Физикохимия поверхности и защита материалов, 2020, T. 56, № 3, стр. 278-285
Структура и свойства покрытий в системе Cr–B–C–N, полученных с использованием катода CrB2 методом импульсного катодно-дугового испарения P-CAE в среде Ar, N2 и C2H4
Ф. В. Кирюханцев-Корнеев 1, *, Т. Б. Сагалова 1, Е. А. Башкиров 1
1 Национальный исследовательский технологический университет “МИСиС”
119049 Москва, Ленинский пр., 4, Россия
* E-mail: kiruhancev-korneev@yandex.ru
Поступила в редакцию 08.04.2019
После доработки 23.04.2019
Принята к публикации 30.04.2019
Аннотация
Технология импульсного катодно-дугового испарения P-CAE успешно применена для осаждения покрытий в системе Cr–B–C–N. Покрытия обладали структурой типичной для дуговых покрытий, со значительной долей конденсированной капельной фазы, однако формирование неблагоприятной столбчатой морфологии было устранено. Покрытия содержали кристаллиты фаз h-CrB2 и с‑CrN, а также большое количество аморфной фазы, состав которой варьировался в зависимости от типа рабочей среды. Покрытия, полученные в аргоне показали наиболее высокую твердость 12 ГПа, в то время как наиболее высокими упруго-пластическими свойствами (упругое восстановление 72%) характеризовались покрытия, полученные в среде C2H4. Коэффициент трения покрытий, нанесенных в среде Ar, N2, и C2H4 составлял 0.7, 0.4, и 0.3 соответственно. Фаза алмазоподобного углерода в последнем случае приводила к понижению коэффициента трения из-за высокой доли sp2-связанного углерода, выполняющего роль твердой смазки. Покрытия оптимального состава обладали высокой стойкостью к высокотемпературному окислению в диапазоне температур 600–1000°С. При высоких температурах процесс окисления сопровождался интенсивной диффузией атомов бора вглубь подложки.
ВВЕДЕНИЕ
В настоящее время к нагруженным деталям и узлам машин предъявляются все более высокие требования по механическим и трибологическим свойствам, поэтому улучшение характеристик поверхностных слоев деталей является важной задачей для науки и техники. Одним из перспективных направлений улучшения свойств поверхности изделий является нанесения на них защитных покрытий на основе боридов переходных металлов [1–5]. Покрытия CrB2 обладают высокой твердостью на уровне 40 ГПа в сочетании с высокой коррозионной и износостойкостью [6–8]. В работе [9] были зафиксированы рекордные показатели: твердость 51 ГПа и модуль упругости 514 ГПа. При осаждении покрытий CrB2 обычно формируется ярко выраженная столбчатая структура, что негативно сказывается на трибологических свойствах [10, 11]. Для устранения этого недостатка покрытия можно легировать углеродом или азотом. У полученных методом магнетронного распыления покрытий CrBC и CrBN был подавлен столбчатый рост зерен диборида хрома за счет образования аморфных прослоек (а-BC и а-BN) на границах зерен, препятствующих коалисценции кристаллитов. Покрытия CrBC и CrBN по сравнению с покрытиями CrB2, обладали более высокими адгезионной прочностью, упругим восстановлением, индексом пластичности и трещиностойкостью [12–15]. Также следует отметить, что введение азота в СrB2 повышает жаростойкость покрытий [15]. Полученные в работах [16–18] покрытия CrBCN имели улучшенную ударную вязкость, низкие значения коэффициента трения (0.33) и скорости износа (2.4 × 10–7 мм3/Нм), высокие антикоррозионные свойства.
Покрытия на основе диборида хрома ранее были получены с применением метода магнетронного напыления на постоянном токе [19–23], в импульсном режиме [24, 25], высокочастотном режиме [26], с помощью высокомощного импульсного магнетронного напыления HIPIMS [27, 28], магнетронного напыления, совмещенного с индукционно-связанной плазмой [29]. Известны работы по нанесению покрытий на основе CrB2 методами химического осаждения из пара [30] и электронно-лучевого термического испарения с активацией процесса за счет ионной бомбардировки [31].
Перспективным является применение вакуумно-дугового испарения, преимущества которого заключается в больших энергиях частиц и преобладании ионов в потоке, переносимом на подложку и, как следствие, в лучшей адгезии покрытий [32]. Для снижения концентрации нежелательной капельной фазы может использоваться импульсный режим испарения [33–35]. В этом случае количество катодных пятен и скорость их перемещения значительно выше [35], что приводит снижению вероятности образования капельной фазы, а также к более равномерному распределению теплового потока по поверхности и объему катода, снижая тем самым возникающие термические напряжения в испаряемом керамическом катоде и сохраняя его от разрушения. Метод катодно-дугового испарения при подаче постоянного тока не позволяет использовать катоды на основе диборида хрома, а может быть применен для испарения хромовых катодов с небольшими (2–20 ат. %) добавками бора [36, 37]. В настоящей работе покрытия на основе CrB2 наносились методом импульсного катодно-дугового испарения (P-CAE, pulsed cathode-arc evaporation) ранее апробированного на примере систем Ti–Cr–B–N [38] и Ti–Ni–Cr–Eu–C–N [39].
Целью данной работы является изучение структурных особенностей, механических и трибологических характеристик, а также жаростойкости покрытий, нанесенных с помощью импульсного катодно-дугового испарения катода CrB2 в среде Ar, N2 и C2H4.
МЕТОДИКА ЭКСПЕРИМЕНТА
В данной работе для испарения использовался катод CrB2, размером 10 × 10 × 50 мм, полученный по технологии силового СВС-компактирования из смеси порошков 70.6% Сr и 29.4% B [40]. Покрытия наносились на пластины монокристаллического кремния КЭФ-4.5 (100) и твердых сплавов марок ВК6М и ТТ20К9, а также диски из титанового сплава типа ВТ-3 и никелевого сплава ЭП718 методом импульсного катодно-дугового испарения. Использовалась установка на базе откачивающей системы УВМ-2М, оснащенная испарителем оригинальной конструкции (рис. 1).
Рис. 1.
Конструкция испарителя. 1 – испаряемый катод; 2 – катодный держатель; 3 – изолятор; 4 – кварцевая колба; 5 – система поджига; 6 – керамика; 7 – система водяного охлаждения; 8 – корпус анода; 9 – медная пластина; 10 – система магнитов; 11 – держатель с подложкой; 12 – зона нанесения покрытия.
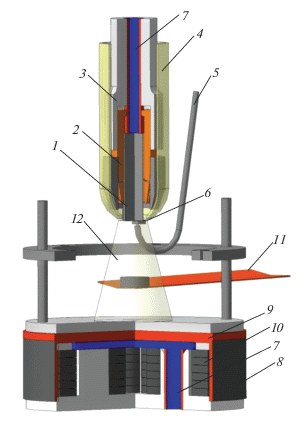
Катод закреплен в держателе испарителя с помощью цанги. Сам держатель крепится к тефлоновой трубке, выполняющей роль несущего изолятора. Также для дополнительного предотвращения пробоев вся конструкция помещается в кварцевую колбу. Поджиг осуществляется через металлическую проволоку, отделенную от катода пластинкой оксида алюминия. Основу конструкции анода составляет магнетрон, имеющий водоохлаждаемую рубашку, служащую для отвода теплоты от поверхности. Подложка закрепляется на удерживающем кольце и располагается в пространстве между катодом и анодом на расстоянии 20 мм от катода. Давление рабочего газа составляло 0.4 Па. В качестве газов применялись Ar (99.9995%), N2 (99.999%) и C2H4 (99.95%). Напряжение и частота поджига составляли 15 кВ и 10 Гц, соответственно. Напряжение разряда колебалось в диапазоне от 160 до 200 В. Перед нанесением покрытий подложки проходили очистку: нагрев до 500°С при подаче на них анодного потенциала в течение 3 мин и ионную бомбардировку при подаче отрицательного напряжения смещения (2 кВ) в течение 5 мин.
Элементные профили покрытий были получены с помощью оптического эмиссионного спектрометра тлеющего разряда (ОЭСТР) с использованием прибора PROFILER-2 (Horiba Jobin Yvon) [41]. Для структурного анализа использовался сканирующий электронный микроскоп Hitachi S-3400N c системой энергодисперсионного анализа NORAN System 7. Рентгенофазовый анализ проводился на дифрактометре D8 ADVANCE компании Bruker с использованием CuKα излучения. Исследования методом Рамановской спектроскопии проводились на приборе NTEGRA NT-MDT с использованием красного лазера (633 нм). Для определения твердости (Н), модуля упругости (Е) и упругого восстановления (W) использовался нанотвердомер Nanohardness Tester (CSM Instruments). Обработка кривых индентирования проводилась по методу Оливера–Фарра. Трибологические испытания проводились на автоматизированной машине трения Tribometer (CSM Instruments) по схеме “шарик-диск”; контр-телом служил шарик из Al2O3; нормальная нагрузка составляла 1 Н; линейная скорость 10 см/с. Фрактографические исследования канавок износа с последующим вычислением величины приведенного износа проводились на оптическом профилометре Veeco WYKO NT1100. Для отжигов на воздухе применялась муфельная печь SNOL, время изотермической выдержки составляло 1 ч. Детальная информация об используемых методах и оборудовании представлена в [42, 43].
РЕЗУЛЬТАТЫ И ИХ ОБСУЖДЕНИЕ
Концентрационные профили покрытий Cr–B–C–N, полученных в различных газовых средах представлены на рис. 3. Усредненный химический состав по толщине покрытий, в пересчете на основные компоненты, представлен в табл. 1. Для покрытия, полученного в аргоне, наблюдалось равномерное распределение элементов по глубине, соотношение B/Cr составляло 1.8. Для покрытий, полученных в реакционных газовых средах (N2, C2H4, N2 + C2H4), выявляется подслой состава CrB2 и верхний слой, содержащий элементы катода и атомы рабочих газов. Содержание кислорода в покрытиях оптимального состава находилось в диапазоне от 0.1 до 0.4 ат. %. Присутствие примесей кислорода, а также азота и углерода (в нереакционном режиме напыления) в покрытии можно объяснить возможным наличием остаточного газа в рабочей камере во время нанесения покрытия, а также частичным проникновением примесей из материала СВС-электрода.
Таблица 1.
Элементный состав покрытий Cr–B–C–N
№ | Среда | Элементный состав покрытий, в ат. % | |||
---|---|---|---|---|---|
Cr | B | C | N | ||
1 | Ar | 34 | 62 | 2 | 2 |
2 | N2 | 29 | 40 | 4 | 27 |
3 | C2H4 | 10 | 20 | 68 | 2 |
Исследования структуры поперечных изломов покрытий, проведенные с помощью РЭМ, показали, что покрытия имели плотную структуру с включениями конденсированной капельной фазы (рис. 3). Наличие капельной фазы определяло повышенную шероховатость поверхности покрытий. На дифрактограммах покрытий, осажденных на твердосплавные пластины, присутствовали только линии соответствующие подложке. Исследования, проведенные методом РФА для покрытий, нанесенных на кремниевые подложки, позволили идентифицировать следующие кристаллические фазы, присутствующие в покрытиях: h-CrB2 с гексагональной структурой и c-CrN с кубической гранецентрированной решеткой (рис. 4). Следует отметить, что на рентгенограмме, соответствующей образцу, полученному в углеродсодержащей среде, пики, характерные для фазы CrB2 имеют низкую интенсивность, однако ярко выражено гало в положении 2Ө ~ 20°, которое можно приписать sp2–sp3 связанному углероду (DLC). Для покрытий, полученных в азотсодержащих средах (N2 и С2Н4 + N2) из-за высокой концентрации азота в покрытии характерно образование фазы с-CrN. Отметим, что пик высокой интенсивности в положении 2Ө ~ 70° на дифрактограммах всех исследованных покрытий связан с отражением от подложки из монокристаллического кремния. Для более детального исследования покрытий, содержащих фазу алмазоподобного углерода (DLC) в данной работе применяли спектроскопию комбинационного рассеяния света. Результаты представлены на рис. 5. Два пика в положениях ~1300 и ~1520 см–1 могут указывать на D и G линии алмазоподобного углерода соответственно [44–47]. Пик при 1127 см–1 может соответствовать фазе B4C. Аналогичный пик был зафиксирован в работах [44, 48, 49].
Данные исследования механических свойств покрытий приведены в табл. 2. При использовании твердосплавных подложек наибольшие значения твердости и модуля упругости (12 и 207 ГПа соответственно) показало покрытие 1. Полученные данные меньше средних значений, представленных в работах [14, 15, 19] для покрытий CrB2, полученных методом магнетронного распыления СВС-катодов аналогичного фазового состава. Данный факт можно объяснить повышенной дефектностью катодно-дуговых покрытий. Отметим, что в работе [50] описаны покрытия CrBх, осажденные методом термического испарения. Вследствие высокой дефектности (поверхностные трещины, присутствие микрочастиц), а также недостаточной толщины, покрытия обладали пониженными твердостью в диапазоне 10–14 ГПа и модулем упругости 60–100 ГПа. Введение азота в состав покрытия, по-видимому за счет увеличения доли мягкой аморфной фазы a-BN [14, 21, 23, 51] привело к снижению механических свойств до значений H = 8 ГПа и E = 121 ГПа (табл. 2). Самые низкие значения механических характеристик были зафиксированы для покрытий Cr–B–C (H = 6 ГПа и E = 58 ГПа), Подобный эффект наблюдался в работе [12], где увеличения концентрации углерода в покрытии приводило к уменьшению механических свойств. Как видно из результатов наибольшую (по сравнению с углеродсодержащими образцами) твердость показали образцы, полученные в азотсодержащей среде, что объясняется содержанием в них твердых фаз CrB2 или CrN. Покрытия, осажденные в этилене, имели низкие механические свойства, что связано с большей объемной долей sp2-связанного углерода. Тем не менее, благодаря этому образец Cr–B–C может быть применен в качестве функционального верхнего слоя, понижающего коэффициент трения, тогда как подслой, осажденный в аргоне или азоте, будет обеспечивать необходимую жесткость и износостойкость всему покрытию в целом. Отметим, что параметр H/E, часто определяющий износостойкость [52], для покрытия 3 составлял максимальную величину 0.1, тогда как для покрытий 1 и 2 значения были на уровне 0.06–0.07.
Таблица 2.
Результаты испытаний механических и трибологических свойств покрытий Cr–B–C–N
№ | Среда | Н, ГПа | Е, ГПа | W, % | F | Vw × 10–7, мм3 Н–1 м–1 |
---|---|---|---|---|---|---|
1 | Ar | 12 | 207 | 39 | 0.70 | 30 |
2 | N2 | 8 (15)* | 121 (244) | 47 (45) | 0.42 | 10 |
3 | C2H4 | 6 (2) | 58 (48) | 72 (45) | 0.33 | 5 |
Для покрытий 2 и 3 были проведены эксперименты по наноиндентированию при использовании в качестве подложек кремния. Отличие данных по механическим характеристикам в случае разных подложек может быть связано с различием в уровне внутренних напряжений в покрытиях, температурой нагрева и теплоотводом с поверхности подложки при нанесении, а также шероховатостью поверхности образцов.
Покрытие, осажденное в аргоне имело коэффициент трения на уровне 0.7, что близко к значению 0.8, типичному для непокрытой подложки (рис. 6) и на 15% ниже, чем ранее опубликованные данные [12]. Введение азота в состав покрытий приводило к снижению значений до 0.4, что может быть объяснено положительным влиянием аморфной фазы a-BN. Для ранее иcпытанных при аналогичных условиях покрытий Cr–B–N, величина коэффициента трения была выше и достигала 0.52 [51]. Следует отметить, что в экспериментах, где в роли контртела выступал шарик из твердого сплава WC–6% Co, для Cr–B–N наблюдались значения коэффициента трения на уровне 0.3–0.45 [15, 51, 53, 54]. Самым низким коэффициентом трения (f = 0.3–0.35) обладало покрытие, нанесенное в этилене, что можно объяснить образованием смазывающей пленки на основе фазы алмазоподобного углерода в зоне трибоконтакта. В зависимости от используемого контртела коэффициент трения покрытий Cr–B–C может составлять 0.12 (шарик из стали 100Cr6) [12] и 0.42 (контр-тело SiC) [16]. Авторы работы, отмечают положительную роль фазы а-BC, играющую роль твердой смазки.
Исследования канавок износа, выполненные на оптическом профилометре, показали, что глубина разрушения нереакционного покрытия, составляет около 1 мкм, что сопоставимо с его толщиной (рис. 7). Введение азота способствовало повышению износостойкости покрытий, в этом случае глубина износа была на уровне 0.1–0.2 мкм. По краям дорожек видны навалы, связанные с выносом продуктов износа из зоны трибоконтакта. Покрытие, осажденное в этилене, имело глубину износа 0.4 мкм, но в некоторых частях длины трэка демонстрировало области значительного разрушения (1.5–2 мкм). Отметим, что хрупкое разрушение, типично для покрытий с высокой долей фазы DLC [54, 55]. Тем не менее, оно не оказывало влияния на коэффициент трения.
Рис. 7.
3D и 2D профили дорожек износа для покрытий Cr–B–C–N, полученных в среде Ar (а), N2 (б), C2H4 (в).
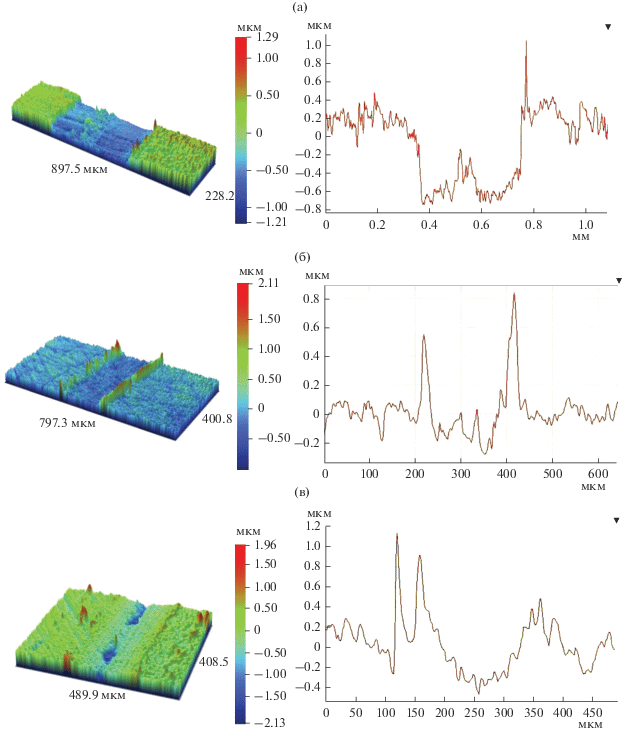
Значения скоростей износа (Vw) показаны в табл. 2. Наибольший приведенный износ 3 × × 10–6 мм3 Н–1 м–1 имеют покрытия системы Cr–B. Такие значения могут быть обусловлены попаданием твердых частиц CrB2, образованных в результате механического воздействия шарика-индентора на покрытие, в дорожку износа. Такие частицы выступают в роли абразивных включений и способствуют быстрому износу покрытия [14]. Это предположение подтверждают профили дорожек износа, представленные на рис. 7, на которых видно, что продукты износа скапливается в центре, а не по краям дорожки. Наименьшим приведенным износом обладают покрытия Cr–B–C, что объясняется присутствием твердой смазки на основе углерода, однако эта фаза плохо сопротивляется механическому воздействию, вследствие чего в локальных местах глубина износа покрытия сопоставима с его толщиной. Приведенный износ покрытий системы Cr–B–N составляет 9.5 × × 10–7 мм3 Н–1 м–1, что почти на порядок лучше, чем у покрытий CrB2, также следует отметить отсутствие локального истирания до подложки, как у покрытий Cr–B–C.
Сравнение с литературными данными показывает, что приведенный износ покрытия 1 ниже, чем для испытанных ранее покрытий CrB2, показавших 18.9 × 10–6 мм3 Н–1 м–1 [15]. Для покрытия 2 износостойкость сопоставима с результами работы [16] по покрытиям Cr–B–N, в которой при использовании шарика WC–6% Co были получены величины 0.8–1.2 × 10–6 мм3 Н–1 м–1 и несколько хуже, чем в работе [53], где при использовании шарика Al2O3 значения Vw составляли (0.4–3.2) × 10–7 мм3 Н–1 м–1. Публикации по системе Cr–B–C [16] сообщают о том, что покрытия обладают Vw = 3.2 × 10–6 мм3 Н–1 м–1, что выгодно отличает изученные покрытия 3, показавшие Vw = 5 × 10–7 мм3 Н–1 м–1.
Результаты исследований высокотемпературных свойств покрытий представлены на рис. 8. Было установлено, что дополнительное введение атомов углерода и азота к покрытиям CrB2, снижает стойкость к высокотемпературному окислению, что можно объяснить интенсивным формированием летучих оксидов на базе этих элементов при нагреве в среде воздуха (CO2, CO, NO2) [57–59]. Лучшие результаты (жаростойкость до 1000°С) были достигнуты для нереакционного покрытия. Важно отметить, что параллельно с процессом окисления происходит интенсивная диффузия бора вглубь подложки из титанового сплава. Ранее подобный эффект наблюдался при высокотемпературных испытаниях покрытий Ti–Cr–B–N [60].
Рис. 8.
Элементные профили покрытий Cr–B–C–N, полученных в среде азота (а), этилена (б), аргона (в–д) после отжигов при 600°С (а–в), 800°С (г) и 1000°С (д).
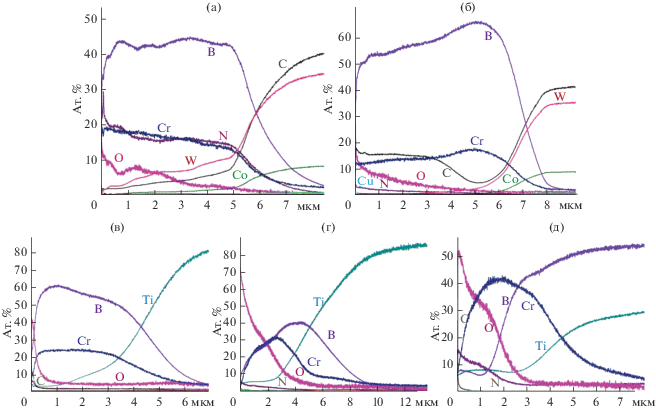
Авторы выражают благодарность М.И. Петржику и Н.В. Швындиной за помощь в проведении исследований методами наноиндентирования и растровой электронной микроскопии. Работа выполнена при поддержке Министерства образования и науки России (Госзадание № 11.7172.2017/8.9).
Список литературы
Jiang J., Wang Y., Zhong Q. et al. // Surface and Coatings Technology. 2011. V. 206. P. 473–478.
Chowdhury S., Polychronopoulou K., Cloud A. et al. // Thin Solid Films. 2015. V. 595. P. 84–91.
Yu L.G., Khor K.A., Sundararajan G. // Surface and Coatings Technology. 2006. V. 201. P. 2849–2853.
Nedfors N., Tengstrand O., Lu J. et al. // Surface and Coatings Technology. 2014. V. 257. P. 295–300.
Mirzaei S., Alishahi M., Souček P. et al. // Surface and Coatings Technology. 2019. V. 358. P. 843–849.
Dahm K.L., Jordan L.R., Haase J., Dearnley P.A. // Surface and Coatings Technology. 1998. V. 108–109. P. 413–418.
Audronis M., Leyland A., Kelly P.J., Matthews A. // Surface and Coatings Technology. 2006. V. 201. P. 3970–3976.
Jha M., Marka S., Krishna M.Gh., Ganguli A.K. // Materials Letters. 2012. V. 73. P. 220–222.
Zhang Sh., Wang Zh., Guo P. et al. // Surface and Coatings Technology. 2017. V. 322. P. 134–140.
Musil J. // Surface and Coatings Technology. 2012. V. 207. P. 50–65.
Cheng C.-H., Lee J.-W., Ho L.-W. et al. // Surface and Coatings Technology. 2011. V. 206. P. 1711–1719.
Nedfors N., Primetzhofer D., Wang L. et al. // Surface and Coatings Technology. 2015. V. 266. P. 167–176.
Boll T., Thuvander M., Koch S. et al. // Ultramicroscopy. 2015. V. 159. P. 217–222.
Kiryukhantsev-Korneev Ph.V., Pierson J.F., Bychkova M.Y. et al. // Tribology Letters. 2016. V. 63. № 3. P. 44.
Kiryukhantsev-Korneev F.V., Novikov A.V., Sagalova T.B. et al. // Physics of Metals and Metallography. 2017. V. 118. P. 1136–1146.
Wang Q., Zhou F., Ma Q. et al. // Applied Surface Science. 2018. V. 443. P. 635–643.
Zhou F., Ma Q., Wang Q. et al. // Tribology International. 2017. V. 116. P. 19–25.
Wang Q., Zhou Fei, Zhu L. et al. // Tribology International. 2019. V. 130. P. 146–154.
Kiryukhantsev-Korneev Ph.V., Pierson J.F., Petrzhik M.I. et al. // Thin Solid Films. 2009. V. 517. P. 2675–2680.
Shtansky D.V., Kiryukhantsev-Korneev F.V., Sheveiko A.N. et al. // Physics of the Solid State. 2005. V. 47. № 2. P. 252–262.
Park I.W., Lin J., Moerbe W.C. et al. // Int. J. Nanomanufacturing. 2007. V. 1. P. 389–429.
Hegedus E., Kovács I., Pécz B. et al. // Vacuum. 2008. V. 82. P. 209–213.
Mallia B., Stüber M., Dearnley P. // Thin Solid Films. 2013. V. 549. P. 216–223.
Audronis M., Rosli Z.M., Leyland A. et al. // Surface and Coatings Technology. 2008. V. 202. P. 1470–1478.
Audronis M., Kelly P.J., Leyland A., Matthews A. // Thin Solid Films. 2006. V. 515. P. 1511–1516.
Zhou M., Nose M., Makino Y., Nogi K. // Thin Solid Films. 2000. V. 359. P. 165–170.
Myoung H., Zhang H.-B., Park T.-F. et al. // J. Kor. Inst. Surf. Eng. 2012. V. 45. P. 232–241.
Kiryukhantsev-Korneev Ph.V., Horwat D., Pierson J.F., Levashov E.A. // Technical Physics Letters. 2014. V. 40. P. 614–617.
Choi H.S., Park B., Lee J.J. // Surface and Coatings Technology. 2007. V. 202. P. 982–986.
Jayaraman S., Klein E.J., Yang Y. // J. Vac. Sci. Technol. A. 2005. V. 23. P. 631–633.
Aouadi S.M., Namavar F., Tobin E. et al. // J. Applied Physics. 2002. V. 91. P. 1040–1045.
Kiryukhantsev-Korneev F.V., Shirmanov N.A., Sheveiko A.N. et al. // Russian Engineering Research. 2010. V. 30. P. 909–919.
Martin P.J., Bendavid A. // Thin Solid Films. 2001. V. 394. P. 1–15.
Witke T., Schuelke T., Schultrich B. et al. // Surface and Coatings Technology. 2000. V. 126. P. 81–88.
Siemroth P., Schülke T., Witke T. // Surface and Coatings Technology. 1994. V. 68–69. P. 314–319.
Polychronopoulou K., Baker M.A., Rebholz C. et al. // Surface and Coatings Technology. 2009. V. 204. P. 246–255.
Rother B., Kappl H. // Surface and Coatings Technology. 1995. V. 73. P. 14–17.
Kiryukhantsev-Korneev Ph.V., Sheveyko A.N., Kuptsov K.A. et al. // Protection of Metals and Physical Chemistry of Surfaces. 2013. V. 49. № 6. P. 677–681.
Kiryukhantsev-Korneev Ph., Sytchenko A., Sheveyko A., Vorotilo S. // Coatings. 2019. V. 9. P. 230.
Kurbatkina V.V., Levashov E.A., Patsera E.I., Kochetov N.A., Rogachev A.S. // Int. J. SHS. 2008. V. 17. № 3. P. 1–6.
Kiryukhantsev-Korneev F.V. // Russian J. Non-Ferrous Metals. 2014. V. 55. P. 494–504.
Levashov E.A., Shtansky D.V., Kiryukhantsev-Korneev Ph.V. et al. // Russian Metallurgy, Metally. 2010. № 10. P. 917–935.
http://www.shs.misis.ru/docs/booklet.equipment.www. shs.misis.ru.pdf
Oliveira J.C., Oliveira M.N., Conde O. // Surface and Coatings Technology. 1996. V. 80. P. 100–104.
Кривченко В.А., Лопаев Д.В., Минаков П.В. и др. // Журн. технической физики. 2007. V. 77. P. 83.
Bachmann P.K., Wiechert D.U. // in Diamond and Diamond-Like Films and Coatings, ed. Clausing, R.E., Plenum Press. New York. 1991. P. 677.
Кирюханцев-Корнеев Ф.В., Бондарев А.В. // Физика металлов и металловедение. 2019, том 120. № 7. с. 764–770.
Shi L., Gu Y., Chen L. et al. // Solid State Communications. 2003. V. 128. P. 5–7.
Tallant D.R., Aselage T.L., Campbell A.N., Emin D. // Physical review B. 1989. V. 40. P. 5649.
Menaka M., Ganguli A.K., Krishna M.Gh. // Surface and Coating Technology. 2012. V. 209. P. 23–31.
Bunda K.P., Mayrhofer P.H., Neidhardt J. et al. // Surface and Coating Technology. 2008. V. 202. P. 3088–3093.
Leyland A., Matthews A. // Wear. 2000. V. 246. P. 1–11.
Jahadova V., Ding X.-Zh., Seng D.H.L. et al. // Thin Solid Films. 2013. V. 544. P. 335–340.
Lin J., Moore J.J., Moerbe W.C. et al. // International J. Refractory Metals and Hard Materials. 2010. V. 28. P. 2–14.
Miyoshi K., Pohlchuck B., Street K.W. et al. // Wear. 1999. V. 225–229. P. 65–73.
Bernoulli D., Häfliger K., Thorwarth K. et al. // Acta Materialia. 2015. V. 83. P. 29–36.
Sairam K., Sonber J., Murthy T.S.R.Ch. et al. // International J. Refractory Metals and Hard Materials. 2012. V. 35. P. 32–40.
Qi B., Liu B., Wu Z. T. et al. // Thin Solid Film. 2013. V. 544. P. 515–520.
Meng Ch., Yang L., Wu Y. et al. // J. Nuclear Material. 2019. V. 515. P. 354–369.
Kiryukhantsev-Korneev F.V., Sheveiko A.N., Komarov V.A. et al. // Russian J. Non-Ferrous Metals. 2011. V. 52. № 3. P. 311–318.
Дополнительные материалы отсутствуют.
Инструменты
Физикохимия поверхности и защита материалов