Физикохимия поверхности и защита материалов, 2020, T. 56, № 3, стр. 297-300
Влияние предварительной магнитной активации электролита на его свойства и структуру покрытий Co–Bi
Т. Г. Шиблева 1, В. В. Поветкин 2, *
1 Тюменский государственный университет
Тюмень, Россия
2 Тюменский индустриальный университет
625000 Тюмень, ул. Семакова, 10, Россия
* E-mail: viktorpovetkin@mail.ru
Поступила в редакцию 13.02.2019
После доработки 09.06.2019
Принята к публикации 13.06.2019
Аннотация
В настоящей работе изучено влияние предварительной магнитогидродинамической активации трилонатного электролита для осаждения сплавов Со–Bi на его некоторые физико-химические характеристики (поверхностное натяжение, смачивание и электропроводность) и качество получаемых покрытий. При этом отмечается повышение скорости осаждения сплава Со–Bi и увеличение диапазона рабочих плотностей тока, что имеет важное значение для практической гальванотехники. Методом растровой и просвечивающей электронной микроскопии установлена структура полученных сплавов, осажденных при различных условиях электролиза. При магнитоэлектролизе в сплаве увеличивается содержание электроположительного компонента, измельчается структура, сглаживается поверхностный рельеф и улучшается качество покрытий.
Одним из способов повышения качества гальванических покрытий является воздействие магнитным полем (МП) на процесс электроосаждения металлов и сплавов.
При этом, в связи с необходимостью значительных затрат на создание магнитного поля при электролизе, практическую полезность может представлять лишь магнитная активация используемого электролита [1–4].
В данной работе изучали влияние предварительного омагничивания электролита для осаждения сплавов Co–Bi на его некоторые физико-химические характеристики (поверхностное натяжение, смачивание и электропроводность) и качество получаемых покрытий.
Для осаждения сплавов использовали трилонатный электролит [5]. Методики получения покрытий и определения служебных характеристик электролита и свойств сплавов не отличались от описанных ранее [2, 3]. Определение коэффициента поверхностного натяжения проводилось капельным методом, измерение краевых углов смачивания методом “сидящей” капли на поверхности твердого покрытия. Измерения микротвердости проводили на приборе ПМТ-3 при нагрузке 20 г. Испытания коррозионной стойкости проводили в течение трех суток погружением в 0.1 н раствор H2SO4.
Структуру осадков Co–Bi изучали методами растровой электронной микроскопии (РЭМ) и просвечивающей электронной микроскопии (ПЭМ). Тонкие фольги для (ПЭМ) готовили методом двусторонней электрополировки в фосфорно-хромовом электролите, предварительно удалив подложку в смеси серной кислоты и хромового ангидрида. Полученные фольги изучали в электронном микроскопе ЭМВ-100Л при ускоряющем напряжении 100 кВ в просмотровом режиме и режиме микродифракции.
В результате проведенных исследований было установлено, что магнитогидродинамическая активация электролита оказывает значительное влияние на его физико-химические характеристики.
При увеличении напряженности магнитного поля наблюдается снижение поверхностного натяжения электролита и краевого угла смачивания. При оптимальной напряженности МП (В = 0.213 Тл), поверхностное натяжение уменьшается примерно на 17%, а краевой угол смачивания на 8%; т.е. поверхность электрода лучше смачивается электролитом после его омагничивания. Уменьшение поверхностного натяжения при омагничивании свидетельствует о том, что уменьшается межмолекулярное взаимодействие между частицами в поверхностном слое жидкость–газ. Однозначно это явление трудно объяснить, поскольку магнитное поле оказывает действие и на структуру воды и на частицы, находящиеся в растворе; кроме того, магнитное поле может оказывать влияние на водородные связи в воде: происходит их изгибание [6], что влечет за собой изменение взаиморасположения молекул и, следовательно, структуры водного раствора. Помимо этого, магнитное поле влияет на степень гидратации ионов, находящихся в растворе [6, 7], которая, в значительной мере определяет состояние границ раздела фаз и структурные изменения в водной системе.
Изменение электропроводности (рис. 1, кривая 3) с увеличением напряженности МП проходит через максимум (В = 0.213Тл), что, вероятно, связано с изменением степени гидратации ионов и с увеличением их подвижности в МП. При более высоких значениях напряженности наблюдается уменьшение электропроводности электролита, что, вероятно, объясняется образованием ионных ассоциатов в растворе электролита.
Рис. 1.
Зависимость поверхностного натяжения σ (1), краевого угла смачивания θ (2) и электропроводности ϰ (3) от напряженности магнитного поля.
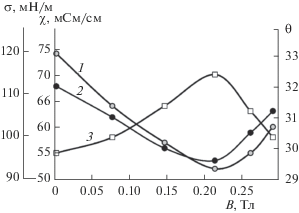
Исходя из полученных результатов, минимальные значения поверхностного натяжения (рис. 1, кривая 1) и краевого угла смачивания (рис. 1, кривая 2) и максимальное значение электропроводности (рис. 1, кривая 3), в дальнейших исследованиях использовали оптимальное значение напряженности магнитного поля В = 0.213 Тл.
При омагничивании электролита происходит обогащение сплава на 6–8% наиболее электроположительным компонентом-Bi, что свидетельствует о снижении диффузионных ограничений при восстановлении ионов висмута и повышении скорости осаждения этого металла, а также о возможной десорбции с поверхности катода трилона Б, который является слабым ПАВом анионного типа и, как следствие, уменьшением катодной поляризации. Зависимости состава сплава Co–Bi от плотности тока, как установлено (рис. 2), удовлетворительно описываются уравнением Кочергина–Победимского [8]:
при iк = 5–10 А/дм2 – стационарный электролиз; при iк = 5–16 А/дм2 – магнитоэлектролиз.Рис. 2.
Зависимость состава Co–Вi от катодной плотности тока: 1 – стационарный электролиз; 2 – магнитоэлектролиз.
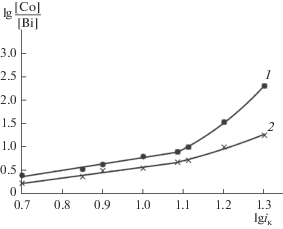
Соблюдение зависимости Кочергина–Победимского в указанных интервалах плотностей тока, свидетельствуют об электрохимической природе поляризации процесса соосаждения металлов в сплав. При дальнейшем повышении плотности тока процесс соосаждения компонентов переходит в другой режим.
Сравнительный анализ условий электролиза и качества покрытий, полученных из неомагниченного и омагниченного электролита показал эффективность использования магнитной активации растворов (табл. 1).
Таблица 1.
Характеристики процесса электроосаждения сплава Co–Bi и его покрытий в зависимости от режима электролиза (t = 25oC, iк = 10 А/дм2, pH 1.5)
Характеристика | Стационарный электролиз |
Магнитоэлектролиз |
---|---|---|
Скорость осаждения, мкм/ч | 58 | 72 |
Рассеивающая способнсть электролита, % | 61 | 70 |
Внешний вид покрытий | Светло-серые, матовые | Светлые, ровные, полублестящие |
Содержание висмута в сплаве, % | 16 | 22 |
Содержание кислорода в сплаве, % | 0.5 | 2.82 |
Микротвердость, МПа | 425 | 488 |
Коррозионная скорость, мг/м2 ч | 3.1 | 2.3 |
Следует отметить, что использование омагниченного электролита позволяет увеличить скорость осаждения покрытий, выход сплава по току, а также рассеивающую способность электролита. Вероятно, в активируемом электролите под действием силы Лоренца улучшается массоперенос разряжающихся ионов к поверхности катода. Кроме того, при магнитоэлектролизе существенно расширяется диапазон рабочих плотностей тока, что дает возможность интенсифицировать процесс электроосаждения [3].
Если в условиях стационарного электролиза светлые, качественные покрытия формируются в диапазоне плотностей тока 5–11 А/дм2, то при магнитоэлектролизе этот диапазон расширяется до 15 А/дм2. Здесь уместно отметить, что эффект омагничивания электролита наблюдается и после снятия магнитного поля еще в течение 5–6 ч.
Согласно растровой электронной микроскопии (РЭМ) покрытия, осажденные из омагниченного электролита, характеризуются более сглаженным рельефом поверхности и дисперсными структурными элементами по сравнению с осадками, полученными в стационарных условиях. Возможно, это объясняется увеличением числа активных, одновременно растущих центров кристаллизации на катоде, т.к. под действием магнитного поля уменьшается толщина диффузионного слоя, что приводит к ускоренному восстановлению ионов металлов. По данным ПЭМ, структура покрытий существенно зависит от условий электролиза. Так, осадки, полученные в стационарных условиях, в основном, кристаллизуются с ГПУ-решеткой и состоят из хорошо сформированных зерен с четкими высокоугловыми границами (рис. 3а).
Рис. 3.
Структура электролитических осадков сплава Сo–Bi, полученных в стационарных условиях (а) и при магнитоэлектролизе (б).
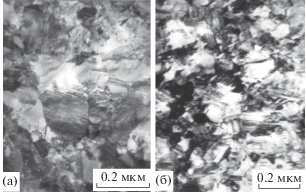
Ряд кристаллитов характеризуется двойниковой структурой; границы субзерен дислокационного типа в таких осадках практически не встречаются. Слоистое строение отдельных кристаллитов и наличие в них двойников свидетельствует о формировании этих покрытий по механизму слоистого роста путем образования двумерных зародышей.
Из омагниченного электролита формируются высокодисперсные осадки с преимущественным содержанием кристаллитов β-Со. Такие осадки состоят из мелких кристаллитов неправильной формы (рис. 3б). Особенностью тонкой структуры этих покрытий является наличие в них большого числа дефектов упаковки. Дефекты упаковки обычно занимают целые зерна и представляют собой многослойные срастания из очень тонких (порядка нескольких нм) параллельных пластин.
Влияние магнитной активации электролита на дисперсность осадков сплава следует объяснить следующим образом: известно [7, 9, 12], что при омагничивании водных растворов в них повышается содержание растворенного кислорода (примерно на 20%) и его химическая активность. Электрокристаллизация осадков в подобных условиях сопровождается измельчением и интенсивным окислением структурных элементов (зерен и субзерен) получаемых осадков. Присутствие по границам зерен окисных включений способствует повышению их твердости и коррозионной стойкости. Аналогичные результаты были получены при электроосаждении никеля и кобальта [9–11] в условиях омагничивания, а также полученные нами результаты при электроосаждении сплава Bi–Pb из предварительно омагниченного трилонатного электролита [4].
Список литературы
Поветкин В.В., Шиблева Т.Г., Житникова А.В. // Физикохимия поверхности и защита материалов. 2008. Т. 44. № 5. С. 557–560.
Поветкин В.В., Шиблева Т.Г., Кислицина Н.А. // Вестник ТюмГУ. 2007. № 3. С. 58–61.
Поветкин В.В., Шиблева Т.Г. Сб. “Найновите постижения на европейската наука”. Химия и хим. технология. София: БялГРАД – БГ. ООД, 2011. Т. 35. С. 31–38.
Поветкин В.В., Шиблева Т.Г. // Вестник ТюмГУ. Тюмень, 2011. № 5. С. 137–141.
Поветкин В.В., Скифский С.В. Патент РФ № 2197567. БИ № 3. 2003.
Классен В.И. Омагничивание водных систем. М.: Химия, 1982. 296 с.
Гончарук В.В., Маляренко В.В. // Химия и технология воды. 2003. Т. 25. № 3. С. 212–227.
Кочергин С.М., Победимский Г.Р. // Тр. Казанского химико-технологического института. Казань, 1964. Вып. 33. С. 124–127.
Matsushima H., Ispas A., Bund A., Plieth W., Fukunaka Y. // J. Solid State Electrochemistry. 2007. V. 11. P. 737–743.
Ganesh V., Vijayaraghavan D., Lakshminarayanan V. // Appl. Surf. Science. 2005. V. 240. Issues 1–4. P. 285–295.
Uhlemann M. // Electroanalitical Chemistry. 2006. V. 587. Is. 1. P. 93–98.
Hinds G., Spada F.E., Coey M.D. // Phys. Chem. 2001, V. 105. P. 9487–9502.
Дополнительные материалы отсутствуют.
Инструменты
Физикохимия поверхности и защита материалов