Вестник РАН, 2022, T. 92, № 10, стр. 940-949
НАУЧНО-ТЕХНИЧЕСКИЙ УРОВЕНЬ ИССЛЕДОВАНИЙ И ПЕРСПЕКТИВЫ ИМПОРТОЗАМЕЩЕНИЯ В ОБЛАСТИ ПРОМЫШЛЕННЫХ КАТАЛИЗАТОРОВ
a Федеральный исследовательский центр “Институт катализа им. Г.К. Борескова СО РАН”
Новосибирск, Россия
* E-mail: noskov@catalysis.ru
Поступила в редакцию 29.04.2022
После доработки 04.05.2022
Принята к публикации 14.06.2022
- EDN: YRAOLF
- DOI: 10.31857/S0869587322100085
Аннотация
В статье приводятся данные об обеспечении предприятий нефтепереработки, нефтехимической, химической и масложировой отраслей промышленности России отечественными базовыми катализаторами. Даётся оценка имеющегося в российских организациях научно-технического задела по катализаторам нефтепереработки (крекинг, риформинг, гидроочистка, гидрокрекинг), азотной промышленности (паровая конверсия природного газа и оксида углерода, синтез метанола), нефтехимии (полимеризация олефинов). Определяются ключевые задачи обеспечения импортонезависимости производства базовых катализаторов, которые связываются с необходимостью завершения НИОКР и создания производства высокотехнологичных сырьевых компонентов (прежде всего цеолитов и особо чистого активного оксида алюминия).
В основу статьи положен доклад, с которым автор выступил на заседании президиума РАН.
Уровень развития каталитических технологий определяет экономическую эффективность и экологическую безопасность почти всех процессов нефтепереработки и нефтехимии, а также химической промышленности. Получение моторного топлива (авиакеросина, дизельного топлива и высокооктанового бензина), крупнотоннажные производства полиэтилена и полипропилена, аммиака и метанола основаны на использовании катализа. В масложировой промышленности только он позволяет получать из растительного масла маргарин и специальные твёрдые жиры. Велика роль каталитических процессов в фармацевтике, поскольку без них не обходится производство лекарственных субстанций. В целом объём выпускаемой в России продукции на основе каталитических технологий можно оценить в 5–6 трлн руб./год.
Необходимым элементом таких технологий служат катализаторы. Их номенклатура включает в себя несколько сотен модификаций. В зависимости от особенностей процессов время жизни катализаторов в реакторе составляет от нескольких часов (каталитический синтез полиэтилена и полипропилена) до 10 лет (процесс метанирования при производстве аммиака). Объём потребления катализаторов в России достигает почти 70 тыс. т в год. В силу разных обстоятельств доля импортных катализаторов в промышлнных процессах составляет от 30–40% (отдельные процессы нефтепереработки) до 100% (большинство процессов нефтехимии). Анализу обеспечения базовыми катализаторами российских предприятий нефтепереработки, нефтехимической, химической и масложировой отраслей промышленности, а также перспективам замещения используемых импортных катализаторов отечественными посвящена настоящая статья.
Оценка текущей ситуации. Исходным материалом для анализа послужили данные рабочей группы по импортозамещению промышленных катализаторов нефтепереработки и нефтехимии при Минэнерго России (руководитель группы член-корреспондент РАН А.С. Носков). Приведённые в таблице 1 сводные данные можно прокомментировать следующим образом.
Таблица 1.
Анализ обеспечения базовыми катализаторами российских предприятий
№ пп |
Катализатор | Объём потребления катализатора, т/год | Доля импорта, % | Обеспечение катализаторами, перспективы развития |
---|---|---|---|---|
Нефтепереработка | ||||
1 | Катализаторы крекинга (FCC/движущийся слой) | (12 000–14 000)/3000 | ~40/0 | Надёжное обеспечение. Запланировано развитие производства в г. Омске (ПАО “Газпром нефть”) |
2 | Катализаторы риформинга (неподвижный/движущийся слой) | 200/100 | ~35/100 | Надёжное обеспечение для неподвижного слоя. Развитие производства в г. Ангарске (ПАО “НК “Роснефть”) |
3 | Катализаторы гидроочистки (нефтяных фракций) | 3500–4000 | 60–70 | В настоящее время значительная зависимость от импорта. Ведутся разработки и промышленное опробование катализаторов в ПАО “НК “Роснефть” и ПАО “Газпром нефть”. Завершается создание производства в г. Омске |
4 | Катализаторы гидрокрекинга | 1000–1500 | ~100 | В настоящее время практически полная зависимость от импорта. Ведутся исследования и разработки отечественных катализаторов |
5 | Катализаторы производства зимних (арктических) топлив и масел | 150–200 | 100 | В настоящее время практически полная зависимость от импорта. Ведутся исследования и разработки отечественных катализаторов |
6 | Катализаторы изомеризации бензиновых фракций | 200–250 | 40(ZrO2)/ 100 (Al2O3) | Надёжное обеспечение отечественными катализаторами на основе ZrO2 и практически полная зависимость от импорта катализаторов на основе Al2O3 |
7 | Катализаторы производства водорода: • риформинг метана • конверсия оксида углерода |
8500–9000 (с учётом производства метанола и аммиака) | Более 90% | Обеспечение отечественными катализаторами только ранее построенных установок на НПЗ. Есть научные заделы для производства современных марок катализаторов |
8 | Активный оксид алюминия (обычный Al2O3/особо чистый Al2O3) | (10 000–15 000)/(200–250) | (5–10)/100 | Производство обычного Al2O3 обеспечивается отечественными производителями. Производство особо чистого Al2O3 отсутствует |
9 | Цеолиты: – ультрастабильный Y |
1500 | 0 | Производство цеолитов типа Y и ZSM-5 обеспечивается российскими предприятиями. Производство остальных цеолитов в России отсутствует |
– ZSM-5 | 150 | 0 | ||
– ZSM-11(12); BETA; ZSM-22; SAPO-41 и др. | 200–300 | 100 | ||
Нефтехимия | ||||
10 | Катализаторы полимеризации олефинов: – этилена – пропилена |
270 54 |
>80 100 |
Практически полная зависимость от импорта |
11 | Катализаторы окисления этилена в этиленоксид | 150–200 | 100 | Зависимость от импорта. Ведутся разработки в российских компаниях |
12 | Катализаторы дегидрирования | |||
– изобутана в изобутилен | 15000–20000 | 0 | Полное обеспечение российскими катализаторами | |
– бутана в бутадиен | 200 | 100 | Зависимость от импорта. Ведутся разработки в российских организациях | |
– изопентана в изопрен | 10000 | 0 | Полное обеспечение российскими катализаторами | |
– пропана в пропилен | 100 | 100 | Зависимость от импорта. Ведутся разработки в российских компаниях | |
13 | Катализаторы производства терефталевой кислоты | 400 | 100 | Полная зависимость от импорта |
14 | Катализаторы синтеза акрилонитрила (НАК) | 150 (300 с Республикой Беларусь) | 100 | Критическая зависимость от импорта. Использование НАК в производстве углеродных волокон |
15 | Катализаторы синтеза винилхлорида | 600 | 100 | Подготовлено производство отечественных катализаторов |
16 | Катализаторы алкилирования бензола | 3000–3500 | _ | Отечественные катализаторы разработаны. Необходим переход с AlCl3 на твердокислотные катализаторы |
17 | Катализаторы синтеза акриловой кислоты | 100–150 | 100 | Зависимость от импорта. Имеется научный задел |
Масложировая промышленность | ||||
18 | Катализаторы гидрирования растительных масел | 400 | 100 | Полная зависимость от импорта. Имеется научный задел |
Каталитические процессы, разработанные и промышленно освоенные в середине XX в., базировались на использовании отечественных катализаторов. В ряде производственных цепочек это удаётся и сейчас. В качестве примеров можно привести обеспеченность российскими катализаторами установок процесса крекинга и риформинга (табл. 1, пп. 1, 2) в нефтепереработке, часть процессов дегидрирования в нефтехимии (табл. 1, п. 12). Имеющийся в России научно-технический задел и производственные мощности по выпуску катализаторов позволяют относительно легко и оперативно восполнить их недостающие объёмы, чтобы заменить импортные аналоги. Уровень отечественных разработок не уступает лучшим зарубежным.
Массовое использование российскими заводами импортных катализаторов на установках крекинга вакуумного газойля, риформинга и изомеризации бензиновых фракций, начиная с последнего десятилетия XX в., обусловлено активным маркетингом и сервисными услугами со стороны зарубежных поставщиков. В настоящее время такие услуги в полной мере предоставляются и российскими производителями катализаторов.
Другая группа крупнотоннажных процессов нефтепереработки начала массово применяться на российских нефтеперерабатывающих заводах преимущественно уже в XXI в. (табл. 1, пп. 3–5). Вследствие требований лицензиаров в этих установках использовались только импортные катализаторы. Однако наличие научного задела в институтах РАН, университетах и исследовательских центрах нефтяных компаний позволило достаточно оперативно разработать технологии синтеза российских аналогов. В настоящее время на ряде заводов ПАО “НК “Роснефть” и ПАО “Газпром нефть” начата эксплуатация отечественных катализаторов собственного производства. Действующие мощности АО “РН-кат” (ПАО “НК “Роснефть”) и вновь создаваемые в Омске (ПАО “Газпром нефть”) вполне обеспечат потребности российских заводов в катализаторах гидроочистки, высок также их экспортный потенциал. Завершена разработка катализаторов гидрокрекинга вакуумного газойля, готовятся их опытно-промышленные испытания. Сложнее ситуация с катализаторами, применяемыми в производстве зимних (арктических) топлив и масел (табл. 1, п. 5). Хотя и здесь отечественные разработки не уступают импортным аналогам, компонентный состав этих катализаторов предполагает использование импортных синтетических цеолитов, поэтому требуется развёртывание производства широкой номенклатуры синтетических цеолитов на российских заводах.
Проблема импортозамещения катализаторов производства водорода (табл. 1, п. 7) двояка: если ранее построенные установки генерации водорода на нефтеперерабатывающих заводах (НПЗ) обеспечиваются российскими катализаторами в полной мере, то вновь построенные установки на НПЗ и, что особенно важно, на заводах по крупнотоннажному производству аммиака и метанола базируются практически полностью на импортных.
Производство современных российских катализаторов нефтепереработки и нефтехимии невозможно без обеспечения необходимым высокотехнологичным сырьём. Это касается прежде всего ряда марок активного оксида алюминия и необходимой номенклатуры синтетических цеолитов (табл. 1, пп. 8, 9). Потребность в активном оксиде алюминия массовых марок вполне обеспечивается его производством на ряде заводов (ООО “КНТ-Групп”, АО “СКТБ катализаторов”, вновь создаваемые мощности ПАО “Газпром нефть” в Омске). Открытым остаётся вопрос выпуска особо чистого активного оксида алюминия, необходимого для катализаторов риформинга бензиновых фракций и дегидрирования пропана в реакторах с движущимся каталитическим слоем. Необходимость создания производства такого оксида алюминия в России обусловлена фактически монопольным положением на мировом рынке компании Sasol (ЮАР–Германия).
В нефтехимии ситуация с импортозамещением катализаторов гораздо сложнее. За исключением разработанных в СССР процессов дегидрирования лёгких углеводородов в кипящем слое (табл. 1, п. 12), практически во все крупнотоннажные установки нефтехимии загружены импортные катализаторы (табл. 1, пп. 10, 11, 13–17). Следует особо отметить проблему производства катализаторов полимеризации олефинов: они служат расходным материалом, и прекращение их поставок из-за рубежа в течение весьма короткого времени (несколько месяцев) может привести к остановке крупнейших российских заводов по производству полиэтилена и полипропилена.
Научный задел в российских НИИ и университетах позволяет достаточно оперативно решить задачу развёртывания отечественного производства катализаторов окисления этилена в этиленоксид (табл. 1, п. 11), дегидрирования бутана в бутадиен под вакуумом (табл. 1, п. 12), синтеза акрилонитрила (табл. 1, п. 14). Для импортозамещения катализаторов синтеза винилхлорида подготовлено их производство (ООО “КНТ-Групп”), при необходимости российские разработки могут быть оперативно введены в эксплуатацию в реакторах с кипящим каталитическим слоем. Аналогично обстоят дела с катализаторами алкилирования бензола (табл. 1, п. 16). Современные процессы алкилирования бензола базируются на применении твердокислотных цеолитсодержащих катализаторов, разработанных совместными усилиями Института нефтехимического синтеза РАН и НТЦ “Газпромнефтехим Салават”. Они используются в промышленных условиях и вполне позволяют заменить традиционные экологически опасные катализаторы (AlCl3) в данных процессах.
Стремительное развитие в России производств терефталевой кислоты (основной компонент синтеза полиэтилентерефталата) и акриловой кислоты, к сожалению, полностью базируется на импортных катализаторах (табл. 1, пп. 13, 17). Отечественные исследования в этой области относятся преимущественно к концу XX в. Сегодня необходимо восстановить научные коллективы, занимавшиеся созданием таких катализаторов, провести дополнительные НИОКР по актуализации ранее полученных результатов, разработке необходимых технологических решений.
Актуальна задача выпуска отечественных катализаторов гидрирования растительных масел (табл. 1, п. 18). Хотя в российских научных организациях есть задел по этой теме, промышленное производство маргарина и специальных жиров полностью базируется на импортных катализаторах, причём, как правило, однократного применения.
Научно-технический и промышленный потенциал российских организаций. В качестве положительных примеров высокого научного уровня исследований, результаты которых нашли применение в производстве катализаторов нефтепереработки, следует, в частности, упомянуть катализаторы крекинга вакуумного газойля и риформинга бензиновых фракций [1–3].
Катализаторы крекинга (рис. 1) представляют собой сложную композиционную систему, где каждый компонент отвечает за реализацию определённых химических реакций. Первичный крекинг высокомолекулярных углеводородов, содержащих более 30 атомов углерода, происходит на неорганических компонентах катализатора (матрице). Следующую стадию обеспечивает ультра-стабильный цеолит типа Y, позволяющий получать из углеводородов высокооктановый бензин. Для получения сырья (олефинов – этилена и пропилена) для нефтехимии служит цеолит ZSM-5.
К настоящему времени разработан широкий ассортимент катализаторов крекинга различного назначения [1]: для максимального выхода бензина (до 60%); получения лёгких олефинов – этилена и пропилена (выход более 25%); переработки тяжёлого вакуумного газойля, содержащего много металлов (до 10000 ppm никеля и ванадия); снижения выбросов токсичных компонентов (оксидов углерода, азота и серы) в газах регенерации катализаторов.
Промышленные мощности АО “Газпромнефть–Омский НПЗ” и ООО “КНТ-Групп” (г. Ишимбай, Башкортостан), а также строящийся в Омске завод АО “Газпромнефть–Каталитические системы” полностью обеспечат все потребности российских НПЗ и возможность выхода на зарубежные рынки. За последние годы российскими заводами произведено около 60 тыс. т катализаторов крекинга, с их применением переработано более 120 млн т сырья (вакуумного газойля) в автомобильный бензин.
Научные исследования в области катализаторов крекинга активно развиваются прежде всего в омском Центре новых химических технологий (ЦНХТ) ФИЦ “Институт катализа СО РАН” [1] и ООО “КНТ-Групп”, что надёжно обеспечивает импортозамещение сегодня и гарантирует его в будущем.
Достаточно продуктивно развиваются научные исследования (с последующим их промышленным использованием) в области катализаторов риформинга для неподвижного слоя, обеспечивающих получение высокооктанового бензина из низкооктанового прямогонного (рис. 2). Катализаторы риформинга базируются на применении особо чистого активного оксида алюминия, промотированного несколькими металлами (цирконий, олово, титан и др.), а в качестве активного компонента выступает платина. В ходе синтеза катализаторов требуется обеспечить необходимую дисперсность платины (около 1 нм) и её стабильность на весь срок службы катализатора (4–6 лет).
Основные научные исследования в области катализаторов риформинга проводятся в упоминавшемся омском ЦНХТ [2] и краснодарском ООО “НПП Нефтехим” [4]. Промышленное производство таких катализаторов осуществляют АО “Ангарский завод катализаторов и органического синтеза” (ПАО “НК “Роснефть”), а также ООО “Нижегородские катализаторы” с участием ООО “НПП Нефтехим”. За последние годы в хозяйственный оборот введено более 1000 т катализаторов риформинга, что позволяет ежегодно перерабатывать более 8 млн т бензинового сырья. Дальнейшее развитие отечественного производства катализаторов такого назначения связано с модернизацией завода в Ангарске, а также с разработкой и началом производства в России специального шарикового катализатора для установок с движущимся слоем. По прогнозным оценкам к 2025 г. использование российских катализаторов риформинга в промышленных установках достигнет 70–75%.
Потребность российских нефтеперерабатывающих заводов в современных катализаторах гидроочистки нефтяных фракций (прежде всего дизельного топлива и вакуумного газойля) обусловила активное развитие исследований в ФИЦ “Институт катализа СО РАН” [5], Самарском государственном техническом университете [6], ООО “РН–ЦИР” (ПАО “НК “Роснефть”), ООО “Газпромнефть–Промышленные инновации” и др. В общем виде схема синтеза катализаторов гидроочистки приведена на рисунке 3. Наибольшее влияние на активность таких катализаторов имеют свойства носителя. Исходным сырьём для получения пористых носителей сложных форм служат соединения алюминия (псевдобемит) специальной морфологии. Другой активный компонент синтеза катализаторов – би(три)металлические комплексы металлов (кобальта, молибдена, никеля, вольфрама). Синтезированные комплексы непременно должны обладать водорастворимостью, что обеспечивает их нанесение на твёрдые пористые носители путём пропитки. На завершающей стадии синтеза нанесённые на носители оксидные комплексы в промышленных реакторах переводятся в каталитически активное состояние с использованием процесса сульфидирования.
В настоящее время катализаторы гидроочистки производят ООО “РН-кат” (г. Стерлитамак, Башкортостан) и ООО “Газпромнефть–Каталитические системы”. В 2020–2022 гг. они ввели в промышленную эксплуатацию около 600 т катализаторов гидроочистки, а после завершения в 2022 г. строительства в Омске нового катализаторного завода (ПАО “Газпром нефть”) суммарное их производство в России составит около 8 тыс. т/год. Это позволит не только полностью обеспечить потребности российских заводов, но и выйти на внешние рынки.
Развитие процессов глубокой переработки нефти обусловило формирование спроса на катализаторы гидрокрекинга тяжёлых нефтяных фракций – вакуумного газойля. Процесс гидрокрекинга – один из самых сложных в нефтепереработке. Он осуществляется при давлении около 200 атм. и большом избытке водорода (объёмное отношение водорода к сырью – до 2000). Такие условия позволяют получать из тяжёлого сырья с температурой кипения до 700°С высококачественное дизельное топливо и авиационный керосин. Степень совершенства процесса гидрокрекинга можно охарактеризовать следующим показателем: в ходе процесса содержание соединений серы снижается в 10 000 раз! Катализаторы гидрокрекинга совмещают в своём составе крекирующие (USY) и гидрирующие (NiMo(W)S) компоненты (рис. 4а). В качестве гидрирующих компонентов выступают сульфиды металлов (никеля, молибдена, вольфрама), а за крекинг тяжёлых углеводородов отвечают ультрастабильные цеолиты типа Y. Необходимым условием обеспечения эффективности катализаторов гидрокрекинга служит наличие в цеолитах мезопористой структуры. Это требует специальных методов обработки исходных синтетических цеолитов с целью увеличения объёма мезопор (рис. 4б), что очень важно, поскольку, например, увеличение объёма мезопор в 2 раза (с 0.19 до 0.39 см3/г) ведёт к росту выхода дизельного топлива и керосина на 10%, а для типичной промышленной установки гидрокрекинга прирост составляет около 200 тыс. т дополнительного моторного топлива в год. Суммарный выход светлых нефтепродуктов (нафта, авиационный керосин, дизельное топливо) в процессе гидрокрекинга превышает 95%.
Рис. 4.
Структура катализаторов гидрокрекинга тяжёлых нефтяных фракций: а – наличие гидрирующего (NiMo(W)S) и крекирующего (USY) компонентов; б – модифицирование цеолита Y
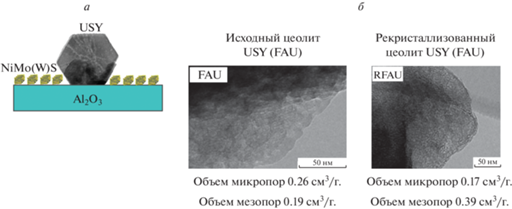
В настоящее время научные исследования ФИЦ “Институт катализа СО РАН”, Института нефтехимического синтеза (ИНХС) РАН, МГУ им. М.В. Ломоносова с участием ПАО “Газпром нефть” [7], ООО “РН-ЦИР” позволили разработать отечественные катализаторы гидрокрекинга, не уступающие известным образцам зарубежных компаний. Промышленное их производство возможно в ООО “РН-кат” в объёме до 1000 т/год и на строящемся заводе ПАО “Газпром нефть” – до 2000 т/год. Необходимым первым шагом по замене импортных катализаторов на отечественные должна стать наработка и испытания опытно-промышленной партии катализатора гидрокрекинга на одной из промышленных установок. Сдерживающими факторами оказываются лицензионные ограничения на использование отечественных катализаторов и большой объём единовременной загрузки катализатора в отдельный реактор (100–200 т). Последнее обстоятельство обусловливает технологический риск при использовании вновь разработанного катализатора гидрокрекинга.
Весьма сложная ситуация складывается с обеспечением отечественными катализаторами предприятий азотной промышленности. Это касается катализаторов для установок получения водорода (катализаторы парового риформинга природного газа и средне(высоко)температурной паровой конверсии CO) в составе комплексов синтеза аммиака и метанола, а также собственно катализаторов синтеза метанола (рис. 5).
Рис. 5.
Катализаторы, используемые в азотной промышленности и при получении водорода: а – катализаторы парового риформинга природного газа; б – катализаторы паровой конверсии оксида углерода; в – катализаторы синтеза метанола
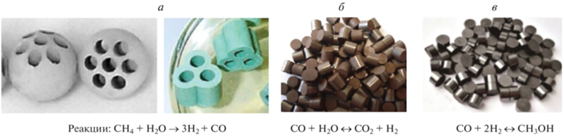
Современные катализаторы парового риформинга природного газа должны демонстрировать устойчивую работу при соотношениях пар/газ не более 2. Избыток водяного пара ведёт к росту энергозатрат. К сожалению, научные исследования в этой области катализа ведутся в России в крайне ограниченном объёме. Продукты, производимые ООО “НИАП-катализатор” (г. Новомосковск, Тульская область) и АО “Ангарский завод катализаторов и органического синтеза”, используются, как правило, на относительно небольших установках азотной промышленности и построенных в ХХ в. установках получения водорода на предприятиях нефтеперерабатывающей промышленности. Суммарный объём производства этих катализаторов в России не превышает 400 т/год, что примерно в 10 раз меньше годовой потребности российских заводов (около 4000 тонн). Для устранения импортозависимости необходимо восстановление опытно-испытательной базы по тестированию катализаторов парового риформинга природного газа (ООО “НИАП-катализатор”) и создание современного их производства на основе российских научных разработок (см. рис. 5).
Несколько более оптимистичны перспективы преодоления импортозависимости в области катализаторов паровой средне- и низкотемпературной конверсии оксида углерода и синтеза метанола. На основе исследований ФИЦ “Институт катализа СО РАН”, Института органической химии РАН, Института нефтехимического синтеза РАН и ООО “НИАП-катализатор” разработана единая технологическая платформа, позволяющая производить упомянутую номенклатуру катализаторов. Технология основана на процессе осаждения катионов металлов из водных растворов солей, обеспечивающем глубокое химическое взаимодействие компонентов и гарантированное качество конечного продукта, она была опробована на Ульбинском металлургическом заводе (г. Усть-Каменогорск, Казахстан) в 1990-е годы. Выпущенные этим предприятием катализаторы успешно эксплуатировались на ряде заводов азотной промышленности. В настоящее время производственные мощности позволяют производить в России не более 400–500 т/год катализаторов средне- и низкотемпературной конверсии оксида углерода и синтеза метанола при годовой потребности в этих катализаторах около 5000 т к 2025 г. Одним из вариантов решения проблемы может стать создание их производства на мощностях АО “ТВЭЛ”.
Пожалуй, наиболее острая на сегодня проблема – импортозамещение катализаторов полимеризации этилена и пропилена. Наряду с практически полной зависимостью российских предприятий нефтехимии от их импорта, ситуация осложнена одноразовым использованием катализаторов полимеризации в технологических процессах. Прекращение поставок этого расходного материала с неизбежностью ведёт к остановке крупнейших производств полиэтилена и полипропилена в России.
В России создан научный задел практически для всей номенклатуры современных катализаторов полимеризации олефинов. Это, в частности, титан-магниевые катализаторы (ТМК) [8, 9], уже производимые на основе российских исследований, но только не в нашей стране, а за рубежом. Предложено и освоено производство хромовых катализаторов полимеризации [10]. Разработан метод синтеза металлоценовых и постметаллоценовых катализаторов полимеризации [11], а также заложены научные основы синтеза носителей для катализаторов на основе диоксида кремния. Исследовательские возможности по синтезу катализаторов полимеризации сосредоточены главным образом в институтах РАН (ФИЦ “Институт катализа СО РАН”, Институт нефтехимического синтеза РАН, Институт химической физики РАН), МГУ им. М.В. Ломоносова и ОАО “Пластполимер” (Санкт-Петербург). Для промышленных испытаний ТМК-синтеза полиэтилена в России имеется опытно-промышленная установка, позволяющая нарабатывать до 1 т катализаторов в год. Для преодоления импортозависимости в области катализаторов полимеризации олефинов необходимо на первом этапе создать производство ТМК мощностью до 150 т/год. Такое производство позволит в дальнейшем расширять номенклатуру выпуска за счёт синтеза перспективных металлоценовых и постметаллоценовых катализаторов, а также нефталатных катализаторов полимеризации. Современный уровень российских разработок вполне позволяет организовать такое производство в течение 3–4 лет.
Одной из составных частей продуктовой безопасности России является производство твёрдых жиров из растительного масла. Объём выпуска маргарина и специальных жиров в России достигает 1.5 млн т/год. Без этой масложировой продукции невозможно обойтись при выпуске широкой номенклатуры продуктов питания, прежде всего хлебобулочной и кондитерской продукции. Технология переработки растительного масла в маргарин и спецжиры основана на его гидрировании. Процесс протекает в больших ёмкостных реакторах на специальных катализаторах с подачей водорода и длится около 5 часов, затем мелкодисперсный катализатор отфильтровывают из продукта и отправляют на металлургические заводы для переработки. Фактически катализатор служит расходным материалом и используется однократно. Традиционные катализаторы представляют собой композицию, состоящую из металла, нанесённого на природный материал – кизельгур. В настоящее время практически все российские масложировые предприятия используют импортные катализаторы. В то же время научный задел в области катализаторов гидрирования позволяет в течение 1.5–2 лет преодолеть такую зависимость и создать производство отечественных катализаторов на основе экологически безопасного синтетического диоксида кремния. Потребность в катализаторах относительно невелика – до 400 т/год, однако значение процессов, в которых применяются эти катализаторы, крайне важно для отечественной пищевой промышленности.
Производство подавляющего большинства современных крупнотоннажных катализаторов нефтепереработки и нефтехимии требует использования высокотехнологичной сырьевой базы. В качестве одного из важнейших сырьевых компонентов выступают синтетические цеолиты (рис. 6). Технология их синтеза предполагает использование высоких давлений и температур и специального оборудования (автоклавов). В катализаторах нефтепереработки и нефтехимии применяются различные марки цеолитов – от простейших типа Y (в катализаторах крекинга вакуумного газойля) до весьма химически сложных по составу и производству цеолитов типа SAPO-31 (катализаторы получения зимних (арктических) топлив и масел). В научных организациях России накоплен значительный потенциал по основам синтеза широкого ассортимента цеолитов: ZSM-5, ZSM-22 и 23, SAPO-31 и 41 и др.
Рис. 6.
Примеры синтетических цеолитов: а – структура цеолитов; б – микрофотография цеолита марки ZSM-5
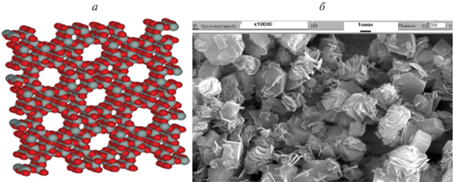
Научные компетенции сотрудников Института нефтехимического синтеза РАН, химического факультета МГУ им. М.В. Ломоносова, ФИЦ “Институт катализа СО РАН”, Башкирского научного центра РАН, а также малого предприятия ООО “Цеолитика” соответствуют мировому уровню. В качестве примера можно привести передовую разработку (ИНХС РАН, ООО “Цеолитика”, МГУ) нового бессточного метода синтеза цеолитов. К сожалению, в России в промышленных масштабах производятся фактически только две марки цеолитов (типа Y и ZSM-5). Для решения проблемы импортозамещения катализаторов нефтепереработки и нефтехимии требуется создание производства широкой номенклатуры синтетических цеолитов мощностью до 800 т/год на основе научных разработок отечественных организаций.
٭ ٭ ٭
Подводя итоги необходимо отметить следующее.
На основе научных разработок институтов РАН, вузов и исследовательских центров крупных компаний создана технологическая база импортонезависимости России в области массовых базовых катализаторов нефтепереработки.
В области катализаторов нефтехимии (прежде всего катализаторов полимеризации) научный задел институтов РАН и отдельных вузов (МГУ) позволяют обеспечить импортозамещение ряда катализаторов при создании промышленных мощностей.
Один из ключевых вопросов импортонезависимости – обеспечение российских производств катализаторов высокотехнологичными сырьевыми компонентами (прежде всего синтетическими цеолитами и особо чистым оксидом алюминия). Для решения этой задачи целесообразна интеграция научных организаций и производственных компаний в едином комплексном проекте.
Список литературы
Доронин В.П., Сорокина Т.П., Потапенко О.В. и др. Возможности современной технологии производства катализаторов крекинга на АО “Газпромнефть–ОНПЗ” // Катализ в промышленности. 2016. № 6. С. 71–76.
Белый А.С., Смольков М.Д., Кирьянов Д.И. и др. Катализаторы риформинга. Разработка и освоение технологии производства // Деловой журнал Nef-tegaz. RU. 2020. № 3 (99). С. 38–42.
Пинаева Л.Г., Доронин В.П., Белый А.С. и др. Современные катализаторы нефтепереработки: научно-технический уровень и обеспечение российскими катализаторами предприятий топливно-энергетического комплекса России // Мир нефтепродуктов. Вестник компаний. 2020. № 2. С. 6–16.
Шакун А.Н., Фёдорова М.Л. Российские катализаторы и технологии для производства высококачественных автомобильных бензинов // Форум “Инновационные технологии в области производства и использования горюче-смазочных материалов”. СПб., 2013. С. 60–68.
Klimov O.V., Pashigreva A.V., Fedotov M.A. et al. Co–Mo Catalysts for Ultra-Deep HDS of Diesel Fuels Prepared via Syntesis of Bimetallik Surfase Compounds // Journal of Molecular Catalysts A: Chemical. 2010. V. 322. № 1–2. P. 80–89.
Пимерзин А.А., Никульшин П.А., Томина Н.Н. Высокоактивные сульфидные катализаторы для гидрогенизационных процессов нефтепереработки // III Российский конгресс по катализу “Роскатализ”. Тезисы докладов конгресса. 2017. С. 244.
Казаков М.О., Надеина К.А., Климов О.В. и др. Разработка новых отечественных катализаторов глубокой переработки вакуумного газойля // Катализ в промышленности. 2016. № 6. С. 85–93.
Салахов И.И., Батыршин А.З., Сергеев С.А. и др. Полимеризация пропилена в жидком мономере в присутствии современных высокоэффективных титан-магниевых катализаторов // Катализ в промышленности. 2014. № 2. С. 27–31.
Микенас Т.Б., Захаров В.А., Никитин В.Е. и др. Нанесённые катализаторы циглерового типа для производства полиэтилена (ПЭ): влияние состава активного компонента, способов его формирования и модификаторов на активность катализаторов и молекулярную структуру ПЭ и сополимеров этилена с α-олефинами // Катализ в промышленности. 2011. № 2. С. 22–28.
Патент РФ 2289591. Способ получения полиэтилена низкого давления. Акланов В.А., Баулин А.А., Бобров Б.Н., Кудряшов В.Н., Поташкин А.Ф. // Опубл. 20.12.2006. Бюл. № 35.
Нифантьев И.Э., Сметанников О.В., Тавторкин А.Н. и др. Титаномагниевые нанокатализаторы полимеризации // Наногетерогенный катализ. 2016. № 1. С. 19–30.
Дополнительные материалы отсутствуют.