Физикохимия поверхности и защита материалов, 2020, T. 56, № 6, стр. 636-639
Об электрохимическом осаждении композиционных покрытий на основе цинка, модифицированных углеродными нанотрубками, из щелочного электролита
В. Н. Целуйкин 1, *, А. А. Стрилец 1, А. В. Яковлев 1
1 Энгельсский технологический институт (филиал) ФГБОУ ВО “Саратовский государственный технический университет им. Ю.А. Гагарина”
413100 Энгельс, пл. Свободы, 17, Саратовская обл., Россия
* E-mail: tseluikin@mail.ru
Поступила в редакцию 14.01.2020
После доработки 17.01.2020
Принята к публикации 24.01.2020
Аннотация
Получены композиционные электрохимические покрытия (КЭП) на основе цинка, модифицированные углеродными нанотрубками (УНТ) из щелочного электролита в импульсном режиме электролиза. Исследованы микроструктура и трибологические свойства данных КЭП. Установлено, что при введении дисперсной фазы УНТ в щелочной электролит цинкования коэффициент трения скольжения формирующихся покрытий снижается в 1.30–1.45 раза. Изучено коррозионно-электрохимическое поведение КЭП цинк–УНТ в 0.5 М растворе H2SO4.
ВВЕДЕНИЕ
Эффективным методом модифицирования металлических поверхностей является нанесение композиционных электрохимических покрытий (КЭП). Принцип получения КЭП основан на совместном осаждении металлов с дисперсными частицами различной природы из электролитов–суспензий [1, 2]. Одним из широко используемых процессов в гальванотехнике является цинкование. Согласно данным [3], около половины мирового производства цинка приходится на долю электрохимических покрытий. КЭП на основе цинка и его сплавов используют для коррозионной защиты стальных изделий с улучшением их физико-механических свойств [4–19]. Эксплуатационные характеристики КЭП в значительной степени определяются природой дисперсной фазы. Цинк обладает сродством к дисперсным частицам различной природы и легко образует с ними композиционные покрытия. В настоящее время активно исследуются КЭП на основе цинка, модифицированные различными наноматериалами [4–8, 12–19], поскольку внедрение наноразмерных частиц в металлическую матрицу позволяет получать конструкционные материалы, превосходящие по функциональным свойствам крупнозернистые аналоги.
Одним из перспективных наноматериалов являются углеродные нанотрубки (УНТ), представляющие собой цилиндрические молекулы, образующиеся в результате сворачивания плоских атомных слоев графита (графенов). УНТ могут быть одно- и многослойными (состоять из нескольких соосных цилиндров). Внутренний диаметр нанотрубок лежит в пределах от 0.4 до нескольких нанометров, а их длина, как правило, не превышает несколько десятков микрометров.
Цель данной работы – получить в импульсном режиме электролиза КЭП на основе цинка, модифицированные УНТ, исследовать их структуру, трибологические свойства и коррозионно-электрохимическое поведение.
Преимущество нестационарных режимов электролиза (в частности, импульсного) заключается в возможности контролировать значительно большее число параметров электроосаждения покрытий. Параметры нестационарных режимов оказывают существенное влияние на динамику роста и свойства осадков металлов. Импульсный режим способствует формированию покрытий с высоким содержанием наночастиц и равномерным их распределением в электролитическом осадке. Это позволяет управлять процессами зародышеобразования и роста зерен и получать электролитические осадки с улучшенными функциональными свойствами [18–22]. Кроме того, в нестационарных условиях электролиза на катоде достигается потенциал, при котором металл может осаждаться на пассивные участки поверхности [23, 24].
МЕТОДИКА ЭКСПЕРИМЕНТА
КЭП на основе цинка получали из щелочного электролита следующего состава, г/л: ZnO 10; NaOH 100; полиэтиленполиамин 5; углеродные нанотрубки 0.05. Покрытия наносили на стальную основу (сталь 45) при комнатной температуре с постоянным перемешиванием электролита. Покрытия чистым цинком осаждали из электролита приведeнного выше состава без добавления дисперсной фазы. Адгезию полученных электролитических осадков оценивали путем нанесения сетки царапин согласно ГОСТ 9.307-89.
В работе использовались УНТ марки “Таунит”, полученные пиролизом углеводородов с никелевым катализатором, которые представляют собой полые волокна, состоящие из графеновых слоeв фуллереноподобной конструкции, диаметром от 10 до 60 нм.
Электрохимическое осаждение цинковых покрытий исследовалось в импульсном режиме при плотностях катодного тока 1–6 А/дм2. Соотношение периодов импульса (tимп) и паузы (tп) составляло 1 : 1 с.
Основные параметры импульсного электроосаждения, включающие скважность Q, частоту импульсов F и рабочий цикл η (табл. 1) рассчитывались по следующим соотношениям:
Таблица 1.
Параметры процесса импульсного электроосаждения покрытий на основе цинка
tимп, с | tп, с | Q | F, Гц | η, % |
---|---|---|---|---|
1 | 1 | 2 | 0.5 | 50 |
Электрохимические измерения проводили на импульсном потенциостате P-30J. Потенциалы задавали относительно насыщенного хлоридсеребряного электрода сравнения и пересчитывали по водородной шкале.
Коэффициенты трения скольжения исследуемых покрытий на основе цинка определяли по следующей формуле:
где Fтр – сила трения скольжения; P – сила, с которой контртело давит на испытуемую поверхность. В качестве контртела использовался стальной образец, масса которого во всех испытаниях составляла 1 г.Для оценки коррозионно-электрохимического поведения изучаемых покрытий получали анодные потенциодинамические кривые в 0.5 М растворе H2SO4 при скорости развёртки потенциала Vр = 8 мВ/с.
РЕЗУЛЬТАТЫ И ИХ ОБСУЖДЕНИЕ
Электролиты, применяемые для осаждения цинковых покрытий, можно условно разделить на кислые, слабокислые, нейтральные и слабощелочные, щелочные. К последнему типу относятся цинкатные электролиты, которые просты по составу, устойчивы и позволяют достичь высокого выхода по току [3]. С цинком легко соосаждаются дисперсные частицы различной природы, влияние которых на кинетику электродных процессов определяется их размером, формой и способностью приобретать положительный заряд [1]. При введении УНТ в состав щелочного электролита цинкования на E, t – кривых наблюдается смещение потенциалов в сторону более отрицательных значений по сравнению с электроосаждением цинка без дисперсной фазы (рис. 1). Одновременно имеет место увеличение скачков потенциала на кривых, полученных при осаждении КЭП цинк–УНТ. Известно [25], что перенос дисперсной фазы к катоду может осуществляться посредством адсорбции на их поверхности катионов осаждаемого металла и водорода. Поэтому, можно предположить, что частицы УНТ продвигаются к катоду и встраиваются в электролитический осадок не только вследствие конвекции, но и за счет адсорбции на их поверхности катионов цинка. Адсорбированные на углеродных нанотрубках ионы участвуют в связывании дисперсной фазы с поверхностью катода. Подобное связывание ослабляет расклинивающее давление прослойки жидкости между частицей УНТ и катодом, усиливая адгезию [2].
При переходе от чистого цинкового покрытия (рис. 2а) к КЭП цинк–УНТ (рис. 2б) наблюдается изменение микроструктуры поверхности электролитических осадков. Композиционное покрытие имеет выраженную мелкокристаллическую структуру, в то время как поверхность цинкового осадка без дисперсной фазы близка к рентгеноаморфной. Очевидно, частицы углеродных нанотрубок выступают в качестве центров кристаллизации, что способствуют равномерному распределению цинка по катодной поверхности и упорядочению структуры формирующегося композиционного покрытия. Следует также отметить, что с ростом толщины осадка КЭП цинк–УНТ не наблюдается его разрыхления. Не ухудшается и адгезия к подложке изученных цинковых покрытий.
Рис. 2.
Микроструктура поверхности электролитического цинка (а) и КЭП цинк–УНТ (б). Плотность тока ik = 6.0 А/дм2. Увеличение ×1000.
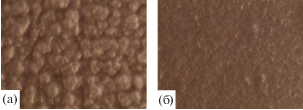
Изменение структуры электролитического осадка должно сказываться на его эксплуатационных свойствах [1, 2]. Одной из важных в практическом отношении характеристик металлических поверхностей является коэффициент трения скольжения f. Согласно закону Амонтона–Кулона, коэффициент трения зависит от природы контактирующих материалов, и не зависит от нагрузки. Для композиционных покрытий значения коэффициента трения скольжения уменьшается в 1.30–1.45 раза по сравнению с электролитическими цинковыми осадками без дисперсной фазы (табл. 2). Вероятно, выявленный эффект обусловлен тем, что частицы УНТ, которые в процессе электроосаждения включаются в структуру композиционных покрытий, выполняют функцию сухой смазки (эксперимент проводился в условиях сухого трения).
Таблица 2.
Коэффициенты трения скольжения f покрытий на основе цинка, полученных при различной плотности катодного тока
ik, А/дм2 Покрытие | 1.0 | 2.5 | 4.0 | 6.0 |
---|---|---|---|---|
Цинк | 0.27 | 0.27 | 0.23 | 0.22 |
КЭП цинк–УНТ | 0.21 | 0.20 | 0.17 | 0.15 |
Другим эксплуатационным свойством электрохимических покрытий, имеющим существенное практическое значение, является защитная способность к коррозионному воздействию. Из анодных потенциодинамических кривых (ПДК) электролитического цинка и КЭП цинк–УНТ (рис. 3) следует, что частицы углеродных нанотрубок повышают потенциал и, соответственно, уменьшают ток активного анодного растворения изученных покрытий. Коррозионное поведение композиционных покрытий в значительной мере обусловлено свойствами металлической матрицы, поэтому потенциалы начала пассивации чистого цинка и КЭП цинк–УНТ близки. Характерной особенностью анодной ПДК композиционного покрытия является существенное уширение пассивной области. В дальней анодной области потенциалов дисперсные частицы УНТ в покрытии оказывают наиболее значительное влияние на ход ПДК (потенциалы перепассивации изученных покрытий заметно различаются). Электрохимические исследования в 0.5 М растворе H2SO4 дают основания утверждать, что стойкость к коррозии КЭП цинк–УНТ будет выше, чем у электролитических цинковых осадков без дисперсной фазы. Полученный результат может быть обусловлен несколькими факторами. Чем меньше размер дисперсных частиц в КЭП, тем более стойким является покрытие к коррозионному воздействию, т.к. при этом обеспечивается более равномерное распределение коррозионного тока между центрами, препятствующими его распространению. Кроме того, влияние дисперсной фазы в композиционных покрытиях на коррозию проявляется лишь в случае образования инкорпорированными частицами в процессе термодинамических реакций на границах фаз или по всему объему соединений, более коррозионностойких, чем металлическая матрица [1]. В противном случае развитие коррозионного процесса не прекратится, а пойдет в обход дисперсной частицы. Поэтому можно достаточно уверенно предположить, что в процессе осаждения КЭП цинк–УНТ происходить образование подобных соединений.
Рис. 3.
Потенциодинамические поляризационные кривые цинка (1) и КЭП цинк–УНТ (2) в 0.5 М Н2SO4 (покрытия получены при ik= 4 А/дм2).
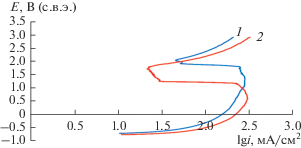
На основании проведенных исследований можно заключить, что введение углеродных нанотрубок в щелочной электролит цинкования способствует формированию КЭП. Частицы УНТ оказывают определяющее влияние на структуру, трибологические свойства и коррозионно-электрохимическое поведение цинковых композиционных покрытий, полученных в импульсном режиме электролиза.
Исследование выполнено при финансовой поддержке РФФИ в рамках научного проекта № 18-29-19048.
Список литературы
Антропов Л.И., Лебединский Ю.Н. Композиционные электрохимические покрытия и материалы. Киев: Техника, 1986. 200 с.
Сайфуллин Р.С. Физикохимия неорганических полимерных и композиционных материалов. М.: Химия, 1990. 240 с.
Окулов В.В. Цинкование. Техника и технология. М.: Глобус, 2008. 252 с.
Ranganatha S., Venkatesha T.V., Vathsala K., Punith kumar M.K. // Surface & Coatings Technology. 2012. V. 208. P. 64–72.
Patrick Ioan Nemes, Maria Lekka, Lorenzo Fedrizzi, Liana Maria Muresan // Surface & Coatings Technology. 2014. V. 252. P. 102–107.
Целуйкин В.Н., Корешкова А.А. // Журн. прикладной химии. 2014. Т. 87. № 9. С. 1255–1258.
Целуйкин В.Н., Корешкова А.А. // Журн. прикладной химии. 2015. Т. 88. № 2. С. 269–272.
Rekha M.Y., Anshul Kamboj, Chandan Srivastava // Thin Solid Folms. 2017. V. 636. P. 593–601.
Musikhina T.A., Zemtsova E.A., Fuks C.L. // IOP Conf. Series: Materials Science and Engineering. 2017. V. 262. P. 012010.
Перевалов В.П., Винокуров Е.Г., Зуев К.В., Василенко Е.А., Цивадзе А.Ю. // Физикохимия поверхности и защита материалов. 2017. Т. 53. С. 115–131.
Boshkov N. // Portugaliae Electrochimica Acta. 2017. V. 35. P. 53.
Al-Dhire T.M., Zuhailawati H., Anasyida A.S. // IOP Conf. Series: J. Physics: Conf. Series 1082. 2018. 012064.
Peshova M., Bachvarov V., Vitkova St., Atanasova G., Boshkov N. // Transactions of the IMF. 2018. V. 96. № 6. P. 324–331.
Kazimierczak H., Szymkiewicz K., Bobrowski P., Swiatek Z., Rogal L., Gileadi E., Eliaz N. // J. The Electrochemical Society. 2018. V. 165. P. 774–782.
Bin Yang, Pengfei Zhang, Guangxin Wang, Aiqin Wang, Xiaofang Chen, Shizhong Wei, Jingpei Xie // Coatings. 2019. V. 9. P. 758.
Rekha M.Y., Chandan Srivastava // Corrosion Science. 2019. V. 152. P. 243–248.
Punith Kumar M.K., Rekha M.Y., Juhi Agrawal, Tushar Mani Agarwal, Chandan Srivastava // J. Alloys and Compounds. 2019. V. 783. P. 820–827.
Целуйкин В.Н., Корешкова А.А. // Физикохимия поверхности и защита материалов. 2018. Т. 54. № 3. С. 293–296.
Целуйкин В.Н., Корешкова А.А. // Физикохимия поверхности и защита материалов. 2018. Т. 54. № 6. С. 582–584.
Кирикова Д.И., Киреева С.Н., Киреев С.Ю., Перелыгин Ю.П. // Гальванотехника и обработка поверхности. 2016. Т. 24. № 3. С. 32–38.
Кругликов С.С., Некрасова Н.Е., Касаткин В.Э., Корнилова С.И. // Гальванотехника и обработка поверхности. 2016. Т. 24. № 4. С. 30–38.
Никитин В.С., Останина Т.Н., Рудой В.М. // Электрохимия. 2018. Т. 54. С. 667–673.
Tao S., Li D.Y. // Nanotechnology. 2006. V. 17. P. 65.
Chang L.M., Chen D., Liu J.H., Zhang R.J. // J. Alloys and Compounds. 2009. V. 479. P. 489.
Сайфуллин Р.С., Абдуллин И.А. // Российский химический журн. 1999. Т. 63. № 3–4. С. 63–67.
Дополнительные материалы отсутствуют.
Инструменты
Физикохимия поверхности и защита материалов