Вестник Военного инновационного технополиса «ЭРА», 2022, T. 3, № 1, стр. 75-84
ПОЛУЧЕНИЕ НОВЫХ ТИПОВ КОМПОЗИТНОГО УГЛЕРОДНОГО ВОЛОКНА ДЛЯ 3D-ПЕЧАТИ НА ОСНОВЕ ВЫСОКОТЕМПЕРАТУРНЫХ ПОЛИМЕРОВ
Д. С. Александрова 1, 2, А. С. Егоров 1, 2, *, М. В. Комарова 1, 2
1 Национальный исследовательский центр “Курчатовский институт”
Москва, Россия
2 Институт химических реактивов и особо чистых химических веществ
Национального исследовательского центра “Курчатовский институт”
Москва, Россия
* E-mail: egorov@irea.org.ru
Поступила в редакцию 15.12.2021
После доработки 11.01.2022
Принята к публикации 11.01.2022
Аннотация
Протестировано аппретирование углеродного волокна композициями различной природы под высокотемпературные полимерные связующие. Для каждого аппретирующего состава подобрана рабочая концентрация. На основе аппретированного волокна получены образцы препрегов с различными связующими с высокими рабочими температурами. Качество полученных препрегов изучено при помощи метода сканирующей электронной микроскопии. С использованием полученных образцов препрегов наилучшего состава напечатаны образцы изделий при помощи метода послойного наплавления.
ВВЕДЕНИЕ
Пластики, армированные при помощи непрерывных волокон (стеклянных, углеродных, полимерных и др.), широко используются в специальных областях современной техники [1–4]. Без их применения в настоящее время уже невозможно представить ракетостроение или авиацию, все большее применение они находят в других областях народного хозяйства – машиностроении, судостроении, строительстве и т.д. Подобное широкое распространение полимерные композиты получают благодаря своей высокой прочности [5, 6], сочетающейся с легкостью [7]. В настоящий момент способы получения армированных волокном композитных изделий достаточно трудоемки и существенно ограничивают геометрию получаемого изделия [8]. Причины этого заключаются в сложности пропитывания волокна вязкими растворами/расплавами полимеров, а также необходимости использования формы или каркаса для формования изделия до момента его отверждения.
Изготовление армированных углеродным волокном композитов при помощи метода послойного наплавления (одной из разновидностей 3D‑печати) является перспективным путем решения проблемы производства изделий сложной формы [9]. Использование этого метода предполагает предварительную пропитку углеродного волокна полимерным связующим с получением специальной композитной нити – препрега, предназначенной для использования в 3D-принтере. Получение препрегов проходит в несколько этапов. Сначала волокно обрабатывают аппретирующим составом – специальной композицией, которая не только предохраняет волокно от повреждений, но и облегчает пропитку и улучшает адгезию между углеродным волокном и полимерным связующим. Подбор подходящего аппрета – важная стадия получения препрегов, так как от нее будет существенно зависеть качество пропитки углеволокна, а также прочность конечного композита [10]. Выбор полимерного связующего для пропитки волокна определяется желаемыми свойствами конечного изделия, а также пластиком, который планируется армировать этим волокном. В настоящее время большой интерес проявляется к композитам на основе высокотемпературных термопластичных связующих [11–13], которые являются идеальными кандидатами для получения препрегов.
Цель данной работы – получение образцов композитного углеродного волокна на основе высокотемпературных пластиков, пригодного для изготовления изделий методом послойного наплавления. В рамках работы изучено влияние аппретирующих составов различной природы на технологические свойства получаемого волокна и дальнейшую пропитку волокна полимерными связующими различного типа. Также предложены разнообразные типы полимерных связующих.
ЭКСПЕРИМЕНТАЛЬНАЯ ЧАСТЬ
Материалы. Для синтеза аппретирующих композиций и пропитывающих полимеров использовали коммерчески доступные реагенты.
Диангидриды карбоновых кислот: диангидрид 3,3', 4,4'-бензофенонтетракарбоновой кислоты (БФДА), пиромеллитовый диангидрид (ПМДА) и 4,4'-(гексафторизопропилиден)дифталевого диангидрид (6-FDA) прокаливали перед использованием в вакууме в течение 8 ч при температурах 220, 215 и 150°С соответственно.
4,4'-оксидианилин (ОДА), толуилендиизоцианат (ТДИ), γ‑изоцианопропил-триметилсилан и (3-аминопропил)триэтоксисилан использовали без дополнительной очистки и подготовки.
9,9-бис-(4´-аминофенил)флуорен получали конденсацией анилина с 9-флуореном, как описано в [14].
Растворители высушивали перегонкой над соответствующим осушителем.
Подготовка мономерных аппретирующих композиций. γ-изоцианопропил-триметилсилан и (3‑аминопропил)триэтоксисилан растворяли в хлороформе для получения растворов соответствующей концентрации. Растворы готовили непосредственно перед проведением эксперимента.
Синтез олигомерных аппретирующих композиций. Получение олигомерных аппретов, включающих ТДИ, проводили в N,N‑диметилацетамиде (ДМАА). Для этого навеску ТДИ (2.2 г, 13.7 ммоль) растворяли в 110 мл ДМАА, после чего прибавляли к раствору навеску БФДА (4.4 г, 13.7 ммоль) для получения аппретирующей композиции 3 либо навеску ПМДА (3.0 г, 13.7 ммоль) для получения аппретирующей композиции 4. Перемешивали смесь до полного растворения диангидрида.
Для получения олигомерного аппрета на основе 6-FDA и 4,4'-оксидианилина (ОДА) 2.3 г диамина (11.7 ммоль) растворяли в 50 мл тетрагидрофурана (ТГФ), после чего прибавляли к смеси 5.2 г (11.7 ммоль) 6-FDA и перемешивали до полного растворения диангидрида.
Синтез полиамидокислоты на основе ПМДА/ОДА. В круглодонную трехгорлую колбу объемом 250 мл, снабженную верхнеприводной мешалкой и вводом/выводом аргона, поместили 9.57 г (47.8 ммоль) ОДА и 85 мл ДМФА. Колбу поместили в водяную баню со льдом. Перемешивали смесь в течение 20 мин при включенном токе аргона до полного растворения ОДА и охлаждения. К охлажденной смеси прибавили 10.43 г (47.8 ммоль) пиромеллитового диангидрида и выдержали смесь в течение 20 ч. Полученный раствор хранили в холодильнике и применяли для аппретирования и пропитки волокна, разбавляя перед использованием путем прибавления соответствующего количества ДМФА.
Подготовка аппретирующего раствора на основе полиимида 6-FDA/ОДА. В круглодонную четырехгорлую колбу объемом 250 мл, снабженную верхнеприводной мешалкой, обратным холодильником и вводом/выводом аргона, поместили 1.72 г (8.6 ммоль) ОДА и 65 мл м-крезола. В токе аргона перемешивали смесь до полной гомогенизации, после чего прибавили 3.8 г (8.6 ммоль) 6‑FDA, а также 1.58 г (12.9 ммоль) бензойной кислоты. Колбу с реакционной массой мутно-желтого цвета нагрели в песочной бане до 90°С и выдержали при этой температуре 4 ч (в процессе цвет смеси изменился на темно-коричневый), после чего увеличили нагрев до 190°С и выдержали еще 12 ч. После указанной выдержки и последующего охлаждения вылили смесь в стакан, содержащий 400 мл этанола. Перемешивали полученную массу при нагревании в течение 10–15 мин, затем полученный осадок отфильтровывали на фильтре Шотта. Повторяли промывку осадка до получения прозрачного фильтрата. Полученный осадок сушили в вакуумном сушильном шкафу при 80°С в течение 6 ч. Масса сухого продукта составила 4.8 г (91.7%).
Навеску полученного полиимида растворяли в необходимом количестве хлороформа непосредственно перед пропиткой.
Подготовка раствора полиэфиримида. 20 г полиэфиримида поместили в колбу и разово прибавили 80 г хлороформа. Быстро размешали до получения однородного раствора. Раствор готовили накануне или непосредственно перед проведением эксперимента.
Синтез растворов полиимидов. Синтез сополиимидов выполняли при помощи сотрудников лаборатории высокомолекулярных соединений ИНЭОС РАН им. А.Н. Несмеянова под руководством д.х.н. профессора Я.С. Выгодского.
Синтез сополиимидов 1 и 2, используемых для пропитки углеродного волокна, проводили по методике, описанной в [15]. Полученные полимеры растворяли в подходящем растворителе непосредственно перед проведением эксперимента и использовали для получения препрегов.
Аппретирование углеродного волокна. Установка для аппретирования представляла собой две последовательно расположенные ванны, разделенные отжимными валками, и двухзонную трубчатую печь. Коммерческое волокно последовательно протягивали через ванну с хлороформом для удаления заводского аппрета, затем – через ванну с аппретирующим составом, после чего волокно протягивали через трубчатую печь для высушивания растворителя. Температура сушки была выбрана, во-первых, исходя из необходимости полного удаления растворителя, во-вторых, достаточная для протекания процессов сшивки для тех аппретирующих составов, где это необходимо, например имидизации амидокислоты в имид. Температура печи составила 250 и 300°С для первой и второй зон соответственно.
Получение препрегов на основе однонаправленного углеродного волокна. Для получения препрегов предварительно аппретированное углеродное волокно последовательно протягивали через две пропиточные ванны с раствором соответствующего полимера, разделенные отжимными валками. После второй пропиточной ванны волокно пропускали через формовочную фильеру диаметром 0.4 мм и затем протягивали через трубчатую печь с двухступенчатым нагревом для высушивания.
Оборудование. Исследовали поверхность аппретированного углеродного волокна и срезов препрегов с помощью сканирующей электронной микроскопии (СЭМ) с использованием микроскопа Hitachi SU1510 (Япония).
Печать образцов композитных изделий с использованием полученных углеродных препрегов осуществляли при помощи 3D-принтерa Anisoprint Composer A4, оборудованного экструдером для печати непрерывным углеродным волокном. Температуру экструдера для печати пластиком задавали исходя из рекомендаций к используемому филаменту, для экструдера, печатающего углеродным волокном, установили температуру 230°С. В качестве пластика при печати использовали полиэтилентерефталат-гликоль (ПЭТГ).
РЕЗУЛЬТАТЫ И ИХ ОБСУЖДЕНИЕ
В ходе работы получили и протестировали аппретирующие композиции разной природы: мономеры, олигомеры и полимеры. На рис. 1 представлены структуры аппретирующих агентов, использованных при проведении исследования.
Рис. 1.
Структуры соединений, использованных в качестве аппретов: состав 1 (а), состав 2 (б), состав 3 (в), состав 4 (г), состав 6 (е). На рис. д приведена структура, соответствующая составам 5 и 7, которые различаются только длиной полимерной цепи.
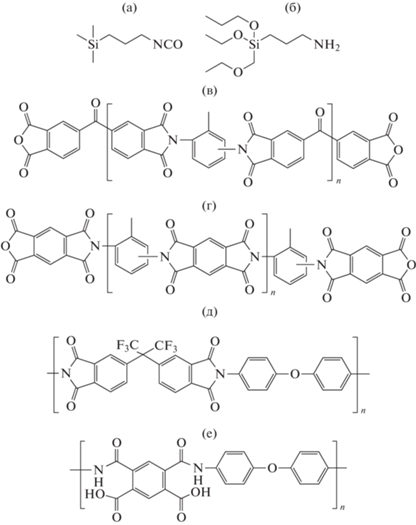
Использование в качестве мономерных аппретов растворов γ‑изоцианопропил-триметилсилана (рис. 1а) и (3‑аминопропил) триэтоксисилана (рис. 1б) обусловлено их коммерческой доступностью и низкой стоимостью, а также тем фактом, что оба соединения являются поверхностно-активными веществами, а значит, потенциально способны облегчить пропитку аппретированного волокна. Выбранные соединения в настоящее время используются, в том числе, в качестве аппретов для стекловолокна.
Состав полимерных аппретов выбирали исходя из требования к их термостойкости, в связи с чем были выбраны соединения из класса полиимидов, которые известны своими высокими термическими характеристиками. Поскольку полиимиды известны также своей плохой растворимостью, в качестве аппретирующего агента выбран полиимид (рис. 1д) на основе 6-FDA и 4,4'-оксидианилина (ОДА), потому как известно, что наличие в молекуле фторсодержащих групп увеличивает растворимость полимера в органических растворителях. Другой подход заключался в том, чтобы использовать для пропитки волокна полиамидокислоту – предшественник полиимида, который обычно получают в виде раствора и который переходит в полиимид при нагревании. Для синтеза полиамидокислоты использовали ПМДА и ОДА (рис. 1е). Полиимд на основе этих мономеров, известный под торговым названием “каптон”, обладает исключительной (до 400°С) термостойкостью.
Олигомерные аппреты использовали с целью получить менее вязкие, чем растворы полимеров, аппретирующие композиции. С другой стороны, предполагалось, что они будут иметь бóльшую термостойкость по сравнению с композициями на мономерной основе. Суть подхода заключалась в смешении мономерных составляющих в подходящем растворителе и незамедлительном нанесении полученного состава на волокно. Таким образом, реакция полимеризации проходила не полностью и не происходило образования цепочек, обладающих значительной молекулярной массой. Для проведения экспериментов был подготовлен олигомерный аппрет на основе 6‑FDA/ОДА (рис. 1д) для сравнения с его полимерным аналогом того же состава. Помимо этого, синтезированы аппреты, включающие в себя ТДИ в сочетании с диангидридами карбоновых кислот: БФДА (рис. 1в) или ПМДА (рис. 1г). ТДИ отличается высокой реакционной способностью, вследствие чего реагирует со слабоактивными ароматическими диангидридами, например П-МДА, быстрее, чем диамины.
В табл. 1 приведены составы использованных аппретирующих композиций, а также протестированные концентрации. В общем случае исходная концентрация аппретирующего состава – 5%. После проведения эксперимента состав разбавляли вдвое, за исключением состава 5, где оказалось затруднительным растворение большого количества ОДА в ТГФ, а также состава 6, который при концентрации 5% имел слишком большую вязкость для пропитки. Результаты аппретирования оценивали в первую очередь визуально: волокно должно быть достаточно мягким и гибким, чтобы образовывать петлю без заломов, но при этом не пушиться и не рваться. Фотографии волокна с недостаточным (а), избыточным (б) и оптимальным (в) количеством аппретов приведены на рис. 2. Чрезмерная жесткость волокна указывает на наличие слишком плотного слоя аппрета на поверхности, что делает невозможным его дальнейшую пропитку термопластом, недостаток аппрета приведет к пушению волокна и невозможности его использования в технологическом процессе. Кроме этого, недостаточное количество аппрета на поверхности углеродного волокна снизит адгезию между волокном и термопластом в конечном композите.
Таблица 1.
Протестированные аппретирующие композиции
Состав | Аппретирующий агент | Растворитель | Протестированные концентрации, мас. % |
---|---|---|---|
1 | γ-изоцианопропил-триметилсилан | CHCl3 | 5, 2, 1 |
2 | (3-аминопропил) триэтоксисилан | CHCl3 | 5 |
3 | БФДА + ТДИ | ДМАА | 5, 2.5, 1.25, 0.6 |
4 | ПМДА + ТДИ | ДМАА | 5, 2.5, 1.25, 0.6, 0.3 |
5 | 6-FDA + ОДА (олигомеры) | ТГФ | 4.4, 2.2, 1, 0.5, 0.25, 0.125 |
6 | ПАК: ПМДА+ОДА | ДМФА | 1.5, 1.0, 0.5, 0.25, 0.125 |
7 | 6-FDA + ОДА (полимер) | CHCl3 | 5, 2.5, 1.25, 0.75, 0.55, 0.2 |
Рис. 2.
Образцы углеродного волокна после аппретирования, с разными технологическими свойствами. Волокно с недостатком аппрета утратило свою компактность (а). Избыток аппрета делает волокно жестким и ломким (б). Достаточное количество аппрета позволяет волокну быть достаточно гибким, сохраняя компактность (в).
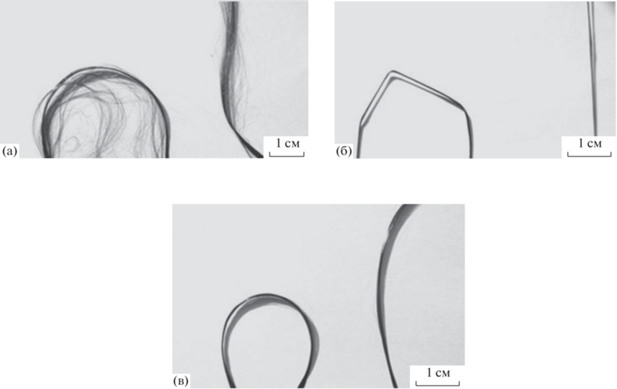
Количество аппретирующего агента на поверхности волокна контролировали также при помощи СЭМ при 1000-кратном увеличении. На рис. 3 представлены образцы с различным количеством аппрета. Во всех случаях можно разглядеть частицы аппрета на волокне, однако равномерный слой можно наблюдать только на рис. 3в, в то время как на рис. 3а можно заметить лишь “островки” аппретирующего состава, а на рис. 3б видно, что избыточное количество аппрета заставляет филаменты слипаться друг с другом.
Рис. 3.
СЭМ-изображения аппретированного волокна, полученные при 1000-кратном увеличении. Недостаток аппрета лишает волокна компактности и упорядоченности (а), при избытке аппрета (б) филаменты слипаются друг с другом. Достаточное количество аппрета (в) придает волокну необходимые технологические свойства.
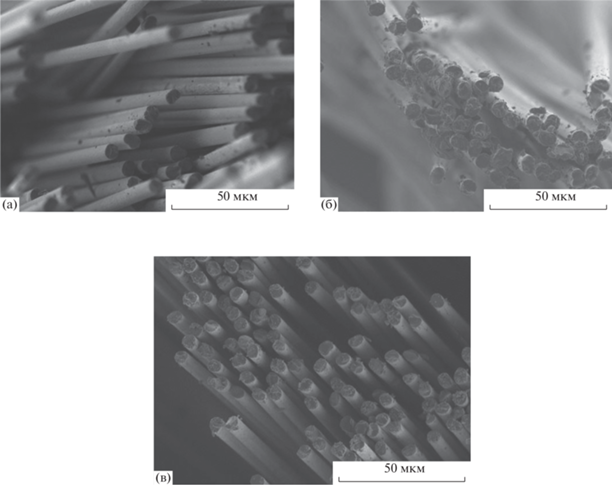
Аппретирование мономерными γ-изоцианопропил-триметилсиланом (состав 1) и (3-аминопропил) триэтоксисиланом (состав 2) не принесло положительного результата: полученное после аппретирования волокно казалось недостаточно аппретированным даже при концентрации раствора 5%. Увеличение концентрации аппретирующего агента показалось экономически и технологически нецелесообразным.
В случае составов на основе полимеров, а именно раствора полиамидокислоты (состав 6) и раствора полиимида (состав 7), даже при низких концентрациях (0.5–0.2 мас. %) аппретов волокно обладало излишней жесткостью.
Наилучшие результаты показали олигомерные аппретирующие композиции (составы 3–5), позволившие получить достаточно гибкое волокно, пригодное для дальнейших манипуляций. Рабочие концентрации растворов во всех трех случаях не превышали 1% и составили 0.6, 0.3 и 0.25% для составов 3–5 соответственно. После определения наилучших композиций и их рабочих концентраций были разработаны лабораторные образцы аппретированного волокна в количестве 50 м для каждого состава.
Следующим этапом работы стало получение препрегов на основе полученных аппретированных волокон.
Для пропитки углеродного волокна и получения термостойкого композитного препрега использовали соединения полиимидной природы, структуры которых представлены на рис. 4. Как упоминалось выше, полиимиды в целом обладают довольно низкой растворимостью, поэтому для получения растворимых соединений использовали 9,9-бис-(4'-аминофенил)флуорен – мономер, содержащий в своем составе кардовый атом углерода, так как известно, что его наличие способствует повышению растворимости и термопластичности полиимидов [16]. Сополиимид 1 (рис. 4а) был получен из указанного диамина в сочетании с диангидридом 3,3',4,4'-тетракарбоксидифенилоксида, обладающего “шарнирным” атомом, который также должен повышать растворимость конечного соединения, и 3,5-диаминобензойной кислотой. Полученный сополиимид оказался растворим в полярных апротонных высококипящих растворителях вроде ДМФА. Для придания еще большей пластичности и растворимости при синтезе сополиимида 2 (рис. 4б) 3,5‑диаминобензойную кислоту заменили гексаметилендиамином, вследствие чего полученный продукт приобрел растворимость в таких растворителях, как хлороформ и ТГФ.
Рис. 4.
Структуры полимеров, использованных для пропитки углеволокна и получения композитной нити: сополиимид 1 (а), сополиимид 2 (б), полиамидокислота на основе ПМДА/ОДА (в), полиэфиримид (г).
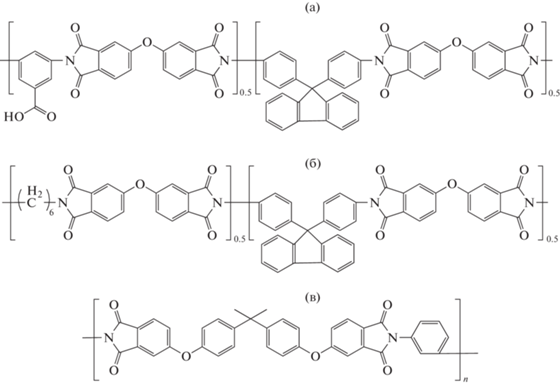
Помимо этого, для пропитки использовали раствор полиамидокислоты ПМДА/ОДА (рис. 4в), а также раствор коммерчески доступного полиэфиримида Ultem-1000 (ПЭИ) (рис. 4г).
Поскольку в соответствии с результатами СЭМ наиболее равномерное распределение аппретирующего агента наблюдалось при использовании состава 5, образцы препрегов на основе различных полимеров изготавливали на этом волокне. Для сравнения были изготовлены образцы препрега на основе волокна, аппретированного составами 3 и 4, и полиэфиримида в качестве полимерного связующего. Характеристики всех изготовленных образцов препрегов приведены в табл. 2.
Таблица 2.
Изготовленные образцы препрегов
Образец | Аппретирующий состав | Полимерное связующее, (концентрация, мас. %) растворитель | Температура, °С зона 1/зона 2 |
---|---|---|---|
I | 5 | Сополиимид 1 (17.5%) НМП | 170/300 |
II | Сополиимид 2 (20%) СНСl3 | 300/370 | |
III | ПМДА/ОДА (13%) ДМФА | 300/370 | |
IV | ПЭИ (20%) СНСl3 | 300/370 | |
V | 4 | ||
VI | 3 |
Полученные препреги оценивали визуально и при помощи микрофотографий среза волокна, выполненных методом СЭМ. На рис. 5 приведены снимки срезов волокна, полученные при 200-кратном увеличении. Видно, что все препреги содержат внутри полости различного размера. Среди препрегов, полученных из волокна, аппретированного составом 5, наиболее равномерно пропитанными оказались образцы на основе полиамидокислоты (ПАК) и ПЭИ (рис. 5в, 5г): образец III, пропитанный ПАК (рис. 5в), имеет небольшие отверстия, а образец IV, пропитанный ПЭИ (рис. 5г), практически не имеет полостей. Оба препрега имеют гладкую однородную поверхность и высокую гибкость. Образец волокна II, пропитанный сополиимидом 2 (рис. 5б), имеет небольшую полость по центру, однако он оказался механически хрупким, что делает его непригодным для использования в 3D-печати, так как волокно не выдержит подачи в экструдер. Препрег I на основе сополиимида 1 (рис. 5а) имеет множество полостей, а также кусочки полимера, застывшие на поверхности. Отметим, что связующие в образцах препрегов I, II, III имеют одинаковую (полиимидную) природу, однако в случае образцов I, II пропитка ведется непосредственно раствором полиимида, в то время как образец III получают, пропитывая волокно раствором прекурсора полиимида – полиамидокислоты, которая имеет меньшую вязкость и, следовательно, способна лучше проникать между филаментами. На стадии сушки происходит термическая имидизация ПАК с образованием полиимида.
Рис. 5.
Снимки срезов композитной нити на основе различных аппретов и пропиточных растворов. Волокно, аппретированное составом 6-FDA/ОДА и пропитанное сополиимидом 1 (а), сополиимилом 2 (б), полиамидокислотой П-МДА/ОДА (в) и полиэфиримидом (г). Волокно с аппретом БФДА/ТДИ (д) и с аппретом ПМДА/ТДИ (е), пропитанное ПЭИ.
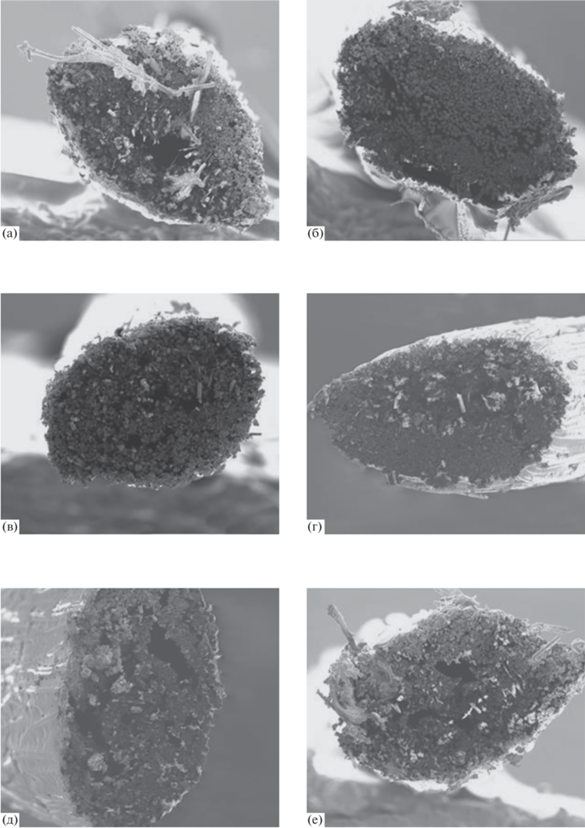
Препреги V, VI, полученные из волокна, аппретированного составами 3 и 4 (рис. 5д, 5е), также продемонстрировали плохую пропитанность связующим. Хотя препрег V на основе состава 3 (рис. 5д) выглядит более аккуратным и содержит полости меньшего размера, он расслаивается на срезе так же, как образец VI, полученный из волокна, аппретированного составом 4 (рис. 5е). При разрезе вдоль в центре наблюдается большое количество непропитанного углеволокна.
Таким образом, по результатам эксперимента по пропитке было отобрано два связующих для получения лабораторных образцов. Для тестирования на 3D-принтере получено по 10 м препрегов III и IV. Печать тестовых образцов выполнялась без осложнений, в полученных изделиях композитное волокно было выложено в соответствии с заданной формой и сцеплено с пластиком.
Образцы изделий, напечатанных с использованием подготовленных препрегов, показаны на рис. 6. Рисунок 6а демонстрирует изделие, изготовленное на основе препрега IV, рис. 6б – на основе препрега III. Видно, что в обоих случаях присутствуют нарушения при выкладке препрега. Для образца IV в некоторых местах препрег не прикрепился к пластику, что вероятнее всего связано с низкой адгезией между ПЭИ и ПЭТГ. В образце III наблюдаются изломы препрега при выкладке частей с малым радиусом. Хотя полного разлома композитного волокна не произошло, даже частичный разлом может в итоге привести к снижению прочности конечного композитного изделия.
ВЫВОДЫ
Проведенные исследования по аппретированию и пропитке углеродного волокна различными составами показали, что наилучшим вариантом аппретирующей композиции является раствор олигомеров имидной природы. Такие композиции позволяют получать углеродное волокно с надлежащими технологическими характеристиками: достаточно мягкое, но при этом не теряющее своей компактности (без пушения). Среди протестированных олигомерных аппретов наиболее впечатляющие результаты показала композиция на основе 6-FDA/ОДА, однако в силу высокой стоимости фторированного диангидрида кажется целесообразным продолжить изучение свойств олигомерных композиций состава БФДА/ТДИ и ПМДА/ТДИ и изучить возможность их дальнейшей модификации для улучшения свойств аппретированного волокна.
Пропитка углеродного волокна полимерными связующими позволила получить два образца композитного волокна, пригодного для тестовой печати: волокно, пропитанное раствором полиэфиримида, и волокно, пропитанное раствором ПАК, с последующей термической имидизацией. В обоих случаях при печати наблюдались видимые дефекты, что свидетельствует о необходимости дальнейших модификаций, однако можно с уверенностью сказать, что такие составы являются перспективными для получения композитного углеродного волокна для 3D-печати.
Авторы выражают благодарность коллективу лаборатории высокомолекулярных соединений ИНЭОС РАН им. А.Н. Несмеянова под руководством д.х.н. профессора Я.С. Выгодского за помощь в проведении синтетических работ по получению сополиимидов с кардовым атомом углерода.
Работа выполнена при поддержке НИЦ “Курчатовский институт”. Аналитические исследования выполнены с использованием научного оборудования ЦКП НИЦ «Курчатовский институт» – ИРЕА при финансовой поддержке Министерства науки и высшего образования РФ (соглашение № 075-15-2022-1157 от 16.08.2022).
Список литературы
Beaumont P.W.R., Soutis C., Hodzic A. The structural integrity of carbon fiber composites: fifty years of progress and achievement of the science, development, and applications. Springer. 2016. 969 p. https://doi.org/10.1007/978-3-319-46120-5
Tang S., Hu C. // J. Mater. Sci. Technol. 2017. V. 33. № 2. P. 117. https://doi.org/10.1016/j.jmst.2016.08.004
Das T.K., Ghosh P., Das N.Ch. // Adv. Compos. Hybrid. Mater. 2019. V. 2. P. 214. https://doi.org/10.1007/s42114-018-0072-z
Forintos N., Czigany T. // Composites. B. 2019. V. 162. P. 331. https://doi.org/10.1016/j.compositesb.2018.10.098
Goh G.D., Dikshit V., Nagalingam A.P. et al. // Mater. Des. 2018. V. 137. P. 79. https://doi.org/10.1016/j.matdes.2017.10.021
Parandoush P., Zhou C., Lin D. // Adv. Eng. Mater. 2019. V. 21. № 2. P. 1800622. https://doi.org/10.1002/adem.201800622
Wu G.M., Schultz J.M. // Polym. Compos. 2000. V. 21. № 2. P. 223. https://doi.org/10.1002/pc.10179
Che D., Saxena I., Han P. et al. // J. Manuf. Sci. Eng. 2014. V. 136. № 3. P. 034001. https://doi.org/10.1115/1.4026526
Brenken B., Barocio E., Favaloro A. et al. // Additive Manufacturing. 2018. V. 21. P. 1.
Dilsiz N., Wightman J.P. // Carbon. 1999. V. 37. P. 1105. https://doi.org/10.1016/S0008-6223(98)00300-5
Vaidya U.K., Chawla K.K. // Int. Mater. Rev. 2008. V. 53. P. 185. https://doi.org/10.1179/174328008X325223
Ramanathan T., Schulz E., Subramanian K. // Compos. Sci. Technol. 2005. V. 65. P. 1. https://doi.org/10.1016/j.compscitech.2004.04.007
Saleem A., Frormann L., Iqbal A. // Polym. Compos. 2007. V. 28. P. 785. https://doi.org/10.1002/pc.20297
Харьков С.Н., Гречушникова Л.П., Чеголя А.С. и др. // Высокомол. соединения. А. 1972. Т. XIV. № 4. С. 817.
Vinogradova S.V., Vasnev V.A., Vygodskii Y.S. // Russ. Chem. Revs. 1996. V. 65. № 3. P. 249. https://doi.org/10.1070/RC1996v065n03ABEH000209
Кузнецов А.А., Акименко С.Н., Цегельская А.Ю. и др. // Высокомол. соединения. Б. 2014. Т. 56. № 1. С. 45.
Дополнительные материалы отсутствуют.
Инструменты
Вестник Военного инновационного технополиса «ЭРА»