Физикохимия поверхности и защита материалов, 2019, T. 55, № 5, стр. 471-478
Функциональные композитные адсорбенты высокой насыпной плотности на основе металлорганических каркасных структур для аккумулирования метана
О. В. Соловцова 1, *, А. В. Школин 1, И. Е. Меньщиков 1, М. К. Князева 1, А. Л. Пулин 1, А. А. Фомкин 1, А. Ю. Цивадзе 1, О. Е. Аксютин 2, А. Г. Ишков 2
1 ФГБУН Институт физической химии и электрохимии им. А.Н. Фрумкина РАН
119071 Москва, Ленинский проспект, 31, стр. 4, Россия
2 Публичное акционерное общество “Газпром”
117997 Москва, ул. Наметкина, 16, Россия
* E-mail: o.solovtsova@phyche.ac.ru
Поступила в редакцию 04.03.2019
После доработки 10.03.2019
Принята к публикации 15.04.2019
Аннотация
Проведено исследование влияния различных видов связующих, давления формования и углеродсодержащих добавок на структурно-энергетические характеристики, плотность и механические свойства формованных композитных адсорбентов на основе металлорганических каркасных структур, а также на их адсорбционные характеристики применительно к системам аккумулирования метана.
1. ВВЕДЕНИЕ
Металлорганические каркасные структуры (МОКС) – класс кристаллических микропористых материалов, структура которых образована ионами металлов или их кластерами, связанных органическими лигандами через координационные связи [1]. От других пористых твердых тел, таких как цеолиты, кремнезем, или активированный уголь, МОКС отличает возможность их структурной перестройки, например, путем изменения вида металла и/или органического лиганда, что ведет к получению веществ с различными свойствами [2]. За почти три десятилетия проведены многочисленные исследования по синтезу и определению свойств материалов МОКС [3–5]. Однако в последние годы все большее внимание уделяется созданию и прикладному использованию материалов на основе МОКС [6, 7]. Так, пористые МОКС могут быть применены в целом ряде областей, таких как катализ, разделение газов, доставка лекарств, а также при создании энергонасыщенных адсорбционных систем аккумулирования таких газов, как природный газ метан и водород [8–13]. Однако, для того, чтобы использовать МОКС в промышленных адсорбционных процессах и установках, должны быть разработаны технологические подходы к их масштабированному производству в различных формах выпуска.
В настоящее время ряд компаний осуществляет промышленное производство МОКС в виде кристаллических порошков [14], а также в форме гранул (например, компания BASF и технологический центр на базе Мичиганского университета) [15]. Сообщается также о производстве таблеток, тонких пленок, пен, листов и полых структур на основе широко известных МОКС – HKUST-1, MOF-5 и т.д. [16]. Однако общей чертой всех предыдущих исследований [17–19], связанных с формованием МОКС является устойчивое ухудшение свойств в результате придания им определенной функциональной формы (при компактировании): деградация пористой структуры, снижение удельной поверхности пор, [20, 21]. Таким образом, для получения функциональных адсорбционных материалов на основе МОКС с приданием им определенной формы необходимо проведение исследований по изучению свойств формованных материалов в зависимости от условий и режимов на каждом этапе изготовления.
Сегодня одним из наиболее перспективных видов МОКС для применения в системах аккумулирования природного газа метана, с точки зрения удельной емкости, является структура типа Cu-BTC, которая и была выбрана в качестве объекта исследования [22–24].
Целью настоящего исследования являлось получение функциональных пористых материалов и композитов высокой насыпной плотности на основе МОКС Cu-BTC с использованием различных связующих и условий формования, а также исследование их структурно-энергетических характеристик и адсорбционной активности по отношению к природному газу метану.
2. ОБЪЕКТЫ ИССЛЕДОВАНИЯ
2.1. Исходный МОКС
В работе проводили формование предварительно синтезированных МОКС на основе меди – Cu-BTC. Синтез Cu-BTC проводили сольвотермальным методом, описание которого приводится в [25, 26]. В предварительно приготовленный раствор нитрата меди (99%, Acros Organics) в N,N- диметилформамиде (ДМФА, х. ч.) при интенсивном перемешивании вводили раствор бензол-1,3,5-трикарбоновой кислоты в том же растворителе (98%, Acros Organics). Образовавшийся золь голубого цвета помещали в герметичный автоклав с фторопластовым вкладышем и выдерживали при температуре 110°С в течение 20 ч. Осадок отделяли от маточного раствора фильтрованием, многократно промывали ДМФА на фильтре, и сушили в вентилируемом термошкафу при температуре 110°С в течение 24 ч. Структурно-энергетические характеристики металлорганической структуры Cu-BTC, определенные по обратимым изотермам адсорбции-десорбции азота при 77 К по методу БЭТ и методу теории объемного заполнения микропор М.М. Дубинина [27], в табл. 1.
Таблица 1.
Структурно-энергетические характеристики металлорганической структуры Cu-BTC
Характеристика, размерность | Значение |
---|---|
Удельная площадь поверхности, SБЭТ, м2/г | 880 |
Удельный объем микропор, W0, см3/г | 0.37 |
Эффективный радиус микропор по Дубинину, х0, нм | 0.31 |
Характеристическая энергия адсорбции азота, Е, кДж/моль | 12.6 |
Характеристическая энергия адсорбции бензола, Е0, кДж/моль | 38.2 |
Суммарный объем пор, Ws, см3/г | 0.40 |
Насыпная плотность, г/см3 | 0.38 |
2.2. Функциональные материалы и композиты высокой плотности на основе МОКС
При создании функциональных адсорбционных материалов высокой насыпной плотности путем формования наиболее важными варьируемыми параметрами являются: фракционный состав исходного адсорбента, тип и концентрация связующего вещества, давление прессования, время выдержки под давлением [28–30]. Подбор оптимальных значений этих параметров позволяет изготавливать адсорбционно-активные материалы высокой плотности практически любых форм, без значительной деградации исходной пористой структуры адсорбента. Уже сегодня на высокой стадии разработки находятся технологии получения формованных углей и цеолитов [31–33].
В случае МОКС, ситуация складывается несколько иным образом. В литературе приводятся данные о том, что добавление углеродных материалов в структуру формованного адсорбента на основе МОКС помогает сохранить, в той или иной степени, исходные характеристики МОКС, а также придать получаемому материалу механическую и термическую стабильность и гидрофобность [34–36]. Так, в работе [34] показано, что введение добавок расширенного графита в состав композита на основе MOF-5 помогает частично защитить кристаллиты MOF-5 от пластической деформации и деградации пористой структуры. Предполагается, что графит обеспечивает поглощение (демпфирование) части сжимающей нагрузки, так как действует как смазка и распределяет механическую энергию. Кроме того, добавление графита в количестве 5–10% по массе в исходный порошок MOF-5 улучшает теплопроводность гранул получаемого композита по сравнению с гранулами чистого MOF-5. В настоящей работе в качестве углеродосодержащей добавки использовали графитированную сажу Carbon Black (CB).
В качестве основных типов связующих в рамках настоящей работы были использованы такие связующие как:
− 5% водный раствор поливинилового спирта Mowiol марки 10-98 (ПВС);
− 2% раствор хитозана в 2% уксусной кислоте (ХТЗ);
− 0.1% водный раствор оксицеллюлозы (ОЦ);
− 10% водный раствор латекса марки СКС-30 УК.
Анализ литературных данных показал возможность применения данных веществ для формования МОКС, однако комплексная оценка пористой структуры и адсорбционных свойств полученных материалов к конкретным газам до и после формования не проводилась [37–40].
При изготовлении формованных материалов, наиболее часто используемым пластификатором является вода, а также смеси органического растворителя и воды. В настоящей работе формование проводили в одном случае, без добавления пластификатора, а в другом, с использованием ДМФА, который затем извлекали из формованного материала путем термовакуумной регенерации [41].
Выбор оптимальных параметров осуществляли по схеме, представленной на рис. 1.
На первом этапе оптимизации осуществляли формование МОКС при различных давлениях, без добавления связующих веществ и углеродосодержащих компонентов (сажи). Целью первого этапа был выбор оптимального давления формования, обеспечивающего высокую плотность без значительной деградации адсорбционных характеристик полученного материала по сравнению с исходным.
На втором этапе производили формование МОКС с разными типами связующих веществ при одном и том же давлении, выбранном на первом этапе, без добавления углеродосодержащих компонентов. Так определяли оптимальное связующее вещество.
На третьем этапе в исходный МОКС добавляли сажу в различных массовых соотношениях, формование производили без связующего и при оптимальном давлении, выбранном на первом этапе.
Упрощенная технологическая схема получения формованных материалов представлена на рис. 2.
Рис. 2.
Технологическая схема получения функциональных материалов и композитов высокой насыпной плотности на основе Cu-BTC.
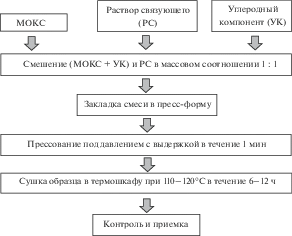
В соответствии со схемой (рис. 2), вначале осуществляли подготовку формуемых компонентов и раствора связующего. После этого формуемые компоненты (чистый порошок Cu-BTC или его смесь с сажей) смешивали с предварительно подготовленным раствором связующего в воде при массовом соотношении 1 : 1. Смесь тщательно гомогенизировали в смесителе. Полученной смесью наполняли цилиндрическую пресс-форму и прессовали с использованием гидравлического пресса, выдерживая образец под давлением в течение 1 мин. Готовые отформованные образцы сушили в вентилируемом термошкафу при температуре 110–120°С в течение 6–12 ч.
В качестве примера, на рис. 3 представлены фотоснимки полученных образцов.
Рис. 3.
Формованные адсорбенты на основе МОКС Cu-BTC: (а) образец Cu-BTC, компактированный при давлении 160 МПа, связующее ПВС, (б) образец Cu-BTC, компактированный с добавлением 5% сажи Carbon Black при давлении 160 МПа, без использования связующего.
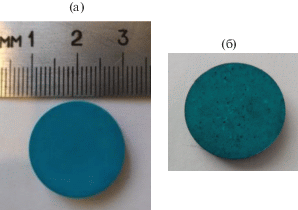
Из рис. 3 следует, что полученные образцы имеют правильную цилиндрическую форму диаметр 20 мм и высоту 2 мм, гладкую и ровную поверхность. У образца с содержанием сажи различимы черные вкрапления углеродного материала – рис. 3б.
После этого для каждого образца проводили измерение насыпной плотности (d, г/см3), твердости, а также исследовали изменение пористой структуры и структурно-энергетических характеристик до и после формования. Кроме того, проводили оценку адсорбционной активности и удельных емкостных свойств полученных материалов к метану.
Структурно-энергетические характеристики полученных образцов определяли по изотерме сорбции стандартного пара азота при 77 К, с использованием многофункционального анализатора удельной поверхности Quantachrome Autosorb iQ. Определение плотности образцов проводили, исходя из их веса и геометрических параметров. Твердость (HB) образцов определяли по стандартному методу Бринелля [42].
Оценку адсорбционной активности образцов к метану производили на основе теории объемного заполнения микропор М.М. Дубинина [27] в интервале температур от 243 до 333 К и давлениях до 30 МПа по методике, изложенной в работах [43, 44]. После этого рассчитывали удельные характеристики систем аккумулирования метана на основе полученных материалов по методике, описанной в [45, 46].
3. ОБСУЖДЕНИЕ РЕЗУЛЬТАТОВ
3.1.1. Формование МОКС без связующего и углеродного компонента. Варьируемый параметр – давление
Повышение плотности адсорбента увеличивает удельные характеристики по объемной плотности запасаемого газа, что приводит к повышению эффективности использования материала для аккумулирования метана [3]. При этом, важнейшим и определяющим технологическим параметром является давление прессования. В табл. 2 представлены характеристики формованных МОКС без добавления связующих веществ и сажи при давлениях от 80 до 240 МПа.
Таблица 2.
Характеристики формованных образцов при различных давлениях, а также изменение параметров их пористой структуры по сравнению с исходным Cu-BTC
№ | Давление, МПа | d, г/см3 | SБЭТ, м2/г | W0, см3/г | Потеря SБЭТ, % | Потеря W0, % | HB, кгc/мм2 |
---|---|---|---|---|---|---|---|
Cu-BTC | – | 0.38 | 880 | 0.37 | – | – | – |
P1 | 80 | 0.99 | 880 | 0.37 | 0 | 0 | 1.51 |
P2 | 160 | 1.29 | 730 | 0.29 | 17 | 21 | 2.7 |
P3 | 240 | 1.32 | 660 | 0.28 | 25 | 25 | * |
Как следует из табл. 2, плотность формованных МОКС увеличивается с 0.99 до 1.32 г/см3 с ростом давления прессования в интервале от 80 до 240 МПа, одновременно с этим показателем ухудшаются параметры пористой структуры SБЭТ и W0. Наибольшим показателем HB, обладает образец, сформованный при давлении 160 МПа, для него же характерны средние изменения в структурных характеристиках по SБЭТ и W0 на уровне 10–12%. Как следует из данных табл. 3, давление формования на уровне 160 МПа, является оптимальным, поскольку позволяет получать адсорбенты с достаточной плотностью и механической прочностью без значительных потерь в структурно-энергетических характеристиках (образец P2).
Таблица 3.
Характеристики формованных образцов с различными типами связующих веществ при давлении 160 МПа, а также изменение параметров их пористой структуры по сравнению с исходным Cu-BTC
№ | Тип связующего | d, г/см3 | SБЭТ, м2/г | W0, см3/г | Потеря SБЭТ, % | Потеря W0, % | HB, кгс/мм2 |
---|---|---|---|---|---|---|---|
Cu-BTC | – | 0.38 | 880 | 0.37 | – | – | – |
С1 | ХТЗ | 1.33 | 500 | 0.19 | 43 | 43 | 0.50 |
С3 | ХТЗ + ДМФА | 1.16 | 697 | 0.29 | 21 | 22 | 0.57 |
С2 | ОЦ | 1.28 | 572 | 0.22 | 35 | 38 | * |
С4 | ПВС | 1.18 | 880 | 0.37 | 0 | 0 | 2.26 |
С5 | Латекс + вода | 1.16 | 634 | 0.26 | 28 | 30 | * |
Для дальнейших исследований было выбрано давление прессования 160 МПа.
3.1.2. Формование МОКС при оптимальном давлении без углеродного компонента. Варьируемый параметр – тип связующего вещества
После того, как было подобрано наиболее подходящее давление формования, определяли оптимальное связующее. В табл. 3 представлены основные характеристики полученных формованных образцов МОКС при использовании различных типов связующих веществ, при давлении 160 МПа, без добавления сажи.
Согласно полученным результатам, представленным в табл. 3, использование 2% раствора ХТЗ в 2% уксусной кислоте приводит к значительному снижению W0 и SБЭТ получаемого материала на величину порядка 43% (образец С1) по сравнению с исходным, при этом насыпная плотность образца достигает 1.33 г/см3 и является максимальной по сравнению с другими образцами. Добавление в формуемую смесь с ХТЗ растворителя ДМФА, который используется при синтезе Cu-BTC, позволило практически в два раза улучшить показатели по сохранению пористой структуры (образец С3). Так, SБЭТ и W0 снизились всего на 21 и 22%, соответственно, по сравнению с исходным МОКС. Кроме того, это позволило незначительно улучшить механические характеристики формованного МОКС с ХТЗ – с 0.50 до 0.57 HB, при сравнении с С1.
Образец, полученный с использованием раствора 0.1% ОЦ обладает очень низкой механической прочностью – при испытаниях образец разрушился (образец С2). В то же время для этого образца наблюдается значительная деградация пористой структуры – SБЭТ и W0 снизились на 35 и 38%, соответственно, по сравнению с исходным МОКС. Непрочными оказались и образцы, формуемые с использованием водного раствора латекса в качестве связующего (образец С5).
Согласно результатам проведенных исследований, наиболее подходящим для формования Cu-BTC является 5% раствор ПВС, применяемый в массовом соотношении 1 : 1 по отношению к массе формуемой смеси (образец С4). Это связующее обеспечивает наиболее высокие механические характеристики формованных материалов с сохранением удельной поверхности по БЭТ и объема микропор исходного МОКС. Аналогичные результаты были получены другими исследователями [41].
Таким образом, ПВС был определен в качестве оптимального типа связующего для получения формованных МОКС. При этом важно отметить, что ПВС, судя по всему, оказывает дополнительное защитное действие на пористую структуру формованного адсорбента. Это следует из сравнения образцов C4 и P2, которые были получены при одном и том же давлении, однако P2 формовали без добавления связующего вещества и углеродного компонента.
3.1.3. Формование МОКС при оптимальном давлении без связующего вещества. Варьируемый параметр – содержание сажи
Данные по формованным композитам Cu-BTC/CB (рис. 3б) представлены в табл. 4. Добавление 2–5% сажи в состав композита приводит к получению образцов с низкими значениями HB, а содержание сажи в 10% приводит к полному разупрочнению композита. Наименьшая потеря адсорбционных характеристик материала достигается при введении в состав исходной смеси минимального количества сажи не более 2%, дальнейшее увеличение содержания CB в интервале от 5 до 10% приводит снижению SБЭТ и W0 на 10–14%. Что касается насыпной плотности, то она также снижается при добавлении углеродного компонента.
Таблица 4.
Характеристики формованных образцов с добавлением различного количества сажи при давлении 160 МПа, а также изменение параметров их пористой структуры по сравнению с исходным Cu-BTC
№ | Содержание сажи, мас. % | d, г/см3 | SБЭТ, м2/г | W0, см3/г | Потеря SБЭТ, % | Потеря W0, % | HB, кгc/мм2 |
---|---|---|---|---|---|---|---|
Cu-BTC | – | 0.38 | 880 | 0.37 | – | – | – |
CB1 | 10 | 0.72 | 765 | 0.32 | 13 | 14 | * |
CB2 | 5 | 0.84 | 792 | 0.33 | 10 | 12 | 0.34 |
CB3 | 2 | 0.92 | 870 | 0.37 | 1 | 0 | 0.31 |
P2/CB4 | 0 | 1.29 | 730 | 0.29 | 17 | 21 | 2.70 |
Из этого можно констатировать, что получение композитных функциональных пористых материалов на основе МОКС с добавлением сажи является нецелесообразным.
3.2 Удельные характеристики полученных материалов по метану
На рис. 4 представлены изотермические зависимости удельной емкости системы хранения природного газа метана на основе исходного МОКС Cu-BTC (АПГ) в сравнении с системой копримированного газа (КПГ) в интервале температур от 243 до 333 К. Из рисунка следует, что удельная объемная емкость аккумулирования метана при давлениях до 10 МПа и температуре может достигать 150 м3(НТД)/м3.
Рис. 4.
Зависимости удельной объемной емкости АПГ на основе исходного Cu-BTC (сплошные линии) и КПГ (пунктирные линии) от давления при температурах, К: 1 – 243; 2 – 273; 3 – 293; 4 – 313; 5 – 333.
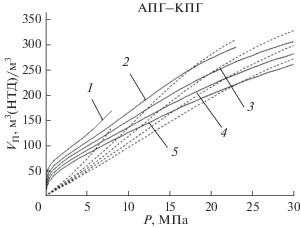
На рис. 5 представлены зависимости удельной объемной емкости от давления системы АПГ на основе наиболее перспективных образцов: P2, полученного формованием при оптимальном давлении в 160 МПа, и С4, полученного с использованием ПВС-связующего.
Из рис. 5а следует, что удельная объемная емкость растет с увеличением давления и достигает максимума при температуре 243 К. Эффективность системы АПГ перед КПГ ограничена интервалом давлений от 0 до 20 МПа, при этом, чем выше температура, тем шире интервал эффективных давлений.
Из рис. 5б следует, что удельная объемная емкость системы растет с увеличением давления газовой фазы и снижением температуры. Так, при температуре 243 К, емкость системы при 8 МПа превышает 200 м3(НТД)/м3, а при 273 К и давлении 10 МПа достигает 190 м3(НТД)/м3, что свидетельствует об эффективности применяемой технологии уплотнения с использованием ПВС.
ВЫВОДЫ
В работе исследованы условия формования металлоорганической каркасной структуры Cu-BTC. Подобраны оптимальные давление, связующее и количество углерод содержащей добавки, позволяющие сохранить в определенной степени пористую структуру МОКС (удельную площадь поверхности и объем пор) исходного МОКС и, вместе с тем, увеличить их плотность и прочность. Показано, что использование 5% раствора ПВС в массовом соотношении 1 : 1 в качестве связующего, давления 160 МПа наилучшим образом отражается на эксплуатационных свойствах получаемых формованных адсорбентов на основе МОКС, что определяет их практическое применение в технологиях хранения энергетических газов и, в частности, метана.
Работа выполнена по проекту Госзадания № 01201353185.
Работа выполнена при поддержке ПАО “Газпром”.
Список литературы
Yaghi O.M., Li H. // J. American Chemical Society. 1995. № 117(41). P. 10401–10402.
Makal T.A., Li J.-R., Lua W., Zhou H.-C. // Chem. Soc. Rev. 2012. V. 41. P. 7761–7779.
He Y., Chen F., Li B., Qian G., Zhou W., Chen B. // Coordination Chemistry Reviews. 2018. V. 373. P. 167–198.
Ren J., Langmi H.W., North B.C., Mathe M. // Int. J. Energy Res. 2015. V. 39. P. 607–620.
Lee Y.-R., Kim J., Ahn W.-S. // Korean J. Chem. Eng. 2013. V. 30. P. 1667–1680.
Knyazeva M.K., Shkolin A.V., Fomkin A.A., Tsivadze A.Yu., Solovtsova O.V., Platonova N.P., Pulin A.L., Men’shchikov I.E., Shiryaev A.A., Vysotskii V.V., Kiselev M.R. // Protection of Metals and Physical Chemistry of Surfaces. 2018. V. 54. № 6. P. 1004–1009.
Tsivadze A.Yu., Aksyutin O.E., Ishkov A.G., Fomkin A.A., Men’shchikov I.E., Pribylov A.A., Isaeva V.I., Kustov L.M., Shkolin A.V., Strizhenov E.M. // Protection of Metals and Physical Chemistry of Surfaces. 2016. V. 52. № 1. P. 24–29.
Moradi S.E., Shabani A.M.H., Dadfarnia S., Emami S. // J. Iran. Chem. Soc. 2016. V. 13. P. 1617–1627.
Khan N.A., Hasan Z., Jhung S.H. // J. Hazard. Mater. 2013. V. 244–245. P. 444–456.
Eddaoudi M., Sava D.F., Eubank J.F., Adil K., Guillerm V. // Chem. Soc. Rev. 2015. V. 44. P. 228–249.
Furukawa H., Müller U., Yaghi O.M. // Angew. Chem. Int. Ed. 2015. V. 54. P. 3417–3430.
Schoedel A., Li M., Li D., O’Keeffe M., Yaghi O.M. // Chem. Rev. 2016. V. 116. P. 12466–12535.
Yaghi O.M. // J. Am. Chem. Soc. 2016. V. 138. P. 15507–15509.
Rubio-Martinez M., Avci-Camur C., Thornton A.W., Imaz I., Maspoch D., Hill M.R. // Chem. Soc. Rev. 2017. V. 46. P. 3453.
Ferreira A.F.P., Santos J.C., Plaza M.G., Lamia N., Loureiro J.M., Rodrigues A.E. // Chemical Engineering J. 2011. V. 167. P. 1–12.
Valizadeh B., Nguyen T.N., Kyriakos, Stylianou C. // Polyhedron. 2018. V. 145. P. 1–15.
Plaza M.G., Ribeiro A.M., Ferreira A., Santos J.C., Lee U.-W., Chang J.-S., Loureiro J.M. Rodrigues A.E. // Sep. Purif. Technol. 2012. V. 90. P. 109–119.
Schell J., Casas N., Blom R., Spjelkavik A.I., Andersen A., Hafizovic Cavka J., Mazzotti M. // Adsorption. 2012. V. 18. P. 213–227.
Asadl T., Ehsanl M.R., Ribeiro A.M., Loureiro J.M., Rodrigues A.E. // Chem.Eng.Technol. 2013. V. 36. P. 1231–1239.
Bohringer B., Fischer R., Lohe M.R., Rose M., Kaskel S., Küsgens P. // MOF Shaping and Immobilization, Metal-Organic Frameworks: Applications from Catalysis to Gas Storage. 2011. Wiley – VCH, Weinheim, Germany. P. 353–382.
Cho H.-Y., Kim J., Kim S.-N., Ahn W.-S. // Microporous Mesoporous Mater. 2013. V. 169. P. 180–184.
Li H., Wang K., Sun Y., Lollar T.C., Li J., Zhou H.C. // Materials Today. 2018. V. 21. № 2. P. 108–121.
Ren J., Langmi H.W., North B.C., Mathe M. // Int. J. Energy Res. 2015. V. 39. P. 607–620.
Mueller U., Schubert M., Teich F., Puetter H., Schierle-Arndt K., Pastré J. // J. Chem. Mater. 2006. V. 16. P. 626–636.
Гранкина Ю.А., Филиппова Л.Ю., Шубина В.Н., Козлова Н.П. // Вестник ТГТУ. 2015. Т. 21. № 3. С. 461–469.
Батракова М.К., Соловцова О.В., Фомкин А.А., Цивадзе А.Ю., Школин А.В., Ширяев А.А., Высоцкий В.В. // Физикохимия поверхности и защита материалов. 2017. Т. 53. № 6. С. 563–568.
Дубинин М.М. Адсорбция и пористость. М. ВАХЗ. 1972.
Syed-Hassan S.S.A., Zaini M.S. // Korean J. Chemical Engineering. 2016. V. 33. № 8. P. 2502–2512.
Li D., Zhou J., Zhang Z., Tian Y., Qiao Y., Li J., Wen L., Wei L. // Materials Letters. 2017. V. 190. P. 127–130.
Prajwal B.P., Ayappa K.G. // Adsorption. 2014. V. 20. P. 769–776.
Lozano-Castello D., Alcaniz-Monge J., de la Casa-Lillo M.A., Cazorla-Amoros D., Linares-Solano A. // Fuel. 2002. V. 81. P. 1777–1803.
Zhang J., Mao Y., Li J., Wang X., Xie J., Zhou Y., Wang J. // Chemical Engineering Science. 2015. V. 138. P. 473–481.
Romanos J., Barakat F., Dargham S.A. Nanoporous Graphene Monolith for Hydrogen Storage // Materials Today: Proceedings, 2018. V. 5. № 9. P. 1747–1748.
Liu D., Purewal J.J., Yang J., Sudik A., Maurer S., Mueller U., Ni J., Siegel D.J. // J. Hydrogen energy. 2012. V. 37. P. 109–117.
Ortmann J.P., Kaisare N.S. // International J. Hydrogen energy. 2016. V. 41. P. 342–354.
Xu C., Yang J., Veenstra M., Sudik A., Purewal J.J., Ming Y., Hardy B.J., Warner J., Maurer S., Mueller U., Siegel D.J. // International J. Hydrogen Energy. 2013. V. 38. P. 3268–3274.
Vinu M., Raja D.S., Jiang Y.-C., Liu T.-Y., Xie Y.-Y., Lin Y.-F., Yang C.-C., Lin C.-H., Alshehri S.M., Ahamad T., Salunkhe R.R., Yamauchi Y., Deng Y.-H., Wu K.-W. // J. Taiwan Institute of Chemical Engineers. 2018. V. 83. P. 143–151.
Kusgens P., Zgaverdea A., Fritz H.G., Siegle S., Kaskel S. // J. Am. Ceram. Soc. 2010. V. 93. P. 2476–2479.
Finsy V., Ma L., Alaert L., De Vos D.E., Baron G.V., Denayer J.F.M. // Microporous Mesoporous Mater. 2009. V. 120. P. 221–227.
Singo M.C., Molepo X.C., Oluwasina O.O., Daramola M.O. // Energy Procedia. 2017. V. 114. P. 2429–2440.
Grande C.A., Agueda V.I., Spjelkavik A., Blom R. // Chemical Engineering Science. 2015. V. 124. P. 154–158.
Tabor D. The Hardness of Metals. N.Y.: Oxford University Press Inc. 1951.
Men’shchikov I.E., Fomkin A.A., Tsivadze A.Yu., Shkolin A.V., Strizhenov E.M., Pulin A.L. // Protection of Metals and Physical Chemistry of Surfaces. 2015. V. 51. № 4. P. 493–498.
Men’shchikov I.E., Fomkin A.A., Arabei A.B., Shkolin A.V., Strizhenov E.M. // Protection of Metals and Physical Chemistry of Surfaces. 2016. V. 52. № 4. P. 575–580.
Men’shchikov I.E., Fomkin A.A., Tsivadze A.Yu., Shkolin A.V., Strizhenov E.M., Khozina E.V. // Adsorption. 2017. V. 23. № 2–3. P. 327–339.
Tsivadze A.Yu., Aksyutin O.E., Ishkov A.G., Men’shchikov I.E., Fomkin A.A., Shkolin A.V., Khozina E.V., Grachev V.A. // Russian Chemical Reviews. 2018. V. 87. № 4. P. 950–983.
Дополнительные материалы отсутствуют.
Инструменты
Физикохимия поверхности и защита материалов