Физикохимия поверхности и защита материалов, 2020, T. 56, № 3, стр. 301-308
Электроосаждение цинк-никелевых покрытий из глицин-содержащего аммиачно-хлоридного электролита
Д. В. Бурляев 1, А. Е. Тинаева 1, К. Е. Тинаева 1, О. А. Козадеров 1, *
1 Воронежский государственный университет
394018 Воронеж, Университетская пл., 1, Россия
* E-mail: ok@chem.vsu.ru
Поступила в редакцию 02.05.2019
После доработки 10.10.2019
Принята к публикации 17.10.2019
Аннотация
Изучены кинетические закономерности процесса электроосаждения сплавных цинк-никелевых покрытий из аммиачно-хлоридного раствора электролита. Установлено влияние добавки аминоуксусной кислоты на механизм процесса электроосаждения, выход по току, морфологию поверхности, химический и фазовый состав синтезируемых покрытий. Процесс электрохимического осаждения сплавов системы Zn–Ni из аммиачно-хлоридного электролита осложнен диффузионным транспортом ионов в жидкой фазе раствора электролита, при этом кинетическая стадия переноса заряда протекает необратимо. Добавка аминоуксусной кислоты не меняет механизма процесса электроосаждения, однако приблизительно на 6% увеличивает выход по току целевого процесса, предположительно, за счет снижения вклада реакции выделения водорода в общую скорость катодного процесса. Добавка глицина улучшает морфологию поверхности синтезируемых покрытий за счет снижения шероховатости и более плотной упаковки зародышей растущей фазы, а также увеличивает содержание никеля в сплаве в среднем на 4 ат. %, но не влияет на фазовый состав покрытий, которые остаются гетерогенными и состоят из γ-фазы Ni2Zn11 и Zn. Проведена количественная оценка противокоррозионной эффективности электроосажденных цинк-никелевых сплавов в зависимости от наличия аминоуксусной кислоты в растворе электролита. Обнаружено, что введение глицина в аммиачно-хлоридный электролит осаждения приводит к облагораживанию коррозионного потенциала и заметному снижению плотности тока коррозии Zn, Ni-сплавного покрытия в водном растворе 3.5% NaCl. Это свидетельствует о повышении устойчивости электрохимически синтезируемого защитного пленочного материала к коррозионному разрушению. Подобраны оптимальные условия электрохимического синтеза морфологически однородных противокоррозионных цинк-никелевых покрытий.
ВВЕДЕНИЕ
При разработке современных материалов и технологий одним из перспективных направлений являются работы в области электроосаждения сплавов как метода получения покрытий с защитными и специальными свойствами. Особое внимание уделяется электрохимическому синтезу пленочных материалов, построенных на основе цинка. Возрастание требований к функциональным свойствам цинковых покрытий вызвало необходимость разработки процессов получения гальванических систем, в основу которых положены сплавы цинка. На практике они особенно эффективны для защиты от коррозии материалов, подвергающихся агрессивному разрушительному воздействию окружающей среды, например, днищ кораблей, аппаратуры и сооружений, работающих в морских условиях солевого тумана. Так, в связи с разработкой ряда новых нефтяных месторождений актуальной становится использование Zn-содержащих материалов для защиты нефтепромыслового оборудования от солевой коррозии [1].
Перспективной является модификация цинкового покрытия с целью увеличения коррозионной и термической стойкости, механической прочности покрытия при уменьшении его толщины. Повышение коррозионной стойкости покрытий на основе цинка с одновременным сохранением его электроотрицательности по отношению к защищаемому материалу (в основном, стали) может быть достигнуто легированием цинка на катоде металлами, образующими с Zn интерметаллические соединения [2]. Это позволяет полностью исключить нежелательное по экологическим причинам применение покрытий на основе токсичного кадмия [3].
Действительно, сплавы системы “цинк–никель” постепенно вытесняют Cd-содержащие системы, используемые в промышленности для защиты металлических материалов от коррозионного разрушения. При этом гомогенный сплав с атомной долей никеля 12–15 ат. %, представляющий γ-фазу состава Ni2Zn11, характеризуется наилучшими противокоррозионными свойствами среди сплавов данной группы, существенно превосходящими покрытия из чистого цинка [4–6]. Более того, большинство функциональных свойств гальванических покрытий определяется структурой, фазовым и химическим составом сплава, наличием инородных включений. Как правило, оптимальными свойствами обладают твердые растворы и интерметаллические фазы, например, пирометаллургические сплавы Zn–Ni (γ-фаза) при содержании 14–20 мас. % Ni. Однако в случае гальванических осадков Zn–Ni, полученных из различных электролитов, одинаковому химическому составу сплава может отвечать различный фазовый состав [1, 6]. Тем не менее, коррозионно-стойкие интерметаллиды на основе никеля (например, Ni5Zn21 (γ-фаза)) обнаруживаются и в электроосажденных сплавах [1, 3, 5]. При этом гальванопокрытия часто превосходят литые сплавы по чистоте осадка, равномерности, мелкокристалличности и ряду других функциональных свойств [1, 6]. Помимо механической и коррозионной защиты гальванопокрытия на основе цинк-никелевых сплавов могут быть использованы как исходные системы для получения пористого (в том числе и нанопористого) никеля путем селективного растворения цинка. Синтезируемый таким образом материал характеризуется большой площадью электрохимически активной поверхности, а потому является перспективным электрокатализатором, например, в реакциях анодного окислении метанола в твердополимерных топливных элементах, получения водорода, гидрирования органических соединений [7, 8]. В этой связи актуальными задачами являются электрохимическое получение цинк-никелевых покрытий, содержащих гомогенные интерметаллические фазы, изучение закономерностей их синтеза, а также оценка коррозионной устойчивости.
Основным методом получения цинк-никелевых сплавных покрытий является катодное электроосаждение [9–11], кинетические закономерности которого, а также свойства синтезируемого материала зависят от наличия в электролите осаждения органических добавок, выступающих в качестве комплексообразователей [12–16]. В качестве такой добавки в настоящей работе используется аминоуксусная кислота (глицин), роль которой в кинетике электроосаждения сплавов системы Zn–Ni, их составе, морфологии и устойчивости к коррозии впервые изучается на основе комплексного подхода.
Цель работы – установление влияния добавки глицина на кинетические закономерности процесса электроосаждения цинк-никелевых сплавных покрытий из аммиачно-хлоридного электролита, состав пленочных сплавов, морфологию поверхности, выход по току целевого процесса, а также оценка противокоррозионной эффективности синтезированных покрытий.
ЭКСПЕРИМЕНТАЛЬНАЯ ЧАСТЬ
Цинк-никелевые покрытия осаждали в потенциостатических или потенциодинамических условиях поляризации на медную или золотую подложку из аммиачно-хлоридного раствора без добавок состава 0.15 M ZnCl2 + 0.30 M NiCl2 + 3.00 M NH4Cl (рН 3.6), а также из раствора электролита с добавкой глицина состава 0.15 M ZnCl2 + 0.30 M NiCl2 + + 3.00 M NH4Cl + 0.30 М NH2CH2COOH (рН 3.2) в условиях естественной аэрации. Для проведения коррозионных испытаний синтезированных цинк-никелевых покрытий использовали 3.5% водный аэрированный раствор NaCl (рН 7.4). Растворы приготовлены на дважды дистиллированной воде (бидистиллятор УПВА-5) из ч. д. а. и х. ч. реактивов. Электрохимические измерения проводили при комнатной температуре 293 ± 2°С в трехэлектродной ячейке без разделения катодного и анодного пространств. Потенциодинамический и потенциостатический режимы электролиза реализованы при помощи компьютеризированного потенциостата/гальваностата IPC-Pro L. Рабочим электродом служила медная пластина (геометрическая площадь Sgeom = 1 см2) или золотой электрод (Sgeom = 0.14 см2) – в экспериментах по электроосаждению, а также цинковый электрод (Sgeom = 0.17 см2) – в коррозионных испытаниях. Подготовка электродов включала зачистку на шлифовальной бумаге, полировку до зеркального блеска на замше с водной суспензией MgO, обезжиривание этанолом, промывание бидистиллированной водой и сушку в токе аргона. Вспомогательный электрод – платиновая пластина, электрод сравнения – хлоридсеребряный электрод. Потенциалы Е в работе приведены по шкале стандартного водородного электрода (ст. в. э.). Плотность тока i рассчитана на единицу геометрической площади электродов.
Морфологию поверхности синтезируемых покрытий исследовали методами металлографической и растровой электронной микроскопии (РЭМ) (микроскопы Altami MET 1T и JSM-6380LV соответственно). Для определения химического состава покрытий использовали метод рентгеноспектрального микроанализа (РСМА) (система микроанализа INCA 250), фазового – метод рентгеновской дифракции (дифрактометр ARL X’TRA Thermo Scientific).
Результаты РЭМ-, РСМА- и дифрактометрических исследований получены на оборудовании ЦКПНО ВГУ.
Циклические вольтамперограммы регистрировали, сканируя потенциал со скоростью V от бестокового стационарного значения вначале в катодную область до Е = –1200 мВ, затем в обратном направлении до +400 мВ. Параметр V варьировали от 5 до 200 мВ/с. Электроосаждение цинк-никелевых покрытий толщиной ~5 мкм осуществляли в потенциостатическом режиме поляризации в интервале катодных потенциалов от –860 до –1000 мВ. Выход по току определяли гравиметрическим методом.
Измерение транзиента коррозионного потенциала и снятие поляризационных кривых с дальнейшим определением потенциала и тока коррозии методом экстраполяции Тафеля являются одними из основных способов оценки противокоррозионной эффективности материалов [17–19]. Коррозионные испытания проводили, погружая образец покрытия в ячейку, заполненную 3.5% водным раствором NaCl и регистрируя изменение стационарного потенциала Ecorr во времени в течение не менее двух часов. После установления постоянного значения Ecorr регистрировали вольтамперограммы, сканируя потенциал электрода со скоростью 5 мВ/с в интервале от Е = Ecorr – 400 мВ до Е = Ecorr + 400 мВ, и перестраивали их в Тафелевых lgi – E координатах.
РЕЗУЛЬТАТЫ И ИХ ОБСУЖДЕНИЕ
Анализ катодных ветвей циклических вольтамперограмм, полученных на Au-электроде в аммиачно-хлоридных растворах при V = const, позволяет сделать вывод, что добавление глицина в электролит приводит к незначительному облагораживанию потенциалов катодного осаждения (рис. 1). В свою очередь, анодные максимумы А1–А3, соответствующие инверсионному растворению покрытий, полученных при катодном сканировании в растворах без добавки и с добавкой аминоуксусной кислоты, также несколько смещены друг относительно друга, что свидетельствует о возможном различии в химическом и/или фазовом составе продуктов осаждения. При этом согласно литературным данным [20–23] анодные пики А1 и А2 относятся к селективному растворению цинка из цинк-никелевых фаз различного состава (α-, γ-, η-фазы), в то время как пик А3 – к растворению никеля из обесцинкованного покрытия.
Рис. 1.
Циклические вольтамперограммы, полученные в аммиачно-хлоридных электролитах с добавкой глицина, без добавки глицина. Подложка – Au, скорость развертки потенциала 10 мВ/с, сканирование потенциала от бестокового значения E ≈ 400 мВ (ст. в. э.) в катодную область, затем в анодную.

С ростом скорости сканирования потенциала высота максимума imax на катодной ветви циклограммы увеличивается, причем imax, V-зависимость линеаризуется в координатах Рендлса–Шевчика (рис. 2а). Увеличение V приводит к сдвигу потенциала максимума в положительную сторону (рис. 2б). Согласно теории линейной вольтамперометрии [24–26], это свидетельствует о том, что процесс осложнен объемно-диффузионным транспортом разряжающихся ионов к поверхности электрода, а кинетическая стадия переноса заряда является необратимой. Таким образом, электроосаждение протекает в смешанно-кинетическом диффузионно-электрохимическом режиме.
Рис. 2.
(а) Зависимость потенциала максимума пика катодного осаждения от десятичного логарифма скорости развертки потенциала; (б) зависимость плотности тока максимума пика катодного осаждения от квадратного корня из скорости сканирования потенциала.
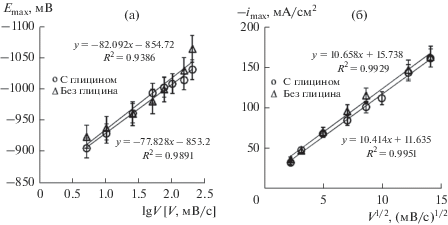
Данный вывод справедлив для обоих типов растворов независимо от наличия глицина, т.е. добавка аминоуксусной кислоты на механизм процесса электроосаждения цинк-никелевых сплавов из аммиачно-хлоридного электролита не влияет. В то же время отрезки, отсекаемые прямыми в координатах Рендлса–Шевчика (рис. 2a) на оси ординат, имеют различную величину для разных растворов (~16 мА/см2 для случая без добавки глицина и ~11 мА/см2 для случая с добавкой глицина). Поскольку данные отрезки, вероятно, характеризуют скорость побочных процессов, протекающих на катоде параллельно с электроосаждением (прежде всего, это выделение водорода), то справедливо отметить, что добавка глицина снижает их вклад в общую скорость приблизительно в полтора раза.
По данным РСМА независимо от потенциала осаждения Еdep и наличия глицина в растворе электролита осаждения сплавные Zn, Ni-покрытия построены на основе цинка (табл. 1). Добавка аминоуксусной кислоты увеличивает содержание никеля в сплаве в среднем приблизительно на 4 ат. %. При этом, однако, не изменяется качественный фазовый состав покрытий (рис. 3), которые являются гетерогенными, поскольку состоят из металлического цинка и γ-фазы системы Zn–Ni, включающей преимущественно интерметаллид Ni2Zn11.
Таблица 1.
Химический состав цинк-никелевых покрытий и выход по току процесса их электроосаждения из аммиачно-хлоридного раствора, не содержащего (числитель) и содержащего (знаменатель) добавку глицина
Edep, мВ | Атомная доля никеля, % | Выход по току, % |
---|---|---|
–860 | $\frac{{9.2 \pm 0.5}}{{14.1 \pm 0.5}}$ | $\frac{{89}}{{94}}$ |
–900 | $\frac{{9.2 \pm 0.5}}{{12.7 \pm 0.5}}$ | $\frac{{86}}{{94}}$ |
–1000 | $\frac{{11.0 \pm 0.5}}{{15.3 \pm 0.5}}$ | $\frac{{86}}{{92}}$ |
Рис. 3.
Рентгеновские дифрактограммы Zn, Ni-покрытий, полученных электроосаждением на медную подложку из аммиачно-хлоридных растворов без глицина (пунктир) и с глицином (сплошная линия) при потенциале осаждения Еdep = –880 мВ.
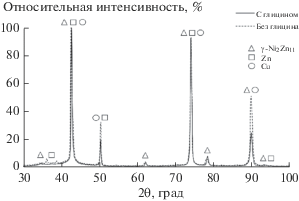
Анализ данных растровой электронной микроскопии (рис. 4) показывает, что покрытия, синтезированные из глицинсодержащего раствора электролита, являются более гладкими за счет снижения общей шероховатости и уменьшения размеров зародышей растущей фазы. Кроме того, они характеризуются отсутствием крупных трещин на поверхности, характерных для покрытий, полученных из раствора без добавки аминоуксусной кислоты. Учитывая, что более равномерные и мелкозернистые покрытия получаются при относительно более низкой скорости осаждения сплава [17], можно прийти к выводу, что наблюдаемый эффект обусловлен, скорее всего, снижением плотности тока катодного осаждения при добавлении глицина.
Рис. 4.
РЭМ-фотографии поверхностей и составы Zn, Ni-сплавов, полученных электроосаждением из аммиачно-хлоридного электролита без добавки (а) и с добавкой глицина (б) при разных потенциалах осаждения.
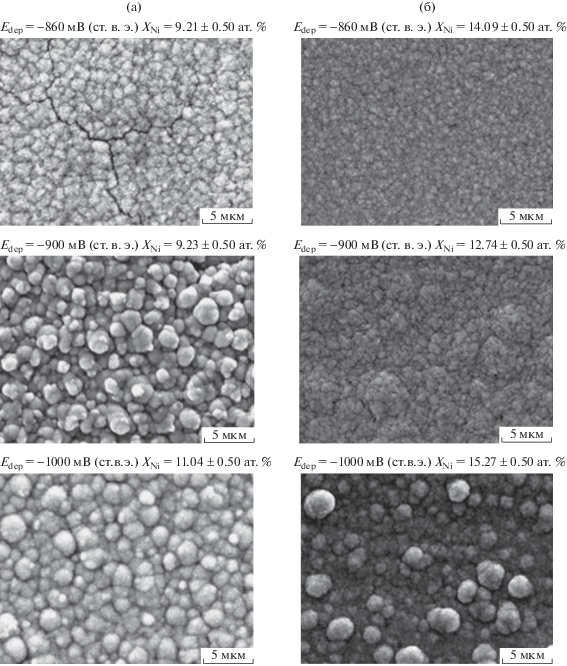
Следует отметить не только улучшение морфологии поверхности покрытия в случае использования добавки NH2CH2COOH, но и отсутствие неровностей, возникающих при выделении газообразного водорода в процессе электроосаждения. Это можно объяснить упомянутым выше уменьшением вклада побочных реакций в общую скорость катодного процесса при введении добавки аминоуксусной кислоты в раствор электролита. Это подтверждает и расчет выхода по току целевого процесса, который почти не зависит от потенциала осаждения Еdep, однако увеличивается приблизительно на 6% при добавлении глицина (табл. 1).
Для оценки противокоррозионной эффективности синтезированных цинк-никелевых покрытий получены зависимости стационарного потенциала Еcorr от времени в 3.5% водном растворе NaCl (рис. 5). Видно, что во всех случаях коррозионный потенциал цинк-никелевых покрытий, устанавливающийся в хлоридной среде, находится в более положительной области по сравнению с коррозионным потенциалом чистого цинка, т.е. происходит облагораживание потенциала свободной коррозии. При этом самым положительным значением коррозионного потенциала, независимо от наличия добавки глицина в электролите осаждения, характеризуются покрытия, синтезированные при потенциале осаждения –1000 мВ, что связано, вероятно, с большим содержанием никеля в таких покрытиях. Во всех случаях Еcorr цинк-никелевых покрытий в хлоридной среде смещается в положительную область и затем стабилизируется. Такое облагораживание коррозионного потенциала, согласно литературным данным [17, 18], может свидетельствовать о частичном обесцинковании поверхности покрытий в ходе коррозионного процесса, что приводит к некоторому обогащению поверхностного слоя более электроположительным компонентом сплава – никелем.
Рис. 5.
Транзиенты коррозионного потенциала, снятые при погружении Zn, Ni-сплавного покрытия (потенциалы осаждения приведены на рисунке) и чистого цинка в 3.5% водный раствор NaCl. Электролит осаждения не содержал (а) и содержал (б) добавку аминоуксусной кислоты.

Рассмотрим поляризационные кривые в Тафелевых координатах, снятые на исследуемых Zn, Ni-покрытиях и на цинке в 3.5% растворе NaCl (рис. 6). Видно, что для покрытий, полученных из глицинсодержащего электролита, характерно смещение коррозионного потенциала в катодную сторону при сдвиге потенциала осаждения в отрицательную область, в то время как для покрытий, синтезированных из электролита без добавки глицина, подобной закономерности не наблюдается.
Рис. 6.
Поляризационные кривые в Тафелевых координатах, полученные в 3.5% NaCl на цинке и цинк-никелевых покрытиях, осажденных при разных потенциалах из аммиачно-хлоридного электролита, не содержащего добавки глицина (а), содержащего добавку глицина (б).

По данным, представленным на рис. 6, методом экстраполяции Тафеля рассчитывали коррозионные потенциалы Ecorr и плотности токов коррозии icorr для всех исследуемых Zn, Ni-покрытий и для цинка с целью оценки их противокоррозионной эффективности (табл. 2). Следует отметить, что во всех случаях Zn, Ni-сплавные покрытия характеризуются существенно меньшими значениями токов коррозии по сравнению с цинком, что согласуется с данными [4–6, 27–33]. При этом покрытия, осажденные из глицинсодержащего электролита, также характеризуются более низкими токами коррозии по сравнению с аналогичными покрытиями, полученными из электролита, не содержащего глицин, при тех же потенциалах осаждения. Кроме того, наблюдается облагораживание коррозионного потенциала, что может быть связано как с улучшением морфологии поверхности покрытий, так и с увеличением содержания никеля в сплавах в связи с добавкой аминоуксусной кислоты.
Таблица 2.
Потенциалы и токи коррозии Zn/Zn, Ni-сплавных покрытий, рассчитанные методом экстраполяции Тафеля. Раствор – 3.5% NaCl. Символ “g” в столбце “потенциал осаждения” означает, что покрытие получено осаждением из глицинсодержащего электролита
Потенциал осаждения, мВ | Состав покрытия | Ecorr, мВ | icorr, μА/см2 | |
---|---|---|---|---|
XZn, % | XNi, % | |||
– | 99.99 | – | –1052 | 13.57 |
–860 | 90.79 | 9.21 | –961 | 3.98 |
–860 (g) | 85.91 | 14.09 | –950 | 2.51 |
–880 | 90.80 | 9.20 | –996 | 6.31 |
–880 (g) | 86.94 | 13.06 | –806 | 1.58 |
–900 | 90.77 | 9.23 | –949 | 2.11 |
–900 (g) | 87.26 | 12.74 | –738 | 0.92 |
–1000 | 88.96 | 11.04 | –998 | 6.60 |
–1000 (g) | 84.73 | 15.27 | –714 | 0.50 |
Для Zn, Ni-покрытий, синтезированных из глицинсодержащего аммиачно-хлоридного электролита, наблюдается следующая тенденция: смещение потенциала электроосаждения покрытия в катодную область приводит к снижению плотности тока коррозии (с 3.98 до 0.50 µА/см2) и облагораживанию коррозионного потенциала (с –950 до –714 мВ). Наиболее вероятной причиной такой закономерности является увеличение содержания никеля в покрытии, подтвержденное экспериментально (табл. 2). Однако не исключено, что наблюдаемые изменения коррозионных характеристик цинк-никелевого сплава связаны также с изменением его количественного фазового состава. Возможно, разблагораживание потенциала осаждения вкупе с введением коплексообразователя в электролит способствуют увеличению доли наиболее коррозионно стойкой γ-фазы в синтезируемом покрытии, что в свою очередь существенно повышает его устойчивость к коррозионному разрушению.
ВЫВОДЫ
1. Процесс электрохимического осаждения сплавов системы Zn–Ni из аммиачно-хлоридного электролита осложнен диффузионным транспортом ионов в жидкой фазе, при этом кинетическая стадия переноса заряда протекает необратимо.
2. Добавка глицина в концентрации 0.30 М не влияет на механизм электроосаждения Zn, Ni-сплавов, но приблизительно в полтора раза снижает вклад побочных реакций (вероятно, выделения водорода) в общую скорость катодного процесса.
3. Пленочные Zn, Ni-сплавы, электрохимически синтезированные из аммиачно-хлоридного электролита, построены на основе цинка, атомная доля которого практически не зависит от потенциала осаждения и в среднем составляет 10 ат. %. Добавление аминоуксусной кислоты в аммиачно-хлоридный электролит приводит к обогащению сплава никелем, доля которого становится примерно на 4 ат. % выше по сравнению со сплавами, полученными из аналогичного электролита без добавки глицина. При этом введение аминоуксусной кислоты в электролит осаждения не оказывает заметного влияния на качественный фазовый состав синтезируемых покрытий, которые во всех случаях представляют собой гетерогенную систему, состоящую из цинка и γ-фазы Ni2Zn11.
4. Электросаждение Zn, Ni-сплавов из глицинсодержащего аммиачно-хлоридного электролита позволяет получать более гладкие и блестящие покрытия, так как добавка аминоуксусной кислоты способствует снижению скорости осаждения сплава и, как следствие, шероховатости его поверхности.
5. Выход по току процесса электроосаждения цинк-никелевых сплавов из аммиачно-хлоридного электролита, не содержащего добавку глицина, слабо зависит от потенциала осаждения и равен в среднем примерно 87%. Добавление аминоуксусной кислоты к аммиачно-хлоридному электролиту осаждения увеличивает выход по току целевого процесса приблизительно на 6%.
6. Синтезируемые в настоящей работе Zn, Ni-покрытия существенно превосходят по противокоррозионной эффективности цинковое покрытие. При этом добавка глицина в аммиачно-хлоридный электролит осаждения дополнительно повышает коррозионную стойкость электроосажденных пленочных сплавов. Для Zn, Ni-покрытий, синтезированных из глицинсодержащего аммиачно-хлоридного электролита, наблюдается следующая тенденция: смещение потенциала электроосаждения сплава в катодную область приводит к снижению плотности тока коррозии (с 3.98 до 0.50 μА/см2) и облагораживанию коррозионного потенциала (с –950 до –714 мВ по шкале ст. в. э.), что, вероятно, связано с увеличением содержания никеля в покрытии и, как следствие, с повышением доли наиболее коррозионно-стойкой γ-фазы.
Список литературы
Шестаков М.А. / Автореф. дис. … канд. хим. наук. Тюмень: Тюменский государственный нефтегазовый университет. 2007. 23 с.
Вячеславов П.М. Электролитическое осаждение сплавов. Л.: Машиностроение, 1986. С. 46.
Гаевская Т.В., Цыбульская Л.С., Бык Т.В. // Химические проблемы создания новых материалов и технологий. 2003. Вып. 2. С. 100.
Vasilache T., Gutt S., Sandu I., Vasilache V., Gutt G., Risca M., Sandu A.V. // Recent Patents on Corrosion Science. 2010. V. 2. P. 1.
Лякишев Н.П. Диаграммы состояния двойных металлических систем. М.: Машиностроение, 2001. Т. 3. С. 670.
Lotfia N., Aliofkhazraeia M., Rahmanib H., Barati Darbanda Gh. // Protection of Metals and Physical Chemistry of Surfaces. 2018. V. 54. № 6. P. 1102.
Hosseini M.G., Abdolmaleki M., Ashrafpoor S. // J. Appl. Electrochem. 2012. V. 42. № 3. P. 153.
Cai J., Xu J., Wang L., Zhang L., Zhou H., Zhong Y., Chen D., Fan H., Shao H., Zhang J., Cao C. // Int. J. Hydrogen Energy. 2013. V. 38. № 2. P. 934.
Feng Z., Li Q., Zhang J., Tang P., Song H., An M. // Surface & Coatings Technology. 2015. V. 270. P. 47.
Kondo K., Yokoyama M., Shinohara K. // J. Electrochem. Soc. 1995. V. 142. № 7. P. 2256.
Garcia E., Sarret M., Müller C., Ortega J.A. // J. Electrochem. Soc. 2002. V. 149. № 5. P. 284.
Conrad H., Corbett J., Goldenz T.D. // J. Electrochem. Soc. 2012. V. 159. № 1. P. 29.
Mosavat S.H., Bahrololoom M.E., Shariat M.H. // Applied Surface Science. 2011. V. 257. № 20. P. 8311.
Tsybulskaya L.S., Gaevskaya T.V., Purovskaya O.G., Byk T.V. // Surface & Coatings Technology. 2008. V. 203. № 3. P. 234.
Muresan L.M. // Studia Universitatis Babes-Bolyai Chemia. 2010. V. 55. № 1. P. 37.
Soares M.E., Souza C.A.C., Kuri S.E. // Surface & Coatings Technology. 2006. V. 201. № 6. P. 2953.
Rajagopalan S.K. Characterization of electrodeposited Zn–Ni alloy coatings as a replacement for electrodeposited Zn and Cd coatings. Montreal: McGill University, 2012. 221 p.
Baldwin K.R., Robinson M.J., Smith C.J.E. // Corrosion Science. 1993. V. 35. № 5–8. P. 1267.
Rahsepar M., Bahrololoom M.E. // Corrosion Science. 2009. V. 51. № 11. P. 2537.
Elkhatabi F., Sarret M., Müller C. // J. Electroanal. Chem. 1996. V. 404. № 1. P. 45.
Lin Y., Selman J.R. // J. Electrochem. Soc. 1993. V. 140. № 5. P. 1299.
Swathirajan S. // J. Electrochem. Soc. 1986. V. 133. № 4. P. 671.
Elkhatabi F., Benballa M., Sarret M., Müller C. // Electrochim. Acta. 1999. V. 44. № 10. P. 1645.
Hosseini M.G., Ashassi-Sorkhabi H., Ghiasvand H.A.Y. // Surface & Coatings Technology. 2008. V. 202. № 13. P. 2897.
Trejo G., Ortega R., Meas Y., Ozil V.P., Chainet E., Nguyen B. // J. Electrochem. Soc. 1998. V. 145. № 12. P. 4090.
Дамаскин Б.Б., Петрий О.А., Цирлина Г.А. Электрохимия. М.: Химия, 2001. 624 с.
Chouchane S., Levesque A., Douglade J., Rehamnia R., Chopart J.P. // Surface & Coatings Technology. 2007. V. 201. № 14. P. 6212.
Fratesi R., Roventi G. // Surface & Coatings Technology. 1996. V. 82. № 1–2. P. 158.
Li G.Y., Lian J.S., Niu L.Y., Jiang Z.H. // Surface & Coatings Technology. 2005. V. 191. № 1. P. 59.
Ghaziof S., Gao W. // Applied Surface Science. 2014. V. 311. P. 635.
Byk T.V., Tsybulskaya L.S., Gaevskaya T.V. // Surface & Coatings Technology. 2008. V. 202. № 24. P. 5817.
Conrad H.A., Corbett J.R., Golden T.D. // J. Electrochem. Soc. 2012. V. 159. № 1. P. 29.
Conde A., Arenas M.A., Damborenea J.J. // Corrosion Science. 2011. V. 53. № 4. P. 1489.
Дополнительные материалы отсутствуют.
Инструменты
Физикохимия поверхности и защита материалов