Физикохимия поверхности и защита материалов, 2020, T. 56, № 3, стр. 243-251
Формирование металл-оксидных наноструктур при оксидировании срезов пластически деформированного железа
В. А. Котенев 1, *, В. В. Высоцкий 1, М. Р. Киселев 1, А. А. Аверин 1, Д. Н. Тюрин 1
1 Институт физической химии и электрохимии им. А.Н. Фрумкина РАН
Москва, Ленинский пр., 31, Россия
* E-mail: m-protect@phyche.ac.ru
Поступила в редакцию 12.10.2019
После доработки 23.10.2019
Принята к публикации 30.10.2019
Аннотация
Методами сканирующей электронной микроскопии с рентгеновским зондом, спектроскопии комбинационного рассеяния и термогравиметрии исследованы морфология и состав оксидного слоя на поверхности срезов стружки железа, полученной металлобработкой в условиях интенсивной пластической деформации сдвига и последующим термооксидированием. Показано, что при отжиге на воздухе при 800°С на поверхности металлической стружки с высокой скоростью формируются массив металл-оксидных наночастиц и наноструктур (вискеров, наноигл, нанолистьев), перспективных для производства новых композиционных материалов с ультрадисперсным металл-оксидным наполнителем. Экономические и экологические выгоды, связанные с повторным использованием отходов металлообработки для производства новых металл-оксидных наноматериалов и композитов на их основе, должны быть значительными.
ВВЕДЕНИЕ
Прогресс в создании конструкционных и функциональных металл-оксидных материалов и покрытий во многом связан с разработкой новых энергосберегающих методов обработки металлов. Особый интерес представляют собой методы комбинированного механического и термического воздействия на металлы и сплавы, что может привести к созданию новых типов металл-оксидных наноструктур, представляющих перспективную основу для создания новых композиционных материалов, демонстрирующих уникальные свойства: конструкционные, защитные, функциональные (каталитические, сенсорные, электрические, оптические и др.) [1–12]. Особо эффективным является получение и использование наночастиц оксидов железа, представляющих собой в общем случае N-мерные металл-оксидные наночастицы: 1-мерные наноусы, 2-мерные ленты, чешуйки, слои и 3-мерные наночастицы различной морфологиии, структуры, состава. Среди известных окислов железа особый интерес представляет гематит (α-Fe2O3) – полупроводниковое соединение, нетоксичное, обладающее целым набором функциональных свойств. Он может быть эффективно использован в качестве фотоанода для фотоэлектролиза воды [13], в качестве активного элемента газовых сенсоров [14], в фотокатализе [15], в качестве обычного катализатора [16].
Металл-оксидные вискеры (нанопроволоки, наноусы гематита и др.) на основе железа были синтезированы в 1950-х [5, 6]. В дальнейшем металл-оксидные вискеры были получены методом термического окисления железной фольги [7] или порошка железа [8] при высокой температуре. В настоящее время металл-оксидные наночастицы получают с использованием целого ряда методов: с использованием темплатов, гидротермальным окислением, золь–гель методами, реактивным распылением и др. [2–4]. Эти методы позволяют получить различные металл-оксидные наночастицы, но они не всегда технологичны и, как результат, стоимость их применения может быть достаточно высока.
Среди методов формирования металл-оксидных наноструктур выделяется своей простотой, экономичностью и технологичностью метод прямого газового оксидирования [21, 22]. При этом условием роста вертикальных к поверхности 1-мерных оксидных наночастиц (вискеров, усов) служат внутренние напряжения в поверхностном слое металла и оксидном слое [17–20]. Кроме того, в целом ряде работ было обнаружено, что условием роста вискеров является первоначальное быстрое формирование оксидного слоя, из зерен которого далее растут оксидные вискеры [23]. Очевидно, отсюда следует требование высокой скорости диффузионных процессов в поверхностных слоях металла и на границе раздела металл–оксид.
Двум отмеченным условиям ускоренного роста оксидных вискеров может удовлетворить технология интенсивной пластической деформации (ИПД) металлов и сплавов [1, 9, 10, 24, 25]. В процессах ИПД формируется мелкозернистая11 структура металла [1], что приводит к высоким начальным скоростям диффузионных процессов в металле [25]. В процессе ИПД и высокотемпературного отжига и оксидирования в поверхностном металл-оксидном слое возникают градиенты внутренних напряжений, что может обеспечить высокие скорости диффузионных процессов для направленного роста оксидных вискеров.
Технология ИПД предполагает объемную деформацию образца с помощью таких процессов, как прокатка, волочение, равноканальное угловое прессование и др. В целом ряде работ [26–29] было показано, что оригинальным процессом ИПД, включающим в себя создание больших степеней деформации с высокими скоростями, является стружкообразование в процессе механической металлообработки (например, при формировании срезов (стружки) металлов на токарном станке). В работе [26] было показано, что характеристики полей деформации при стружкообразовании отличаются от других процессов интенсивной пластической деформации: значения деформации, скорости деформации и температуры в зонах сдвига значительно выше, чем при других обычных операциях интенсивного пластического деформирования, таких как, например, равноканальное угловое прессование.
В работе [27] исследовали стружку различных металлов и сплавов, полученную токарной обработкой (ИПД тонкого поверхностного слоя), и обнаружили, что стружка имеет наноструктуру с размерами металлических зерен от 100 до 800 нм. Было показано, что механическая резка металлов является перспективным процессом для создания нанокристаллических материалов.
В настоящей работе исследована возможность применения технологии интенсивной пластической деформации сдвига, позволяющей создавать мелкозернистые наноструктурированные металлы в виде стружки для последующего выращивания одномерных наночастиц оксидов.
МЕТОДИКА ЭКСПЕРИМЕНТА
В качестве обрабатываемого и контрольного (исходного) образцов использовали цилиндрические образцы железа Армко диаметром 8 мм. Использовалась механическая обработка образца железа на токарном станке – процесс, в котором жесткий клиновидный индентор (резец) удаляет материал (стружку) с поверхности твердого тела путем интенсивной пластической деформации
На рис. 1 приведен снимок стружки, полученной резкой металлического образца железа. Формирование стружки происходит за счет концентрированной деформации сдвига вдоль узкой зоны, называемой плоскостью сдвига (рис. 1а и 1б). Видно, что стружка имеет 2 поверхности: деформируемая поверхность (левая сторона стружки на рис. 1) и поверхность среза стружки (правая часть стружки на рис. 1). В работе морфологически исследовалась поверхность среза стружки, непосредственно контактировавшая с индентором (резцом) при срезании поверхностного слоя металла.
Рис. 1.
(а) Схема процесса механической обработки металла с формированием стружки: Vo – направление и скорость движения металла относительно резца, Vc – направление и скорость движения стружки; (б) микрофотография (SEM) фрагмента стружки.
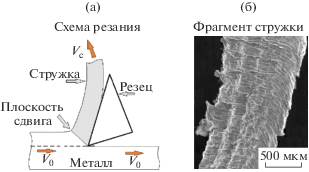
Скорость вращения образца – 300 об./мин. Подача образца: 0.038/оборот. Скорость резки = = 0.12 м/с.
После токарной обработки цилиндрического образца железа собирались образцы стружки. Данные образцы стружки нагревали на термовесах TA INSTRUMENT Q500 со скоростью 30 град/мин (ТГА-отжиг) до 800°С в атмосфере аргона (для предотвращения окисления образцов до выхода на рабочую температуру 800°С). Затем переходили в изотермический режим оксидирования при 800°С в течение 2 ч с заменой Ar на осушенный воздух. За процессом окисления следили по приращению массы образцов. Результаты представлены в виде отдельных и совмещенных кривых TGA. Представлены сравнительные кривые: стружка и исходный необработанный образец в зависимости от времени и температуры.
Для контроля морфологии поверхностей среза образцов стружки использовали метод электронной микроскопии. Использовался растровый электронно-микроскопический комплекс (РЭМ) с полевым катодом Quanta 650 FEG (FEI, Нидерланды) в режиме детектирования вторичных электронов.
Фазовый состав пленок контролировался с использованием зондовой спектроскопии комбинационного рассеяния света на спектрометре Senterra “Bruker” в области 200–800 см–1. Спектры зарегистрированы при λвозб = 532 нм и мощности лазера, равной 0–20 мВт. Для регистрации спектра использовали 50× объектив (диаметр измеряемой площадки ~2 мкм), в качестве источника излучения – полупроводниковый Nd : YAG лазер с длиной волны λ = 532 нм. Мощность лазера, для избежания нагрева и разрушения/доокисления образца, составляла 2 мВт. Идентификация фазового состава пленок спектров велась сравнением полученных КР-спектров с известными спектрами поглощения индивидуальных оксидов или КР-спектрами оксидных пленок [30–35].
РЕЗУЛЬТАТЫ
ТГА-оксидирование
На рис. 2 приведены результаты ТГА-анализа процесса оксидирования стружки и исходного образцов железа. На рис. 3 приведен спектр РСМА (элементного состава) неокисленного образца (а) и окисленной (б) стружки.
Рис. 2.
Термогравиметрия процесса оксидирования стружки (1) и исходного необработанного объемного образца (2).
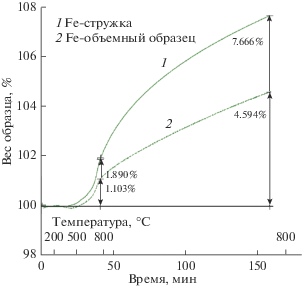
Поскольку оксидирование велось на воздухе, исходя из диаграммы состояния системы Fe–O [41] и данных PCMA полагалось, что область оксидирования при 800°С соответствует формированию фаз вюстита, магнетита и гематита.
В образцах стружки приращение массы при изотермическом ТГА-отжиге при 800°С было примерно в 1.6–2 раза больше чем в образце исходного железа. Заметная разница скоростей оксидирования наблюдалась к 120 мин окисления (для стружки – 7.67%, для исходного образца железа – 4.59%) (рис. 2а, 2б). При этом при нагревании до 800°С температурная зависимость не показала тенденцию к запределиванию, что очевидно при больших экспозициях позволяет получить более значительные приросты массы оксидного слоя.
Полученная кинетика прироста массы образца стружки на начальных стадиях роста не соответствовала чисто диффузионному контролю, характерному для исходного образца (рис. 2), что, очевидно, было связано не только с диффузионным контролем процесса оксидирования стружки при 800°С [41]. Очевидно, более высокая начальная скорость оксидирования стружки по сравнению с исходным образцом говорит о более высокой скорости диффузионных процессов и приповерхностных слоях пластически деформированного металла. Поэтому быстрое торможение процесса окисления в деформированных образцах стружки с ростом экспозиции (по сравнению с исходным образцом) может быть связано не только с формированием защитного оксидного слоя на поверхности стружки, но также рекристаллизацией металла на границе металл–оксид. (Крупные зерна, растущие при высокотемпературном оксидирующем отжиге и рекристаллизации нанокристаллического металла стружки, уменьшают площадь границ зерен поверхностного слоя металла, что очевидно замедляет зернограничную диффузию из металла и общую скорость окисления стружки.)
Скорость прироста массы стружки падала с экспозицией за 100 мин более резко, чем для исходного образца. С ростом времени (к 100 мин) оксидирования скорость прироста массы стружки приближалась к скорости прироста массы исходного образца (рис. 2) что говорит о диффузионном контроле процесса оксидирования толстым слоем окалины на данных стадиях уже как основном.
Спектроскопия комбинационного рассеяния (КР)
На рис. 4 приведены спектры КР термообработанных образцов стружки. Наблюдаемые в спектрах полосы поглощения в основном соответствуют оксидам железа [30–35]. В низкочастотной области спектра доминируют полосы (225 и 279 см–1), 410, 495 см–1 , которые можно отнести к гематитовой фазе. В более высокочастотной области спектра наблюдается широкая полоса 590–620 см–1, которую можно отнести как к гематитовой, так и к магнетитовой фазам, полоса 645 см–1 – полоса вюстита, а также интенсивная полоса 1320 см–1, которую можно отнести к фазе гематита.
Рис. 4.
Спектры комбинационного рассеяния термообработанных образцов Область (а) – внешняя сторона окалины, область (б) – область стружки, где пленка отслоена.
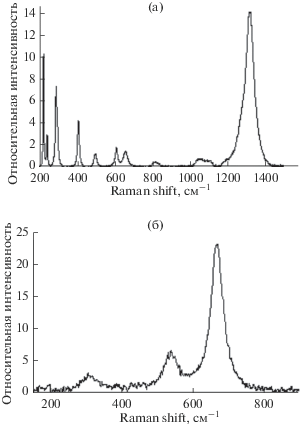
На рис. 4а представлен типичный спектр окалины, образовавшейся после оксидирования среза стружки при температуре 800°С и соответствует α-Fe2O3 + Fe3O4 + FeO. Данная окалина легко отслаивается от части поверхности образца (рис. 6-I). Спектры с поверхности стружки без окалины представлена на рис. 4б, и соответствуют Fe3O4 + FeO.
Области стружки: А – окалина, Б – место, где пленка отслоилась, на поверхности находится Fe3O4 и FeO.
Окалина состоит из 3 подслоев: примыкающий к металлу подслой Fe3O4 + FeO (обладающий высокой адгезией к металлу), толстый слой окалины – объемного слоя вюстита и магнетита, слой гематита и над ним – слой гематитовых вискеров [36].
SEM-микроскопия
На рис. 1, 5, 6 приведены SEM-изображения поверхности стружки до и после оксидирующего отжига. На рис. 3 приведен спектр РСМА окисленной стружки (а) и окисленного исходного образца (б), показывающий более высокую степень окисления при оксидировании стружки по сравнению с оксидированным исходным образцом. При этом повышенное соотношение атомарного кислорода к металлу говорит в пользу повышенного содержании термодинамически обусловленной при 800°С вюститной фазы в окисленной стружке по сравнению с оксидированным исходным образцом.
Рис. 5.
Структура поверхности стружки окисленной на воздухе при 300°С в течение 2 часов (3 разных увеличения).
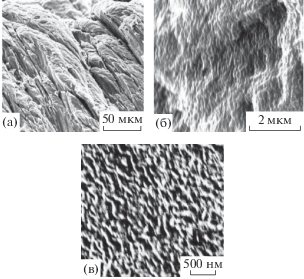
Образец стружки (до высокотемпературной термообработки) (рис. 5) имеет нерегулярную структуру и состоит из соприкасающихся вытянутых зерен со средним разбросом размеров в вытянутом направлении от 0.5 до 5 мкм. Отчетливо видна сильная деформация зерен, очевидно с высокой плотностью дислокаций. На образце исходного образца после оксидирования наблюдается окалина с зернами гематита субмикронных размеров без каких-либо выраженных 1-мерных структур типа вискеров (рис. 6в).
Рис. 6.
SEM-изображения поверхности стружки после отжига в течение 2 часов при 800°С: I – обзорный снимок отожженной стружки после отслаивания части окалины (А – область окалины, Б – область отслоившейся окалины), II – область А с разными увеличениями, III – изображение поверхности образца после отжига: область Б стружки и исходного образца.
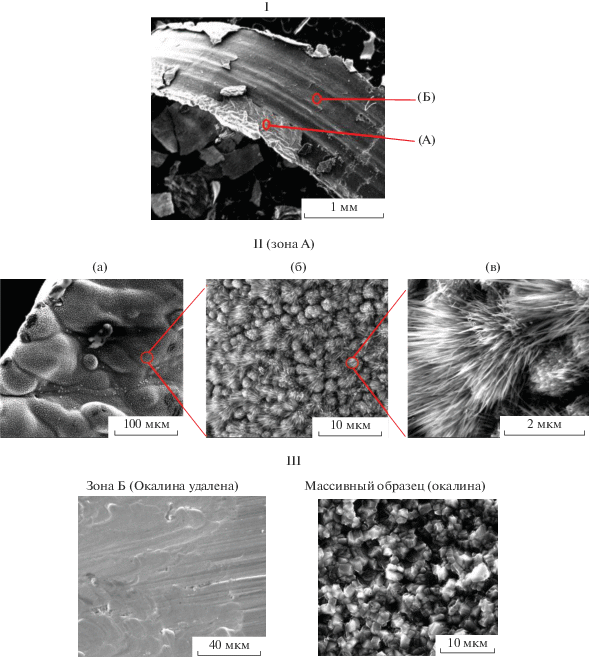
Особенностью оксидированной стружки (рис. 6а–6в) является появление слоя преимущественно ориентированных под прямым углом к поверхности 1-мерных оксидных наночастиц гематита (рис. 6в), формирующих “гематитовый лес” [20–23]. По данным Раман-спектроскопии на оксидированной поверхности среза стружки регистрируется фаза гематита, рис. 4а. На рис. 6б приведены особенности структуры оксидированной стружки. Видно, что на поверхности присутствуют локальные выпуклости, которые по размерам сопоставимы с нанозернами металла и из которых происходит клумбообразный радиальный рост 1-мерных вискеров. По краям выпуклостей наблюдаются области поверхности, из которых также растут 1-мерные вискеры (усы). Если предположить, что поверхностный слой металла после деформации и оксидирования представляет собой контактирующие и сросшиеся зерна железа, отсюда следует, что наиболее интенсивно 1-мерные наночастицы гематита растут по межчастичным (межзеренным) границам22.
Очевидно, при формировании такого массива наночастиц удельная поверхность гематита резко возрастает, что очевидно позволяет объяснить наблюдаемый в целом ряде работ [47–49] рост функциональных свойств (каталитических, фотоэлектрохимических и др.) такого “гематитового леса”.
Адгезия окалины на части поверхности оксидированной стружке понижена, так что окалина здесь может быть отделена. На рис. 6а приведены снимки поверхности стружки, частично покрытой толстой окалиной и частично – с отслоенной окалиной. Видно, что после отслаивания поверхность внешней стороны стружки (поверхность среза стружки) достаточно гладкая.
По данным Раман-спектроскопии на поверхности с отслоенной окалиной регистрируются магнетит-вюститные формы оксидов железа.
На различных участках поверхности стружки, в зависимости от положения относительно краев чипов стружки, тип оксидных наночастиц может кардинально меняться. На рис. 7 приведены различные типы металл-оксидных наноструктур, сформированных на различных участках поверхности стружки: (а) – 3-мерные оксидные наночастицы, (б) – 1-мерные вискеры (наноусы), (в) – 2-мерные нанолистья, (г) – 2-мерная оксидная “сетевая” структура.
ОБСУЖДЕНИЕ
Механическая обработка металла на токарном станке вызывает обширную и неравномерную деформацию образующейся стружки. Эта деформация приводит к формированию вытянутых в направлении вращения вала станка крупных поверхностных зерен (рис. 5), а также к параллельному формированию мелкозернистой структуры металла стружки. Крупные поверхностные зерна, растущие при последующем высокотемпературном оксидирующем отжиге и рекристаллизации, уменьшают площадь границ зерен, что очевидно замедляет зернограничную диффузию из металла и общую скорость окисления стружки. Кроме того, происходящая в железе при 800°С рекристаллизация приводит к ослаблению адгезионных сил между оксидом (вюститом) и железом на локальных участках поверхности [41, 42]. Железные вакансии, диффундирующие в сторону металла через оксидную пленку могут агломерировать в этих областях, вызывая образование полостей. Такие полости препятствуют диффузии, и поэтому активность железа во внешней оксидной пленке снижается, что приводит к дальнейшему уменьшению скорости окисления железной фазы33.
Отсюда следует казалось бы очевидный вывод, ранее сделанный для компактированного порошка железа [20], что механическая обработка и последующий оксидирующий отжиг должны обеспечивать большую стойкость к окислению металла.
Однако этот вывод сделан без учета временного фактора, а также без учета влияния деформации обработанного металла и оксида на скорость роста оксида и оксидных вискеров. Действительно, на начальных стадиях скорость оксидирования достаточно высока, что связано с мелкозернистой структурой ИПД-обработанного металла. Поэтому на наноструктурированной поверхности стружки (когда крупные зерна еще не успели вырасти и заметно ограничить скорость диффузии) скорость оксидирования может достаточно высока по сравнению с необработанным металлом, что подтверждается рис. 2.
Кроме того, при деформировании и оксидировании металла обычно происходит формирование сильно сжатых слоев межфазной металл-оксидной фазы44. Результирующий градиент внутренних напряжений от границы металл–оксид к границе оксид–газ приводит к массопереносу металла от границы металл–оксид к границе оксид–газ [37, 38]. Такой направленный массоперенос может служить причиной как спекания [50], так и ускоренного роста наноусов и нанолистьев при оксидировании металла даже при сравнительно невысоких температурах [20, 37]. Эффект может быть гораздо более выражен при гетерофазных реакциях в слое окалины при повышенных температурах.
Таким образом отсюда следует, что механическая обработка и последующий оксидирующий отжиг, обеспечивающие соответственно начальное ускорение и последующее торможение скорости роста оксидных фаз, могут вызвать существенное ускорение роста оксидных вискеров перпендикулярно к поверхности металла. При этом неоднородность процессов рекристаллизации и скорости оксидирования вдоль границы металл-окалина очевидно приводят к формированию различных типов металл-оксидных наночастиц (рис. 7).
Помимо гематитовой не исключена магнетитовая природа наблюдаемых вискеров и наноструктур, инициируемых пластической деформацией в металле [38]. Данные структуры помимо собственных функциональных (сенсорных, каталитических, полупроводниковых, адсорбционных) также обладают выраженными свойствами праймеров для дальнейшего нанесения и формирования защитных и функциональных поверхностных слоев [44–46].
ВЫВОДЫ
В настоящей работе для создания темплатов для последующего роста наноструктур гематита применена технология интенсивной пластической деформации сдвига поверхностного слоя металла на металлорежущем (токарном) станке. В результате формируется и срезается нанокристаллический слой металла (стружка), на котором при дальнейшем оксидирующем отжиге на воздухе формируется слой металл-оксидных наночастиц (наноигл, нанолистьев), перспективных для производства новых композиционных материалов с ультрадисперсным оксидным наполнителем, обладающих выраженными эксплуатационными (прочностными, защитными, функциональными и др.) свойствами.
Несмотря на то, что использован высокотемпературный отжиг (800°С), приводящий к рекристраллизации и росту зерен металла, высокая начальная скорость высокотемпературного оксидирования при 800°С может обеспечить высокую производительность процесса выращивания оксидных вискеров.
Таким образом механическая металлообработка может быть перспективным методом получения материалов с нанокристаллической и мелкозернистой структурой для последующего роста на них массивов металл-оксидных наночастиц. Огромное количество производимой в процессе промышленной металлообработки стружки, которая в настоящее время переплавляется или утилизируется в виде лома, состоит из ультрадисперсных структур. После технологических операций оксидирования и компактирования из данной стружки можно получать металл-оксидные наноматериалы с повышенными конструкционными и функциональными свойствами. Поэтому использование отожженной стружки в качестве наполнителя композиционных и волокнистых материалов представляется весьма перспективным.
Экономические и экологические преимущества повторного использования таких отходов металлообрабатывающей промышленности, как металлическая стружка, представляются весьма значительными.
Работа выполнена в рамках госзадания по теме госзадания “Физикохимия функциональных материалов на основе архитектурных ансамблей металл-оксидных наноструктур, многослойных наночастиц и пленочных нанокомпозитов”. Регистрационный номер НИОКТР АААА-А19-119031490082-6.
Список литературы
Gleiter H. // Nanostruct. Mater. 1992. V. 1. № 1. P. 1.
1-Dimensional Metal Oxide Nanostructures. Growth, Properties, and Devices // Ed. Zainovia Lockman // Advances in Materials Science and Engineering. CRC Press. Taylor & Francis Group. 2019.
Суздалев И.П. Нанотехнология: физикохимия нанокластеров, наноструктур и наноматериалов. М.: КомКнига, 2006. 592 с.
Synthesis, properties, and applications of oxide nanomaterials // Ed. by José A. Rodríguez, Marcos Fernández-García // JohnWiley & Sons, Inc., Hoboken, New Jersey, 2007.
Takagi R. // J. Phys. Soc. Jpn. 1957. V. 12. P. 1212.
Laukonis J.V., Coleman R.V. // J. Appl. Phys. 1959. V. 30. P. 1364.
Srivastava H., Tiwari P., Srivastava A.K., Nandedkar R.V. // J. Appl. Phys. 2007. V. 102. P. 054303.
Chioncel M.F., Diaz-Guerra C., Piqueras J. // J. Appl. Phys. 2008. V. 104. P. 124311.
Колмаков А.Г., Баринов С.М., Алымов М.И. Основы технологий и применение наноматериалов. М.: ФИЗМАТЛИТ, 2012. 208 с.
Гусев И.А. // УФН. 1998. Т. 68. № 1. С. 55–83.
Karbasi M., Tavangarian F., Vardak S., Saidi A. // Prot. Met. Phys. Chem. Surf. 2013. V. 49. № 5. P. 548.
Uros Cvelbar, Zhiqiang Chen, Mahendra K. Sunkara, Miran Mozetic // Small. 2008. V. 4. № 10. P. 1610–1614.
Kennedy J.H., Anderman M. // J. Electrochem. Soc. 1983. V. 130. P. 848.
Chauhan P., Annapoorni S., Trikha S. // Thin Solid Films. 1999. V. 346. P. 266.
Ohmori T., Takahashi H., Mametsuka H., Suzuki E. // Phys. Chem. Chem. Phys. 2000. V. 2. P. 3519.
Weiss W., Zscherpel D., Schlogl R. // Catal. Lett. 1998. V. 52. P. 215.
Lu Yuana, Yiqian Wangb, Rongsheng Caib, Qike Jiangc, Jianbo Wangc, Boquan Lid, Anju Sharmae, Guangwen Zhou // Materials Science and Engineering B. 2012. V. 177. P. 327–336.
Wen Xiaogang, Wang Suhua, Ding Yong et al. // J. Phys. Chem. B. 2005. V. 109. P. 215.
Yingying Xu, Guanxiang Yun, Zhao Dong et al. // Nanoscale. 2012. V. 4. P. 257.
Kotenev V.A., Zhorin V.A., Kiselev M.R., Vysotskii V.V., Averin A.A., Roldugin V.I., Tsivadze A.Yu. // Protection of Metals and Physical Chemistry of Surfaces. 2014. V. 50. № 6. P. 792–796.
Raynaud G., Rapp R. // Oxidation of Metals. 1984. V. 21. P. 89.
Fu Y., Chen J., Zhang J. // Chem. Phys. Lett. 2001. V. 350. P. 491.
Tu K.N., Li J.C.M. // Mater. Sci. Eng. A. 2005. V. 409. P. 131.
Koch C.C., Ovid’ko I.A., Sudipta S.S., Veprek S. Structural nanocrystalline materials: Fundamentals and applications. Cambridge, University Press, 2007.
Валиев Р.З., Александров И.В. Наноструктурные материалы, полученные интенсивной пластической деформацией. М.: Логос, 2000. 272 с.
Jaspers S.P.F.C., Dautzenberg J.H. // J. Mater. Process. Technol. 2002. V. 121. P. 123–135.
Brown T.L., Swaminathan S., Chandrasekar S., Compton W.D., King A.H., Trumble K.P. // J. Mater. Res. 2002. V. 17. P. 2484–2488.
Deng W.J., Xia W., Li C., Tang Y. // J. Materials Processing Technology. 2009. V. 209. P. 4521–4526.
Deng W.J., Xia W., Li, Tang Y. // Materials and Manufacturing Processes. 2010. V. 25. P. 355–359.
Gardiner D.J., Littleton C.J., Thomas K.M., Stratford K.N. // Oxidation of Metals. 1987. V. 27. P. 57.
Tjong S.C. // Mater. Res. Bull. 1983. V. 18. P. 157.
Singh Raman R.K., Gleeson B., Young D.J. // Materials Science and Technology. 1998. V. 14. P. 373.
Thibeau R.J., Brown C.W., Heidersbach R.H. // Appl. Spectroscopy. 1978. V. 32. P. 532.
Nasibulin A.G., Rackauskas S., Jiang H., Tian Y., Mudimela P.R., Shandakov S.D., Nasibulina L.I., Jani Sainio J., Kauppinen E.I. // Nano Res. 2009. V. 2. P. 373–379.
de Faria D.L.A., Silva V., de Oliveira M.T. // J. Raman Spectroscopy. 1997. V. 28. P. 873–878.
Voss D.A., Butler E.P., Mitchell T.E. // Metallurgical transactions A. 1982. V. 13A. P. 929–935.
Kotenev V.A., Kiselev M.R., Vysotskii V.V., Averin A.A., Tsivadze A.Yu. // Protection of Metals and Physical Chemistry of Surfaces. 2016. V. 52. № 5. P. 825–831.
Tohmyoh H., Watanabe A. // J. Phys. Soc. Jpn. 2013. V. 82. P. 044804.
Herring C. // J. Appl. Phys. 1950. V. 21. P. 437.
Korhonen M.A., Borgesen P., Tu K.N., Li C.-Y. // J. Appl. Phys. 1993. V. 73. P. 3790.
Окисление металлов Т. 2 / Под ред. Бенара Ж.М.: Металлургия, 1969. 444 с. [Oxydation des Metaux / Ed. Benard J. Paris: Gauthier-Villars, 1962. V. 2.]
Svedung I., Hammar B., Vannerberg N. // Oxidation of Metals. 1973. V. 6. № 1. P. 21–44.
Dunnington B., Beck F., Fontana M. // Corrosion. 1952. V. 8. P. 2.
Wei Jiangi, Jiaping Qiu, Shaojun Yuan, Ying Wan, Jiemin Zhong, Bin Liang // Protection of Metals and Physical Chemistry of Surfaces. 2015. V. 51. P. 435.
Руднев В.С., Wybornov S., Лукиянчук И.В., Черных И.В. // Физикохимия поверхности и защита материалов. 2014. Т. 50. С. 174.
Soliman H., Hamdy Abdel Salam // Protection of Metals and Physical Chemistry of Surfaces. 2015. V. 51. P. 620.
Vayssieres L., Manthiram A. // One-Dimensional Metal Oxide Nanostructures – Encyclopedia of Nanoscience and Nanotechnology. 2008. V. 8. P. 147.
Lu J., Chang P., Fan Z. // Mater. Sci. Eng. 2006. V. R52. P. 49.
Comini E., Baratto C., Faglia G. et al. // Prog. Mater Sci. 2009. V. 54. P. 1.
Kotenev V.A., Kiselev M.R., Zolotarevskii V.I., Tsivadze A.Yu. // Protection of Metals and Physical Chemistry of Surfaces. 2014. V. 50. N 4. P. 488–492.
Kotenev V. A. // Protection of Metals and Physical Chemistry of Surfaces. 2018. V. 54. N 5. P. 969–975.
Дополнительные материалы отсутствуют.
Инструменты
Физикохимия поверхности и защита материалов