Физикохимия поверхности и защита материалов, 2021, T. 57, № 1, стр. 106-112
Проблемы гидродинамической коррозии в мультифазных трубопроводах
Г. Г. Исмайылов 1, *, Э. Х. Искендеров 1, Ф. Б. Исмайылова 1
1 Азербайджанский государственный университет нефти и промышленности
Az1010 Баку, пр. Азадлыг, 20, Азербайджан
* E-mail: asi_zum@mail.ru
Поступила в редакцию 15.05.2019
После доработки 12.09.2020
Принята к публикации 19.09.2020
Аннотация
В статье проанализированы причины коррозионных и эрозионных процессов в мультифазных трубопроводных системах сбора-транспорта углеводородов промысловых технологических трубопроводов месторождений Азербайджана. При различных значениях начального давления и диаметра были вычислены оптимальные значения дальности перекачки гетерогенных продукций скважин с учетом изменений вязкости и рельефа трассы трубопроводов. Было исследовано влияние фракционного состава содержащихся в нефти механических примесей на эрозионно-коррозионные процессы в внутрипромысловых трубопроводах с учетом гидродинамики мультифазных потоков. Предложены конкретные возможные варианты снижения скорости динамической коррозии в мультифазных трубопроводах и утилизации отделившихся механических примесей и воды в промысловых условиях.
ВВЕДЕНИЕ
Добыча, сбор, подготовка и транспортировка углеводородов основаны на движения мультифазных систем нефти, пластовой воды, нефте-газовых смесей и механических частиц, которые охватывают процессы, включающие подъем продукции скважин на поверхность земли, направлению ее на пункты сепарации, разделение их на фазы и внутри промысловую транспортировку [1]. К проблемам добычи полезных ископаемых, связанных с мультифазностью продукции можно отнести: движение рабочей среды (продукта), пульсацию давления и других осложнений в сети сбора нефти, а также учет добываемого продукта, коррозию промыслово-технологических трубопроводов, использование мультифазных насосов и др.
На практике эксплуатации месторождений углеводородов, где осуществляется добыча и транспортировка нефти и газа одним из основных факторов является, возникновение разливов нефти в результате аварий в системе трубопроводов, которые негативно влияют на окружающую среду. Анализ показывает, что подавляющее большинство разрушения труб – это эрозия или разрушение эрозионно-коррозионного характера. Разрушение трубопровода происходит на его нижней поверхности и в течении короткого времени разрушает стенку трубы [2, 3].
ОБЪЕКТ ИССЛЕДОВАНИЯ
Статистика разрушения отдельных трубопроводов показывает, что транспортировка компонентов по отдельности по промысловым трубопроводам не представляет серьезной угрозы. В целом, согласно исследованиям по коррозионной активности, если нефть и газ не содержат газообразного сероводорода, они считаются средой с низкой коррозионной активностью. Как правило, скорость коррозии стальных труб не очень велика и составляет 0.1 мм/год. Пластовая вода, которая имеет высокий уровень минерализации, обладает умеренной коррозионной активностью в таких статических условиях. Скорость коррозии стальных конструкций в такой среде не превышает 0.3 мм/год. Относительно большая скорость коррозии наблюдается при транспортировке водонефтяных эмульсий, в основном при меньших скоростях транспортировки и низких скоростях потока в промысловых трубопроводах. Скорость коррозии в это время достигает 3–5 мм/год, и это не случайно, т.к. эти трубопроводы могут разрушаться через 2–3 года.
Промысловый опыт также подтверждает, что при больших скоростях транспортировки стальные трубопроводы более устойчивы к коррозии. Согласно существующим фактам можно утверждать, что корреляция между скоростью коррозии и режимами движения потока значительно сильнее [4].
Недавние исследования показали, что щелевая коррозия в трубопроводе, наряду с общей коррозионной активностью, также связана с присутствием механических соединений в составе мультифазных нефтегазоводных смесей.
А при транспортировке газонефтеводяных смесей скорость коррозии трубопроводов превышает 4–5 мм/год. Скорость коррозии может еще увеличится для слоистых режимов течений водонефтяных эмульсий. Фактором, который играет наиболее важную роль, является изменения гидродинамического режима для таких потоков. Поэтому основными причинами щелевой коррозии в трубопроводах являются:
– общая коррозионная активность;
– наличие механических смесей в транспортируемых смесях нефти, газа и воды.
Авторы [4, 5] считают, что одним из методов защиты нефте- и газопроводов от разрушения является выбор гидродинамического режима, позволяющего избежать транспортировки мультифазной смеси в расслоенном виде.
Анализ и наблюдения показывают, что активные разрушения происходят чаще в начале восходящих участков трубопроводов. Большая степень эрозии этих частей обусловлена тем, что на этих местах кроме жидкостей собираются также твердые механические частицы, и происходит их периодическое движения вверх-вниз по потоку. Коррозионные разрушения, наблюдаемые в нижней части труб, для технологических нефтегазопроводов относительно большого диаметра, очень характерны для системы сбора нефти и газа Азербайджанских месторождений [6, 7]. Эти эрозионно-коррозионные трещины могут иметь ширину от 20 до 60 мм и длину от 5 до 20 м. Как происходят разрушения такой длины в очень неактивной коррозионной среде, которая образуется в нижней части, требует своего объяснения. Большинство исследователей коррозии объясняют возникновение таких случаев тем, что процесс коррозии металла происходит в кислой среде. А в общем, действия происходящих гидравлических ударов, вибраций, механическо-химической растворимости не могут быть предсказаны, и эти эффекты не могут быть объяснением локальных коррозионных разрушений, наблюдаемых в нижних частях труб. При небольшой скорости (до 1 м/с) потока образуются слоистые структурные формы газожидкостных смесей и водная фаза, движущаяся по нижней части трубопровода представляет собой отдельную фазу, выше которой движутся нефть, газ или нефтяная эмульсия. Из-за разницы между вязкостями контактирующих фаз образуются волны между жидкими фазами. Между тем, механические смеси (частицы) в водной фазе (карбонаты и сульфиды железа, песок, глина и т.д.) попадают в жидкую каплю фазы и оказывают постоянное гидроэрозионное воздействие на защитный слой карбонатов в нижней части внутренней поверхности труб. Поэтому, происходит очищение покрытия на нижней части трубы, что ускоряет коррозионно-эрозионный процесс. Многолетний опыт и анализ показывают, что использование ингибиторов коррозии не может предотвратить такие процессы.
ПОСТАНОВКА ВОПРОСА
Решение проблемы предотвращения коррозионно-эрозионных процессов в мультифазных трубопроводах требует больших исследований. Эти процессы, происходящие, прежде всего, из-за внутренних факторов, требуют учитывать гидравлические особенности мультифазных потоков, в том числе содержащих механические смеси. Прежде всего, необходимо учитывать расчетные значения приведенного диаметра линий сбора нефти и газа на стадии обустройства (или во время их эксплуатации), чтобы обеспечить оптимальный уровень скорости движения смесей нефти, газа и воды, т.е., по крайней мере, нельзя допускать разделения воды из мультифазных смесей. Известно, что разработка нефтяных и газовых месторождений в Азербайджанском секторе Каспийского моря в основном осуществляется на скважинах морских платформ, и транспортировка продукции производится подводными трубопроводами. Протяженность промыслово-технологических трубопроводов для транспортировки нефти и газа достигает от нескольких километров до десятков. В большинстве случаев по этим трубопроводам транспортируются мультифазные и многокомпонентные смеси (нефть–газ, нефть–газ–вода, газовый конденсат, газ–конденсат–вода, включая механические смеси), и при этом возникают некоторые трудности и осложнении.
Часть проблем, возникающих при транспортировке мультифазных систем, связана с разнообразием рельефа трубопроводов. Часто встречающие профили трассы для морских подводных трубопроводов Азербайджана с учетом коэффициента рельефа Rк (отношение длины восходящих участков к общей длины трубопровода) показаны на рис. 2. Как видно из рис. 2, для морских трубопроводов, основной причиной осложнения, связанных с рельефными условиями является то, что сборные коллекторы с разных платформ имеют спуски в море и подъемы на платформы. Поэтому, при рассмотрении влияния профиля на величину гидравлического сопротивления, следует учесть особенности мультифазного потока. Среди факторов, влияющих на эффективность функционирования коллекторов нефти и газа, помимо профиля рельефа играет немаловажную роль и вязкость гетерогенной системы. Анализ проведенных нами расчетов показывает, что важно оценить дальность сбора и транспорта мультифазных систем. В табл. 1 приведены значения оптимального расстояния транспорта многофазных систем в зависимости от рельефа трассы и вязкости системы, при различных объемах продукции и диаметрах трубопровода. Для различных диаметров (D = 0.255 и 0.509 м) трубопровода и значений начального давления были построены зависимости оптимального расстояния транспортировки мультифазных систем от коэффициента рельефа, которые представлены на рис. 3 и 4. Как видно из рис. 3 и 4, с увеличением давления в трубопроводе, дальность транспортировки увеличивается, а при увеличении коэффициента рельефа она уменьшается.
Таблица 1.
Изменения оптимального расстояния транспортировки мультифазных систем в зависимости от рельефа трассы и вязкости продукции скважин
Объем продукции т/год | Начальное давление трубопровода, MПa | Внутренний диаметр трубопровода, м | Вязкость продукции скважин (нефть, газ, вода), м2/с | ||||||||
---|---|---|---|---|---|---|---|---|---|---|---|
10–5 | 8 ×10–5 | 2 × 10–4 | |||||||||
коэффициент рельефа трассы, R = h/L, м/км | |||||||||||
15 | 30 | 40 | 15 | 30 | 40 | 15 | 30 | 40 | |||
оптимальное расстояние транспортировки мультифазных систем (Lопт), км | |||||||||||
100 | 1.5 | 0.255 | 21.6 | 11.8 | 8.3 | 20.0 | 11.5 | 8.2 | 17.3 | 10.3 | 7.3 |
300 | 0.357 | 21.0 | 11.6 | 8.2 | 19.4 | 11.3 | 8.0 | 18.0 | 10.6 | 7.4 | |
1000 | 0.509 | 19.7 | 11.3 | 8.1 | 17.9 | 10.8 | 7.8 | 16.3 | 10.0 | 7.2 | |
100 | 2.0 | 0.255 | 36.7 | 19.6 | 14.6 | 34.0 | 19.0 | 14.3 | 29.1 | 17.0 | 12.5 |
300 | 0.357 | 35.7 | 19.4 | 14.5 | 33.3 | 18.7 | 14.1 | 30.0 | 17.4 | 12.7 | |
1000 | 0.509 | 33.7 | 18.9 | 14.2 | 30.6 | 18.0 | 13.7 | 27.8 | 16.7 | 12.4 | |
100 | 3.0 | 0.255 | 70.0 | 38.1 | 33.8 | 63.8 | 37.4 | 32.0 | 54.6 | 31.7 | 25.0 |
300 | 0.357 | 66.3 | 37.9 | 33.5 | 64.8 | 37.0 | 32.3 | 56.4 | 32.6 | 25.6 | |
1000 | 0.509 | 65.5 | 37.2 | 32.2 | 60.0 | 35.6 | 31.5 | 53.5 | 31.5 | 25.0 |
Рис. 3.
Зависимость оптимальной дальности мультифазных систем сбора от коэффициента релефа при различрых значениях давлении (D = 0.255 м).
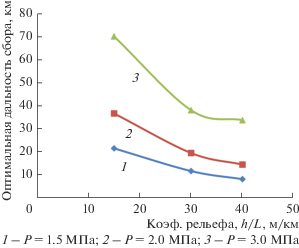
Рис. 4.
Зависимость оптимальной дальности мультифазных систем сбора от коэффициента релефа при различрых значениях давлении (D = 0.509 м).
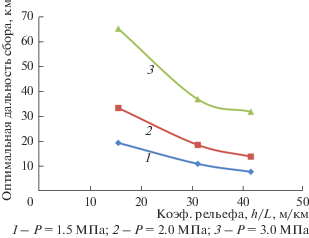
Результаты расчетов показали, что в отличие от однофазного потока дальность сбора мультифазных газоконденсатных систем не может увеличиваться беспредельно с увеличением диаметра газопровода и в зависимости от объема и давления перекачки, а также от диаметра трубопровода имеет ограничение (максимум) [8].
РЕШЕНИЕ И ОБСУЖДЕНИЕ ПРОБЛЕМЫ
С учетом вышеотмеченных особенностей функционирования технологических трубопроводов были проанализированы некоторые коррозионно-эрозионные проблемы мультифазных систем. Как известно из механики, сила эффекта эрозии – мощность силы трения (N) определяется следующим образом [9, 10].
где N – мощность силы трения на поверхности труб механических смесей;
F – сила трения частицы;
$v$ – скорость частицы (эта скорость принимается равным скорости течения жидкости в точке, соответствующей центру тяжести частицы).
Во время движения по трубопроводу сила трения для механической частицы определяется следующей зависимостью:
(2)
$F = ({{\rho }_{{{\text{м}}{\text{.ч}}{\text{.}}}}} - {{\rho }_{{\text{ж}}}})g\varphi \pi {{{{d}^{3}}} \mathord{\left/ {\vphantom {{{{d}^{3}}} 6}} \right. \kern-0em} 6}.$Здесь d – диаметр механической частицы;
${{\rho }_{{{\text{м}}{\text{.ч}}{\text{.}}}}}$ и ${{\rho }_{{\text{ж}}}}$ – плотность механической частицы и жидкости соответственно;
φ – коэффициент трения частицы о металл.
Для нахождения скорости смещения механической частицы, может быть использовано следующее правило распределения скорости по поперечному сечению трубопровода:
Здесь $u$ – можно рассматривать как среднерасходную скорость потока.
r – это расстояние между осями механической частицы и потока.
Учитывая, что r = $\frac{{D - d}}{2}$, то имеем:
Подставляя выражения F и v в уравнении (1), получим:
(5)
$N = 10.3({{\rho }_{{{\text{м}}{\text{.ч}}{\text{.}}}}} - {{\rho }_{{\text{ж}}}})~\varphi u~(2 - {d \mathord{\left/ {\vphantom {d D}} \right. \kern-0em} D}){{{{d}^{4}}} \mathord{\left/ {\vphantom {{{{d}^{4}}} D}} \right. \kern-0em} D}.$Последнее уравнение указывает на то, что мощность эрозионного воздействия на трубопровод больше зависит от диаметра механических частиц.
Ниже рассмотрены и проанализированы коррозионные процессы нефте-промысловых технологических трубопроводов на примере месторождений Азербайджане с учетом динамики мультифазных смесей.
История добычи нефти в Азербайджане показывает, что механические смеси в мультифазных потоках системы сбора скважин не только загрязняют технологическое оборудование и трубопроводы сбора и транспортировки, но также подвергают их коррозии и коррозионно-эрозионному воздействию. Наблюдения и исследования на морских месторождениях НГДУ “Абшероннефть”, “Нефтяные Камни” и “28 мая” показывают, что каждый литр жидкости содержит механические смеси от 0.5 до 5 г, размером 0.01 до 0.4 мм (в основном песок). Технологическое оборудование, после осадки механических частиц загрязняется в течении короткого времени (несколько недель). Рабочие части насосов разрушаются механическими частицами в течение 3–4 мес., происходят утечки и потери углеводородов, загрязняется окружающая среда. Следует отметить, что в это время много времени и сил уходит на очистку оборудования в основном от донных отложений.
Учитывая, что глубина моря достигает на месторождениях “Апшерон Банкасы” 8–20 м, “Нефтяные камни” 15–50 м и “Гюнешли” 80–150 м, то при транспортировке продукции скважин между платформами на местах соединения труб восходящего потока (от морского дна до поверхности воды) в связи с осадкой механических загрязнений, парафина и соли уменьшается рабочий диаметр трубопровода. Любая остановка транспортных трубопроводов может быть причиной накопления загрязнений на дне трубопровода и возникновения пробок. В результате воздействия давлений потока нефти и газа скважин высокого давления на линии скважин низкого давления рабочий режим этих скважин нарушается.
Учитывая тот факт, что залежи нефти в этих месторождениях в основном представляют собой песок, песчаник и алевролиты, то относительное распределение отдельных фракций по их средним размерам и влиянию на трубы можно рассматривать, как показано в табл. 2. Согласно данным табл. 2, мощность эффекта эрозии на трубопроводе была рассчитана по выражению (5). Расчеты были основаны на следующих предварительных данных:
Таблица 2.
Зависимость мощности трения от размеров механических примесей в промыслово-транспорных трубопроводах при различных значениях скорости потока
Средний диаметр механических частиц, мм | Их доля в объеме | Мощность трения (при различных скоростях течения), N, 10–11 Вт | |||||||
---|---|---|---|---|---|---|---|---|---|
0.5 м/с | 1.0 м/с | 1.5 м/с | 2.0 м/с | ||||||
мощность | доля в объеме | мощность | доля в объеме | мощность | доля в объеме | мощность | доля в объеме | ||
2.00 | 0.01 | 16350.00 | 0.72 | 32690.00 | 0.72 | 49040.00 | 0.72 | 65390.00 | 0.72 |
1.50 | 0.02 | 5179.00 | 0.23 | 10360.00 | 0.23 | 15540.00 | 0.23 | 20710.00 | 0.23 |
1.00 | 0.03 | 1024.00 | 0.05 | 2048.00 | 0.05 | 3073.00 | 0.05 | 4097.00 | 0.05 |
0.50 | 0.05 | 64.09 | 0.00 | 128.20 | 0.00 | 192.30 | 0.00 | 256.40 | 0.00 |
0.30 | 0.25 | 8.31 | 0.00 | 16.62 | 0.00 | 24.93 | 0.00 | 33.24 | 0.00 |
0.20 | 0.16 | 1.64 | 0.00 | 3.28 | 0.00 | 4.93 | 0.00 | 6.57 | 0.00 |
0.10 | 0.15 | 0.10 | 0.00 | 0.21 | 0.00 | 0.31 | 0.00 | 0.41 | 0.00 |
0.08 | 0.05 | 0.04 | 0.00 | 0.08 | 0.00 | 0.12 | 0.00 | 0.17 | 0.00 |
0.06 | 0.03 | 0.01 | 0.00 | 0.03 | 0.00 | 0.04 | 0.00 | 0.05 | 0.00 |
0.04 | 0.06 | 0.00 | 0.00 | 0.01 | 0.00 | 0.01 | 0.00 | 0.01 | 0.00 |
0.02 | 0.08 | 0.00 | 0.00 | 0.00 | 0.00 | 0.00 | 0.00 | 0.00 | 0.00 |
0.01 | 0.11 | 0.00 | 0.00 | 0.00 | 0.00 | 0.00 | 0.00 | 0.00 | 0.00 |
1.00 | 1.00 | 1.00 | 1.00 |
D = 200 мм = 0.2 м;
${{\rho }_{{{\text{м}}{\text{.ч}}{\text{.}}}}}$ = 1800 кг/м3;
${{\rho }_{{\text{ж}}}}$ = 800 кг/м3;
$v$ = 0.5; 1.0; 1.5; 2.0 м/с.
Результаты расчетов приведены в табл. 2 и на рис. 5. Как видно из табл. 2, доля почти 100% фрикционных частиц приходится в основном на частицы размером d > 0.5 мм. Интересно, что подавляющее большинство эффектов эрозии (95%) создают фракции с наибольшим диаметром (1–2 мм) и хотя частицы размером от 0.1 до 0.3 мм составляют более половины (56%) от общего объема механических примесей, их доля в общей мощности трения практически не замечена. Как видно из рис. 5, мощность эрозионного воздействия на трубопровод во многом зависит также от скорости потока и с увеличением скорости растет.
Рис. 5.
Зависимость мощности трения от размеров механических примесей в промысловых трубопроводах при различных значениях скорости потока.
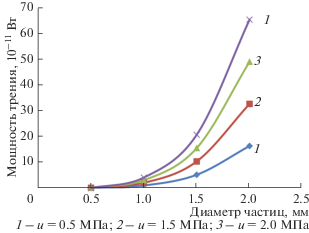
Эрозионное воздействие механических частиц основано на силах гравитации. Оно может быть предотвращено или в значительной мере ослаблено силами, имеющими противоположное направление, т.е. силы Бернулли, возникающее в пристенной области градиентно-скоростного поля [11]. Гидродинамическим режимом исключить контакт воды или механических частиц с поверхности трубопровода невозможно. Поэтому, для защиты трубопровода от эрозии твердыми частицами необходимо обеспечить вынос твердых частиц в ядро потока без контакта с поверхностью трубопровода. Для защиты трубопровода от коррозии при движении мультифазных систем необходимо и достаточно обеспечить эмульсионный режим движения, при котором градиент статического давления в потоке будет больше разности удельных весов механических частиц и нефти (или газа):
(6)
${{dP} \mathord{\left/ {\vphantom {{dP} {dr}}} \right. \kern-0em} {dr}} > \left( {{{\rho }_{{{\text{м}}{\text{.ч}}{\text{.}}}}} - {{\rho }_{{\text{г}}}}} \right)g.$Для определения скорости смеси, обеспечивающий защиту трубопровода (в частности газопровода) от коррозии, можно использовать зависимость (6), решенную относительно скорости. С учетом того, что максимальное значение (${{dP} \mathord{\left/ {\vphantom {{dP} {dr}}} \right. \kern-0em} {dr}}$)м = $16{{u}^{2}}\rho \alpha {{(1 - {{d}^{2}})} \mathord{\left/ {\vphantom {{(1 - {{d}^{2}})} D}} \right. \kern-0em} D}$ и подавляющее большинство эффектов эрозии (95%) создает фракция песка в основном размером $d > 0.5$ мм, тогда при $\alpha $ = 0.995 слой с толщиной 0.005D, который остается на дне трубопровода для коррозионно-эрозионного процесса практически никакой опасность не представляет ($\alpha $ = $\frac{r}{R}$ – относительная координата, равная отношению расстояния от оси потока до исследуемой точки, к половине диаметра поперечного сечения потока), для определения скорости переноса обеспечивающей защиту трубопровода от коррозии-эрозии получим:
(7)
$\vartheta = A\sqrt {\left( {1 - \frac{{{{\rho }_{{\text{г}}}}}}{{{{\rho }_{{{\text{м}}{\text{.ч}}{\text{.}}}}}}}} \right)D} ,$где А = 7.86 $\frac{{\sqrt {\text{м}} }}{{\text{с}}}.$
Согласно уравнению (7) была вычислена скорость переноса механических частиц в газовом потоке для различных диаметров газопровода (рис. 6). Как видно из рис. 6, скорость переноса с увеличением диаметра трубопровода монотонно растет.
ЗАКЛЮЧЕНИЕ
Скорость динамической коррозии мультифазных трубопроводов, которая иногда достигает до 20 мм/год будет определяется мощностью сил трения, величина которой определяется не столько количеством механических примесей, сколько их размером. Для снижения скорости коррозии примерно в 10 раз достаточно удалить из потока всего 1% наиболее крупных (более 1 мм) частиц. Для защиты мультифазных трубопроводов от эрозионно-коррозионных процессов необходимо обеспечить вынос твердых частиц и воды в ядро потока без контакта с поверхностью трубопровода. В частности для мультифазного газопровода была вычислена скорость переноса твердых механических частиц в ядре газового потока. Эффективным способом борьбы с динамической коррозией может стать удаление крупных частиц, поступающих в поток из нефтяных пластов методом фильтрации или гидроциклонной обработки потока в начале нефтегазопроводной сети.
Список литературы
Гужов А.И. Совместный сбор и транспорт нефти и газа. М.: Недра, 1973. С. 280.
Сулейманов А.Б., Кулиев Р.П. и др. Эксплуатация морских нефтегазовых месторождений. М.: Недра, 1986. С. 285.
Лутошкин Г.С. Сбор и подготовка нефти, газа и воды. М.: Недра. 1977. С. 192.
Маричев Ф.Н., Гетманский М.Д., Тетерина О.П. и др. // ВНИИОЕНГ, Коррозия и зашита в нефтегазовой промышленности. 1981. № 8. С. 44.
Бабенко А.П., Стрелец И.В. // Строительство уникальных зданий и сооружений. 2013. Т. 6. С. 11.
Искендеров Э.Х. // Сборник материалов Международной научно-практической конференции “Достижения, проблемы и перспективы развития нефтегазовой отрасли”. Т. 1. 25–28 октября 2017. Альметьевск, С. 443–447.
Ismayilov G.G., Iskandarov E.K. // Proceedings of the International Conference dedicated to the 90th anniversary of Academician Azad Khalil oglu Mirzajanzade, December 13–14, 2018. Baku, p. 444–446.
Нурмамедова Р.Г., Исмайылова Ф.Б. // Трубопроводный транспорт [теория и практика]. 2015. Т. 48. № 2. С. 22.
Манжосов В.К., Новикова О.Д., Новиков А.А. Теоретическая механика. Часть II. Динамика. Аналитическая механика / Ульяновский государственный технический университет. Ульяновск, 2011. С. 194.
Пустовойт Б.В. Механика движения жидкостей в трубах. М.: Недра, 1980. С. 160.
Лебедева Е.В., Ситенков В.Т. // Технология масел и топлив. 1999. № 1. С. 17–18.
Дополнительные материалы отсутствуют.
Инструменты
Физикохимия поверхности и защита материалов