Физикохимия поверхности и защита материалов, 2020, T. 56, № 5, стр. 548-556
Влияние уплотнения перманганатом калия на коррозионную устойчивость анодированного сплава алюминия АД31
М. А. Осипенко 1, *, Д. С. Харитонов 1, 2, **, И. В. Макарова 3, A. Wrzesińska 4, И. И. Курило 1
1 Белорусский государственный технологический университет
220006 Минск, ул. Свердлова, 13а, Беларусь
2 Jerzy Haber Institute of Catalysis and Surface Chemistry, Polish Academy of Sciences
30-239 Krakow, Niezapominajek, 8, Poland
3 Lappeenranta University of Technology
FI-53850 Lappeenranta, Skinnarilankatu 34, Finland
4 Lodz University of Technology, Department of Molecular Physics
90-924 Lodz, Zeromskiego st., 116, Poland
* E-mail: marikaosipenko@gmail.com
** E-mail: nckharyt@cyf-kr.edu.pl
Поступила в редакцию 15.11.2019
После доработки 14.04.2020
Принята к публикации 21.04.2020
Аннотация
Методами сканирующей электронной микроскопии, спектроскопии комбинационного рассеяния, потенциодинамической поляризации, электрохимической импедансной спектроскопии, а также испытаниями в камере соляного тумана установлено влияние условий получения и параметров финишной обработки модифицированных перманганат-ионами анодно-оксидных покрытий на сплаве алюминия АД31 (АА6063) на их физико-механические и защитные свойства. Показано, что уплотнение в растворах перманганата калия и последующий обжиги последующий обжиг в течение 5 мин позволяет увеличить коррозионную стойкость сформированного анодно-оксидного слоя более чем в 200 раз.
ВВЕДЕНИЕ
Алюминий и его сплавы благодаря своим уникальным химическим и механическим свойствам находят широкое применение в строительной, автомобильной и авиационной промышленности. Для обеспечения повышенной механической прочности при сохранении пластичности алюминий легируют Si и Mg. Однако из-за присутствия в составе сплавов Al–Mg–Si интерметаллических частиц они обладают пониженной коррозионной устойчивостью по сравнению с чистым алюминием, подвержены локальным видам коррозии и коррозионному растрескиванию под напряжением [1–4]. Одним из эффективных методов повышения коррозионной устойчивости кремний- и магнийсодержащих сплавов алюминия является анодирование и последующее химическое уплотнение полученных анодно-оксидных покрытий различными модифицирующими растворами [5, 6].
В настоящее время широкое промышленное применение находит сернокислое оксидирование в 15−20% растворе серной кислоты. В процессе оксидирования на поверхности образуется двухслойная пленка, состоящая из внутреннего тонкого беспористого барьерного слоя и толстого (до 3 мкм), имеющего ячеистую шестиугольную структуру пористого слоя, формирование которого происходит перпендикулярно поверхности металла. Присутствие интерметаллических частиц в структуре сплава приводит к образованию дефектов и трещин в процессе анодирования. Это обусловливает необходимость дальнейшей обработки анодно-оксидных покрытий (АОП) – уплотнения в различных растворах, что приводит к герметизации, закупориванию пор, а также задержке проникновения к подложке агрессивных ионов [7–11].
Традиционно уплотнение АОП проводят в горячей дистиллированной воде или растворах соединений хрома(VI), однако перспективным является применение электролитов, содержащих менее опасные ингибиторы коррозии на основе соединений церия(III), циркония(IV), которые позволяют значительно увеличить коррозионную стойкость сплавов алюминия [8, 12]. При этом необходимо учесть, что уплотнение в горячей воде очень энергозатратно, применение электролитов на основе хрома(VI) экологически небезопасно, а использование при финишной обработке электролитов, содержащих соли редкоземельных металлов, экономически невыгодно. Это обусловливает актуальность разработки новых составов модифицирующих растворов и режимов финишной обработки анодно-оксидных покрытий на алюминиевых сплавах, обеспечивающих повышенную коррозионную стойкость и экологическую безопасность.
Перспективным направлением является использования электролитов уплотнения на основе марганецсодержащих систем [13]. Валентность марганца варьируется в диапазоне от +7 до 0, что определяет возможность протекания окислительно-восстановительных процессов с его участием и формирования пассивационных пленок на основе оксидов марганца. Кроме того, подобно хроматам, перманганаты обладают эффектом “самозалечивания” [12], что обеспечивает высокую коррозионную стойкость марганецсодержащих АОП.
Целью данной работы являлось изучение влияния уплотнения в перманганате калия анодно-оксидных покрытий, сформированных на сплаве алюминия АД31, на их физико-химические и антикоррозионные свойства.
МЕТОДИКА ЭКСПЕРИМЕНТА
АОП получали на сплаве алюминия марки АД31 (АА6063), микроструктура и коррозионная характеристика которого детально описаны в наших предыдущих работах [2, 4]. Для получения АОП использовали сернокислый электролит, содержащий 2.0 моль/дм3 H2SO4. Анодирование проводили с использованием источника тока Элатек Б5-80 в течение 40 мин при комнатной температуре (≈22°С) и плотности тока 1 А/дм2. Материал катодов – свинец.
Последующее уплотнение АОП проводили методом горизонтального погружения оксидированных образцов в рабочий раствор, содержащий 0.2 М KMnO4, при температуре 100 ± 1°С. Время уплотнения – 20 мин. Уплотненные образцы подвергали финишной термообработке в муфельной печи при температуре 300 ± 1°С, время обжига варьировали от 0 до 60 мин.
Морфологию и элементный состав покрытий изучали методами сканирующей электронной микроскопии (СЭМ) и энергодисперсионного рентгеновского микроанализа (EDX) с использованием микроскопа JEOL JSM-5610 LV, оснащенного системой химического микрорентгеноспектрального анализа EDX JED-2201.
Фазовый состав полученных покрытий изучали методом конфокальной спектроскопии комбинационного рассеяния (КСКР). Спектры КСКР снимали с использованием Ar+-лазерa с длиной волны 514.5 нм в диапазоне комбинационного сдвига 200‒1100 см‒1 при комнатной температуре на спектрометре JobinYvon T64000, оснащенном конфокальным микроскопом Olympus BX40 с объективом 50× (NA 0.75). Спектры регистрировали в течение 300°С, количество накоплений ‒ 2.
Для исследования коррозионной стойкости полученных покрытий использовали потенциостат/гальваностат PGSTAT 302N (Methrom Autolab), оснащенный модулем анализа частот FRA32M. Рабочий электрод – образец сплава алюминия АД31, электрод сравнения – насыщенный хлоридсеребряный, вспомогательный электрод – платиновая сетка. Поляризационные кривые снимали в диапазоне потенциалов от –300 до +300 мВ от стационарного потенциала, скорость развертки потенциала составляла 1 мВ/с.
Снятие спектров импеданса проводили в диапазоне частот 105–10–2 Гц с амплитудой колебаний тока 10 мВ. Анализ спектров, подбор эквивалентных схем и расчет параметров их элементов проводили с использованием ПО “ZView 3.2” и “Nova 2.1”.
Исследования полученных покрытий в камере соляного тумана S120is (ASCOTT) проводили в соответствии с ASTM B117–16. Испытанию подвергали одну сторону образца, оборотную изолировали кремнийорганическим лаком КО-85. Испытания проводили в 5% NaCl в течение 510 ч при температуре 35 ± 2°C. Для анализа состояния поверхности образцы периодически вынимали из камеры, промывали дистиллированной водой, сушили и фотографировали цифровой камерой Nikon D60.
РЕЗУЛЬТАТЫ И ИХ ОБСУЖДЕНИЕ
Анализ поверхности анодированных образцов показал, что при анодировании в растворе серной кислоты на поверхности формируются матовые АОП с характерным серым окрасом. Уплотнение в растворе KMnO4 вследствие заполнения пористого оксидного слоя соединениями марганца приводит к формированию АОП, окрашенных в светло-розовый цвет. Дальнейшая термическая обработка в течение 5–60 мин приводит к изменению окраски поверхности образца от золотистой до землисто-бурой.
Анализ микрофотографий АОП, представленных на рис. 1а, показывает, что структура анодированных образцов является достаточно неоднородной. В анодированном слое наблюдается образование большого количества дефектов, что обусловлено селективным растворением в процессе анодирования нано- и микроразмерных интерметаллических частиц, входящих в структуру сплава [3, 8].
Рис. 1.
Микрофотографии АОП без уплотнения (а), уплотненных горячей водой (б) и перманганат-ионами (в–д), в зависимости от времени обжига, мин: 0 (в), 5 (г), 60 (д).
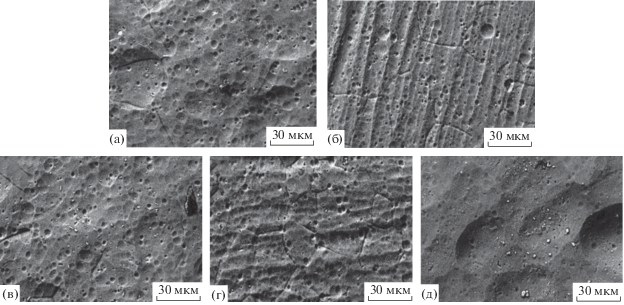
Последующее уплотнение АОП приводит к заполнению внешнего пористого слоя марганецсодержащими соединениями (рис. 1в–1д). Термическая обработка способствует увеличению числа микротрещин в АОП, что связано с различными значениями коэффициентов объемного расширения оксидного слоя и алюминиевой матрицы. Уменьшение количества видимых пор при увеличении длительности термообработки может быть связано с их заполнением марганецсодержащими соединениями.
На рис. 2 представлены EDX-карты элементного состава поверхности модифицированных марганецсодержащими соединениями АОП после термической обработки в течение 5 мин. Согласно полученным данным, основными элементами в структуре АОП являются Al и O. Большое содержание S вызвано использованием серной кислоты для формирования АОП, а присутствие кремния обуславливается его малой растворимостью в серной кислоте. Карты также показывают локальное внедрение соединений марганца в структуру АОП.
Рис. 2.
Микрофотография АОП. Уплотненного перманганат-ионами, и карты распределения химических элементов по поверхности при времени обжига 5 мин.
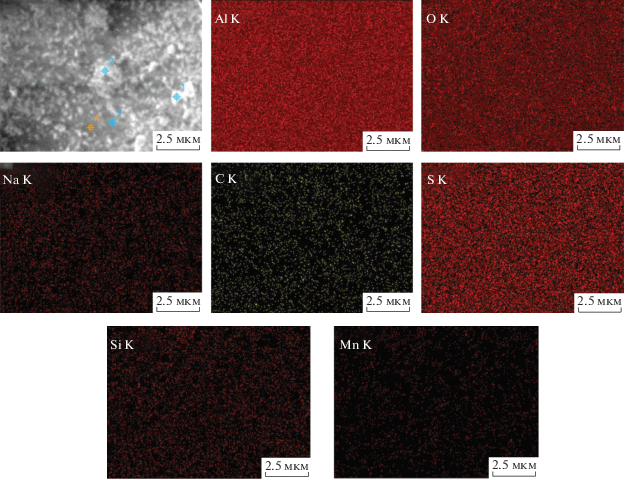
Анализ элементного состава (табл. 1) показал, что после уплотнения полученных АОП в растворе KMnO4 содержание марганца составляет 0.90 мас. %. Последующая термическая обработка в течение 5, 30 и 60 мин приводит к снижению количества марганца до 0.71, 0.56 и 0.31 мас. % соответственно. Уменьшение доли марганца в процессе термообработки обусловлено изменением фазового состава покрытия в результате протекания процессов термического разложения марганецсодержащих компонентов и окисления составляющих АОП и алюминиевой подложки, а также более равномерным распределением марганца по толщине покрытия.
Таблица 1.
Элементный состав модифицированных перманганат-ионами АОП на сплаве АД31
Время обжига, мин | Элементный состав, мас. % | ||||||
---|---|---|---|---|---|---|---|
С | O | Na | Si | Al | S | Mn | |
0 | 4.99 | 44.24 | 0.40 | 0.30 | 41.52 | 7.65 | 0.90 |
5 | 2.71 | 43.16 | 0.36 | 0.25 | 45.08 | 7.73 | 0.71 |
30 | 2.07 | 45.42 | 0.36 | 0.40 | 43.18 | 8.01 | 0.56 |
60 | 2.27 | 44.35 | 0.35 | 0.31 | 44.33 | 8.08 | 0.31 |
Для изучения фазового состава сформированных АОП, модифицированных марганецсодержащими соединениями, использовали метод спектроскопии комбинационного рассеяния света (рис. 3). Как видно из представленных данных, спектры образцов до и после термической обработки идентичны. Пики поглощения с максимумом интенсивности в области комбинационного сдвига 623 и 352 см–1 идентифицированы как сигналы от соединений трехвалентного марганца, находящихся в виде оксида Mn3O4 и метагидроксида MnOOH соответственно [15–17].
Рис. 3.
Спектры комбинационного рассеяния уплотненных перманганат-ионами АОП при времени обжига, мин: 1 – 0, 2 – 5, 3 – 30, 4 – 60.
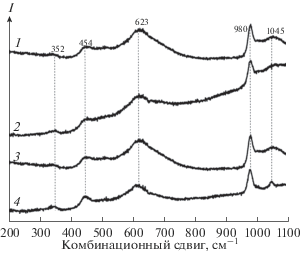
Образование Mn3O4, вероятно, происходит в процессе гидротермальной обработки анодированного сплава алюминия. На начальной стадии перманганат калия восстанавливается по реакциям:
(1)
$\begin{gathered} {\text{6KMn}}{{{\text{O}}}_{4}} + {\text{1}}0{\text{Al }} + {\text{ 24}}{{{\text{H}}}_{2}}{\text{S}}{{{\text{O}}}_{{\text{4}}}}{\text{ }} = \\ = {\text{ 5A}}{{{\text{l}}}_{{\text{2}}}}{{\left( {{\text{S}}{{{\text{O}}}_{{\text{4}}}}} \right)}_{{{\text{3 }}}}} + {\text{ 3}}{{{\text{K}}}_{{\text{2}}}}{\text{S}}{{{\text{O}}}_{{{\text{4 }}}}} + {\text{ 6MnS}}{{{\text{O}}}_{{{\text{4 }}}}} + {\text{24}}{{{\text{H}}}_{{\text{2}}}}{\text{O,}} \\ \end{gathered} $(2)
$\begin{gathered} {\text{2KMn}}{{{\text{O}}}_{{{\text{4 }}}}} + {\text{2Al }} + {\text{ }}{{{\text{H}}}_{{\text{2}}}}{\text{O }} = \\ = {\text{A}}{{{\text{l}}}_{{\text{2}}}}{{{\text{O}}}_{{{\text{3 }}}}} + {\text{ 2KO}}{{{\text{H}}}_{{\text{ }}}} + {\text{ 2Mn}}{{{\text{O}}}_{{\text{2}}}}{\kern 1pt} {\text{,}} \\ \end{gathered} $(3)
$\begin{gathered} {\text{18KMn}}{{{\text{O}}}_{{\text{4}}}} + 26{\text{Al}} + {\text{9}}{{{\text{H}}}_{{\text{2}}}}{\text{O }} = \\ = 13{\text{A}}{{{\text{l}}}_{{\text{2}}}}{{{\text{O}}}_{{\text{3}}}} + {\text{18KOH}} + {\text{6M}}{{{\text{n}}}_{{\text{3}}}}{{{\text{O}}}_{{\text{4}}}}. \\ \end{gathered} $Процессы (2) и (3) возможны при условии, что в порах АОП рН существенно выше его значения в объеме электролита. Образующиеся соединения марганца(II) могут восстанавливаться до соединений марганца(IV):
(4)
$\begin{gathered} {\text{3MnS}}{{{\text{O}}}_{{{\text{4 }}}}} + {\text{2KMn}}{{{\text{O}}}_{{\text{4}}}} = \\ {\text{ = }}\,\,{{{\text{K}}}_{{\text{2}}}}{\text{S}}{{{\text{O}}}_{{\text{4}}}} + {\text{Mn}}{{\left( {{\text{S}}{{{\text{O}}}_{{\text{4}}}}} \right)}_{{\text{2}}}} + {\text{4Mn}}{{{\text{O}}}_{{\text{2}}}}. \\ \end{gathered} $Термообработка также приводит к образованию дополнительных количеств оксида марганца(IV):
(5)
${\text{KMn}}{{{\text{O}}}_{{\text{4}}}} \to {{{\text{K}}}_{2}}{\text{Mn}}{{{\text{O}}}_{{{\text{4 }}}}} + {{{\text{O}}}_{{\text{2}}}} + {\text{Mn}}{{{\text{O}}}_{2}}.$При взаимодействии с алюминиевой матрицей оксид марганца(IV) может восстанавливаться до смешанного оксида:
(6)
${\text{9Mn}}{{{\text{O}}}_{{{\text{2 }}}}} + {\text{4Al}} = {\text{3M}}{{{\text{n}}}_{{\text{3}}}}{{{\text{O}}}_{{\text{4}}}} + 2{\text{A}}{{{\text{l}}}_{{\text{2}}}}{{{\text{O}}}_{{\text{3}}}}.$Образование MnOOH, вероятно, происходит при окислении Mn3O4 в процессе гидротермальной обработки анодированного алюминия по следующей реакции [18, 19]:
(7)
${\text{2M}}{{{\text{n}}}_{{\text{3}}}}{{{\text{O}}}_{{{\text{4 }}}}} + {\text{3}}{{{\text{H}}}_{{\text{2}}}}{\text{O}} + {{\text{1}} \mathord{\left/ {\vphantom {{\text{1}} {\text{2}}}} \right. \kern-0em} {\text{2}}}{{{\text{O}}}_{{{\text{2 }}}}} = {\text{6MnOOH}}{\text{.}}$Широкая полоса комбинационного рассеивания в диапазоне от 980–1045 см–1 показывает присутствие сульфат-ионов [16, 20, 21], что свидетельствует об образовании Al2(SO4)3 и MnSO4.
Полоса поглощения в области 454 см–1 идентифицирована как сигнал от AlOOH, который формируется на стенках пор барьерного слоя АОП в процессе уплотнения [22]:
(8)
${\text{A}}{{{\text{l}}}_{2}}{{{\text{O}}}_{3}} + {{{\text{H}}}_{{\text{2}}}}{\text{O}} \to {\text{2AlOOH}}{\text{.}}$Коррозионную стойкость полученных АОП оценивали методом снятия потенциодинамических поляризационных кривых (рис. 4). Для образца без уплотнения на границе раздела фаз АОП/электролит стационарный потенциал составляет 0.608 В. Уплотнение АОП в дистиллированной воде и растворе перманганата калия приводит к смещению стационарного потенциала и потенциала коррозии Eкорр в область электроотрицательных значений.
Рис. 4.
Потенциодинамические поляризационные кривые образцов сплава АД31 в 0.5 М NaCl. Уплотнение анодированного сплава алюминия АД31 перманганат-ионами с различным временем обжига, мин: 1 – 5, 2 – 10, 3 – 15, 4 – 30, 5 – 45, 6 – 60, 7 – без обжига, 8 – уплотнение в воде, 9 – без уплотнения.
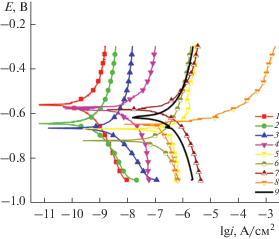
Как видно из представленных данных (табл. 2), для образцов, подвергшихся стандартному гидротермическому уплотнению в горячей дистиллированной воде, значение плотности тока коррозии составляет iкорр = 3.95 × 10−8 А/см2. Уплотнение в растворе перманганата калия приводит к снижению токов коррозии до iкорр = 1.73 × 10−9 А/см2. Это указывает на тот факт, что образующиеся в процессе уплотнения на стенках пор марганецсодержащие гидроксидно-оксидные покрытия Al(OH)х–Mn(OH)х обеспечивают лучшую герметизацию пористого слоя оксида алюминия, а, следовательно, обладают большой устойчивостью к воздействию окружающей среды, чем образующийся при стандартном гидротермическом наполнении бемит AlOOH.
Таблица 2.
Электрохимические параметры, полученные из анализа потенциодинамических поляризационных кривых
Вид обработки | |bк|, В | ак, В | ba, В | aa, В | iкорр, А/см2 | Eкорр, В |
---|---|---|---|---|---|---|
Уплотнение в KMnO4 + 5 мин обжиг | 0.0112 | –0.6859 | 0.0132 | –0.4144 | 7.87 × 10‒12 | –0.559 |
Уплотнение в KMnO4 + 10 мин обжиг | 0.0088 | –0.7380 | 0.0072 | –0.5638 | 1.30 × 10‒11 | –0.643 |
Уплотнение в KMnO4 + 15 мин обжиг | 0.0075 | –0.7409 | 0.0063 | –0.5979 | 4.34 × 10‒11 | –0.664 |
Уплотнение в KMnO4 + 30 мин обжиг | 0.0085 | –0.6590 | 0.0050 | –0.5205 | 5.50 × 10‒11 | –0.577 |
Уплотнение в KMnO4 + 45 мин обжиг | 0.0044 | –0.7049 | 0.0042 | –0.6301 | 2.01 × 10‒9 | –0.669 |
Уплотнение в KMnO4 + 60 мин обжиг | 0.0075 | –0.6429 | 0.0104 | –0.4952 | 5.61 × 10‒9 | –0.720 |
Уплотнение в KMnO4, без обжига | 0.0079 | –0.7880 | 0.0072 | –0.6557 | 1.73 × 10‒9 | –0.581 |
Уплотнение горячей водой | 0.0214 | –0.8051 | 0.0096 | –0.5756 | 3.95 × 10‒8 | –0.627 |
Без уплотнения | 0.0717 | –0.9268 | 0.0808 | –0.1585 | 7.64 × 10‒8 | –0.608 |
Для достижения большей коррозионной устойчивости уплотненные перманганат-ионами оксидированные образцы подвергались последующей термической обработке. Минимальное значение плотности тока (iкорр = 7.87 × 10–12 А/см2), а, следовательно, наибольшую устойчивость показали образцы при времени обжига 5 мин. Это может быть связано с уменьшением остаточного напряжения, более полной герметизацией пористого слоя оксида алюминия и, как следствие, с препятствием миграции хлорид-ионов в глубину АОП.
С увеличением времени обжига происходит постепенный рост значений плотностей токов коррозии, а значит, и ухудшение антикоррозионных свойств термообработанных покрытий. Это может быть обусловлено различием коэффициентов теплового расширения уплотненного перманганат-ионами пористого внешнего и беспористого внутреннего слоев, что приводит к тепловому растрескиванию и способствует интенсификации диффузии хлорид-ионов к подложке [23].
Результаты импедансной спектроскопии, представленные в виде диаграмм Найквиста, приведены на рис. 5. На спектрах импеданса всех исследуемых образцов отсутствует индукционная область, что свидетельствует о высокой коррозионной устойчивости изучаемых покрытий в хлоридсодержащих средах.
Рис. 5.
Диаграммы Найквиста АОП, уплотненных перманганат-ионами (1–3), горячей водой (4) и без уплотнения (5) в зависимости от времени обжига, мин: 0 (1), 5 (2), 60 (3).
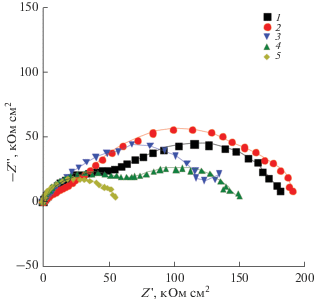
Наибольший диаметр окружности на диаграмме Найквиста, а, следовательно, наибольшая коррозионная устойчивость наблюдается для АОП с финишной термической обработкой в течение 5 мин, что хорошо согласуется с данными поляризационных исследований (рис. 4, табл. 2).
Для всех исследуемых образцов на диаграммах Найквиста наблюдаются две полуокружности (рис. 5). Наличие полуокружности в области высоких и средних частот характерно для процессов с лимитирующей электрохимической стадией и объясняется электрическими свойствами поверхности сплава и уплотненного АОП. Полуокружность, наблюдаемая в области низких частот представленных спектров, свидетельствует о протекании двух параллельных процессов: разрушения уплотненного оксидного слоя анодированного алюминия и адсорбции образующихся продуктов коррозии на поверхности образца.
Для термически обработанных в течение 60 мин образцов на диаграмме Найквиста (рис. 5, кривая 3) присутствует одна полуокружность в области высоких и средних частот. Характер дальнейшего хода спектра импеданса в исследованном диапазоне низких частот неоднозначен. Данный участок, наиболее вероятно, описывает процессы разрушения бемита AlOOH и марганецсодержащих соединений, запирающих пористый барьерный слой, с последующим появлением диффузионных ограничений, связанных с включением в структуру покрытия продуктов коррозии.
Результаты подбора параметров эквивалентных схем представлены в табл. 3. Экспериментальные данные описывали схемами, представленными на рис. 6, в которых, R1 – сопротивление внешнего пористого слоя, R2 – сопротивление внутреннего барьерного слоя, CPE1 и CPE2 – элементы постоянной фазы, отвечающие пористому и барьерному слоям соответственно.
Таблица 3.
Параметры эквивалентных схем, полученные из анализа спектров импедансной спектроскопии
Вид обработки | R1, Ом см2 | R2, Ом см2 | Y1, Ом см2 cn | Y2, Ом см2 cn | n1 | n2 |
---|---|---|---|---|---|---|
Уплотнение в KMnO4 | 179 550 | 49 740 | 1.678 × 10–6 | 4.930 × 10–7 | 0.784 | 0.671 |
Уплотнение в KMnO4 + 5 мин обжиг | 183 390 | 83 505 | 1.472 × 10–6 | 2.260 ×10–6 | 0.835 | 0.488 |
Уплотнение в KMnO4 + 60 мин обжиг | 136 530 | 6965 | 3.093 × 10-6 | 8.060 × 10–6 | 0.720 | 0.541 |
Уплотнение горячей водой | 125 000 | 90 345 | 1.858 ×10–6 | 1.403 × 10–7 | 0.659 | 0.780 |
Без уплотнения | 57 819 | – | 2.772 × 10–6 | – | 0.700 | – |
В случае кривой 3 на рис. 5 нижней границы исследованных частот не достаточно, чтобы однозначно сделать вывод о необходимости использования элемента Варбурга при расшифровке полученных данных, поэтому в данном случае также использовали схему с двумя элементами постоянной фазы.
Анализ полученных данных показал, что наименьшее значение сопротивления пористого слоя (57 819 Ом см2) характерно для неуплотненных образцов.
Для образцов, подвергшихся гидротермическому уплотнению и уплотнению перманганат-ионами без финишной термообработки, сопротивление пористого слоя составляет 125 000 и 179 550 Ом см2 соответственно. Наибольшее сопротивление внешнего пористого слоя (183 390 Ом см2) показали образцы с последующей термической обработкой в течение 5 мин. С увеличение времени обжига наблюдается уменьшение сопротивления пористого слоя до 150400 Ом см2. Сопротивление электролита изменяется незначительно, а его значения сопоставимы для всех проведенных испытаний.
На рис. 7 представлены фотографии поверхности образцов сплава алюминия АД31 до и после испытаний в камере соляного тумана в течение 510 ч. На поверхности образца сравнения без АОП после 48 ч испытаний наблюдается большое количество очагов локальной коррозии, через 510 ч – практически вся поверхность образца покрыта продуктами коррозии белого цвета. В свою очередь, образцы, модифицированные перманганат-ионами, вне зависимости от наличия термообработки показали высокую коррозионную стойкость в хлоридсодержащей среде. После 510 ч испытаний структура их поверхности практически не изменилась, очагов коррозии не обнаружено. Однако для образцов, термически обработанных в течение 60 мин, на поверхности после 510 ч испытаний присутствуют очаги питтинговой коррозии.
ВЫВОДЫ
1. Данные СЭМ показали, что в процессе анодирования сплава алюминия АД31 формируется АОП с большим количеством дефектов, что обусловлено селективным растворением нано- и микроразмерных интерметаллических частиц, входящих в структуру сплава. Последующее уплотнение образцов в растворе перманганата калия и термообработка при 300°C приводят к заполнению внешнего пористого слоя марганецсодержащими соединениями и уменьшению количества дефектов на поверхности покрытия. Увеличение длительности термообработки от 5 до 60 мин приводит к снижению количества микропор и увеличению числа макротрещин в АОП, что связано с различными значениями коэффициентов объемного расширения оксидного слоя и алюминиевой матрицы.
2. Результаты EDX-анализа и полученные спектры комбинационного рассеяния показали, что уплотнение в растворах перманганата калия приводит к формированию АОП, включающих фазы смешанного состава Mn3O4 и MnOOH и содержащих до 0.90 мас. % марганца. Термообработка полученных образцов в течение 5, 30 и 60 мин не приводит к существенному изменению фазового состава марганецсодержащих соединений, входящих в состав АОП, но способствует снижению доли марганца на поверхности до 0.71, 0.56 и 0.31 мас. % соответственно.
3. Поляризационные исследования полученных образцов в 0.5 М растворе NaCl показали, что уплотнение в растворе перманганата калия приводит к снижению токов коррозии более чем в 40 раз. Термическая обработка уплотненных АОП в течение 5 мин способствует уменьшению их остаточного напряжения и более полной герметизации пористого слоя оксида алюминия и, как следствие, снижению токов коррозии более чем в 200 раз. Увеличение времени обжига от 5 до 60 мин приводит к росту значений плотности тока коррозии от 7.87 × 10–12 до 5.61 × 10‒9 А/см2 соответственно, что связано с растрескиванием покрытия из-за различия коэффициентов теплового расширения уплотненного перманганат-ионами пористого внешнего и беспористого внутреннего слоев.
4. Результаты электрохимической импедансной спектроскопии исследованных образцов в 0.5 М растворе NaCl показали, что уплотнение в растворах перманганата калия позволяет увеличить сопротивление пористого слоя АОП более, чем в 3 раза и достигает максимума при термической обработке в течение 5 мин. Увеличение длительности термообработки от 5 до 60 мин приводит к снижению сопротивления поверхности от 183.4 до 150.4 кОм см2 соответственно.
5. Испытания в камере соляного тумана в течение 510 ч показали, что практически вся поверхность образца сравнения без АОП покрыта продуктами коррозии. Для АОП, уплотненных в растворах перманганата калия и термически обработанных в течение 60 мин, наблюдаются единичные очаги питтинговой коррозии. Структура поверхности остальных образцов в процессе испытаний практически не изменилась.
Список литературы
Davis J.R. et al. Light Metals and Alloys. Alloying: Understanding the Basics // ASM International. 2001. P. 349.
Kharitonov D.S. et al. // Corros. Sci. 2019. V. 148. P. 237–250.
Kharitonov D.S. et al. // J. Electrochem. Soc. 2018. V. 165. № 3. P. 116–126.
Kharitonov D.S., Dobryden I.B., Sefer B. // Protection of Metals and Physical Chemistry of Surfaces. 2018. V. 54. № 2. P. 291–300.
Zhang F., Nilsson J., Pan J. // J. Electrochemical Society. 2016. V. 163. № 9. P. 609–618.
Ma Y. et al. // Surface and Interface Analysisi. 2013. V. 45. P. 1479–1484.
Shang Y. et al. // Int. J. Electrochem. Sci. 2016. V. 11. № 6. P. 5234–5244.
Chahboun N. et al. // J. Electrochem. Soc. 2016. V. 163. № 3. P. 69–75.
Figueroa R., Nóvoa X.R., Pérez C. et al. // Electrochim. Acta. 2019. V. 303. P. 56–66.
Ding Z.V. et al. // Surf. Coat. Technol. 2018. P. 1–32.
Wu H. et al. // 2019. P. 1–41.
Carangelo A. et al. // J. Electrochem. Soc. 2016. V. 163. № 10. P. 619–626.
Wang R. et al. // Surf. Coat. Technol. 2018. P. 1–34.
Mokaddem M. et al. // Electrochem. commun. 2011. V. 13. № 1. P. 42–45.
Hussain S. et al. // Sci.World J. 2013. V. 2013. P. 1–8.
Guo X. et al. // J. Phys. Chem. A. 2010. V. 114. № 23. P. 6480–6486.
Julien C.M., Massot M., Poinsignon C. // 2004. V. 60. P. 689–700.
Ristić M. et al. // J. Mol. Struct. 2013. V. 1044. P. 255–261.
Murray J.W., Dillard G., Moers H. // 1985. V. 49. № May 1983. P. 463–470.
Frost R.L. et al. // Spectrochim. Acta – Part A Mol. Biomol. Spectrosc. 2013. V. 116. P. 165–169.
Tomikawa K., Kanno H. // J. Phys. Chem. A. 1998. V. 102. № 30. P. 6082–6088.
Kiss A.B., Keresztury G., Farkas L. // Spectrochim. Acta Part A Mol. Spectrosc. 1980. V. 36. № 7. P. 653–658.
Lee J. et al. // Appl. Surf. Sci. 2013. V. 283. P. 941–946.
Дополнительные материалы отсутствуют.
Инструменты
Физикохимия поверхности и защита материалов