UO2F, UOF2, UO2F2, UOF3, UOF4 при практически полном отсутствии свободного фтора, как молекулярного, так и атомарного.
Поэтому синтез UF6 по схемам (2) и (3) целесообразно проводить в режиме горения. Из результатов термодинамического расчета следует, что при слоевом сжигании октаоксида триурана или тетрафторида урана во фторе возможно восстановление UF6, например, с образованием UF5, за пределами фторной зоны, т.е. UF6 может выступать в качестве фторирующего агента по отношению к низшим оксидам, фторидам и оксифторидам урана, что может привести к наличию в продуктах процесса низших фторидов урана. Поэтому процесс горения U3O8 или UF4 во фторе осуществляют в факельном режиме, подавая твердые соединения урана и фтор в верхнюю часть вертикального реактора типа “туннельная горелка” в соотношении, близком к стехиометрическому, когда в зоне реакции температура близка к адиабатической, а охлаждение потока продуктов осуществляют вне зоны реакции [21, 22].
В реакторе типа “туннельная горелка” скорость переработки фтора при производстве UF6 из U3O8 в режиме горения составляет величину порядка 500 мг с–1 л–1.
Тетрафторид углерода. Известно, что при взаимодействии углерода и фтора при различной температуре могут быть получены различные фторуглероды [12]:
(4)
$\begin{gathered} {{{\text{C}}}_{{\text{s}}}} + {\text{ }}0.5{{{\text{F}}}_{{{\text{2g}}}}} \to {\text{ }}{{({\text{C}}{{{\text{F}}}_{х}})}_{n}}, \hfill \\ {\text{где}}\,\,х \approx 1,\,\,\,Т \approx 700{\kern 1pt} --{\kern 1pt} 800\,\,{\text{К}}, \hfill \\ \end{gathered} $(5)
$\begin{gathered} {{{\text{C}}}_{{\text{s}}}} + {{a}_{1}}{{{\text{F}}}_{{{\text{2g}}}}} \to {{b}_{1}}{\text{C}}{{{\text{F}}}_{{{\text{4g}}}}} + {{b}_{2}}{{{\text{C}}}_{{\text{2}}}}{{{\text{F}}}_{{{\text{6g}}}}} + {{b}_{3}}{{{\text{C}}}_{{\text{3}}}}{{{\text{F}}}_{{{\text{8g}}}}} + \ldots , \\ Т \approx 800{\kern 1pt} --{\kern 1pt} 900\,\,\,{\text{К}}, \\ \end{gathered} $(6)
${{{\text{C}}}_{{\text{s}}}} + 2{{{\text{F}}}_{{{\text{2g}}}}} \to {\text{C}}{{{\text{F}}}_{{{\text{4g}}}}}--933\,\,\,{\text{кДж}},\,\,\,Т > 1000\,\,\,{\text{К}}.$Адиабатическая температура продуктов процесса (6) без учета диссоциации существенно превышает 4000 К, при которой степень диссоциации молекулярных структур должна быть значительной.
В табл. 2 приведены термодинамически равновесные составы веществ в системе элементов С–F в зависимости от температуры. При Т < 2000 К практически единственным фторуглеродом является CF4. Вещества с количеством атомов углерода более одного, а также полифторид углерода (CFx)n отсутствуют. При температуре выше 2500 К в термодинамически равновесной смеси присутствуют фторметильные радикалы, атомарный фтор и дифторацетилен.
Таблица 2.
Термодинамически равновесный состав веществ в системах элементов С–F для различной температуры при атмосферном давлении
Соотношение атомов | Т, К | CM, мол. % | ||||||
---|---|---|---|---|---|---|---|---|
СF4 | C2F2 | CF3 | CF2 | CF | F | Cтв | ||
С–4F | 1500 | 100.0% | – | – | – | – | – | – |
2000 | 99.5% | – | 0.1% | 0.1% | – | 0.3% | – | |
2500 | 82.4% | 0.1% | 1.6% | 4.6% | – | 11.3% | – | |
3000 | 8.9% | 2.1% | 2.3% | 22.3% | 1.1% | 63.3% | – | |
С–F | 1500 | 25.0% | – | – | – | – | – | 75.0% |
2000 | 24.8% | 0.1% | 0.1% | 0.2% | – | – | 74.8% | |
2500 | 19.1% | 4.5% | 0.9% | 6.7% | 0.1% | 1.5% | 67.2% | |
3000 | 1.3% | 19.4% | 0.8% | 20.5% | 2.7% | 14.8% | 40.5% |
Термическая диссоциация CF4:
(7)
${\text{C}}{{{\text{F}}}_{{\text{4}}}} \leftrightarrow {\text{CF}}_{{\text{3}}}^{\centerdot } + {\text{F}}$становится заметной лишь при температуре выше 2400 К, рис. 2. Поэтому получение CF4 целесообразно проводить в режиме слоевого сжигания углерода во фторе.
Рис. 2.
Зависимость состава веществ в системе элементов C–4F в термодинамически равновесной смеси в зависимости от температуры: 1 – CF4, 2 – F, 3 – CF2, 4 – CF3, 5 – C2F2, 6 – CF.
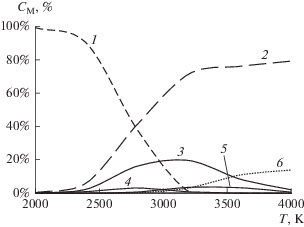
Промышленный синтез CF4 осуществляют в режиме фильтрационного горения, подавая фтор в неподвижный слой порошкообразного углерода, по схеме (6) [4].
При эксплуатации промышленного реактора с неподвижным слоем порошка графита, в котором исключен контакт высокотемпературной зоны реакции с термостатированными поверхностями реактора, и погруженной в слой порошка термостатированной форсункой для подачи фтора, CF4 был получен в качестве единственного фторуглерода в процессе фильтрационного горения. Это свидетельствует о том, что температура в зоне фильтрационного горения не превышала величину порядка 2000–2500 К. Термостабилизация зоны реакции на указанном уровне была достигнута на основе теплового излучения высокотемпературного слоя углерода на охлаждаемую форсунку при варьировании расхода фтора. Таким образом, в этом случае в режиме слоевого сжигания синтезировали вещество, соответствующее термодинамическому равновесию.
В реакторе слоевого сжигания зона реакции обычно имеет существенно меньший размер, чем характерный размер реактора. Известно, что при окислении порошкообразного углерода кислородом в режиме горения ширина кислородной зоны обычно составляет единицы и десятки миллиметров и зависит в основном от размера зерен углерода [23]. Также известно, что коэффициент диффузии D ∝ M–0.5, где M – молекулярный вес [24]. Следовательно, коэффициент диффузии фтора в тетрафториде углерода будет примерно на 20% ниже аналогичного показателя для диоксида углерода и кислорода.
В промышленном реакторе по синтезу CF4 характерный размер зерен графита составлял величину порядка 5 мм, таким образом, толщина зоны конверсии фтора составляла около 30 мм. При характерном размере реактора 1 м удельная производительность зоны реакции по конверсии фтора составляет 150 мг с–1 л–1.
Гексафторид серы. Другой весьма распространенный в химической технологии процесс – получение гексафторида серы из простых веществ.
При взаимодействии серы и фтора в зависимости от условий взаимодействия могут быть получены различные фториды серы [5]:
(8)
$\begin{gathered} {\text{S}} + {{a}_{1}}{{{\text{F}}}_{{\text{2}}}} \to {{b}_{1}}{\text{S}}{{{\text{F}}}_{6}} + {{b}_{2}}{\text{S}}{{{\text{F}}}_{4}} + \\ + \,\,{{b}_{3}}{{{\text{S}}}_{{\text{2}}}}{{{\text{F}}}_{{10}}} + {{b}_{4}}{\text{S}}{{{\text{F}}}_{2}} + {{b}_{5}}{{{\text{S}}}_{{\text{2}}}}{{{\text{F}}}_{2}}, \\ \end{gathered} $наибольшее промышленное значение среди которых имеет SF6, газовый диэлектрик в электротехническом оборудовании [25].
Тепловой эффект реакции:
таков, что температура продуктов может существенно превышать 4000 К, поэтому при контакте серы и фтора высока вероятность реализации режима горения.
В табл. 3 приведены результаты расчета термодинамически равновесного состава веществ в системе элементов S–F для различной температуры.
Таблица 3.
Термодинамически равновесный состав веществ в системе элементов S–F при различном количестве атомов и для различной температуры при атмосферном давлении
Соотношение атомов | Т, К | CM, мол. % | ||||||
---|---|---|---|---|---|---|---|---|
SF6 | SF5 | SF4 | SF3 | SF2 | F2 | F | ||
S–6F | 1000 | 100.0% | – | – | – | – | – | – |
1500 | 88.7% | 1.0% | 3.1% | – | – | – | 7.2% | |
2000 | 0.5% | 1.3% | 23.1% | 5.2% | 1.4% | 0.2% | 68.3% | |
S–4F | 1000 | 3.9% | – | 90.5% | 3.2% | 2.3% | – | – |
1500 | 4.8% | 1.1% | 84.6% | 7.2% | 1.9% | – | 0.3% | |
2000 | 0.1% | 0.8% | 33.8% | 17.3% | 10.6% | – | 37.3% |
Согласно табл. 3, при соотношении элементов S–6F диссоциация SF6 с образованием низших фторидов, в основном SF4, и атомарного фтора не существенна при температуре ниже 1500 К. Если же соотношение атомов составляет S–4F, то основным фторидом серы в широком диапазоне температуры является SF4. Поэтому целесообразно проводить синтез SF6 из простых веществ в режиме факельного горения, подавая серу и фтор в зону реакции в близком к стехиометрии соотношении.
Жидкая сера (Тm = 386 K, Тe = 719 K) характеризуется аномальной зависимостью вязкости от температуры – в интервале температуры 407–465 K вязкость возрастает почти в 5000 раз, достигая 93 Па с, при дальнейшем повышении температуры медленно снижается. Поэтому использование форсунки для подачи серы в зону ее контакта со фтором в дисперсно-капельном состоянии затруднено и на промышленном уровне процесс горения серы во фторе был реализован в горизонтальном реакторе диаметром 400 мм и длиной 3 м, заполненном жидкой серой так, что в верхней части оставался газовый сегмент, в который подавали под углом к поверхности расплава серы [26]. Взаимодействие серы и фтора протекало в режиме газофазного диффузионного горения при этом конфигурацию струи фтора (в основном угол ее наклона к поверхности расплава серы и диаметр сопла) экспериментально подбирали так, чтобы расходы фтора и испаряющейся серы примерно соответствовали соотношению S–6F. Основным продуктом процесса был SF6 при избытке фтора не более 10%. Производительность газового сегмента реактора по фтору составляла величину порядка 10 мг с–1 л–1.
Трифторид хлора. Примером газофазного фторирования, реализуемого в режиме горения, является получение ClF3 из простых веществ.
Известно, что при взаимодействии хлора и фтора в зависимости от условий могут быть получены различные фториды хлора [27]:
(10)
${\text{C}}{{{\text{l}}}_{{{\text{2g}}}}} + {{a}_{1}}{{{\text{F}}}_{2}} \to {{b}_{1}}{\text{Cl}}{{{\text{F}}}_{{\text{g}}}} + {{b}_{2}}{\text{Cl}}{{{\text{F}}}_{{{\text{3g}}}}} + {{b}_{3}}{\text{Cl}}{{{\text{F}}}_{{{\text{5g}}}}}.$Наиболее востребованным является трифторид хлора ClF3, который рассматривали в качестве окислителя в ракетной технике, а сейчас применяют для очистки трактов газовых центрифуг от отложений фторидов и оксифторидов урана [28, 29].
Тепловой эффект реакции получения ClF3
(11)
${\text{C}}{{{\text{l}}}_{{{\text{2g}}}}} + 3{{{\text{F}}}_{2}} \to 2{\text{Cl}}{{{\text{F}}}_{{{\text{3g}}}}}$составляет –329.2 кДж и адиабатическая температура продуктов может составлять около 2300 К.
На рис. 3 представлен термодинамически равновесный состав веществ в системе элементов Cl–3F при атмосферном давлении в зависимости от температуры. В равновесной смеси присутствуют ClF и ClF3, а ClF5 практически отсутствует, при температуре выше 600–700 К ClF3 подвергается диссоциации с образованием молекулярного фтора и ClF.
Рис. 3.
Термодинамически равновесный состав веществ в системе элементов Cl-3F в зависимости от температуры: 1 – ClF3, 2 – F2, 3 – F, 4 – ClF, 5 – Cl.
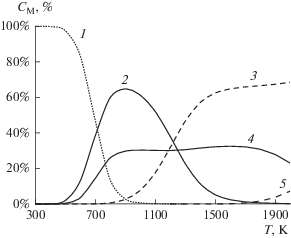
Поэтому синтез ClF3 осуществляют в режиме горения в реакторе типа “туннельная горелка”, подавая в зону горения хлор и фтор по стехиометрии процесса (11). За зоной горения располагают зону термостабилизации, в которой поддерживают температуру стенки на уровне 473–573 К, обеспечивая протекание экзотермического процесса
(12)
${\text{Cl}}{{{\text{F}}}_{{\text{g}}}} + {{{\text{F}}}_{2}} \to {\text{Cl}}{{{\text{F}}}_{{{\text{3g}}}}}$так, чтобы выход ClF3 составлял 60–80% от теоретического. Производительность реактора по фтору составила около 1000 мг с–1 л–1.
Пентафторэтан. Реализовать процесс фторирования элементным фтором в режиме горения с технологически приемлемым выходом целевого продукта иногда оказывается возможным и в том случае, когда в термодинамически равновесной смеси целевое вещество отсутствует. Примером такой технологии является получение пентафторэтана [16, 17]:
(13)
${\text{C}}{{{\text{F}}}_{{\text{3}}}}{\text{CF}}{{{\text{H}}}_{{{\text{2g}}}}} + {{{\text{F}}}_{{{\text{2g}}}}} \to {{{\text{C}}}_{{\text{2}}}}{{{\text{F}}}_{{\text{5}}}}{{{\text{H}}}_{{\text{g}}}} + {\text{H}}{{{\text{F}}}_{{\text{g}}}}--473\,\,\,{\text{кДж}}.$Адиабатическая температура продуктов процесса (10) может составить около 2000 К. В табл. 4 приведены термодинамически равновесные составы веществ в системе элементов С–H–F в зависимости от температуры при атмосферном давлении. Из полученных данных следует, что в интервале температуры 500–2000 К двухуглеродные молекулы в равновесной смеси отсутствуют, а основными ее компонентами являются HF и CF4. Поэтому можно предположить, что при проведении процесса (13) в режиме горения основным фторуглеродом будет CF4.
Таблица 4.
Термодинамически равновесный состав веществ в системе элементов C–H–F в зависимости от температуры при атмосферном давлении
Соотношение атомов | Т, К | CM, мол. % | ||||||
---|---|---|---|---|---|---|---|---|
HF | CF4 | Cтв | F | CF2 | CF3 | C2F2 | ||
C–H–3F | 500 | 49.7% | 25.1% | 25.1% | – | – | – | – |
1000 | 50.0% | 25.0% | 25.0% | – | – | – | – | |
2000 | 50.0% | 24.6% | 24.6% | 0.1% | 0.4% | 0.1% | 0.2% | |
C–H–2.25F | 500 | 49.8% | 15.7% | 34.5% | – | – | – | – |
1000 | 50.0% | 15.6% | 34.4% | – | – | – | – | |
2000 | 50.0% | 15.4% | 34.1% | 0.1% | 0.3% | 0.1% | 0.1% |
В тоже время известно, что при газофазном фторировании CF3CFH2 в стационарном тепловом режиме при концентрации фтора в смеси на уровне единиц процентов при температуре 373–423 K удается добиться водородзаместительного фторирования и исключить фторирование углеродной связи [17]. Практического отсутствия фторирования углеродной связи удалось добиться и при взаимодействии CF3CFH2 и фтора в режиме горения с предварительным смешением компонентов, которое обеспечивает отсутствие локальных областей высокой концентрации фтора.
При концентрации фтора в предварительно приготовленной смеси 25–30 об. %, т.е. примерно в 3 раза ниже стехиометрической для процесса получения C2F5H, основным продуктом процесса гомогенного горения был C2F5H, концентрация которого в реакционной смеси составляла около 25%, концентрация C2F6 – 2–3%, а концентрация фторметанов – менее 1%. Адиабатическая температура продуктов этого процесса составляла около 1200 К при начальной температуре 290 К.
Производительность реактора типа “туннельная горелка” по фтору составила 2000 мг с–1 л–1. За реактором был смонтирован высокоэффективный (α ~ 100 Вт м–2 К–1) щелевой теплообменник, в котором скорость охлаждения продуктов реакции составляла величину порядка 300 К с–1, чтобы сократить время пребывания фторэтанов при температуре порядка 1000 К и обеспечить отсутствие деструкции углеродной связи.
Таким образом, при реализации процессов фторирования простых веществ и соединений элементным фтором в режиме горения достигаются высокие скорости фторирования – порядка 10–103${\text{м}}{{{\text{г}}}_{{{{{\text{F}}}_{{\text{2}}}}}}}$ с–1 л–1, что связано с высокой температурой, которая развивается в зоне горения и которая близка к адиабатической температуре процесса.
ФТОРИРОВАНИЕ ЭЛЕМЕНТНЫМ ФТОРОМ В СТАЦИОНАРНОМ ТЕПЛОВОМ РЕЖИМЕ
Для того чтобы при протекании экзотермической химической реакции сформировать стационарный тепловой режим необходимо увеличивать значение теплового потока из зоны реакции [30], который в свою очередь определяется значением коэффициента теплоотдачи.
Высокие значения коэффициента теплоотдачи реализуются в реакционных системах, где одним из реагентов или растворителем является жидкая фаза. В жидкостных реакторах с мешалкой, работающей с частотой порядка 101 Гц, значение коэффициента теплоотдачи составляет величину порядка 103 Вт м–2 К–1 [31]. В реакционных системах газ–твердое и твердое–твердое повысить мощность теплового потока из зоны реакции можно, перемешивая порошок потоком газа или механическими устройствами. В этом случае значение коэффициента теплоотдачи составляет величину порядка 102 Вт м–2 К–1 [32, 33].
Синтез перфторалканов и фторида углерода из простых веществ. Выше было сказано, что при взаимодействии углерода и фтора в зависимости от температуры могут быть получены различные вещества (4)–(6). Чтобы получить смесь перфторалканов CF4, C2F6, C3F8, C4F10 нужно поддерживать температуру в зоне реакции на уровне 800–900 К. При этом, согласно табл. 3, в термодинамически равновесной смеси перфторалканы с числом атомов углерода более 1 отсутствуют.
Обеспечить термостабилизацию зоны реакции фтора и графита можно, используя псевдоожиженный слой графита и недостаток фтора в зоне реакции. Так в [9] было показано, что в реакторе с псевдоожиженным слоем графита при α ~ 500 Вт м–2 К–1 в стационарном тепловом режиме, реализация которого была зафиксирована с помощью измерения температуры, при температуре 800–900 К вышеперечисленные перфторалканы находились в сравнимых количествах в продуктах реакции, в отличие от режима фильтрационного горения углерода во фторе, единственным продуктом которого являлся CF4. Удельная производительность реактора с псевдоожиженным слоем в этом случае составляла около 30 ${\text{м}}{{{\text{г}}}_{{{{{\text{F}}}_{{\text{2}}}}}}}$ с–1 л–1.
При температуре порядка 723–773 K основным продуктом взаимодействия углерода и фтора является полифторид углерода [9, 11]:
(14)
${{{\text{C}}}_{{\text{s}}}} + 0.5{{{\text{F}}}_{{{\text{2g}}}}} \to {{({\text{C}}{{{\text{F}}}_{x}})}_{{n{\text{s}}}}}--198\,\,\,{\text{кДж}}\,\,\,{\text{при}}\,\,x = {\text{ }}1,$вещество в термодинамически равновесной смеси отсутствующее во всем диапазоне изменения температуры. В реакторе с псеводоожиженным слоем при фторировании в стационарном тепловом режиме при температуре 723–773 K скорость взаимодействия фтора с графитом и сибунитом при поучении (CFx)n составила около 20 мг с–1 л–1.
Трифторид азота. Фторированием элементным фтором полифторида аммония NH4F · zHF в современной промышленности получают трифторид азота NF3 [12].
В табл. 5 приведены результаты расчета термодинамически равновесного состава веществ в системе элементов N–H–F. Из табл. 5 следует, что трифторид азота присутствует в термодинамически равновесной смеси при температуре ниже 1000 К.
Таблица 5.
Термодинамически равновесный состав веществ в системе элементов N–H–F для различной температуры при атмосферном давлении
Соотношение атомов | Т, К | CM, мол. % | ||||
---|---|---|---|---|---|---|
F | F2 | HF | N2 | NF3 | ||
N–5H–8F | 500 | – | – | 83.2% | – | 16.7% |
1000 | 4.1% | 17.9% | 70.5% | 6.7% | 0.8% | |
2000 | 35.2% | 0.1% | 58.9% | 5.9% | – | |
N–3H–6F | 500 | – | – | 74.9% | – | 25.1% |
1000 | 4.9% | 25.0% | 59.5% | 9.1% | 1.6% | |
2000 | 46.0% | 0.1% | 46.2% | 7.7% | 0.0% |
Взаимодействие азота и фтора с получением NF3 в литературе не описано, но, согласно [34], его можно получить фторированием аммиака фтором в режиме горения:
(15)
${\text{N}}{{{\text{H}}}_{{{\text{3g}}}}} + 3{{{\text{F}}}_{{{\text{2g}}}}} \to {\text{N}}{{{\text{F}}}_{{{\text{3g}}}}} + 3{\text{H}}{{{\text{F}}}_{g}}--\,\,905.5\,\,\,{\text{кДж}}.$Адиабатическая температура продуктов процесса (15) может достигать величины более 4000 К и, следовательно, основным продуктом взаимодействия аммиака и фтора в нестационарном тепловом режиме будут не NF3, а азот и фтор (табл. 5). Чтобы провести процесс (15) при температуре порядка 500 К, когда содержание NF3 в термодинамически равновесной смеси велико, необходимо разбавлять аммиак и фтор инертным газом, например, азотом так, чтобы их концентрации составляли 1 и 3% соответственно. Это приводит к очень высоким энергозатратам на стадии выделения NF3 из реакционной смеси.
Провести синтез трифторида азота с использованием элементного фтора можно в стационарном тепловом режиме, используя жидкий носитель азота – полифторид аммония NH4F ∙ zHF [12]:
(16)
$\begin{gathered} {\text{N}}{{{\text{H}}}_{{\text{4}}}}{\text{F}} \cdot z{\text{H}}{{{\text{F}}}_{{\text{f}}}} + {{{\text{F}}}_{{{\text{2g}}}}} \to \\ \to \,\,{\text{N}}{{{\text{F}}}_{{{\text{3g}}}}} + {\text{N}}{{{\text{H}}}_{{\text{4}}}}{\text{F}} \cdot (z + k){\text{H}}{{{\text{F}}}_{{\text{f}}}}, \\ \end{gathered} $(17)
${\text{N}}{{{\text{H}}}_{{\text{4}}}}{\text{F}} \cdot (z + k){\text{H}}{{{\text{F}}}_{{\text{f}}}} + {\text{N}}{{{\text{H}}}_{{{\text{3g}}}}} \to {\text{N}}{{{\text{H}}}_{{\text{4}}}}{\text{F}} \cdot z{\text{H}}{{{\text{F}}}_{{\text{g}}}}.$В реакторе с высокооборотной мешалкой в циркуляционном контуре, где коэффициент теплоотдачи составлял около 2000 Вт м–2 К–1 при температуре около 413 K при непрерывной подаче фтора и аммиака в расплав NH4F ∙ zHF (16), (17) выход NF3 на поданный аммиак составлял около 70%, а скорость синтеза в пересчете на фтор – около 3 ${\text{м}}{{{\text{г}}}_{{{{{\text{F}}}_{{\text{2}}}}}}}$ с–1 л–1 [12].
Фторирование CF3CFH2 и CH4 в газожидкостном реакторе. Для реакционной системы газ–газ при протекании в ней процесса фторирования элементным фтором обеспечить стационарный тепловой режим синтеза в промышленном масштабе представляется весьма затруднительным, так как для газофазных систем коэффициент теплоотдачи не высок – 100–101 Вт м–2 К–1. Поэтому обычно фторирование газообразных веществ фтором протекает в режиме горения.
Добиться высокой мощности теплового потока из зоны реакции можно, проводя фторирование газообразных соединений в среде перфторированной жидкости в реакторе с интенсивным перемешиванием. Например, реакцию (11) проводили в изотермическом режиме при температуре порядка 373 K в газожидкостном реакторе с высокоборотной мешалкой, где в качестве жидкой фазы использовали стабильные по отношению ко фтору перфтордекалин и перфтордиметилциклогексани в качестве основного продукта получали C2F5H, а выход фторметанов был более, чем на порядок ниже [14, 15].
Таким образом, было получено вещество, которое отсутствует в термодинамически равновесной смеси, табл. 3, но синтез которого, водород-заместительным фторированием термодинамически не запрещен.
Скорость превращения фтора в газожидкостном реакторе в этом процессе составляла около 5 ${\text{м}}{{{\text{г}}}_{{{{{\text{F}}}_{{\text{2}}}}}}}$ с–1 л–1.
При фторировании метана в режиме горения в широком диапазоне изменения концентраций метана и фтора в инертных газах и их мольного соотношения удалось получить в основном лишь термодинамически равновесные продукты (табл. 4) [25]:
(18)
${\text{C}}{{{\text{H}}}_{{{\text{4g}}}}} + {{{\text{F}}}_{{{\text{2g}}}}} \to {\text{C}}{{{\text{F}}}_{{{\text{4g}}}}} + {\text{H}}{{{\text{F}}}_{{\text{g}}}}.$При реализации фторирования метана в газожидкостном реакторе в стационарном тепловом режиме при температуре порядка 373 K основными продуктами процесса были моно-, ди-, три- и тетрафторметан:
(19)
${\text{C}}{{{\text{H}}}_{{\text{4}}}} + {{{\text{F}}}_{{\text{2}}}} \to {\text{C}}{{{\text{H}}}_{{\text{3}}}}{\text{F}} + {\text{C}}{{{\text{H}}}_{{\text{2}}}}{{{\text{F}}}_{2}} + {\text{CH}}{{{\text{F}}}_{{\text{3}}}} + {\text{C}}{{{\text{F}}}_{4}},$т.е. удалось получить фторметаны, отсутствующие в термодинамически равновесной смеси.
Скорость превращения фтора при фторировании метана в газожидкостном реакторе составляла величину порядка 0.5 ${\text{м}}{{{\text{г}}}_{{{{{\text{F}}}_{{\text{2}}}}}}}$ с–1 л–1.
Фторирование полимеров в газожидкостном реакторе. Поверхностная модификация фтором полимерных изделий хорошо освоена в современной промышленности [13, 35]. Процесс проводят в стационарном тепловом режиме, но, так как он лимитируется твердофазной диффузией, удается лишь получить слой фторированного полимера толщиной 0.1–10 мкм на поверхности изделия. Попытки же фторирования порошков элементным фтором приводят к формированию режима горения, продуктами которого являются вещества, характерные для термодинамически равновесной смеси – в основном CF4 и HF.
В последние годы развивается направление по фторированию порошков полимеров в среде перфторированной жидкости в стационарном тепловом режиме. При применении этого метода удалось получить фторпроизводные поли (2.6-диметилфениленоксида-1.3) [16].
ЗАКЛЮЧЕНИЕ
Тепловые эффекты процессов фторирования простых веществ и соединений элементным фтором сопровождаются высоким тепловыделением – на уровне сотен килоджоулей на моль фтора и температура продуктов в адиабатическом режиме составляет тысячи кельвинов.
Если целевые продукты фторирования элементным фтором вещества присутствуют в термодинамически равновесной смеси в технологически приемлемой концентрации при температуре, близкой к адиабатической, то процесс их промышленного получения целесообразно проводить в нестационарном тепловом режиме (режиме горения), охлаждая полученные вещества в основном за зоной реакции. В режиме горения достигается очень высокая удельная производительность реакционного объема – в пересчете на фтор порядка 102–103${\text{м}}{{{\text{г}}}_{{{{{\text{F}}}_{{\text{2}}}}}}}$ с–1 л–1.
Если в термодинамически равновесной смеси целевые фториды отсутствуют, то фторирование целесообразно проводить в стационарном тепловом (близком к изотермическому) режиме, отводя выделяющееся тепло в зоне реакции и создавая в реакторе коэффициент теплоотдачи на уровне 102–103 Вт м–2 К–1. В стационарном тепловом режиме производительность процессов фторирования относительно невелика – порядка 0.1–10 ${\text{м}}{{{\text{г}}}_{{{{{\text{F}}}_{{\text{2}}}}}}}$ с–1 л–1.
Работа выполнена в рамках проекта FSWW-2020-0020 при поддержке Министерства науки и высшего образования Российской Федерации.
ОБОЗНАЧЕНИЯ
a | количество исходных веществ, моль |
b | количество продуктов реакции, моль |
CM | мольная концентрация, % |
D | коэффициент диффузии, м2 с–1 |
l | характерный размер переноса, м |
М | молекулярная масса, г моль–1 |
n | количество молекул фторида углерода, моль |
R(F) | фторсодержащие соединение |
T | температура, К |
t | время превращения веществ, с |
u | нормальная скорость распространения пламени, см с–1 |
x | количество атомов фтора в молекуле фторида углерода |
y | количество атомов фтора образовавшихся в процессе диссоциации фторсодержащего соединения |
z, k | количество молекул фтористого водорода в составе полифторида аммония, моль |
α | коэффициент теплоотдачи, Вт м–2 К–1 |
δ | толщина ламинарного пламени, см |
ИНДЕКСЫ
Список литературы
Белов Г.В. Моделирование равновесных состояний многокомпонентных гетерогенных систем // Мат. модел. 2005. Т. 17. № 2. С. 81.
Ватолин Н.А., Моисеев Г.К., Трусов Б.Г. Термодинамическое моделирование в высокотемпературных неорганических системах. М.: Металлургия, 1994.
Исикава Н., Кобаяси Е. Фтор. Химия и применение. М.: Мир, 1982.
Пашкевич Д.С., Мухортов Д.А., Петров В.Б., Алексеев Ю.И., Асович В.С., Барабанов В.Г. Синтез тетрафторметана фторированием графита элементным фтором // Журн. прикл. хим. 2004. Т. 77. № 1. С. 96.
Пашкевич Д.С., Алексеев Ю.И. Технология получения тетрафторида серы в реакторе с падающим слоем при одновременном дозировании серы и фтора // Тез. докл. 1 Международный сибирский семинар “Современные неорганические фториды Intersibfluorine – 2003”. Новосибирск, 2003. С. 10.
Снегирев А.Ю. Основы теории горения. М.: Политехнический университет, 2014.
Канторович Б.В. Основы теории горения и газификации твердого топлива. М.: АН СССР, 1958.
Лисиенко В.Г., Щелоков Я.М., Ладыгичев М.Г. Топливо. Рациональное сжигание, управление и технологическое использование. Топливо. Рациональное сжигание, управление и технологическое использование: справочник в 3 кн. М.: Теплотехник, 2003.
Pashkevich D.S., Shelopin G.G., Mukhortov D.A., Petrov V.B., Alekseev Yu. I., Asovich V.S. Synthesis of perfluoroalkanes by high-temperature reaction of graphite with fluorine in a fluidized bed // Russ. J. Appl. Chem. 2004. V. 77. № 11. P. 1847.
Пашкевич Д.С., Шелопин Г.Г. Алексеев Ю.И. Митькин В.Н. Влияние интенсификации процессов переноса на параметры синтеза полифторида углерода // Тез. докл. 2 Международный сибирский семинар “Современные неорганические фториды, Intersibfluorine – 2006”. Томск, 2006. С. 362.
Пашкевич Д.С., Мухортов Д.А., Алексеев Ю.И., Асович В.С., Камбур М.П., Лантратова О.В и др. Новые аспекты безотходной технологии получения трифторида азота высокой чистоты фторированием расплава кислого бифторида аммония фтором // Тез. докл. 2 Международный сибирский семинар “Современные неорганические фториды, Intersibfluorine – 2006”. Томск, 2006. С. 222.
Пашкевич Д.С., Барабанов В.Г., Максимов Б.Н. Разработка и внедрение промышленных технологий получения фторсоединений с применением элементного фтора // Памяти Б.В. Гидаспова. Научные чтения. СПб.: Теза, 2008. С. 169.
Харитонов А.П., Логинов Б.А. Прямое фторирование полимерных изделий – от фундаментальных исследований к практическому использованию // Росс. хим. журн. 2008. С. 106.
Камбур П.С., Пашкевич Д.С., Петров В.Б., Алексеев Ю.И., Ямпольский Ю.П., Алентьев А.Ю. Газожидкостное фторирование 1,1,1,2-тетрафторэтана и метана элементным фтором в среде перфторированной жидкости // Журн. прикл. хим. 2019. Т. 92. № 7. С. 888.
Камбур П.С., Пашкевич Д.С., Алексеев Ю.И., Ямпольский Ю.П., Алентьев А.Ю. Взаимодействие перфторированных жидкостей с фтором в газожидкостном реакторе // Журн. прикл. хим. 2019. Т. 92. № 5. С. 27.
Blinov I., Mukhortov D., Yampolskii Y., Belov N., Alentiev A., Chirkov S., Bondarenko G., Kostina Y., Legkov S., Perepuchov A., Kambur M., Kambur P., Kapustin V., Vozniuk O., Kurapova E. Direct fluorination of poly-2,6-dimethyl-1,4-phenylene oxide in perfluorinated liquid medium // J. Fluorine Chem. 2020. V. 234.
Пашкевич Д.С., Мухортов Д.А., Подпалкина Е.А., Барабанов В.Г. Кинетика газофазного фторирования 1,1,1,2-тетрафторэтана элементным фтором // Журн. хим. фтора. 1999. № 6. С. 3.
Пашкевич Д.С., Мухортов Д.А., Алексеев Ю.И., Асович В.С., Рождественская О.В. Синтез фторуглеводородов этанового ряда с применением элементного фтора // Журн. прикл. хим. 2002. Т. 75. С. 1295.
Пашкевич Д.С., Мухортов Д.А., Алексеев Ю.И., Асович В.С., Рождественская О.В. Газофазное фторирование фторэтанов фтором // Журн. прикл. хим. 2001. Т. 74. № 7. С. 1120.
Тураев Н.С., Жерин И.И. Химия и технология урана М.: ЦНИИАТОМИНФОРМ, 2005.
Бутов В.Г., Солоненко В.А., Зятиков П.Н., Демиденко А.А., Галата А.А., Котов С.А., Рудников А.И., Пешкичев Ю.Е., Ледовских К.А. Опытно-промышленные испытания пламенного реактора с модернизированным вводом технологического фтора // Изв. высш. учебн. завед. Физ. 2012. Т. 55. № 9(3). С. 30.
Зятиков П.Н., Демиденко А.А., Бутов В Г., Солоненко В.А., Лазарчук В.В., Ледовских А.К. и др. Способ получения гексафторида урана и реактор для осуществления способа. Пат. 2456242 РФ. 2012.
Михеев В.П. Газовое топливо и его сжигание: учебное пособие. Л.: Недра, 1966.
Дытнерский Ю.И., Брыков. В.П., Каграманов Г.Г. Мембранное разделение газов. М.: Химия, 1991.
Максимов Б.Н., Барабанов В. Г., Серушкин И. Л. и др. Промышленные фторорганические продукты. Л.: Химия, 1990.
Авдулов Г.И., Королев В.Л., Масличенко А.П. и др. Реактор получения гексафторида серы. А. с. 295070 СССР.
Суховерхов В.Ф., Шишков В.Д., Аленчикова И.Ф. Химия галоидных соединений фтора. М.: Наука, 1968.
Shrewsberry R., Williamson L. Chemistry of the chlorinetrifluoride – uranylfluoride reaction // J. Inorg. Nucl. Chem. 1966. V. 28. P. 2535.
Kinkead S.A., Asprey L.B., Eller P.G. Low temperature synthesis of chlorine pentafluoride using dioxygen difluoride // J. Fluorine Chem. 1985. V. 29. № 4. P. 459.
Франк-Каменецкий Д.А. Основы макрокинетики. Диффузия и теплопередача в химической кинетике. Долгопрудный: Интеллект, 2008.
Пашкевич Д.С., Камбур П.С. Мухортов Д.А. Изучение тепло- и массообмена в зависимости от газосодержания в газожидкостном аппарате с высокоскоростной мешалкой в циркуляционном контуре // Ж. прикл. хим. 2009. Т. 82. № 9. С. 1467.
Пашкевич Д.С., Алексеев Ю.И., Моисеенко А.А., Радченко С.М. Теплообмен динамических слоев порошков с теплонесущей поверхностью. Спирально-винтовой шнек и горизонтальный вращающийся цилиндр // Инж.-физ. журн. 1999. Т. 72. № 1. С. 3.
Пашкевич Д.С., Краснокутский В.Н., Петров В.Б., Королев В.Л. Теплообмен динамических слоев порошков с теплонесущей поверхностью. Пылегазовый поток // Инж.-физ. журн. 1999. Т. 72. № 1. С. 9.
Пашкевич Д.С., Алексеев Ю.И., Асович В.С., Машков Ю.В., Мамаев В.В. Трифторид азота – наиболее перспективный носитель фтора для процессов травления кремния в промышленности полупроводников // Тез. докл. 1 Международный сибирский семинар “Современные неорганические фториды Intersibfluorine – 2003”. Новосибирск, 2003. С. 159.
Nazarov V.G. Structure and composition of the surface layer in polymers modified by elemental fluorine // J. Appl. Polym. Sci. 2005. V. 95. № 4. P. 897.
Дополнительные материалы отсутствуют.
Инструменты
Теоретические основы химической технологии