Физикохимия поверхности и защита материалов, 2020, T. 56, № 2, стр. 197-201
Об электрохимическом осаждении и свойствах композиционных покрытий на основе никеля
В. Н. Целуйкин 1, *, А. В. Яковлев 1
1 Энгельсский технологический институт (филиал) ФГБОУ ВО “Саратовский государственный технический университет им. Ю.А. Гагарина”
413100 Саратовская обл., Энгельс, пл. Свободы, 17, Россия
* E-mail: tseluikin@mail.ru
Поступила в редакцию 19.11.2018
После доработки 19.03.2019
Принята к публикации 26.03.2019
Аннотация
Получены композиционные электрохимические покрытия (КЭП) на основе никеля, модифицированные нитратом графита. Исследованы их микроструктура и функциональные свойства (коэффициент трения скольжения, защитная способность). Установлено, что при введении дисперсии нитрата графита в сульфатно-хлоридный электролит никелирования коэффициент трения скольжения формирующихся КЭП снижается вдвое, а область потенциалов пассивного состояния данных композиционных покрытий увеличивается в 1.26–1.32 раза.
ВВЕДЕНИЕ
Одним из важных направлений химической технологии является создание композиционных электрохимических покрытий (КЭП). Принцип получения КЭП основан на совместном осаждении металлов с дисперсными частицами различной природы из электролитов-суспензий [1–4]. Области применения композиционных покрытий определяются их свойствами. Наибольшее распространение среди КЭП получили никелевые покрытия. КЭП на основе никеля характеризуются высокой твердостью и износостойкостью, устойчивостью в коррозионных средах и хорошим внешним видом. С никелем легко соосаждаются дисперсные частицы различной природы [1, 2].
Эксплуатационные характеристики КЭП во многом зависят от природы дисперсной фазы [1, 3, 4]. В настоящее время значительное внимание уделяется композиционным покрытиям, модифицированным различными углеродными материалами. В частности, получены и исследованы КЭП на основе никеля, модифицированные карбидами металлов [5–9], наноалмазами [10, 11], фуллереном С60 [12], углеродными нанотрубками [7, 13, 14], графеном [15, 16]. Подобный интерес связан с улучшением функциональных свойств КЭП, которого можно достичь при включении в металлическую матрицу материалов на основе углерода [3, 4]. Хорошие перспективы в этом направлении открываются для графита и его производных. Главной особенностью графита является то, что он имеет ярко выраженную слоистую структуру. В слоях каждый атом С прочно связан с тремя другими атомами углерода, находящимися на расстоянии 1.42 Å. Расстояние между слоями значительно больше и составляет 3.35 Å. Слои графита расположены таким образом, что половина атомов одного слоя находится под центрами шестигранников другого, а вторая половина – друг под другом [17]. Вследствие слоистой структуры, графит способен образовывать соединения внедрения с различными интеркалирующими агентами (анионы и молекулы кислот, катионы металлов, кислородсодержащие соединения и др.) [18]. Графитовый слой может выступать как акцептор, взаимодействуя с сильными восстановителями или в качестве донора, реагируя с окислителями. Так, в присутствии сильных окислителей формируются соединения внедрения графита с минеральными кислотами. В частности, при взаимодействии с азотной кислотой образуется нитрат графита.
Цель настоящей работы – получить КЭП на основе никеля, модифицированные нитратом графита, исследовать процесс их электроосаждения, а также структуру, трибологические свойства и коррозионное поведение данных покрытий.
МЕТОДИКА ЭКСПЕРИМЕНТА
КЭП на основе никеля получали из электролита состава, г/л: NiSO4 ⋅ 7H2O 220; NiCl2 ⋅ 6H2O 40; CH3COONa 30; нитрат графита 10. Покрытия осаждали на стальную основу (сталь 45) при комнатной температуре с постоянным перемешиванием электролита. Покрытия чистым никелем осаждали из раствора приведенного состава без дисперсной фазы. Адгезию полученных никелевых покрытий оценивали путем нанесения сетки царапин (ГОСТ 9.02-79).
В работе использовали нитрат графита, синтезированный анодным окислением дисперсного порошка природного графита в 58% растворе HNO3 в гальваностатическом режиме при токе I = 100 мА/г графита с сообщением емкости Q = = 400 мА ч/г. Рабочим электродом служил дисперсный графит, противоэлектродом – платина. Частицы графита к токоотводу поджимали подвижным поршнем, который в процессе реакции внедрения перемещался, увеличивая объем суспензионного электрода [19, 20].
Состав композиционных покрытий исследовали методом лазерного микроспектрального анализа [21]. Использовался лазерный спектроаналитический комплекс включающий в себя лазер на Nd : YAG (длина волны 1.06 мкм), работающий в режиме гигантского импульса, длительность импульса 9 нс. Частота следования импульсов 25 Гц. Система регистрации – дифракционный спектрограф ДФС-458С и ПЗС-приставка МИРС, включающая в себя блок из восьми ПЗС-приемников, плату сопряжения с компьютером и соответствующее программное обеспечение “SPEKTRAN 8”, позволяющее производить качественный и количественный спектральный анализ.
Электрохимические измерения проводили на импульсном потенциостате P-30J. Потенциалы задавали относительно насыщенного хлоридсеребряного электрода сравнения и пересчитывали по водородной шкале.
Коэффициенты трения скольжения покрытий на основе никеля определяли по следующей формуле:
где Fтр – сила трения скольжения; P – сила, с которой контртело давит на испытуемую поверхность. В качестве контртела использовался стальной образец, масса которого во всех испытаниях составляла 1 г.Коррозионные испытания никелевых покрытий проводились путем снятия анодных потенциодинамических кривых в 3% растворе NaCl при скорости развертки потенциала Vp = 10 мВ/с. Кривые снимали до резкого подъема тока. О коррозионной стойкости исследуемых покрытий судили по протяженности области потенциалов пассивного состояния.
РЕЗУЛЬТАТЫ И ИХ ОБСУЖДЕНИЕ
Поляризационные i, E – кривые электроосаждения никеля, снятые при получении покрытий без дисперсной фазы, а также при наличии в растворе нитрата графита, показывают, что введение дисперсных частиц в сульфатно-хлоридный электролит никелирования приводит к возрастанию скорости катодного процесса (рис. 1). На это указывает тот факт, что в присутствии нитрата графита осаждение никеля происходит при менее отрицательных потенциалах. Соответственно, значения токов возрастают при получении композиционных покрытий по сравнению с никелевыми осадками без дисперсной фазы. Можно предположить, что процесс переноса частиц нитрата графита к катоду и встраивания их в электролитический осадок протекает не только вследствие конвекции, но и посредством адсорбции катионов осаждаемого металла на их поверхности. Получив таким способом заряд, дисперсная фаза переносится к катоду, и там заращиваются разряжающимся металлом. При этом ионы, адсорбированные на частицах, участвуют в мостиковом связывании дисперсной фазы с катодной поверхностью [4, 22]. Такое связывание приводит к ослаблению расклинивающего давления жидкостной прослойки между частицей и катодом. Соответственно, усиливается адгезия. На поверхности катода дисперсные частицы становятся центрами кристаллизации и определяют дальнейшее формирование растущего электролитического осадка.
Рис. 1.
Потенциодинамические поляризационные кривые осаждения никеля без добавки (1) и совместно с нитратом графита (2).

Если вести процесс осаждения никелевых покрытий в гальваностатическом режиме, наблюдается смещение потенциалов в положительную сторону при введении в сульфатно-хлоридный электролит дисперсной фазы нитрата графита (рис. 2). На гальваностатических кривых в начальный момент времени имеет место скачок потенциала, затем процесс переходит в стационарный режим. Данный скачок можно объяснить тем, что при включении тока необходимы большие затраты энергии на образование зародышей металла. По результатам гальваностатических исследований была рассчитана поляризационная емкость процесса электроосаждения с помощью выражения:
Рис. 2.
Гальваностатические кривые осаждения никеля без добавки (1) и совместно с нитратом графита (2) при ik = 7 А дм–2.
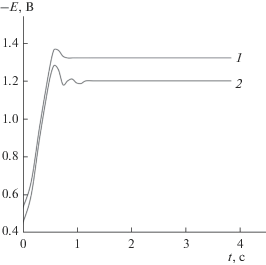
Поляризационная емкость снижается при переходе от чистых никелевых осадков к КЭП никель–нитрат графита (табл. 1). Данный эффект можно объяснить тем, что вхождение дисперсных частиц в двойной электрический слой приводит к увеличению его размеров.
Таблица 1.
Значения поляризационной емкости С × 103, Ф см–2 при электроосаждении никеля и КЭП на его основе
ik, А дм–2 | С × 103, Ф/см2 | |
---|---|---|
никель | КЭП никель–нитрат графита |
|
2 | 22.3 | 14.3 |
3 | 40.1 | 19.5 |
4 | 52.9 | 25.5 |
5 | 67.4 | 38.1 |
6 | 79.7 | 47.7 |
7 | 92.8 | 49.3 |
8 | 107.3 | 51.0 |
9 | 119.9 | 55.4 |
10 | 133.2 | 61.7 |
При переходе от никелевого покрытия без дисперсной фазы (рис. 3а) к КЭП никель–нитрат графита (рис. 3б) наблюдается изменение микроструктуры поверхности. На микрофотографии композиционного покрытия видны включения дисперсной фазы в никелевую матрицу. Очевидно, частицы нитрата графита выступают в качестве центров кристаллизации, что способствуют равномерному распределению никеля по катодной поверхности и упорядочению структуры формирующегося покрытия. Следует отметить, что с ростом толщины осадка КЭП никель–нитрат графита не наблюдается его разрыхления. Не ухудшается и адгезия к подложке изученных покрытий.
Рис. 3.
Микроструктура поверхности электролитического никеля (а) и КЭП никель–нитрат графита (б). Плотность тока ik = 10 А/дм2. Увеличение ×1000.
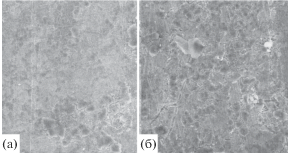
При включении в металлическую матрицу дисперсной фазы, наблюдаются изменения в структуре формирующегося электролитического осадка, которые сказываются на его эксплуатационных свойствах [3, 4]. В практическом отношении значительный интерес представляют трибологические характеристики металлических поверхностей. Например, для деталей, работающих в узлах механизмов и машин, существенное значение имеет коэффициент трения скольжения f. Его величина, по закону Амонтона–Кулона, определяется природой контактирующих материалов и не зависит от нагрузки. При сухом трении на воздухе (без смазки) значения f меняются в интервале от 0.1 до 1.
Для изученных КЭП величина коэффициентов трения скольжения снижается вдвое по сравнению с гальванопокрытиями на основе никеля без дисперсной фазы (табл. 2). Очевидно, данный эффект связан с тем, что дисперсные частицы нитрата графита, включающиеся в металлическую матрицу при электроосаждении, выполняют функцию сухой смазки (экспериментальное исследование проводилось при сухом трении на воздухе). Уменьшение коэффициента трения композиционных покрытий никель–нитрат графита по сравнению с чистым никелем, очевидно, определяется слоистой структурой дисперсной фазы. Исследование состава КЭП никель–нитрат графита методом лазерного микроспектрального анализа показало, что содержание дисперсной фазы максимально в поверхностных слоях и уменьшается по мере продвижения вглубь осадков (рис. 4).
Таблица 2.
Коэффициенты трения скольжения f покрытий на основе никеля, полученных при различной плотности катодного тока
ik, А/дм2 | 6 | 7 | 8 | 9 | 10 |
---|---|---|---|---|---|
Никель | 0.38 | 0.34 | 0.34 | 0.33 | 0.30 |
Никель–нитрат графита | 0.16 | 0.16 | 0.15 | 0.14 | 0.14 |
Рис. 4.
Распределение углерода по толщине композиционного покрытия никель–нитрат графита, осажденного при ik = 10 А/дм2.
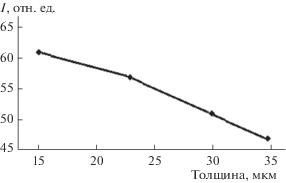
Другим важным эксплуатационным свойством гальванических осадков является защитная способность к коррозионному воздействию. КЭП представляют собой многокомпонентные фазы. Механизм и кинетика коррозионного разрушения многокомпонентной фазы определяется химическим составом, типом кристаллической решетки, природой агрессивной среды, концентрацией раствора, с которым контактирует металлическое изделие, а также температурой [23, 24]. Коррозионные исследования никелевых осадков в 3% растворе NaCl, показали, что область потенциалов пассивного состояния ЕП для КЭП никель–нитрат графита в 1.26–1.32 раза превышает значения данной величины у никелевых гальванопокрытий, не содержащих дисперсной фазы (табл. 3).
Таблица 3.
Ширина области пассивного состояния ЕП, В покрытий на основе никеля, полученных при различной плотности катодного тока
ik, А/дм2 | 6 | 7 | 8 | 9 | 10 |
---|---|---|---|---|---|
Никель | 0.60 | 0.62 | 0.66 | 0.68 | 0.68 |
Никель–нитрат графита | 0.78 | 0.78 | 0.86 | 0.88 | 0.90 |
Рассмотрим влияние нитрата графита на увеличение коррозионной стойкости КЭП на основе никеля. Данный эффект можно объяснить совместным действием нескольких факторов. При осаждении из сульфатно-хлоридных электролитов формируются матовые пористые никелевые покрытия [25]. В процессе включения в никелевую матрицу частиц нитрата графита происходит перекрытие пор. Согласно данным лазерного микроспектрального анализа, наибольшее количество дисперсной фазы закрепляется в поверхностных слоях изученных композиционных покрытий. Следовательно, достаточно велика площадь перекрытия (укрывистости) поверхности осадков частицами нитрата графита. Независимо от вида коррозионного процесса, влияние дисперсных частиц в КЭП проявляется лишь когда данные частицы в термодинамических реакциях образуют на границах фаз в твердом растворе или по всему объему осадка соединения, более стойкие к коррозионному воздействию, чем матрица композиционного покрытия [1]. В ином случае, влияние частиц дисперсной фазы на коррозионный процесс будет незначительным: развитие коррозии не прекратится полностью, а пойдет в обход частицы с небольшим уменьшением скорости. Исходя из этого, можно уверенно предположить, что в случае КЭП никель–нитрат графита будет происходить образование подобных соединений. В совокупности названные факторы обеспечивают увеличение коррозионной стойкости изученных композиционных покрытий.
ЗАКЛЮЧЕНИЕ
На основании результатов проведенных исследований можно заключить, что при введении дисперсной фазы нитрата графита в сульфатно-хлоридный электролит никелирования наблюдается увеличение скорости процесса электроосаждения и формируются композиционные покрытия. Дисперсные частицы нитрата графита содержатся преимущественно в поверхностных слоях электрлитических осадков, и оказывают определяющее влияние на структуру, трибологические свойства и защитную способность изученных композиционных покрытий.
Исследование выполнено при финансовой поддержке РФФИ в рамках научного проекта № 8-29-19048\18.
Список литературы
Антропов Л.И., Лебединский Ю.Н. Композиционные электрохимические покрытия и материалы. Киев: Техника, 1986. 200 с.
Сайфуллин Р.С. Физикохимия неорганических полимерных и композиционных материалов. М.: Химия, 1990. 240 с.
Целуйкин В.Н. // Российские нанотехнологии. 2014. Т. 9. № 1–2. С. 25–35.
Целуйкин В.Н. // Физикохимия поверхности и защита материалов. 2016. Т. 52. № 2. С. 171–184; 2018. Т. 54. N 3. С. 293–296; 2018. Т. 54. N 6. С. 582–584.
Gül H., Kılıc F., Uysal M. et al. // Applied Surface Science. 2012. V. 258. № 10. P. 4260–4267.
Gupta R.N., Das A.K., Nagahanumiah, Henal Shah // Materials and Manufacturing Processes. 2016. V. 31. № 1. P. 42–47.
Mosallanejad M.H., Shafyei A., Akhavan S. // Canadian Metallurgical Quarterly. 2016. V. 55. № 2. P. 147–155.
Gobinda Gyawali, Bhupendra Joshi, Khagendra Tripathi, Soo Wohn Lee // J. Materials Engineering and Performance. 2017. V. 26. № 9. P. 4462–4469.
Alok Kumar Chaudhari, Dhananjay Kumar Singh, Singh V.B. // Materials Research Express. 2018. V. 5. № 5.
Буркат Г.К., Долматов В.Ю. // Физика твердого тела. 2004. Т. 46. № 4. С. 685–692.
Chayeuski V.V., Zhylinski V.V., Rudak P.V. et al. // Applied Surface Science. 2018. V. 446. P. 18–26.
Целуйкин В.Н. // Физикохимия поверхности и защита материалов. 2017. Т. 53. № 3. С. 278–281.
Giannopoulos F., Chronopoulou N., Bai J. et al. // Electrochimica Acta. 2016. V. 207. P. 76–86.
Gizem Hatipoglu, Muhammet Kartal, Mehmet Uysal et al. // Tribology International. 2016. V. 98. P. 59–73.
Algul H., Tokur M., Ozcan S. et al. // Applied Surface Science. 2015. V. 359. P. 340–348.
Ghulam Yasin, Muhammad Abubaker Khan, Muhammad Arif et al. // J. Alloys and Compounds. 2018. V. 755. P. 79–88.
Уббелоде А.Р., Льюис Ф.А. Графит и его кристаллические соединения. М.: Мир, 1965. 256 с.
Фиалков А.С. Углерод, межслоевые соединения и композиты на его основе. М.: Аспект-пресс, 1997. 718 с.
Яковлев А.В., Забудьков С.Л., Финаенов А.И., Яковлева Е.В. // Журн. прикладной химии. 2006. Т. 79. № 11. С. 1761–1771.
Яковлев А.В., Яковлева Е.В., Рахметулина Л.А. и др. // Известия высших учебных заведений. Химия и химическая технология. 2018. Т. 61. № 7. С. 121–128.
Павлычева Н.К., Пеплов А.А., Демин А.П. // Оптический журнал. 2007. Т. 74. № 3. С. 29–32.
Сайфуллин Р.С., Абдуллин И.А. // Российский химический журнал. 1999. Т. 63. № 3–4. С. 63–67.
Кеше Г. Коррозия металлов. Физико-химические принципы и актуальные проблемы М.: Металлургия, 1984. 400 с.
Маршаков И.К. // Защита металлов. 2002. Т. 38. № 2. С. 139–145.
Гальванические покрытия в машиностроении: Справочник в 2-х тт. / Под ред. Шлугера М.А. М.: Машиностроение. Т. 1. 1985. 240 с.
Дополнительные материалы отсутствуют.
Инструменты
Физикохимия поверхности и защита материалов