Физикохимия поверхности и защита материалов, 2020, T. 56, № 2, стр. 208-214
Влияние ультразвукового воздействия на физико-химические и трибологические свойства электрохимических покрытий Cu–Sn–TiO2
А. А. Касач 1, *, Д. С. Харитонов 1, 5, A. Wrzesińska 2, I. Bobowska 2, А. А. Предко 3, В. И. Романовский 1, 4, И. М. Жарский 1, И. И. Курило 1
1 Белорусский государственный технологический университет
220006 Минск, ул. Свердлова, 13а, Беларусь
2 Lodz University of Technology
90-924 Lodz, ul. Zeromskiego, 116, Poland
3 Государственное научное учреждение “Физико-технический институт Национальной академии наук Беларуси”
220141 Минск, ул. Академика Купревича, 10, Беларусь
4 Национальный исследовательский технологический университет “МИСиС”, Научно-исследовательский центр “Конструкционные керамические наноматериалы”
119049 Москва, Ленинский пр-т, 4, Россия
5 Jerzy Haber Institute of Catalysis and Surface Chemistry of Polish Academy of Sciences
30-239 Krakow, Niezapominajek 8, Poland
* E-mail: kasach2018@bk.ru
Поступила в редакцию 27.11.2018
После доработки 16.08.2019
Принята к публикации 23.08.2019
Аннотация
Композиционные покрытия Cu–Sn–TiO2 были получены из щавелевокислого электролита бронзирования, дополнительно содержащего 4 г/дм3 дисперсной фазы TiO2. Методами энергодисперсионной рентгеновской спектроскопии и рентгеннофлоуресцентного анализа установлено влияние ультразвукового воздействия, а также токовой нагрузки на включение и распределение дисперсной фазы TiO2 в металлической матрице Cu–Sn. При помощи сканирующей электронной микроскопии установлено, что наложение ультразвукового воздействия приводит к формированию более однородных покрытий Cu–Sn–TiO2. Показано, что повышение катодной плотности тока от 0.5 до 1.5 А/дм2 приводит к формированию покрытий c большим содержанием TiO2. Исследовано влияние ультразвукового воздействия и токовой нагрузки на микротвердость, трибологические свойства и коррозионную стойкость формируемых композиционных покрытий Сu–Sn–TiO2.
ВВЕДЕНИЕ
Сплавы меди с оловом, называемые оловянистые бронзы, вследствие их привлекательного внешнего вида и достаточно высокой коррозионной устойчивости широко используются в качестве защитных и декоративных покрытий [1]. Кроме того, покрытия сплавами Cu–Sn являются альтернативой никелевым покрытиям, продукты коррозии которых при контакте с кожей человека могут вызывать развитие дерматитов [2, 3].
Одним из направлений совершенствования функциональных свойств гальванопокрытий, среди которых повышение твердости и износостойкости, обеспечение самосмазывания и др., являются исследования по разработке многофазных композиционных покрытий. Композиционные электрохимические покрытия получают путем соосаждения из электролитов-суспензий, содержащих нерастворимые частицы инертной фазы [4]. В зависимости от назначения покрытий, в качестве инертной фазы предложено использовать TiO2 [5, 6], Al2O3 [7, 9], SiC [4], ZrO2 [11], MoS2 [12], УДА [13, 14] и др. На основе оловянистых бронз разработаны гальванические композиционные покрытия Сu–Sn–SiC [15], Cu–Sn–графит [16], обладающие улучшенными трибологическими и физико-механическими свойствами.
В качестве инертной фазы при получении электрохимических композиционных покрытий перспективным материалом является оксид титана(IV), который нерастворим во многих жидких средах, что позволяет использовать электролиты самого различного состава. Однако склонность к агломерации и, как следствие, низкая дисперсионная стабильность частиц TiO2 в водных растворах, вызывают определенные сложности для их включения в гальванопокрытия. Для решения этой проблемы перспективным направлением является использование соноэлектрохимического осаждения композиционных покрытий, поскольку ультразвук (УЗ) способствует деагломерации частиц инертной фазы в электролите и, следовательно, обеспечивает более равномерное распределение TiO2 в металлической матрице [5]. Кроме того, УЗ обработка приводит к существенному увеличению диапазона рабочих катодных плотностей тока [17, 18].
Ранее было исследовано влияние параметров ультразвукового поля на процесс электроосаждения сплава Cu–Sn из щавелевокислого электролита и установлено благоприятное влияние УЗ на скорость процесса и качество формируемых покрытий [18]. Целью данной работы является изучение влияния сонохимической обработки на количественный состав, морфологию, трибологические и коррозионные свойства композиционных гальванических покрытий Cu–Sn–TiO2, полученных из щавелевокислого электролита.
ЭКСПЕРИМЕНТАЛЬНАЯ ЧАСТЬ
Состав щавелевокислого электролита и технологические параметры электрохимического нанесения композиционного покрытия Cu–Sn–TiO2 представлены в табл. 1. Для приготовления электролита использовали реактивы марки х. ч.
Таблица 1.
Состав электролита и параметры электролиза для получения покрытия Cu–Sn–TiO2
Состав электролита, г/дм3 | |
---|---|
CuSO4 · 5H2O | 20 |
SnSO4 | 6 |
(NH4)2C2O4 | 55 |
C2H3O2Na | 20 |
TiO2 | 4 |
Параметры электролиза | |
Катодная плотность тока, А/дм2 | 0.5–1.5 |
pH | 5 ± 0.1 |
Температура, оС | 25 ± 1 |
В качестве инертной фазы использовали TiO2 (модификация – анатаз) с размером частиц 50–200 нм. Измерение pH проводили при помощи автотитратора TitroLine easy. Корректировку pH осуществляли 0.1 М H2SO4. Содержание ионов меди и олова в электролите корректировали по данным химического анализа. В качестве анодов использовали пластины из оловянистой бронзы (15 мас. % Sn, 85 мас. % Cu). Катодами служили заготовки из стали марки 08кп, которые предварительно последовательно обрабатывали наждачной бумагой марок Р500–P2000, подвергали обезжириванию, а затем – активации в 0.1 М H2SO4. Для обезжиривания использовали раствор следующего состава, г/дм3: Na2CO3 – 30, Na3PO4 ⋅ 12H2O – 30, СИНТАНОЛ ДС10 – 3. Площадь рабочей поверхности электродов составляла 400 мм2. В качестве источника УЗ колебаний использовали гомогенизатор ультразвуковой UP 200 Ht, оснащенный титановым генератором (рог) диаметром 12 мм. Электролиз проводили при частоте УЗ 26 кГц и выходной мощности 32 Вт/дм3. Расстояние между пьезоэлектрическим излучателем и катодом составляло 30 мм. Постоянную температуру электролита поддерживали при помощи термостата ВТ3-1. Для нанесения покрытия Cu–Sn использовали электролит состава аналогичного приведенному в табл. 1, не содержащий инертную фазу TiO2, при тех же условиях проведения процесса электроосаждения.
Состав и морфологию формируемых покрытий исследовали при помощи сканирующего электронного микроскопа JSM-5610 LV, оснащенного системой химического анализа EDX JED-2201 JEOL. Для определения содержания TiO2 в составе покрытия использовали волновой рентгенофлуоресцентный спектрометр PANalytical Axios.
Микротвердость полученных покрытий исследовали при помощи оптического микроскопа–твердомера AFRI-MVDM8. Трибологические свойства покрытий изучали при комнатной температуре с использованием трибологической испытательной машины по схеме “стержень–диск”, материал стержня – сталь ШХ 15. Нагрузка составляла 1 Н, скорость вращения контртела – 200 об./мин, радиус вращения – 10 мм.
Коррозионные исследования проводили в 3% растворе NaCl с использованием потенциостата/гальваностата Metrohm Autolab PGSTAT 302N в стандартной трехэлектродной ячейке с боковым креплением рабочего электрода, насыщенным хлоридсеребряным электродом сравнения и вспомогательным электродом в виде платиновой сетки. Потенциодинамические поляризационные кривые снимали при скорости развертки потенциала 2 мВ/с в интервале от –200 до +200 мВ относительно бестокового потенциала. Все потенциалы в работе пересчитаны в шкалу стандартного водородного электрода. Определение электрохимических параметров коррозии проводили с использованием алгоритма Левенберга–Марквардта в программном обеспечении CorrView 3.2c.
ОБСУЖДЕНИЕ РЕЗУЛЬТАТОВ
В отсутствие сонохимической обработки щавелевокислого электролита (стационарные условия) качественные блестящие покрытия Сu–Sn формируются при катодной плотности тока 0.5 А/дм2. Наложение УЗ поля мощностью 32 Вт/дм3 позволяет расширить диапазон рабочих катодных плотностей тока от 0.5 до 1.5 А/дм2 и способствует формированию полублестящих покрытий. Повышение плотности тока более 1.5 А/дм2 приводит к снижению катодного выхода по току сплава, а также к уменьшению адгезии покрытия к подложке вследствие интенсивного выделения водорода. В табл. 2 представлен качественный и количественный состав по данным метода рентгенофлуоресцентного анализа композиционных покрытий Cu–Sn–TiO2, полученных при различных токовых нагрузках без и при УЗ воздействии.
Таблица 2.
Влияние режимов электроосаждения на состав покрытий Cu–Sn–TiO2
Плотность тока, А/дм2 | Мощность УЗ, Вт/дм3 | Содержание в покрытии, мас. % | ||
---|---|---|---|---|
TiO2 | Cu | Sn | ||
0.5 | – | 0.30 | 63.20 | 36.50 |
0.5 | 32 | 0.10 | 74.70 | 25.20 |
1 | 32 | 0.12 | 66.20 | 33.68 |
1.5 | 32 | 0.20 | 65.30 | 34.20 |
В стационарных условиях при катодной плотности тока 0.5 А/дм2 формируются покрытия, содержащие 63.2 маc. % меди и 36.5 маc. % олова. Наложение УЗ при данной плотности тока, как показано в работе [18], приводит к формированию сплава при более низких перенапряжениях и, вследствие этого, к снижению содержания олова до 25.2 мас. %. По мере повышения токовой нагрузки наблюдается увеличение содержания олова в формируемом покрытии, что обусловлено ростом катодной поляризации. В отсутствие УЗ обработки при катодной плотности тока 0.5 А/дм2 количественное содержание наноразмерных частиц TiO2 в металлической матрице составило 0.3 мас. %, а в условиях соноэлектрохимического осаждения наблюдается снижение количества TiO2 в покрытии до 0.1 мас. %. Повышение катодной плотности тока приводит к увеличению содержания TiO2 в покрытии. Так, при катодной плотности тока 1.5 А/дм2 формируются покрытия, включающие до 0.2 мас. % TiO2. Снижение количества TiO2 в покрытиях Cu–Sn–TiO2 полученных соноэлектрохимическим способом, по-видимому, обусловлено кавитационными явлениями, которые препятствуют включению крупных агломератов в матрицу сплава [19, 20].
На рис. 1 представлены микрофотографии покрытий Сu–Sn (рис. 1а) и Cu–Sn–TiO2 (рис. 1б–1д), полученных из исследуемого щавелевокислого электролита без и при наложении УЗ поля. В стационарных условиях из электролита, не содержащего TiO2, при катодной плотности тока 0.5 А/дм–2 формируются качественные, гладкие покрытия. Введение наночастиц TiO2 в электролит способствует формированию осадков с более крупнокристаллической структурой. В условиях соноэлектрохимического осаждения наблюдается формирование более мелкокристаллических покрытий с меньшим количеством дефектов. Это объясняется тем, что УЗ воздействие за счет возникновения в электролите кавитационных явлений способствует десорбции крупных агломератов с поверхности электрода и, вследствие этого, формированию более равномерных покрытий. При сонохимической обработке наиболее качественные покрытия получаются при катодной плотности тока 1 А/дм2.
Рис. 1.
Микрофотографии покрытий Cu–Sn (a) и Cu–Sn–TiO2 (б–д), полученных без УЗ обработки (а, б) и при наложении УЗ колебаний мощностью 32 Вт/дм3 (в–д). Катодная плотность тока, А/дм2: (а–в) – 0.5; (г) – 1; (д) – 1.5.
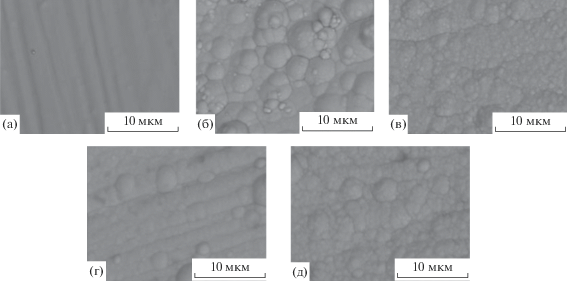
Для оценки влияния УЗ обработки на распределение TiO2 по поверхности осажденного композиционного покрытия Cu–Sn–TiO2 был проведен количественный EDX-анализ поверхности по линии, пересекающей характерные участки осажденных покрытий (рис. 3). Установлено, что TiO2 включается в структуру покрытий в виде агломератов (рис. 2а, 2в), при этом УЗ обработка во время электроосаждения способствует уменьшению их размеров (рис. 2б, 2г).
Рис. 2.
СЭМ изображения поверхности покрытий Cu–Sn–TiO2, полученных в стационарных условиях (а) и при УЗ воздействии (б) (катодная плотность тока 0.5 А/дм2), и результаты количественного EDX анализа (в, г) по линейным профилям, показанным на (а, б). Профили над линиями на (а, б) соответствуют распределению титана.
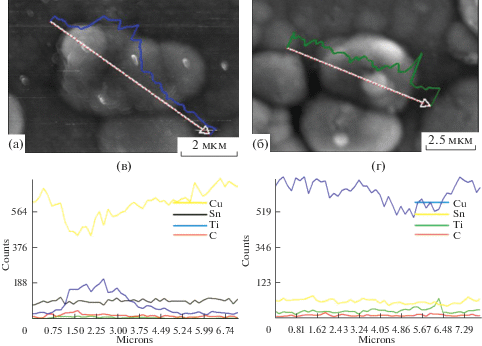
Рис. 3.
Зависимость коэффициента трения Ктр от времени износа покрытий Cu–Sn (a) и Сu–Sn–TiO2 (б–г), полученных в стационарных условиях (а, б) и при наложении УЗ мощностью 32 Вт/дм3 (в, г). Катодная плотность тока, А/дм2: (а–в) – 0.5; (г) – 1.
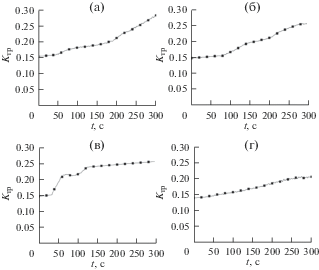
В табл. 3 представлены значения микротвердости покрытий Cu–Sn и Cu–Sn–TiO2 полученных при различных токовых нагрузках и при воздействии УЗ поля. При катодной плотности тока 0.5–1.5 А/дм2 из электролита, не содержащего дисперсную фазу TiO2, вне зависимости от наличия УЗ обработки формируются покрытия Сu–Sn с микротвердостью 300–317 HV. Из электролита, содержащего частицы TiO2, при катодной плотности тока 0.5 А/дм2 в стационарных условиях и в УЗ поле формируются покрытия Cu–Sn–TiO2 с микротвердостью 352 и 367 HV соответственно. Увеличение микротвердости покрытий при введении в электролит TiO2, по-видимому, объясняется так называемым эффектом дисперсионного упрочнения [20–22]. Дисперсионное упрочнение обусловлено распределением в металлической матрице частиц TiO2, которые препятствуют движению дислокаций в структуре сплава, что, в свою очередь, приводит к возрастанию микротвердости покрытия. Тот факт, что покрытия Сu–Sn–TiO2, полученные соноэлектрохимическим способом, несмотря на более низкое содержание TiO2 и олова, обладают более высокими значениями микротвердости по сравнению с покрытиями, полученными в стационарных условиях, вероятно, можно объяснить более равномерным распределением TiO2 в матрице сплава при наложении УЗ поля (рис. 2).
Таблица 3.
Микротвердость покрытий Cu–Sn и Cu–Sn–TiO2
Покрытие | Мощность УЗ, Вт/дм3 | Плотность тока, А/дм2 | Микротвердость, HV |
---|---|---|---|
Сu–Sn | – | 0.5 | 315 |
32 | 0.5 | 300 | |
32 | 1.0 | 317 | |
32 | 1.5 | 316 | |
Сu–Sn–TiO2 | – | 0.5 | 352 |
32 | 0.5 | 362 | |
32 | 1 | 372 | |
32 | 1.5 | 380 |
Зависимости коэффициента трения (Kтр) полученных покрытий от времени испытаний без смазочного материала представлены на рис. 3. На начальном этапе испытаний коэффициент трения покрытий Cu–Sn, полученных в стационарных условиях при плотности тока 0.5 А/дм2 (рис. 3а), составлял около 0.15. Дальнейшее увеличение времени испытаний покрытий Cu–Sn в диапазоне 50–175 с характеризуется монотонным возрастанием значений Kтр от 0.17 до 0.20, а в диапазоне 175–300°C – от 0.20 до 0.28. Для покрытий Cu–Sn–TiO2 (рис. 3б–3д) зависимость коэффициента трения от времени испытаний существенно отличается. Так для композиционного покрытия, полученного в стационарных условиях при катодной плотности тока 0.5 А/дм2, во время испытаний в диапазоне 50–125°C наблюдается резкое увеличение значений Kтр от 0.15 до 0.23, что связано с более выраженной неоднородностью структуры композиционных покрытий (рис. 1б). Однако при дальнейшем увеличении времени испытаний значение коэффициента трения практически не изменяется и через 300 с составляет 0.25, что свидетельствует о более низком износе композиционных покрытий по сравнению со сплавом Сu–Sn.
При одинаковом времени испытаний покрытия Сu–Sn–TiO2, полученные соноэлектрохимическим способом, характеризуются более низкими значениями коэффициента трения по сравнению с образцами, полученными в стационарных условиях при той же токовой нагрузке. Увеличение плотности тока от 0.5 до 1.0 А/дм2 также приводит к существенному снижению Kтр. Полученные закономерности можно объяснить, с одной стороны, относительно равномерным включением в металлическую матрицу частиц TiO2 меньшего размера за счет их диспергирования при наложении УЗ; с другой стороны – формированием более гладких осадков с более высоким содержанием олова в сплаве (рис. 1в, 1г) [18].
Результаты коррозионных исследований, полученных покрытий Cu–Sn и Cu–Sn–TiO2 в 3%-ном растворе NaCl представлены на рис. 4. Рассчитанные по данным потенциодинамической поляризации параметры процесса коррозии исследуемых покрытий представлены в табл. 4.
Рис. 4.
Потенциодинамические поляризационные кривые в 3% растворе NaCl покрытий Cu–Sn (1) и Сu–Sn–TiO2 (2–5), полученных в стационарных условиях (1, 2) и при наложении УЗ мощностью 32 Вт/дм3 (3–5). Катодная плотность тока, А/дм2: 1, 2, 3 – 0.5; 4 – 1; 5 – 1.5.
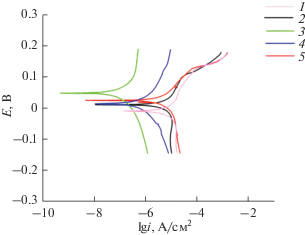
Таблица 4.
Параметры электрохимического процесса, полученные из анализа потенциодинамических поляризационных кривых
Покрытие | Мощность УЗ, Вт/дм3 | Плотность тока электроосаждения, А/дм2 | iкор, мкА/см2 |
---|---|---|---|
Cu–Sn | – | 0.5 | 2.10 |
Cu–Sn–TiO2 | – | 0.5 | 0.90 |
32 | 0.5 | 0.03 | |
32 | 1.0 | 0.12 | |
32 | 1.5 | 1.80 |
Из анализа коррозионных кривых на рис. 4 и данных табл. 4 видно, что потенциал коррозии для всех исследованных композиционных покрытий Cu–Sn–TiO2 смещается в электроположительную сторону по сравнению с покрытием Cu–Sn. Это, наиболее вероятно, обусловлено химической инертностью дисперсной фазы и формированием покрытий с более высоким содержанием электроположительного компонента сплава (Сu).
Для покрытия Cu–Sn, полученного в стационарных условиях (рис. 4, кривая 1), рассчитанное значение плотности тока коррозии составило 2.10 мкА/см2. На анодных участках поляризационных кривых присутствует активно-пассивная область, отвечающая формированию на поверхности исследуемых образцов адсорбированного слоя малорастворимых продуктов коррозии. Растворение основного компонента сплава (меди) в хлоридсодержащей среде может протекать через стадию образования иона Cu+ по реакциям [21–24]:
либо прямой ионизацией по схеме:При высоких концентрациях хлорид-ионов в приэлектродном слое возможно образование ионов CuCl–, которые взаимодействуя с молекулами воды образуют на поверхности образца слой малорастворимого Cu2O [21]:
(4)
${\text{CuC}}{{{\text{l}}}^{ - }} + {{{\text{H}}}_{{\text{2}}}}{\text{O}} \to {\text{ C}}{{{\text{u}}}_{{\text{2}}}}{\text{O + }}2{{{\text{H}}}^{ + }} + 4{\text{C}}{{{\text{l}}}^{ - }},$Для покрытий Cu–Sn–TiO2 поляризационные зависимости носили аналогичный характер. Введение в электролит дисперсной фазы анатаза приводит к формированию композиционных покрытий Cu–Sn–TiO2 (рис. 4, кривая 2) с большей коррозионной стойкостью, чем у полученных при аналогичных условиях покрытий Cu–Sn. Уменьшение значений плотности тока коррозии композиционных покрытий обусловлено тем, что TiO2, как указано выше, способствует дисперсионному упрочнению металлической матрицы уменьшая ее коррозионное разрушение и ускоряя формирование на поверхности пассивирующей оксидной пленки. Для покрытий Cu–Sn–TiO2, осажденных в стационарных условиях, значение плотности тока коррозии составило 0.90 мкА/см2.
Для образцов композиционных покрытий, полученных в условиях сонохимической обработки при той же токовой нагрузке наблюдались наименьшие значения плотности тока коррозии (0.03 мкА/см2). Увеличение плотности тока осаждения сплава Cu–Sn–TiO2 приводит к ускорению осаждения электроотрицательного компонента сплава (олова), чем объясняется обнаруженное возрастание плотности тока коррозии данных образцов (табл. 4).
ВЫВОДЫ
1. Введение в щавелевокислый электролит дисперсной фазы анатаза к количестве 4 г/дм3 в отсутствии УЗ воздействия проводит к формированию композиционных покрытий Cu–Sn–TiO2, содержащих 63.2 мас. % меди, 36.5 мас. % олова и 0.3 мас. % оксида титана(IV). В условиях соноэлектрохимического осаждения кавитационные явления препятствуют включению в состав покрытия крупных агломератов TiO2 и способствуют деполяризации катода, что, приводит к уменьшению содержания олова (до 25.2–34.2 мас. %) и оксида титана(IV) (до 0.1–0.2 мас. %) в составе композиционного покрытия.
2. Сонохимическое воздействие в процессе электролиза способствует увеличению диапазона рабочих плотностей тока до 0.5–1.5 А/дм2 и формированию более равномерных мелкокристаллических композиционных покрытий Cu–Sn–TiO2 с меньшим количеством дефектов по сравнению с образцами, полученными без наложения УЗ.
3. Покрытия Cu–Sn–TiO2 за счет дисперсионного упрочнения, а также изменения состава матричного сплава обладают более высокими значениями микротвердости, износостойкости и коррозионной устойчивости по сравнению с покрытиями Cu–Sn, полученными в аналогичных условиях.
Список литературы
Bengoa L.N., Tuckar W.R.T, Zabala N., Egli W.A. // Surf. Coat. Tech. 2014. V. 253. P. 241–248.
Hovestad A., Tacken R.A., Mannetje H.H. // Physica Status Solidi. 2008. V. 5. P. 3506–3509.
Jung M., Lee G., Choi J. // Electrochim. Acta. 2017. V. 241. P. 229–236.
Walsh F.C., de Leon C.P. // Transactions of the IMF. 2014. V. 92. P. 83–98.
Baghery P., Farzam M., Mousavi A.B., Hosseini M. // Surf. Coat. Tech. 2010. V. 204. P. 3804–3810.
Васильева Е.А., Цуркан А.В., Проценко В.С., Данилов Ф.И. // Физикохимия поверхности и защита материалов. 2016. Т. 52. С. 331–336. (Vasil’eva E.A., Tsurkan A.V., Protsenko V.S., Danilov F.I. Prot. Met. Phys. Chem. Surf. 2016. V. 52. P. 532–537.)
Rezaeiolum A., Aliofkhazraei Karimzadeh M. et al. // Surf. Eng. 2017. V. 34. P. 423–432.
Aruna S., Srinivas G. // Surf. Eng. 2015. V. 31. P. 708–713.
Lajevardi S., Shahrabi T., Szpunar J. // Appl. Surf. Sci. 2013. V. 279. P. 180–188.
Velichenko A.B., Knysh V.A., LukYanenko T.V. et al. // Russ. J. Electrochem. 2008. V. 44. P. 1251–1256.
Bogomazova N.V., Antikhovich I.V., Chernik A.A., Zharskii I.M. // Russ. J. App. Chem. 2014. V. 87. P. 1235–1239 (Богомазова Н.В., Антихович И.В., Черник А.А., Жарский И.М. // ЖПХ. 2014. Т. 87. № 9. С. 1239–1243).
Zhou N., Wang S., Walsh F.C. // Electrochim. Acta. 2008. V 283. P. 568–577.
Yaskel’chik V.V., Anan’ev M.V., Ostanina T.N. et al. // Izv. Vyssh. Uchebn. Zaved., Powder Metall. Funct. Coatings, 2017. № 4. P. 53–61.
Chayeuski V.V., Zhylinski V.V., Rudak P.V. et al. // Appl. Surf. Sci. 2018. P. 18–26.
Cui G., Bi Q., Niu M. et al. // Tribol. Int. 2013. V. 60. P. 25–35.
Nickchi T., Ghorbani M. // Surf. Coat. Tech. 2009. V. 203. P. 3037–3043.
Kasach A.A., Kurilo I.I., Kharitonov D.S. et al. // Russ. J. Appl. Chem. 2018. V. 91. P. 207–213 (Касач А.А., Курило И.И., Харитонов Д.С. и др. // ЖПХ. 2018. Т. 91. № 2. С. 192–198).
Kasach A.A., Kurilo I.I., Kharitonov D.S. et al. // Russ. J. Appl. Chem. 2018. V. 91. P. 591–596 (Касач А.А., Курило И.И., Харитонов Д.С. и др. // ЖПХ. 2018. Т. 91. № 4. С. 522–527).
Lampke T., Dietrich D., Leopold A. et al. // Surf. Coat. Tech. 2008. V. 202 P. 3967–3934.
Wielage B., Lampke T., Zacher M., Dietrich D. // Key Eng. Mat. 2008. V. 384 P. 283–309.
Metikoš-Huković M., Babić R., Škugor I., Grubač Z. // Corr. Sci. 2011. V. 53. P. 347–352.
Ma A.L., Jiang S.L., Zheng Y.G., Ke W. // Corr. Sci. 2015. V. 91. P. 245–261.
Thurber C.R., Ahmad Y.H., Sanders S.F. et al. // Current Appl. Physics. 2016. V. 16. P. 387–396.
Metikoš-Huković M., Škugor I., Grubač Z., Babić R. // Electrochim. Acta. 2010. V. 55. P. 3123–3129.
Дополнительные материалы отсутствуют.
Инструменты
Физикохимия поверхности и защита материалов