Химия высоких энергий, 2023, T. 57, № 1, стр. 73-79
Лазерная абляция стирол-метакрилатных композитов
Н. В. Бузин a, Г. М. Мухаметова a, С. Н. Холуйская a, А. Г. Киселев a, В. Н. Калиниченко b, А. А. Гриднев a, *
a Федеральный исследовательский центр институт химической физики им. Н.Н. Семенова РАН
119334 Москва, ул. Косыгина, 4, Россия
b Институт биохимической физики им. Н.М. Эмануэля РАН
119334 Москва, ул. Косыгина, 4, Россия
* E-mail: 99gridnev@gmail.com
Поступила в редакцию 02.02.2022
После доработки 03.09.2022
Принята к публикации 05.09.2022
- EDN: DDSTZI
- DOI: 10.31857/S0023119323010023
Аннотация
Исследованы различные стирол-метакрилатные композиты с минеральными наполнителями в качестве подложки при нанесении медных дорожек на поверхностях после лазерной абляции. Показано, что как недостаточный нагрев лазером подложки с нанесенным лаком, так и ее перегрев, негативно сказывается на проведении химического меднения. Применение сшитых стирол-метакрилатных полимеров позволяет достигать устойчивого меднения обработанной лазером поверхности подложки с нанесенным лаковым слоем. Показано, что при целесообразном подборе параметров абляции в качестве наполнителя лака можно использовать такие мелкодисперсные минералы как тальк, селадонит, аквамарин, шунгит, оксиды хрома и железа (охра) для проведения химического меднения обработанных лазером частей подложки.
ВВЕДЕНИЕ
В последнее время наблюдается растущий интерес к применению лазеров для производства электронных компонентов и интегрированных монтажных плат с целью упрощения производства и снижения веса электронных приборов. Предложенный десять лет назад немецкой компанией LPKF [1] метод прямого лазерного структурирования (DLS) нашел широкое применение в электронике для создания антенн в мобильных устройствах и трехмерных проводящих структур на литых монтажных основаниях (3D-MID).
Под методом прямого лазерного структурирования понимается нанесение токопроводящих дорожек на диэлектрики при помощи лазера. Сущность его заключается в покрытии поверхности подложки, обычно литьевого полимера, композитным лаком с последующим нанесением лазером необходимого рисунка/структуры. Лазерный луч разлагает и испаряет органическую компоненту лака, обнажая неорганическую составляющую с активатором меднения. После этого изделие химически меднят в результате чего на поверхности диэлектрика образуются токопроводящие дорожки. Условия и состав меднящего раствора подбираются таким образом, чтобы меднение протекало только в местах травления лазером [2].
Метод прямого лазерного структурирования содержит значительное ноу-хау. Достаточно сказать, что патентная заявка метода составлена из одних общих деклараций без единого примера. Несколько публикаций на тему прямого лазерного структурирования от компании LPKF [3] не содержат подробных деталей. С подборкой этих публикаций можно ознакомиться на сайте компании LPKF [4]. Не содержит технических деталей и другая патентная заявка [5].
Поскольку этот метод, по сведениям компании LPKF, используется для создания примерно половины всех трехмерных проводящих структур на литых монтажных основаниях, разными исследователями были предприняты определенные попытки исследовать метод прямого лазерного структурирования и его усовершенствовать. В основном, были предложены различные композиционные материалы в качестве подложки, такие как полиамиды, поликарбонаты, полистирол-малеиновый агидрид, полифениленсульфид, полипропилен и другие полимеры. Эти материалы были экструзионно наполнены такими неорганическими наполнителями, как титан, алюминий, медный порошок, стеклянные волокна, соли меди [6–11].
Введение наполнителей в подложку предполагает использование лазера как для удаления органической компоненты из материала подложки при нагревании лазером, так и для одновременной модификации неорганической компоненты. Кроме того, одной из причин введения различных добавок в матрицу является исключение операции травления подложки солями палладия после обработки лазером. Металлизация обработанных лазером панелей в литературе описана недостаточно. Обычно при этом происходит либо использование коммерческих смесей, либо меднение проводится сторонней организацией [12, 6 ]. Только некоторые исследователи детально описывают процесс меднения [13, 14], причем применяются достаточно многокомпонентные химические системы.
В литературе приведены энергетические параметры для луча лазера, но не обсуждается химизм разложения полимерной матрицы, который, как показывают тестовые эксперименты, существенно влияет на свойства поверхности подвергшейся воздействию лазера. Лазерный луч вызывает очень быстрый разогрев пластика. Ударная тепловая обработка поверхности приводит к образованию продуктов разложения, состав и свойства которых зависят от состава исходного пластика. Температура пластика под действием лазерного луча может достигать, по-видимому, нескольких сотен градусов. При таких температурах часть продуктов разложения подложки может быть летучей, но часть может оставаться жидкой, особенно в областях непосредственно прилегающих к точке применения лазерного теплового удара. Таким образом, помимо частично испаренной полимерной матрицы при лазерной абляции возможно образование большого количества продуктов частичной карбонизации.
Многочисленные данные по термогравиметрическому анализу очень условно могут быть полезны в предсказании поведения материала подложки под ударным нагреваниeм лучом лазера из-за временной разницы этих двух аспектов разложения полимера подложки. Если в термогравиметрическом анализе скорость нагревания достигает, примерно, 10°/мин, то при абляции лазером скорость нагрева в точке применения лазера на подложке на несколько порядков выше. Таким образом, при использовании термогравиметрического анализа, в отличие от лазерной обработки, весьма возможно протекание вторичных реакций конденсации и образования частично карбонизированных нелетучих продуктов, устойчивых к дальнейшему разложению. При ударном термолизе при лазерной абляции более вероятно испарение полимерной подложки после ее деструкции. При этом важнейшими показателями должны быть, во-первых, легкость деструкции полимера до мелких фрагментов, и, во-вторых, полнота удаления таких фрагментов.
На это косвенно указывают результаты работы исследовательской группы Zhou [14], в которой исследовалось применение метода прямого лазерного структурирования, где в качестве подложки использовалась экструдированная смесь пластика акрилонитрил-бутадиен-стирола (АБС) с хромитом меди. В работе [14] представлены фотографии поверхности подложки после обработки лазером, на которых видно, что поверхность представляет собой сетчатую (сотовую) структуру с черными обугленными доменами, появившимися в результате проколов поверхности пульсирующим лазерным лучом. В центре этих доменов спорадически проявляются точки восстановленной меди. Большая часть доменов покрыта обуглившимися остатками подложки. Для сравнения были использованы подложки композитного материала изготовленными из АБС-пластика с наполнителем СuO. После обработки лазером на их поверхности также образуется сетчатая структура карбонизированного пластика, но без вкраплений металлической меди. Эти образцы не покрываются медью при химическом меднении. Вероятно, что продукты лазерного разложения пластика покрывают остатки СuO или ее возможной восстановленной формы, препятствуя тем самым дальнейшему осаждению меди на этих участках.
Подобные результаты получены и с композитом пластика АБС с гидрофосфатом меди(I) [10] и оксалатом меди [14]. Можно заметить, что медь во всех этих соединениях должна под действием лазерного облучения восстанавливаться до металлической меди, особенно в оксалате (температура разложения 304°С) [15]. Однако образование меди не наблюдается вне полимерной матрицы при действии лазера на оксалат меди. Это указывает на то, что либо температура подложки под воздействием лазерного луча не поднимается существенно выше 350°С, либо повышение температуры было слишком кратковременным.
Цель работы – исследование характеристик стирол-метакрилатных полимеров в качестве связующего для неорганического наполнителя при нанесении токопроводящих дорожек на подложки под действием лазера. В отличие от используемого некоторыми авторами подхода получения подложки посредством экструзионного наполнения, в данной работе для создания поверхности абляции был использован композитный лак. Стирол-метакрилатный лак, содержащий неорганический наполнитель, наносился на поверхность полимерных пластин (АБС-пластик). Такой подход, на наш взгляд, имеет определенные преимущества по сравнению с экструзионным наполнением. Во-первых, он позволяет использовать любую литую монтажную плату, что удешевляет производство. Во-вторых, использование лака позволяет легко менять поверхностные свойства подложки посредством изменения состава лака.
ЭКСПЕРИМЕНТАЛЬНАЯ ЧАСТЬ
Лазерную абляцию проводили с помощью иттербиевого лазера GARD MINI 20 (Garden Technology Co.) с длиной волны 1064 нм и максимальной мощностью излучения 15 Вт. Тип излучателя – CNI, управляющая линза – CINO-GALVO. Управляющая программа – EzCAD. Абляцию проводили при скорости луча 500–2000 мм/с, расстояние между дорожками 5–20 мкм, мощность луча 1.5–10 Вт. Удельное электрическое сопротивление ρ измеряли с помощью миллиомметра СТ-2258С (Suzhou Jingge Electronic Co., Ltd) с помощью четырехточечного зонда с расстоянием между контактами 2 мм.
Диспергирование проводили с помощью диспергатора Стеглер DG-360 (Stegler Co.) c диаметром ротора 10 мм при 20000 об./мин. Лак наносили на пластины АБС-пластика методом распыления аэрографом JAS-1146 (Jas Co.) при давлении 1 атм (толщина слоя лака 20–30 мкм) или поливом (толщина слоя лака 100–130 мкм). Фигуры абляции (прямоугольник) имели размеры шириной 8–15 мм и длиной 8–50 мм.
В качестве наполнителя использовали тальк марок МТ-ЭГС (ГОСТ 19284-79), Т-20 (ТУ 5727-001-49439345-02), ТМО (ГОСТ 2135-75). Тальк взбалтывали в этилацетате и пропускали через стеклянный фильтр с маркировкой ПОР160 под вакуумом. Фильтрат сушили на воздухе до постоянного веса. Пигменты шунгит, селадонит, оксид хрома(III), охра красная приобретали в ООО “Натуральные пигменты”. Все реактивы, используемые для синтеза полимера (Aldrich, США), применяли без дополнительной очистки.
В качестве связующих были использованы следующие системы несшитых сополимеров: метилметакрилат : бутилметакрилат = 2 : 1; фенилэтилметакрилат : бутилметакрилат = 18 : 14; бутилметакрилат : стирол = 14 : 18; метилметакрилат : альфа-метилстирол = 1 : 1; стирол : бутилметакрилат : гидроксиэтилметакрилат = 20 : 14 : 13; фенилэтилметакрилат : бутилметакрилат : гидроксиэтилметакрилат = 19 : 11 : 7; стирол : бутилметакрилат : акриловая кислота : гидроксиэтилметакрилат = 20 : 7 : 3 : 13. Состав дан по объемному соотношению мономеров перед полимеризацией. Кроме того, в качестве связующего была использована система полиизоцианатнеопентилгликоль : изофорондиизоцианат = 1 : 1.
Полимер для приготовления лака синтезировали по следующей методике. В 100 мл колбу помещали 0.8 г АИБН (азо-бис(изобутиронитрил), ДИНИЗ) и 50 мл толуола. После растворения АИБНа при комнатной температуре последовательно добавляли 2 мл метилметакрилата и 1 мл бутилметакрилата, продували раствор азотом и грели 4 ч при 75°С, затем 4 ч при 80°C, 3 ч при 85°C, 1.5 ч при 90°С и 1 ч при 100°С. Вязкий раствор выливали в стакан с 300 мл гексана и перемешивали шпателем 0.5 ч. Полимер отделяли и сушили в чашках Петри при 100–120°С до постоянного веса.
Сшитый полимер получали следующим образом. Навеску полимера массой 1.3 г растворяли в 20 мл смеси этилацетат–бутилацетат (в соотношении 2 : 1). После растворения полимера к раствору добавляли 0.18 г талька и гомогенизировали 6 мин при 20 000 об./мин. К получившейся суспензии добавляли 0.3 мл олигомера гексаметилендиизоцианата (биурет) и 0.6 мл раствора дибутилоловодилаурата в этилацетате (0.0025 мл/мл). Затем перемешивали 5 мин на магнитной мешалке и наносили поливом или распыляли на пластину из АБС-пластика и сушили в течение суток при комнатной температуре.
Химическое меднение образцов согласно [15] осуществляли после предварительной сенсибилизации. Для сенсибилизирования предварительно подвергнутые абляции пластины погружали на 2 мин в аммиачный раствор серебра, затем образцы промывали дистиллированной водой и обсушивали фильтровальной бумагой. Аммиачный раствор для активации готовили следующим образом. К 1 г нитрата серебра в 70 мл дистиллированной воды добавляли по каплям водный аммиак до растворения образовавшегося осадка, затем доводили объем дистиллированной водой до 100 мл.
Для меднения готовили раствор следующего состава: CuSO4·7H2O – 30 г/л; NaOH – 50 г/л; Na2CO3 – 20 г/л; (HOOCCH2)2N(CH2)2N(CH2COO)2Na2 – 85 г/л; KSCN – 0.003 г/л; NiCl2·6H2O – 10 г/л; K3[Fe(CN)6] – 0.5 г/л; CH2O – 20 мл/л. Реакцию химического меднения проводили на воздухе при повышенной температуре (30–40°С) в течение 40 мин при постоянном перемешивании. После окончания меднения пластину подложки протирают под струей воды губкой или ватным тампоном для удаления рыхлого слоя меди, образующейся на необработанной лазером поверхности. Удаление меди на обработанной лазером поверхности указанным способом невозможно.
РЕЗУЛЬТАТЫ И ОБСУЖДЕНИЕ
При проведении лазерной обработки очень важно правильно подобрать фокусное расстояние линзы. Фокусировку лазера проводили по результатам абляции и химического меднения обработанной подложки. При низком расположении фокуса управляющей линзы происходит расплавление и термодеструкция подложки под нанесенным лаковым слоем. Лаковый слой в этом случае вспучивается. При проведении меднения на этих участках не происходит осаждения меди. При слишком высоком расположении фокуса обработка лазерным лучом приводит к потемнению верхнего слоя, на котором медь также не осаждается. При оптимальном положении фокуса управляющей линзы на поверхности лака, содержащего тальк, после обработки лазером образуется слой светло-серого, практически белого цвета, слегка шероховатый на ощупь.
Попытки применить схему прямого лазерного структурирования c использованием синтезированных полимеров в качестве связующих дает неудовлетворительную воспроизводимость результатов. Причем плохая воспроизводимость наблюдалась в случае лаков с разными минеральными наполнителями и разными связующими. Часто наблюдалось частичное омеднение обработанных лазером фигур (рис. 1б – омеднение произошло только по краям квадрата).
Рис. 1.
Результаты меднения обработанной лазером пластины: (а) до меднения; (б) после меднения. Связующее фенилэтилметакрилат : бутилметакрилат = 18 : 14. Наполнитель – оксид хрома(III). Толщина слоя лака l – 30 мкм, мощность лазера I – 12 Вт, расстояние между дорожками d – 0.02 мм, скорость луча $v$ – 2 м/с.
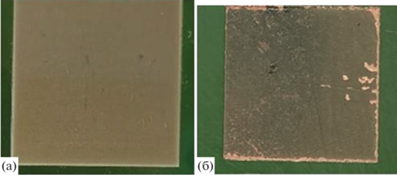
Оказалось, что результаты обработки лазером поверхности подложки сильно зависят не только от мощности лазера, скорости луча лазера, но и от траектории лазера и расстояния между дорожками, выжигаемыми лазерным лучом. Термодеструкция полимерного связующего под действием лазера определяется скоростью нагрева и диссипацией энергии в не нагретой области поверхностного слоя. Если при гравировке линий последние два параметра не имеют значения, то при обработке лазерным лучом по площади они оказываются решающими. На рис. 2а и рис. 2б показаны два вида штриховки лазером площадных деталей. Одна из них “последовательно параллельные линии” (рис. 2а) и вторая “по улитке” (рис. 2б).
Рис. 2.
Траектории лазерного луча при обработке площадных элементов: (а) последовательно-параллельные линии; (б) “по улитке” от периферии к центру.
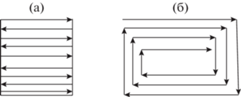
В случае со штриховкой последовательно-параллельными линиями (на рис. 2а) в обрабатываемой площади наблюдается равновесие между нагреванием и диссипацией энергии равномерно по всей фигуре, за исключением очень небольших по площади краевых областей. В случае штриховки “по улитке” диссипация энергии по краям фигуры будет максимальной, но будет уменьшаться по мере продвижения луча к центру, поскольку при равномернoм движении луча в центральной части параллельные лучи будут чаще проходить рядом друг с другом, по сравнению с периферией. В результате области прямоугольника прогреваются тем сильнее, чем ближе они к центральной части.
Для образца на рис. 3а скорость лазерного луча в два раза больше по сравнению со скоростью луча для образца на рис. 3б. То есть, плотность теплового потока на подложку для образца на рис. 3а в 2 раза меньше, чем для образца, представленного на рис. 3б. По-видимому, именно это приводит к тому, что на образце, представленном на рис. 3б, наблюдается частичное омеднение центральной части прямоугольника. Если же в условиях теплового потока для образца (рис. 3б) изменить штриховку с “по улитке” на параллельно последовательную, т.е. уменьшить диссипацию энергии, передаваемую лазером на обрабатываемую поверхность и, соответственно, приблизить условия абляции к условиям центральной части, то это приводит к полной активации поверхности.
Рис. 3.
Влияние параметров обработки лазером площадной фигуры на меднение. Слева – фотография омедненной после обработки лазером пластины АБС-пластика; (а) и (в) – обработка лазером “по улитке”; (б) – последовательно-параллельная обработка. Справа – косой штриховкой выделена область меднения. Связующее – сополимер фенилэтилметакрилат : бутилметакрилат = 18 : 14. Наполнитель – тальк МТ-ЭГС. Мощность лазера I – 4.5 Вт, расстояние между линиями луча лазера d – 5 мкм, скорость луча $v$ для (а) – 2 м/с, (б) и (в) – 1 м/с.
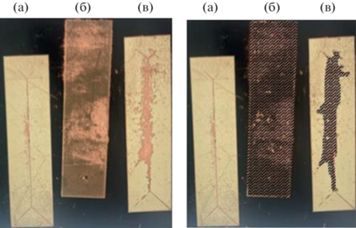
На рис. 3 представлен случай, когда мощности лазера недостаточно для полного обнажения минерального наполнителя подложки, обработанной “по улитке”, но вполне достаточно при обработке лазерным лучом последовательно-параллельными линиями. Если слегка увеличить интенсивность нагрева пластины АБС-пластика лазером, то наблюдается ситуация, когда обработка “по улитке” приводит к лучшим результатам при меднении, чем обработка последовательно параллельными линиями (рис. 4б по сравнению с рис. 4д). По-видимому, это происходит из-за того, что при перегреве пластины АБС-пластика выделяются продукты пиролиза, которые закрывают поверхность наполнителя, препятствуя осаждению активатора. При последовательно-параллельном ходе луча лазера (рис. 4г, 4д) показан описанный случай.
Рис. 4.
Влияние способа штриховки площадной фигуры лазером на качество химического меднения: (а)–(в) обработка лазером “по улитке”; (а) до меднения; (б), (в) после меднения. Косой штриховкой на (в) выделена зона покрытая слоем меди. (г), (д) – обработка последовательно-параллельными линиями: (г) до меднения; (д) после меднения. Полимер – метилметакрилат : бутилметакрилат = 2 : 1. Наполнитель – тальк Т-20. Мощность лазера I – 4.5 Вт, расстояние между линиями d – 10 мкм, скорость луча $v$ – 2 м/с.
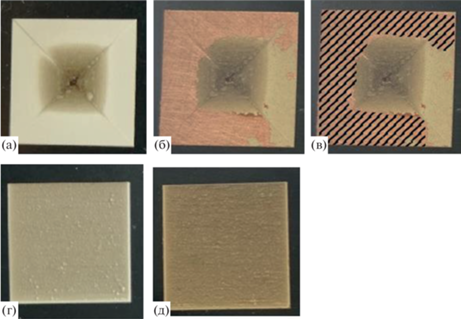
При этом после обработки “по улитке” (рис. 4а) меднится почти вся периферийная часть квадрата (рис. 4б). В центральной части квадрата нагрев избыточен – происходит образование черного налета. Хорошо видно, что темная окраска сгущается по мере движения луча лазера к центру. Таким образом, на рис. 4а наличествуют сразу три области возможного результата абляции – недогрев (правая часть рис. 4а), достаточный нагрев (левая часть рис. 4а) и перегрев (центральная часть рис. 4а). Применение последовательно-параллельной штриховки приводит к равномерному перегреву по всему квадрату (рис. 4г), на что указывает серый цвет обработанной лазером поверхности на рис. 4г, по сравнению с практически белой поверхностью образца на рис. 4а.
Применение всех указанных в экспериментальной части связующих на примере композитов с тальком показало плохую воспроизводимость результатов лазерной абляции по вышеуказанным причинам. При использовании всех систем несшитых полимерных связующих лака наблюдаются эффекты аналогичные показанным на рис. 3 и 4. При этом примерно в половине случаях после лазерной абляции меднения не происходит, т.е. можно констатировать плохую предсказуемость получения токопроводящих дорожек. На соотношение подаваемой лазером энергией и ее диссипацией подложкой, по-видимому, влияют не только траектория луча лазера, но и другие параметры: материал лака и наполнителя, а также характер распределения наполнителя в лаке, причем последнее зависит от способа нанесения лака и скорости седиментации. В случае, когда “перегрев” лазером можно сразу распознать по появлению темного цвета на обработанных лазером местах, то в случае с “недогревом” сделать это до проведения меднения сложнее.
Преодолеть эффект “перегрева” удалось применением сшитого связующего. Для этого стирол–метакрилатный сополимер, содержащий гидроксильные группы, сшивали с помощью олигомера гексаметилендиизоцианата (олигомер биуретного типа). Помимо стирол–метакрилатного сополимера, аналогичные положительные результаты показали метакрилатный сополимер фенилэтилметакрилат : бутилметакрилат : гидроксиэтилметакрилат = 19 : 11 : 7. Уменьшение содержания изоцианатного отвердителя приводит к уменьшению твердости покрытия.
Полученный сшитый лак оказался значительно менее подверженным вариациям энергетического параметра лазерного луча и способам нанесения рисунка. Устойчивое медное покрытие на обработанных пластинах наблюдалось при значениях параметров мощности от 3 до 8 Вт, скорости луча 2 м/с, при расстоянии между дорожками 10 мкм. Медное покрытие на обработанной лазером поверхности сшитого лака имело удельное сопротивление около 6 мОм см–1. Трехкратное последовательное меднение приводило к снижению удельного сопротивления полученного медного слоя до 1.4–1.6 мОм cм–1.
Поскольку указанный выше сшитый лак содержит в своем составе все компоненты несшитого лака (сополимеры стирола и метакрилатов, полиуретан), то можно заключить, что повышенная пригодность сшитого лака для лазерной абляции вызвана его неспособностью мигрировать на поверхность минерального наполнителя при нагревании лазерным лучом. Поверхность талька под действием лазерного луча, таким образом, после лазерной абляции остается непокрытой ни органическим полимером, ни продуктами его термодеструкции. В результате этого в местах, подвергнувшихся воздействию лазера, образуется поверхность, имеющая свойства отличные от свойств исходного лака и легко сорбирующая серебро, что, в свою очередь, приводит к прочному сцеплению минерального наполнителя с осаждаемой медью.
В качестве минерального наполнителя, кроме талька, успешно использовался селадонит, аквамарин, охра (оксиды железа), оксид хрома(III), шунгит. При использовании аквамарина осаждения меди на обработанную лазером поверхность не происходило. По-видимому, за исключением аквамарина, все перечисленные пигменты способны адсорбировать серебро, которое активирует поверхность для последующего химического меднения. Кроме того, эти эксперименты показывают, что нет необходимости применять минеральный наполнитель, поглощающий свет в области рабочей частоты лазера, как об этом неоднократно сообщали другие авторы до этого.
Размеры частиц минерального наполнителя сказываются на гладкости медного слоя. Для того чтобы добиться образования гладкого медного слоя необходимо уменьшить размеры частиц наполнителя. Для этого тальк взбалтывался в этилацетате и пропускался через стеклянный фильтр под вакуумом. Другим методом получения мелкодисперсного наполнителя является обработка суспензии механическим диспергатором. Ультразвуковой диспергатор оказался менее эффективным. Образовавшаяся суспензия довольно быстро осаждалась, в результате чего распыление приводило к неравномерному распределению минерального наполнителя на подложке. На скорость осаждения талька сильно влияет химический состав полимерного связующего. Полимер, содержащий кислотные группы, приводит к заметно большей стабильности суспензии, особенно в тяжелых растворителях типа тетрахлорэтана или тетрахлорэтилена.
Проведенная оптимизация состава раствора для химического меднения показала, что часто применяемые компоненты можно исключить из состава раствора. Наличие в растворе для меднения хлорида никеля, также часто рекомендуемого в литературе, не приводит к увеличению проводимости слоя меди (5.58 и 5.51 мОм см–1 в присутствии и без добавления хлорида никеля соответственно). Добавление в раствор гексацианоферрата калия и роданида калия также не привело к получению медного покрытия с высоким значением электропроводимости. Таким образом, значительно упрощается состав раствора для химического меднения по сравнению с составами, описанными в литературных методиках.
После меднения типичные значения удельного сопротивления составили 5.5–6.5 мОм см–1. Медный слой представляет собой покрытие красного или коричневого цвета, покрытый микробугорками (матовость) и легко разглаживается шпателем до появления характерного зеркального медного блеска. Удельное электрическое сопротивление при этом не изменяется, что указывает на то, что цвет и матовость не влияют на целевой параметр – удельную проводимость токопроводящего слоя.
ЗАКЛЮЧЕНИЕ
При нанесении токопроводящих дорожек на диэлектрик принципиально важны не только энергетические параметра лазера (мощность лазера, фокусировка, скорость перемещения луча), но и геометрические параметры обрабатываемой фигуры и ход луча лазера. Для получения готовых изделий, таким образом, нужно применять параметры лазерной абляции в зависимости от геометрии фигуры – узкие дорожки требуют большего подвода тепла лазером, чем площадные фигуры. После проведения лазерной абляции поверхность минерального наполнителя не должна иметь видимых темных пятен карбонизированных фрагментов связующего или подложки.
При проведении химического меднения важна доступность минерального наполнителя для адсорбции активаторов меднения. Как неполное удаление полимерного связующего, закрывающего центры активации (недогрев), так и покрытие центров активации продуктами пиролиза (перегрев), препятствуют осаждению меди на обработанную лазером поверхность.
В качестве связующего для метода прямого лазерного структурирования рекомендовано использовать стирол–метакрилатные сополимеры. Применение сшитых сополимеров метакрилатов резко уменьшает влияние перегрева поверхностного слоя подложки. Показано, что метод химического меднения можно упростить по сравнению с методом, описанным в литературе.
Показано, что целый ряд минеральных наполнителей, не имеющих высокое поглощение в области рабочей частоты лазера, можно использовать в качестве наполнителя для формирования токопроводящих дорожек с помощью лазера.
Список литературы
Adelaar H. A method for plating a copper interconnection circuit on the surface of a plastic device. Pat. 2267184 EP. 2010.
Heininger N. // J. Microwave. 2012. V. 6. № 1. P. 46.
Huske M., Kickeilhaim J., Muller J., Eber G. // Mater. Sci. 2002. V. 38. № 8. P. 51.
URL: https://www.lpkfusa.com/products/mid/articles_and_technical_papers/ сайт фирмы “LKPF”, 2021 (дата обращения: 23.08.2021).
Goosey M. Laser-activated dielectric material and method for using the same in an electroless deposition process. Pat. 0212632 GB. 2003.
Balzereit S., Proes F., Altstadt V., Emmelmann C. // Mater. Sci. 2018. V. 23. P. 347. doi: 10-1016/j-addma.2018.08.016
Schrauwen B.A.G. Polycarbonate Composition for laser direct structuring. Pat. 3898808A1 EP. 2020.
Yu Z., Wang J.H., Li Y., Li Y. // Polym. Eng. Sci. 2020.V. 60. № 4. P. 860. https://doi.org/10.1002/pen.25345
Kim K., Lee J., Ryua S. Kim J. // RSC Advances. 2018. V. 8. № 18. P. 9933. https://doi.org/10.1039/c8ra00967h
Jiratti T., Mavinkere R.S., Suchart S., Catalin I.P. // Polymers. 2020. V. 12. № 6. P. 1408. https://doi.org/10.3390/polym12061408
Xu H., Zhang J., Feng J., Zhou T. // Ind. Eng. Chem. Res. 2021. V. 60. № 24. P. 8821. https://doi.org/10.1021/acs.iecr.1c01668
Rytlewski P., Jagodzinski B., Karasiewicz I.N., Augustyn P., Kaczor D., Malinowski R., Szablinski K., Mazurkiewicz M., Moraczewski K. // Materials. 2020. V. 13. № 10. P 2224. https://doi.org/10.3390/ma13102224
Zhang J., Zhou T., Wen L., Zhang A. // ACS App. Mater. Inter. 2016. V. 8. № 49. P. 33999. https://doi.org/10.1021/acsami.6b11305
Zhang J., Zhou T., Wen Y. // ACS App. Mater. Inter. 2017. V. 9. № 10. P. 8996. https://doi.org/10.1021/acsami.6b15828
Пивоваров Д.А., Голубчикова Ю.Ю., Ильин А.П. // Изв. Томск. политех. университета // 2012. Т. 321. № 3. С. 11.
Дополнительные материалы отсутствуют.
Инструменты
Химия высоких энергий