Физикохимия поверхности и защита материалов, 2020, T. 56, № 2, стр. 202-207
Оксидирование стали AISI 304 в Al-, Ti-содержащих растворах
В. В. Штефан 1, *, Н. А. Канунникова 1, **
1 Национальный технический университет “Харьковский политехнический институт” МОН Украины
61002 Харьков-2, ул. Кирпичева, 2, Украина
* E-mail: vvshtefan@ukr.net
** E-mail: nadiia.ka13@gmail.com
Поступила в редакцию 11.02.2019
После доработки 12.09.2019
Принята к публикации 19.09.2019
Аннотация
Исследование посвящено изучению влияния состава электролита на анодное поведение нержавеющей стали. Изучена морфология и рентгенофазовый состав оксидных покрытий, полученных в Al-, Ti-содержащих электролитах. Электрическая проводимость и дефектность покрытий изучена методом импедансной спектроскопии. Установлено, что введение в состав покрытий оксидов алюминия или титана снижает скорости коррозии стали в хлоридных средах.
ВВЕДЕНИЕ
В настоящее время в химической промышленности и атомной энергетике активно применяется оборудование и трубопроводы из высоколегированных сталей аустенитного класса AISI 304 [1–3]. Их применение обусловлено наличием хорошей коррозионной стойкости в широком диапазоне условий, поскольку при взаимодействии с водными растворами на поверхности нержавеющих сталей образуются пассивные пленки, представляющие собой смесь оксидов железа и хрома. Эти пленки невидимы, стабильны, тонкие и самовосстанавливающиеся. Однако устойчивость пассивных пленок определяется условиями окружающей среды [4, 5].
При эксплуатации оборудования и трубопроводов из нержавеющей стали наблюдались узкие и локализованные повреждения в виде питтингов [6–8]. Выводя из строя приборы и аппараты, стоимость которых превышает часто в сотни и тысячи раз стоимость самих металлов, из которых они изготовлены, влечет за собой нарушения технологических процессов, остановку работы оборудования, сбой функционирования сооружений и, как следствие, техногенные аварии [9, 10]. Интерес к этому опасному и не поддающемуся непрерывному наблюдению виду коррозии отражается в расширяющемся за последнее 10–20 лет объему литературы, посвященной ее механизму, методам защиты и ускоренным испытаниям на стойкость против нее [4, 7–9].
Одним из распространенных и доступных методов защиты от коррозии нержавеющей стали является метод электрохимического оксидирования, позволяющий сформировать оксидные покрытия на металлах или сплавах. Преимущества этого метода состоит в том, что анодирование сталей не вызывает водородного охрупчивания и при этом размеры деталей существенно не изменяются [11–14]. Согласно литературным данным [15–18] оксидные пленки на стали AISI 304, полученные в 5 M H2SO4 при 50°C, в своей структуре преимущественно содержат FeO и имеют недостатки, если их сравнивать с пленками на титане, цирконии, тантале и других “вентильных” металлах. Они пористые, что ограничивает их использование как защитных покрытий [18]. Модифицирование оксидных покрытий соединениями металлов и неметаллов давно используется и приводит к улучшению заданных свойств композиционных материалов [19–22]. Введение соединений алюминия и титана в состав пленок позволит изменить структуру оксидов, что отразится на морфологии и защитных свойствах покрытий.
Целью данной работы является исследование анодного поведения стали AISI 304 в растворах H2SO4 и NaCl с добавками Al2(SO4)3 ⋅ 18H2O, TiOSO4; изучение морфологии, фазового состава, а также дефектности, электрической проводимости, противокоррозионных свойств полученных оксидных покрытий методами импедансной спектроскопии и линейной вольтамперометрии.
МЕТОДИКА ЭКСПЕРИМЕНТА
Синтез покрытий
В качестве образцов использовали пластины из стали AISI 304 (0.08% C, 17–19% Cr, 69% Fe, 9–11% Ni, ≤0.8 Si%, ≤0.2% Mn) с площадью поверхности 4 см2.
Формирование оксидных покрытий осуществляли в гальваностатическом режиме при плотности тока 8 А/дм2 в течении 25 мин в электролитах, приведенных в табл. 1. В качестве катода использовали платиновую нить. Анод – сталь AISI 304. Процесс проводили в ячейке с рабочим объемом 200 мл при непрерывном перемешивании. Температура электролита 50–55°С.
Таблица 1.
Результаты поляризационных исследований стали AISI 304 в кислых растворах
№ п/п | Состав электролита с, г/л |
Электрохимические параметры | Плотность тока коррозии | |||||
---|---|---|---|---|---|---|---|---|
Ej = 0, мВ | Еp, мВ | jp, мА см–2 | Еpp, мВ | jpp, мА см–2 | ${{Е}_{{{{{\text{О}}}_{{\text{2}}}}}}}$, мВ | jк, мкА/см2 | ||
1 | 300H2SO4, 50NaCl | –540 | –490 | 52 | –228 | 0.5 | 825 | 2.5 × 10–3 |
2 | 300H2SO4, 50NaCl, 10Al2(SO4)3 · 18H2O |
–473 | –414 | 168 | –177 | 0.2 | 885 | 6.5 × 10–6 |
3 | 300H2SO4, 50NaCl, 10TiOSO4 |
–407 | –323 | 187 | –130 | 35 | 936 | 3.2 × 10–4 |
Электрохимические методы исследования
Анодные поляризационные зависимости получали с помощью потенциостата IPC-pro со скоростью развертки потенциала 2 мВ/с. В качестве рабочего электрода использовалась сталь AISI 304. Вспомогательным электродом служила платиновая нить. Контроль потенциала осуществляли по хлорсеребряному электроду.
Исследования электрохимического импеданса и коррозионные испытания проводили на полученных оксидных покрытиях стали AISI 304 в 3% растворе NaCl. Измерения электрохимического импеданса выполнили с помощью потенциостата IPC-pro и частотного анализатора FRA. Диапазон частот составлял от 0.03 Гц до 50 кГц по последовательной схеме замещения [19, 22]. Для коррозионных испытаний поляризацию рабочего электрода осуществляли в области ±100 мВ от стационарного потенциала, выдержанного в течение 1 ч в растворе.
Физико-химические методы исследования
Исследования морфологии полученных покрытий осуществляли с помощью металлографического микроскопа ZEISSAxio с цифровой видеокамерой AxioCamMRc 5, обеспечивающего увеличение в 50–1000 раз. Исследования фазового состава полученных покрытий проводили на рентгеновском дифрактометре ДРОН-3.0 (CuKα-излучение).
РЕЗУЛЬТАТЫ И ОБСУЖДЕНИЕ
Поляризационные исследования
Характер зависимости электродного потенциала от времени экспозиции нержавеющей стали и от состава раствора предоставляют целый ряд важных сведений об анодном поведении металлов и сплавов. Хронопотенциограммы стали AISI 304 в кислых растворах при добавлении Al2(SO4)3 · 18H2O, TiOSO4 в электролит № 1 (табл. 1) демонстрирует, что потенциал (Ej = 0) смещается в электроположительную сторону (рис. 1). Дальнейшее увеличение продолжительности времени экспозиции стали в растворах не влияет на величину стационарного потенциала.
Процесс формирования оксидных покрытий в Al-, Ti-содержащих растворах исследован с помощью метода линейной вольтамперометрии (ЛВА). Анодные поляризационные зависимости стали AISI 304 имеют классический вид для металлов и сплавов склонных к пассивности (рис. 2). Характер и устойчивость пассивного состояния в зависимости от состава электролита весьма различны. Это иллюстрируется анализом реальных анодных поляризационных зависимостей [23].
При анодной поляризации начинается процесс растворения стали, которому отвечает резкий подъем плотности тока. Растворение железа и хрома описываются уравнениями:
Вследствие чего приэлектродный слой обогащается катионами Fe2+, Cr2+. Поскольку катионы железа, хрома нестабильны, то они быстро окисляются до Fe3+ и Cr3+. Так как, стандартные потенциалы для системы Fe2+/Fe, Cr2+/Cr, Cr2+/Cr3+ имеют более электроотрицательные значения, нежели водородный и кислородный электроды, что создает условия для образования ди- и триоксидов металлов.
В растворах № 2, 3 плотность тока пассивации (jp) намного выше, чем в растворе № 1 (табл. 1), что указывает на влияние соединений алюминия и титана на процесс образования кислородсодержащих поверхностных пленок.
При дальнейшем смещении потенциала в анодную область ток резко падает, и поверхность нержавеющей стали переходит в пассивное состояние (Еpp – ${{Е}_{{{{{\text{О}}}_{{\text{2}}}}}}}$). В этой области происходит перестроение структуры поверхностных слоев и электрохимическое образование пассивной оксидной пленки. Значения плотности токов полной пассивации (jpp) указывает, что наличие в составе пассивной пленки оксида титана увеличивает ее проводимость, а оксида алюминия незначительно снижает.
При достижении ${{Е}_{{{{{\text{О}}}_{{\text{2}}}}}}}$ происходит резкое увеличение силы тока, что отвечает началу выделения кислорода. На зависимостях (2) и (3) ${{Е}_{{{{{\text{О}}}_{{\text{2}}}}}}}$ наступает позже, что доказывает влияние состава электролита на протяжность области пассивности стали.
Поляризационные зависимости стали AISI 304 с оксидными покрытиями (рис. 3), полученные в 3% NaCl, указывают, что введение в состав покрытий алюминий-, титансодержащих соединений смещает потенциал коррозии в электроположительную сторону.
Рис. 3.
Поляризационные зависимости в 3% NaCl стали AISI 304 с оксидными покрытиями, полученными в растворах: 1 – без покрытия, 2 – № 1, 3 – № 2, 4 – № 3.
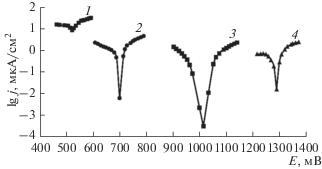
Экспериментальное определение плотности тока коррозии (jk) из тафелевских координат Е-lg j в точке пересечения линейных участков анодных и катодных поляризационных зависимостей при потенциале коррозии, показало увеличение защитных свойств (табл. 1) для покрытий, полученных в электролитах № 2, 3. Низкая скорость коррозии наблюдается для алюминийсодержащих оксидных покрытий, что полностью согласуется с результатами ЛВА.
Импедансная спектроскопия
Согласно научным работам авторов [24], импедансный спектр системы “металл–оксид–электролит” на примере тантала в кислых растворах описывается уравнением:
(1)
$\begin{gathered} Z = r - \frac{1}{{\omega {{C}_{0}}}}\frac{1}{{1 + {{{\left( {\frac{1}{{\omega {{C}_{0}}{{R}_{y}}}} + {\text{tg}}{{\delta }_{0}}} \right)}}^{2}}}} \times \\ \times \,\,\left( {\frac{1}{{\omega {{C}_{0}}{{R}_{y}}}} + {\text{tg}}{{\delta }_{0}} + j} \right), \\ \end{gathered} $Для последовательных эквивалентных емкости Cs и сопротивления Rs систем “металл–оксид–электролит” зависимости 1/Cs ~ lg f и Rs ~ 1/f линейны. Отсюда следует, что тангенс угла диэлектрических потерь tg δ = ωRsCs, должен очень слабо изменяться с изменением частоты, т.е. tg δ = = ωRsCs ≈ const, что подтверждается экспериментально для тантала и алюминия, титана [14, 24].
В данной работе были определены параметры импеданса из экспериментальной графика зависимости tg δ от частоты (рис. 4) и Rs по формулам, приведенным в [24]:
где tgδ – тангенс угла активных потерь.Рис. 4.
Зависимость tg δ от частоты для оксидных покрытий, полученных в растворах: 1 – без покрытия, 2 – № 1, 3 – № 2, 4 – № 3.
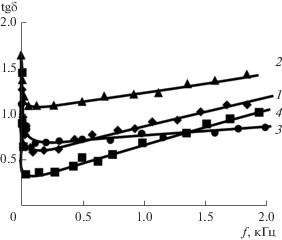
Эквивалентное последовательное сопротивление для покрытий с малым числом дефектов
где r – сопротивление слоя электролита между электродами.На графике и в таблице вместо круговой частоты ω стоят частоты f в Гц.
График зависимости tg δ от частоты представленный на рис. 3 полностью соответствует уравнению (1).
Значения tg δ0 найденные экстраполяцией линейной части зависимости tg δ ~ f к нулю (рис. 4) и по наклону прямых Rs ~ 1/f (рис. 5) близки по значению, что есть доказательством точности полученных расчетов. Так, например, для покрытия, полученного из электролита № 2, значение tg δ0, рассчитанное экстраполяцией правой ветви зависимости tg δ ~ f к нулю, равно 0.672, а значение tg δ0, рассчитанное по наклону прямых Rs ~ 1/f, равно 0.677.
Рис. 5.
Зависимость эквивалентного последовательного сопротивления Rs от частоты для оксидных покрытий, полученных в растворах: 1 – без покрытия, 2 – № 1, 3 – № 2, 4 – № 3.
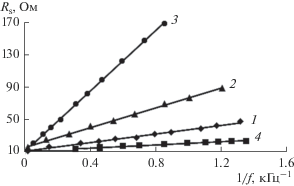
Покрытие, полученное из электролита № 1 обладает большим количеством дефектов, об этом свидетельствует повышенное значение tg δ0. Введение в состав покрытий Ті-содержащих соединений приводит к увеличению значения Ry, а Al-содержащих – к резкому увеличению сопротивления Ry (табл. 2). Это указывает на уменьшение дефектности алюминий-, титансодержащих оксидных покрытий по сравнению с покрытием, полученного из электролита № 1.
Таблица 2.
Зависимость параметров системы “металл–оксид–электролит” от состава электролита
№ | r, Ом | Ry, кОм | С0, мкФ | fmin, Гц | tg δ0 |
---|---|---|---|---|---|
Без покрытия | 9.9 | 3.01 | 39.8 | 140 | 0.636 |
1 | 13.25 | 14.72 | 26.4 | 130 | 1.035 |
2 | 8.7 | 975.55 | 58.03 | 125 | 0.672 |
3 | 9.46 | 55.84 | 53.9 | 120 | 0.33 |
Незначительный рост tg δ0 наблюдается, при исследовании полученного покрытия из алюминийсодержащего раствора, что объясняется наличием дефектов в оксидной пленке, но их малое количество не определяет общие сопротивление Ry. Значения tg δ0 и Ry указывают на формирование оксидных покрытий более совершенной структуры. Полученные данные полностью подтверждают результаты коррозионных испытаний.
Морфология полученных покрытий
На рис. 6 представлены микрофотографии поверхности образцов стали AISI 304 с оксидными покрытиями, полученные методом электрохимического оксидирования (увеличение в 500 раз). При введении Al2(SO4)3 ⋅ 18H2O, TiOSO4 к электролиту № 1 на микрофотографии наблюдается более мелкая глобулярная морфология покрытий, а размеры глобул составили 1–3 мкм, что отражается на плохой электрической проводимости оксидного слоя.
РФА
Как показал рентгенофазовый анализ, покрытия состоят в основном из оксидов железа, а также были обнаружены фазы FeAl2O4, Al2O3, Ni2Al18O29 (рис. 7); CrTiO5, CrTiO3, TiO2, Ni2TiO4 (рис. 8). Образование оксидов алюминия и титана различных степеней окисления уменьшает дефектность, электрическую проводимость оксидных покрытий, что подтверждают результаты импедансной спектроскопии и коррозионных испытаний. Структура покрытий кристаллическая.
ЗАКЛЮЧЕНИЕ
Методом линейной вольтамперометрии исследовано анодное поведение стали AISI 304 в кислых растворах, содержащих соединения алюминия и титана.
Сформированы оксидные покрытия из кислых электролитов методом электрохимического оксидирования с последующим изучением морфологии и фазового состава. Установлено, что введение Al2(SO4)3 ⋅ 18H2O, TiOSO4 в состав покрытий существенно влияет на морфологию поверхности формируемых покрытий.
Согласно полученным результатам РФА, в составе оксидных покрытий преобладают оксиды железа, однако, в покрытиях, сформированных в Al-, Ti-содержащих растворах присутствуют оксиды алюминия и титана.
Для исследования свойств оксидных покрытий применен метод импедансной спектроскопии и проведены коррозионные испытания. Установлено, что введение в состав покрытий оксидов алюминия и титана уменьшает дефектность, электрическую проводимость оксидных пленок, а также существенно снижает скорости коррозии в хлоридных средах.
Результаты всех проведенных исследований показывают целесообразность введения в состав покрытий Al- и Ti-содержащих соединений для повышения защитных свойств стали AISI 304.
Список литературы
Taveira L.V. et al. // Corrosion Science. 2010. V. 52. P. 2813–2818.
Зубченко А.С. // Автоматическая сварка. 2008. № 11. С. 208–213.
Ajeel S.A. et al. // Mechanical Engineering and Technology (IJMET). 2013. V. 4. № 3. P. 63–74.
Zhan-wen Wu et al. // Transactions of Nonferrous Metals Society of China. 2014. V. 24. P. 1989−1994.
Krouse D. et al. // Corrosion engineering science and technology. 2014. V. 49. P. 521.
Наривский А.Э., Солидор Н.А. // Вісник ПДТУ. 2011. Т. 23. № 2. С. 87–97.
Cavanaugh M.K. et al. // Corrosion Science. 2010. V. 52. P. 3070.
Chen Y.Y. et al. // Materials Chemistry and Physics. 2006. V. 96. P. 37–49.
Белоус В.Я., Гурвич Л.Я., Ерофеева В.Л. и др. // Защита металлов. 1995. Т. 31. № 2. С. 184–190.
Варченко Е.А., Курс М.Г. // Труды ВИАМ. 2018. Т. 67. № 7. С. 96–105.
Nishimura R. // Corrosion Science. 2007. V. 49. P. 81–91.
Saifu D. et al. // International J. Electrochemical Science. 2017. V. 12. P. 1106–1117.
Aydogbu G.H. et al. // Corrosion Science. 2006. V. 48. P. 3565–3583.
Bellezze T. et al. // Materials and Corrosion. 2008. V. 59. № 9. P. 727–731.
Vasconcelos K.O. et al. // J. Brazilian Chemical Society. 2010. V. 21.3. P. 469–475.
Shtefan V.V., Smyrnov O.O., Bezhenko A.O. et al. // Materials Science. 2019. V. 54. № 4. P. 512–518.
Пат. Украина 119022 (опубл. 2019). Способ электрохимического оксидирования нержавеющей стали.
Мирзоев Р.А., Давыдов А.Д. Анодные процессы электрохимической и химической обработки металлов. СПб.: Изд-во Политехн. ун-та, 2013. С. 382.
Shtefan V.V., Smirnova A.Y. // Russian J. Electrochemistry. 2015. V. 51. № 12. P. 1168–1175.
Смирнова А.Ю., Штефан В.В. // Коррозия: материалы, защита. 2014. № 8. С. 14–19.
Shtefan V.V., Bairachnyi B.I., Lisachuk G.V. et al. // Materials Science. 2016. V. 51. № 5. P. 711–718.
Shtefan V.V., Smirnova A.Y. // Protection of Metals and Physical Chemistry of Surfaces. 2017. V. 53. № 2. P. 322–328.
Shtefan V., Kanunnikova N., Pilipenko A. et al. // Materials Today: Proceedings. 2019. V. 6. № P2. P. 149–156.
Одынец Л.Л., Прохорова Л.А., Чекмасова С.С. // Электрохимия. 1974. Т. 10. № 8. С. 1225–1228.
Дополнительные материалы отсутствуют.
Инструменты
Физикохимия поверхности и защита материалов