Физикохимия поверхности и защита материалов, 2020, T. 56, № 3, стр. 309-316
Химическое полирование алюминия с помощью обратных микроэмульсий, содержащих кислоту
Н. М. Мурашова 1, *, С. Ю. Левчишин 1, Е. Н. Субчева 1, О. Г. Краснова 1, Е. В. Юртов 1
1 Российский химико-технологический университет им. Д.И. Менделеева
Москва, Россия
* E-mail: namur_home@mail.ru
Поступила в редакцию 23.01.2018
После доработки 25.01.2018
Принята к публикации 01.02.2018
Аннотация
На примере алюминия исследовано химическое полирование металлов с помощью наноструктурированных сред – обратных микроэмульсий. Показано снижение шероховатости поверхности алюминиевой фольги при ее обработке обратной микроэмульсией ди-(2-этилгексил)фосфата натрия в керосине, содержащей внутри капель водный раствор соляной кислоты с концентрацией 0.11 моль/л. При времени полирования 2 ч средняя шероховатость снижалась с 54 до 28 нм. Составы, не образующие микроэмульсии (водный раствор соляной кислоты, раствор аддукта трибутилфосфата с соляной кислотой в керосине, дисперсия ди-(2-этилгексил)фосфата натрия в водном растворе соляной кислоты), не обладают таким действием. Дополнительное воздействие ультразвука при таком же времени проведения процесса, введение в состав микроэмульсии трибутилфосфата и замена соляной кислоты на уксусную или азотную практически не влияет на результат химического полирования.
ВВЕДЕНИЕ
Наноструктурированные жидкие среды, такие как микроэмульсии, лиотропные жидкие кристаллы, прямые и обратные мицеллы, являются перспективными системами для различных отраслей науки и технологии. Микроэмульсии – термодинамически устойчивые изотропные дисперсии неполярной органической и водной фаз, стабилизированные поверхностно-активным веществом (веществами). Диаметр капель микроэмульсии составляет от нескольких нанометров до десятков нм. Микроэмульсии применяют для очистки поверхностей твердых тел от загрязнений, для повышения нефтеотдачи скважин, в строительстве как гидрофобизаторы, для разделения веществ в аналитической химии. Микроэмульсии могут применяться как среды для ферментативных реакций, для проведения полимеризации с получением наноразмерных частиц латексов, для синтеза неорганических наночастиц, для жидкостной и мембранной экстракции органических и неорганических веществ, как носители для адресной доставки лекарственных веществ [1].
Микроэмульсии в качестве наноструктурированных носителей реагентов могут использоваться для разработки и усовершенствования различных процессов, происходящих в системах “жидкость–твердая фаза”. Ранее был предложен метод извлечения металлов из частиц твердой фазы с помощью микроэмульсий (микроэмульсионное выщелачивание). Метод микроэмульсионного выщелачивания предполагает извлечение металлов из техногенного сырья (концентратов, шламов, зол, пылей и т.д.) путем контакта с экстрагент-содержащей микроэмульсией, что позволяет сочетать выщелачивание и экстракцию в одном процессе. Для выщелачивания предлагалось использовать микроэмульсии на основе ди-(2-этилгексил)фосфата натрия (Д2ЭГФNa), содержащие известные экстрагенты ди-(2-этилгексил)фосфорную кислоту и трибутилфосфат [2–4].
Микроэмульсия, как носитель реагента, растворяющего металл, может применяться для снижения шероховатости поверхности (химического полирования) металлов. Часто для химического полирования применяют смеси концентрированных кислот с небольшим количеством воды. При этом результат полирования улучшается при наличии вязкого диффузионного слоя рядом с поверхностью металла, который способствует растворению выступов на поверхности и затрудняет доступ реагента к углублениям [5]. Если кислота будет локализована внутри капель микроэмульсии, то можно снизить ее суммарную концентрацию в полирующей жидкости (микроэмульсии), а также добиться лучшего эффекта полирования за счет диффузионных ограничений. Для химического полирования представляет интерес применение микроэмульсии типа “вода в масле” (обратная микроэмульсия), где дисперсионной средой является неполярный органический растворитель, плохо проводящий электричество. Это поможет избежать возникновения локальных токов, влияющих на процесс химического полирования [5, 6]. Отметим, что литературные данные, посвященные применению микроэмульсий для травления или химического полирования, крайне немногочисленны.
Была показана возможность применения обратных микроэмульсий для травления меди. Использовались микроэмульсии в системах бис-(2-этилгексил)сульфосукцинат натрия (АОТ) – изооктан – вода и Pluronic L62 – ксилол – вода, в каплях которых находился водный раствор смеси хлорида меди(II) и хлорида калия в мольном соотношении 1 : 1. Средняя шероховатость фольги после травления микроэмульсиями на основе Pluronic L62 (содержала 0.05 М KCl + 0.05 M CuCl2) и АОТ (содержала 1.0 М KCl + 1.0 M CuCl2) составила 44 и 70 нм соответственно. После травления водными растворами KCl CuCl2 с той же концентрацией, что была в водной фазе микроэмульсий, значения средней шероховатости были выше: 84 и 88 нм соответственно. Авторы связывают подобный эффект с тем, что капли микроэмульсии, в отличие от растворенных в воде солей, будут лучше взаимодействовать с выступающими дефектами поверхности, чем с микротрещинами. Капля обратной микроэмульсии обладает большими размерами по сравнению с ионами солей в водном растворе. Это будет затруднять доступ реагента из микроэмульсии в микротрещины на поверхности [7].
Показано применение обратной микроэмульсии, содержащей в каплях водный раствор KH2PO4 с концентрацией от 0.01 до 0.1 моль/л, для химико-механического полирования кристаллов KH2PO4. Средняя шероховатость поверхности кристалла KH2PO4 снизилась с 4.6 до 1.5 нм после обработки микроэмульсией в системе Triton X-100–деканол–0.03 М водный раствор KH2PO4 [8].
Нами была показана возможность снижения шероховатости поверхности никеля с помощью обратной микроэмульсии на основе Д2ЭГФNa, содержащей внутри капель водный раствор соляной кислоты. Концентрация HCl, в пересчете на весь объем микроэмульсии, составляла 0.026 моль/л, процесс проводили в течение 2 ч. В тех же условиях обработка поверхности никеля водным раствором HCl с концентрацией 0.026 моль/л приводила к увеличению шероховатости [9]. Это можно объяснить тем, что коэффициенты диффузии вещества в молекулярном растворе на два порядка величин выше, чем для вещества, локализованного в каплях микроэмульсии. Доступ капель микроэмульсии к углублениям на поверхности металла будет затруднен вследствие диффузионных ограничений. Реагент, локализованный в каплях, будет лучше взаимодействовать с выступающими частями поверхности, что приведет к преимущественному растворению выступов и снижению средней шероховатости.
Целью данной работы являлось изучение химического полирования металла с помощью наноструктурированных сред (обратных микроэмульсий), на примере полирования алюминия. В качестве полирующей среды была выбрана хорошо изученная ранее [3, 10, 11] микроэмульсия на основе ди-(2-этилгексил)фосфата натрия, содержащая соляную, азотную или уксусную кислоты.
ЭКСПЕРИМЕНТАЛЬНАЯ ЧАСТЬ
Для получения микроэмульсии использовалась ди-(2-этилгексил)фосфорная кислота “Acros Organics” (содержание основного вещества не менее 95 мас. %) и гидроксид натрия квалификации “ч.”. В качестве органического растворителя был использован керосин марки “Осветительный” КО-25 (“Эксперт-Ойл”, Россия). В микроэмульсию вводили соляную, азотную и уксусную кислоты квалификации “ч.”. В ряде случаев в микроэмульсию вводили трибутилфосфат “Acros Organics” (содержание основного вещества не менее 99 мас. %). Дистиллированная вода была получена стандартным методом.
Микроэмульсию Д2ЭГФNa получали согласно описанной ранее методике [2, 3]. Водная фаза микроэмульсии представляла собой раствор гидроксида натрия в дистиллированной воде. Органическая фаза представляла собой раствор ди-(2-этилгексил)фосфорной кислоты, и, при необходимости, трибутилфосфата, в керосине. Для получения микроэмульсии смешивали необходимое количество водной и органической фазы. В процессе перемешивания происходила реакция нейтрализации между гидроксидом натрия и ди-(2-этилгексил)фосфорной кислотой с образованием поверхностно-активного вещества ди-(2-этилгексил)фосфата натрия, который стабилизировал капли микроэмульсии. При этом наблюдалось превращение мутной эмульсии в прозрачную гомогенную микроэмульсию. Далее в полученную микроэмульсию вводили необходимое количество концентрированной соляной или азотной или уксусной кислоты.
Гидродинамический диаметр капель микроэмульсии определяли методом динамического светорассеяния с помощью анализатора размера частиц Zetasizer Nano ZS (Malvern, Великобритания). Для удаления пыли образец подготавливается к измерению центрифугированием на центрифуге ОПН-8 (Россия) при 8000 об./мин (ускорение 150g) в течение 30 мин. Для получения статистически достоверного результата каждое измерение проводится не менее 5 раз.
Химическое полирование алюминиевой фольги (фольга для упаковки ГОСТ 745-2003) проводили по следующей методике. В бюкс на 50 мл помещали 30 мл микроэмульсии, потом погружали пластинку металла размером 20 × 20 мм в микроэмульсию таким образом, чтобы вся исследуемая поверхность была погружена в жидкость. Растворение металла проводили в закрытом сосуде при температуре 80°С и при механическом перемешивании (300 об./мин) в течение 1–3 ч. В некоторых экспериментах в дополнение к механическому перемешиванию применялось воздействие ультразвука. Ультразвук мощностью 10 Вт генерировался ультразвуковым диспергатором УЗГ 13-0.1/22. В ходе процесса полирования микроэмульсия оставалась стабильной, ее помутнения и расслаивания не наблюдалось. После полирования поверхность металла очищали от адсорбировавшихся поверхностно-активных веществ последовательным промыванием пластинки в гексане, этиловом спирте и воде. Результаты полирования сравнивали с контрольным образцом – пластинкой из алюминиевой фольги, последовательно промытой в гексане, этаноле и воде.
Поверхность образов анализировали методом атомно-силовой микроскопии (АСМ) на атомно-силовом микроскопе Ntegra Prima (NT-MDT, Россия, Зеленоград). Использовался кантилевер – кремневый с золотым покрытием NSG10 (NT-MDT, Россия). Режим работы – полуконтактный. Средняя шероховатость (Average Roughness, Sa) рассчитывалась для площадки 10 × 10 мкм согласно стандарту ISO 4287/1 с помощью программного обеспечения прибора.
РЕЗУЛЬТАТЫ И ИХ ОБСУЖДЕНИЕ
Ранее было показано снижение шероховатости поверхности никеля после взаимодействия с обратной микроэмульсией в системе Д2ЭГФNa– керосин–водный раствор HCl [8]. Поэтому для химического полирования алюминия была выбрана микроэмульсия ди-(2-этилгексил)фосфата натрия в керосине такого же состава, что и использованный ранее: СД2ЭГФNa = 1.22 моль/л; Своды = = 13.2 моль/л; СHCl = 0.026 моль/л. Это соответствует содержанию водной фазы в микроэмульсии, равному 22.5 об. %, и концентрации соляной кислоты в водной фазе, равной 0.11 моль/л. Гидродинамический диаметр капель такой микроэмульсии, определенный методом динамического светорассеяния, составил 13.3 ± 0.6 нм (рис. 1). Отметим, что при проведении процесса химического полирования никеля капельная структура обратной микроэмульсии сохранялась, наблюдалось только незначительное изменение гидродинамического диаметра капель: 13.3 ± 0.6 нм до полирования и 8.4 ± 0.7 нм после полирования в течение двух часов. Диаметр капель микроэмульсии того же состава, не содержащей соляной кислоты, равнялся 3.0 ± 0.1 нм. Такое изменение диаметра капель микроэмульсии в процессе химического полирования объясняется снижением концентрации соляной кислоты, которая расходуется на растворение металла.
Рис. 1.
Гидродинамический диаметр капель микроэмульсии, использованной для химического полирования. Состав микроэмульсии: СД2ЭГФNa = 1.22 моль/л; Своды = 13.2 моль/л; СHCl = 0.026 моль/л.
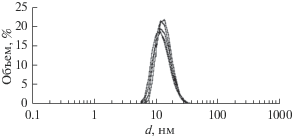
Поскольку поверхность алюминия покрыта оксидной пленкой, в процессе полирования алюминия могут протекать следующие химические реакции:
(1)
$2{\text{Al}} + 6{\text{HCl}} \to 2{\text{AlC}}{{{\text{l}}}_{3}} + 3{{{\text{H}}}_{2}}~{\kern 1pt} ,$(2)
${\text{A}}{{{\text{l}}}_{2}}{{{\text{O}}}_{3}} + 6{\text{HCl}} \to 2{\text{AlC}}{{{\text{l}}}_{3}} + 3{{{\text{H}}}_{2}}{\text{O}}.~$Было изучено влияние времени проведения процесса на снижение шероховатости. Результаты исследования методом АСМ поверхности образцов алюминиевой фольги до полирования (контроль) и после 1, 2 и 3 ч проведения процесса показаны на рис. 2. Значения средней шероховатости в зависимости от времени химического полирования микроэмульсией приведены в табл. 1. Как видно из представленных данных, средняя шероховатость поверхности алюминиевой фольги снижается в течение первых двух часов полирования, а затем незначительно возрастает. Поэтому для дальнейших экспериментов было выбрано время проведения процесса полирования, равное двум часам.
Рис. 2.
Рельеф поверхности алюминия до и после химического полирования микроэмульсией, содержащей соляную кислоту: (а) – контроль; (б) – 1 час; (в) – 2 часа; (г) – 3 часа. Состав микроэмульсии: СД2ЭГФNa = 1.22 моль/л; Своды = = 13.2 моль/л; СHCl = 0.026 моль/л.
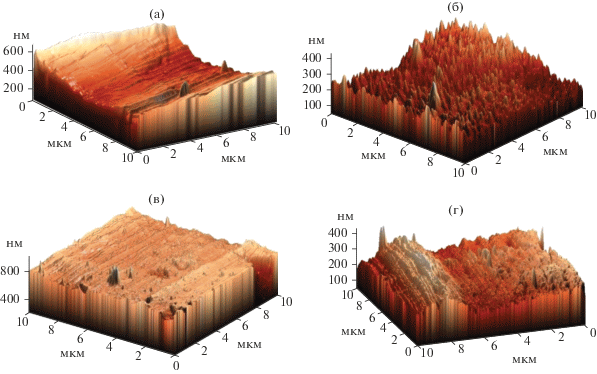
Таблица 1.
Средняя шероховатость поверхности образцов, по данным АСМ, до и после химического полирования микроэмульсией, содержащей HCl
Время проведения процесса, ч | 0 (контроль) | 1 | 2 | 3 |
---|---|---|---|---|
Средняя шероховатость, нм | 54 | 35 | 28 | 32 |
Для химического полирования смесями концентрированных кислот время проведения процесса составляет минуты и даже доли минут. Такое малое время полирования вызывает ряд технологических затруднений, связанных с необходимостью быстрой отмывки изделий от полирующего раствора [5]. При использовании микроэмульсий длительность химического полирования составляет часы. С одной стороны, такой медленный процесс легче контролировать. С другой стороны, 2 ч – это очень долго с точки зрения создания эффективной технологии. Поэтому необходимо разработать меры по ускорению химического полирования с помощью микроэмульсий.
Процесс взаимодействия оксида меди с экстрагент-содержащей микроэмульсией Д2ЭГФNa (микроэмульсионного выщелачивания) протекает в смешанном режиме, то есть контролируется и диффузией и химической реакцией [12]. Можно предположить, что и скорость процесса химического полирования с помощью микроэмульсии будет контролироваться диффузией и химической реакцией. В этом случае повышения скорости можно добиться следующими способами:
– путем повышения температуры,
– путем дополнительной активации с помощью ультразвука,
– путем повышения концентрации растворяющего металл реагента (кислоты),
– путем облегчения диффузии кислоты из капли водной фазы к поверхности металла через слой органической фазы.
В данной работе процесс химического полирования уже ведется при 80°С. Дальнейшее повышение температуры нежелательно из-за возможного интенсивного испарения растворителя (керосина) и ограниченной области существования микроэмульсий. Значительное повышение концентрации кислоты в микроэмульсии затруднительно вследствие невысокой солюбилизационной емкости исследованной микроэмульсии по отношению к кислотам. Поэтому была изучена возможность проведения процесса полирования при воздействии ультразвука и в условиях облегчения диффузии кислоты через слой органической фазы за счет добавления трибутилфосфата.
Было исследовано влияние ультразвукового перемешивания полирующей среды (микроэмульсии) на результаты химического полирования. Состав микроэмульсии был такой же, как и в предыдущем эксперименте: СД2ЭГФNa = 1.22 моль/л; Своды = = 13.2 моль/л; СHCl = 0.026 моль/л; время проведения процесса составляло 2 ч. В табл. 2 приведены значения средней шероховатости поверхности образцов после химического полирования в отсутствие перемешивания микроэмульсии, при ее механическом перемешивании и при действии механического перемешивания и ультразвука.
Таблица 2.
Средняя шероховатость поверхности образцов, по данным АСМ, после химического полирования микроэмульсией, содержащей HCl, при различных режимах перемешивания
Режим перемешивания микроэмульсии | Средняя шероховатость, нм |
---|---|
Без перемешивания | 49 |
Механическое перемешивание | 28 |
Механическое перемешивание и действие ультразвука | 25 |
Контроль (до полирования) | 54 |
Как видно из представленных в табл. 2 данных, при отсутствии перемешивания наблюдается существенно меньшее снижение шероховатости, чем при механическом перемешивании. Сочетание ультразвукового и механического перемешивания незначительно влияет на результат химического полирования. При ультразвуковом воздействии в ходе полирования микроэмульсия оставалась стабильной, ее помутнения и разрушения на отдельные фазы не наблюдалось. Это дает возможность комбинировать механическое и ультразвуковое перемешивание при полировании с помощью микроэмульсии. Для более точного понимания роли ультразвукового воздействия при химическом полировании металла с помощью микроэмульсии потребуются более детальные исследования кинетики процесса.
Другой подход к ускорению химического полирования с помощью микроэмульсии связан с облегчением диффузии реагента от капли к поверхности металла через слой органической фазы. Трибутилфосфат (ТБФ) – известный промышленный экстрагент, он экстрагирует неорганические кислоты из водных растворов в органическую фазу за счет образования аддуктов [13]. Поэтому трибутилфосфат может облегчить перенос молекул HCl из водной капли через слой органической фазы к поверхности металла. Кроме того, введение ТБФ в состав микроэмульсии дает возможность увеличить количество кислоты, которое можно солюбилизировать в микроэмульсии. Это позволит применять для химического полирования микроэмульсии с более высокой концентрацией кислоты. Например, при одинаковом содержании воды, максимальная концентрация уксусной кислоты в микроэмульсии Д2ЭГФNa, не содержащей ТБФ, составляла 0.25 моль/л; в присутствии 0.45 моль/л ТБФ максимальная концентрация CH3COOH возрастала до 0.51 моль/л. В табл. 3 представлены данные по солюбилизации кислот в микроэмульсии Д2ЭГФNa, содержащей 0.15 моль/л ТБФ.
Таблица 3.
Солюбилизация кислот в микроэмульсии. Состав микроэмульсии: СД2ЭГФNa = 1.22 моль/л, СТБФ = = 0.15 моль/л, Своды = 13.2 моль/л. Т = 20°С
Кислота | Азотная | Соляная | Серная | Уксусная |
---|---|---|---|---|
Максимальная концентрация кислоты в микроэмульсии, моль/л | 0.073 | 0.091 | 0.035 | 0.310 |
Было изучено влияние введения ТБФ в микроэмульсию на процесс полирования поверхности алюминия. Использовалась микроэмульсия следующего состава: СД2ЭГФNa = 1.22 моль/л; Своды = 13.2 моль/л; СHCl = 0.026 моль/л; СТБФ = 0.15 моль/л. Время проведения полирования составило 1 и 2 ч. Значения средней шероховатости поверхности образцов приведены в табл. 4.
Таблица 4.
Средняя шероховатость поверхности образцов, по данным АСМ, после химического полирования микроэмульсией, содержащей ТБФ и HCl
Время проведения процесса, ч | 0 (контроль) | 1 | 2 |
---|---|---|---|
Средняя шероховатость, нм | 54 | 47 | 29 |
Как видно из данных, представленных в табл. 1 и 4, введение ТБФ практически не влияет на химическое полирование алюминиевой фольги микроэмульсией Д2ЭГФNa, содержащей соляную кислоту. В дальнейших экспериментах была использована микроэмульсия, содержащая ТБФ и различные кислоты.
Было исследовано влияние природы кислоты на химическое полирование поверхности алюминия микроэмульсией. Концентрация кислот в микроэмульсии составляла 0.026 моль/л, что существенно ниже, чем их максимальное содержание (табл. 3), концентрации других компонентов: СД2ЭГФNa = 1.22 моль/л; Своды = 13.2 моль/л; СТБФ = 0.15 моль/л; время проведения процесса – 2 ч. Результаты исследования поверхности образцов методом АСМ приведены на рис. 3, значения средней шероховатости – в табл. 5.
Рис. 3.
Рельеф поверхности алюминия после химического полирования микроэмульсией, содержащей ТБФ и кислоты: (а) – соляную кислоту; (б) – уксусную кислоту; (в) – азотную кислоту. Состав микроэмульсии: СД2ЭГФNa = 1.22 моль/л; Своды = 13.2 моль/л; СТБФ = 0.15 моль/л. Концентрация кислот в микроэмульсии равна 0.026 моль/л. Время полирования – 2 часа.
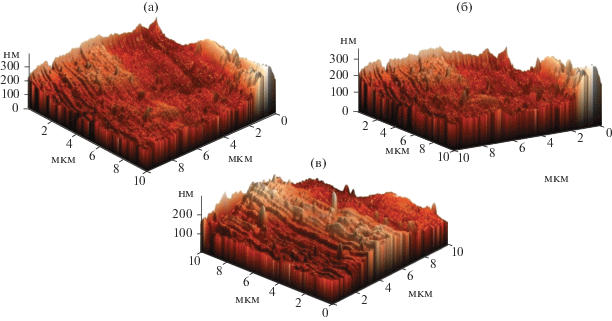
Таблица 5.
Средняя шероховатость поверхности образцов, по данным АСМ, после химического полирования микроэмульсией, содержащей ТБФ и различные кислоты
Кислота | Соляная | Уксусная | Азотная |
---|---|---|---|
Средняя шероховатость, нм | 29 | 29 | 30 |
Из представленных данных (рис. 3, табл. 5) видно, что все исследованные микроэмульсии снижают шероховатость образцов примерно в равной степени. Поэтому все три использованные кислоты могут входить в состав микроэмульсий для химического полирования металлов. При этом наибольшее содержание в микроэмульсии (наибольшая солюбилизационная емкость) наблюдается для уксусной кислоты (табл. 3). Увеличение концентрации кислоты в микроэмульсии позволит повысить скорость процесса химического полирования. Возможно, уксусная кислота является наиболее перспективной для дальнейшей разработки процессов химического полирования металлов с помощью обратных микроэмульсий.
Для того чтобы показать, что именно наноструктурированная среда (микроэмульсия) обеспечивает условия для химического полирования, был проведен эксперимент по полированию поверхности алюминия следующими смесями реагентов.
1. Водная дисперсия Д2ЭГФNa, содержащая соляную кислоту. Состав дисперсии: СД2ЭГФNa = = 0.0013 моль/л; СHCl = 0.026 моль/л.
2. Раствор ТБФ в керосине, содержащий соляную кислоту. Состав раствора: СТБФ = 0.15 моль/л; СHCl = 0.026 моль/л.
3. Водный раствор соляной кислоты СHCl = = 0.026 моль/л.
Результаты сравнивались с образцом, не подвергшимся полированию (контроль) и образцом, обработанным микроэмульсией, содержащей ТБФ и соляную кислоту. Состав микроэмульсии: СД2ЭГФNa = 1.22 моль/л; Своды = 13.2 моль/л; СHCl = = 0.026 моль/л; СТБФ = 0.15 моль/л. Рельеф поверхности алюминия и значения средней шероховатости образцов приведены на рис. 4 и в табл. 6.
Рис. 4.
Рельеф поверхности алюминия после обработки смесями реагентов: (а) – контроль (до обработки); (б) – водной дисперсией Д2ЭГФNa, содержащей HCl (СД2ЭГФNa = 0.0013 моль/л; СHCl = 0.026 моль/л); (в) – раствором ТБФ в керосине, содержащем HCl (СТБФ = 0.15 моль/л; СHCl = 0.026 моль/л); (г) – микроэмульсией (СД2ЭГФNa = 1.22 моль/л; Своды = 13.2 моль/л; СHCl = 0.026 моль/л; СТБФ = 0.15 моль/л); (д) – водным раствором HCl (СHCl = 0.026 моль/л). Время обработки – 2 часа.
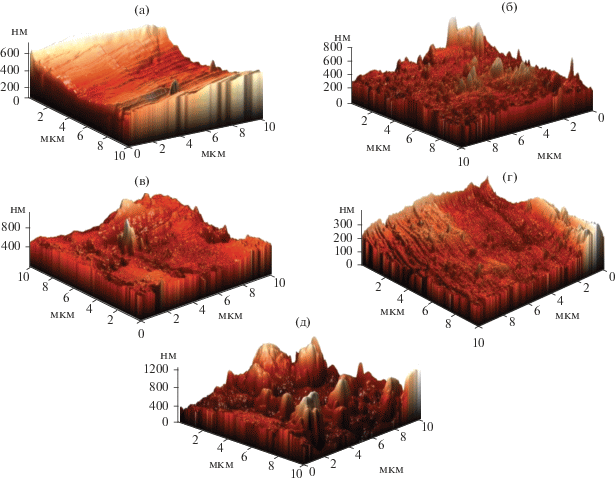
Таблица 6.
Средняя шероховатость поверхности образцов, по данным АСМ, после обработки смесями реагентов
Состав смеси реагентов | Средняя шероховатость, нм |
---|---|
Контроль (до обработки) | 54 |
Микроэмульсия Д2ЭГФNa, содержащая HCl и ТБФ | 29 |
Водная дисперсия Д2ЭГФNa, содержащая HCl | 56 |
Раствор ТБФ в керосине, содержащий HCl | 74 |
Водный раствор HCl | 60 |
Как видно из представленных на рис. 4 и в табл. 6 данных, и ни одно из сочетаний используемых компонентов, не образующее микроэмульсию, не приводит к существенному снижению шероховатости поверхности металла. Обработка поверхности алюминия водной дисперсией Д2ЭГФNa, содержащей HCl, вызывает незначительное изменение средней шероховатости по сравнению с контролем, на поверхности заметны неровности в виде пиков (рис. 4б). При обработке металла раствором ТБФ в керосине, содержащем HCl, и водным раствором HCl наблюдается увеличение шероховатости (растравливание) поверхности алюминия (рис. 4в и 4д). Только действие наноструктурированной среды (микроэмульсии) приводит к сглаживанию поверхности алюминия (рис. 4г).
Таким образом, показана возможность химического полирования металла с помощью обратной микроэмульсии, содержащей кислоту. Механизм полирования, вероятно, заключается в ограничении диффузии кислоты к углублениям на поверхности металла и преимущественному растворению выступов за счет локализации реагента в каплях с размером порядка 10 нм.
ЗАКЛЮЧЕНИЕ
Было исследовано химическое полирование металла с помощью наноструктурированных сред – обратных микроэмульсий. Показана возможность снижения шероховатости поверхности алюминиевой фольги при ее обработке микроэмульсией Д2ЭГФNa, содержащей соляную кислоту. При времени полирования 2 ч средняя шероховатость поверхности снижалась с 54 до 28 нм. Дополнительное воздействие ультразвука при таком же времени проведения процесса незначительно влияет на результат полирования. Введение ТБФ в микроэмульсию практически не влияет на химическое полирование алюминиевой фольги микроэмульсией, содержащей кислоту. Замена соляной кислоты в составе микроэмульсии на уксусную или азотную не оказывает влияния на результат химического полирования.
Показано, что использование наноструктурированной среды (микроэмульсии) для химического полирования позволяет существенно снизить шероховатость поверхности алюминиевой фольги. Составы, не образующие микроэмульсии (водный раствор соляной кислоты, аддукта трибутилфосфата с соляной кислотой в керосине, дисперсия Д2ЭГФNa в водном растворе соляной кислоты), не обладают таким действием.
Полученные результаты могут стать основой для дальнейшей разработки новых методов химического полирования металлов.
Список литературы
Fanum M. (Ed.). Microemulsions: Properties and Applications. Boca Raton, London, New York: CRC Press, Taylor & Francis Group, 2009. 560 c.
Yurtov E.V., Murashova N.M. // Theoretical Foundations of Chemical Engineering. 2011. V. 45. № 5. P. 726. https://doi.org/10.1134/S0040579511050174
Murashova N.M., Levchishin S.Yu., Yurtov E.V. // J. Surfactants and Detergents. 2014. V. 17. № 6. P. 1249. https://doi.org/10.1007/s11743-014-1598-x
Murashova N.M., Levchishin S.Yu., Yurtov E.V. // Hydrometallurgy. 2018. V. 175. P. 278. https://doi.org/10.1016/j.hydromet.2017.12.012
Грилихес С.Я. Электрохимическое и химическое полирование: теория и практика. Влияние на свойства металлов. 2-е изд., перераб. и доп. Л.: Машиностроение. Ленингр. отд-ние, 1987. 232 с.
Догадкина Е.В., Донцов М.Г., Парфенюк В.И. // Физикохимия поверхности и защита материалов. 2016. Т. 32. № 5. С. 554. https://doi.org/10.7868/S0044185616040082
Huang Y.-J., Yates M.Z. // Colloid and Surfaces A: Physicochemical and Engineering Aspects. 2006. № 281. P. 215. https://doi.org/10.1016/j.colsurfa.2006.02.041
Dong H., Wang L., Gao W. et al. // Materials. 2017. V. 271. № 10. P. 1. https://doi.org/10.3390/ma10030271
Левчишин С.Ю., Краснова О.Г., Субчева Е.Н. и др. // Успехи в химии и химической технологии. 2014. Т. 28. № 6. С. 58.
Юртов Е.В., Мурашова Н.М. // Коллоидный журн. 2004. Т. 66. № 5. С. 702. https://doi.org/10.1023/B:COLL.0000043847.13437.5e
Мурашова Н.М., Левчишин С.Ю., Юртов Е.В. // Химическая технология. 2011. Т. 12. № 7. С. 405.
Мурашова Н.М., Левчишин С.Ю., Юртов Е.В. // Химическая технология. 2012. Т. 13. № 1. С. 19.
Rydberg J., Cox M., Musikas C., Choppin G.R. (Eds.). Solvent Extraction Principles and Practice. New York, Basel: Marcel Dekker, Inc., 2004. 480 c.
Дополнительные материалы отсутствуют.
Инструменты
Физикохимия поверхности и защита материалов