Высокомолекулярные соединения (серия Б), 2022, T. 64, № 2, стр. 124-138
Затравочная полимеризация стирола с обратимой передачей цепи для синтеза устойчивых дисперсий амфифильных блок-сополимеров и композиционных наночастиц
Н. С. Серхачева a, *, К. А. Рыжиков a, Н. И. Прокопов a, А. В. Плуталова b, А. В. Большакова b, Е. В. Черникова b
a МИРЭА – Российский технологический университет
Институт тонких химических технологий имени М.В. Ломоносова
119571 Москва, пр. Вернадского, 86, Россия
b Московский государственный университет имени М.В. Ломоносова. Химический факультет
119991 Москва, Ленинские горы, 1, стр. 3, Россия
* E-mail: natalia-serkhacheva@yandex.ru
Поступила в редакцию 23.12.2021
После доработки 14.01.2022
Принята к публикации 24.01.2022
- EDN: VQDZAF
- DOI: 10.31857/S2308113922020085
Аннотация
Впервые исследованы закономерности затравочной полимеризации стирола в водно-спиртовой среде, где в качестве затравочных частиц использованы частицы триблок-сополимера акриловой кислоты и бутилакрилата, содержащего тритиокарбонатную группу внутри цепи и выполняющего функцию агента обратимой передачи цепи. Изучено влияние состава дисперсионной среды и концентрации компонентов на кинетику полимеризации, молекулярно-массовые характеристики продуктов реакции и на распределение образующихся частиц по размерам. Была осуществлена иммобилизация наночастиц TiO2 на полимерные частицы блок-сополимеров в ходе затравочной полимеризации стирола. Получены устойчивые суспензии гибридных частиц со средним диаметром от 60 до 130 нм, содержащих TiO2 и блок-сополимер акриловой кислоты, бутилакрилата и стирола.
ВВЕДЕНИЕ
В последние десятилетия развитие полимерной науки в области макромолекулярного дизайна и синтеза макромолекул сложной архитектуры послужило толчком к созданию совершенно новых гибридных полимерных материалов. Среди таких объектов особое распространение получили нанокомпозиционные частицы, роль полимерной матрицы в которых выполняют частицы амфифильных блок-сополимеров, а роль наполнителя – неорганические наночастицы различной природы и морфологии [1]. Дисперсии гибридных частиц амфифильных блок-сополимеров широко востребованы в различных областях и в зависимости от набора свойств полимерных блоков и неорганического наполнителя могут применяться, например, в катализе, для создания нанореакторов, наноконтейнеров доставки биологически активных и лекарственных веществ и т.д. [2–7].
В последние годы для получения дисперсий частиц амфифильных блок-сополимеров все чаще стали использовать полимеризацию с обратимой деактивацией цепи. Из всех известных способов ее реализации наибольшее распространение получила полимеризация с обратимой передачей цепи по механизму присоединения–фрагментации (ОПЦ), так как она применима к широкому кругу мономеров, не имеет ограничений по температурному режиму, не предполагает применения каталитических систем, загрязняющих конечный продукт, не требует сложного аппаратурного оформления, реализуется как в гомогенных, так и в гетерогенных условиях [8–11]. В последнем случае ОПЦ-полимеризацию проводят в гетерофазных системах, что позволяет не только синтезировать дисперсии уже готовых структурированных частиц блок-сополимеров с относительно высокой концентрацией полимера (10–30 мас. %), но и регулировать в процессе полимеризации длину блоков, а, следовательно, и морфологию будущих амфифильных частиц. Полученные таким образом частицы блок-сополимеров, как правило, сохраняют не только свою устойчивость во времени, но и способность к ОПЦ-механизму в дальнейшей полимеризации [12].
Для иммобилизации неорганических наночастиц на полимерный носитель существует несколько подходов. Первый вариант основан на предварительной модификации поверхности неорганического наполнителя ОПЦ-агентом и проведении дальнейшей полимеризации, что позволяет осуществить прививку полимерных цепей на поверхности неорганической частицы за счет химической реакции между функциональными группами [13]. Закрепление ОПЦ-агента на поверхности может быть выполнено через Z-группу (стабилизирующую) или R-группу (уходящую), однако в большинстве исследований был выбран вариант через R-группы, который приводит к сценарию, более похожему на “прививку от” [14]. Механизм прикрепления через Z-группы к поверхности наночастиц аналогичен подходу “прививка к”. При использовании этого подхода количество полимерных цепей, которые можно привить к поверхности, обычно невелико, так как свободный объем, занимаемый каждой привитой полимерной цепью, действует как барьер для прикрепления последующих цепей. Следовательно, прививка становится все более трудной по мере добавления большего количества цепей на поверхность, ограничивая контроль молекулярной массы и дисперсности полимерных цепей [15]. Кроме того, использование подхода “прививка от” с инициаторами, изначально закрепленными на поверхности, позволяет повысить плотность прививки и лучше контролировать молекулярную массу и дисперсность полимеров, поскольку молекулы мономера могут легко диффундировать на поверхность частиц. Прививка полимерных цепей позволяет решить одну из самых больших проблем применения наноразмерных материалов. Из-за чрезвычайно большого соотношения площади поверхности/размера частиц наночастицы имеют тенденцию к сильной агрегации, что приводит к снижению их свойств в нанокомпозите [16]. Привитые полимерные цепи разделяют и соединяют наночастицы, переплетаются с полимерной матрицей, что позволяет свести к минимуму агломерацию наночастиц и усилить взаимодействие наполнителя с матрицей [15, 17]. Сложность получения индивидуальных частиц и обеспечения равномерной плотности привитых цепей на поверхности наполнителя являются основными недостатками такого способа.
Второй вариант предполагает проведение гетерофазной ОПЦ-полимеризации, где в качестве мономерной фазы будет использована устойчивая дисперсия неорганических наночастиц в мономере. В основе этого процесса лежит способность амфифильных блок-сополимеров к самосборке в процессе полимеризации, которая приводит к возникновению нового типа формирования полимерных частиц путем самоорганизации, вызванной полимеризацией, в зарубежной литературе получившей название PISA – polymerization induced self-assembly [18–25]. В данном случае в качестве ОПЦ-агента используют полимерный прекурсор и проводят полимеризацию “чужого мономера”. Причем дисперсионную среду выбирают таким образом, чтобы она являлась термодинамически хорошим растворителем для полимерного прекурсора и плохим для “растущего” блока [26–28]. При применении несимметричного ОПЦ-агента следует ожидать формирование диблок-сополимера АВ, что уже хорошо изучено и позволяет предположить морфологию будущих частиц [29–31]. Если в качестве прекурсора использовать симметричный ОПЦ-агент, то, вероятнее всего, будут образовываться частицы триблок-сополимера типа ABA, которые являются более сложными и могут иметь дополнительные потенциальные преимущества, например более низкую критическую концентрацию мицеллобразования или более высокую стабильность по сравнению с аналогичными частицами диблок-сополимеров [32–34].
Наличие неорганических наночастиц на этой стадии может внести серьезные изменения в механизм формирования частиц. Во-первых, сложно создать условия, при которых в процессе самоорганизации будет обеспечено попадание наночастиц в полимерную частицу. Во-вторых, существует вероятность того, что полимеризация пройдет в микрокаплях, содержащих наполнитель, при этом полимерный ОПЦ-агент будет выполнять лишь роль стабилизатора полимерно-мономерных частиц. Кроме того, можно будет наблюдать еще один отрицательный эффект, который за счет возникновения диффузионных затруднений при попадании мономера или олигорадикалов со стороны наночастиц может привести не только к уменьшению скорости полимеризации и потере устойчивости частиц, но и к нарушению ОПЦ-механизма или даже к полному ингибированию реакции.
Альтернативой данному методу стал другой вариант гетерофазной полимеризации – затравочная ОПЦ-полимеризация. Такую реакцию осуществляют в две стадии, на первой стадии дисперсионной (или эмульсионной) ОПЦ-полимеризацией получают затравочные частицы, представляющие собой водные, водно-органические или органические дисперсии частиц амфифильных блок-сополимеров. На второй стадии проводят затравочную полимеризацию гидрофобного или гидрофильного мономера. Как правило, в случае полимеризации гидрофобного мономера он встраивается в ядро частицы, а при полимеризации гидрофильного мономера в зависимости от длины растущего блока могут происходить морфологические переходы с обращением фаз. Для осуществления реакции с целью иммобилизации неорганических наночастиц проводят затравочную полимеризацию мономерной фазы с равномерно диспергированными в объеме наночастицами. Такой подход обеспечит не только сохранение морфологии исходных затравочных частиц, но и локализацию наночастиц на их поверхности, что в свою очередь будет уменьшать вероятность агрегации наночастиц, способствовать сохранению их уникальных свойств и приведет к увеличению устойчивости конечной полимерной суспензии. Также это позволит с большей вероятностью провести полимеризацию согласно закономерностям ОПЦ-механизма, т.е. с обеспечением контроля молекулярно-массовых характеристик.
Цель настоящей работы – изучение иммобилизации наночастиц диоксида титана затравочной полимеризацией стирола с обратимой передачей цепи в присутствии частиц триблок-сополимера акриловой кислоты (АК) и н-бутилакрилата (БА) с морфологией “ядро–оболочка”. Наночастицы TiO2, известные химической и термической стабильностью, фотокаталитическими, сорбционными, антимикробными свойствами, часто используют для создания гибридных полимерных материалов. Разнообразие свойств наноразмерного TiO2 дает возможность получать материалы, востребованные в самых разных областях техники и технологии, например фильтрующие материалы, материалы для электронной техники или для биомедицины.
Чтобы использовать частицы амфифильных блок-сополимеров в качестве затравочных, они должны отвечать определенным требованиям: быть унимодальными, иметь узкое распределение частиц по размерам, определенную морфологию. Надо отметить, что в большинстве литературных источников для этой цели служат частицы диблок-сополимера, что в свою очередь на стадии затравочной полимеризации приводит к формированию триблок-сополимера [35–38]. Публикаций с использованием частиц триблок-сополимеров для получения гибридных частиц крайне мало. В связи с этим, основываясь на наших ранее проведенных исследованиях [39], в настоящей работе в качестве затравочных частиц мы выбрали частицы триблок-сополимера АК и БА с морфологией ядро–оболочка, полученные гетерофазной полимеризацией БА под действием полиакриловой кислоты с тритиокарбонатной группой внутри цепи в смеси метанола и воды. При сохранении ОПЦ-механизма симметричное строение полимерного прекурсора позволит получить новые гибридные частицы, не описанные ранее.
ЭКСПЕРИМЕНТАЛЬНАЯ ЧАСТЬ
Мономеры – АК, БА, стирол (99%, фирмы “Aldrich”) перед применением перегоняли под вакуумом. Инициатор ДАК перекристаллизовывали из метанола. Растворители очищали по стандартным методикам. ОПЦ-агент – дибензилтритиокарбонат (БТК) синтезировали как описано ранее и охарактеризовывали методом ЯМР [40]. Наночастицы диоксида титана модификации “анатаз” со средним диаметром менее 25 нм (99.7%, фирмы “Aldrich”) и стабилизатор моноолеат сорбитана, Span-80 (фирмы “Aldrich”) использовали без дополнительной очистки.
Для приготовления суспензии TiO2 в стироле к навеске TiO2 (1–15 мас. %) добавляли раствор Span-80 (1 мас. %) в стироле и оставляли при постоянном перемешивании на 30–60 мин. Для повышения диспергирования стеклянный стакан с приготовленной суспензией помещали в емкость с холодной водой/льдом и обрабатывали ультразвуком в течение 2 мин на установке “Ultrasonic Processor” (“Cole-Parmer Instruments”, США) с амплитудой УЗ-обработки 25% от максимально возможной (70 кГц), длительность импульса 10 с, время между импульсами 2 с.
Полиакриловую кислоту с тритиокарбонатной группой синтезировали следующим образом. БТК (5 × 10–2 моль/л) и ДАК (1 × 10–3 моль/л) растворяли в 1,4-диоксане, к раствору добавляли акриловую кислоту. Объемное отношение АК : 1,4-диоксан составляло 1 : 1. Полимеризацию проводили при 80°С до предельной конверсии. Полученный полимер лиофильно высушивали из 1,4-диоксана, растворяли в воде, диализовали против воды и лиофильно сушили. По данным ГПХ, Mn = 9.6 × × 103, Ð = 1.31.
Затравочные частицы получали дисперсионной полимеризацией БА в присутствии синтезированного полимерного ОПЦ-агента полиакриловой кислоты (ПАК). В смеси метанола и воды (4 : 1 по объему) растворяли заданное количество ПАК (1.1 × 10–3 моль/л в расчете на количество цепей) и ДАК (5.5 × 10–4 моль/л). Раствор переносили в трехгорлую колбу объемом 100 мл, погруженную в масляную баню, снабженную якорной мешалкой с двигателем и стеклянным холодильником Либиха, продували азотом в течение 30 мин, добавляли БА (суммарное объемное отношение БА : водно-метанольная смесь равно 1.0 : 7.5). Полученную смесь продували азотом при постоянном перемешивании со скоростью 80 об/мин в течение 1 ч и полимеризовали при 65°С в течение 3 ч. В начале реакции добавляли 15% от общего объема мономера, через 5 мин остальные 85%. Предельная конверсия мономера составила 70%. Полученные частицы очищали диализом против воды. Средний диаметр частиц после очистки составил 57 нм. По данным ГПХ, Mn = 17.1 × 103, Ð = 1.51.
Затравочную полимеризацию стирола проводили в трехгорлой колбе объемом 100 мл. В колбу, продутую азотом, помещали дисперсию затравочных частиц, добавляли стирол, перемешивали в течение 10–15 мин и помещали в масляную баню, разогретую до 65°С. Затем в колбу переносили заранее приготовленный раствор ДАК в метаноле. При полупериодическом введении мономера заданную часть мономерной фазы смешивали в колбе с затравочными частицами и оставляли для предварительного набухания при медленном перемешивании в течение 1 ч. Колбу помещали в баню, добавляли раствор ДАК в метаноле и через 5 мин оставшуюся часть мономерной фазы вносили по каплям в течение 6–7 мин. Полимеризацию проводили в течение 3 ч. При изучении кинетики набухания затравочных частиц реакционные смеси, содержащие дисперсию затравочных частиц и мономер, оставляли при постоянном перемешивании в течение заданного времени в атмосфере азота. Для изучения кинетики полимеризации через требуемые промежутки времени отбирали пробы объемом 2 мл, охлаждали на ледяной бане, добавляли гидрохинон для предотвращения дальнейшей полимеризации и высушивали пробу до постоянной массы при 45°С. Конверсию мономера определяли гравиметрически по сухому остатку с учетом массы исходных затравочных частиц.
Средний диаметр частиц полимерных дисперсий находили методом динамического рассеяния света с помощью лазерного анализатора частиц “Zetasizer Nano-ZS” фирмы “Malvern (Великобритания), снабженного гелий-неоновым лазером с длиной волны 633 нм и мощностью источника света 5 мВт. Диапазон измерения частиц 0.6–6000 нм. Угол детектирования рассеяния света 173°. Полученные дисперсии предварительно разбавляли водно-метанольной смесью воды (метанол : вода = 4 : 1 по объему). Измерения проводили при комнатной температуре по методике, рекомендованной производителем.
Определение молекулярно-массовых характеристик полимеров проводили методом ГПХ. Все полученные образцы содержали карбоксильные группы АК, поэтому были предварительно метилированы диазометаном [41]. Измерения выполняли на хроматографе GPC-120 фирмы “PolymerLabs” при 50°С со скоростью потока 1 мл/мин. В качестве элюента использовали ДМФА с 0.1 мас. % LiBr. Хроматограф был снабжен двумя колонками PLgel 5 µm MIXED B. Для калибровки применяли узкодисперсные стандарты ПММА.
Образцы дисперсий исследовали методом ПЭМ с использованием ПЭМ LEO 912AB с Омега фильтром (“Carl Zeiss”, Germany), рабочее напряжение 80 кВ. Образцы наносили на медные сеточки с формваровым покрытием и высушивали.
РЕЗУЛЬТАТЫ И ИХ ОБСУЖДЕНИЕ
Затравочная полимеризация стирола в присутствии триблок-сополимера ПАК–блок–ПБА–блок–ПАК
Ранее нами была продемонстрирована принципиальная возможность реализации затравочной полимеризации стирола в условиях ОПЦ-процесса под действием симметричных тритиокарбонатов [39]. В данной работе мы подробно изучили влияние условий проведения полимеризации на кинетику процесса и характеристики образующихся продуктов. Затравочные частицы синтезировали дисперсионной полимеризацией БА в водно-спиртовой среде в присутствии полимерного ОПЦ-агента – ПАК, содержащего тритиокарбонатную группу внутри цепи ПАК–SC(=S)–S–ПАК. В результате такой полимеризации формируются частицы триблок-сополимеров ПАК–блок–ПБА–SC(=S)–S–ПБА–блок–ПАК со структурой ядро–оболочка, в которых центральный блок ПБА с тритиокарбонатной группой образует ядро, а концевые блоки ПАК – оболочку, стабилизирующую частицы в дисперсионной среде [39]. В ходе затравочной полимеризации гидрофобного мономера – стирола возможны два пути реализации процесса – ОПЦ-полимеризация и радикальная полимеризация стирола (рис. 1). В первом случае следует ожидать, что блок ПС создаст внутреннее ядро в исходных затравочных частицах (рис. 1а), а во втором – гомополимер ПС случайным образом будет распределяться в ядре: в виде микродоменов (рис. 1б) или непрерывного слоя внутри (рис. 1в) или в приповерхностном слое ядра (рис. 1г). Такое микрофазовое разделение должно произойти вследствие низкой термодинамической совместимости ПС и ПБА [42].
Рис. 1.
Схема образования возможных продуктов затравочной ОПЦ-полимеризации стирола. Цветные рисунки можно посмотреть в электронной версии.
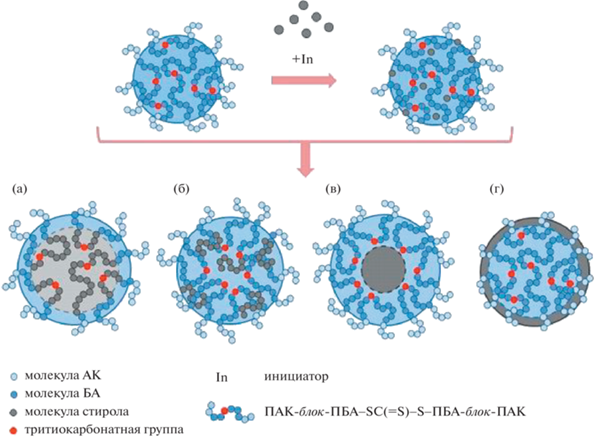
Для осуществления затравочной полимеризации обычно проводят предварительное набухание мономера в затравочных частицах. Чтобы определить необходимое для набухания время и количество стирола, способного диффундировать внутрь частиц, была изучена зависимость среднечисленного диаметра Dn затравочных частиц от продолжительности набухания стирола в водно-метанольной среде (метанол : вода = 9 по объему). При массовом отношении стирола к затравочным частицам, равном 1 и 2, наблюдается унимодальное распределение частиц по размерам, при этом Dn частиц увеличивается в течение 1 ч с 57 до 90–120 нм и далее почти не изменяется (рис. 2, точки 1, 2). Можно предположить, что в этих условиях весь мономер попадает внутрь затравочных частиц, что исключает гомополимеризацию стирола вне частиц. При трехкратном массовом избытке стирола распределение частиц по размерам становится бимодальным, и помимо набухания затравочных частиц (рис. 2, точки 3), вероятно, формируются микрокапли мономера с Dn = 150–300 нм (рис. 2, точки 3′).
Рис. 2.
Зависимость Dn затравочных частиц от времени набухания стирола. Объемное отношение метанол : : вода = 9 и стирол : дисперсионная среда = 1 : 25. Массовое отношение стирол : затравочные частицы = = 1 (1), 2 (2) и 3 (3, 3').
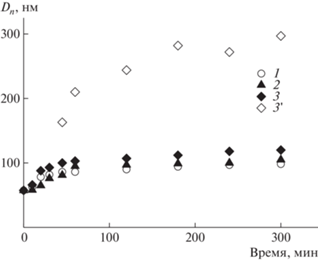
На следующем этапе необходимо было подобрать оптимальный состав водно-метанольной смеси. Стирол имеет низкую растворимость в воде, но хорошую растворимость в метаноле. Это подтверждается изменением среднечисленного диаметра частиц и распределения частиц по размерам в зависимости от содержания воды в смеси (рис. 3). Ни в метаноле, ни при объемном отношении метанол : вода, равном 9, образование микрокапель стирола не регистрируется. Лишь при отношении метанол : вода = 4 наблюдается легкая опалесценция и формируются микрокапли с бимодальным распределением частиц по размерам с Dn основной фракции 145 нм и Dn второй фракции 693 нм. Дальнейшее увеличение содержания воды приводит снова к унимодальному распределению частиц по размерам, и Dn микрокапель меняется от 300 до 400 нм, а при равном содержании метанола и воды Dn = 400 нм.
Рис. 3.
Гистограммы распределения частиц по размерам в водно-спиртовой смеси при объемном отношении метанол : вода, равном 1 : 0 (а), 9 : 1 (б), 4 : 1 (в) и 1 : 1 (г).
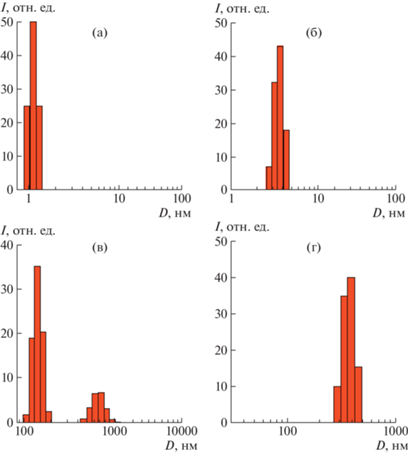
Используя полученные результаты, для осуществления затравочной ОПЦ-полимеризации стирола выбрали объемное отношение метанол : вода, равное единице, и массовое отношение стирола к затравочным частицам, равное двум, провели набухание затравочных частиц в течение разного времени и исследовали кинетику полимеризации (рис. 4). Видно, что увеличение продолжительности набухания затравочных частиц, т.е. повышение содержания в них стирола, приводит к замедлению полимеризации и появлению на кинетических кривых индукционного периода. Более того, уменьшается не только общая скорость полимеризации, но и предельно достижимые конверсии мономера. Возможные причины этого явления будут обсуждаться ниже. Полученные результаты позволяют предположить, что предварительное набухание частиц мономером нежелательно для реализации ОПЦ-процесса, поэтому в дальнейших экспериментах мы отказались от этого подхода.
Рис. 4.
Зависимость конверсии мономера от времени полимеризации при объемном отношении метанола к воде 1 : 1 и стирола к дисперсионной среде – 1 : 25. Массовое отношение стирола к затравочным частицам 2 : 1; [стирол] = = 0.34 моль/л, [ДАК] = 5.5 × × 10–4 моль/л, Т = 65°С, время набухания частиц 20 мин (1), 3 ч (2) и 12 ч (3).
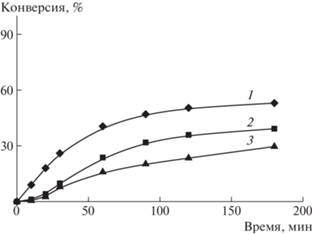
На рис. 5 приведены зависимости степени превращения мономера от времени в ходе затравочной полимеризации при изменении состава дисперсионной среды и концентрации инициатора (а), массового отношения стирола и затравочных частиц (б) и содержания затравочных частиц в дисперсионной среде при их постоянном массовом отношении к стиролу (в). Видно, что с ростом содержания воды достигается более высокая предельная конверсия мономера. Одновременно с этим на кинетической кривой появляется индукционный период, длительность которого не зависит от концентрации инициатора. Уменьшение концентрации инициатора в 1.6 раза практически не влияет на начальную кинетику полимеризации, но приводит к резкому понижению предельной конверсии мономера. Причина данного явления не ясна и требует дальнейших исследований. Увеличение массового отношения стирола к затравочным частицам способствует вначале резкому повышению общей конверсии мономера на участке, начиная с 20%, а затем к ее слабому росту. Напротив, даже при незначительном повышении содержания затравочных частиц в реакционной среде при их постоянном массовом отношении к мономеру скорость полимеризации резко понижается.
Рис. 5.
Зависимость конверсии мономера от времени затравочной полимеризации при 65°С в водно-метанольной смеси. а: [стирол] = 0.34, [ДАК] = 5.5 × 10–4 (1, 2) и 3.5 × 10–4 моль/л (3); массовое отношение стирола к затравочным частицам 2 : 1, объемное отношение стирола к дисперсионной среде 1 : 25, метанол : вода = 1 : 1 (1), 1 : 3 (2, 3); б: [ДАК] = 5.5 × 10–4 моль/л; объемное отношение стирола к дисперсионной среде 1 : 25 и метанола к воде 1 : 3; массовое отношение стирола к затравочным частицам 1 (1), 1.5 (2) и 2 (3); в: [ДАК] = 5.5 × 10–4 моль/л; объемное отношение метанола к воде 1 : 1 и массовое отношение стирола к затравочным частицам 2 : 1; содержание затравочных частиц в смеси 2.5 (1), 3.0 (2) и 3.5 мас. % (3).
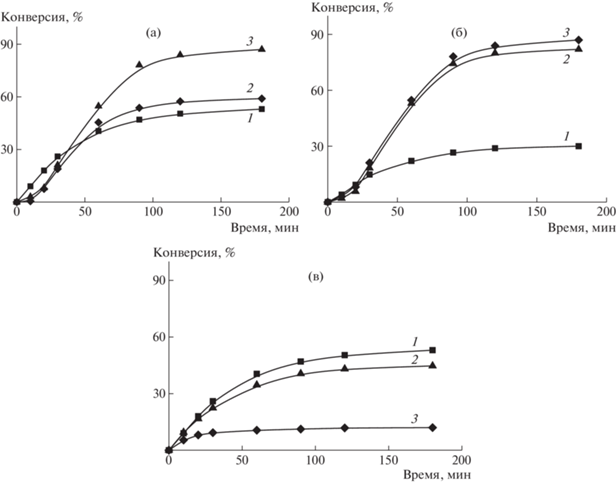
Стоит отметить, что практически для всех исследованных систем распределение частиц по размерам унимодальное. При этом значение Dn частиц уже на начальных конверсиях быстро возрастает в ⁓1.5 раза (на ~50 нм) и далее практически не изменяется до конверсии мономера ~60% (рис. 6). При более высоких конверсиях Dn частиц увеличивается еще в 1.5–2 раза, что, вероятно, связано с агрегацией частиц. Следовательно, можно предполагать, что стирол проникает в затравочные частицы в начале реакции, и основная часть полимеризации идет внутри этих частиц. В некоторых случаях наблюдали появление в ходе полимеризации второй фракции частиц, значение Dn которой в 1.5–3 раза выше, однако ее содержание в продукте реакции не превышало 3–5%.
Рис. 6.
Зависимость среднечисленного диаметра Dn частиц от конверсии мономера в ходе затравочной полимеризации стирола при 65°С. [Стирол] = 0.34, [ДАК] = 5.5 × 10–4 (1, 2) и 3.5 × 10–4 моль/л (3); массовое отношение стирола к затравочным частицам 2 : 1, объемное отношение стирола к дисперсионной среде 1 : 25, метанола к воде 1 : 1 (1), 1 : 3 (2, 3).
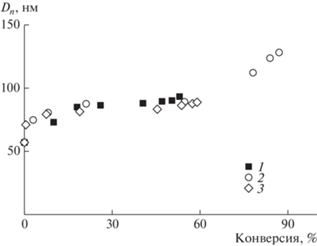
Для доказательства механизма ОПЦ были изучены молекулярно-массовые характеристики полученных продуктов. По данным ГПХ, с ростом конверсии кривые ММР всех синтезированных полимеров сдвигаются в область более высоких ММ (рис. 7). Видно, что исходный блок-сополимер медленно расходуется в ходе процесса. Мода, отвечающая растущему полимеру, трансформируется и на ней наблюдаются плечи в высокомолекулярной области. Наблюдаемые закономерности не зависят от содержания воды в системе, концентрации инициатора и массового соотношения стирола и затравочных частиц. Следовательно, можно предположить, что при накоплении полимера в затравочных частицах контроль ММР ухудшается. Вместе с тем Mn образующихся полимеров линейно увеличивается с ростом конверсии мономера (рис. 8а), однако дисперсность полимера Đ повышается, что обусловлено, вероятно, высокой концентрацией ДАК и его вкладом в образование “мертвых” цепей (рис. 8б).
Рис. 7.
Нормированные к единичной площади кривые ГПХ продуктов затравочной полимеризации стирола при 65°С. [ДАК] = 5.5 × 10–4 (а, б, г) и 3.5 × 10–4 моль/л (в). Объемное отношение мономера к дисперсионной среде 1 : 25, метанола к воде 1 : 3 (а, в, г) и 1 : 1 (б); массовое отношение стирола к затравочным частицам 2 (а–в) и 1.5 (г).
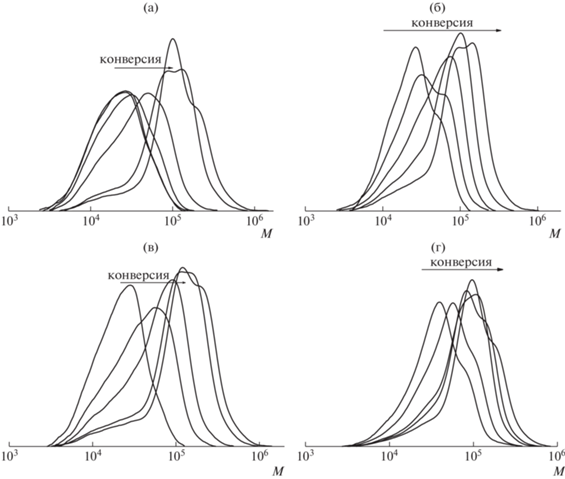
Рис. 8.
Зависимости Mn (а) и Ð(б) полимеров от конверсии при затравочной полимеризации стирола при 65°С и [ДАК] = 5.5 × 10–4 моль/л. Массовое отношение стирола к затравочным частицам 2 (1, 2) и 1.5 (3); объемное отношение метанола к воде 1 : 3 (1, 3) и 1 : 1 (2), стирола к дисперсионной среде 1 : 25.
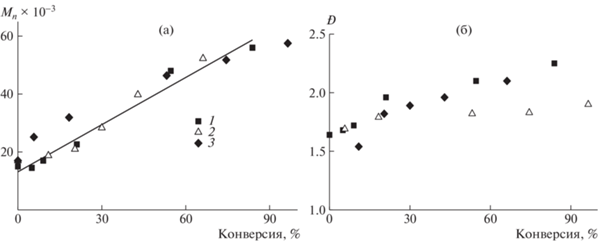
Таким образом, мы установили, что затравочная полимеризация стирола протекает по ОПЦ-механизму. При этом исследование кинетики полимеризации показывает замедление полимеризации, усиливающееся с ростом содержания затравочных частиц, а анализ конверсионного изменения ММР свидетельствует о нарушении ОПЦ-механизма. Объяснить полученные результаты можно, предположив, что при полимеризации стирола внутри затравочных частиц происходит обрыв на радикальных интермедиатах, характерный для ОПЦ-полимеризации стирола [43]:
В результате уменьшается число активных центров, и как следствие, скорость процесса, и образуются звездообразные продукты, ММ которых выше, чем у линейного полимера. Тем не менее, можно утверждать, что основным продуктом затравочной полимеризации является блок-сополимер ПАК–блок–ПБА–блок–ПС–SC(=S)–S–ПС–блок–ПБА–блок–ПАК.
Иммобилизация наночастиц TiO2 в процессе затравочной ОПЦ-полимеризации стирола
На следующем этапе мы применили затравочную ОПЦ-полимеризацию для иммобилизации неорганических наночастиц TiO2 с Dn ~ 25 нм. Предварительно наночастицы гидрофобизировали стерическим стабилизатором Span 80 и затем готовили их суспензию в мономере. Наибольшей устойчивостью при хранении в течение 3 ч характеризовались суспензии наночастиц (1–15 мас. %) в мономере, полученные в присутствии 1 мас. % Span 80, обработанные ультразвуком в течение 1 мин.
Кинетические закономерности затравочной ОПЦ-полимеризации стирола в присутствии наночастиц TiO2 оказались близкими к рассмотренным выше. Скорость полимеризации увеличивается по мере повышения содержания воды в дисперсионной среде и максимальна в чистой воде (рис. 9а). Рост содержания TiO2 в мономерной фазе сопровождается появлением индукционного периода и увеличением его длительности, а также уменьшением скорости полимеризации в целом (рис. 9б). При этом данный результат не зависит от способа введения мономера в синтез. Можно предположить, что наночастицы TiO2 адсорбируются на поверхности затравочных частиц, оболочку которых составляют блоки ПАК. В итоге создается стерическое препятствие для проникновения стирола или его олигорадикалов внутрь частиц. Увеличение концентрации инициатора и мономера позволяет повысить скорость полимеризации и сократить индукционный период (рис. 9в, 9г). Существенного роста скорости полимеризации удалось достичь в случае, когда затравочные частицы вначале подвергли набуханию в присутствии части мономерной фазы, содержащей наночастицы TiO2, а оставшийся мономер вносили спустя некоторое время после начала полимеризации (полупериодический способ) (рис. 9д).
Рис. 9.
Зависимость конверсии мономера от времени затравочной полимеризации в присутствии наночастиц TiO2 при 65°С в водно-метанольной смеси. а: [ДАК] = 1.6 × 10–3 моль/л (3); 1 мас. % TiO2; массовое отношение стирола к затравочным частицам 1 : 1, объемное отношение метанол : вода = 1 : 0 (1), 1 : 1 (2), 1 : 3 (3) и 0 : 1 (4); б: [ДАК] = 1.6 × 10–3 моль/л; массовое отношение стирола к затравочным частицам 1 : 1 содержание TiO2 равно 1 (1), 5 (2, 4), 2 (3) и 10 мас. % (5); введение мономерной фазы в воду периодическим (1, 2) и полупериодическим способом (3–5); в: массовое отношение стирола к затравочным частицам 1 : 3, содержание TiO2 равно 5 (1, 2) и 10 мас. % (3, 4); введение мономерной фазы в воду полупериодическим способом; [ДАК] × 103 = 1.6 (1), 2.5 (2), 3 (3) и 5 моль/л (4); г: [ДАК] = 3 × 10–3 моль/л, 5 мас. % TiO2; введение мономерной фазы в воду полупериодическим способом; массовое отношение стирола к затравочным частицам 5 (1), 4 (2), 3 (3) и 2 (4); д: [ДАК] = 1.6 × 10–3 моль/л, 2 мас. % TiO2, массовое отношение стирола к затравочным частицам 1 : 3; введение мономерной фазы в воду периодическим (1) и полупериодическим способом, по каплям (2, 3); объем стирола 50 (2) и 25% (3) .
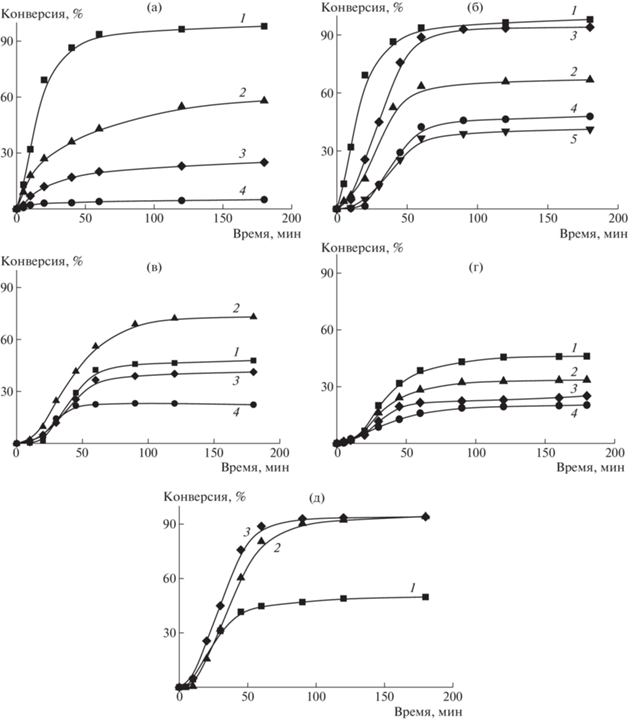
Анализ распределения частиц по размерам всех суспензий композиционных частиц показал, что их средний диаметр Dn увеличивается на 30–40 нм по сравнению с исходными затравочными частицами (рис. 10а). При этом независимо от способа введения мономера гистограммы распределения частиц по размерам сдвигаются в область более низких значений Dn с увеличением концентрации TiO2 (рис. 10). Варьирование объема порций мономерной фазы, вводимых на стадии набухания и в ходе реакции, способствовало не только повышению скорости, но и формированию частиц с узким распределением частиц по размерам.
Рис. 10.
Гистограммы распределения по размерам затравочных частиц (а) и частиц при затравочной ОПЦ-полимеризации при 65°С в водной среде при полупериодическом введении мономера в присутствии 2 (б), 5 (в) и 10 мас. % TiO2 (г). Массовое отношение стирол : затравочные частицы = 1 : 3, [ДАК] = 1.6 × 10–3 моль/л.
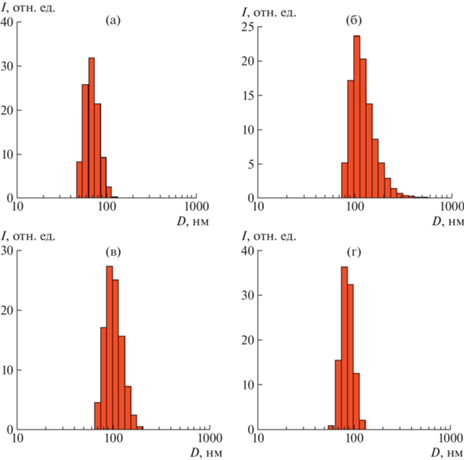
Полученные кинетические результаты и данные анализа размера частиц позволяют предполагать, что наночастицы TiO2 создают на поверхности затравочных частиц стерические затруднения, которые препятствуют попаданию стирола в место реакции и отвечают за замедление полимеризации. Подтверждением этому служат эксперименты, выполненные при концентрации TiO2 5 и 10 мас. % при разной концентрации инициатора. Dn частиц, полученных при 5 мас. % TiO2 и [ДАК] = 1.6 × 10–3 и 2.5 × 10–3 моль/л, имеют значения 103 и 99 нм соответственно. В то же время Dn частиц, полученных при 10 мас. % TiO2 и [ДАК] = 3 × 10–3 и 5 × 10–3 моль/л, равны 85 и 87 нм.
Схематично процесс формирования композиционных частиц в ходе затравочной ОПЦ-полимеризации можно представить как показано на рис. 11.
О дисперсном составе полученных суспензий блок-сополимеров можно также судить по данным просвечивающей электронной микроскопии. Значения Dn коррелируют с данными динамического рассеяния света. В отсутствие TiO2 суспензия представляет собой суспензию индивидуальных частиц блок-сополимера (рис. 12а). При проведении затравочной полимеризации в присутствии TiO2 (5 мас. %) можно заметить, что частицы склонны к агломерации (рис. 12б), причем с уменьшением содержания стирола агломерация усиливается (рис. 12в и 12г). Также по микрофотографиям видно, что содержание наночастиц в полимерной матрице было не высоким (рис. 12г).
Рис. 12.
ПЭМ-микрофотографии частиц, полученных затравочной ОПЦ-полимеризацией в водной среде при полупериодическом введении мономера в отсутствие (а) и в присутствии TiO2 (5 мас. %) при массовом соотношении стирол : затравочные частицы: 1 : 1 (б), 1 : 3 (в) и 1 : 5 (г). [ДАК] = 3 × 10–3 моль/л, Т = 65°С.
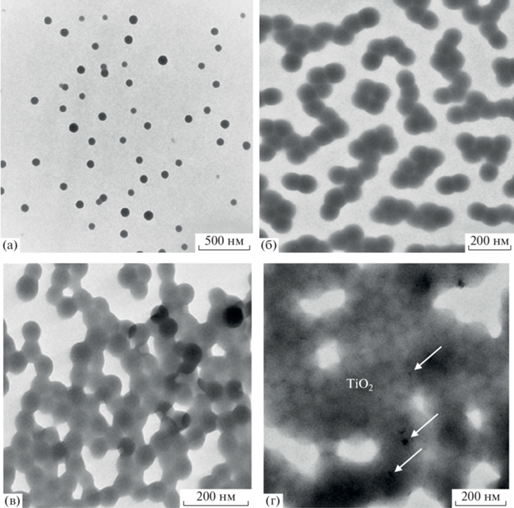
ЗАКЛЮЧЕНИЕ
В результате проведенных исследований были изучены закономерности затравочной ОПЦ-полимеризации стирола в отсутствие и в присутствии наночастиц диоксида титана. В качестве затравочных частиц использовали дисперсии амфифильных триблок-сополимеров ПАК–блок–
ПБА–блок–ПАК, содержащих тритиокарбонатный фрагмент внутри цепи. Кинетика затравочной полимеризации регулируется содержанием воды, затравочных частиц, массовым отношением стирола и затравочных частиц и концентрацией инициатора. Полимеризация в выбранных условиях протекает по ОПЦ-механизму и характеризуется ростом молекулярной массы полимеров с увеличением конверсии мономера. Существенно, что полученные суспензии, даже в отсутствие традиционных поверхностно-активных веществ, характеризовались унимодальным распределением частиц по размерам и сохраняли устойчивость в течение длительного времени. Следовательно, структура ядро–оболочка (функцию оболочки выполняют концевые блоки ПАК) сохраняется в ходе затравочной полимеризации.
На примере наночастиц TiO2 была определена возможность использования иммобилизации наночастиц в процессе затравочной ОПЦ-полимеризации стирола. Полученные кинетические закономерности оказались близкими к закономерностям затравочной полимеризации в отсутствие наночастиц. Однако в первом случае наблюдается более отчетливое замедление полимеризации, которое может быть вызвано тем, что наночастицы TiO2 создают на поверхности затравочных частиц стерические затруднения и препятствуют попаданию стирола в место реакции. В результате были получены устойчивые суспензии композиционных частиц TiO2 и блок-сополимера акриловой кислоты, бутилакрилата и стирола со средним диаметром частиц от 60 до 130 нм. Методом просвечивающей электронной микроскопии было показано, что повышение концентрации наночастиц приводит к увеличению склонности гибридных частиц к агломерации.
Список литературы
Holder S.J., Sommerdijk N.A.J.M. // Polym. Chem. 2011. V. 2. P. 1018.
Li N.K., Fuss W.H., Tang L., Gu R., Chilkoti A., Zauscher S., Yingling Y.G. // Soft. Matter. 2015. V. 11. P. 8236.
Colombani O., Ruppel M., Burkhardt M., Drechsler M., Schumacher M., Gradzielski M., Schweins R., Muller A.H.E. // Macromolecules. 2007. V. 40. P. 4351.
Blanazs A., Armes S.P., Ryan A.J. // Macromol. Rapid Commun. 2009. V. 30. P. 267.
Ge Z., Xie D., Chen D., Jiang X., Zhang Y., Liu H., Liu S. // Macromolecules. 2007. V. 40. P. 3538.
Biswas S., Kumari P., Lakhani P.M., Ghosh B. // Eur. J. Pharm. Sci. 2016. V. 83. P. 184.
Song S., Zhou H., Manners I., Winnik M.A. // Chem. 2021. V. 7. P. 1.
Tan J., Sun H., Yu M., Sumerlin B.S., Zhang L. // ACS Macro Lett. 2015. V. 4. P.1249.
Tan J., Bai Y., Zhang X., Huang C., Liu D., Zhang L. // Macromol. Rapid Commun. 2016. V. 37. P. 1434.
Tan J., Zhang X., Liu D., Bai Y., Huang C., Li X., Zhang L. // Macromol. Rapid Commun. 2017. V. 38. P. 1600508.
Xu S., Ng G., Xu J., Kuchel R.P., Yeow J., Boyer C. // ACS Macro Lett. 2017. V. 6. P. 1237.
Huo F., Gao C., Dan M., Xiao X., Su Y., Zhang W. // Polym. Chem. 2014. V. 5. 2736.
Hojjati B., Charpentier P.A. // J. Polym. Sci., Polym. Chem. 2008. V. 46. P. 3926.
Hernandez-Guerrero M., Davis T.P., Barner-Kowollik C., Stenzel M.H. // Eur. Polym. J. 2005. V. 41. P. 2264.
Hojjati B., Sui R., Charpentier P.A. // Polymer. 2007. V. 48. P. 5850.
Jordan J., Jacob K.I., Tannenbaum R., Sharaf M.A., Jasiuk I. // Mater. Sci. Eng. A. 2005. V. 393. P. 1.
Pyun J., Jia S., Kowalewski T., Patterson G.D., Matyjaszewski K. // Macromolecules. 2003. V. 36. № 14. P. 5094.
Znang W.J., Hong C.Y., Pan C.Y. // Macromol. Rapid Commun. 2018. V. 40. P. 1800279.
Wang X., An Z.S. // Macromol. Rapid Commun. 2019. V. 40. P. 1800325.
Dai X.C., Yu L.L., Znang Y.X., Zhang L., Tan J.B. // Macromolecules. 2019. V. 52. № 19. P. 7468.
Zhang W.J., Kadirkhanov J., Wang C.H., Ding S.G., Hong C.Y., Wang F., You Y.Z. // Polym. Chem. 2020. V. 11. P. 3654.
Gurnani P., Perrier S. // Progr. Polym. Sci. 2020. V. 102. P. 101209.
D'Agosto F., Rieger J., Lansalot M. // Angew. Chem. Int. Ed. 2020. V. 59. P. 8368.
Canning S.L., Smith G.N., Armes S.P. // Macromolecules. 2016. V. 49. № 6. P. 1985.
Pearce S., Perez-Mercader J. // Polym. Chem. 2021. V. 12. P. 29.
Su Y., Xiao X., Li S., Dan M., Wang X., Zhang W. // Polym. Chem. 2014. V. 5. № 2. P. 578.
Semsarilar M., Ladmiral V., Blanazs A., Armes S.P. // Langmuir. 2013. V. 29. P. 7416.
Xiao X., He S., Dan M., Su Y., Huo F., Zhang W. // J. Polym. Sci., Polym. Chem. 2013. V. 51. P. 3177.
Can A., Hoeppener S., Guillet P., Gohy J.F., Hoogenboom R., Schubert U.S. // J. Polym. Sci., Polym. Chem. 2011. V. 49. № 17. P. 3681.
Barthel M.J., Rudolph T., Crotty S., Schacher F.H., Schubert U.S. // J. Polym. Sci., Polym. Chem. 2012. V. 50. № 23. P. 4958.
Xiong D., He Z., An Y., Li Z., Wang H., Chen X., Shi L. // Polymer. 2008. V. 49. № 10. P. 2548.
Hu Y., Darcos V., Monge S., Li S. // J. Polym. Sci., Polym. Chem. 2013. V. 51. № 15. 3274.
Charbonneau C., Lima M.D.S., Chassenieux C., Colombani O., Taco N. // Phys. Chem. Chem. Phys. 2013. V. 15. P. 3955.
Ward M.A., Georgiou T.K. // J. Polym. Sci., Polym. Chem. 2013. V. 51. № 13. P. 2850.
Li X., Tan J., Xu Q., He J., Zhang L. // Macromol. Rapid Commun. 2018. V. 39. P. 1800473.
Chen S., Shi P., Zhang W. // Chin. J. Polym. Sci. 2017. V. 35. № 4. P. 455.
Zhou H., Liu C., Qu Y., Gao C., Shi K., Zhang W. // Macromolecules. 2016. V. 49. P. 8167.
Xiao X., He S., Dan M., Huo F., Zhang W. // Chem. Commun. 2014. V. 50. № 30. P. 3969.
Serkhacheva N.S., Chernikova E.V., Prokopov N.I., Ogai V.V., Mineeva K.O., Tselousov D.S., Plyusnina I.O. // Polymer Science B. 2020. V. 62. № 5. P. 499.
Chernikova E.V., Terpugova P.S., Bui C., Charleux B. // Polymer. 2003. V. 44. № 5. P. 4101.
Giordanengo R., Viel S., Hidalgo M., Allard-Breton B., Thévand A., Charles L. // J. Am. Soc. Mass Spectrom. 2010. V. 21. № 6. P. 1075.
Chalykh A.E., Nikulova U.V., Shcherbina A.A., Chernikova E.V. // Polymer Science A. 2019. V. 61. № 2. P. 175.
Chernikova E.V., Sivtsov E.V. // Polymer Science B. 2017. V. 59. № 2. P. 117.
Дополнительные материалы отсутствуют.
Инструменты
Высокомолекулярные соединения (серия Б)