Физикохимия поверхности и защита материалов, 2021, T. 57, № 2, стр. 160-165
Влияние процессов адсорбции на структурные и каталитические свойства никеля
А. В. Афинеевский 1, *, Д. А. Прозоров 1, **, Т. Ю. Осадчая 1, К. А. Никитин 1, А. В. Князев 2
1 ФГБОУ ВО “Ивановский государственный химико-технологический университет”
153000 Иваново, Шереметьевский просп., 7, Россия
2 ФГАОУ ВО “Национальный исследовательский Нижегородский государственный университет
им. Н.И. Лобачевского”
Нижний Новгород, просп. Гагарина, 23, Россия
* E-mail: afineevskiy@mail.ru
** E-mail: prozorovda@mail.ru
Поступила в редакцию 06.02.2020
После доработки 13.02.2020
Принята к публикации 20.02.2020
Аннотация
Изучено влияние условий проведения реакции жидкофазной гидрогенизации нитрогруппы на массивном никелевом катализаторе в бинарном растворе вода–спирт. Показано, что каждая стадия протекания каталитического процесса приводит к изменению структуры поверхности активного никеля. Исследовано влияние адсорбции водорода, адсорбции каталитического яда, химических актов на поверхности катализатора, а также гидродинамических условий протекания процесса на размер частиц катализатора, структуру и морфологию поверхности. Экспериментально доказано, что возникающая адсорбционно-каталитическая деформация приводит к росту скоростей восстановления соединений, содержащих нитрогруппу при низких степенях превращения.
ВВЕДЕНИЕ
На поверхности гетерогенных катализаторов реакций гидрогенизации протекает множество процессов, часть из которых идет с высвобождением значительного количества энергии. Известно, что процесс адсорбции водорода обладает высокими значениями теплот, в частности для скелетного никеля теплота адсорбции водорода может достигать –160 кДж/моль [1], теплота восстановления двойной связи >C=C< достигает значений –150 кДж/моль. Часто выделение такого количества тепла используется в установках адиабатического типа, где выделяющееся тепло расходуется на подогрев всей каталитической системы. Тем не менее, вследствие того, что большинство гетерогенных катализаторов имеет неоднородную поверхность – высвобождение таких значительных количеств энергии может приводить к локальным перегревам и другим побочным процессам, которые могут изменять структуру поверхности катализатора.
При исследовании каталитических процессов достаточно часто рассматривают состояние катализатора до его использования (свежеприготовленный) и после значительной нагрузки исследуемым процессом, при этом зачастую рассматриваются исключительно механические (физические) или химические причины возникновения деформаций и структурных изменений. Рассматривание же влияния физико-химических процессов, происходящих на поверхности часто остается за рамками проводимых исследований.
Однако, при исследовании адсорбентов, в частности, циклических нагрузок при адсорбции из газовой фазы на твердые адсорбенты, где нет движущихся элементов, рассмотрение именно влияния адсорбционной деформации в литературе встречается довольно часто [2, 3]. Экспериментально доказано, что процесс адсорбции реакционноспособных газов вызывает явление адсорбционных деформаций на твердых адсорбентах, размер которых зависит от природы адсорбата, адсорбента и внешних условий (температура и давления).
Очевидно, что на массивных металлических катализаторах такие эффекты будут проявляться значительно сильнее, чем на нанесенных, так как процессы, приводящие к адсорбционно-каталитической деформации, будут протекать преимущественно на активных центрах катализатора. В данной работе в качестве объекта исследования был использован массивный скелетный никель. Скелетный никель, как катализатор, был предложен Ренеем в начале двадцатого века, но, тем не менее, до сих остается одним из самых используемых в промышленности благодаря своей доступности, легкости изготовления, высокой активности и ряда других причин [4, 5].
Ранее были получены данные по теплотам адсорбции водорода на поверхности скелетного никеля. Анализ данных представленных в работах [6], свидетельствует, что при адсорбционно-калориметрических и потенциометрических исследованиях процесса адсорбции водорода имеют место побочные процессы, приводящие к значительным ошибкам в расчетах теплот адсорбции. Анализ материального баланса показал, что в системе присутствовали побочные процессы: окисление остаточного алюминия, адсорбция органического реагента-титранта на поверхности катализатора и другие возможные процессы, которые необходимо учитывать при описании таких сложных химических реакций, как процессы гидрогенизации.
Цель работы – рассмотреть влияние физико-химических процессов, происходящих на поверхности катализатора, на адсорбционно-каталитическую деформацию, и влияние ее на кинетические закономерности реакций жидкофазной гидрогенизации.
ЭКСПЕРИМЕНТАЛЬНАЯ ЧАСТЬ
Катализатор гидрирования
В работе был использован скелетный никелевый катализатор, полученный согласно патенту [7], адсорбционные и каталитические свойства соответствовали “классическому” скелетному никелю [8]. Катализатор готовили из никель-алюминиевого сплава состава Ni : Al = 49.5 : 50.5 мас. %. Для получения катализатора сплав измельчали на мельнице “Активатор-2SL”. Катализатор, полученный по данной методике, имел удельную площадь поверхности, определенную по низкотемпературной адсорбции аргона, 170 ± 2 м2/г, пористость 0.50 ± 0.05 см3/см3 катализатора, максимум функции распределения пор по радиусам, отвечающий среднему радиусу пор 2 нм, скелетный никель проявлял высокую каталитическую активность в реакциях восстановления органических соединений [9, 10].
Свежеприготовленный катализатор подвергался следующим воздействиям, позволяющим контролировать адсорбционные равновесия водорода, основа данного подхода по изучению катализаторов гидрогенизации описана в работах [4, 11]:
1. Насыщение каталитической системы водородом, при атмосферном давление, температуре, гидродинамических режимах соответствующих эксперименту;
2. Введение в систему дозированных количеств каталитического яда (в данной работе использовали сульфид натрия);
3. Использование различных растворителей для проведения каталитической реакции гидрогенизации (методика кинетического эксперимента подробно описана в работе [4]).
Методы исследования структурной чувствительности
Рентгенофазовый (РФА) анализ проводили на дифрактометре Bruker D8 Advance с использованием CuKα-излучения (λ = 0.15406 нм, 40 кВ, 20 мА, углы 2Θ = 10°–100°, скорость сканирования 4°/мин, дискретность – 0.01°). Для идентификации данных рентгенофазового анализа использовались кристаллографическая база данных МИНКРИСТ.
Лазерный анализ распределения частиц по размерам проводился на приборе Analysette 22 Compact.
Удельная поверхность определялась с помощью аппаратного комплекса “Sorbi MS”, методом низкотемпературной адсорбции азота по методу БЭТ.
Микрофотографии получены с помощью растрового электронного микроскопа VEGA 3 TESCAN.
Процесс гидрогенизации проводили статическим методом, в закрытой системе при интенсивном перемешивании жидкой фазы, исключающем влияние внешнего массопереноса на результаты эксперимента. Конструкция жидкостного реактора позволяла измерять скорость реакции гидрогенизации по объему водорода, поглощенному в ходе реакции, при интенсивном перемешивании реакционной среды. Параметры проведения гидрирования в данной работе: Объем реактора: 400 см3; Масса катализатора: 0.25–0.5 г; Растворитель: вода – 2-пропанола (0.073, 0.191, 0.68 мольные доли), объем растворителя: 95–110 мл; Температура проведения экспериментов: 303 K; Частота вращения лопастной мешалки составляла 4500 об./мин [12].
ОБСУЖДЕНИЕ РЕЗУЛЬТАТОВ
С помощью РФА были исследованы образцы катализатора: свежеприготовленного, после проведения гидрогенизации 4-нитротолуола, а также после адсорбции на поверхности катализатора сульфид-ионов. Рентгенограммы представлены на рис. 1.
Рис. 1.
Рентгенограммы свежеприготовленного скелетного никеля (1); после гидрогенизации 4-нт (2); сульфидированного никелевого катализатора с начальными концентрациями сульфида: –1 ммоль Na2S г–1 Ni (3).
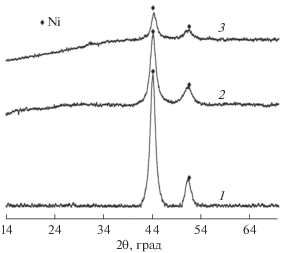
Анализ рентгенограмм, представленных на рис. 1, позволяет утверждать, что в результате любых процессов, протекающих на поверхности, увеличивается полуширина на полувысоте пика, и появляется гало, что свидетельствует об уменьшение размера частиц и их кристалличности. Проследить за изменением размера частиц позволяют функции распределения частиц по диаметру, рис. 2.
Рис. 2.
Распределение частиц скелетного никеля (%) по их диаметру (мкм): 1 – NiAl сплав на воздухе; 2 – после выщелачивания и промывки в воде; 3 – наводораживание в реакторе с водой; 4 – 0.05 ммоль Na2S/г Ni; 5 – 2 ммоль Na2S г–1 Ni; 6 – после гидрогенизации 4-нт.
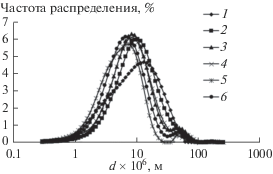
Для более наглядного результата влияния протекания реакции восстановления на изменения размеров частиц и морфологию поверхности катализатора была использована растровая электронная микроскопия (VEGA 3 Tescan). Результат приведен на рис. 3.
Рис. 3.
Микрофотографии свежеприготовленного скелетного никелевого катализатора и после проведения различных процессов на его поверхности. Размер поля обзора и по ширине, и по высоте составляет 31.4 мкм, шкала масштаба (белая линия в левом нижнем углу микрофотографии) – 5 мкм.
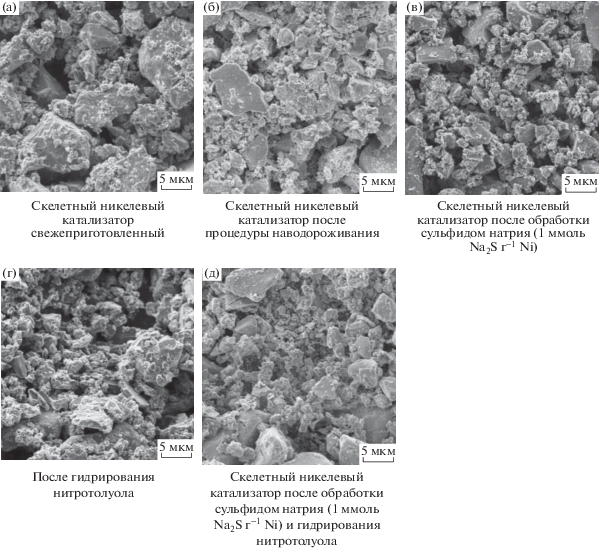
Анализ микрофотографий показывает, что свежеприготовленный катализатор имеет самое большое соотношение крупных частиц к мелким по сравнению с катализаторами, подвергшимися обработке. Данная закономерность хорошо коррелирует с аналогичной зависимостью функций распределения частиц по диаметру – рис. 2.
Сами частицы представляют из себя неправильные многогранники со скошенными краями и небольшой шероховатостью поверхности, при этом на многих частицах присутствуют трещины и сломы. На микрофотографиях можно условно разделить частицы на три группы: крупные (5–15 мкм), средние (2–5 мкм), мелкие (0.1–2 мкм). Свежеприготовленный катализатор содержит наибольшее число крупных частиц по сравнению с другими образцами, также в большом количестве представлены частицы среднего размера. После обработки водородом количество крупных частиц уменьшается и растет количество частиц среднего размера. Последующие обработки каталитическим ядом и протекание химической реакции приводят к почти полному удалению крупных частиц.
На основании полученных результатов были рассчитаны средние радиусы частиц катализатора после различных процессов, полученные данные были сведены в табл. 1.
Таблица 1.
Теплоты реакций гидрогенизации и адсорбции сульфид-иона и влияние этих процессов на адсорбционную деформацию
Полученные данные говорят о несомненном влиянии процессов, протекающих на поверхности катализатора, на структуру поверхности катализатора. Очевидно, что такие изменения должны отражаться не только на физическом состоянии катализатора, но и на его каталитических свойствах. Причем при восстановлении нитрогруппы такие изменения должны быть более существенными.
На рис. 4 представлены кинетические кривые скорости поглощения водорода в ходе гидрирования 4-нитротолуола на скелетном никелевом катализаторе. Из анализа кривой 1 на рис. 4 очевидно, что, либо идет смена механизма процесса, либо происходят побочные процессы, однако согласно данным литературы [15, 16] первое невозможно, а второе не может быть вызвано побочными химическими процессами. Таким образом, возникновение “горба” на кривой 1 (рис. 4) и последующее его исчезновение на кривых 2 и 3 может быть объяснено только возникновением побочных физико-химических процессов, которые имеют место только в первых двух случаях, а для третьего ввода реагента отсутствуют. Этому требованию идеально удовлетворяет вызванная в результате каталитических процессов (подход реагентов к границе раздела фаз, адсорбция, реакция на поверхности, десорбция и др.) адсорбционная деформация (далее для краткости адсорбционно-каталитическая деформация). Известно [17], что при измельчении частицы будет возрастать ее поверхностная энергия, этот рост предотвращает бесконечное измельчение частиц в заданных условиях среды. Исходя из этого, адсорбционно-каталитическая деформация может приводить к уменьшению размеров частиц только до определенных пределов, которые очевидно и достигаются на втором вводе (см. кривую 2 на рис. 4). Таким образом, при первом и втором вводе (рис. 4 кривые 1 и 2) возникает побочный физико-химический процесс – адсорбционно-каталитическая деформация – который приводит к раскалыванию частиц катализатора, что приводит к образованию новой поверхности на сколах. Очевидно, что эта вновь возникшая поверхность будет по своему составу и свойствам подобна исходному сплаву, из которого получен использованный нами скелетный никелевый катализатор. Эта вновь возникшая поверхность должна содержать никель и алюминий, при этом реакция гидрирования 4‑нитротолуола может протекать на такой поверхности [16, 18] и окислять алюминий, что должно приводить к временному увеличению активности катализатора, которая будет падать с окислением вновь возникшей поверхности.
Рис. 4.
Последовательное гидрирование 4-нитротолуола на одной порции катализатора. Растворитель: вода – 2-пропанола (0.073 мольная доля), Т = 303 К, n4-нт = = 4.4 × 10–3 моль/г. Ni, nДЭМК = 13.9 × 10–3 моль/г, Ni, mkat = 0.50 ± 0.01 г. α – степень превращения в системе.
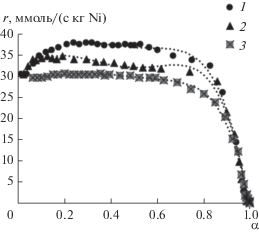
Согласно табл. 1 дезактивация катализатора сульфид-ионами также должна существенно влиять на поверхность катализатора. При этом во время адсорбционной деформации могут оголяться другие активные центры, что может приводить к другим эффектам, выраженным в увеличении активности катализатора. Поэтому было проведено исследование влияние введения дезактивирующего агента на активность катализатора (рис. 5).
Рис. 5.
Гидрирование 4-нитротолуола в растворе вода– изопропиловый спирт (концентрация спирта ◆ 1 – 0.073; ◼ 2 – 0.191; ▲ 3 – 0.68 мольных долей), при различном количестве введенного дезактивирующего агента. На графике буквой A обозначена активность, нормированная на свежеприготовленный недезактивированный катализатор, буквой C – нормированное количество дезактивирующего агента в долях от максимального количества, которое необходимого для полной дезактивации катализатора (1 ммоль Na2S г–1 Ni).
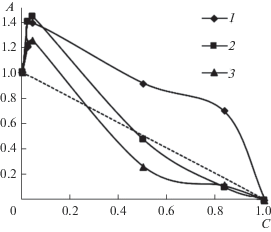
Согласно данным, представленным на рис. 6, площадь удельной поверхности возрастает с 169 до 259 м2/г Ni при введении в систему 0.3 ммоль S2–/г Ni. После достижения пороговой концентрации, когда сульфид блокирует все активные центры катализатора, значения удельной площади поверхности резко снижаются. Изменение радиуса частиц при сульфидировании катализатора подтверждают сделанные предположения. При малых количествах вводимого сульфида натрия радиус гранул катализатора резко снижается, что, по всей видимости, вызвано большими энергиями взаимодействия поверхностных атомов никеля с сульфид-ионами. После прохождения пороговой концентрации в 0.3 ммоль Na2S/г Ni, соответствующей максимальной удельной поверхности – падение замедляется.
ЗАКЛЮЧЕНИЕ
Условия проведения реакции жидкофазной гидрогенизации значительно влияют на возникновение адсорбционно-каталитической деформации. Учитывая вышесказанное, очевидно, что для процессов с высокими теплотами адсорбции и/или реакции необходимо учитывать адсорбционную деформацию при рассмотрении кинетики протекания этих процессов.
Экспериментальная часть выполнена в рамках лаборатории синтеза, исследований и испытания каталитических и адсорбционных систем для процессов переработки углеводородного сырья (созданной при поддержке Минобрнауки на 2020–2022 гг.). Теоретическая часть выполнена при финансовой поддержке гранта Президента для молодых ученых – кандидатов наук (проект МК-771.2020.3). План работ согласован с НИР Научного совета РАН по физической химии на 2020 (№ 20-03-460-27). Исследование проведено с использованием ресурсов Центра коллективного пользования научным оборудованием ФГБОУ ВО “ИГХТУ”.
Список литературы
Barbov A.V., Denisov S.V., Ulitin M.V. et al. // Russian J. Physical Chemistry A. 2007. V. 81. № 2. P. 272–276.
Школин А.В., Фомкин А.А., Синицын В.А. // Физикохимия поверхности и защита материалов. 2011. Т. 47. №. 5. С. 451–457.
Ребиндер П.А., Щукин Е.Д. // Успехи физических наук. 1972. Т. 108. №. 9. С. 3–42.
Прозоров Д.А., Афинеевский А.В., Князев А.В. и др. Каталитические свойства и дезактивация скелетного никеля в реакциях жидкофазной гидрогенизации // Под ред. Князева А.В. Казань: Бук, 2018. С. 316.
Навалихина М.Д., Крылов О.В. // Успехи химии. 1998. Т. 67. № 7. С. 656–687.
Кузнецов В.В., Осадчая Т.Ю., Афинеевский А.В. и др. // Российский химический журнал. 2018. Т. LXII. № 3. С. 29–38.
Прозоров Д.А., Афинеевский А.В., Никитин К.А. и др. / Пат. РФ 2669201 // опубл. 09.10.2018. Бюл. № 28.
Фасман А.Б., Леонард Е.В., Вишневский Е.А. и др. // Журн. физической химии. 1983. Т. 57. № 6. С. 1401–1403.
Улитин М.В., Лефедова О.В., Барбов А.В. и др. // Известия вузов. Химия и химическая технология. 2005. Т. 48. № 7. С. 62–72.
Прозоров Д.А., Афинеевский А.В., Осадчая Т.Ю. и др. // Известия вузов. Химия и химическая технология. 2017. Т. 60. №.6. С. 17–22.
Лукин М.В., Улитин М.В., Вдовин Ю.А. // Кинетика и катализ. 2013. Т. 54. № 4. С. 434.
Афинеевский А.В., Лукин М.В. // Катализ в промышленности. 2016. Т. 16. № 2. С. 6–10.
Födisch R., Hönicke D., Xu Y. et al. // Microreaction Technology. Springer Berlin Heidelberg. 2001. P. 470–478.
Glemser O. // Academic Press. 1963. N.Y. V. 2. P. 1551.
Захаров О.В., Улитин М.В., Комаров А.А. // Известия вузов. Химия и химическая технология. 2010. Т. 53. № 7. С. 85–89.
Лефедова О.В., Барбов А.В., Шаронов Н.Ю. и др. Теория и практика процессов жидкофазной гидрогенизации замещенных нитробензолов // Под ред. Койфмана О.И. М.: Красанд. 2016. С. 528.
Парфит Г., Рочестер К. Адсорбция из растворов на поверхностях твердых тел. М.: Мир. 1986. С. 347.
Ulitin M.V., Romanenko Y.E., Lefedova O.V. // Russian J. Physical Chemistry A. 2012. V. 86. № 6. P. 953–958.
Дополнительные материалы отсутствуют.
Инструменты
Физикохимия поверхности и защита материалов