Физикохимия поверхности и защита материалов, 2020, T. 56, № 2, стр. 192-196
О стойкости в хлорсодержащей среде покрытий ZrO2 + TiO2 на титане, сформированных плазменно-электролитическим оксидированием
И. В. Малышев 1, *, В. С. Руднев 1
1 Институт химии Дальневосточного отделения Российской академии наук
690022 Владивосток, проспект 100-летия Владивостока, 159, Россия
* E-mail: malishev@ich.dvo.ru
Поступила в редакцию 04.12.2018
После доработки 14.11.2019
Принята к публикации 21.11.2019
Аннотация
Изучены закономерности влияния длительности гальваностатического формирования покрытий в электролите Zr(SO4)2 на их состав, строение, угол смачивания поверхности водой и время возникновения электростимулированного питтинга при контакте образцов с водным раствором NaCl. Показано, что с точки зрения противокоррозионных свойств представляют интерес покрытия, сформированные на титане в области перехода от стадии искрения к стадии более мощных микродуговых электрических разрядов. Взаимосвязь между противокоррозионными свойствами ПЭО-покрытий и стадиями их роста может носить общий характер при ПЭО-обработке различных по природе вентильных металлов и сплавов в электролитах разного состава.
1. ВВЕДЕНИЕ
Исследованию ZrO2-содержащих оксидных слоев на алюминии, титане, цирконии, магнии и других металлах и сплавах, сформированных в электролитах действием в приэлектродной области электрических искровых и/или дуговых разрядов (плазменно-электролитическое оксидирование, ПЭО), уделяют заметное внимание [1–12]. Формируемые на поверхности слои Al2O3–ZrO2, TiO2–ZrO2, MgO–ZrO2 или ZrO2 на цирконии обладают защитными [4, 5], термостабильными и термобарьерными [6, 7], светоотражательными [8, 9] и биосовместимыми свойствами [10], перспективны как катализаторы и носители каталитически активной массы [11], как газочувствительные элементы в сенсорных устройствах [12].
В общем случае состав, строение и свойства ПЭО-слоев зависят от природы обрабатываемого металла, состава электролита и режимов формирования. Ранее показано, что ПЭО-покрытия, сформированные на титане в электролите с 35 г/л Zr(SO4)2 ⋅ 4H2O, состоят из оксидов ZrO2 и TiO2, а их поверхностный слой обогащен цирконием [13]. Сформированные в гальваностатическом режиме в течение 10 мин слои имеют достаточно регулярное распределение по поверхности пор диаметром около или меньше 1 мкм и, согласно данным импедансных и поляризационных измерений, обладают защитными свойствами в хлорсодержащих средах [14]. Полученные в электролите с Zr(SO4)2 композиции ZrO2 + TiO2/Ti перспективны как носители в гетерогенных катализаторах [11], в качестве имплантатов в медицинской практике [10]. При применении таких покрытий важно знать их противокоррозионные свойства, химическую стабильность в различных средах, закономерности, позволяющие управлять этими параметрами.
В настоящей работе приведены результаты исследований влияния времени гальваностатической обработки на состав, строение и поведение в хлорсодержащей среде покрытий на титане, формируемых в электролите с Zr(SO4)2.
2. МАТЕРИАЛЫ И МЕТОДЫ
Оксидные слои формировали на образцах из сплавов титана ВТ1-0 размером 20 × 20 × 0.5 мм. Предварительно образцы подвергали механической обработке, затем химически полировали в смеси кислот HF : HNO3 = 1 : 3, промывали в проточной и дистиллированной воде, сушили на воздухе.
Применяя дистиллированную воду, готовили электролит, содержащий 35 г/л Zr(SO4)2 ⋅ 4H2O. Электрохимическую обработку выполняли в ванне из нержавеющей стали с рубашкой водяного охлаждения. Противоэлектрод – корпус ванны. Электролит перемешивали механической мешалкой. Источник тока – управляемый компьютером тиристорный агрегат ТЕР4-100/460, работающий в однополярном режиме. ПЭО-покрытия формировали в гальваностатическом режиме при эффективной плотности тока i = 0.08 А/см2 в течение 1–20 мин. Температура электролита не превышала 20°С. Образцы с покрытиями промывали дистиллированной водой и сушили на воздухе.
Толщину покрытий измеряли с помощью толщиномера “ВТ-201” (Россия). Элементный состав покрытий определяли на электронном рентгеноспектральном микроанализаторе JXA-8100 (Япония) с энергодисперсионной приставкой INCA (Англия), глубина анализа в зависимости от состава образца от 2 до 5 мкм. Снимки поверхности получали на электронном сканирующем микроскопе высокого разрешения Hitachi S5500 (Япония).
Противокоррозионные свойства покрытий оценивали при помощи собранной лабораторной установки [15]. Плюс источника напряжения через миллиамперметр подключали к металлической основе образца, минус – на противоэлектрод. В зазор между электродами помещали каплю 3% раствора NaCl – аналог морской воды. Радиус площади контакта капля/поверхность ~3 мм. На электроды подавали разность потенциалов U = 50 В. Секундомером измеряли промежуток времени τр от момента касания капли раствора покрытия до резкого возрастания тока через образец. От величины разности потенциалов зависит время образования в покрытии проводящего электрический ток канала (время электростимулированного образования питтинга). Величина U = 50 В была подобрана в ходе предварительных испытаний образцов, сформированных в течение 10 мин. Критерием выбора служило время электростимулированного образования питтинга τр ~ 1 мин, удобное при проведении экспериментов. В [16] показано, что изменение величины τр при одинаковым U коррелирует с изменением противокоррозионных свойств ПЭО-покрытий на сплаве магния, определенных на основе снятия поляризационных кривых. Чем выше величина τр, тем выше противокоррозионные свойства покрытий. В каждом случае измеряли не менее 8 значений τр на обеих сторонах образцов, полученные данные усредняли.
На основе анализа ЭСМ снимков поверхности изучаемых покрытий строили гистограммы распределения диаметров пор и рассчитывали величину удельной поверхностной пористости ε:
Краевой угол смачивания покрытий дистиллированной водой определяли методом “сидящей” капли [17].
3. РЕЗУЛЬТАТЫ И ИХ ОБСУЖДЕНИЕ
Полученная зависимость времени электростимулированного образования питтинга τр от времени формирования покрытий tф представлена на рис. 1а. Видно, что величина τр – сложная функция времени формирования покрытий tф. При увеличении tф до ~8 мин τр монотонно увеличивается. При tф 9–11 мин наблюдается резкое возрастание времени образования питтинга. Затем при tф > 11 мин, τр уменьшается. То есть с увеличением времени формирования поведение противокоррозионных свойств покрытий меняется не монотонно, а скачкообразно, что ранее не отмечалось.
Рис. 1.
Влияние длительности ПЭО-обработки tф на время образования питтинга τр (а), толщину (б), краевой угол (в), элементный состав (г) покрытий и величину отношения времени образования питтинга к единице толщины покрытия τр/h (д).
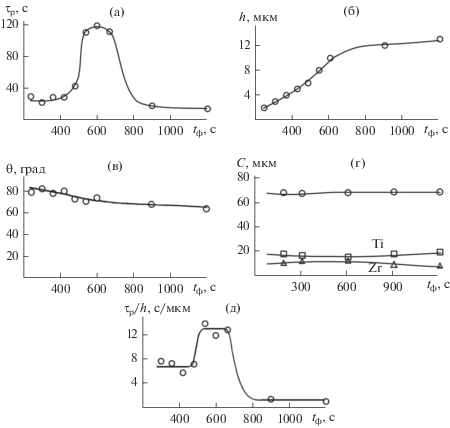
Между тем толщина покрытия h, рис. 1б, угол смачивания покрытия водой θ, рис. 1в, и элементный состав покрытий, рис. 1г, с ростом времени гальваностатического формирования tф меняются монотонно, резких изменений этих характеристик покрытий не наблюдается. Т.е. связать немонотонное поведение величины τр с изменением контролируемых характеристик покрытий затруднительно.
На рис. 1д отложены значения времени образования электростимулированного питтинга τр, отнесенного к единице толщины h формируемых покрытий во всем диапазоне изученных tф. По данным рис. 1д можно выделить три временных интервала, для которых характерно примерно постоянное значение τр/h. Из постоянства величин τр/h следует, что на каждом временном интервале увеличение времени τр пропорционально росту толщины h, т.е. покрытия растут с примерно одинаковой внутренней структурой. Наиболее плотные и стойкие к проникновению хлор-ионов покрытия при выбранной плотности тока и концентрации соли в электролите получены, в исследуемом случае, при времени формирования tф 9–11 мин.
Известно, что при гальваностатическом ПЭО с ростом tф происходит смена стадий роста покрытий: доискровая (I), искровая (II) и микродуговая (III) [18]. На рис. 2 приведена зависимость изменения напряжения на электродах от времени формирования U = f(tф), наблюдаемая в наших экспериментах. На основе ее анализа, согласно точкам перегиба, на ней выделены характерные стадии гальваностатического ПЭО.
Сравнение рис. 1а, 1д и 2 показывает, что в стадии формирования покрытий искровыми разрядами (tф < 400 с) величина τр/h выше, чем в стадии формирования более мощными микродуговыми разрядами (tф > 700 с). В то же время при промежуточных значениях tф, т.е. в начале реализации микродуговой стадии, наблюдается резкое возрастание стойкости покрытий к электростимулированному образованию питтинга, иными словами образуются более плотные и менее дефектные покрытия.
Похожие результаты были получены ранее при изучении противокоррозионных свойств ПЭО-покрытий на сплаве магния, формируемых в силикатно-щелочном электролите в присутствии и отсутствие фтор-ионов [16]. Наиболее плотные и стойкие к образованию электростимулированного разницей потенциала U = 1.5 В питтинга покрытия также сформированы в начале реализации микродуговой стадии. Возможно, это общее свойство ПЭО-покрытий, формируемых на вентильных металлах разной природы и в разных по составу электролитах в гальваностатических условиях. Отметим, что закономерности противокоррозионного поведения покрытий на магнии, выявленные путем измерения времени электростимулированного времени образования питтинга τр, коррелировали с противокоррозионными характеристиками этих покрытий, полученными методом снятия поляризационных кривых [16].
Следует отметить, что после прохождения области формирования наиболее стойких к электростимулированному образованию питтинга покрытий (tф ~ 600 с), с увеличением tф наблюдаются перегибы на зависимостях h = f(tф), рис. 1б, θ = f(tф), рис. 1в, изменении с tф элементного состава, рис. 1г. При tф = 600 с, т.е. в условиях формирования наиболее стойких покрытий, можно отметить тенденцию изменения на поверхности отношения содержаний титана и циркония в пользу последнего, рис. 1г. Все это свидетельствует об изменениях в механизме образования и строении покрытий при временах формирования tф меньших и больших 600 с.
На рис. 3 представлены микрофотографии поверхности покрытий, сформированных в течение 5, 10 и 20 мин, т.е. в характерных стадиях гальваностатического формирования, рис. 2. На поверхности чередуются поры (на снимках темные округлые или овальные участки), поднятия вокруг пор и впадины между поднятиями. Такое строение поверхности характерно для покрытий, формируемых методом ПЭО. Согласно полученным на основе анализа снимков гистограммам распределения пор по размерам во всех трех случаях наиболее характерные диаметры устьев пор ~0.3 мкм, хотя наблюдаются отдельные поры диаметром до 2 мкм. С ростом tф постепенно уменьшается число крупных пор на поверхности, а количество пор на единицу поверхности, как и доля поверхности, занятой порами, уменьшаются, (табл. 1).
Таким образом, сложную зависимость времени образования питтинга с выраженным максимумом при времени формирования 9–11 мин, рис. 1а, связать с изменением толщины или поверхностной пористости покрытий, особенностями смачивания поверхности водным раствором затруднительно. Изменение стойкости формируемых при разных длительностях покрытий может быть связано с поведением таких их характеристик, как распределение элементов, образование кристаллических фаз, строение и геометрия пор в массиве покрытий, приводящих к дефектности и неоднородности состава и строения формируемых слоев по толщине.
Ранее показано, что во временном интервале гальваностатического формирования исследуемых покрытий около 10 мин на поверхности образуются выступающие участки, островки, рис. 4 [13]. Их образование было объяснено возникновением, наряду с искровыми и микродуговыми, распространяющихся электрических разрядов. Возможно, что действие распространяющихся разрядов изменяет число и размеры пор, соотношение элементов в поверхностной части и в конечном итоге стойкость покрытий к образованию питтинга в области времен формирования 9–11 мин. Далее под действием распространяющихся разрядов возвышающиеся участки распространяются на всю площадь поверхности и это может приводить к повышению дефектности внутренней части покрытий и снижению их стойкости к электростимулированному образованию питтинга.
Рис. 4.
Поверхность покрытий с выступающими участками. Покрытия получены при tф = 12 (а) и 25 (б) минутах [13].
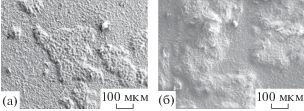
Также было найдено, что на стенках и дне пор формируемых покрытий присутствуют металлические титан и цирконий [19]. Нельзя исключить, что изменение стойкости к электростимулированному образованию питтинга с ростом tф связано с изменением состава стенок, дна и строения пор в целом.
Как отмечено выше, при анализе поведения с величиной tф таких контролируемых параметров покрытий, как τр = f(tф), рис. 1а, h = f(tф), рис. 1б, θ = f(tф), рис. 1в, элементного состава, рис. 1г выделяются два участка: до ~600 с и после. По-видимому, в исследуемом случае реализуются разные механизмы образования покрытий до и после этой граничной величины длительности гальваностатического формирования. Возможно, именно на этой временной границе происходит смена процесса формирования покрытий искровыми разрядами на формирование более мощными микродуговыми, и, соответственно, определение стадий гальваностатического формирования на основе точек перегиба формовочной кривой не совсем корректно.
4. ВЫВОДЫ
1. Получены данные по влиянию длительности гальваностатического формирования методом плазменно-электролитического оксидирования на состав, толщину, угол смачивания водой, удельную поверхностную пористость и поведения в 3% NaCl покрытий ZrO2 + TiO2 на титане, сформированных в электролите с Zr(SO4)2.
2. Установлено, что время электростимулированного образования питтинга τр при контакте с 3% NaCl сложным образом зависит от времени формирования покрытий. Наблюдается выраженный максимум в стойкости покрытий к хлор-ионам при переходе от искровой стадии формирования к микродуговой.
3. Не найдено простых взаимосвязей между величиной времени образования электростимулированого питтинга и изменением толщины, элементного состава, поверхностной удельной пористости покрытий, смачивания их водой.
4. Выявленная закономерность позволяет получать покрытия с регулируемой стойкостью к хлор-ионам при временах формирования до 20 мин. Она может носить общий характер для покрытий, формируемых на вентильных металлах и сплавах разной природы в гальваностатическом режиме в различных по составу электролитах.
Работа выполнена в рамках государственного задания 0265-2018-0001.
Список литературы
Руднев В.С., Яровая Т.П., Килин К.Н. и др. // Физикохимия поверхности и защита материалов. 2010. Т. 46. № 4. С. 380–386.
Akatsu T., Kato T., Shinoda Y., Wakai F. // Surf. Coat. Technol. 2013. V. 223. P. 47–51.
Wang C., Hao J.M., Xing Y.Z. et al. // Surf. Coat. Technol. V. 261. P. 201–207.
Barati N., Yerokhin A., Golestanifard F. et al. // J. Alloy. Compd. 2017. V. 724. P. 435–442.
Al Zoubi W., Kamil M.P., Ko Y.G. // Phys. Chem. Chem. Phys. 2017. V. 19. № 3. P. 2381–2391.
Apelfeld A.V., Ashmarin A.A., Borisov A.M. et al. // Surf. Coat. Technol. 2017. V. 328. P. 513–517.
Савушкина С.В., Полянский М.Н., Борисов А.М. и др. // Поверхность: рентгеновские, синхротронные и нейтронные исследования. 2016. № 4. С. 45–50.
Недозоров П.М., Килин К.Н., Яровая Т.П. и др. // Журн. прикл. спектроскопии. 2001. Т. 68. № 4. С. 511–514.
Yao Z., Su P., Shen Q. et al. // Surf. Coat. Technol. 2015. V. 269. P. 273–278.
Kaluđerović M.R., Schreckenbach J.P., Graf H.-L. // Mater. Sci. Eng., C. 2014. V. 44. P. 254–261.
Rudnev V.S., Tyrina L.M., Lukiyanchuk I.V. et al. // Surf. Coat. Technol. 2011. V. 206. № 2–3. P. 417–424.
Efimenko A.V., Semenova T.L. // Russ. J. Electrochem. 1999. V. 35. № 11. P. 1168–1172.
Руднев В.С., Килин К.Н., Малышев И.В. и др. // Физикохимия поверхности и защита материалов. 2010. Т. 46. № 6. С. 634–639.
Руднев В.С., Яровая Т.П., Недозоров П.М. и др. // Физикохимия поверхности и защита материалов. 2011. Т. 47. № 5. С. 517–524.
Руднев В.С., Ваганов-Вилькинс А.А., Цветников А.К. и др. // Физикохимия поверхности и защита материалов. 2015. Т. 51. № 1. С. 79–93.
Oleynik S.V., Rudnev V.S., Kuzenkov Yu.A. et al. // Int. J. Corros. Scale Inhib. 2018. V. 7. № 1. P. 78–86.
Адамсон А. Физическая химия поверхности. М.: Мир, 1979. 275 с.
Гюнтершульце А., Бетц Г. Электролитические конденсаторы. М.: Оборонгиз, 1938. 198 с.
Руднев В.С., Малышев И.В., Лукиянчук И.В., Курявый В.Г. // Физикохимия поверхности и защита материалов. 2012. Т. 48. № 4. С. 391–397.
Дополнительные материалы отсутствуют.
Инструменты
Физикохимия поверхности и защита материалов