Физикохимия поверхности и защита материалов, 2020, T. 56, № 5, стр. 539-547
Влияние физико-механических свойств подложки на поведение покрытий Zr–Si–B при трении скольжения и воздействии циклических ударно-динамических нагрузок
Ф. В. Кирюханцев-Корнеев 1, *, А. Д. Сытченко 1
1 Национальный исследовательский технологический университет “МИСиС”
119049 Москва, Ленинский проспект, 4, Россия
* E-mail: kiruhancev-korneev@yandex.ru
Поступила в редакцию 19.03.2020
После доработки 02.04.2020
Принята к публикации 09.04.2020
Аннотация
Методом магнетронного распыления мишени ZrB2–20% Si были получены покрытия на подложках из молибдена, хромистого и твердого сплава. Исследованы состав, структура и трибологические свойства покрытий. Установлено влияние физико-механических свойств подложек на поведение покрытий при трении скольжении и воздействии ударно-динамических нагрузок. Покрытие обладало малодефектной структурой и содержало гексагональную фазу ZrB2 c размером кристаллитов 15–30 нм. Трибологические испытания подложек показали, что при нагрузке 1 Н коэффициент трения находился в пределах 0.6–0.8. После нанесения покрытий данная величина составила 0.7–0.75. При использовании в качестве подложки твердого сплава в зоне трибоконтакта наблюдалось хрупкое разрушение покрытия при наименьшей глубине проникновения контр-тела. В случае покрытий на подложках с низкой твердостью и модулем упругости, достигалась максимальная глубина износа, происходила выраженная деформация, причем доля пластической составляющей сокращалась после нанесения покрытий. Стойкость подложек к ударно-динамическим нагрузкам при 100, 300 и 500 Н закономерно увеличивалась при увеличении их твердости и индекса пластичности. Покрытие, полученное на твердосплавной подложке с твердостью 19 ГПа и индексом пластичности 0.03, показало глубину кратера 0.45 мкм, что в 16 и 5 раз меньше, чем для покрытий на молибденовом и хромистом сплавах.
ВВЕДЕНИЕ
В области инженерии поверхности активно ведутся разработки, направленные на получение покрытий на основе диборида циркония, которые обладают высокой твердостью (Н) на уровне 25–45 ГПа [1, 2], хорошей износостойкостью и стойкостью к окислению до 1000°С [3]. Модификация базовых покрытий кремнием увеличивает его твердость более чем в 1.5 раза [4] и значительно повышает жаростойкость [5, 6]. Известно большое количество покрытий на основе диборида циркония, полученных различными методами. В качестве примеров можно указать покрытия: ZrB2–SiC, получаемые методом спекания [7], вакуумного плазменного напыления [8] и методом диффузионного насыщения [9], ZrB2–MoSi2, изготовленные методом плазменного напыления низкого давления [10, 11] и магнетронного распыления [12], а также покрытия на основе ZrB2–TiSi2 и ZrB2–TaSi2, осаждаемые методами термического напыления и паровой инфильтрации [13–15]. Известны работы по нанесению покрытий системы Zr–Si–B методом электроискрового легирования в различных газовых средах [16]. В предыдущих работах были получены покрытия Zr–Si–B методом магнетронного распыления мишеней, полученных с помощью самораспространяющегося высокотемпературного синтеза [17]. Покрытия Zr–Si–B характеризовались Н ~ 22 ГПа и высокой стойкостью к окислению при температурах T ≥ 1500°C [18]. Жаростойкость данных покрытий напрямую зависит от состава: увеличение концентрации кремния способствует снижению скорости окисления в 9 раз [19]. Отметим, что трибологические исследования покрытий в системе Zr–Si–B ранее не проводились.
Для прогнозирования поведения покрытий в реальных условиях эксплуатации необходимо установить взаимосвязь между свойствами подложки и триботехническими характеристиками покрытий. Так, например, в работе [20] были изучены твердые покрытия на основе карбонитирида титана, полученные методом магнетронного распыления на подложках с различным модулем упругости (E). Было показано, что в случае царапания покрытия на материале с низким индексом пластичности, H/Е, преобладает упругая деформация. В то время как высокий Н/Е подложки приводит к преобладанию пластической составляющей деформации. Свойства подложки оказывают влияние на механизм локализованной деформации покрытий [21]. Также на механизм локализованной деформации оказывает влияние параметр H3/Е2 [22]. Величины H и E подложки могут оказывать влияние на значения соответствующих характеристик, измеренных при индентировании. Эффекты связаны, во-первых, с процессами деформации подложки, и, во-вторых, с проникновением полей упругих напряжений вглубь подложки [23]. Трибологические испытания покрытий на основе TiSiB показали, что покрытия на никелевом сплаве демонстрируют непрерывный рост коэффициента трения вследствие вдавливания покрытия в относительно мягкую подложку и увеличения площади трибоконтакта, тогда как в случае высокомодульной и твердой подложки из оксида алюминия, значения коэффициента трения стабильны во времени [24].
Целью данной работы является исследование покрытий Zr–Si–B, полученных на подложках с сильно отличающимися физико-механическими свойствами, при трении скольжения и воздействии ударно-динамических нагрузок, определение закономерностей влияния характеристик подложек на поведение покрытий.
МЕТОДИКА
Покрытия получали методом магнетронного распыления. Керамические мишени ZrSiB (17.4 ат. % Zr, 47.7 ат. % Si, 34.9 ат. % B) диаметром 120 мм и толщиной 6 мм были получены методом самораспространяющегося высокотемпературного синтеза [17]. Распыление проводилось с помощью вакуумной установки на базе откачивающей системы УВН-2М при следующих условиях: ток 2 А, напряжение 500 В, атмосфера Ar (99.9995%), рабочее давление в вакуумной камере 0.1–0.2 Па. В качестве подложек использовались диски из твердого сплава ВК6М размером Ø30 × 5 мм, диски из молибдена MЧ-1 размером Ø18 × 4 мм и хромистого сплава Х65НВФТ размером Ø25 × 5 мм. Физико-механические свойства подложек указаны в табл. 1.
Из всех используемых подложек наиболее интенсивное диффузионное взаимодействие при нагреве покрытий наблюдается в сплавах, содержащих никель [25]. Поэтому в случае хромистого сплава Х65НВФТ наносился диффузионно-барьерный подслой CrAlSiB, подробно описанный в [26]. Перед нанесением покрытия подложки очищали в изопропиловом спирте на установке УЗДН-2Т с рабочей частотой 22 кГц в течение 5 мин. После чего образцы подвергались очистке в вакууме с использованием ионного источника щелевого типа (ионы Ar+, 2 кэВ) в течение 20–25 мин.
Элементный состав и структуру покрытий изучали с помощью сканирующей электронной микроскопии с использованием микроскопа S-3400 Hitachi (Япония), оснащенного приставкой Noran-7 Thermo для энергодисперсионной спектроскопии. Рентгенофазовый анализ (РФА) проводили на дифрактометре Bruker (Германия) с использованием CuKα излучения. Элементные профили получали с помощью оптического эмиссионного спектрометра тлеющего разряда Profiler-2 HORIBA JY (Франция). Просвечивающая электронная микроскопия проводилась на приборе JEM-2100 Jeol. Трибологические испытания по определению коэффициента трения покрытий проводили на машине трения HT-Tribometer CSM Instruments (Швейцария) по схеме “стержень–диск”. Образцы были испытаны в контакте с шариком из Al2O3 диаметром 6 мм при нагрузке 1 Н с линейной скоростью 10 см/с. Испытание на динамическое воздействие осуществляли с помощью прибора Impact Tester (CemeCon, Германия). Исследуемые покрытия подвергались ряду ударов с постоянной частотой 50 Гц с использованием шарика из твердого сплава WC-6%Co диаметром 5 мм при нагрузках 100, 300 и 500 Н. Количество ударов составило 105. Для определения параметров кратеров и дорожек износа использовали оптический профилометр WYKO-NT1100.
РЕЗУЛЬТАТЫ И ИХ ОБСУЖДЕНИЕ
Номера и составы покрытий показаны в табл. 2. Все покрытия имели близкие значения концентраций основных элементов. Покрытие 1 содержало 16.4 ат. % Zr, 31.7 ат. % Si и 51.9 ат. % B. Для покрытия 2 и 3 наблюдались более высокие концентрации Zr и B в пределах 17.3–18.4 и 53.1–53.5 ат. % соответственно. Концентрация кремния составила 28.5–29.2 ат. %. В случае покрытия 2 подслой, наблюдаемый на глубине 1.3–5 мкм, имел следующий состав: 53.0 ат. % Cr, 8.2 ат. % Al, 9.4 ат. % Si, 29.4 ат. % B. Согласно профилям распределения элементов по глубине толщина покрытий находилась в пределах 1–2 мкм (рис. 1). Для всех образцов было характерно равномерное распределение элементов по глубине. По данным сканирующей электронной микроскопии покрытия имели плотную и однородную структуру.
Таблица 2.
Состав покрытий
Покрытие | Сплав | Элементный состав покрытий, ат. % | ||
---|---|---|---|---|
Zr | Si | В | ||
1 | МЧ-1 | 16.4 | 31.7 | 51.9 |
2 | Х65НВФ | 17.3 | 29.2 | 53.5 |
3 | ВК6М | 18.4 | 28.5 | 53.1 |
Согласно данным РФА (рис. 2), все покрытия содержали гексагональную фазу на основе ZrB2. Размер кристаллитов h-ZrB2, определенный по формуле Шеррера, находился в пределах 15–30 нм. На дифрактограммах также присутствовали пики от фаз, соответствующих материалам подложки. В случае покрытия 1 были найдены пики металлического молибдена Mo (карточка JCPDS 895156), для покрытия 2 – пики интерметаллида Ni11Cr9 [28] и твердого раствора никеля в хроме Ni–Cr (JCPDS 260429). Покрытие 3 содержало фазы карбида вольфрама WC (JCPDS 892727) и твердый раствор на основе Co (JCPDS 894307). Просвечивающая электронная микроскопия подтвердила, что основу покрытий составляет фаза h-ZrB2; размер зерна, определенный из темнопольных изображений составлял от 4 до 17 нм. Согласно данным, полученным в [17] покрытие Zr–Si–B обладало следующими механическими характеристиками: Н = 22 ГПа, Е = 256 ГПа, W = = 60%, H/E = 0.90, H3/E 2 = 0.17 ГПа.
Исследования по определению коэффициента трения (f) подложек при нагрузке 1 Н (рис. 3а) показали, что установивший коэффициент трения подложки МЧ-1 находился в пределах 0.75–0.80, для образца Х65НВФТ f = 0.54–0.63. Установившийся f для ВК6М был равен 0.71–0.80.
Рис. 3.
Зависимость коэффициента трения от дистанции: (а) сплав МЧ-1 (1), сплав Х65НВФТ (2) и сплав ВК6М (3); (б) покрытие 1 (1), покрытие 2 (2), покрытие 3 (3), нанесённые на соответствующие подложки.
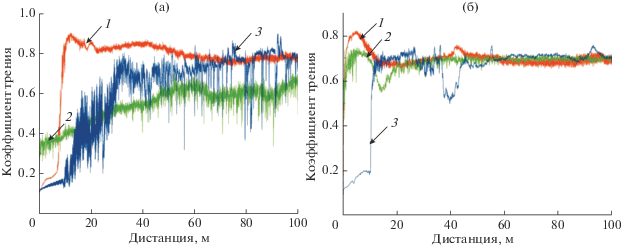
При нагрузке 1 Н покрытие 1 показало начальный f = 0.13 (рис. 3б). После 15 м испытания достигался коэффициент трения 0.81, затем происходил выход значений f на величину ~0.7. В случае образца 2 начальный f = 0.25. На дистанции 0–14 м f = 0.73, затем, вероятно после полного разрушения, снижается до ~0.7. Начальный f составил 0.13 для образца 3. На отрезке 0.1–10 м фиксировались значения f = 0.09–0.20. На установившейся стадии f ~ 0.70.
Таким образом, начальный участок зависимости (дистанция до 20 м) определяется физико-механическими свойствами подложек. В случае твердой подложки (ВК6М) покрытие разрушается уже при минимальном пробеге и коэффициент трения образца с покрытием соответствует непокрытому материалу (рис. 3). В случае более пластичных подложек (МЧ-1, Х65НВФТ) наблюдается зависимость с достижением максимальных значений f = 0.73–0.81, что может быть связано с деформацией системы покрытие-подложка и увеличением площади зоны трибоконтакта по аналогии с [24]. Последующее снижение можно объяснить началом разрушения покрытия. Подложка практически не оказывает влияния на f для покрытий 1–3 после пробега 20 м: фиксируются близкие значения f в пределах 0.70 ± 0.02, коэффициент трения определяется в основном не характеристиками подложек, а продуктами разрушения покрытия.
Трибологические испытания при нагрузке 5 Н показали, что после дистанции 2 м наблюдался выход коэффициента трения на значения подложек 0.8–0.85. Что свидетельствует о том, что все покрытия износились.
Трехмерные профили дорожек износа подложек, а также значения их глубины (h) и ширины (В) показаны на рис. 4 и 5. При нагрузке 1 Н наблюдался неравномерный износ сплавов МЧ-1 и Х65НВФТ, связанный с их пластической деформацией [24, 31]. При трибоконтакте происходит вдавливание контр-тела в материал подложки до достижения максимальных напряжений, в результате чего наблюдается разные h и B по всей длине дорожки износа. В свою очередь твердосплавная подложка практически не износилась в глубину – видны лишь поверхностные следы контакта. Максимальная ширина дорожек износа подложек МЧ-1 и Х65НВФТ не отличалась и составила ~350 мкм, а для сплава ВК6М В ~ 400 мкм. Несмотря на это h убывала в последовательности MЧ-1 → Х65НВФТ → ВК6М со значениями 7, 6 и 0.8 мкм соответственно.
Рис. 4.
Трехмерные профили дорожек износа подложек и покрытий после трибологических испытаний при нагрузках 1 и 5 Н.
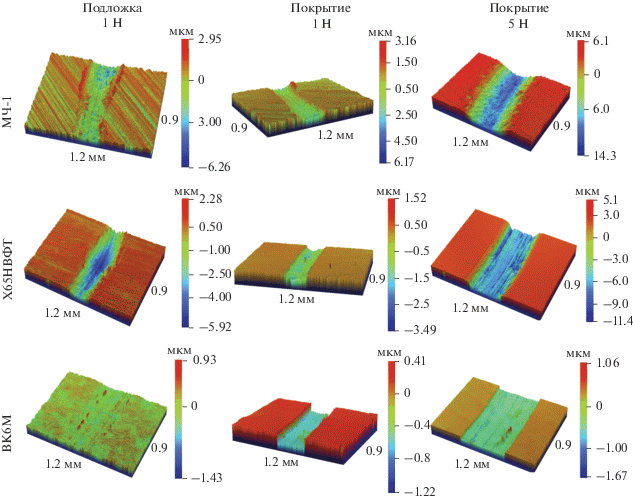
Стоит отметить, что после нанесения покрытий в случае подложек из молибдена и хромистого сплава характер их износа изменился, разброса по B и h дорожки практически не наблюдалось (рис. 4). Данный эффект говорит об уменьшении доли пластической деформации и преобладании упругой вследствие нанесения покрытия с высокими W, H/Е и H3/E 2. Покрытие 3 на твердом сплаве показало хрупкий характер разрушения, наблюдалось осыпание покрытия из-за жестких условий трибоконтакта (недеформируемые подложка и контр-тело). Величина В для покрытий 1–3 превосходила их толщину как при нагрузке 1, так и при 5 Н (рис. 5). При 1 Н покрытия 1–3 показали близкую В = 250–275 мкм. Покрытие 1 характеризовалось h = 2.5 мкм. Максимальной h = 3.8 мкм обладало покрытие 2, а минимальную h = 1.2 мкм показало покрытие 3. Можно установить следующую закономерность: для покрытий, полученных на мягких подложках, преобладает вязкое разрушение, а для покрытий на твердых подложках – хрупкое. При нагрузке 5 Н В дорожек износа для покрытий 1, 2 и 3 составила 575, 475 и 525 мкм соответственно. В то время как h дорожки снижалась в ряде покрытие 1 (13 мкм) → покрытие 2 (8.3 мкм) → → покрытие 3 (1.5 мкм).
Результаты ударно-динамических испытаний подложек из молибдена, хромистого и твердого сплавов показаны на рис. 6 и 7. При нагрузке 100 Н размеры кратера для сплава из молибдена твердостью 1.2 ГПа составили: диаметр, D = 360 мкм и глубина, h = 6 мкм, а для хромистого слава (Н = = 3.7 ГПа) D = 300 мкм и h = 3.8 мкм. Твердый сплав показал наименьшие геометрические размеры кратера при нагрузке 100 Н: D = 125 мкм и h = 0.4 мкм. Увеличение нагрузки до 300 и 500 Н показало аналогичную зависимость: с увеличением H подложки, диаметр и глубина кратеров снижались (рис. 7).
Рис. 7.
Диаметр (D) и глубина (h) кратеров на поверхности после ударно-динамических испытаний подложек.
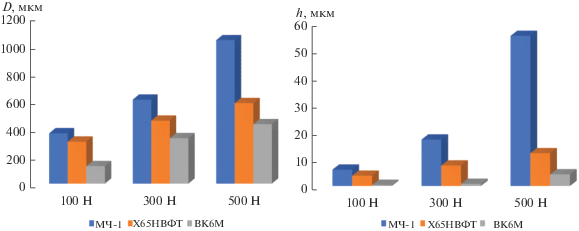
Трехмерные профили и размеры кратеров после испытаний на ударно-динамическое воздействие покрытий показаны на рис. 8 и 9. При приложенной нагрузке 100 Н для покрытия 1 были характерны следующие размеры кратера: D = = 440 мкм и h = 7.5 мкм. Образец 2 показал D = 275 мкм и h = 2.3 мкм. А покрытие 3, аналогично чистой подложке, показало наименьшую h = 0.45 мкм. D был в 4.4 и 2.8 раза ниже по сравнению с покрытиями 1 и 2 соответственно и составил 100 мкм.
Анализ полученных данных показал, что h кратера покрытия 3 при 100 Н была в 16 и 5 раз ниже по сравнению с h, полученными для покрытий 1 и 2. Для значений твердости подложек наблюдалась аналогичная закономерность: Н сплава ВК6М в 16 и 5 раз выше H сплавов МЧ-1 и Х65НВФТ соответственно. При нагрузках 300 и 500 Н тенденция сохранилась: размеры кратера уменьшались в последовательности: покрытие 1 → 2 → 3. Данное явление говорит о преобладающем влиянии твердости подложек на стойкость покрытий к ударно-динамическим воздействиям. Увеличение параметра Н/Е, характеризующего стойкость материала к упругой деформации [22, 32–34], подложки с 0.0035 до 0.03 приводило к изменению глубины кратера покрытий с 7.5 до 0.45 мкм. Таким образом, показатель H/E описывает разницу в геометрических размерах кратеров хуже, чем H.
ЗАКЛЮЧЕНИЕ
В настоящей работе были получены покрытия системы Zr–Si–B толщиной ~1 мкм на подложках из чистого молибдена, хромистого и твердого сплава методом магнетронного напыления. Покрытия характеризовались равномерным распределением элементов по глубине и содержали гексагональную фазу ZrB2 с размером кристаллитов 15–30 нм. Было показано, что коэффициент трения покрытий определяется свойствами подложки до момента разрушения, а на установившейся стадии испытаний, основную роль играют продукты износа покрытия. Наименьшей глубиной дорожки износа 1.2 и 1.5 мкм при нагрузках 1 и 5 Н обладало покрытие, полученное на твердом сплаве ВК6М. В то время как образцы, осажденные на подложках МЧ-1 и Х65НВФТ, при нагрузке 1 Н показали значения 2.5 и 3.8 мкм, при 5 Н 13 и 8.2 мкм соответственно. Индекс пластичности H/E подложек не оказывал влияния на износостойкость покрытий.
После ударно-динамических испытаний глубина кратера покрытия на твердом сплаве при нагрузке 100 Н была 0.45, что в 16 и 5 раз ниже по сравнению с покрытиями, полученными на молибденовом и хромистом сплавах. Это хорошо коррелирует с твердостью подложек. Твердость сплава ВК6М (Н = 19 ГПа) в 16 и 5 раз выше H МЧ-1 и Х65НВФТ. При 300 и 500 Н установленные закономерности были аналогичными. Параметр H/E подложки влияет на поведение покрытий, но не так явно, как H. В случае воздействия циклических ударно-динамических нагрузок покрытие на подложке с высоким H/E = 0.03 подвергалось хрупкому разрушению. В то время как для образцов, полученных на молибденовом сплаве с H/E = 0.0035 и хромистом сплаве с H/E = 0.0148, преобладала пластическая деформация.
Таким образом, главным показателем, влияющим на износостойкость и стойкость покрытий к ударно-динамическому нагружению, является твердость H подложки. Индекс пластичности H/E определяет характер разрушения в случае динамических испытаний, и не влияет на поведение покрытий при трении скольжении. Явной взаимосвязи между параметром H 3/E2 и поведением покрытий в различных трибологических схемах не обнаружено.
Список литературы
Broitman E., Tengdelius L., Hangen U.D. et al. // Scripta Materialia. 2016. V. 124. P. 117.
Tengdelius L., Broitman E., Lu J. et al. // Acta Materialia. 2016. V. 111. P. 166.
Tay C.Y., Harris I.R., Wright S.J. // J. Electronic Materials. 1989. V. 18. P. 511.
Choi H., Jang J., Zhang T. et al. // Surf. Coat. Technol. 2014. V. 259. P. 707.
Ren X., Shi H., Wang W. et al. // J. European Ceramic Society. 2020. V. 40. P. 203.
Kiryukhantsev-Korneev Ph.V., Iatsyuk I.V., Shvindina N.V. et al. // Corrosion Science. 2017. 123. P. 319.
Ren X., Sun X., Wang W. et al. // J. Alloys and Compounds. 2018. V. 769. P. 387.
Aliasgarian R., Naderi M., Mirsalehi S.E. et al. // J. Alloys and Compounds. 2018. V. 742. P. 797.
Yao X., Li H., Zhang Y. et al. // Ceramics International. 2012. V. 38. P. 2095.
Jinyuan M., Min L., Chunming D. et al. // Rare Metal Materials and Engineering. 2016. V. 45. P. 1386.
Dou H., Qiangang F., Tianyu L., Mingde T. // J. European Ceramic Society. V. 40. 2020. P. 212.
Yanjiao Y., Mingjiang D., Chunbei W. et al. // Rare Metal Materials and Engineering. 2017. V. 46. P. 3663.
Li J., Zhang Y., Wang H. et al. // J. Alloys and Compounds. 2020. P. 153934.
Ren Y., Qian Y., Xu J. et al. // Ceramics International. 2019. In Press.
Wang Z., Niu Y., Hu C. et al. // Ceramics International. 2015. V. 41. P. 14868.
Kudryashov A.E., Kiryukhantsev-Korneev Ph.V., Petrzhik M.I. et al. // CIS Iron and Steel Review. 2019. V. 18. P. 46.
Iatsyuk I.V., Lemesheva M.V., Kiryukhantsev-Korneev Ph.V. et al. // IOP Conf. Series: Materials Science and Engineering. 2018. V. 347. P. 012028.
Kiryukhantsev-Korneev Ph.V., Lemesheva M.V., Shvindina N.V. et al. // Protection of Metals and Physical Chemistry of Surfaces. 2018. V. 54. № 6. P. 1147.
Kiryukhantsev-Korneev F.V., Yatsyuk I.V. // Physics of Atomic Nuclei. 2019. V. 82. № 11. P. 1437.
Shtansky D.V., Petrzhik M.I., Bashkova I.A. et al. // Physics of the Solid State. 2006, V. 48. №. 7. P. 1301.
Levashov E.A., Petrzhik M.I., Shtansky D.V. et al. // Materials Science and Engineering: A. 2013. V. 570. P. 51.
Shtansky D.V., Kulinich S.A., Levashov E.A. et al. // Thin Solid Films. 2012. V. 420–421. P. 330.
Saha R., Nix W.D. // Acta Materialia. 2002. V. 50. P. 23.
Кирюханцев-Корнеев Ф.В., Петржик М.И. // Нанотехнологии: наука и производство. 2018. Т. 1. С. 3.
Kiryukhantsev-Korneev F.V., Sheveiko A.N., Komarov V.A. et al. // Russian J. Non-Ferrous Metals. 2011. V. 52. P. 311.
Kiryukhantsev-Korneev Ph.V., Pierson J.F., Kuptsov K.A. et al. // Applied Surface Science. 2014. V. 314. P. 104.
Метотехника: [сайт]. URL: https://www.metotech.ru/molibden-opisanie.htm
Каширцев В.В. // Диссертация канд. техн. наук: 05.02.07. М., 2014. 165 с.
Куксенова Л.И. / Износостойкость конструкционных материалов: учеб. пособие / М.: Изд-во МГТУ им. Н.Э. Баумана, 2011. 237 с.
Kiryukhantsev-Korneev Ph.V., Sheveiko A.N. // Protection of Metals and Physical Chemistry of Surfaces. 2018. V. 54. P. 963.
Xi H.-H., He P.-F., Wang H.-D. et al. // International J. Refractory Metals and Hard Materials. 2020. V. 86. P. 05095.
Kumar D.D., Kumar N., Kalaiselvam S. et al. // Ceramics International. 2015. V. 41. P. 9849.
Picas J.A., Forn A., Baile M.T., Martín E. // International J. Refractory Metals and Hard Materials. 2005. V. 23. P. 330.
Leyland A., Matthews A. // Wear. 2000. V. 246. P. 1.
Дополнительные материалы отсутствуют.
Инструменты
Физикохимия поверхности и защита материалов