Теоретические основы химической технологии, 2021, T. 55, № 5, стр. 632-641
Анализ условий электролитического формирования ансамблей металлических нанопроволок в порах трековых мембран
С. С. Кругликов a, *, Д. Л. Загорский b, В. А. Колесников a, И. М. Долуденко b, С. А. Бедин c
a Российский химико-технологический университет им. Д.И. Менделеева
Москва, Россия
b Федеральный научно-исследовательский центр “Кристаллография и фотоника” РАН
Москва, Россия
c Московский педагогический государственный университет
Москва, Россия
* E-mail: skruglikov@mail.ru
Поступила в редакцию 27.01.2021
После доработки 15.02.2021
Принята к публикации 15.02.2021
Аннотация
Рассмотрена и проанализирована роль состава электролита, условий массопереноса, диаметра пор, расстояния между ними и электрических параметров на процесс формирования ансамбля нанопроволок при электроосаждении индивидуальных металлов и сплавов в поры полимерных пленок, а также при чередовании слоев сплавов разного химического состава. На основе результатов экспериментальных исследований рекомендованы условия проведения процесса электроосаждения, позволяющие стабилизировать состав осаждаемого сплава по длине нанопроволоки, а при послойном осаждении – уменьшить изменения состава в пределах каждого слоя.
ВВЕДЕНИЕ
Технический прогресс в производстве электронной техники и в ряде смежных отраслей привел к появлению в последние десятилетия новых электрохимических процессов: катодного и анодного микроформирования с использованием новых методов управления макро- и микрораспределением тока [1–3], электроосаждения металлов и сплавов на электропроводных волокнистых и пористых материалах [4–6]. Значительно больше внимания уделяется решению экологических проблем гальванотехники, в частности, разработке безотходной технологии кадмирования [7] и хромирования с использованием электромембранных процессов [8].
В последние три десятилетия сформировалось еще одно новое направление – электроосаждение металлов и сплавов в порах неэлектропроводных материалов – так называемое темплатное электроосаждение. Ансамбли нанопроволок, получаемые электроосаждением в порах оксида алюминия или полимерной мембраны с катодным токоподводом на дне пор, могут быть использованы для создания новой электронной техники, миниатюрных устройств магнитной памяти, оптоэлектроники, сенсоров, суперконденсаторов [9–23]. Это новое направление в гальванотехнике пока находится в стадии становления, и в большинстве опубликованных работ не приводятся такие важнейшие параметры процесса, как истинные значения катодной плотности тока и катодного потенциала, что осложняет интерпретацию результатов экспериментальных исследований и делает невозможной их воспроизведение. В то же время при решении большинства практических задач для разработки оптимальных составов электролитов и режимов электролиза необходим теоретический анализ влияния состава электролита и параметров электролиза на протекание каждой стадии процесса темплатного электроосаждения, что позволит получить нанопроволоки с требуемыми характеристиками.
В данной работе рассмотрена взаимосвязь между параметрами электролиза и химическим составом, а также структурными особенностями одно- и многослойных нанопроволок, сформированных в порах полимерных мембран толщиной около 10–12 мкм.
ТЕОРЕТИЧЕСКИЙ АНАЛИЗ
Массоперенос участников катодных реакций. При электроосаждении металла или сплава в каналах пор специфическая особенность катодного процесса – непрерывное уменьшение эффективной толщины диффузионного слоя d, начиная с момента включения тока и до заполнения канала поры металлом:
Здесь dout – внешняя часть эффективной толщины диффузионного слоя (над мембраной), din – внутренняя часть толщины диффузионного слоя, равная глубине, не заполненной металлом части канала поры:
Здесь h – начальная глубина поры, практически равная толщине мембраны, а x – толщина слоя металла в поре (длина сформировавшейся части нанопроволоки).Если среднее расстояние между порами не менее, чем на порядок превышает их диаметр, то толщину внешней части диффузионного слоя можно принять приблизительно равной диаметру пор [23, 24 ] . Подобная ситуация имеет место, когда число пор диаметром 50–200 нм на одном квадратном сантиметре поверхности мембраны не превышает 108. В этом случае концентрационное поле для участников электродных реакций в устье каналов пор имеет полусферическую форму и располагается практически в неподвижной части пограничного гидродинамического слоя, а эффективная толщина внешней части диффузионного слоя равна радиусу канала поры, то есть не превышает 25–100 нм [23]. В не заполненной металлом части канала поры концентрационное поле является однородным и там имеет место линейная диффузия [9, 23, 24 ] . При этом в процессе электролиза массоперенос участников электродных реакций в каждый момент времени можно рассматривать как квазистационарный, поскольку приближенная оценка переходного времени τ для установления стационарного режима диффузии с помощью соотношения
(D – коэффициент диффузии диффундирующих частиц) показывает, что переходное время составляет менее 1 с, в то время как заполнение поры металлом или сплавом продолжается десятки-сотни секунд.
Таким образом, формирование нанопроволок начинается в условиях, когда эффективная толщина диффузионного слоя приблизительно равна 10–12 мкм, а заканчивается, когда она снизится до 25–100 нм. Соответственно, предельная диффузионная плотность тока в начальной стадии процесса превышает на 1–2 порядка, предельную плотность тока на макрокатоде в отсутствие перемешивания, а заканчивается, когда это превышение может достигать 3–4 порядков.
Если же количество пор – не менее 109 см–2, то расстояние между порами становится соизмеримым с их диаметром, а эффективная толщина внешней части диффузионного слоя может многократно превысить максимальное значение внутренней части, равное толщине мембраны. Это благоприятно скажется на стабилизации режима массопереноса в процессе электролиза, хотя и существенно ограничит максимальную скорость формирования ансамбля нанопроволок.
Необходимо также отметить, что увеличение суммарной толщины диффузионного слоя приведет к увеличению переходного времени для установления стационарного режима массопереноса, что следует учитывать при использовании нестационарных электрических режимов электролиза.
При формировании нанопроволок в электролитах, используемых, для получения гальванических покрытий, отсутствие диффузионных ограничений даже при высоких катодных плотностях тока позволяет проводить процесс с очень высокой скоростью. При этом состав раствора непосредственно у катодной поверхности практически не отличается от состава раствора в объеме электролизера, так как высокая катодная плотность тока, тем не менее, существенно ниже предельной.
Необходимо также иметь в виду специфическую особенность структуры металлического осадка, формирующегося на поверхности катода в условиях диффузионных ограничений скорости процесса – преимущественный разряд ионов на тех участках катодной поверхности, к которым быстрее идет доставка разряжающихся ионов. Поэтому в условиях диффузионных ограничений вполне возможно лишь частичное заполнение канала поры металлом, что аналогично формированию дендритного осадка на макрокатодах. Таким образом, для равномерного заполнения канала поры металлом процесс желательно проводить в условиях отсутствия диффузионных ограничений скорости электроосаждения металла.
Во многих случаях экспериментальные исследования процесса электроосаждения нанопроволок проводятся в условиях квазипотенциостатического режима [11, 18] или даже при постоянном напряжении между катодом и анодом [21, 22]. Это позволяет определить верхнюю границу диапазона катодной плотности тока, где заведомо отсутствуют диффузионные ограничения скорости процесса. В качестве такой границы можно принять уменьшенную в 5–10 раз максимальную реализованную в эксперименте парциальную плотность тока осаждения металла. Для определения последней можно использовать значения максимальной скорости заполнения канала поры, достигнутые в экспериментах, а затем, зная глубину поры, рассчитать среднюю плотность тока в процессе заполнения поры:
Здесь i – рассчитанная величина парциальной плотности тока для разряда ионов металла на поверхности растущей нанопроволоки, k – плотность металла, F – число Фарадея, А – атомная масса металла, t – время, по истечении которого некоторая часть пор полностью заполняется металлом и начинается рост “шляпок” приводящий к быстрому увеличению суммарной катодной поверхности.
При совместном осаждении нескольких металлов в каналах пор следствием наличия диффузионных ограничений хотя бы для одного компонента осаждаемого сплава будет неоднородность химического состава нанопроволок по их длине, а возможно, и по диаметру.
В гальваностатическом режиме электролиза по мере заполнения канала поры металлом будет возрастать доля более электроположительного компонента, как результат уменьшения эффективной толщины диффузионного слоя. Однако по рассмотренным выше причинам этот эффект будет наблюдаться только при относительно небольшой поверхностной плотности пор.
При числе пор 109 см–2 эффективная толщина диффузионного слоя может достигать десятков или сотен микрометров, и она практически не изменяется в процессе заполнения пор металлом. Толщина внутренней части диффузионного слоя, уменьшающаяся в процессе заполнения пор металлом, в этом случае будет составлять незначительную долю суммарной толщины диффузионного слоя. Достигаемая при этом стабилизация условий массопереноса будет способствовать стабилизации состава осаждаемого сплава даже при наличии диффузионных ограничений для скорости разряда ионов. С другой стороны, многократное увеличение эффективной толщины диффузионного слоя существенно увеличит переходное время установления стационарного режима массопереноса. Применение потенциостатического режима электролиза в этих условиях, возможно, уменьшит, но не устранит полностью неоднородность состава осаждаемого сплава. Различные виды униполярных импульсных режимов (с паузами и без пауз) будут только усиливать неоднородность химического состава.
Таким образом, при формировании ансамбля нанопроволок из сплава определенного химического состава равномерное заполнение канала каждой поры сплавом постоянного состава возможно лишь при выборе такого электролита, из которого можно осаждать сплав требуемого состава в отсутствие диффузионных ограничений для всех участников катодного процесса.
В тех случаях, когда скорость разряда ионов одного из компонентов сплава контролируется скоростью диффузии, целесообразно использовать мембраны с количеством пор на поверхности порядка 109 см–2 для стабилизации условий массопереноса в процессе заполнения пор сплавом. При этом эффективная толщина внешней части диффузионного слоя существенно увеличивается и будет зависеть и от среднего расстояния между порами, и от гидродинамических условий. В перемешиваемом растворе эффективная толщина диффузионного слоя у макроэлектрода обычно находится в диапазоне нескольких десятков мкм, а при отсутствии перемешивания возрастает до 0.3–0.5 мм. Толщина внутренней части диффузионного слоя становится пренебрежимой по сравнению с толщиной внешней части и ее уменьшение по мере заполнения канала поры металлом не будет влиять на скорость массопереноса.
Таким образом, малое расстояние между устьями пор обеспечивает постоянство эффективной толщины диффузионного слоя в процессе заполнения пор металлом, что положительно скажется на стабилизации режима массопереноса всех участников электродных реакций.
В процессах электроосаждения многослойных нанопроволок, то есть при чередовании слоев различного химического состава обычно используют один и тот же раствор для осаждения всех слоев, причем изменение состава слоев достигается путем периодического изменения режима электролиза – силы тока в цепи, катодного потенциала или напряжения на электродах. Как уже отмечалось выше, при количестве пор не более 108 см–2 переходное время для установления квазистационарного режима массопереноса не превышает 1 с, а это означает, что толщина переходной зоны между чередующимися слоями будет соответствовать толщине слоя металла или сплава, осажденного за время порядка одной секунды. Однако в тех случаях, когда в процессе получения многослойных нанопроволок продолжительность формирования каких-либо слоев окажется соизмеримой с переходным временем для установления стационарного режима массопереноса, химический состав таких слоев не будет постоянным.
Выбор состава электролита. При выборе электролита для электроосаждения индивидуального металла целесообразно ориентироваться на те составы, при использовании которых наблюдается минимальный выход по току водорода, так как образование пузырька газа в канале поры блокирует процесс осаждения металла. Электроосаждение металлов группы железа (железо, никель, кобальт) сопровождается побочным процессом выделения водорода, который контролируется скоростью диффузии ионов гидроксония к поверхности катода. Ввиду этого pH электролита целесообразно поддерживать вблизи верхней границы рабочего диапазона для электроосаждения этих металлов на макрокатодах.
Сплавы на основе металлов группы железа, например, пермаллой, могут быть получены в форме нанопроволок без существенных диффузионных ограничений, и, следовательно, могут иметь стабильный состав по длине проволоки. Можно ожидать, что увеличение числа пор на поверхности мембраны будет только способствовать стабилизации состава сплава по длине проволоки. В тех же случаях, когда для уменьшения доли компонента в сплаве приходится снижать его концентрацию в электролите и таким образом снижать скорость диффузии его ионов к катоду, целесообразно использовать мембраны с числом пор не менее 109 см–2, так как в этих условиях степень диффузионных ограничений и состав сплава не будут существенно изменяться по мере роста нанопроволок.
Для электроосаждения сплавов, у которых стандартные потенциалы компонентов отстоят далеко друг от друга (латуни, бронзы, мельхиор, сплавы на основе драгметаллов), пригодны лишь электролиты на основе комплексных солей, например, цианидные, пирофосфатные, трилонатные, так как при использовании простых солей более электроотрицательный компонент начнет соосаждаться вместе с электроположительным только тогда, когда фактическая катодная плотность тока превысит предельный ток для электроположительного компонента, а катодный потенциал достигнет значения, достаточного для разряда ионов электроотрицательного компонента. Как уже указывалось выше, режим предельного тока не может обеспечить получение качественных электролитических осадков даже индивидуальных металлов, а для сплавов – в дополнение к этому – и стабильный состав.
Параметры электрического режима. При получении нанопроволок применяются самые разнообразные электрические режимы: гальваностатический, потенциостатический, режим постоянного напряжения на электродах, различные виды импульсных и динамических режимов. Проведение предварительных экспериментов с выбранным составом электролита при нескольких постоянных значениях катодного потенциала или напряжения на электродах позволит определить реальный диапазон значений скорости электроосаждения и, тем самым, верхнюю границу области, в которой практически отсутствуют диффузионные ограничения [23]. На основе полученных результатов можно определить оптимальный диапазон катодной плотности тока для последующих экспериментов, проводимых в гальваностатических условиях, что особенно важно при формировании многослойных проволок с контролируемыми толщиной и химическим составом слоев. Становится также возможной оценка вклада падения потенциала в растворе в измеренную величину катодного потенциала и определение границы области, за которыми потенциостатический режим становится уже квазипотенциостатическим [23].
ЭКСПЕРИМЕНТАЛЬНАЯ ЧАСТЬ
Методика проведения процесса электроосаждения. В экспериментах по электроосаждению нанопроволок использовали полиэтилентерефталатные трековые мембраны толщиной 10–12 мкм и порами диаметром 40–200 нм. Число пор на одном квадратном сантиметре поверхности мембраны – от 108 до 109. Для создания токоподвода на одну сторону мембраны (будущую тыльную сторону) наносили тонкий слой меди методом вакуумного напыления, после чего мембрану помещали в сернокислый электролит меднения и продолжали увеличивать толщину слоя меди до 2–10 мкм, чтобы обеспечить образование сплошного слоя меди на тыльной стороне мембраны. После такой подготовки образцов в нижней части канала каждой поры на боковых стенках неизбежно осаждалось некоторое количество напыленной меди, на которой затем формировался слой электроосажденной меди. Процесс осаждения меди на внутренней поверхности нижней части каналов пор заканчивался лишь после полного зарастания отверстий, т.е. когда средняя толщина медного осадка превысила радиус канала поры. В результате этого площадь катодной поверхности одной поры в начальной стадии процесса формирования нанопроволок могла существенно превосходить площадь дна каждой поры, а затем постепенно уменьшалась по мере заполнения нижней части поры металлом.
Эксперименты по получению нанопроволок проводили в ячейке без разделения катодного и анодного пространств. При электроосаждении индивидуальных металлов использовали растворимые аноды из металла, осаждаемого на катоде. При электроосаждении сплавов анодом служил металл, являющийся одним из компонентов осаждаемого сплава.
В качестве источника тока использовали различные устройства, в том числе позволяющие генерировать импульсы с регулируемой длительностью или регулируемым количеством электричества, проходящего за один импульс. Параметрами регулирования и контроля в большинстве экспериментов были сила тока и напряжение на электродах. В ряде случаев использовали хлорид-серебряный электрод сравнения. В этих экспериментах процесс электролиза проводили при постоянном значении разности потенциалов между катодом и электродом сравнения, открытый конец капилляра которого находился на расстоянии 1 мм от поверхности мембраны. При такой конструкции фактический режим электролиза следует рассматривать как квазипотенциостатический и то лишь до момента выхода осадка на поверхность мембраны, после чего падение потенциала в растворе между катодом и электродом сравнения начинает быстро увеличиваться, а катодный потенциал смещается в положительном направлении на соответствующую величину [11, 18].
Методика измерений и расчетов. При получении нанопроволок из индивидуальных металлов решающую роль играют параметры электрического режима, в частности, истинные значения катодного потенциала и парциальной плотности тока, соответствующей скорости электроосаждения металла. Для определения численных значений этих параметров и их последующей оптимизации проводили серию опытов по электроосаждению металла в порах полимерных мембран толщиной 10–12 мкм при различных и постоянных в каждом опыте значениях напряжения на клеммах электролизера или потенциала катода, измеренного относительно электрода сравнения [11, 18].
Продолжительность электролиза, после которой начинается участок подъема на кривых ток–время электролиза, соответствует полному заполнению металлом существенной доли пор и дает возможность рассчитать фактическую парциальную плотность тока осаждения металла с помощью формулы (3).
Для определения истинных значений катодного потенциала в процессе заполнения каналов пор металлом рассчитывали поправку, учитывающую падение потенциала в растворе на участке от поверхности катода до открытого конца капилляра электрода сравнения [23].
Проведена серия экспериментов по получению нанопроволок из сплава никель–кобальт, никель–железо и кобальт–железо. Важная особенность этой группы процессов – проведение электролиза в условиях наличия существенных диффузионных ограничений для разряда ионов железа, что заставляет отдать предпочтение мембранам с числом пор 109 см–2, чтобы обеспечить постоянство состава по длине проволоки и при необходимости регулировать состав, изменяя электрические параметры и концентрацию ионов металлов в растворе.
К сожалению, при электроосаждении сплавов металлов, стандартные потенциалы которых существенно различались в растворах простых солей, не использовали электролиты на основе комплексных соединений. Состав осаждаемого сплава регулировали, уменьшая концентрацию соли того компонента, разряд ионов которого начинался при более положительном потенциале, т.е. создавали диффузионные ограничения скорости разряда его ионов. Наряду с этим в качестве средства регулирования использовали изменение электрических параметров процесса (катодного потенциала, силы тока или напряжения на электродах). В этих процессах электроположительным компонентом являлась медь, а электроотрицательным вышеперечисленные металлы группы железа.
Экспериментальные данные о составе таких сплавов и времени, в течение которого происходит заполнение канала пор или формируется участок нанопроволоки определенной длины, позволяют рассчитать величину парциальной предельной плотности тока разряда ионов меди и эффективной толщины диффузионного слоя [формулы (1) и (3)].
В экспериментах по электроосаждению многослойных нанопроволок чередовали слои бинарного сплава медь–металл из группы железа с разным соотношением его компонентов в отдельных слоях, регулируя состав сплава в каждом слое изменением силы тока или потенциала (напряжения на электродах) и задавая требуемую толщину слоев путем изменения длительности импульсов и пауз между ними или изменяя количество электричества, прошедшего за один импульс.
РЕЗУЛЬТАТЫ И ИХ ОБСУЖДЕНИЕ
Нанопроволоки из индивидуальных металлов. Получены нанопроволоки из кобальта, никеля и железа [11]. Этот наиболее простой объект ранее был использован для количественной оценки скорости массопереноса и вклада падения потенциала в растворе на участке между электродом сравнения и в измеряемый катодный потенциал при различных и известных значениях катодного потенциала [23]. Экспериментальные данные получены в условиях квазипотенциостатического режима с использованием хлорид-серебряного электрода сравнения только для мембран с количеством пор 109 см–2. Данные о составе растворов и режиме процесса приведены в табл. 1.
Таблица 1.
Состав электролитов и режим электролиза для процесса формирования нанопроволок из кобальта, никеля и железа [11]
Состав электролита | Электролит кобальтирования CoSO4 ⋅ 7H2O – 320 г/л Н3BO3 – 40 г/л |
Электролит никелирования NiSO4 ⋅ 7H2O – 200 г/л NiCl2 ⋅ 6H2O – 20г/л H3BO3 – 30 г/л |
Электролит железнения FeSO4 ⋅ 7H2O – 200 г/л AlCl3 ⋅ 6H2O – 50 г/л Аскорбиновая кислота – 2 г/л |
pH | 3.5–3.8 | 4.4–4.7 | 2.4–2.5 |
Температура, °C | 40–45 | 50–55 | 20–60 |
В качестве примера на рис. 1 показаны кривые ток–время, полученные при электроосаждении кобальтовых нанопроволок в порах диаметром 200 нм.
Рис. 1.
Зависимость ток–время для процесса формирования кобальтовых нанопроволок диаметром 100 нм при постоянных значениях измеренного катодного потенциала (относ. с. в. э.): 1 – –680 мВ; 2 – –630; 3 – –580; 4 – –530 мВ.
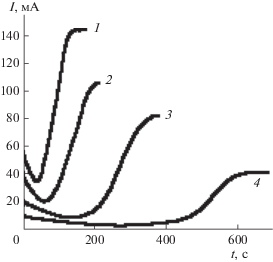
Поскольку начало участка подъема кривых на рис. 1 соответствует моменту полного заполнению металлом существенной доли пор [23], то это позволяет рассчитать i – среднее значение парциальной плотности тока осаждения металла за этот промежуток времени.
Значения парциальной плотности тока осаждения кобальта для разных измеренных значений потенциала катода даны в табл. 2. Оценка на основе этих данных падения потенциала в растворе на участке от поверхности растущей нанопроволоки и капилляром электрода сравнения показывает, что его величина при средних и низких плотностях тока (до 0.1 А/см2) не превышает нескольких милливольт. Таким образом, в данном случае режим электролиза можно рассматривать как потенциостатический (без приставки “квази”).
Таблица 2.
Влияние измеренных значений потенциала катода на время заполнения пор кобальтом и катодную плотность тока [18]
№ эксперимента | Измеренный потенциал катода, В (относ. с.в.э.) | Время заполнения пор металлом, с | Катодная плотность тока, А/см2 |
---|---|---|---|
1 | –0.680 | 43 | 0.66 |
2 | –0.630 | 90 | 0.33 |
3 | –0.580 | 180 | 0.16 |
4 | –0.555 | 240 | 0.12 |
5 | –0.530 | 400 | 0.075 |
6 | –0.505 | 720 | 0.041 |
При высоких плотностях тока и, в особенности, после выхода растущей проволоки на поверхность мембраны и образования “шляпки” падение потенциала в растворе может возрасти до десятков милливольт [23].
В процессе заполнения каналов пор металлом площадь катодной поверхности составляет порядка 10% площади мембраны и поэтому градиент концентрации ионов металла быстро снижается по мере удаления от поверхности мембраны, а эффективная толщина внешней части диффузионного слоя по порядку величины приближается к среднему расстоянию между порами. В итоге фактическая парциальная плотность тока разряда ионов кобальта в порах превышает приблизительно в 10 раз предельный ток диффузии к макрокатоду с такой же габаритной поверхностью (соответственно 0.66 и 0.06 А/см2).
Нанопроволоки из сплава. Изучен процесс формирования ансамблей нанопроволок из сплава железо–кобальт. Данные о составе электролита и режиме электролиза приведены в табл. 3.
Таблица 3.
Состав электролитов для осаждения сплава железо–кобальт
Состав электролита | FeSO4 ⋅ 7H2O – 150 г/л CoCl2 ⋅ 6H2O – 42,7 г/л AlCl3 ⋅ 6H2O – 40 г/л Аскорбиновая кислота – 2 г/л |
рН | 1.9 |
Температура | Комнатная |
Электролиз проводили в квазипотенциостатическом режиме, используя хлорид-серебряный электрод сравнения.
Кривые ток–время для электроосаждения сплава железо–кобальт в порах диаметром 50 нм приведены на рис. 2.
Рис. 2.
Зависимость ток–время при электроосаждении сплава железо–кобальт в поры диаметром 50 нм при постоянных значениях измеренного катодного потенциала (относ. с. в. э.): 1 – –900 мВ; 2 – –850; 3 ––800; 4 – –700 мВ.
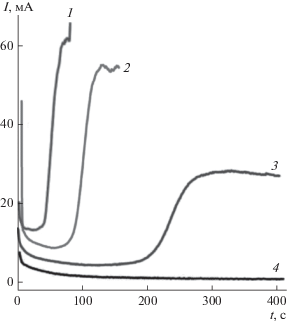
Диапазон значений катодного потенциала в этих экспериментах включал и область высоких плотностей тока – до 0.5–0.7 А/см2. Поэтому состав сплава мог обнаружить некоторую нестабильность в тех случаях, когда по мере заполнения канала поры изменение эффективной толщины диффузионного слоя сказывалось в большей степени на ускорении доставки к катодной поверхности ионов кобальта, молярная концентрация которых в растворе была существенно ниже концентрации ионов железа. В области средних плотностей тока состав сплава по длине проволоки, по-видимому, был более стабильным и близким к атомному отношению Fe/Co – 3.9.
Для стабилизации состава сплава по длине проволок более перспективным будет, вероятно, не потенциостатический, а гальваностатический режим электроосаждения при котором влияние изменения условий массопереноса по мере роста нанопроволок устранено путем использования мембраны с количеством пор на 1 см2 не менее 109.
Многослойные нанопроволоки. Для получения ансамбля нанопроволок с чередующимися слоями разного химического состава в ряде экспериментальных исследований использовали электролиты, содержащие сочетания никель–медь и кобальт–медь [19, 21, 22]. В табл. 4 даны составы электролитов и режимы электролиза для получения многослойных проволок никель–медь и кобальт–медь.
Таблица 4.
Составы электролитов для электроосаждения меди и ее сплавов с никелем и кобальтом
Тип осаждаемого сплава | Никель–медь | Кобальт–медь |
---|---|---|
Компоненты электролитов | NiSO4 ⋅ 7H2О – 197 г/л | CoSO4 ⋅ 7H2O – 200 г/л |
CuSO4 ⋅ 5H2O – 6.2 г/л | CuSO4 ⋅ 5H2O – 8 г/л | |
H3BO3 – 31.6 г/л | H3BO3 – 40 г/л |
В тех случаях, когда в качестве анода использовали медь, осаждение медных слоев проводили при напряжении на электродах 0.5–0.8 В, а слоев, содержащих сплав никеля или кобальта с медью – при напряжении 1.5–1.8 В. Толщину осаждаемых слоев задавали путем регулирования величины заряда, проходящего через цепь в каждом импульсе. Длительность импульсов изменяли в пределах от 1 до 300 с. В качестве дополнительного механизма регулирования использовали также длительность пауз, следовавших за импульсом высокого напряжения. Однако введение таких пауз, как и следовало ожидать, привело только к увеличению толщины последующего слоя меди, поскольку во время паузы ионы меди не расходовались, но продолжали диффундировать к катоду с предельной скоростью, а затем разряжались в начале следующего катодного импульса. Фактическая толщина каждого слоя изменялась в пределах от 50 до 400 нм, а число пар слоев составляло 10, 20 и 50. В этой серии экспериментов не происходило полного заполнения каналов пор.
Для рассматриваемых сплавов разность стандартных потенциалов их компонентов составляет около 0.6 В, а учитывая высокое перенапряжение разряда ионов никеля и кобальта, фактическая разность потенциалов электроосаждения может приблизиться к 0.8–1.0 В. Это означает, что потенциалы, при которых только начинается разряд ионов кобальта или никеля, на несколько сотен милливольт отрицательнее потенциалов, при которых ионы меди разряжаются уже в режиме предельного диффузионного тока.
Регулирование толщины чередующихся слоев и содержания электроположительного компонента (в данном случае меди) в соответствующих слоях представляет собой весьма простую задачу. Можно, например, измерить силу тока при заполнении пор металлической медью, используя растворы с несколькими разными значениями концентрации сульфата меди и постоянной концентрацией остальных компонентов. Напряжение на электродах при этом должно быть существенно ниже того, при котором начинается разряд ионов кобальта и никеля.
Затем с помощью полученных калибровочных кривых выбирают концентрацию сульфата меди, силу тока, и длительность катодных импульсов, обеспечивающие получение слоев чистой меди заданной толщины и слоев сплава с пониженным содержанием меди.
Для раствора конкретного состава используют следующую последовательность действий: на электроды подают постоянное напряжение 0.6–0.8 В в течение 1–2 мин и измеряют габаритную катодную плотность тока, применяемую в дальнейшем для осаждения медных слоев. Затем на новый электрод подают напряжение 1.5–1.7 В и измеряют среднюю габаритную катодную плотность тока, используемую в дальнейшем для осаждения слоев сплава, после чего продолжают вести электролиз при постоянном напряжении на электродах до начала резкого подъема плотности тока. Найденное таким образом время заполнения пор сплавом используют для расчета истинной катодной плотности тока или отношения истинной и габаритной катодной поверхности и для расчета продолжительности осаждения слоев меди и сплава заданной толщины:
(4)
${{i}_{{\text{и}}}} = {{\left( {hk2F} \right)} \mathord{\left/ {\vphantom {{\left( {hk2F} \right)} {\left( {At} \right)}}} \right. \kern-0em} {\left( {At} \right)}} = {{i}_{{\text{г}}}}({{{{S}_{{\text{г}}}}} \mathord{\left/ {\vphantom {{{{S}_{{\text{г}}}}} {{{S}_{{\text{и}}}}}}} \right. \kern-0em} {{{S}_{{\text{и}}}}}}).$Здесь iи – истинная катодная плотность тока в порах, iг – габаритная плотность тока, отнесенная ко всей фронтальной поверхности образца, k – плотность осаждаемого металла или сплава, F – число Фарадея, A – атомная масса металла, t – продолжительность осаждения, Sи – истинная площадь катодной поверхности, Sг – габаритная поверхность фронтальной стороны образца.
Измерив экспериментально время заполнения пор металлом, можно рассчитать отношение Sг/Sи и далее рассчитать время осаждения слоев заданной толщины. Изменяя концентрацию соли меди в растворе, можно пропорционально изменять предельный ток разряда ее ионов и, тем самым, регулировать содержание меди в сплаве:
(5)
$t = \left( {{{2Fk} \mathord{\left/ {\vphantom {{2Fk} A}} \right. \kern-0em} A}} \right)({{{{S}_{{\text{и}}}}} \mathord{\left/ {\vphantom {{{{S}_{{\text{и}}}}} {{{S}_{{\text{г}}}}}}} \right. \kern-0em} {{{S}_{{\text{г}}}}}})({1 \mathord{\left/ {\vphantom {1 {{{i}_{{\text{г}}}}}}} \right. \kern-0em} {{{i}_{{\text{г}}}}}})\Delta h.$Здесь t – продолжительность осаждения слоя меди заданной толщины, iг – габаритная плотность тока, измеренная при напряжении 0.6–0.8 В, k – плотность меди, i – экспериментально определенная габаритная плотность тока при подаче на электроды напряжения 0.6–0.8 В, Δh – требуемая толщина медных слоев.
Аналогичную формулу используют для расчета времени осаждения слоев сплава, но в данном случае в формулу подставляют значения габаритной плотности тока, измеренные при напряжении на электродах 1.5–1.7 В.
Описываемый метод основан на следующих принципиальных положениях: (1) при уменьшении концентрации в растворе электроположительного компонента пропорционально снижается скорость разряда его ионов и концентрация его атомов в осаждаемом сплаве; (2) смещение потенциала в отрицательном направлении от значений, при которых начинается разряд ионов электроотрицательного компонента, увеличивает скорость разряда только ионов электроотрицательного компонента, оставляя постоянной скорость разряда ионов электроположительного компонента (меди).
В данной работе использовали электролит с постоянной концентрацией всех компонентов, а регулирование состава сплава в осаждаемых слоях осуществляли только путем изменения напряжения на электродах. Стабилизации условий массопереноса в процессе заполнения пор способствовало использование мембран с количеством не менее 109 см–2. Однако увеличение эффективной толщины внешней части диффузионного слоя, достигаемое при этом, неизбежно сопровождается возрастанием переходного времени при чередовании разных электрических режимов и “размыванием” границ между слоями – т.е. образованием промежуточных зон с переменным составом сплава. Поэтому представляется целесообразным уменьшить и стабилизировать толщину внешней части диффузионного слоя применением перемешивания раствора.
Необходимо также подчеркнуть обреченность попыток получить чередующиеся тонкие слои с таким же стабильным соотношением компонентов сплава, как и для более толстых слоев, если время осаждения этих тонких слоев приближается к переходному времени установления стационарного режима массопереноса в прикатодной зоне раствора. Сплав промежуточного состава будет осаждаться в начальной стадии каждого импульса с повышенной плотностью тока (более отрицательным катодным потенциалом или повышенным напряжением на электродах).
Образование слоев промежуточного состава на границе слоя сплава и следующего за ним слоя электроположительного компонента, по-видимому, можно предотвратить путем введения паузы после окончания стадии осаждения слоев сплава с высоким содержанием электроотрицательного компонента. Пауза позволит накопить в приэлектродной зоне раствора ионы электроположительного компонента. В противоположность этому невозможно полностью исключить образование промежуточных слоев с изменяющимся соотношением компонентов при переходе от слоя чистого электроположительного компонента к слою сплава. Для максимального уменьшения толщины этих промежуточных слоев следует уменьшить эффективную толщину диффузионного слоя и, тем самым, переходное время при чередовании двух режимов массопереноса.
Анализ отдельных слоев, из которых состояли полученные нанопроволоки, показал, что в слоях, осажденных при повышенном напряжении, содержание меди в среднем составляло около 25%, а в слоях, осажденных при низком напряжении – более 95%. Возможная причина этого – образование зон промежуточного состава, но может быть также связана с ростом кристаллов и образованием пустот на границе медь/стенки поры, которые затем заполняются электроотрицательным металлом.
Как уже указывалось выше, при необходимости можно снизить содержание меди в слоях с преобладанием никеля или кобальта, а также уменьшить переходное время и, тем самым, толщину зон с промежуточным составом сплава, если применять перемешивание электролита и более высокую катодную плотность тока.
ЗАКЛЮЧЕНИЕ
Для стабилизации массопереноса в процессе формирования однослойных нанопроволок из индивидуального метала целесообразно использовать гальваностатический режим при любом расстоянии между порами. При электроосаждении нанопроволок из сплава для стабилизации его состава по длине проволоки предпочтительно использовать мембраны со средним расстоянием между порами, соизмеримым с их диаметром, в сочетании с гальваностатическим режимом.
При получении многослойных проволок более перспективен режим гальваностатических импульсов и мембраны, у которых среднее расстояние между порами существенно превышает их диаметр, что позволит уменьшить толщину промежуточных зон между слоями разного химического состава.
Новым перспективным направлением дальнейших исследований представляется электроосаждение нанопроволок из электролитов, содержащих добавки, используемые в гальванотехнике для управления микрораспределением электроосажденных металлов и сплавов. Поскольку воздействие таких добавок на кинетику электроосаждения металлов и сплавов контролируется скоростью их диффузии к катодной поверхности, можно надеяться, что с их помощью удастся добиться более равномерного роста нанопроволок в каналах всех пор.
Работа выполнена при поддержке Министерства науки и высшего образования в рамках выполнения работ по государственному заданию ФНИЦ “Кристаллография и фотоника” РАН в части выращивания металлических нанопроволок.
ОБОЗНАЧЕНИЯ
A | атомная масса |
d | эффективная толщина диффузионного слоя, см |
h | глубина поры, см |
I | сила тока, А |
i | плотность тока, А/см2 |
k | плотность металла или сплава, г/см3 |
R | сопротивление, Ом |
r | радиус поры, см |
S | площадь катодной поверхности, см2 |
t | время осаждения металла или сплава в порах, с |
x | толщина слоя металла в поре, см |
ρ | удельное сопротивление раствора, Ом см |
τ | переходное время, с |
ИНДЕКСЫ
Список литературы
Datta V., Landolt D. Fundamental aspects and applications of microfabrication // Electrochim. Acta. 2000. V. 45. P. 2535.
Solovjev D.S., Potlov A.Yu., Litovka Yu.V. Reduction of non-uniformity in the thickness of a galvanic coating using disabable anode sections under current reversal conditions // Theor. Found. Chem. Eng. 2019. V. 53. № 1. P. 97. [Соловьев Д.С., Потлов А.Ю., Литовка Ю.В. Снижнение неравномерности распределения толщины гальванического покрытия с использованием отключаемых анодных при реверсировании тока // Теор. осн. хим. технол 2019. Т. 53. № 1. С. 102.]
Kruglikov S.S., Kolesnikov V.A., Nekrasova N.E., Gubin A.F. Role of macro- and microdistribution in the formation of metal and alloy layers in the production of printed circuits and other components of electronic devices // Theor. Found. Chem. Eng. 2018. V. 52. № 6. P. 975. [Кругликов С.С., Колесников В.А., Некрасова Н.Е., Губин А.Ф. Роль факторов макро- и микрораспределения в процессах формирования слоев металлов и сплавов в производстве печатных плат и других компонентов электронных устройств // Теор. осн. хим. технол. 2018. Т. 52. № 6. С. 663.]
Koshev A.N., Varentsov V.K. Mathematical Modeling of Effective Systems of Reactors with Flow-Through 3D Electrodes // Theor. Found. Chem. Eng. 2018. V. 52. № 1. P. 87. [Кошев А.Н., Варенцов В.К. Математическое моделирование эффективных систем реакторов с проточными трехмерными электродами // Теор. осн. хим. технол. 2018. Т. 52. № 1. С. 93.]
Varentsov V.K., Koshev A.N., Sukhov I.F. Mathematical modeling and experimental studies of the joint electrodeposition of gold and silver from sulfuric acid thiourea solutions on flow-through 3D electrodes taking into account its nonstationary state // Theor. Found. Chem. Eng. 2018. V. 52. P. 495. [Варенцов В.К., Кошев А.Н., Сухов И.Ф. Процессы совместного электроосаждения золота и серебра из сернокислых растворов на проточном электроде // Теор. осн. хим. технол. 2018. Т. 52. С. 391.]
Koshev A.N., Varentsov V.K. Mathematical modeling of operation of a reactor with flow-through three-dimensional electrodes at limiting diffusion current under non-steady-state conditions // Theor. Found. Chem. Eng. 2018. V. 52. P. 779. [Кошев А.Н., Варенцов В.К. Математическое моделирование работы реактора с проточными трехмерными электродами в режиме предельного диффузионного тока в условиях нестационарности // Теор. осн. хим. технол. 2018. Т. 52. С. 497.]
Kruglikov S.S., Nekrasova N.E., Kuznetsov V.V., Filatova E.A. An electromembrane process for cadmium recovery from dilute cadmium electroplating dragout solutions // Membr. Membr. Technol. 2019. V. 1. № 2. P. 120. [Кругликов С.С., Некрасова Н.Е., Кузнецов В.В., Филатова Е.А. Электромембранный метод извлечения ионов кадмия из разбавленных растворов ванн улавливания после электрохимического кадмирования // Мембр. мембр. технол. 2019. Т. 9. № 2. С. 146.]
Kruglikov S.S., Kolesnikov V.A., Kuznetsov V.V., Gubin A.F. Regeneration of chromium electroplating electrolytes by the application of electromembrane processes // Theor. Found. Chem. Eng. 2018. V. 52. № 5. P. 800. [Кругликов C.C., Колесников В.А., Кузнецов В.В., Губин А.Ф. Регенерация электролитов хромирования с помощью электромембранных процессов // Теор. осн. хим. технол. 2018. Т. 26. № 5. С. 519.]
Коротков В.В., Кудрявцев В.Н., Кругликов С.С., Загорский Д.Л., Сульянов С.Н., Бедин С.А. Электроосаждение металлов группы железа в поры трековых мембран для получения нанопроволок // Гальванотех. обраб. поверхн. 2015. Т. 23. № 1. С. 24. [Korotkov V.V., Kudriavtsev V.N., Kruglikov S.S., Zagorskiy D.L., Sulianov S.N., Bedin S.A. Electrodeposition of metals of iron group into the pores of track membranes for the preparation of nanowires // Gal’vanotekh. Obrab. Poverkhn. 2015. № 1. P. 24.]
Davyidov A.D., Volgin V.M. Template electrodeposition of metals. Review // Russ. J. Electrochem. 2016. V. 52. P. 806. [Давыдов А.Д., Волгин В.М. Темплатное электроосаждение металлов (обзор) // Электрохимия. 2018. Т. 52. № 9. С. 905.]
Zagorskiy D.L., Korotkov V.V., Frolov K.V., Sulyanov S.N., Kudryavtsev V.N., Kruglikov S.S., Bedin S.A. Track Pore Matrixes for the Preparation of Co, Ni and Fe Nanowires: Electrodeposition and their Properties // Phys. Procedia. 2015. V. 80. P. 144.
Proenca M.P., Sousa C.T., Ventura J., Vazquez M., Araujo J.P. Nickel growth inside ordered arrays of alumina nanopores // Electrochim. Acta. 2012. V. 72. P. 215.
Tzaneva B.R., Naydenov A.I., Todorova S.Zh., Videkov V.H., Milusheva V.S., Stefanov P.K. Cobalt electrodeposition in nanoporous anodic aluminium oxide for application as catalyst for methane combustion // Electrochim. Acta. 2016. V. 191. P. 192.
Wang X.W., Yuan Z.H., Li J.S. Orientation growth of magnetic metal nanowires with face-centered cabio structure using template synthesis technique // Mater. Charact. 2011. V. 62. P. 642.
Bakonyi I., Peter L. Electrodeposited multilayer-films with giant magnetoresistance (GMR): Progress and problems // Prog. Mater. Sci. 2010. V. 55. P. 107.
Valizadeh S., George J.M., Leisner P., Hultman L. Electrochemical synthesis of nanowires in porous polycarbonate membranes // Thin Solid Films. 2002. V. 402. P. 262.
Pullini D., Busquets D., Ruotolo A., Innocenti G., Amigo V. Insights into pulsed of GMR multilayered nanowires // J. Magn. Magn. Mater. 2007. V. 316. P. e242.
Zagorskiy D.L., Frolov K.V., Bedin S.A., Perunov I.V., Chuev M.A., Lomov A.A., Doludenko I.M. Structure and Magnetic Properties of Nanowires of Iron Group Metals Produced by Matrix Synthesis // Phys. Solid State. 2018. V. 60. № 11. P. 2115. [Загорский Д.Л., Фролов К.В., Бедин С.А., Перунов И.В., Чуев М.А., Ломов А.А., Долуденко И.М. Структура и магнитные свойства нанопроволок из металлов группы железа, полученных методом матричного синтеза // Физ. тверд. тела. 2018. № 11. С. 2075.]
Ohgai T., Hashiguechi K. Functional Nanowires Array Electrodeposited into Nano-porous Membrane Thin Films // Phys.: Conf. Ser. V. 417. P. 012047.
Blanco S., Vagras R., Mostany J., Bonnas C., Scharifker B.R. Modeling the Growth of Nanowire Arrays in Porous Membrane Templates // J. Electrochem. Soc. 2014. V. 161. № 8. P. 3341.
Zhigalina O.M., Doludenko I.M., Khmelenin D.N., Zagorskiy D.L., Bedin S.A., Ivanov I.M. Structure of Cu/Ni Nanowires Obtained by Matrix Synthesis // Crystallogr. Rep. 2018. V. 63. № 3. P. 480. [Жигалина О.М., Долуденко И.М., Хмеленин Д.Н., Загорский Д.Л., Бедин C.А., Иванов И.М. Структура нанопроволок Cu/Ni, полученных методом шаблонного синтеза // Кристаллография. 2018. Т. 63. № 3. С. 455.]
Zhigalina O.M., Khmelenin D.N., Ivanov I.M., Zagorskiy D.L., Bedin S.A., Doludenko I.M. Electron microscopy of nanostructures formed by Cu-Ni layer nanowires // Nanomater. Nanostruct. – ХХI. V. 9. № 2. P. 23. [Жигалина О.М., Хмеленин Д.Н., Иванов И.М., Загорский Д.Л., Бедин С.А., Долуденко И.М. Электронная микроскопия слоистых наноструктур из нанопроволоки меди и никеля // Наноматер. нанострукт. – ХХI век. Т. 9. № 2. С. 23.]
Кругликов С.С. О некоторых особенностях использования потенциостатического режима при электроосаждении металлов и сплавов // Гальванотех. обраб. поверхн. 2016. Т. 24. № 1. С. 40. [Kruglikov S.S. Certain Features of the Electrodeposition of Metals and Alloys under Potentiostatic Conditions // Gal’vanotekh. Obrab. Poverkhn. 2016. № 1. P. 40.]
Дополнительные материалы отсутствуют.
Инструменты
Теоретические основы химической технологии