Физикохимия поверхности и защита материалов, 2020, T. 56, № 6, стр. 640-650
Влияние H, W, H/E, H3/E 2, структуры и химического состава на стойкость покрытий Ti–B–(N), Mo–B–(N), Cr–B–(N) и Zr–B–(N) к циклическим ударным воздействиям
Ф. В. Кирюханцев-Корнеев 1, *, А. Д. Сытченко 1
1 Национальный исследовательский технологический университет “МИСиС”
119049 Москва, Ленинский проспект, 4, Россия
* E-mail: kiruhancev-korneev@yandex.ru
Поступила в редакцию 29.05.2020
После доработки 05.06.2020
Принята к публикации 15.06.2020
Аннотация
Покрытия на основе боридов переходных металлов (Ti, Mo, Cr, Zr) были получены с помощью магнетронного распыления керамических мишеней в газовых средах Ar и Ar–15% N2. Испытания на стойкость покрытий к циклическим ударным воздействиям выполнены шариком из WC–6% Co при нагрузке 1 кН для 105 циклов с использованием импакт-тестера CemeCon. Проведен анализ взаимосвязи между характеристиками структуры, химическим составом, механическими и упруго-пластическими свойствами, геометрическими параметрами и характером разрушения покрытий.
ВВЕДЕНИЕ
Бориды переходных металлов являются перспективными материалами для их использования в качестве защитных покрытий для металлообрабатывающего инструмента [1–4]. Так, например компания CERATIZIT создала наносимые по технологии CVD покрытия TiB2 и TiB2–TiN для резания труднообрабатываемых материалов [5]. Фирмой PLATIT разработаны и внедрены в производство составы на основе TiB2 [6], обладающие твердостью до 30 ГПа, коэффициентом трения на уровне 0.35 и рабочей температурой до 600°С. А также боросодержащие покрытия AlCrBN, с повышенной твердостью 44 ГПа и жаростойкостью 900°С [7]. Показан положительный эффект применения покрытий на основе диборида хрома на операциях фрезерования и точения [8, 9]. Апробировано использование боридных покрытий для повышения срока службы пресс-форм для обработки алюминия [10]. Боридные покрытия могут быть использованы также для повышения ресурса работы тяжело нагруженных узлов трения [11], топливных ячеек [12], деталей авиакосмической промышленности [13] и т.д. благодаря высоким значениям твердости, износо-, жаро- и коррозионной стойкости, диффузионно-барьерным свойствам, низкому коэффициенту трения. За последние два десятилетия были изучены покрытия в системах Ta–B [14, 15], V–B [1, 16], Ti–B [5, 6, 17], Zr–B [18, 19], Hf–B [20], W–B [21], Ru–B [22] и др.
Легирование боридных покрытий азотом позволяет сформировать нанокомпозиционную структуру, состоящую из наноразмерных кристаллитов борида и/или нитрида переходного металла и аморфных прослоек на основе нитрида бора, и характеризующуюся уникальным сочетанием характеристик: твердостью свыше 40 ГПа, упругим восстановлением 70–90%, термической стабильностью и жаростойкостью до 900–1000°С, а также повышенные трибологические свойства и коррозионную стойкость [23]. Можно отметить работы по боронитридным покрытиям в системах Zr–B–N [24], Hf–B–N [25], V–B–N [26], Ti–B–N [23, 24, 27] и Cr–B–N [8, 28–30], в которых показано, что управление структурой, механическими свойствами и износостойкостью может осуществляться за счет варьирования содержания азота в покрытиях.
Важной характеристикой с точки зрения практического применения покрытий является адгезионная/когезионная прочность, трещиностойкость и износостойкость в условиях циклических ударно-динамическим воздействий [31–33]. Для определения этих характеристик применяются импакт-тестеры различных марок, например Impact Tester CemeCon [34, 35]. Литературные данные о циклических ударных испытаниях боридных покрытий ограничены. Можно отметить статью [36] по исследованию покрытий на основе CoB, а также [37] посвященную покрытиям Ti–B–N и Ti–Al–B–N. Важными характеристиками, позволяющими прогнозировать поведение покрытий в условиях трибологического воздействия могут быть твердость (H), упругое восстановление (W), индекс пластичности (H/E, где E – модуль упругости), сопротивление пластической деформации разрушения (H 3/E 2) [38–40]. Однако в ряде случаев более важным для обеспечения высоких свойств является химический, фазовый состав и структура покрытий, а также состав продуктов износа [8, 30]. Вопрос взаимосвязи указанных характеристик и стойкости покрытий к разрушению в условиях ударных воздействий требует дополнительного изучения.
Целью данной работы является проведение циклических ударно-динамических испытаний двух и трехкомпонентных покрытий Ме–B–(N) (Me = Mo, Cr, Ti, Zr), установление взаимосвязи между их составом, параметрами структуры, механическими и упруго-пластическими характеристиками и стойкостью к такому типу воздействий.
МЕТОДИКА ЭКСПЕРИМЕНТА
Катоды MoB, TiB, TiB2, ZrB2, CrB2 диаметром 120 мм и толщиной 4–9 мм были получены методом самораспространяющегося высокотемпературного синтеза (СВС) из элементных порошков металлов и бора. Магнетронное распыление катодов проводилось в режиме постоянного тока с использованием источника питания Pinnacle Plus 5 × 5 (Advanced Energy) при силе тока и напряжении 2 А и 500 В. Принципиальная схема установки для осаждения покрытий представлена в [41]. Распыление мишеней проводилось в среде Ar и Ar + 15% N2 при давлении рабочего газа 0.2 Па. В качестве подложек использовались диски из твердого сплава ВК6М. Время осаждения составляло 40 мин. Осуществлялась ультразвуковая очистка подложек в изопропиловом спирте и последующая – травлением в вакууме ионами Ar+ с энергией 1.5–2 кэВ в течение 10 мин с помощью ионного источника щелевого типа. Данные о составе, структуре и свойствах покрытий были получены с использованием методов оптической эмиссионной спектроскопии тлеющего разряда [42] (PROFILER-2 Horiba JY), растровой электронной микроскопии (Hitachi S4800), рентгенофазового анализа (Bruker D8), наноиндентирования (Nano-Hardness Tester CSM Instruments), трибо-теста “стержень-диск” (Tribometer CSM Instruments), оптической профилометрии (Wyko-1100NT Veeco), ступенчатых отжигов (SNOL 7.2/1200 Umega). Более детально методы оценки механических и трибологических свойств покрытий описаны в работе [16]. Результаты исследований сведены в табл. 1 и 2 [43]. В настоящей работе основное внимание уделено анализу взаимосвязи ранее определенных параметров структуры и свойств с результатами ударно-динамических испытаний.
Таблица 1.
Состав и структура покрытий
№ | Мишень | N2, % | Концентрация | Структура | |||||||
---|---|---|---|---|---|---|---|---|---|---|---|
Me, ат. % | B, ат. % | N, ат. % | Me/B | Me/N | Me/(B,N) | фазы | CS, нм | текстура | |||
1 | TiB | 0 | 58 ± 3 | 42 ± 2 | – | 1.381 | – | 1.381 | o-TiB | <2 | (201) |
2 | 15 | 48 ± 2 | 34 ± 2 | 18 ± 3 | 1.412 | 2.667 | 0.923 | o-TiB | <2 | (110) | |
3 | TiB2 | 0 | 35 ± 2 | 65 ± 3 | – | 0.538 | – | 0.538 | h-TiB2 | <13 | (001) |
4 | 15 | 29 ± 2 | 55 ± 2 | 16 ± 1 | 0.527 | 1.813 | 0.408 | h-TiB2 | <3 | (100) | |
5 | MoB | 0 | 51 ± 1 | 49 ± 2 | – | 1.041 | – | 1.041 | t-MoB | <1 | (211) |
6 | 15 | 47 ± 2 | 43 ± 2 | 10 ± 2 | 1.093 | 4.700 | 0.887 | t-MoB | <1 | (211) | |
7 | CrB2 | 0 | 32 ± 2 | 68 ± 2 | – | 0.471 | – | 0.471 | h-CrB2 | <3 | (001) |
8 | 15 | 31 ± 2 | 57 ± 3 | 12 ± 2 | 0.544 | 2.583 | 0.449 | h-CrB2 | <2 | (101) | |
9 | ZrB2 | 0 | 24 ± 2 | 76 ± 2 | – | 0.316 | – | 0.316 | h-ZrB2 | <11 | (001) |
10 | 15 | 18 ± 2 | 61 ± 2 | 21 ± 2 | 0.295 | 0.857 | 0.220 | h-ZrB2 | <2 | (100) |
Таблица 2.
Свойства покрытий
№ | Мишень | N2, % | Механические свойства | Трибологические свойства | T, °C | |||||
---|---|---|---|---|---|---|---|---|---|---|
Н, ГПа | E, ГПа | W, % | H/E | H3/E2, ГПа | WR × 10–6, мм3 Н–1м–1 | FC | ||||
1 | TiB | 0 | 23 | 270 | 53 | 0.085 | 0.167 | 16.1 | 0.8 | 800 |
2 | 15 | 43 | 390 | 72 | 0.110 | 0.523 | 1.1 | 0.5 | 700 | |
3 | TiB2 | 0 | 61 | 420 | 64 | 0.145 | 1.287 | 0.9 | 0.5 | 600 |
4 | 15 | 23 | 250 | 58 | 0.092 | 0.195 | 1.0 | 0.5 | 600 | |
5 | MoB | 0 | 27 | 330 | 50 | 0.082 | 0.181 | 21.1 | 0.7 | 600 |
6 | 15 | 22 | 290 | 48 | 0.076 | 0.127 | 0.8 | 0.4 | 600 | |
7 | CrB2 | 0 | 39 | 380 | 61 | 0.103 | 0.411 | 18.9 | 0.8 | 900 |
8 | 15 | 14 | 150 | 54 | 0.093 | 0.122 | 1.2 | 0.3 | >1000 | |
9 | ZrB2 | 0 | 22 | 342 | 62 | 0.064 | 0.091 | 8.2 | 0.9 | 600 |
10 | 15 | 23 | 266 | 72 | 0.086 | 0.172 | 1.3 | 0.4 | 600 |
Испытание на циклическое ударно-динамическое воздействие проводили на приборе Impact Tester CemeCon (Германия, Греция). Принцип действия прибора основан на ударном циклическом воздействии на исследуемую поверхность шариком-индентором с фиксированной нагрузкой (100–1500 Н) и частотой (50 Гц). В результате нагружения возникает деформация материала (упругая или пластическая), вследствие чего образуется отпечаток (кратер) и наблюдается когезионное или адгезионное разрушение покрытия. Impact Tester состоит из подвижного блока (1), поршня (2), на котором закреплен держатель для шарика-индентора (3), пьезодатчика (4), двухпозиционного столика (5) для установки образцов (6), а также модуля компьютерного управления (рис. 1а). Подвижный блок в свою очередь состоит из постоянного магнита (1), цилиндрической пружины (2) и магнитной катушки (3) (рис. 1б). При подаче тока на магнитную катушку возникает магнитное поле, в результате чего сердечник опускается и осуществляется удар по образцу. После контакта с образцом пьезодатчик срабатывает на отключение подачи тока на катушку и сердечник возвращается обратно. Таким образом осуществляется колебательное движение подвижного блока. Необходимая нагрузка устанавливается за счет перемещения всего блока установки по вертикальной оси. Во время испытания сила удара постоянно контролируется с помощью пьезодатчика. Колеблющийся шарик-индентор последовательно проникает в покрытый образец с постоянной максимальной силой. Управление установкой осуществляется с помощью модуля компьютерного управления, который состоит из персонального компьютера, оснащенного пропорционально-интегральным и дифференциальным контролером. Параметры испытания задаются с помощью программного обеспечения ITControl (CemeCon) путем варьирования двух основных характеристик – сила удара и количество ударов. Исследуемые покрытия подвергались испытаниям, состоящим из 105 ударов в условиях сухого воздуха при приложенной нагрузке 1000 Н. В качестве контр-тела использовали шарик из твердого сплава WC–Co диаметром 5 мм. Кратеры после испытаний на циклические ударно-динамическое нагружение исследовали с помощью оптического профилометра.
ПОЛУЧЕННЫЕ РЕЗУЛЬТАТЫ
Данные исследований структуры покрытий, среди которых концентрации металлов (Me), бора и азота, соотношения Me/B, Me/N, Me/(B,N), фазовый состав, средний размер (CS) и преимущественная ориентировка кристаллитов основной фазы представлены в табл. 1. Результаты определения свойств, таких как твердость (H), модуль упругости (E), упругое восстановление (W), индекс пластичности (H/E), сопротивление материала пластичной деформации разрушения (H 3/E 2), коэффициент трения (FC), скорость износа (WR), максимальная рабочая температура (T), до которой покрытия сопротивляются окислению на воздухе, сведены в табл. 2. Геометрические параметры кратеров после ударных испытаний, глубина (h), диаметр (d) и объем (V) кратера отражены в табл. 3. В ней также приводятся толщины покрытий (t), а также отношения h/t.
Таблица 3.
Данные циклических ударных испытаний покрытий
№ | Мишень | N2, % | t, мкм | Параметры кратера | h/t | ||
---|---|---|---|---|---|---|---|
h, мкм | d, мкм | V × 103, мкм3 | |||||
1 | TiB | 0 | 1.9 | 2 | 400 | 1.7 | 1.05 |
2 | 15 | 2.7 | 20 | 720 | 302.5 | 7.40 | |
3 | TiB2 | 0 | 2.1 | 3.5 | 610 | 8.0 | 1.67 |
4 | 15 | 6.4 | 3.3 | 575 | 6.5 | 0.52 | |
5 | MoB | 0 | 4.7 | 6 | 675 | 25.8 | 1.28 |
6 | 15 | 5.8 | 3 | 430 | 4.1 | 0.52 | |
7 | CrB2 | 0 | 3.3 | 9.3 | 560 | 51.3 | 2.81 |
8 | 15 | 4 | 2.5 | 500 | 3.3 | 0.62 | |
9 | ZrB2 | 0 | 2.1 | 7.5 | 537 | 32.0 | 3.57 |
10 | 15 | 2.7 | 17 | 675 | 205.2 | 6.30 |
3D профили отпечатков после ударно-динамических испытаний показаны на рис. 2. В случае покрытия 1 (TiB) наблюдается минимальная из всех исследованных покрытий зона износа, она имеет неравномерную форму, содержит кольцевую трещину и скопления продуктов износа. Покрытие 2 с азотом имеет больший диаметр кратера, у центра сконцентрированы области, связанные с износом глубже подложки, обнаруживаются кольцевые сколы покрытия по периметру кратера. В случае покрытия 3 (TiB) наблюдается хрупкое разрушение, границы кратера образуют вертикальные стенки, дно кратера имеет плоскую форму. Заметен дефект, связанный с локальным выкрашиванием подложки. Отличительной особенностью является очень большой диаметр зоны разрушения. При переходе к реакционному покрытию 4 системы Ti–B–N, происходит заметное уменьшение диаметра кратера, стенки имеют покатую форму. В случае покрытия 5 Mo–B наблюдается ситуация, схожая с данными для образца 3 TiB, – хрупкое разрушение и большой диаметр кратера. На стенке кратера заметна столбчатая структура покрытий, т.е. разрушение идет по межзеренным границам грубых колонных зерен. Переход к реакционному режиму (покрытие 6 MoBN) сопровождается изменением характера разрушения. Глубина проникновения и диаметр кратера заметно снижаются, в его центре наблюдаются продукты износа, а на периферии образуется сетка радиальных трещин. Покрытия 7 (CrB) и 8 (CrBN) имели близкие диаметры кратеров, однако для нереакционного покрытия в центре заметно интенсивное разрушение, тогда как азотсодержащие покрытие имеет ровное дно, по краям которого скапливаются продукты износа. Покрытие 9 (ZrB) показало хрупкое разрушение, аналогичное наблюдаемому для нереакционных боридных покрытий 3 и 5. Введение азота (покрытие 10 ZrBN) не повлияло на характер разрушения существенно, кроме того, наблюдался интенсивный износ в центре кратера, по-видимому, уже самой подложки, что можно объяснить малой толщиной покрытия.
Связывая структурные особенности покрытий и их поведение можно заключить, что нереакционные покрытия 3 и 9 с гексагональной структурой (h-MeB2), большим размером зерна (11–13 нм) и текстурой (001), совпадающей с направлением роста покрытий, а также покрытие 5 (t-MoB) демонстрируют хрупкое разрушение с выкрашиванием столбчатых зерен. Введение азота позволяет поменять механизм поведения покрытий и уменьшить зону разрушения. Важно отметить, что безазотное покрытие 1 с орторомбической структурой (табл. 1) показало наилучшие результаты.
Анализ 2D профилей показал, что в покрытиях 2 и 10 происходит глубинный износ, индентор (шарик WC–Co) проникает на h = 17–20 мкм вглубь материала. Соотношение глубины износа к толщине покрытий составляет h/t = 6.3–7.4 (табл. 3). Интересно отметить, что оба этих покрытия из всех исследованных образцов имели максимальное упругое восстановление W = 72%. Также покрытия 2 и 10 имели максимальное содержание азота 18 и 21 ат. % соответственно. Введение небольших концентраций азота, в случае покрытий 3–8 приводит к уменьшению h. Было обнаружено, что величина h возрастает при повышении W (рис. 3а). Внутри каждой системы покрытий (1–2, 3–4, 5–6, 7–8, 9–10) значения h тем меньше, чем ниже H, W, а также параметры H/E и H3/E 2 (табл. 3). Для примера на рис. 4 показаны сравнительные диаграммы по результатам определения H, H/E и h, которые наиболее наглядно иллюстрируют выявленные закономерности. Аналогичным образом от механических свойств зависит величина h/t. Для реакционных покрытий 3–8 значение h/t = 0.52–0.62, т.е. <1, тогда как для покрытий без азота эта величина составляет h/t = 1.28–2.81. То есть благоприятным для снижения h/t является введение небольших добавок азота. Также установлено, что чем больше металла содержится в покрытиях, чем выше соотношения Me/(BN) и Me/B, тем меньше h и соотношение h/t (табл. 3). Особенно эта зависимость выражена для нереакционных покрытий (рис. 3б).
Анализ данных определения диаметра кратера (D) показал следующее. В каждой системе (1–2, 3–4, 5–6, 7–8, 9–10) значение D повышается при повышении E (за исключением 9 и 10), H, H 3/E 2, H/E и W (табл. 3, рис. 4). Минимальный диаметр кратера на уровне D = 400 мкм зафиксирован для покрытия 1 с максимальной концентрацией металла (58 ат. %) и отношении Me/(B,N) = 1.381. С увеличением концентрации азота наблюдается тенденция к росту D (рис. 5). Максимальный диаметр, также как и максимальная глубина наблюдается в случае покрытий 2 и 10. Можно отметить, что анализируя полученный массив данных по всем изученным покрытиям, следует сделать вывод, что повышение значений всех механических характеристик приводит к росту диаметра (рис. 6).
Результаты вычисления объемов кратеров приведены в табл. 3. Обнаружено, что в паре “нереакционное–реакционное” покрытие, чем выше твердость, параметры H/E и H3/E2, тем больше объем. Чем больше E, тем выше V (кроме случаев 9 и 10). Переход к реактивному режиму распыления вызывает снижение объема кратера (кроме 1, 2, 9, 10). Минимальный V в случае большего содержания металла и соотношения Me(B,N). Максимальный объем кратера зафиксирован при максимальной концентрации азота, и максимальном значении W. Значения V возрастают с ростом W (рис. 7а). Закономерной является зависимость, связывающая глубину кратера и его объем: чем меньше параметр h/t, тем меньше V (рис. 7б).
Зависимость разницы между значениями W для реакционного и нереакционного покрытия в каждой системе покрытий от разницы h/t представлена на рис. 8. Внутри каждой системы покрытий работает закономерность – повышение W дает повышение параметра h/t.
Рис. 8.
Зависимость Δh/t от ΔW при переходе от нереакционного распыления к реакционному в каждой паре покрытий 1–2, 3–4, 5–6, 7–8, 9–10.
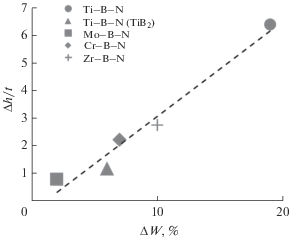
Важно отметить, что полученные данные по износостойкости покрытий в условиях ударно-динамического нагружения не коррелируют с данными испытаний в условиях трения скольжения (табл. 2 и 3). Тем не менее общим является позитивная роль подавления грубой кристаллической структуры при введении азота в каждой системе.
ОБСУЖДЕНИЕ
Морфология покрытий оказывает первостепенное влияние на их поведение в условиях трибоконтакта. Известно, что столбчатая структура при механическом нагружении достаточно легко разрушается вследствие интенсивного распространения микротрещин по границам колонных элементов от поверхности вглубь материала [44–46]. Подавление колонного роста способствует росту износостойкости [47]. Причем переход к равноостной структуре положительно влияет на трещиностойкость, износостойкость при трении скольжении, стойкость к абразивному воздействию и стойкость к ударному нагружению [48, 49]. Подобный эффект наблюдался и в исследованных покрытиях: те образцы, что имели однофазную грубую структуру с зернами гексагональной фазы размером ~10 нм, вытянутые в направлении роста, разрушались наиболее сильно. С изменением морфологии и размера частиц можно также связать закономерности, наблюдаемые в паре нереакционное–реакционное покрытие в каждой системе (покрытия 3–4, 5–6, 7–8). Здесь введение азота в небольших количествах (12–16 ат. %) приводит к снижению h, D и V за счет уплотнения структуры и формирования нанокомпозитной структуры, состоящей из кристаллитов борида металла (MeBx) и аморфных участков (BN), характеризующейся высокими прочностными характеристиками [50, 51]. В то же время большие концентрации азота (18–21 ат. %) повышают долю аморфной фазы, обладающей повышенной хрупкостью [51, 52], что ведет к быстрому разрушению в процессе испытаний. Отсюда следует также объяснение того, что стойкость к ударному нагружению возрастает с ростом концентрации металла в покрытии, а также соотношения Me/(B,N). Отметим, что минимальный износ был получен в случае покрытия 1, обладающего толщиной 1.9 мкм. Ранее было отмечено, что покрытия с малой толщиной обладают самой высокой стойкостью к ударным нагрузкам [53].
Наиболее интересным в полученных результатах является необычная зависимость стойкости к циклическому ударному нагружению от механических характеристик. Обычно износостойкость объемных материалов и покрытий напрямую зависит от их твердости и прочности [54, 55]. Кроме того, для покрытий наблюдается хорошая корреляция износостойкости с параметрами W, H/E, H 3/E 2, особенно если рассматривается разрушение покрытий в условиях трения скольжения [38, 56, 57]. В настоящей работе установлена обратная зависимость: чем выше механические свойства покрытия, в первую очередь, упругое восстановление, тем ниже стойкость к ударному нагружению.
Важно рассмотреть известные исследования, где обнаруживались такие же закономерности. В работе [58] покрытие Graphit-iC (Н = 13.9 ГПа, Е = 181 ГПа) показало улучшенную стойкость к ударным нагрузкам по сравнению с покрытием Dymon-iC (Н = 17 ГПа, Е = 139 ГПа), несмотря на более низкую твердость и низкий H/E. Авторы связали эффект с тем, что меньшая разница в твердости между покрытием и подложкой в Graphit-iC помогает покрытию приспосабливаться к пластической деформации подложки без растрескивания. Более твердое покрытие может в большей мере испытывать хрупкое разрушение и показывать сильный износ. Влияние пластической деформации подробно рассмотрено на примере покрытий TiAlN и TiN в работе [59]. Более твердое покрытие TiAlN, обладающее H3/E 2 = = 0.18 ГПа, показало высокую стойкость к ударам на начальной стадии динамических испытаний, чем покрытие TiN с H 3/E 2 = 0.11 ГПа. Однако покрытие TiAlN после критического количества ударов быстро выходило из строя вследствие хрупкого разрушения, в то время как покрытие TiN продемонстрировало небольшую пластическую деформацию и сохранялось. В работе [60] также было показано, что покрытие TiN по сравнению AlTiN демонстрирует выраженный пластичный отклик при ударно-динамических испытаниях и для достижения максимальной глубины кратера необходимо большее воздействие на покрытие. Упоминаются покрытия с невысокими H, H/E и H 3/E 2, которые обладают меньшей глубиной кратера после ударно-динамических испытаний благодаря преобладающей пластической составляющей деформации [61]. В работе [62] отмечается, что параметр H3/E 2 определяет стойкость покрытий к ударным воздействиям до определенных значений нагрузок, после превышения которых разрушаются покрытия как с низким, так и с высоким значением H3/E 2.
Отметим, что для объемных материалов усталостные свойства связаны с такими механическими свойствами как предел текучести, предел прочности на растяжение и в ряде случаев наблюдается корреляция между пределом усталости и твердостью [55]. Известно, что увеличение прочности приводит к увеличению усталостной долговечности. Однако, когда пластическая деформация при усталостных испытаниях становится доминирующей, высокая пластичность материала также положительно влияет на предел усталости [63, 64]. В работе [65] было установлено, что влияние пластичности преобладает приблизительно до 100 или 1000 ударов. При меньшем числе ударов пластичный материал с низкой прочностью будет лучше сопротивляться повторным ударам, чем менее пластичный материал с высокой прочностью. Однако для большего числа ударов более прочный материал будет более долговечным. Вопрос на каком уровне находится критическая величина в случае покрытий требует дополнительного исследования.
Интересно, что предел усталости (σ1) для углеродистых сталей σ1 = 0.128–0.156 Н, для легированных σ1 = 0.168–0.222 Н, тогда как для более пластичных алюминиевых сплавов σ1 = 0.19 Н [55]. Прочный материал полезен в режиме многоцикловой усталости, в время как для режима малоцикловой усталости более стойким является пластичный материал [66]. Для лучшего понимания требуются комплексные исследования покрытий при варьировании количества циклов, нагрузок с построением классических усталостных кривых. В случае покрытий, при испытаниях важно учитывать физико-механические свойства подложек [59, 67], определяющие поведение системы покрытие-подложки. Поэтому для дальнейших экспериментов важно рассмотреть изученные покрытия, нанесенные на другие типы подложек. В заключение следует отметить, что за время подготовки данной статьи, был опубликован материал по покрытиям на основе углерода и WC, в котором показана обратная зависимость стойкости к ударным воздействиям от H, H/E и H3/E2 [69]. Результаты коррелируют с нашими данными.
ВЫВОДЫ
1) Проведены циклические ударно-динамические испытания покрытий на основе боридов и нитридов переходных металлов (Ti, Mo, Cr, Zr), полученных методом магнетронного напыления на подложках из твердого сплава WC–6% Co.
2) Покрытия, обладающие грубой, сильно текстурированной в направлении роста, структурой на основе фаз с гексагональной решеткой и размером кристаллитов ~10 нм, демонстрировали самую низкую стойкость к ударно-динамическим нагрузкам.
3) Наименьшее разрушение наблюдалось для покрытий Ti–B с орторомбической решеткой и минимальной толщиной 1.9 мкм.
4) Установлено, что снижение твердости, упругого восстановления, индекса пластичности и других механических свойств, приводит к уменьшению глубины, диаметра и объема кратера, образующегося в процессе испытаний. Эта закономерность справедлива как в паре нереакционное-реакционное покрытие, так и в целом для всех систем. Наиболее явным является повышение стойкости к ударным нагрузкам с понижением упругого восстановления.
5) Введение азота в оптимальных количествах (12–16 ат. %) положительно влияло на стойкость к ударно-динамическим нагрузкам, в то время как большие концентрации оказывали негативный эффект. Повышение содержания металла, а также отношения Me/(B,N), в покрытиям способствовали улучшению прочностных характеристик в условиях циклического нагружения.
Список литературы
Uhlmann E., Riemer H., An S. et al. // Procedia Manufacturing. 2019. V. 33. P. 618.
Holubar P., Jilek M., Sima M. // Surface and Coatings Technology. 2000. V. 133–134. P. 145.
Kiryukhantsev-Korneev F.V., Shirmanov N.A., Sheveiko A.N. et al. // Russian Engineering Research. 2010. V. 30. № 9. P. 909.
Kiryukhantsev-Korneev F.V., Sheveiko A.N., Komarov V.A. et al. // Russ. J. Non-ferrous Metals. 2011. V. 52. P. 311.
Schleinkofer U., Czettl C., Michotte C. // Comprehensive Hard Materials. 2014. P. 453.
https://www.platit.com/en/coatings/tib2-scil
https://www.platit.com/en/coatings/borac-arc
Kiryukhantsev-Korneev P.V., Pierson J.F., Bychkova M.Y. et al. // Tribol. Lett. 2016. V. 63. P. 44.
Dearnley P.A., Schellewald M., Dahm K.L. // Wear. 2005. V. 259. P. 861.
Muller K.B. // J. Mater. Process. Technol. 2002. V. 130–131. P. 432.
Taktak S. // Surface and Coatings Technology. 2006. V. 201. P. 2230–2239.
Hassan H.B., Abdel Z. // International J. Hydrogen Energy. 2011. V. 36. P. 849.
Li H., Yao D., Fu Q. et al. // Carbon. 2013. V. 52. P. 418.
Ribeiro R., Ingole S., Usta M. et al. // Wear. 2007. V. 262. P. 1380.
Гончаров А.А., Игнатенко П.И., Петухов В.В. и др. // ЖТФ. 2006. Т. 76. № 10. С. 87.
Goncharov A.A., Petukhov V.V., Terpii D.N. et al. // Inorganic Materials. 2005. V. 41. № 7. P. 696.
Kunc F., Musil J., Mayrhofer P.H., Mitterer C. // Surface and Coatings Technology. 2003. V. 174–175. P. 744.
Takeyama M.B., Noya A., Nakadai Y. et al. // Applied Surface Science. 2009. V. 256. P. 1222.
Kiryukhantsev-Korneev F.V., Lemesheva M.V., Shvyndina N.V. et al. // Prot. Met. Phys. Chem. Surf. 2018. V. 54. P. 1147.
Chatterjee A., Jayaraman S., Gerbi J.E. et al. // Surface and Coatings Technology. 2006. V. 201. P. 4317.
Khor K.A., Yu L.G., Sundararajan G. // Thin Solid Films. 2005. V. 478. P. 232.
Rau J.V., Latini A., Generosi A. et al. // Acta Materialia. 2009. V. 57. P. 673.
Levashov E.A., Shtansky D.V., Kiryukhantsev-Korneev Ph.V. et al. // Russian Metallurgy (Metally). 2010. V. 2010. № 10. P. 917.
Holzschuh H. // Thin Solid Films. 2004. V. 469–470. P. 92.
Jayaraman S., Gerbi J.E., Yang Y. et al. // Surface and Coatings Technology. 2006. V. 200. P. 6629.
Bazhin A.I., Goncharov A.A., Petukhov V.V. et al. // Vacuum. 2006. V. 80. P. 918.
Kiryukhantsev-Korneev F.V., Petrzhik M.I., Sheveiko A.N. et al. // The Physics of Metals and Metallography. 2007. V. 104. № 2. P. 167.
Cheng C.-H., Lee J.W., Ho L.W. et al. // Surf. Coat. Technol. 2011. V. 206. P. 1711.
Sakamaoto Y., Nose M., Mae T. et al. // Surf. Coat. Technol. 2003. V. 174–175. P. 444.
Shtansky D.V., Kiryukhantsev-Korneev F.V., Sheveiko A.N. et al. // Phys. Solid State. 2005. V. 47. P. 252.
Kiryukhantsev-Korneev Ph.V., Sytchenko A.D., Levashov E.A. // Russian J. Non-Ferrous Metals. 2019. V. 60. № 6. P. 662.
Bouzakis K.-D., Siganos A. // Surface and Coatings Technology. 2004. V. 185. P. 150.
Zha X., Jiang F., Xu X. // Surface and Coatings Technology. 2018. V. 344. P. 689.
Bouzakis K.-D., Vidakis N., Leyendecker T. et al. // Surface and Coatings Technology. 1996. V. 86–87. P. 549.
Hadjiyannis S., Charalambous N., Tourlidakis A., Michaelides K. // Proceedings of ASME Turbo Expo 2009: Power for Land, Sea and Air GT2009, June 8–12, 2009, Orlando, Florida, USA.
Meneses-Amador A., Sandoval-Juárez D., Rodríguez-Castro G.A. // Surface and Coatings Technology. 2018. V. 353. P. 346.
Rebholz C., Ziegele H., Leyland A., Matthews A. // J. Vacuum Science and Technology A. 1998. V. 16. P. 2851.
Leyland A., Matthews A. // Wear. 2000. V. 246. P. 1.
Shtansky D.V., Kulinich S.A., Levashov E.A. et al. // Thin Solid Films. 2002. V. 420–421. P. 330.
Levashov E.A., Petrzhik M.I., Shtansky D.V. et al. // Materials Science and Engineering: A. 2013. V. 570. P. 51.
Shtansky D.V., Sheveyko A.N., Sorokin D.I. et al. // Surface and Coatings Technology. 2008. V. 202. P. 5953.
Kiryukhantsev-Korneev F.V. // Russ. J. Non-ferrous Metals. 2014. V. 55. P. 494.
Kiryukhantsev-Korneev F.V., Novikov A.V., Sagalova T.B. et al. // Phys. Metals Metallogr. 2017. V. 118. P. 1136.
Roa J.J., Jimenez-Pique E., Martínez R. et al. // Thin Solid Films. 2014. V. 571. P. 308.
Jayaram V., Bhowmick S., Xie Z.-H. et al. // Materials Science and Engineering: A. 2006. V. 423 P. 8.
Shia X., Lia H., Beake B.D. et al. // Surface and Coatings Technology. 2020. V. 383. № 25288.
Joseph M.C., Tsotsos C., Baker M.A. et al. // Surface and Coatings Technology. 2005. V. 190. P. 345.
Rebholz C., Ziegele H., Leyland A., Matthews A. // Surface and Coatings Technology. 1999. V. 115. P. 222.
Mirzaei S., Alishahi M., Soucek P. et al. // Surface and Coatings Technology. 2020. V. 383. № 125274.
Xu J., Li Z.Y., Xie Z.-H., Munroe P. // Scripta Materialia. V. 74. 2014. P. 88–91.
Neidhardt J., O’Sullivan M., Reiter A.E. et al. // Surface and Coatings Technology. 2006. V. 201. P. 2553.
Lin J., Mishra B., Moore J.J. et al. // Surface and Coatings Technology. 2008. V. 203. P. 588–593.
Beake B.D., Isern L., Endrino J.L., Fox-Rabinovich G.S. // Wear, 2019. V. 418–419. P. 102.
Leyland A., Matthews A. // Coatings Technology. 2004. V. 177–178. P. 317–324.
Золоторевский В.С. Механические свойства металлов: Учебник для вузов. М.: Металлургия. 1983. 352 с.
Borgaonkar A.V., Syed I. // Sādhanā 2020. V. 45. № 30.
Murray J.W., Ahmed N., Yuzawa T. et al. // Tribology International. 2020. V. 150. № 106392.
Beake B.D., Liskiewicz T.W., Bird A., Shi X. // Tribology International. 2019. № 105732.
Yoon S.Y., Yoon S.-Y., Chung W.-S., Kim K.H. // Surface and Coatings Technology. 2004. V. 177–178. P. 645.
Chen J., Li H., Beak B.D. // Surface and Coatings Technology. V. 308. 2016. P. 289.
Fox-Rabinovich G.S., Beake B.D., Endrino J.L. et al. // Surface and Coatings Technology. 2006. V. 200. P. 5738.
Beake B.D., Vishnyakov V., Colligon J.S. // J. Phys. D: Appl. Phys. 2011. V. 44. № 085301.
Höppel H.W., Göken M. // Nanostructured Metals and Alloys. 2011. P. 507.
Новиков И.И., Золоторевский В.С., Портной В.К., Белов Н.А. и др. Металловедение. Основы металловедения. Т. 1. / Под ред. проф. Золоторевского В.С. М.: МИСиС, 2009. 496 с.
Forrest P.G. Fatigue of Metals. Oxford, 1962. 352 p.
Morrow J. Cyclic Plastic Strain Energy and Fatigue of Metals. / In: Lazan B.J., West Conshohocken, PA: ASTM International. 1965.
Shtansky D.V., Petrzhik M.I., Bashkova I.A. et al. // Physics of the Solid State. 2006, V. 48. № 7. P. 1301
Kiryukhantsev-Korneev Ph.V., Sheveiko A.N. // Protection of Metals and Physical Chemistry of Surfaces, 2018. V. 54. № 5. P. 963–968.
Qinglin Li, Shaomiao Shi, Xia Li, Shiyan Ding, Chenglong Fan, Guangan Zhang, Study on low velocity cyclic impact wear of amorphous carbon films with different mechanical properties, Surface and Coatings Technology, 2020, 126339.
Дополнительные материалы отсутствуют.
Инструменты
Физикохимия поверхности и защита материалов