Физикохимия поверхности и защита материалов, 2019, T. 55, № 3, стр. 287-294
Влияние добавок ацетонитрила в тетраборатный электролит на состав и морфологию ПЭО-слоев на титане
М. С. Васильева 1, 2, **, В. С. Руднев 1, 2, *, В. Г. Курявый 2
1 Дальневосточный федеральный университет
Владивосток, Россия
2 Институт химии ДВО РАН
Владивосток, Россия
** E-mail: marina_x@mail.ru
* E-mail: rudnevvs@ich.dvo.ru
Поступила в редакцию 07.02.2018
После доработки 11.12.2018
Принята к публикации 26.12.2018
Аннотация
Изучено влияние добавок ацетонитрила CH3CN к тетраборатному электролиту на состав и морфологию оксидных слоев на титане, формируемых методом плазменно-электролитического оксидирования. Состав и морфология покрытий исследованы методами электронной сканирующей микроскопии, энергодисперсионного и рентгенофазового анализов. Добавление 3 об. % ацетонитрила в состав тетраборатного электролита, не изменяя электрических параметров процесса, приводит к уменьшению пористости покрытий и включению в них до 20 ат. % азота. При добавлении ацетонитрила к тетраборатному электролиту с ацетатом марганца формируются оксидные слои с низким содержанием марганца и отсутствием азота. Поверхность Mn-содержащих оксидных слоев неоднородна, на поверхности наблюдаются отдельные участки, представляющие собой “листьевидные” структуры с повышенным содержанием марганца.
1. ВВЕДЕНИЕ
Одним из современных методов модифицирования поверхности металлов и сплавов является плазменно-электролитическое оксидирование (ПЭО). В настоящее время этот метод широко используют с целью получения многокомпонентных оксидных покрытий для защиты металлов от коррозии и механического износа [1, 2], перспективных для применения в катализе [3, 4], фотокатализе [5–7], в качестве сенсоров при мониторинге окружающей среды [8, 9] и магнитоактивных материалов [4, 10]. Функциональные свойства нанесенных методом ПОЭ оксидных покрытий на металлах определяются прежде всего их составом и морофологией, управлять которыми можно варьируя параметры процесса и состав электролита. В большинстве случаев в качестве электролита для ПЭО используют водные растворы неорганических соединений [1–12]. Применение в качестве электролита для ПЭО безводного ацетонитрила [13] или водных электролитов с добавлением различных органических соединений, в том числе, поверхностно-активных веществ (ПАВ) [14, 15], этанола [16], мочевины [17], метанола [18], глицерина [19] или ЭДТА [20–22] позволяет резко изменить состав и морфологию поверхности. Например, в [17] показано, что добавка мочевины в электролит на основе алюмината натрия повышает содержание азота в ПЭО-слое, уменьшает его толщину, увеличивает пористость, препятствует образованию α-оксида алюминия. Авторы [18] показали, что добавление CH3OH до 8 об. % в водные электролиты приводит к увеличению толщины покрытий и уменьшению среднего диаметра пор. Следствием добавления определенных количеств глицерина в силикатный электролит является уменьшение размеров пор и микротрещин, сглаживание рельефа покрытий, полученных на магниевом сплаве ZK60 [19]. Подобные результаты по формированию гладкой, малопористой поверхности ПЭО-покрытий на металлах описаны в работах [14] при добавлении ПАВ [22] – при добавлении ЭДТА.
Одним из интересных и малоизученных органических веществ, применяемых для формирования анодных пленок, является ацетонитрил CH3CN, который относится к диполярным апротонным растворителям. Высокая полярность нитрильной группы ацетонитрила предопределяет возможность адсорбции его на металлических поверхностях с последующим электрохимическим превращением [13, 23]. Например, в [13] в потенциодинамическом режиме при высоких напряжениях вплоть до 3000 В и плотностях тока до 10 мА/см2 в безводном ацетонитриле на титане получены кристаллические анодные пленки, включающие в состав оксид титана в модификациях рутил и анатаз, а также нитрид и карбид титана. Авторы работы [23] показали, что при низких напряжениях порядка 5 В и токах до 80 рА из ацетонитрила на металлических поверхностях осаждаются тонкие полимерные пленки, при синтезе которых, по мнению авторов, протекают процессы, подобные явлению пробоя. В обоих случаях электрохимический синтез покрытий проводили в однокомпонентном безводном ацетонитриле. Однако вследствие хорошей растворимости ацетонитрила в воде, его способности образовывать комплексные соединения по донорно-акцепторному механизму с солями переходных металлов [24–26], добавление ацетонитрила к водным электролитам различного состава может оказывать влияние на механизм и свойства формируемых методом ПЭО покрытий. В то же время этот вопрос, ранее, насколько нам известно, в научной литературе не рассматривался.
В данной работе представлены результаты влияния добавок ацетонитрила в водный электролит на закономерности плазменно-электролитического формирования оксидных слоев на титане, их состав, морфологию поверхности и каталитическую активность в окислении СО.
2. ЭКСПЕРИМЕНТАЛЬНАЯ ЧАСТЬ
Электроды для плазменно-электролитического оксидирования изготавливали из титановой фольги марки ВТ1 0 в виде пластинок размером 2.5 × 2.5 см2. Образцы химически полировали в смеси концентрированных кислот HF : HNO3 = = 1 : 3 при 60–80°С в течение 2–3 с, промывали дистиллированной водой и сушили на воздухе.
Ячейка для ПЭО − стакан из термостойкого стекла объемом 1 л. Оксидные покрытия формировали гальваностатически на погруженном в электролит анодно-поляризованном титане. Противоэлектродом (катодом) служил змеевик, выполненный из полой (диаметр 0.5 см) трубки из нержавеющей стали. Для охлаждения электролита через полый змеевик пропускали холодную воду. Электролит в стакане перемешивали при помощи магнитной мешалки. В качестве источника тока использовали тиристорный агрегат ТЕР4-63/460Н с однополярной импульсной формой тока.
Обработку осуществляли в гальваностатическом режиме при эффективной плотности тока i = 0.1 А/см2 в течение 10 мин или 0.2 А/см2 в течение 5 мин. После ПЭО образцы ополаскивали дистиллированной водой и сушили на воздухе при комнатной температуре.
Для приготовления электролитов использовали коммерческие реактивы Na2B4O7 · 10H2O (х. ч.), Mn(CH3COO)2 · 4H2O (ч.), CH3CN (х. ч.), и дистиллированную воду. Оксидирование проводили в водных электролитах, содержащих 0.1 М Na2B4O7 или 0.1 М Na2B4O7 + 10 г/л Mn(CH3COO)2, в том числе с добавлением 1–7 об. % CH3CN.
Фазовый состав определяли методом рентгенофазового анализа (РФА) на дифрактометре D8 ADVANCE (Германия) в CuKa-излучении. Идентификация соединений, входящих в состав исследуемых образцов, выполнена в автоматическом режиме поиска EVA с использованием банка данных (PDF-2).
Морфологию поверхности изучали с помощью сканирующего электронного микроскопа (СЭМ) Hitachi S-5500 с энергодисперсионным спектрометром UltraDry (Therma Scientific, USA).
Для оценки каталитической активности образцов в реакции окисления СО в СО2 использовали проточную каталитическую установку BI-CATflow производства Института катализа СО РАН (г. Новосибирск). В кварцевый реактор объемом 3 см3 помещали 2 титановые пластинки общей геометрической площадью 25 см2 с нанесенным марганецсодержащим покрытием. Исходная реакционная смесь состояла из 79% Ar, 20% O2, 1% CO. Скорость потока газа − 70 мл/мин. Измерения выполнены при температурах от комнатной до 500°С. Скорость изменения температуры в реакторе − 10°С мин–1. Состав газовой смеси определяли через 30 мин после установления в реакторе заданной температуры. Газообразные компоненты анализировали с помощью газоанализатора ПЭМ-2М производства Института катализа СО РАН.
3. РЕЗУЛЬТАТЫ И ИХ ОБСУЖДЕНИЕ
3.1. Влияние добавок ацетонитрила в тетраборатный электролит
На рис. 1 приведены кривые изменения напряжения U, В на электродах от времени оксидирования t, мин при формировании оксидных слоев на титане в тетраборатном электролите без добавления и с добавлением ацетонитрила.
Рис. 1.
Зависимость напряжения U от времени формирования t покрытий в электролитах, содержащих 0.1 М Na2B4O7 и CH3CN об. %: 1 − 0; 2 − 1, 3 − 3. Плотность тока формирования i = 0.1 А/см2.
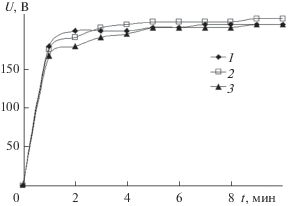
Во всех случаях в первые минуты ведения процесса наблюдается быстрый рост напряжения на электродах, которое в течение ∼4−6 мин достигает значений 200–210 В и далее, за время ведения процесса до 10 мин, меняется незначительно. В целом вид кривых U = f(t) одинаков для всех исследуемых электролитов и не зависит от добавок ацетонитрила.
Согласно данным элементного анализа на поверхности покрытий, сформированных в тетраборатном электролите (табл. 1), обнаружены кислород и титан в соотношении 1.6, что свидетельствует об образовании оксида титана. В тетраборатном электролите с ацетонитрилом формируются покрытия, содержащие в поверхностной части дополнительно углерод и значительное количество азота. Последнее, очевидно, обусловлено сорбцией на поверхности титана молекул ацетонитрила с участием неподеленной электронной пары азота нитрильной группы с последующим их термопревращением в ходе ПЭО и миграцией атомов углерода и азота вглубь растущей оксидной пленки. Внедрение значительного количества азота и углерода в оксидную пленку наблюдали также авторы [13] при ведении процесса в чистом ацетонитриле.
Таблица 1.
Элементный и фазовый составы покрытий, сформированных в 0.1 М растворе Na2B4O7 с добавлением CH3CN. Плотность тока формирования i = 0.1 А/см2
№ | С (CH3CN), об. % |
Фазовый состав | Элементный состав, ат. % | |||
---|---|---|---|---|---|---|
O | Ti | C | N | |||
1 | 0 | TiO2 (анатаз, рутил) | 60.9 | 39.1 | – | – |
2 | 1 | TiO2 (анатаз, рутил) | 50.0 | 17.9 | 6.7 | 25.4 |
3 | 3 | TiO2 (анатаз, рутил) | 51.5 | 19.7 | 5.6 | 23.2 |
С помощью метода электронной микроскопии установлено, что добавление ацетонитрила в тетраборатный электролит оказывает влияние на морфологию формируемых покрытий, рис. 2. В тетраборатном электролите с добавлением 3 об. % ацетонитрила образуются более сглаженные покрытия с меньшим размером пор. Предположительно, ацетонитрил ведет себя подобно молекулам ПАВ. По предположению авторов работы [14] адсорбция молекул ПАВ на поверхность анода приводит к изменению поверхностного натяжения на границе раздела газ/жидкость, жидкость/твердое тело и как следствие к улучшению условий смачивания раствором электролита поверхности растущего оксида, уменьшению размеров газовых пузырей, отрывающихся в ходе анодирования от поверхности и соответственно уменьшению диаметров устьев пор на поверхности.
Рис. 2.
СЭМ-снимки поверхности покрытий, сформированных в 0.1 М растворе Na2B4O7 (а, б) и в 0.1 М Na2B4O7 с добавлением 3 об. % CH3CN (в, г). Плотность тока формирования i = 0.1 А/см2.
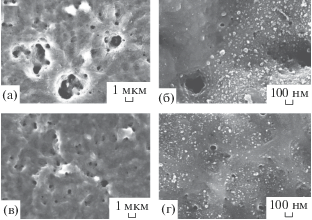
Таким образом, добавление небольших количеств ацетонитрила в тетраборатный электролит, не влияя на вид формовочных кривых, приводит к заметному изменению морфологии и элементного состава формируемых покрытий.
3.2. Влияние добавок ацетонитрила в тетраборатный электролит с ацетатом марганца
Дополнительное введение в тетраборатный электролит ацетата марганца приводит к формированию слоев, содержащих во внешней части наряду с рутилом оксиды марганца Mn2O3 и Mn3O4 [16]. Количество марганца в поверхностном слое зависит от условий формирования и концентрации ацетата марганца в электролите. Полученные марганецсодержащие структуры на титане проявляют каталитическую активность в реакции окисления СО в СО2 в области температур 250–350°С. Каталитическая активность определяется количеством марганца в слоях, его распределением по поверхности и морфологией поверхности.
Добавление к электролиту этанола, способствует сглаживанию поверхности и, возможно, приводит к формированию в составе покрытий оксидов с разной степенью окисления марганца (за счет создания более восстановительной среды на аноде) [16].
В данном разделе приведены данные по влиянию добавок ацетонитрила в электролит с тетраборатом натрия и ацетатом марганца на образование, состав, морфологию поверхности формируемых покрытий и их каталитическую активность в окислении СО в СО2.
На рис. 3 приведены зависимости U = f(t) для процессов образования покрытий в электролитах, содержащих 0.1 М Na2B4O7, 10 г/л Mn(CH3COO)2 и ацетонитрил. Добавление ацетата марганца к исходному тетраборатному электролиту приводит к выпадению белого аморфного осадка гидроксида марганца и снижению более чем в два раза (от ~200 до 75 В) напряжению на электродах в процессе формирования покрытия, (сравни рис. 1 и рис. 3а, 3б, кривые 1). Последнее по-видимому связано с изменением ионного состава электролита. При этом формируются темно-коричневые покрытия с неудовлетворительной адгезией к титановой основе. Добавление ацетонитрила от 1 до 7 об. % к водному тетраборатному электролиту с ацетатом марганца приводит к постепенному увеличению напряжения формирования до 130 В. В водно-органических электролитах образуются светло-коричневые покрытия, имеющие хорошее сцепление с титановой основой. Увеличение плотности тока от 0.1 до 0.2 А/см2 еще больше повышает напряжение формирования и адгезию формируемых марганецсодержащих покрытий к металлу основы.
Рис. 3.
Зависимость напряжения U от времени формирования t покрытий в электролитах, содержащих 0.1 М Na2B4O7, 10 г/л Mn(CH3COO)2 и CH3CN. (а) i = = 0.1 А/см2, С (CH3CN), об. %: 1 − 0; 2 − 1, 3 − 3, 4 − 5; (б) i = 0.2 А/см2, С (CH3CN), об. %: 1 − 0; 2 − 3, 3 − 5, 4 − 7.
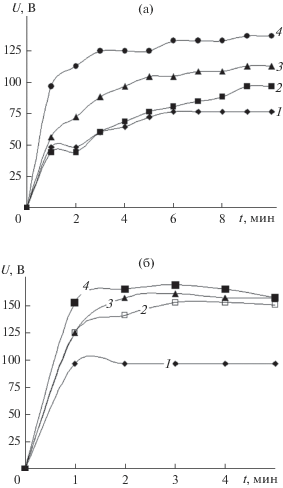
Таким образом, напряжение формирования в ацетатно-тетраборатном электролите увеличивается как с повышением плотности тока, так и в результате добавления ацетонитрила в электролит. Одновременно это позволяет формировать более равномерные с высокой адгезией к основе покрытия.
Из табл. 2 и 3 видно, что добавление ацетонитрила к тетраборатному электролиту с ацетатом марганца (раствору с аморфным осадком гидроксида марганца) приводит к формированию покрытий с более низким содержанием марганца и более высоким содержанием титана. Следует также отметить, что в электролитах, содержащих аморфный осадок (дисперсные частицы гидроксида марганца) и ацетонирил, формируются покрытия, включающие в состав углерод, но не содержащие азот. Данный факт свидетельствует о том, что добавленный в тетраборатный электролит с ацетатом марганца ацетонитрил взаимодействует с дисперсными частицами гидроксида марганца, приводя к выше описанным последствиям. Можно предположить, что в результате координации ацетонитрила к иону марганца за счет неподеленной электронной пары атома азота происходит образование нитрильных комплексов марганца СН3–CN : Mn(OH)2. Таким образом меняется состав и как следствие заряд и подвижность дисперсных частиц. Последнее приводит к тому, что дисперсным частицам сложнее достигать поверхности анода, что объясняет уменьшение марганца в составе ПЭО-слоев. Кроме того, вследствие связывания ацетонитрила в комплексы, он не может взаимодействовать с поверхностью анода, что и объясняет отсутствие азота в составе ПЭО-слоев. Таким образом, в результате изменения природы и количества дисперсных частиц, попадающих на поверхность анода, изменяются электрические параметры процесса и свойства образующегося покрытия.
Таблица 2.
Элементный и фазовый составы покрытий на титане, сформированных в электролите, содержащем 0.1 М Na2B4O7, 10 г/л Mn(CH3COO)2 и CH3CN. Плотность тока формирования i = 0.1 А/см2
№ | С (CH3CN), об. % |
Фазовый состав | Элементный состав, ат. % | ||||
---|---|---|---|---|---|---|---|
Mn | Ti | Na | O | C | |||
1 | – | MnO2 (следы) | 46.0 | 0.0 | 2.2 | 41.4 | 10.4 |
2 | 1 | TiO2 (анатаз, рутил) | 34.7 | 1.0 | 1.2 | 50.1 | 12.7 |
3 | 3 | TiO2 (анатаз, рутил) | 4.6 | 26.9 | 0.0 | 64.3 | 4.2 |
4 | 6 | TiO2 (анатаз, рутил) | 6.3 | 19.2 | 2.0 | 66.5 | 5.9 |
Таблица 3.
Элементный и фазовый составы покрытий на титане, сформированных в электролите, содержащем 0.1 М Na2B4O7, 10 г/л Mn(CH3COO)2 и CH3CN. Плотность тока формирования i = 0.2 А/см2
№ | С (CH3CN), об. % | Фазовый состав | Элементный состав, ат. % | |||||
---|---|---|---|---|---|---|---|---|
Mn | Ti | Na | O | C | N | |||
1 | – | Mn2O3 | 30.3 | 3.4 | 0.6 | 42.9 | 22.5 | – |
2 | 3 | TiO2 (анатаз, рутил) | 5.5 | 20.4 | 0.4 | 60.2 | 13.5 | – |
3 | 5 | TiO2 (анатаз, рутил) | 9.7 | 19.4 | 0.8 | 63.2 | 6.9 | – |
4 | 6 | TiO2 (анатаз, рутил) | 7.3 | 27.1 | 0.6 | 53.1 | 11.9 | – |
5 | 7 | TiO2 (анатаз, рутил) | 5.5 | 20.2 | 0.8 | 65.5 | 4.8 | 3.1 |
На снимках СЭМ видно (рис. 4), что добавление ацетата марганца к тетраборатному электролиту приводит к формированию неоднородных поверхностей, морфология которых зависит от условий оксидирования. При получении пленок в тетраборатно-ацетатном электролите в течение 10 мин при i = 0.1 А/см2 образуются неоднородные покрытия с чередующимися гладкими участками и участками, покрытыми множеством гранул (рис. 4а). Большее увеличение позволило обнаружить два вида наноструктур на поверхности этих покрытий – гранулообразные частицы, ассоциированные в более крупные микроструктуры (рис. 4б) и упорядоченные “листьевидные” сетчатые наноструктуры (рис. 4в). При получении в тетраборатно-ацетатном электролите в течение 5 мин при i = 0.2 А/см2 образуются неоднородные покрытия, покрытые множеством гранул (рис. 4г). Наноструктурные объекты, подобные покрытиям, сформированных при более низкой плотности тока, не обнаружены (рис. 4д, 4е).
Рис. 4.
СЭМ-снимки поверхности покрытий, сформированных в электролите, содержащем 0.1 М Na2B4O7 и 10 г/л Mn(CH3COO)2. Плотность тока формирования: i = 0.1 А/см2, t = 10 мин (а–в) и 0.2 А/см2, t = 5 мин (г–е).
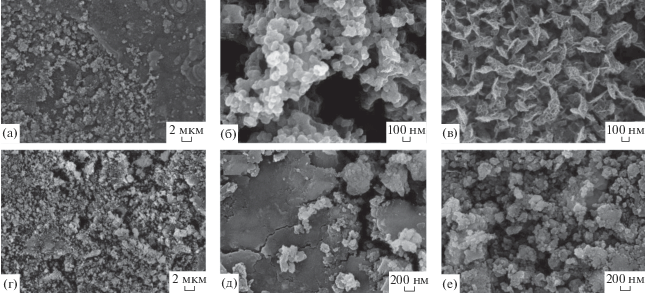
Введение ацетонитрила в тетраборатно-ацетатный электролит во всех случаях приводит к заметному изменению морфологии формируемых покрытий. Как и в случае с тетраборатным электролитом, поверхность становится более гладкой (сравни снимки рис. 4а и рис. 5а, рис. 4г и рис. 5г).
Рис. 5.
СЭМ-снимки поверхности покрытий, сформированных в электролите, содержащем 0.1 М Na2B4O7, 10 г/л Mn(CH3COO)2 и CH3CN, об. %: 3 (а–е); 5 (ж–и); 7 (к–м). Плотность тока формирования: i = 0.1 А/см2 (а–в) и 0.2 А/см2 (г–м).

Более детальное исследование поверхности позволило обнаружить на поверхности всех покрытий кристаллоподобные наноструктурированные объекты, локализованные на отдельных участках поверхности, рис. 5б, 5в, 5д–5м. Объекты напоминают капли (или “ежей”) с развитой структурой в виде листьевидных образований. Отметим, что “листьевидные” образования наблюдали на поверхности покрытий, полученных и в отсутствие в электролите ацетонитрила, рис. 4в). Эти факты позволяют предположить, что образование кристаллоподобных локально расположенных на поверхности объектов связано с попаданием в эти участки дисперсных частиц гидроксида марганца не связанных с аценонитрилом. Согласно данным элементного анализа области, содержащие наноструктуры (область 1, рис. 6), включают ат. %, 11.2 Mn, 18.5 Ti, 56.2 O, 14.1 C, соседние участки (область 2, рис. 6) обеднены марганцем и содержат ат. %, 6.3 Mn, 26.3 Ti, 58.6 O, 7.8 С, 1.1 Na.
Рис. 6.
СЭМ-снимок поверхности покрытия, сформированного в электролите, содержащем 0.1 М Na2B4O7, 10 г/л Mn(CH3COO)2 и 5 об. % CH3CN. Плотность тока формирования: i = 0.2 А/см2.
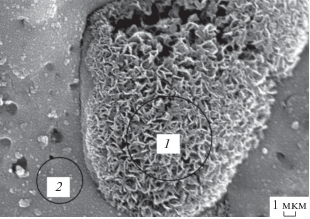
Результаты исследования каталитической активности сформированных марганецсодержащих оксидных слоев в реакции окисления СО в СО2 приведены на рис. 7. Степень конверсии СО в СО2 при 400°С в присутствии образцов, сформированных в тетраборатном электролите с аморфным осадком гидроксида марганца при плотности тока 0.1 А/см2, составляет 98.8% (рис. 7, кривая 1), тогда как покрытия, сформированные электролите с добавлением ацетонитрила, не активны в исследуемой реакции (рис. 7, кривая 2). Таким образом следствием добавления ацетонтрила к тетраборатному электролиту с ацетатом марганца является изменение морфологии поверхности покрытий, значительное снижение содержания в них марганца и, как следствие, потеря образцами активности в окислении СО в СО2.
ЗАКЛЮЧЕНИЕ
Таким образом, добавление ацетонитрила в электролит с тетраборатом натрия или с тетраборатом и ацетатом марганца приводит к сглаживанию поверхности формируемых ПЭО-покрытий и увеличению из адгезии к металлу основы. Добавление 3 об. % ацетонитрила в состав тетраборатного электролита, не изменяя электрических параметров процесса, сопровождается включением в состав покрытий до 20 ат. % азота. В электролите с тетраборатом и ацетатом марганца ацетонитрил меняет механизм встраивания марганца в покрытия в результате взаимодействия с дисперсными частицами гидроксида марганца, изменяя их заряд и подвижность. По-видимому, добавление ацетонитрила в электролиты-суспензии может уменьшать осаждение в ПЭО-покрытия гидроксидов различных переходных металлов. Поверхность Mn-содержащих оксидных слоев неоднородна, на поверхности наблюдаются отдельные участки, представляющие собой “листьевидные” структуры с повышенным содержанием марганца.
Работа частично поддержана грантом РФФИ № 18-03-00418.
Список литературы
Ракоч А.Г., Дуб А.В., Гладкова А.А. Анодирование легких сплавов при различных электрических режимах. Плазменно-электролитическая нанотехнология. М.: “Старая Басманная”, 2012. 496 с.
Суминов И.В., Белкин П.Н., Эпельфельд А.В. и др. Плазменно-электролитическое модифицирование поверхности металлов и сплавов: в 2-х томах Т. II / под общ. ред. Суминова И.В. М.: Техносфера, 2011. 512 с.
Patcas F., Krysmann W. // Appl. Catal. A: Gen. 2007. V. 316. P. 240.
Rudnev V.S., Lukiyanchuk I.V., Vasilyeva M.S. et al. // Surf. Coat. Technol. 2016. V. 307. P. 1219.
Salami N., Bayati M.R., Golesta ni-Fard F. et al. // Mater. Res. Bull. 2012. V. 47. P. 1080.
Oh H.-J., Chi Ch.-S. // Mater. Lett. 2012. V. 86. P. 31.
Petrović S., Stojadinović S., Rožić Lj. et al. // Surf. Coat. Technol. 2015. V. 269. P. 250.
Vasilyeva M.S., Rudnev V.S., Arefieva O.D. et al. // Int. J. Environ. Anal. Chem. V. 96. P. 1128.
Marinina G.I., Vasilyeva M.S., Lapina A.S. et al. // J. Electroan. Chem. 2013. V. 689. P. 262.
Rudnev V.S., Adigamova M.V., Lukiyanchuk I.V. et al. // J. Alloys Compd. 2015. V. 618. P. 623.
Черненко В.И., Снежко Л.А., Папанова И.И. Получение покрытий анодно-искровым электролизом. Л.: Химия, 1991. 128 с.
Yerokhin A.L., Nie X., Leyland A. et al. // Surf. Coat. Technol. 1999. V. 122. P. 73.
Schlottig F., Schreckendach J., Dietrich D. et al. // Appl. Surf. Sci. 1995. V. 90. P. 129.
Guo H., An M. // Thin Solid Films. 2006. V. 500. P. 186.
Васильева М.С., Руднев В.С., Коротенко И.А. и др. // Физикохимия поверхности и защита материалов. 2012. Т. 48. № 1. С. 87.
Rudnev V.S., Vasilyeva M.S., Kondrikov N.B. et al. // Appl. Surf. Sci. 2005. V. 252. P. 1211.
Yeh S.-C., Tsai D.-S., Guana S.-Y. et al. // Appl. Surf. Sci. 2015. V. 356. P. 135.
Yongyi H., Li C., Zongcheng Y., Yalei Z. et al. // Plasma Sci. Technol. 2015. V. 17. P. 761.
Qiu Z., Zhang Y., Li Y. et al. // RSC Adv. 2015. V. 5. P. 63 738.
Васильева М.С., Руднев В.С., Устинов А.Ю. и др. // Журн. прикл. химии. 2010. Т. 83. № 3. С. 435.
Rogov A.B. // Mater. Chem. Phys. 2015. V. 167. P. 136.
Kamil M.P., Kaseem M., Ko Y.G. // Scientific Reports 2017. V. 7. Article number: 44458.
Cassidy J., Khoo B.S., Pons S.J. // J. Phys. Chem. 1985. V. 89. P. 3933.
Дюмаева И.В., Рекута Ш.Ф., Егоров Н.А. // Башкирский химический журнал. 2009. Т. 16. № 2. С. 178.
Мовсум-заде Н.Ч., Дюмаева И.В., Поляков А.Д. // Башкирский химический журнал. 2008. Т. 15. № 3. С. 87.
Зильберман Е.Н. Реакции нитрилов. М.: Химия, 1972. 448 с.
Дополнительные материалы отсутствуют.
Инструменты
Физикохимия поверхности и защита материалов