Физикохимия поверхности и защита материалов, 2019, T. 55, № 4, стр. 402-407
Структурно-фазовое состояние и термоциклическая стабильность термобарьерных покрытий Zr–Si–O, осажденных микроплазменным методом на медной подложке
Т. И. Дорофеева 1, *, Т. А. Губайдулина 1, Б. П. Гриценко 1, 2, В. П. Сергеев 1, 2
1 Институт физики прочности и материаловедения СО РАН
634055 Томск, пр. Академический, 2/4, Россия
2 Национальный исследовательский Томский политехнический университет
634050 Томск, пр. Ленина, 30, Россия
* E-mail: dorofeevatomsk@rambler.ru
Поступила в редакцию 22.05.2018
После доработки 23.10.2018
Принята к публикации 15.11.2018
Аннотация
В данной работе показано получение термобарьерных покрытий на основе оксида циркония. Предложена поэтапная обработка медной подложке с целью получения на ней слоистого оксидного термобарьерного покрытия. Поверхность образца наноструктурируется, затем послойно осаждается титан (вакуумно-дуговым методом), затем цирконий (магнетронным методом), далее цирконий преобразуется в диоксид циркония микроплазменным методом. Сформированные оксидно-керамические покрытия содержат элементы раствора по результатам элементного анализа и диоксид циркония в тетрагональной и моноклинной модификациях по результатам рентгено–структурного анализа. Проведено исследование термоциклической стабильности и выявлено, что увеличение времени микроплазменной обработки до определенного значения положительно влияет на термоциклические свойства полученного слоистого материала, и он способен выдержать более 90 циклов без серьезных разрушений поверхностного слоя.
ВВЕДЕНИЕ
Диоксид циркония является одним из перспективных керамических материалов, привлекающих пристальное внимание исследователей [1, 2]. Он успешно применяется для высокотемпературной (до 2770 К) теплоизоляции [3]. Благодаря низкой теплопроводности и отличной химической стойкости в сочетании с большой твердостью и прочностью ZrO2 используют для защиты от коррозии и эрозии деталей турбореактивных (ТРД) и газотурбинных (ГТД) авиационных и жидкостных ракетных двигателей (ЖРД) [4, 5].
Уровень свойств прочности и вязкости диоксида циркония сильно меняется при его частичной стабилизации в результате введения легирующих добавок. В качестве таких добавок применяют оксиды иттрия, магния, кальция и других соединений [6]. Степень стабилизации ZrO2 зависит от вида стабилизатора, его количества, температуры стабилизирующего обжига, количества примесей, содержащихся в диоксиде циркония, и некоторых других факторов [7].
Нанесение диоксида циркония в качестве покрытия на поверхность металлических материалов осуществляется различными методами, в том числе напылением. Так, для повышения эксплуатационной температуры детали горячего тракта ТРД и ГТД защищают термобарьерными покрытиями на основе оксида циркония, легированного различными элементами. Для этого обычно применяют электронно-лучевые и газотермические методы напыления покрытий [8–10]. Однако некоторые проблемы технической реализации этих способов обработки деталей пока не позволяют поднять температуру эксплуатации до требуемых развитием авиакосмической техники пределов. Поэтому актуальным является поиск альтернативных методов получения термобарьерных покрытий.
Одним из перспективных способов обработки поверхности с целью получения наноструктурных оксидно-керамических покрытий, отличающихся повышенными эксплуатационными характеристиками, является метод микроплазменного оксидирования (МПО) [11, 12]. Он позволяет превращать за относительно короткий период времени поверхностный слой таких металлов как цирконий, титан, алюминий и другие вентильные металлы в тугоплавкие твердые оксиды. Поскольку для изготовления деталей горячего тракта ТРД и ГТД используются жаропрочные никелевые и интерметаллидные сплавы [4], а для сопел ЖРД – медные сплавы [5], то перед процессом МПО требуется нанесение металлического слоя циркония или его сплавов. Эта промежуточная операция не представляет технологических сложностей и выполняется на предварительной стадии подготовки поверхности деталей.
МПО представляет собой электрохимический процесс, который протекает при высокой напряженности электрического поля и сопровождается образованием микроплазменных разрядов и микрообластей с высоким давлением за счет образующихся газов, это приводит к протеканию высокотемпературных химических превращений, и транспорту вещества в дуге [11]. При высоковольтном импульсном воздействии на границу раздела двух сред раствор электролита – металл формируются микроплазменные оксидно-керамические нанопористые покрытия на поверхности металла, состоящие из оксидов материала основы и элементов раствора электролита [11].
Так, при микроплазменном оксидировании в растворе цирконий гидролизуется, образующийся продукт подвергается термопревращению с образованием диоксида циркония (смесь моноклинной и тетрагональной модификаций), с которым соосаждаются оксиды элементов электролита (продукт окисления), что приводит к формированию композитных ZrO2–МеnOm покрытий [12, 13].
Целью настоящей работы является изучение процесса высокоскоростного формирования многослойных нанокомпозитных покрытий на основе оксида циркония методом микроплазменного оксидирования циркониевого слоя, нанесенного на медную подложку (после ее наноструктурирования потоком ионов титана и нанесением титанового подслоя), а также исследование термоциклической стойкости и структурно-фазового состояния таких многослойных термобарьерных покрытий.
МАТЕРИАЛЫ И МЕТОДИКА ЭКСПЕРИМЕНТА
В качестве подложек использовались пластины размером 20 × 30 × 3 мм, вырезанные из медного листа марки М1. Рабочую поверхность образцов шлифовали и полировали до величины шероховатости Ra = 0.16 мкм. Далее на нее последовательно осаждали вакуумно-дуговым методом – слой титана ВТ-1-0 и магнетронным методом – слой циркония Э110. Перед осаждением титана поверхностный слой медной подложки подвергали бомбардировке ионами титана при подаче потенциала смещения на подложку 900 В, при этом происходило его наноструктурирование [14]. Процесс обработки подложки и осаждения металлического покрытия проводили с помощью вакуумной установки UVN-05MD “Quantum” (Techimplant Ltd.) [15], оснащенной круговым планарным магнетроном мощностью до 3 кВт с циркониевой мишенью и вакуумно-дуговым источником ионов титана с плотностью ионного тока до 5 мА/см2. Питание магнетрона осуществлялось от импульсного источника с частотой повторения импульсов тока до 50 кГц и амплитудой до 5 А. Толщина осаждаемых слоев покрытий во всех исследуемых случаях была одинаковой: титана – 40 мкм, циркония – 40 мкм. Происходящий при этом процесс наноструктурирования поверхностного слоя подложки приводит к изменению его морфологии, структурно-фазового состояния и комплекса физико-механических свойств. В результате адгезия осаждаемых наноструктурных покрытий повышается в 2–5 раз, а термоциклическая стойкость – в 1.5–2 раза [14].
Микроплазменная обработка (МПО) полученных образцов с поверхностным слоем циркония проводилась с помощью источника питания “КОРУНД М1”, предназначенного для формирования пористых наноструктурных оксидных покрытий на вентильных металлах импульсными биполярными токами под действием высокоэнергетических потоков, локализованных в нанослоях на границе раздела фаз [11, 16]. Использовался импульсный режим работы с трапецеидальной формой импульса напряжения при длительности 200 мкс, частоте 50 Гц, задающем напряжении 350 В, времени нанесения покрытий до 10 мин [17]. Процесс шел в ванне со стандартным раствором силикатного электролита (0.6 г/л гидроокись натрия и 70 г/л метасиликата натрия) [13].
Полученные образцы после МПО были исследованы на сканирующем электронном микроскопе LEO EVO-50XVP, оснащенного спектрометрами для элементного анализа Oxford INCA Energy X-act и INCA Wave. Структурно-фазовое состояние покрытий исследовали методом рентгеноструктурного анализа (РСА) дифрактограмм, полученных с помощью рентгеновского дифрактометра ДРОН-7, ПАО “Буревестник”. Для определения термоциклической стойкости образцы нагревали в муфельной печи до 1000°С в течение 90 с с последующим резким охлаждением до комнатной температуры в воде, после каждого цикла проводилась фотосъемка поверхности образца со стороны покрытия с помощью металлографического микроскопа Axiovert 25 CA, Zeiss. Испытания прекращались, когда отслаивалось более 50% покрытия. Количество циклов, которое выдерживали покрытия в ходе этих испытаний, принималось за величину их термоциклической стойкости (ТЦС).
После проведения термоциклических испытаний образцов было проведено исследование морфологии оставшегося после термоциклических испытаний покрытия и определен химический состав поверхностного слоя методом ИК-спектрометрии на ИК-Фурье спектрометре Nicolet 5700.
РЕЗУЛЬТАТЫ И ИХ ОБСУЖДЕНИЕ
При микроплазменной обработке образцов в стандартном электролите процесс формирования покрытия протекает равномерно, оксидный слой образуется фактически за шесть минут. Далее процесс выходит на завершающую стадию, и продолжение его нецелесообразно. Происходит быстрый нагрев электролита, при этом не происходит интенсивного газовыделения. После снятия нагрузки напряжение падает относительно быстро, что может говорить о наличии в покрытии сквозных пор [18]. В результате при обработке в стандартном электролите получается светло-серое однородное покрытие.
На рис. 1 и 2 показаны электронно-микроскопические изображения морфологии поверхности образцов после формирования микроплазменного оксидно-керамического покрытия. На поверхности отсутствуют мелкодисперсные образования, покрытие однородно. При МПО в течение 6 мин (рис. 1) формируются пористые покрытия с малыми размерами пор от 100 до 400 нм и сеткой мельчайших трещин (ширина трещин около 140 нм).
Рис. 1.
Морфология поверхности оксидно-керамического микроплазменного покрытия. Время обработки 6 мин (образец № 1).
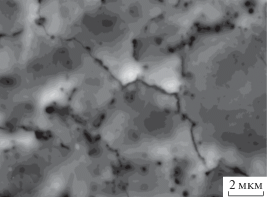
Рис. 2.
Морфология поверхности оксидно-керамического микроплазменного покрытия. Время обработки 10 мин (образец № 2).
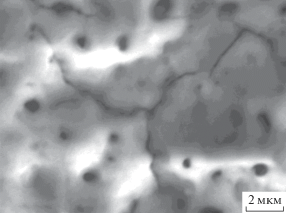
С увеличением времени обработки до 10 мин (рис. 2) размер пор возрастает (средний размер пор около 350 нм), но уменьшается их количество, происходит заращивание образующихся мелких пор, трещины сохраняются (ширина около 100 нм).
При исследовании качественного и количественного элементного состава покрытий, выявлено, что концентрация элемента циркония составляет 21.09 ат. % для времени микроплазменной обработки 6 мин и 15.48 ат. % для времени 10 мин. Элемент кремний в покрытии обнаруживается в концентрациях 6.75 и 11.25 ат. % для времени микроплазменной обработки 6 и 10 мин соответственно. С увеличением времени обработки возрастает количество атомов элементов, входящих в состав покрытия из раствора, а именно кремния. Т.е. в состав покрытия наряду с диоксидом циркония входят соединения кремния (до 11.25%), соединения титана в поверхностном слое не диагностируются, что свидетельствует об отсутствии пробоя пленки напыленного циркония в период микроплазменного оксидирования образца.
Основным оксидом является оксид циркония. Этот результат подтверждается данными рентгеноструктурного анализа (РСА) (рис. 3).
При помощи РСА выявлено наличие в поверхностном слое образца (верхнем слое) моноклинной и тетрагональной фаз ZrO2. Моноклинная фаза составила 28 об. %, параметры решетки: a = = 5.3129, b = 5.2125, c = 5.1471. Тетрагональная фаза составила 72 об. %: параметры решетки a = = 5.1200, c = 5.2500.
Диоксид циркония обладает полиморфизмом. Моноклинная модификация, устойчивая при нагреве до температуры около 1270 К, переходит в тетрагональную форму, устойчивую лишь при высоких температурах. При охлаждении до температуры ниже 1270 К происходит обратный переход в моноклинную модификацию. Кубическая форма ZrO2, образуется при 2300 К без заметных объемных изменений [19]. Фазовое превращение ZrO2 происходит с разрывом существующих связей в решетке. Оно протекает сравнительно медленно, и температура перехода точно не фиксируется [20]. Обратимый характер фазового превращения ZrO2 сопровождается переменным сжатием и расширением при нагреве и последующем охлаждении. Чтобы устранить растрескивание материала при нагреве, являющееся следствием обратимого перехода одной модификации ZrO2 в другую, был найден способ, который позволил предотвратить обратный переход нестабильной высокотемпературной тетрагональной фазы ZrO2 в моноклинную. Этот процесс получил название стабилизации диоксида циркония [20].
В нашей работе наличие тетрагонального оксида циркония возможно связано со стабилизацией оксидом кремния, образующимся в поверхностном слое образца при оксидировании в силикатном электролите, а также за счет быстрого охлаждения оксидного слоя при микроплазменном оксидировании. Отсутствие на дифрактограмме рефлексов оксида кремния может быть обусловлено его рентгеноаморфностью или вхождением его в твердый раствор с основной фазой ZrO2.
Испытания образцов с покрытиями, при термоциклическом нагружении с нагревом до 1000°С и быстром охлаждении, показали следующие результаты. После многократного термоциклирования покрытие вне зависимости от времени микроплазменной обработки лишь изменяет цвет со светло-серого до темно-серого. Имея первоначально гладкую поверхность, микроплазменное покрытие с увеличением количества циклов становится все более шероховатым. Разрушение покрытия, полученного при длительности МПО 10 мин, с частичным его отщелкиванием до медной подложки начинается с 44 цикла, при этом первоначально обнажившийся участок медной подложки не только не увеличивается по площади, но и исчезает (заращивается) к 57-му циклу. При продолжении термоциклирования эффект обнажения локальных участков медной подложки с последующим их заращиванием наблюдается вплоть до 70 цикла. Далее появляющиеся обнаженные участки медной подложки начинают увеличиваться по площади, процесс заращивания их начинает ослабевать. Таким образом, к 90-му циклу остается не менее 70% площади подложки под покрытием, остальная часть площади медной подложки обнажена (рис. 4). Поперечный размер локальных обнажений находится в пределах от 5 до 500 мкм, при этом на подложке они распределены случайным образом. При термоциклировании наблюдается сильное коробление первоначально плоского образца с покрытием, и после 95 циклов испытание на термоциклическую стойкость прекращается, При этом на поверхности образцов сохраняется около 50% покрытия. Следует отметить, что на всем протяжении процесса термоциклирования сохраняется адгезионная связь слоев по границам титан-цирконий даже после 95 циклов испытаний. Для покрытия, полученного при длительности МПО 6 мин термоциклическая стойкость ниже, а именно, к 86 циклу более 50% покрытия отделяется от подложки, т.е. наблюдается меньшая ТЦС.
Рис. 4.
Фотографии поверхности образца с оксидным покрытием (образец № 2) после 90 циклов термоциклических испытаний; оптическая микроскопия.
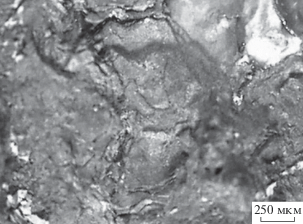
На рис. 4 приведено изображение в оптическом микроскопе фрагмента поверхности образца, на котором видна обнажившаяся медная основа и оставшиеся покрытие. Как видно, оставшееся покрытие достаточно целостное, без явных трещин в структуре.
Исследовано состояние поверхности после термоциклических испытаний в области обнажения медной основы с помощью сканирующего электронного микроскопа.
На рис. 5 представлен плавный переход покрытия (левый угол) к материалу подложки – меди (правый угол). Граница соединения покрытие – подложка нечеткая, без подъемов и углублений под покрытие. Покрытие плотно прилегает к поверхности.
После термоциклических испытаний сохраняется развитая структура покрытия (рис. 6). Если до термоциклических испытаний развитая структура поверхности характеризуется наличием пор и трещин (рис. 2), то после термоциклирования на рис. 6 наблюдаем наличие гофрированного объемного слоя. Из этих фотографий следует, что поверхность покрытия достаточно однородная и плотная с развитым микрорельефом. Увеличение микрорельефа покрытия и, как следствие, увеличение объема покрытия в процессе проведении термоциклирования обуславливает заращивание участков меди на поверхности, описанное выше.
Анализ поверхностного слоя образца после термоциклических испытаний в области с сохранившимся покрытием методом ИК-спектрометрии, показал наличие ряда оксидов в поверхностном слое: ZrO2 (1101.1 см–1), CuO (592.1 см–1), Cu2O (510.9 см–1), а так же TiO2 (791.9 см–1). Это свидетельствует о частичном разрушении покрытия при термоциклическом нагружении и о последующем участии ионов подложки и подслоя в окислительных реакциях.
ЗАКЛЮЧЕНИЕ
Создана слоистая структура на медной подложке, состоящая из последовательно осажденных металлических слоев титана и циркония с последующим преобразованием циркония в диоксид циркония, модифицированный оксидом кремния.
Установлены условия и режимы микроплазменного процесса получения равномерных оксидно-керамических покрытий на сложной слоистой подложке.
Исследована морфология поверхности полученных покрытий до и после термоциклических испытаний. Перед термоциклическими испытаниями покрытие пористое с сеткой мельчайших трещин, после испытаний покрытие становится беспористым с увеличенным микрорельефом. После термоциклических испытаний меняется состав покрытия, а именно, в составе покрытия наряду с оксидом циркония обнаруживаются оксиды титана и меди.
Комбинированным методом, включающим наноструктурирование, вакуумно-дуговое напыление титанового подслоя, магнетронное осаждение циркониевого слоя и его микроплазменное оксидирование, сформированы покрытия способные выдержать более 90 циклов термоциклических испытаний с минимальным растрескиванием поверхностного слоя и минимальным отслаиванием покрытия.
Список литературы
Третьяков Ю.Д. Керамика – материал будущего. М.: Знание, 1987. С. 48.
Шевченко В.Я., Баринов С.М. Техническая керамика. М.: Наука, 1993. С. 187.
Каныгина О.Н., Пак Е.М. Влияние оксидов иттрия, кальция и алюминия на структуру и свойства циркониевой керамики // Вестн. КГНУ. Сер. ест.-техн. наук. 1996. Вып. 1. Ч. 2. С. 53–56.
Авиационные материалы и технологии. 80 лет / Под ред. Каблова Е.Н. Изд-во: ВИАМ, 2012. С. 476.
Салахутдинов Г.М. Развитие методов теплозащиты жидкостных ракетных двигателей. М.: Наука, 1984. С. 144.
Лукин Е.С., Попова Н.А., Здвижкова Н.И. Прочная керамика на основе оксида алюминия и диоксида циркония // Стекло и керамика. 1993. № 9–10. С. 25–29.
Баранов Р.В. Исследование процесса получения и свойств циркониевой керамики с малыми добавками металла // 22 Гагар. чтения: Сб. тез. докл. молод. науч. конф. Ч. 3. М., 1996. С. 48.
Ceramics and Society / Ed. Brook R.J. Faenza: Techna, 1995. P. 158.
Панин В.Е., Коротеев А.С., Сергеев В.П., Ризаханов Р.Н. В ракетном горниле // Наука из первых рук. 2011. № 4. С. 96–103.
Панин В.Е., Сергеев В.П., Панин А.В. Наноструктурирование поверхностных слоев конструкционных материалов и нанесение наноструктурных покрытий. Томск: изд-во ТПУ, 2010. С. 254.
Мамаев А.И., Мамаева В.А., Бориков В.Н., Дорофеева Т.И. Формирование наноструктурных неметаллических неорганических покрытий путем локализации высокоэнергетических потоков на границе раздела фаз: Учеб. пособие. Томск: Изд-во Том. ун-та, 2010. С. 360.
Appelfeld A.V., Suminov I.V. Microarc oxidation: The course of lectures for foreign students. M.: “MATI” Russian State Technological University named after K.E. Tsiolkovsky, 2006. P. 82.
Дорофеева Т.И., Мамаева В.А. Особенности микроплазменной обработки напыленного циркония в силикатном электролите различного состава // Физика и химия обработки материалов. 2010. № 2. С. 18–25.
Fedorischeva M.V., Kalashnikov M.P., Sergeev V.P., Neufeld V.V. Changes in the structural phase state of a copper substrate’s surface layer bombarded with titanium ions // Bulletin of the Russian Academy of Sciences. Physics. 2014. V. 78. № 8. P. 710–712.
Сергеев В.П., Яновский В.П., Параев Ю.Н., Сергеев О.В., Козлов Д.В., Журавлев С.А. Установка ионно-магнетронного напыления нанокристаллических покрытий (КВАНТ) // Физическая мезомеханика. 2004. Т. 7. Спец. выпуск. Ч. 2. С. 333–336.
Емельянова Е.Ю., Дорофеева Т.И., Мамаев А.И., Мамаева В.А., Будницкая Ю.Ю. Формирование слоистых наноструктурных неметаллических неорганических покрытий // Известия вузов. Физика. 2011. Т. 54. № 10/2. С. 132–138.
Mamaev A.I., Borikov V.N., Mamaeva V.A., Dorofeeva T.I. A Computer System Measuring the Electrical Parameters of Microplasma Processes in Solutions // Protection of Metals. 2005. V. 41. № 3. P. 254–258.
Дорофеева Т.И., Мамаев А.И., Мамаева В.А. Взаимосвязь циклических вольтамперных характеристик и свойств оксидно-керамических покрытий во времени при микроплазменном оксидировании поверхности алюминиевых сплавов // Перспективные материалы. 2007. № 5. С. 48–52.
Балкевич В.Л. Техническая керамика. М.: Стройиздат, 1984. С. 189.
Калинович Д.Ф., Кузнецова Л.И., Денисенко Э.Т. Диоксид циркония: свойства и применение (Обзор зарубежной литературы) // Порошковая металлургия. 1987. № 11. С. 98–102.
Дополнительные материалы отсутствуют.
Инструменты
Физикохимия поверхности и защита материалов