Физикохимия поверхности и защита материалов, 2020, T. 56, № 6, стр. 579-590
Углеродные нанопористые адсорбенты из скорлупы грецкого ореха для улавливания паров сжиженного природного газа в системах криогенного хранения
И. Е. Меньщиков 1, *, А. А. Фомкин 1, Ю. А. Романов 1, М. Р. Киселев 1, А. Л. Пулин 1, С. С. Чугаев 1, А. В. Школин 1
1 ФГБУН Институт физической химии и электрохимии им. А.Н. Фрумкина РАН
119071 Москва, Ленинский проспект, 31, стр. 4, Россия
* E-mail: i.menshchikov@phyche.ac.ru
Поступила в редакцию 12.03.2020
После доработки 14.04.2020
Принята к публикации 21.04.2020
Аннотация
Разработана концепция одностадийного синтеза микропористых активных углей из скорлупы грецкого ореха методом физической газовой активации в атмосфере СО2 для систем аккумулирования метана в области низких температур 120, 160 и 178 К. Область карбонизации исходного сырья лежит в интервале 240–950°С. Оптимальный температурный режим для развития микропористой системы адсорбента в атмосфере СО2 соответствует температуре около 900°С. Активация в этих условиях позволяет достигать степеней обгара до 70 мас. % и сформировать оптимальную пористую структуру для адсорбционного аккумулирования паров метана (СПГ). Полученный адсорбент имеет высокий объем микропор W0 = 0.59 см3/г, объем мезопор WМЕ = 0.33 см3/г, удельную поверхность SБЭТ = = 1490 м2/г и полуширину микропор 0.59 нм, которые обеспечивают его высокую адсорбционную активность по метану. Наличие мезопор позволяет обеспечить дополнительный вклад в адсорбцию за счет капиллярной конденсации. Теоретическая оценка адсорбционной активности адсорбента к метану показала, что при температурах 120, 160 и 178 К и давлениях до 6 бар величины равновесной адсорбции достигают 15, 13.5 и 12 ммоль/г соответственно.
ВВЕДЕНИЕ
Известно, что в процессе хранения сжиженного природного газа (СПГ), происходит его постепенное испарение в результате теплопритоков в криогенный резервуар с жидкостью (~111 К) из окружающей среды. При отсутствии потребления газа, пары СПГ сбрасываются в окружающую среду или сжигаются на факеле с целью предотвращения повышения избыточного давления внутри криогенного резервуара и его разрушения, что приводит к значительным потерям ценного энергоресурса. Для решения этой проблемы целесообразно использовать специальные адсорбционные аккумуляторы высокой емкости [1], которые позволяют улавливать и удерживать пары СПГ, с возможностью их дальнейшего полезного применения. Особенно актуальной эта проблема является для пользователей автономных систем энергоснабжения на основе СПГ малой мощности.
Эффективными адсорбентами для применения в системах адсорбционного аккумулирования природного газа метана, в том числе и в условиях криогенных температур, могут быть активные угли (АУ) на основе сырья растительного происхождения [1], полученные различными методами активации – химической или физической [2].
Перспективными в этом направлении, в силу высокой плотности и низкой зольности исходного сырья, могут быть высокоактивные углеродные адсорбенты из скорлупы грецкого ореха (Júglans régia). В России сырьевая база по скорлупе грецкого ореха (СГО) по современным оценкам составляет порядка 5 тыс. т в год [3]. Производство активных углей из СГО может быть особенно выгодным, в первую очередь в районах, где произрастает культура грецкого ореха. Это связано с тем, что транспортировать исходную ореховую косточку куда-либо невыгодно. Экономически целесообразно аккумулировать переработку косточки в районе (районах), приближающихся к местам их произрастания и сбора.
К настоящему времени в области синтеза активных углей из СГО проведено достаточно большое количество исследований [4–15]. Большинство из них ориентировано на получение и исследование адсорбентов для решения задач экологии, в частности для применения в системах водоочистки.
Тем не менее, для адсорбционных систем аккумулирования газов требуются адсорбенты со специально созданной пористой структурой, структурно-энергетические характеристики которых, должны быть оптимальными для термодинамических условий работы системы хранения и свойств концентрируемого газа [16, 17].
На сегодняшний день работы по исследованию синтеза и использования активных углей из СГО для получения эффективных адсорбентов для аккумулирования паров СПГ не проводились, что делает эту задачу крайне важной и актуальной. Ниже кратко представлены результаты основных работ, посвященных синтезу углей из СГО и исследованиям их пористой структуры.
В [5, 6, 10, 11] проведено исследование влияния условий синтеза адсорбентов из СГО в среде углекислого газа на их конечные адсорбционные свойства, рассмотрены режимы и условия синтеза, такие как температура ТА, количество ступеней активации, время выдержки τ. В [11] показано, что образцы, полученные при помощи одноступенчатой активации исходного сырья в потоке CO2, обладают превосходящими параметрами пористой структуры (SБЭТ = 680 м2/г, ТА = 800°С) по сравнению с материалами, синтезированными из карбонизата, заранее подготовленного в инертной среде аргона (SБЭТn = 470 м2/г, ТА = 800°С). Этот факт обусловлен меньшим общим временем контакта с газом-активатором. В то же время, как отмечено в [10], увеличение времени активации материала в потоке CO2, до 480 мин при подъеме температуры активации до ТА = 850°С способствует росту SБЭТ до 1300 м2/г и W0 до 0.72 см3/г. Полуширина микропор полученных образцов составляет 0.7 нм.
В качестве эффективного активатора при синтезе углей из СГО может использоваться и водяной пар [10, 14]. Используя данный подход, в [10] были получены образцы с удельной поверхностью SБЭТ = 1360 м2/г и W0 = 0.74 см3/г при времени активации τ = 60 мин и температуре ТА = 850°С.
Термохимическая активация способствует образованию развитой пористой структуры. Так, использование KOH позволяет существенно увеличить удельную поверхность по БЭТ (до 2250 м2/г) и объем микропор (до 1.07 см3/г) в сходных термических условиях активации (ТА = 800°С) [11]. В работе [15] отмечается, что температуры карбонизации ТC = 700°С и активации ТА = 800°С в присутствии активатора KOH, обеспечивают получение углей из СГО с высокоразвитой пористой структурой. При этом изменение массового соотношения KOH/карбонизат от 1/1 до 4/1 обеспечивает подъем SБЭТ с 440 до 1880 м2/г [15].
Известны работы, где в качестве активирующего агента при синтезе активных углей из СГО, предназначенных для очистки воды, использовали ZnCl2 [4, 12, 13]. Используя термохимический синтез с агентом ZnCl2 в условиях пониженных давлений, авторам [12] удалось обеспечить параметры SБЭТ и WT на уровне 1800 м2/г и 1.176 см3/г соответственно.
Следует отметить, что адсорбенты, полученные при помощи физической активации, обладают более широким спектром применения в силу того, что конечный продукт содержит минимальное количество посторонних вредных примесей, требующих специальной отмывки, чего нельзя сказать про активные угли, синтезированные в присутствии химических агентов.
В целом, химический способ переработки углеродсодержащих материалов имеет две основные положительные стороны: более высокий выход готового продукта (не менее, чем в 2 раза по сравнению с продуктом, полученным “физическим” способом); более развитый объем микропор.
К отрицательным сторонам термохимической технологии относятся:
− необходимость использования при оформлении аппаратурного процесса коррозионностойких (в том числе к термической обработке) материалов и применения дополнительного оборудования, а также химических реагентов;
− значительное количество сточных вод, требующих утилизации, что понижает экономическую привлекательность технологии;
− дополнительные требования при проектировании технологической линии изготовления активного угля.
С точки зрения получаемого продукта, при химической активации адсорбирующие поры представляют микропоры на уровне 95–98%, а при физической активации развиваются как микропоры, так и транспортные мезопоры [11], что может позитивно сказаться для адсорбционного аккумулирования паров газов, в том числе и для СПГ.
Таким образом, активные угли, получаемые классическим методом физической активации, имеют ряд технологических и качественных преимуществ по сравнению с адсорбентами, получаемыми термохимическим способом, особенно в условиях малотоннажного производства. В связи с этим, целью настоящей работы являются исследование механизма образования пористой структуры и поиск оптимальных режимов синтеза углеродных адсорбентов на основе СГО при помощи физической активации в потоке CO2, а также исследование их адсорбционных характеристик. При этом в качестве основного режима синтеза выбрали одностадийную активацию исходного сырья.
ЭКСПЕРИМЕНТАЛЬНАЯ ЧАСТЬ
Образцы адсорбентов
Из анализа представленных выше работ по синтезу активных углей растительного происхождения при помощи физической активации в среде СО2 [5, 6, 10, 11], следует, что оптимальные температуры для активации прекурсора находятся в интервале от 750 до 850°С, где происходит наиболее интенсивное развитие структуры и объема адсорбирующих пор. Наряду с температурой, важным параметром синтеза является время выдержки карбонизата при температуре активации. В то же время, для сокращения продолжительности синтеза и количества подаваемого активатора, представляется целесообразным увеличение температуры активации выше указанных пределов.
Синтез углеродных адсорбентов в большинстве случаев осуществляется в две отдельные стадии и включает карбонизацию с получением полупродукта – карбонизата (1 стадия) и активацию уже самого полупродукта (2 стадия). Такой способ получения активных углей оправдан при больших объемах перерабатываемого сырья на специальных технологических линиях. В рамках настоящей работы предлагается рассмотреть возможность получения высокоэффективных активных углей, в одну стадию, когда ступени карбонизации и активации непрерывно связаны друг с другом: за этапом карбонизации сразу следует этап активации. При таком упрощенном подходе температура активации TА будет фактически соответствовать конечной температуре карбонизации TC.
С целью изучения механизма образования пористой структуры и определения оптимальных режимов синтеза было получено две серии образцов адсорбентов. На рис. 1 представлены типовые схемы получения образцов.
Синтез образцов серии “C” ограничивался получением карбонизатов и заключался в пиролизе СГО в среде СО2 от комнатной температуры до конечных 240, 320, 400, 750, 900 и 950°С со скоростью 20°С в минуту без изотермической выдержки и последующего охлаждения до комнатной температуры. На основе анализа пористой структуры образцов серии “C” выбирали наиболее эффективный температурный режим карбонизации (TC) исходного сырья для получения образцов серии “А”, но уже с учетом дальнейшей активации при температуре TА = TC до различной степени обгара δ по отношению к исходной массе карбонизата – от 0 до 70 мас. %. В качестве контролируемого параметра был принят массовый выход продукта по отношению к карбонизату.
Получение образцов адсорбентов осуществляли следующим образом. Скорлупу грецкого ореха из южных регионов РФ предварительно отмывали в воде и сушили в термошкафу при температуре 110°С в течение 24 ч, после чего производили дробление и рассев сырья на вибросите. Для синтеза активных углей выбирали фракцию дробленого сырья с размерами 0.5–1.5 мм.
Синтез адсорбентов осуществляли в термогравиметрическом анализаторе (ТГА) фирмы TA Instruments (модель TGA Q500) в потоке углекислого газа в одну стадию, без предварительной подготовки и обработки карбонизата. Дробленое сырье в количестве 200–250 мг укладывали в лабораторный керамический тигель, подвешивали на специальную тягу весов и опускали в трубчатую печь ТГА. В качестве активатора использовали углекислый газ по ГОСТ 8050 [18], который подавали в рабочую камеру печи с расходом 60 мл/мин на протяжении всего эксперимента. Полученные образцы адсорбентов имели вид крупнодисперсного порошка с размером гранул до 1 мм.
Исследование структурно-энергетических характеристик
Для определения структурно-энергетических характеристик полученных образцов были проведены измерения адсорбции паров азота при 77 К на установке Autosorb iQ (фирма Quantachrome Instr.).
Структурно-энергетические характеристики исследуемых адсорбентов, такие как удельный объем микропор W0, стандартную характеристическую энергию адсорбции по бензолу E0, и эффективную полуширину микропор x0 рассчитывали по методу Теории объемного заполнения микропор (ТОЗМ) на основе экспериментальных данных по адсорбции стандартного пара азота при температуре 77 К, с учетом коэффициента подобия β = 0.33 между азотом и бензолом [20]. Величину удельной поверхности SБЭТ рассчитывали в соответствии с [21]. Расчет параметров мезопористой структуры образцов, таких как объем мезопор WМЕ, удельную поверхность мезопор SМЕ осуществляли по [22].
ОБСУЖДЕНИЕ РЕЗУЛЬТАТОВ
Термогравиметрический анализ
На рис. 2а представлены характерные зависимости ТГА для образцов серии “C”, а на рис. 2б представлена ТГА-диаграмма и кривая производной dm/dτ (τ – время). Ось τ на диаграммах не представлена, так как изменение температуры шло с равным шагом по времени (20°С). ТГА-диаграммы образцов С4, С5, С7, на рис. 2a не обозначены для облегчения восприятия информации, однако они по характеру кривых полностью соответствуют свойствам ТГА представленных образцов (С1, С2, С3, С6, С8).
Рис. 2.
Диаграммы ТГА образцов из СГО серии С. (а) Диаграмма ТГА образцов, карбонизированных при температурах, °С: 240 (C1), 320 (C2), 400 (C3), 750 (C6) и 950 (C8). (б) Диаграмма ТГА образца C6 и кривая производной изменения массы по времени dm/dτ. Скорость нагрева 20°C/мин. Вертикальным пунктиром отмечены зоны реализации состояний.
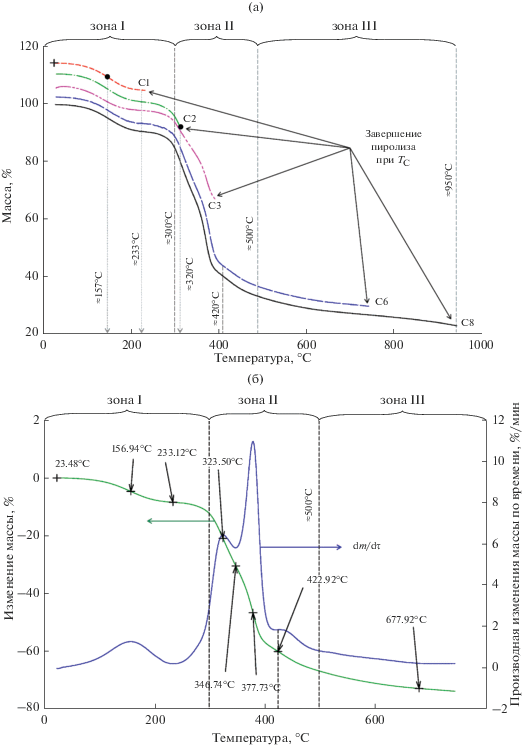
Исходя из полученных результатов зависимостей потери массы образцов от температуры карбонизации, можно выделить три характерные зоны потери массы.
Зона I – зона удаления внутриструктурной химически связанной воды и начала пиролиза с выделением высокомолекулярных смолистых соединений. При нагреве образца до температуры порядка 300°С наблюдается снижение массы на величину около 8–10 мас. %, что связано с началом дегидратации образца и пиролизом органических компонентов исходного сырья СГО. В интервале температур от комнатной до 150°С наблюдается рост скорости потери массы dm/dτ, которая достигает максимума (рис. 2б) при ~157°С и далее идет на спад до минимума при Т ~ 233°С. В переходной области между зонами I и II при температуре нагрева свыше 233°С скорость потери массы опять увеличивается вплоть до локального максимума (рис. 2б) при 320–324°С, находящегося в зоне II. Максимальная скорость потери массы в зоне I не превышает 3 мас. % в минуту.
Зоны II. При температуре около 300°С начинается участок (зона II) резкого снижения массы образца (интегральная потеря более 50 мас. %), обусловленный, очевидно, разложением высокомолекулярных соединений. В зоне II скорость пиролиза может достигать 11 мас. % в минуту при температуре около 378°C (рис. 2б). Этот участок является критическим с точки зрения массового выхода готового продукта и эффективности использования сырья.
Интенсивное снижение массы образца происходит до температур 400–420°С, после чего кривая потери массы становится более пологой, при температуре около 450°С начинается процесс интенсивной карбонизации образца, его обогащение углеродом, происходит плавный переход в зону III. В целом зона II характеризуется, как зона деструкции материала с выделением высокомолекулярных соединений и заканчивается при температуре 450–500°С.
Зона III начинается от температур 450–500°C, что связано с остаточным удалением высокомолекулярных продуктов терморазложения скорлупы и началом выделения низкомолекулярных продуктов. В интервале 500–600°C третьей зоны происходит значительное выделение низкомолекулярных летучих веществ из углеродсодержащего скелета (так называемые топохимические превращения), что может свидетельствовать о формировании регулярной пористой структуры материала.
При температуре свыше 700°C изменение веса с температурой плавно уменьшается. Остаточная масса образца на выходе из зон II и III соответственно составляет в среднем около 40 и 25 мас. % по отношению к исходной.
Таким образом, пиролиз образца C1 завершается в границах зоны I, образцов C2–C4 – в границах зон I–II, а C5–C8 – в II–III.
Структурно-энергетические характеристики
Изотермы адсорбции азота при 77 К на образцах первой серии “C” представлены на рис. 3. Из них следует, что с увеличением температуры пиролиза закономерно растет величина адсорбции азота, свидетельствующая о развитии пористости образцов.
Рис. 3.
Изотермы адсорбции азота при 77 К на образцах серии “C” – карбонизатов, полученных при температурах, °С: 1 – 240 (C1), 2 – 320 (C2), 3 – 400 (C3), 4 – 500 (C4), 5 – 600 (C5), 6 – 750 (C6), 7 – 900 (C7) и 8 – 950 (C8). Закрашенные символы – адсорбция, не закрашенные – десорбция. Сплошные линии – аппроксимация. Планки погрешности на образце C4 – 5%.
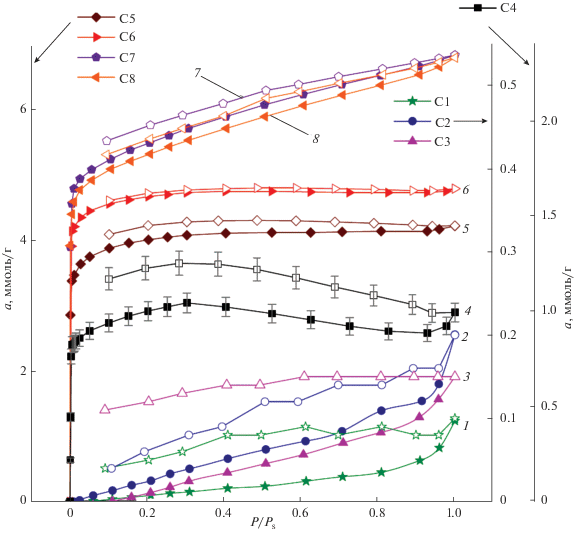
На образцах C1–C3, полученных при температурах карбонизации 240–320°С, наблюдается необратимость изотерм адсорбции и десорбции, что указывает на эффект капсулирования молекул азота в порах, при этом абсолютное значение адсорбции не превышает 0.2 ммоль/г. Изотермы азота для образцов С1–С3 в целом характеризуют их как материалы, где отсутствует сформированная микропористая структура.
При температурах свыше 600°C (образцы C5–C8), изотермы приобретают Г-образный вид, характерный для микропористых углеродных адсорбентов. Следует отметить, что увеличение температуры карбонизации материала свыше 900°C не приводит к дальнейшему росту адсорбции, сильнее проявляется петля гистерезиса, которая свидетельствует о развитии мезопористости.
Структурно-энергетические характеристики образцов углеродных адсорбентов представлены в табл. 1, откуда следует, что образец C7, полученный при температуре термообработки 900°C имеет наиболее оптимальные характеристики и обладает потенциалом для получения высокоактивного адсорбента при его последующей активации.
Таблица 1.
Структурно-энергетические характеристики образцов серии “С”
Обр. | W0, см3/г | E0, кДж/моль | х0, (Д-Р), нм | а0, (Д-Р) ммоль/г | SБЭТ, м2/г | WS, см3/г | WME, см3/г | ТС,°С |
---|---|---|---|---|---|---|---|---|
C1 | – | – | – | – | ≈0 | (0.002) | – | 240 |
C2 | – | – | – | – | ≈0 | (0.006) | – | 320 |
C3 | – | – | – | – | ≈0 | (0.003) | – | 400 |
C4 | 0.03 | 35.3 | 0.34 | 0.89 | 80 | 0.04 | 0.01 | 500 |
C5 | 0.14 | 22.2 | 0.54 | 4.03 | 330 | 0.15 | 0.01 | 600 |
C6 | 0.16 | 26.1 | 0.46 | 4.68 | 380 | 0.17 | 0.01 | 750 |
C7 | 0.19 | 26.7 | 0.45 | 5.35 | 440 | 0.24 | 005 | 900 |
C8 | 0.18 | 25.5 | 0.47 | 5.15 | 430 | 0.24 | 0.06 | 950 |
С целью наглядного представления механизма развития пористой структуры карбонизатов были построены зависимости W0, WS, от температуры карбонизации TC образцов – рис. 4.
Рис. 4.
Зависимости удельного объема микропор W0, полного объема пор WS, а также средней эффективной полуширины микропор x0 образцов от температуры карбонизации (обжига) исходного сырья СГО в интервале 240–950°C – образцы серии “C”. Скорость нагрева 20°C/мин.
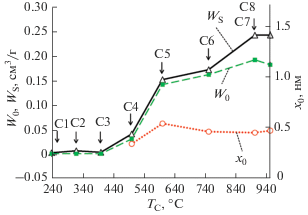
Представленные данные свидетельствуют о том, что при температурах ниже 400°C (образцы C1–C3) образования пористой структуры практически не происходит. При температурах свыше 500°C процесс формирования микропористости активизируется, формируются поры стабильной эффективной ширины, происходит значительная усадка материала. В интервале температур 500–600°C зоны III, происходит значительное выделение низкомолекулярных летучих веществ из углеродсодержащего карбонизата (так называемые топохимические превращения), что обеспечивает вскрытие микропор и приводит к резкому увеличению объема микропор, а также к увеличению их размеров.
Дальнейшее увеличение температуры от 600 до 750°C приводит к незначительному повышению объема микропор и усадке углеродсодержащего карбонизата, вследствие чего микропоры несколько уменьшаются в размерах. Одновременно с микропорами в области температур пиролиза, превышающих 600°C, происходит формирование мезопористой структуры.
В диапазоне температур 750–950°C размеры микропор остаются практически постоянными, но повышается объем сорбционного пространства за счет некоторого увеличения объема микропор и более заметного роста объема мезопор.
Наиболее оптимальное сочетание структурно-энергетических характеристик наблюдается у образца C7. Он обладает наибольшей величиной объема микропор 0.19 см3/г при высокой характеристической энергии адсорбции на уровне 26 кДж/моль и полуширине микропор 0.47 нм.
Исходя из анализа полученных данных, для дальнейшей работы по активации углеродных адсорбентов был выбран режим термообработки для карбонизата C7, полученного при температуре 900°С.
Термогравиметрический анализ
Образцы серии “А” были подвергнуты активации в потоке СО2 с расходом 60 мл/мин при температуре 900°C до разных степеней обгара от 10 до 70% сразу после завершения процесса карбонизации. Таким образом, синтез адсорбентов происходил в упрощенном режиме в одну ступень, что может положительно сказаться при разработке малотоннажной технологии производства углеродных адсорбентов, локального типа.
На рис. 5, в качестве примера представлена развернутая диаграмма термогравиметрического анализа (ТГА) образца адсорбента из СГО, полученного посредством непрерывного подъема температуры исходного сырья до температуры 900°С со скоростью 20°С/мин в среде СО2 с последующей выдержкой при этой температуре (активацией) до степени обгара на уровне 43 мас. % от исходной массы карбонизата (образец А5). В целом ТГА-диаграмма образца А5 в области первичной карбонизации (температуры до 900°C) может быть охарактеризована зонами I–III, как и для образцов серии “С”.
Рис. 5.
Диаграмма ТГА образца А5, полученного в среде CO2 при реализации одностадийного синтеза адсорбента.
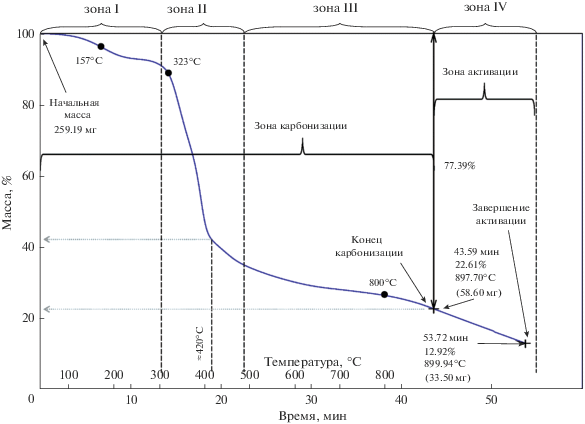
Одностадийный синтез углеродного адсорбента (рис. 5) характеризуется следующими условиями его реализации:
1. Карбонизат получен в интервале температур от комнатной до 900°C (1173 К) со скоростью подъема температуры 20°C/мин в среде CO2.
2. Последующая активация полупродукта в среде CO2 при этой же температуре до степени обгара около 43 мас. %.
3. Масса исходного образца – 259.19 мг; масса карбонизата – 58.60 мг; масса активированного образца (готового продукта) – 33.50 мг.
Из рис. 5 следует, что помимо трех характерных зон изменения массы прекурсора, которые вместе формируют общую зону карбонизации, наблюдается дополнительная зона IV, которая соответствует зоне активации. При температуре свыше 800°С скорость потери массы увеличивается, так как завершается процесс формирования первичной пористости и начинается этап активации образца с развитием объема порового пространства непосредственно в углеродной матрице.
К моменту выхода процесса пиролиза на изотермический участок активации при 900°С (зона IV), остаточная масса материала (карбонизата) по отношению к исходному сырью составляет около 22–23%. Далее осуществляется активация карбонизата в соответствии с формулой:
(1)
$2{\text{C}} + {\text{C}}{{{\text{O}}}_{2}}\xrightarrow{{T = 900^\circ {\text{C}}}}{\text{C}} + {\text{ }}2{\text{CO}}{\text{.}}$Изотермический участок активации карбонизата при 900°С имеет линейный вид. Массовый выход готового продукта составил 33.50 мг, что составляет 12.92 и 57.17% по отношению к исходному сырью СГО и карбонизату (обгар около 43 мас. %) соответственно.
Структурно-энергетические характеристики и формирование пористой структуры
На рис. 6 представлены экспериментальные изотермы адсорбции азота на углеродных адсорбентах серии “A”, откуда следует, что с увеличением степени активации образцов закономерно увеличивается величина адсорбции из-за развития объема микропор.
Рис. 6.
Изотермы адсорбции азота при 77 К на образцах адсорбентов серии “A” c различной степенью обгара (активации) исходного карбонизата, мас. %: 1 – 0 (А1/C7), 2 – 10 (А2), 3 – 20 (А3), 4 – 30 (А4), 5 – 40 (А5), 6 – 70 (А6).
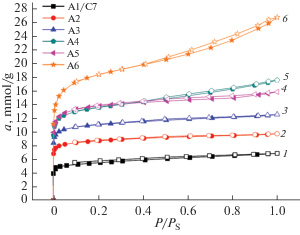
Изотермы адсорбции качественно имеют Г-образный вид с резким подъемом в области начальных заполнений, что соответствует проявлению адсорбции в микропористой структуре образцов. Из табл. 2 следует, что при увеличении степени обгара δ от 0 до 30% (образцы А1/C7-А4), адсорбция азота растет с ростом степени обгара. Однако в дальнейшем адсорбционная активность а0 образцов А4 и А5, которые синтезированы при обгарах 30 и 40% соответственно, практически одинакова, объемы микропор близки W0 (0.45–0.47 см3/г), но резко уменьшается объем WМЕ и поверхность SME мезопор. Максимальной адсорбцией обладает образец А6. Для образцов со степенью активации свыше 30% наблюдается петля гистерезиса, которая свидетельствует о развитии мезопор.
Таблица 2.
Структурно-энергетические характеристики образцов серии “А”
Обр. | W0, см3/г | E0, кДж/моль | х0, (Д-Р), нм | а0, (Д-Р) ммоль/г | SБЭТ, м2/г | WS, см3/г | SME, м2/г | WME, см3/г | δ, мас. % | ТA = ТС, °С |
---|---|---|---|---|---|---|---|---|---|---|
А1/C7 | 0.19 | 25.7 | 0.47 | 5.35 | 440 | 0.24 | − | 0.05 | 0 | 900 |
А2 | 0.30 | 27.0 | 0.44 | 8.49 | 705 | 0.34 | 21 | 0.04 | 8 | |
А3 | 0.38 | 24.9 | 0.48 | 10.86 | 900 | 0.43 | 31 | 0.05 | 19 | |
А4 | 0.45 | 23.6 | 0.51 | 12.97 | 1100 | 0.61 | 87 | 0.16 | 30 | |
А5 | 0.47 | 21.8 | 0.55 | 13.58 | 1120 | 0.55 | 40 | 0.08 | 43 | |
А6 | 0.59 | 20.3 | 0.59 | 16.95 | 1490 | 0.92 | 173 | 0.33 | 70 |
На рис. 7 представлены зависимости ключевых структурно-энергетических характеристик синтезированных образцов серии “А” от степени обгара (активации) δ.
Рис. 7.
Зависимости удельного объема микропор, объема сорбирующих пор и средней эффективной полуширины микропор (а), а также удельной поверхности по БЭТ и стандартной характеристической энергии адсорбции (б) образцов на основе скорлупы грецких орехов от степени обгара (активации) по отношению к исходному карбонизату в потоке CO2 при температуре 900 °С (1173 К).
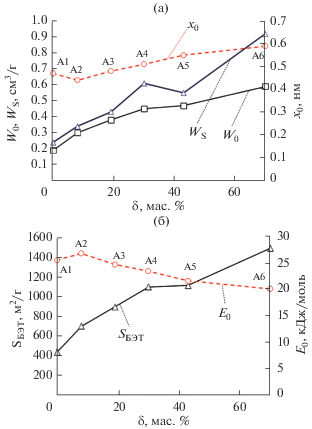
Исходя из характера зависимостей на рис. 7а, следует, что с увеличением δ, закономерно растет объем микропор образцов с 0.19 до 0.59 см3/г, то есть практически в 3 раза. Похожая по характеру зависимость наблюдается для величины поверхности по БЭТ, которая растет с 440 до 1490 см2/г (рис. 7б).
Что касается средней эффективной полуширины микропор, то она меняется от 0.44 до 0.59 нм во всем интервале степени активации, то есть в пределах 30% от начального значения. Этот эффект является положительным с точки зрения целевого использования адсорбента для адсорбции метана, так как наиболее эффективная ширина микропор для сорбции этого газа (около 1.1–1.2 нм) приходится как раз на максимум объема микропор [23]. При этом незначительно меняется и величина характеристической энергии адсорбции E0 (25.7 → 20.3 кДж/моль), что свидетельствует о сохранении высоких энергий взаимодействия в системе “адсорбент–адсорбат” – рис. 7б. На рис. 7а также идентифицируется ступень снижения эффективной полуширины микропор с 0.47 до 0.44 в области обгара 0–10 мас. %, что может быть интерпретировано начальной усадкой материала.
На рис. 8 представлены сравнительные зависимости развития суммарного порового пространства и объема микропор от обратной величины массового выхода готового адсорбента, которая определяется по соотношению:
(2)
$\Omega = {1 \mathord{\left/ {\vphantom {1 {\left( {1{\text{ }}--{\delta \mathord{\left/ {\vphantom {\delta {100}}} \right. \kern-0em} {100}}} \right).~}}} \right. \kern-0em} {\left( {1{\text{ }}--{\delta \mathord{\left/ {\vphantom {\delta {100}}} \right. \kern-0em} {100}}} \right).~}}$Рис. 8.
Зависимости удельного объема микропор и полного объема пор образцов на основе СГО от обратной величины массового выхода готового адсорбента. Планки – относительная погрешность 10%.
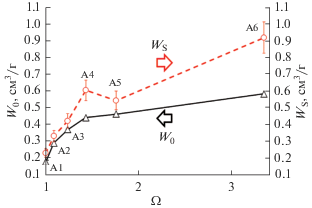
Наиболее интенсивный рост W0 наблюдается в области величин Ω от 1 до 1.5 (δ от 0 до 30 мас. %), что обусловлено выгоранием аморфного углерода, уменьшением размера углеродных нанокристаллитов и, как следствие, формировании микропор в пространстве между нанокристаллами углерода [24]. Далее рост объема микропор замедляется, так как интенсифицируется процесс формирования мезопористости (δ свыше 30 мас. %).
Исходя из анализа полученных данных следует, что адсорбент А6, активированный до степени обгара карбонизата 70%, имеет наиболее выдающиеся структурно-энергетические характеристики. Среди них следует отметить высокий объем микропор 0.59 см3/г и полуширину микропор, равную 0.59 нм, которые потенциально могут обеспечить оптимальную энергию взаимодействия “адсорбент–адсорбат” и обеспечить максимальную плотность метана в порах. Кроме того, этот адсорбент обладает существенной долей мезопор, которая может оказывать положительный эффект с точки зрения адсорбции метана в докритической области и обеспечить дополнительный вклад в адсорбцию за счет капиллярной конденсации. В связи с этим, для предварительной оценки адсорбционных свойств по метану был выбран образец А6. К недостатку образца А6 следует отнести низкий массовый выход готового адсорбента, величина которого не превышает 10%.
Адсорбция паров СПГ
В работе [17] было показано, что углеродные адсорбенты растительного происхождения обладают высоким потенциалом для использования в системах адсорбционного улавливания и хранения паров СПГ. В качестве возможных условий функционирования адсорбционных систем улавливания приводятся температурные режимы 120, 160 и 180 К, а также давления 2 бар – для 120 К и 6 бар для 160 и 180 К [17, 25, 26]. Аналогичные условия для оценки адсорбционных свойств полученного адсорбента А6 были приняты и в настоящей работе.
Для оценки адсорбционной активности синтезированных адсорбентов к метану, был использован подход Теории объемного заполнения микропор, который позволяет с высокой точностью рассчитывать адсорбционные равновесия [17, 27, 28] по известному уравнению Дубинина–Радушкевича:
(3)
$a = {{a}_{0}}\exp \left[ { - {{{\left( {\frac{{RT\ln \left( {{{{{f}_{s}}} \mathord{\left/ {\vphantom {{{{f}_{s}}} f}} \right. \kern-0em} f}} \right)}}{{\beta {{E}_{0}}}}} \right)}}^{2}}} \right],$Величину предельной адсорбции a0 при температуре T рассчитывают по уравнению Дубинина–Николаева:
где $a_{0}^{0}$ – предельная адсорбция в ммоль/г при температуре кипения T0; α – термический коэффициент предельной адсорбции, К–1. В соответствии с [29], при адсорбции метана в микропористых активных углях в интервале от температуры кипения до критической температуры α = 1.52 × 10–3 К–1.Свойства метана, использованные для расчетов адсорбционных равновесий: молекулярная масса М = 16.0426 г/моль; температура кипения Тb = 111.66 К; критическая температура Тсr = = 190.77 К; критическое давление pсr = 4.641 МПа [19]. В опытах использовали метан чистотой 99.999%.
На рис. 9 представлены расчетные изотермы адсорбции метана на адсорбенте А6 при температурах 120, 160 и 178 К, а также экспериментальная рассчитанная по ТОЗМ изотерма адсорбции метана на коммерческом адсорбенте АУ-1 из скорлупы кокосового ореха, который имеет сходные параметры пористой структуры [17, 30]: W0 = 0.62 см3/г, x0 = 0.61 нм, E0 = 19.7 кДж/моль.
Рис. 9.
Зависимости адсорбции метана от давления на адсорбенте А6, рассчитанные по (3) при температурах, К: 120 (1), 160 (2) и 178 (3), а также на коммерческом адсорбенте АУ-1 при 178 К (4, 5). Кривая 4 – экспериментальные данные по адсорбции СН4 на адсорбенте АУ-1 [30]; 5 – расчет по (3). Планки относительной погрешности расчета по ТОЗМ для системы “СН4-АУ-1” – 15%.
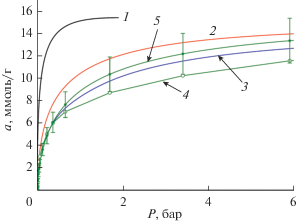
Рассчитанная по ТОЗМ адсорбция метана на коммерческом АУ-1 (рис. 9) демонстрирует завышенные значения по сравнению с экспериментальными величинами в области давлений свыше 1 бар. Тем не менее, расхождение эксперимента и расчета не превышает 15%, что позволяет использовать теорию для предварительной оценки адсорбционных равновесий метана.
Результаты оценки величин адсорбции метана, представленные на рис. 9, позволяют сделать вывод о том, что при 178 К система на основе А6 в первом приближении немного уступает системе на основе коммерческого активного угля АУ-1 по величине адсорбции метана, в основном за счет меньшего объема микропор, и достигает 12 ммоль/г. Однако при практическом использовании адсорбентов важны характеристики объемной (насыпной) плотности адсорбентов, которая может быть оптимизированa за счет использования специального гранулометрического состава. При температурах 120 и 160 К максимальные величины адсорбции метана в А6 в указанном интервале давлений (2–6 бар) соответствуют 15 и 13.5 ммоль/г.
ВЫВОДЫ
Разработана концепция одностадийного синтеза микропористых активных углей из скорлупы грецкого ореха при физической газовой активации в атмосфере СО2.
Оптимальная температура для развития исходной пористости соответствует 900°С при скорости нагрева 20С/мин. Активация в этих условиях позволяет достигать степеней обгара до 70 мас. % и формировать оптимальную пористую структуру для аккумулирования природного газа метана в системах СПГ. Полученные данные свидетельствуют о том, что эффективная пористость формируется только при условиях высокой степени активации не менее 70 мас. %. При этом полученный адсорбент имеет значительный объем микропор 0.59 см3/г и полуширину микропор 0.59 нм, которая потенциально может обеспечивать высокую плотность метана в порах [23]. Кроме того, этот адсорбент имеет некоторую долю мезопор, которая может оказывать положительный эффект с точки зрения адсорбции метана в докритической области и обеспечить дополнительный вклад в адсорбцию за счет капиллярной конденсации.
Адсорбция метана при температурах 120, 160 и 178 К и давлениях 2–6 бар достигает 15, 13.5 и 12 ммоль/г соответственно, что позволяет полученному адсорбенту конкурировать с коммерческими аналогами.
Работа выполнена в соответствии с государственным заданием (Проект № 01201353185) и планом Научного совета РАН по физической химии (тема № 20-03-460–01) с использованием оборудования Центра коллективного пользования ИФХЭ РАН.
Список литературы
Men’shchikov I.E., Fomkin A.A., Tsivadze A.Y., Shkolin A.V., Strizhenov E.M., Khozina E.V. // Adsorption. 2017. V. 23. P. 327–339.
Фенелонов В.Б. Пористый углерод. Новосибирск: Ин-т катализа, 1995. 513 с.
Агроинвестор [Электронный ресурс] // URL: https://www.agroinvestor.ru/markets/news/30896-dolya-rossii-v-mirovom-sbore-orekhov-ne-prevyshaet-1/
Jin-Wha Kim, Myoung-Hoi Sohn, Dong-Su Kim, Seung-Man Sohn, Young-Shik Kwon // J. Hazardous Materials. 2001. V. 85. P. 301–315.
Wartelle L.H., Marshall W.E. // J. Chemical Technology and Biotechnology. 2001. V. 76. P. 451–455.
Lupascu T., Dranca I., Popa V.T., Vass M. // J. Thermal Analysis and Calorimetry. 2001. V. 63. P. 855–863.
Vicente Gómez-Serrano, Eduardo M. Cuerda-Correa, M. Carmen Fernández-González, María F. Alexandre-Franco, Antonio Macías-García // Smart Materials and Structures. 2005. V. 14. P. 363–368.
Martínez M.L., Torres M.M., Guzmán C.A., Maestri D.M. // Industrial Crops and Products. 2006. V. 23. P. 23–28.
Kambarova G.B., Sarymsakov Sh. // Solid Fuel Chemistry. 2008. V. 42. P. 183–186.
Juan F. González, Silvia Román, Carmen M. González-García, Valente Nabais J.M., Luis Ortiz A. // Industrial & Engineering Chemistry Research. 2009. V. 48. P. 7474–7481.
Piotr Nowicki, Robert Pietrzak, Helena Wachowska // Catalysis Today. 2010. V. 150. P. 107–114.
Juan Yang, Keqiang Qiu // Chemical Engineering J. 2010. V. 165. P. 209–217.
Zabihi M., Haghighi Asl A., Ahmadpour A. // J. Hazardous Materials. 2010. V. 174. P. 251–256.
Wookeun Bae, Jongho Kim, Jinwook Chung // J. Air & Waste Management Association. 2014. V. 64. P. 879–886.
Qiongfen Yu, Ming Li, Ping Ning, Honghong Yi, Xiaolong Tang // Separation Science and Technology. 2014. V. 49. P. 2366–2375.
Men’shchikov I.E., Fomkin A.A., Shkolin A.V., Yakovlev V.Y., Khozina E.V. // Russian Chemical Bulletin. 2018. V. 67. P. 1814–1822.
Чугаев С.С., Фомкин А.А., Меньщиков И.Е., Стриженов Е.М., Школин А.В. // Физикохимия поверхности и защита материалов. Т. 56, № 5, 2020. (В печати).
ГОСТ 8050–85. Двуокись углерода газообразная и жидкая. Технические условия. М.: Издательство стандартов, 1995.
Lemmon E.W., Huber M.L., McLinden M.O. NIST Standard Reference Database 23: Reference Fluid Thermodynamic and Transport Properties-REFPROP. Version 9.1. 2013.
Dubinin M.M. // Progress in Surface Membrane Science. 1975, V. 9. P. 1–70.
Brunauer S., Emmett P. H., Teller E. // J. Am. Chem. Soc. 1938. V. 60. I. 2. P. 309–319.
Кельцев Н.В. Основы адсорбционной техники. М.: Химия, 1976. 511 с.
Anuchin K.M., Fomkin A.A., Korotych A.P., Tolmachev A.M. // Protection of Metals and Physical Chemistry of Surfaces. 2014. V. 50. P. 173–177.
Dubinin M.M. // Carbon. 1989. V. 27. P. 457–467.
Sibnath Kayal, Baichuan Sun, Anutosh Chakraborty // Energy. 2015. V. 91. P. 772–781.
Seo-Yul Kim, Jo Hong Kang, Seung-Ik Kim, Youn-Sang Bae // Chemical Engineering J. 2019. V. 365. P. 242–248.
Men’shchikov I.E., Fomkin A.A., Tsivadze A.Yu., Shkolin A.V., Strizhenov E.M., Pulin A.L. // Protection of Metals and Physical Chemistry of Surfaces. 2015. V. 51. P. 493–498.
Men’shchikov I.E., Fomkin A.A., Arabei A.B., Shkolin A.V., Strizhenov E.M. // Protection of Metals and Physical Chemistry of Surfaces. 2016. V. 52. P. 575–580.
Shkolin A.V., Fomkin A.A. // Russian Chemical Bulletin. 2009. V. 58. P. 717–721.
Strizhenov E.M., Shkolin A.V., Fomkin A.A., Sinitsyn V.A., Zherdev A.A., Smirnov I.A., Pulin A.L. // Protection of Metals and Physical Chemistry of Surfaces. 2014. V. 50. P. 15–21.
Дополнительные материалы отсутствуют.
Инструменты
Физикохимия поверхности и защита материалов