Высокомолекулярные соединения (серия Б), 2019, T. 61, № 4, стр. 252-256
Получение микрочастиц полистирола с использованием метода неизотермической полимеризации в среде сверхкритического диоксида углерода
А. Ю. Костин a, *, В. И. Торбов a, Е. Н. Шатунова a
a Институт проблем химической физики Российской академии наук
142432 Московская обл., Черноголовка, пр. ак. Семёнова, 1, Россия
* E-mail: akostin@icp.ac.ru
Поступила в редакцию 24.12.2018
После доработки 21.03.2019
Принята к публикации 04.04.2019
Аннотация
Исследован процесс получения и микронизации полимерных материалов с использованием оригинального метода неизотермической полимеризации в среде сверхкритического флюида. Синтезированы микрочастицы и волокна полистирола. Оценено влияние условий проведения процесса микродиспергирования на морфологию выделяемого продукта.
ВВЕДЕНИЕ
Разработка новых высокоэффективных методов получения микродисперсных полимерных порошков и функциональных материалов на их основе представляет значительный интерес. Они применяются при производстве лакокрасочных покрытий, строительных материалов, адсорбентов, носителей катализаторов и т.д. Перспективным направлением является разработка систем адресной доставки и контролируемого высвобождения лекарственных препаратов на основе полимерных микрочастиц [1].
Традиционные методы микродиспергирования полимерных материалов, как правило, основаны на механическом измельчении, использовании растворителей, дисперсных сред, либо переработке полимера в расплаве. Среди недостатков механических методов можно выделить значительную полидисперсность, неоднородную морфологию и загрязнение порошков примесью материала дробящих тел, а также механодеструкцию полимера; порошки, синтезированные из растворов и дисперсий, требуют тщательной очистки от следов растворителей, эмульгаторов и других вспомогательных веществ, а получение из расплавов затруднено значительной вязкостью и процессами термодеструкции полимера. Область применения материала также может накладывать дополнительные ограничения. Так, например, при производстве лекарственных препаратов предъявляются повышенные требования к содержанию посторонних примесей и вредных веществ в полимере, а многие биологические и фармацевтические субстанции, выступающие в роли наполнителей, чувствительны к действию повышенной температуры и агрессивной среды.
Одним из путей решения этой проблемы может быть использование сверхкритических флюидов. Уникальные свойства их в качестве растворителя уже на протяжении достаточно долгого времени привлекают широкий круг исследователей и разработчиков, заинтересованных в модернизации существующих и создании новых технологических процессов в самых разных областях науки и промышленности [2, 3]. В зависимости от требований к физико-химическим свойствам сверхкритических флюидов растворителя применяются органические и неорганические соединения как жидкие, так и газообразные (при нормальных условиях). Наиболее используемым считается диоксид углерода CO2, поскольку он легко доступен, обладает приемлемыми с технологической точки зрения параметрами перехода в сверхкритическое состояние (Тск ∼ 31°С, Рск ∼ 73 бар), не горюч и не токсичен, при нормальных условиях является газом, благодаря чему легко удаляется из готового продукта.
Особенностью полимерного синтеза в СО2 можно назвать ограниченную растворимость в нем большинства наиболее крупнотоннажных и востребованных в промышленности полимеров; практически только фтор- и силоксановые полимеры обладают достаточной растворимостью для проведения гомогенной полимеризации. В связи с этим, работы, направленные на изучение процессов полимеризации и получения полимерных микрочастиц с использованием сверхкритического СО2, в подавляющем большинстве посвящены процессам гетерогенной полимеризации (дисперсионной, эмульсионной, суспензионной) [4–6].
Как было отмечено выше, данные процессы требуют использования поверхностно-активных веществ для стабилизации дисперсной фазы в реакционной среде, а также в случае эмульсионной полимеризации, дополнительного растворителя, например воды или метанола. Существенной проблемой здесь можно назвать несовместимость применяемых в полимерном синтезе в традиционных растворителях поверхностно-активных веществ с СО2 и необходимость использования специальных, как правило, фторсодержащих либо силоксановых ПАВ [4]. Получаемый этими методами полимер требует дополнительных стадий очистки от загрязнений подобного типа, при этом ПАВ, имеющие углеводородные цепочки, способны отщеплять водород в ходе радикальной полимеризации, что может повлечь ковалентное связывание с полимером, либо при наличии длинной СО2-фобной части механически запутываться в полимерных клубках, затрудняя полную очистку конечного продукта (или делая ее невозможной).
В связи с очевидными затруднениями, попыткам получения не содержащих фтор и кремний полимеров в среде сверхкритического СО2 без применения ПАВ посвящено крайне ограниченное число работ. Среди применяемых методов можно отметить, в частности, дисперсионную полимеризацию стирола и метилметакрилата под действием ультразвука [7], а также получение сополимера стирола с метилметакрилатом в массе с насыщением смеси СО2 в пределах его растворимости в полимере (до 20 мас. %) [8].
Рассматриваемый в данной работе подход к получению полимера высокой степени чистоты за счет изначального отказа от использования вспомогательных веществ, загрязняющих конечный продукт, основан на проведении полимеризации до небольших степеней превращения со сбором СО2 и остаточного мономера в конце процесса и их рекуперацией для повторного использования в цикле. В этом случае мономер выступает в роли сорастворителя и предотвращает выпадение полимера в отдельную фазу.
Развиваемый авторами оригинальный метод неизотермической полимеризации [9] позволяет проводить весь процесс – от исходного мономера до конечного продукта – в единой герметичной технологической цепи. В отличие от традиционных технологий полимеризации (в суспензии, в эмульсии, в растворе) метод не предполагает использования значительного количества воды или органических растворителей в качестве реакционной среды, сам же процесс полимеризации протекает в автотермическом тепловом режиме с применением собственного тепловыделения реакции, позволяя тем самым уменьшить затраты энергии на очистку и утилизацию отходов производства, а также на поддержание теплового режима процесса.
Технологическая схема процесса дает возможность реализовать введение в исходную реакционную смесь диоксида углерода с целью полимеризации в среде сверхкритического CO2. При этом снижается вязкость смеси и уменьшается удельное тепловыделение в результате протекания реакции полимеризации, позволяя вести процесс в более “жестких” условиях [10] с сохранением контроля над ним. Переходящий в газовую фазу при сбросе давления на выходе из реактора CO2 также увлекает за собой растворимый в нем остаточный мономер [11]; затем они могут быть возвращены обратно в цикл, позволяя тем самым создать малоотходное производство. Одновременно, в зависимости от условий проведения процесса, таких как давление перед диспергирующим устройством, температура смеси, концентрация компонентов (полимер, мономер, СО2), возможно вспенивание или диспергирование образуемого полимера с получением пенопластов, пленок, волокон и микрочастиц различной морфологии.
Цель настоящей работы − изучение влияния давления и концентрации полимера в реакционной смеси на морфологию частиц, получаемых при ее дросселировании через капилляр, расположенный на выходе из реактора.
ЭКСПЕРИМЕНТАЛЬНАЯ ЧАСТЬ
Экспериментальные исследования проводили на лабораторной установке, принципиальная схема которой приведена на рис. 1. Установка включает в себя плунжерные насосы высокого давления, сосуд-смеситель, а также трубчатый реактор неизотермической полимеризации оригинальной конструкции, описанный в работе [9], и диспергирующее устройство. Лабораторная установка не оснащена предусмотренными полной технологической схемой системами рекуперации и повторного использования СО2 и остаточного мономера.
Рис. 1.
Принципиальная схема лабораторной установки неизотермической полимеризации в среде сверхкритического CO2: 1 – баллон с CO2, 2 – расходомер, 3 – емкость с мономером, 4 – теплообменник, 5 – криостат, 6 и 7 – насосы высокого давления, 8 – смеситель, 9 – термостат, 10 и 12 – вакуумный насос, 11 – трубчатый реактор, 13 – криогенная ловушка, 14 – фильтр, 15 – диспергирующее устройство, 16 – распылительная камера.
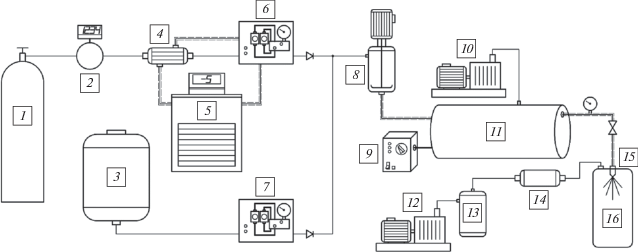
Порядок проведения экспериментов на лабораторной установке следующий: диоксид углерода в жидком состоянии из баллона (1), а также исходный мономер стирола из емкости (3) при помощи плунжерных насосов (6) и (7) подаются в смеситель (8), из которого с заданным расходом под давлением поступают в трубчатый реактор неизотермической полимеризации (11). Реактор представляет собой длинную трубку из нержавеющей стали, свитую в спираль и помещенную с воздушным зазором в теплообменник, температура которого поддерживается постоянной. Реактор с теплообменником помещены в вакуумируемый теплоизолирующий кожух. По длине трубки, на ее наружной поверхности, закреплены термопары для регистрации реакционных разогревов и распределения температуры по длине реактора. В реакторе протекает экзотермический процесс превращения мономера в полимер в неизотермическом тепловом режиме в условиях, соответствующих сверхкритическому состоянию диоксида углерода (T > 31°C, P > 73 бар).
Из реактора смесь форполимера и CO2 поступает в диспергирующее устройство (15), представляющее собой обогреваемый вентиль тонкой регулировки с набором сменных капилляров различного диаметра и длины. В выходящей из диспергирующего устройства со сверхзвуковой скоростью струе реагента возникает ударная волна, в которой происходит образование микрочастиц полимера. При этом переходящий в газовую фазу CO2 “уносит с собой” остаточный мономер и другие растворимые примеси.
РЕЗУЛЬТАТЫ И ИХ ОБСУЖДЕНИЕ
За основу при получении микрочастиц взяли полистирол как модельный полимер с хорошо изученной макрокинетикой неизотермической полимеризации [9, 12]. Мономер стирола квалификации ч. (ТУ 6-09-11- 2034-87) перед проведением опытов очищали от стабилизатора и других примесей двукратной перегонкой под вакуумом. В качестве сверхкритического флюида использовали диоксид углерода высшего сорта по ГОСТ 8050-85 (чистота > 99.8%). В ходе эксперимента осуществляли термическую полимеризацию стирола в трубчатом реакторе при температуре теплообменника 180 ± 5°С. Начальная концентрация мономера в СО2 во всех опытах 25% по объему, конечную конверсию определяли путем численного расчета на основе модели, описанной в работе [10], исходя из времени пребывания смеси в реакторе и в различных экспериментах, она составляла от 5 до 40%. Нижняя граница указанного диапазона была обусловлена чрезмерным снижением производительности процесса, в то время как верхняя – преимущественным образованием полимерных волокон вместо микрочастиц. Давление в реакторе в процессе диспергирования поддерживали постоянным в пределах ±5%, в различных экспериментах оно составляло от 75 до 250 бар. В качестве выходного капилляра использовали тонкостенную трубку из нержавеющей стали длиной 3 см и внутренним диаметром 0.3 мм.
Образцы полимерных частиц для последующего изучения готовили путем напыления частиц на поверхность пластинок из алюминия, вносимых в поток на выходе из капилляра на определенном расстоянии от его среза. Далее на пластинки напыляли проводящий слой углерода, после чего частицы на их поверхности фотографировали при помощи сканирующего автоэмиссионного электронного микроскопа с катодом Шоттки “Zeiss SUPRA-25”.
Анализ фотографий продуктов микродиспергирования, полученных при варьировании температуры теплообменника трубчатого реактора и давления перед распыляющим устройством, демонстрирует сильную зависимость их морфологии от указанных параметров.
В рассмотренных условиях проведения процесса (при давлении в диапазоне от 90 до 150 бар и концентрации полимера в диспергируемой смеси менее 6%) образуются микрочастицы правильной сферической формы диаметром 0.5–5.0 мкм (рис. 2а).
Рис. 2.
Микрофотографии продуктов диспергирования: а – микрочастицы, давление в реакторе Р = 130 бар, расчетное содержание полимера в смеси C = 5%; б – микрочастицы, P = 220 бар, C = 5%; в – микрочастицы и волокна, P = 200 бар, C = 8%; г – образования неправильной формы, P = 80 бар, C = 6%.
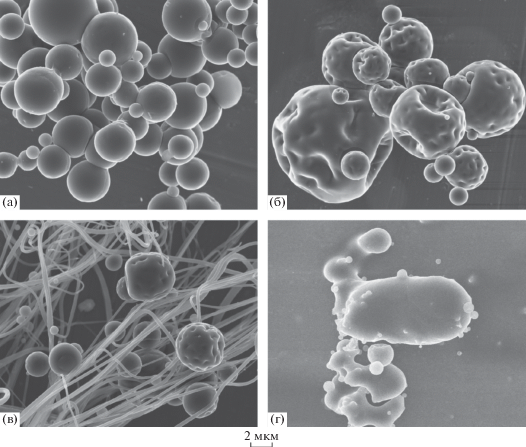
Повышение давления свыше 150 бар вызывает формирование характерной деформации в виде нерегулярных углублений на поверхности частиц при сохранении ими в целом сферической формы (рис. 2б). Данное явление можно объяснить образованием внутренней пористости в полимерных частицах при резком сбросе давления в результате перехода растворенного в полимере диоксида углерода в газовую фазу в условиях, когда скорости переноса CO2 диффузией из глубины частицы наружу становится недостаточно, и начинается формирование полостей, заполненных газом, внутри самой частицы. При дальнейшем охлаж-дении частицы в потоке адиабатически расширяющегося газа давление в порах падает, в результате чего тонкие стенки расположенных возле поверхности частицы пор втягиваются внутрь, образуя углубления на ее наружной поверхности. При этом необходимо отметить, что на частицах наблюдаются исключительно закрытые поры. Это указывает на образование пор, начиная только с определенной глубины внутри частицы, что служит подтверждением рассмотренного механизма их формирования.
При концентрации полимера в диспергируемой смеси выше 6% по объему (расчетная конверсия 24%) совместно с микрочастицами формируются полимерные волокна диаметром 0.1–0.5 мкм с нерегулярной структурой (рис. 2в). При концентрации свыше 10% (расчетная конверсия 40%) образуются преимущественно волокна.
При значениях давления ниже 80–90 бар частицы оседают на подложку в виде образований неправильной формы (рис. 2г). Причиной этому является снижение массовой доли СО2 в смеси в силу уменьшения его плотности со снижением давления, что, в свою очередь, приводит к уменьшению количества мономера, экстрагируемого СО2 при сбросе давления. В указанном диапазоне давления остаточного мономера становится достаточно для пластификации частиц, которые в ходе движения в потоке газа и при соударениях с подложкой теряют сферическую форму и сливаются вместе.
ЗАКЛЮЧЕНИЕ
В результате проведенных исследований показана принципиальная возможность создания технологии получения полимерных микрочастиц методом неизотермической полимеризации в среде сверхкритического флюида без применения поверхностно-активных веществ и сорастворителей, за исключением собственного мономера. Были получены микрочастицы и волокна полистирола и оценено влияние давления в реакторе и конверсии мономера на их морфологию.
Работа выполнена в рамках Программы фундаментальных научных исследований государственных академий наук на 2013–2020 гг. (шифр темы 0089-2014-0032) с использованием оборудования Центра коллективного пользования “Новые нефтехимические процессы, полимерные композиты и адгезивы” (№ 77601) и Аналитического центра коллективного пользования Института проблем химической физики РАН (№ 40607).
Список литературы
Andrew Choi, Kyoung Duck Seo, Do Wan Kim, Bum Chang Kim, Dong Sung Kim // Lab on a Chip. 2017. V. 17. P. 591.
Залепугин Д.Ю., Тилькунова Н.А., Чернышова И.В., Поляков В.С. // Сверхкритические флюиды: Теория и практика. 2006. Т. 1. № 1. С. 3.
Edward Ramsey, Qiubai Sun, Zhiqiang Zhang, Chongmin Zhang, Wei Gou // J. Environ. Sci. 2009. V. 21. № 6. P. 720.
Cédric Boyère, Christine Jérôme, Antoine Debuigne // Eur. Polym. J. 2014. V. 61. P. 45.
Colin D. Wood, Andrew I. Cooper, Joseph M. DeSimone // Curr. Opin. Solid State Mater. Sci. 2004. V. 8. № 5. P. 325.
Andrew I. Cooper // J. Mater. Chem. 2000. V. 10. P. 207.
Ruolei Wang, Michael H. // J. Supercrit. Fluids. 2005. V. 33. № 3. P. 269.
Sabine Beuermann, Michael Buback, Moritz Gadermann, Michael Jürgens, Durga Prasad Saggu // J. Supercrit. Fluids. 2006. V. 39. № 2. P. 246.
Butakov A.A., Shatunova E.N., Kostin A.Y. // Theor. Found. Chem. Eng. 2012. V. 46. P. 172.
Butakov A.A., Kostin A.Y., Shatunova E.N. // Russ. J. Phys. Chem. B. 2011. V. 5. P. 1155.
Alsoy S., Duda J.L. // Proc. Polym. Supercrit. Fluids., Chem. Eng. Technol. 1999. V. 22. № 11. P. 971.
Kuzub L.I., Peregudov N.I., Irzhak V.I. // Polymer Science A. 2005. V. 47. № 10. P. 1063.
Дополнительные материалы отсутствуют.
Инструменты
Высокомолекулярные соединения (серия Б)