Физикохимия поверхности и защита материалов, 2019, T. 55, № 4, стр. 391-395
Бестемплатный синтез и свойства мезопористого титаната кальция
К. В. Иванов 1, *, О. В. Алексеева 1, А. С. Краев 1, А. В. Агафонов 1
1 Федеральное государственное бюджетное учреждение науки Институт химии растворов им. Г.А. Крестова Российской академии наук
153045 Иваново, Академическая ул., 1, Россия
* E-mail: ivk@isc-ras.ru
Поступила в редакцию 24.10.2017
После доработки 16.01.2019
Принята к публикации 07.02.2019
Аннотация
Бестемплатным синтезом, включающим золь–гель процесс и соосаждение, был получен рентгеноаморфный порошок. Показано, что формирование мезопористого титаната кальция происходит при прокаливании порошка до 800°С. Структура и морфология термически обработанных при температурах 200, 400, 600 и 800°С образцов были исследованы методами сканирующей электронной микроскопии, рентгенофазового и термогравиметрического анализа, ИК-спектроскопии. На основании данных низкотемпературной адсорбции-десорбции паров азота и лазерного дифракционного анализа установлено, что полученный материал – порошок титаната кальция – имеет высокоразвитую поверхность более 100 м2/г со средним размером частиц порошка от 99 до 290 нм и значительный объем пор.
ВВЕДЕНИЕ
Оксиды со структурой перовскита в настоящее время находят широкое применение в различных областях: от функциональных элементов электроники и спинтроники до твердотельных оксидных топливных элементов и медицины.
Из всего многообразия перовскитов можно выделить титатанат кальция (CaTiO3), имеющий уникальные фотохимические свойства, химическую стабильность и совместимость с биологическими тканями, что позволяет использовать его в качестве материала для изготовления имплантов.
Для формирования высококачественных биологически совместимыех покрытий наибольшие перспективы имеет мезопористый титанат кальция [1–3].
В последние годы в литературных источниках появилось большое количество публикаций, посвященных синтезу и свойствам мезопористого титаната кальция [4–6]. В основе опубликованных методов синтеза мезопористого титаната кальция лежит темплатный метод. В качестве темплатов для получения мезоструктурированного предшественника титаната кальция используются поверхностно-активные вещества и полимеры. Однако, описанные подходы и приемы связаны с многоступенчатым синтезом и высокотемпературной обработкой продуктов, выделенных из растворов, для удаления темплата и получения фазы титаната кальция и не позволяют получить мезопористые структуры CaTiO3, удовлетворяющие критериям его применения в качестве биоимпланта [7–12]. Поэтому разработка новых высокоэффективных путей получения мезопористых порошков титанатов кальция, изучение процессов эволюции структуры данных материалов при различных температурах, а также исследование их физико-химических свойств является актуальной задачей.
Цель работы заключалась в получении мезопористого порошка титаната кальция методом бестемплатного синтеза и исследовании влияния температурной обработки на его структуру, морфологию и физико-химические свойства.
ЭКСПЕРИМЕНТАЛЬНАЯ ЧАСТЬ
Титанат кальция был синтезирован комбинированным методом, включающим золь–гель процесс и соосаждение. 2.5 г Ca(OH)2 растворяли в 25% водном растворе аммиака. В полученный раствор по каплям добавляли тетрабутилат титана Ti[C7H9O]4 в количестве 11.49 г при интенсивном перемешивании. В результате образовывался рыхлый белый осадок. Формирование осадка может быть обусловлено следующими процессами:
Отцентрифугированный осадок многократно промывали водой до постоянства рН с целью удаления гидроксида аммония и бутилового спирта. Отмытый осадок высушивали до постоянной массы при 100°С и отжигали при температурах 200, 400, 600 и 800°С.
Образцы термически обработанных порошков были исследованы с помощью ряда физико-химических методов исследования. Морфология порошков была проанализирована методом электронной сканирующей микроскопии (микроскоп VEGA3 SBH TESCAN) при напряжении 5.0 кВ. Размер частиц был установлен с помощью лазерного дифракционного анализатора “Zetasizer Nano ZS” (Malvern Instruments) в диапазоне от 0.3 нм до 10 мкм. Для исследования распределения частиц по размерам порошки предварительно обрабатывали в ультразвуковой ванне в среде изопропилового спирта в течение 1 ч с целью разрушения агломератов. Удельную поверхность определяли методом низкотемпературной (77 К) адсорбции и десорбции паров азота на высокоскоростном газовом сорбционном анализаторе NOVA 1200e. Площадь поверхности вычисляли по уравнению БЭТ из изотерм адсорбции. Общий объем пор композита, распределение пор по размерам рассчитаны с применением модели BJH. Рентгеноструктурный анализ синтезированных порошков был выполнен на дифрактометре (ДРОН-2) с источником излучения CuKα и напряжением 40 кВ. Термический анализ синтезированного порошка был проведен на NETZSCH STA 409 C/CD. ИК-спектры порошков синтезированных соединений в виде таблеток с KBr регистрировали на ИК-Фурье спектрометре VERTEX 80v.
РЕЗУЛЬТАТЫ И ОБСУЖДЕНИЕ
Термический анализ полученного материала (рис. 1а) с учетом масс-спектрометрического анализа отходящих газов (рис. 1б) позволил детально рассмотреть тепловые процессы, протекающие при его термодеструкции. На термограмме образца синтезированного материала рис. 1а можно выделить 3 участка. Первый участок находится в интервале температур от 25–250°С. На этом участке наблюдается удаление адсорбированных молекул воды и CO. Убыль массы составила 10%. Второй участок 250–500°С сопровождается удалением CO, а также гидратной воды. Убыль массы при этом составляет около 6%. В интервале температур 500–800°С термические процессы сопровождаются потерей массы, связанной с появлением в газовой фазе молекул CO2.
Рис. 1.
(а) ТГ/ДТГ/ДСК синтезированного материала. (б) Масс-спектры паровой фазы при нагреве синтезированного материала.
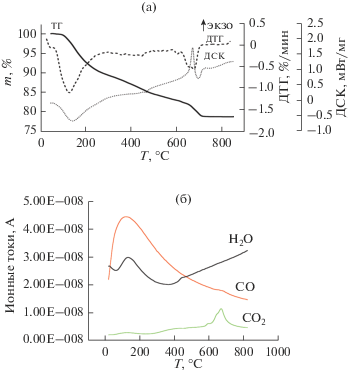
Данные РФА хорошо согласуются с результатами термического анализа и позволяют идентифицировать ряд эффектов на кривых ТГ/ДТГ/ДСК. На рис. 2 представлены рентгенограммы, характеризующие термическую эволюцию фазового состава синтезированного материала в результате нагрева в течение часа при температурах 100, 200, 400, 600 и 800°С. Результаты РФА показывают, что в интервале температур 100–400°С материал представляет собой рентгеноаморфную фазу, это связано с тем, что материал образован ультрадисперсными гидратными формами. Присутствующие на данном фоне рефлексы 2θ = 28.28°, 34.59°, присущи карбонату кальция. Дифрактограмма материала, прокаленного при 600°С, содержит рефлексы в области углов 2θ = 23.77°, 34.49°, 47.54°, 59.45°, 69.53°, относящиеся к фазе титаната кальция в орторомбической сингонии. При этом на дифрактограмме сохраняются рефлексы от следов карбоната кальция. С ростом температурной обработки до 800°С рефлексы от примеси CaCO3 пропадают. Происходит процесс декарбонизации, сопровождающийся спеканием оксидов кальция и титана.
ИК-спектры, характеризующие термическую эволюцию порошка полученного материала в интервале температур 100–800°С приведены на рис. 3. Для ИК-спектров характерны полосы с максимумами поглощения в области: 4500–3500 см–1, соответствующие OH– группам, 1456 см–1 – колебаниям ${\text{CO}}_{{\text{3}}}^{{{\text{2}} - }}$, характерным для карбонатных включений. Наличие размытого пика при 569 см–1 относится к связи Ca–Ti–O. Как следует из ИК-спектров, следы карбоната присутствуют в титанате кальция после часового отжига при 800°С. Появление полосы поглощения при 1456 см–1, характеризующей колебание C–O в отожженном материале при 800°С, вероятно, обусловлено адсорбированном на порошке CO2 из воздуха.
На рис. 4 представлены микрофотографии порошков, полученные при разрешении 2 и 20 мкм и напряженности поля 5 кВ. Показано, что порошки синтезированного материала, термически обработанные при 100 и 800°С, представляют полидисперсные частицы в виде агломератов микрометрического размера от 1 до 30 мкм.
На рис. 5 представлены результаты распределения частиц по размерам порошков, термически обработанных при температурах от 100 до 800°С. С ростом температуры обжига средний размер частиц увеличился от 99 до 290 нм, что связано с их спеканием, образованием агломератов, формированием кристаллической фазы.
Характеристики пористости и удельной поверхности порошков были получены по результатам адсорбции и десорбции паров азота при 77 К. На рис. 6 в качестве примера приведены изотермы адсорбции азота на образцах, прокаленных при 100 и 800°С.
Рис. 6.
Сорбционные характеристики на образцах при 100 и 800°С (а) изотермы сорбции – десорбции азота и (б) диаметр пор.

Изотермы адсорбции-десорбции азота по классификации IUPAC относятся к IV типу.
На основании изотерм сорбции и десорбции были определены общая удельная поверхность и диаметр пор порошка (табл. 1).
Таблица 1.
Адсорбционные характеристики порошков
100°C | 200°C | 400°C | 600°C | 800°C | |
---|---|---|---|---|---|
S (БЭТ), м2/г | 166 | 140 | 129 | 117 | 35 |
Dпор, нм (BJH) | 6 | 6 | 7 | 24 | 3 |
Vпор, см3/г (BJH) | 0.44 | 0.39 | 0.36 | 0.30 | 0.07 |
Как видно из табл. 1, полученные комбинацией золь–гель метода и соосаждения и высушенные при 100°С порошки, имеют площадь поверхности 166 м2/г. Следует отметить, что площадь поверхности мезопористого титаната кальция, синтезированного авторами работ [4, 5], не превышает 60 м2/г. С ростом температуры отжига до 600°С площадь поверхности и суммарный объем пор закономерно снижаются. Это сопровождается тепловыми эффектами на кривой термического анализа и может быть связано с разложением карбонатных включений, и синтезом титаната кальция. Дальнейший рост температуры отжига до 800°С приводит также к уменьшению площади поверхности порошка до 35 м2/г, резкому снижению объема и диаметра пор, что обусловлено процессом спекания.
Таким образом, в соответствие с данными низкотемпературной адсорбции-десорбции паров азота исследуемый порошок титаната кальция можно отнести к материалу с мезопористой структурой.
ЗАКЛЮЧЕНИЕ
Показано, что использование комбинированного метода, совмещающего (золь–гель процесс и соосаждение в щелочной среде гидролиза тетраизопропилата титана с взаимодействием с гидроксидом кальция) приводит к получению рентгеноаморфного осадка, содержащего гидратированные наночастицы титаната кальция. Термический отжиг полученного образца при температуре до 800°С позволяет получить материал в виде порошка с высокоразвитой поверхностью более 100 м2/г и мезопористой структурой со значительным объемом пор. Полученный мезопористый CaTiO3 может быть использован в качестве материала для изготовления биоимплантов и носителя каталитически активной фазы.
Список литературы
Holliday S., Stanishevsky A. // Surface & Coatings Technology. 2004. V. 188–189. P. 741–744.
Dubey A.K., Tripathi G., Basu B. // J. Biomedical materials Research B: Applied Biomaterials. 2010. V. 95B. № 2. P. 320–329.
Figueiredo A.T., Longo V.M., Lazaro S., Mastelaro V.R., Vicente F.S., Hernandes A.C., Li M.S., Varela J.A., Longo E. // J. Lumin. 2007. V. 126. P. 403–407.
Yahya N.Y., Ngadi N., Jusoh M., Halim N.A.A. // Energy Conversion and Management. 2016. V. 129. P. 275–283.
Cesconeto F.R., Borlaf M., Nieto M.I., Oliveira A.P.N., Moreno R. // Ceramics International. 2017. doi.org/ https://doi.org/10.1016/j.ceramint.2017.09.173
Li Z.J., Zhang Y.J., Zhang H.W., Fu H.X. // Microporous and Mesoporous Materials. 2013. V. 176. P. 48–54.
Kay H.F., Bailey P.C. // J. Acta Cryst. 1957. V. 10. P. 219–226.
Zhang X., Zhang J., Ren X., Wang X.J. // J. Solid State Chem. 2008. V. 181. P. 393–398.
Lee S.J., Kim Y.C., Hwang J.H. // J. Ceram. Process Res. 2004. V. 5. P. 223–226.
Kutty T.R.N., Vivekanandan R., Murugaraj P. // J. Mater Chem. Phys. 1988. V. 19. P. 533–546.
Cavalcante L.S., Marques V.S., Sczancoski J.C., Escote M.T., Joya M.R., Varela J. et al. // J. Chem. Eng. 2008. V. 143. P. 299–307.
Moreira M.L., Paris E.C., Nascimento G.S., Longo V.M., Sambrano J.R., Mastelaro V.R. et al. // Acta Mater. 2009. V. 57. P. 5174–5185.
Дополнительные материалы отсутствуют.
Инструменты
Физикохимия поверхности и защита материалов