Физикохимия поверхности и защита материалов, 2021, T. 57, № 3, стр. 312-321
Изучение коррозионного поведения модифицированных анодно-оксидных покрытий на сплаве алюминия АД31
М. А. Осипенко 1, *, Д. С. Харитонов 2, **, И. В. Макарова 3, В. И. Романовский 4, И. И. Курило 1
1 Белорусский государственный технологический университет
220006 Минск, ул. Свердлова, 13а, Беларусь
2 Jerzy Haber Institute of Catalysis and Surface Chemistry of Polish Academy of Sciences
30-239 Krakow, Niezapominajek, 8, Poland
3 Lappeenranta University of Technology
FI-53850 Lappeenranta, Skinnarilankatu, 34, Finland
4 Институт общей и неорганической химии Национальной академии наук Беларуси
220072 Минск, ул. Сурганова, 9/1, Беларусь
* E-mail: marikaosipenko@gmail.com
** E-mail: dmitry.kharitonov@ikifp.edu.pl
Поступила в редакцию 24.08.2020
После доработки 10.12.2020
Принята к публикации 12.01.2021
Аннотация
Методами сканирующей электронной микроскопии, потенциодинамической поляризации, электрохимической импедансной спектроскопии, а также испытаниями в камере соляного тумана установлены зависимости защитных свойств анодно-оксидных покрытий на сплавах алюминия АД31, модифицированных нитратами магния, калия и некоторых 3d-элементов, от составов растворов уплотнения и параметров финишной обработки. Предложен механизм формирования модифицированных анодно-оксидных покрытий в процессе уплотнения и последующей термической обработки.
ВВЕДЕНИЕ
В последние десятилетия особое внимание уделяется разработке легких, долговечных металлических материалов, обладающих высокими механическими и антикоррозионными свойствами. По этим показателям сплавы алюминия обладают значительными преимуществами перед другими широко применяемыми в технике металлами, например, сплавами магния.
Естественный анодно-оксидный слой, образующийся на поверхности сплавов алюминия при контакте с влагой и воздухом, обеспечивает достаточно хорошую антикоррозионную защиту во многих слабоагрессивных средах [1]. Тем не менее, при их промышленном использовании достаточно часто необходима более надежная антикоррозионная защита. Для этих целей широко применяется электрохимическое наращивание анодно-оксидного покрытия (АОП) с необходимой структурой, толщиной и твердостью.
Толщина и структура АОП определяются параметрами процесса анодирования: типом электролита, величиной напряжения или плотности тока, температурой, наличием перемешивания и др. [2]. Наиболее распространено анодирование в растворах кислот, в результате которого образуется покрытие, состоящее из внутреннего беспористого и внешнего пористого слоев [3]. Увеличение толщины АОП происходит с сохранением пористости и требует последующей герметизации (уплотнения, финишной обработки) для увеличения коррозионной устойчивости [4].
Традиционно уплотнение АОП проводят в горячей дистиллированной воде или растворах соединений хрома(VI). Однако перспективным является применение электролитов, содержащих менее опасные соединения [5]. В настоящее время разработан ряд новых способов и электролитов уплотнения АОП. Наиболее часто в промышленности используют способ высокотемпературного уплотнения в растворах фторида никеля [6]. Чахбун, Рокка и др. [7] предложили химическое уплотнение пористого оксидного слоя смесью солей Zr(IV) и Cr(III), что позволило повысить коррозионную стойкость поверхности примерно в 300 раз по сравнению со стандартным гидротермическим уплотнением. Синвэнь Юй и Чунянь Цао [8] показали эффективность использования для уплотнения АОП нитрата церия. В работе [9] была показана эффективность использования для уплотнения АОП перманганата калия.
Таким образом, практический интерес вызывает поиск экологически безопасных и экономически целесообразных растворов уплотнения для получения на алюминиевых сплавах модифицированных анодно-оксидных покрытий.
Целью данной работы являлось изучение влияния составов электролитов уплотнения и параметров финишной обработки на коррозионное поведение анодно-оксидных покрытий на сплаве алюминия АД31, модифицированных кальцием, магнием и некоторыми металлами 3d группы.
МЕТОДИКА ЭКСПЕРИМЕНТА
В качестве объектов исследования в данной работе был выбран сплав алюминия марки АД31 (АА6063). Анодирование проводили с использованием источника тока Элатек Б5-80 в течение 40 мин при комнатной температуре (≈22°С) и плотности тока 1 А/дм2 в сернокислом электролите, содержащем 2.0 моль/дм3 H2SO4, материал катодов – свинец. Перед проведением процесса образцы подготавливали в соответствии с ГОСТ 9.402–2004. Последующее уплотнение АОП проводили методом горизонтального погружения оксидированных образцов в рабочие растворы, содержащие одну из солей; Mg(NO3)2, Ca(NO3)2, Zn(NO3)2, Ni(NO3)2, Co(NO3)2 или Cu(NO3)2 в количестве 0.2 моль/дм3. Температура растворов составляла 100 ± 1°С, время уплотнения – 20 мин. После уплотнения образцы промывали в дистиллированной воде и сушили при помощи термовоздуходувки.
Финишную термическую обработку уплотненных образцов проводили в муфельной печи при температуре 300 ± 1°С, время обжига – 30 мин.
Элементный состав и морфологию покрытий изучали методами сканирующей электронной микроскопии (СЭМ) и энергодисперсионного рентгеновского микроанализа (EDX) с использованием микроскопа JEOL JSM–5610 LV, оснащенного системой химического микрорентгеноспектрального анализа EDX JED-2201.
Оценку коррозионной стойкости полученных покрытий в 0.5 М растворе хлорида натрия проводили с использованием потенциостата/гальваностата PGSTAT 302N (Methrom Autolab), оснащенного модулем импеданса FRA32M. В исследованиях использовали насыщенный хлоридсеребряный электрод в качестве электрода сравнения и платиновую сетку в качестве вспомогательного электрода. Потенциодинамические поляризационные кривые снимали в диапазоне потенциалов от –300 до +300 мВ от стационарного потенциала, скорость развертки потенциала составляла 1 мВ/с.
Спектры импеданса регистрировали в диапазоне частот 105–10–2 Гц с амплитудой колебаний тока 10 мВ. Анализ спектров, подбор эквивалентных схем и расчет параметров их элементов проводили с использованием ПО “ZView 3.2” и “Nova 2.1”.
Исследования полученных покрытий в камере соляного тумана S120is (ASCOTT) проводили в соответствии с ASTM B117–16. Испытанию подвергали одну сторону образца, оборотную изолировали кремнийорганическим лаком КО-85. Испытания проводили в 5% NaCl в течение 510 ч при температуре 35 ± 2°C. Для анализа состояния поверхности образцы периодически вынимали из камеры, промывали дистиллированной водой, сушили и фотографировали цифровой камерой Nikon D60.
РЕЗУЛЬТАТЫ И ИХ ОБСУЖДЕНИЕ
В процессе анодирования в растворе серной кислоты на поверхности сплава АД31 формировалось АОП серого цвета толщиной около 20 мкм. Микрофотографии поверхности полученных АОП, уплотненных в растворах Mg(NO3)2, Ca(NO3)2, Zn(NO3)2, Ni(NO3)2, Co(NO3)2, Cu(NO3)2 без и с последующей термической обработкой представлены на рис. 1 и рис. 2 соответственно.
Рис. 1.
Микрофотографии АОП, уплотненных в 0.2 М растворах: (а) Mg(NO3)2, (б) Ca(NO3)2, (в) Zn(NO3)2, (г) Ni(NO3)2, (д) Co(NO3)2, (е) Cu(NO3)2.
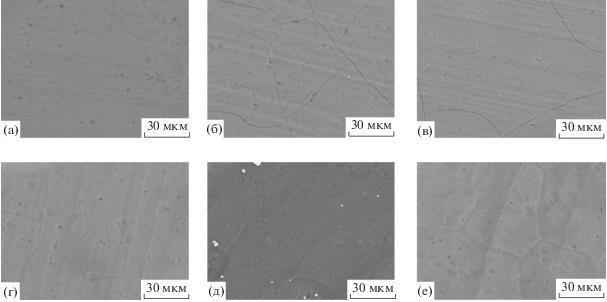
Рис. 2.
Микрофотографии АОП, уплотненных в 0.2 М растворах: (а) Mg(NO3)2, (б) Ca(NO3)2, (в) Zn(NO3)2, (г) Ni(NO3)2, (д) Co(NO3)2, (е) Cu(NO3)2 после обжига в течение 30 мин при температуре 300°С.
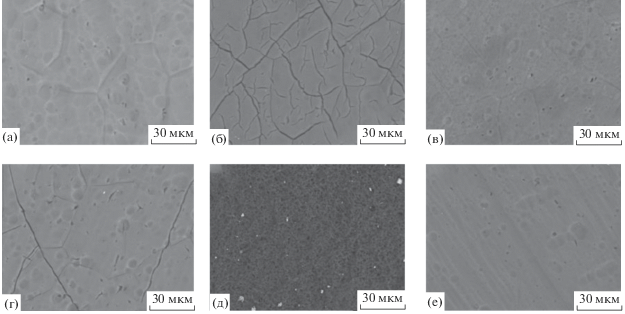
Как видно из анализа микрофотографий, уплотнение АОП в растворах исследуемых нитратов приводит к формированию покрытий с большим количеством микровключений (рис. 1а–1д). Для всех покрытий характерна неоднородная структура, при этом на поверхности некоторых образцов присутствуют углубления и трещины.
Исследуемый сплав АД31 содержит в своем составе легирующие добавки в виде анодных и катодных интерметаллических частиц [9–12]. Селективное растворение данных частиц в процессе анодирования может оказывать существенное влияние на микроструктуру АОП. Различие химического состава алюминиевой матрицы и интерметаллических частиц сплава приводит к изменению морфологии пор, появлению дефектов и трещин, вызванных избыточными остаточными внутренними напряжениями в сформированном оксидном слое [12–14]. Необходимо отметить, что предварительная промывка слоя АОП дистиллированной водой приводит к тому, что на начальном этапе уплотнения температура в глубине пор меньше, чем у поверхности, что может способствовать возникновению механических напряжений и растрескиванию АОП [14–16].
Термическая обработка уплотненных АОП может приводить к кристаллизации аморфного оксидного слоя и модифицирующей добавки, оказывая значительное влияние на микроструктуру и защитные свойства сформированных покрытий. На микрофотографиях поверхности образцов после обжига при температуре 300°С в течение 30 мин заметно увеличение общей неоднородности поверхности покрытий, появление локальных дефектов и увеличение количества микротрещин (рис. 2). Это, вероятно, объясняется увеличением хрупкости покрытия и его растрескиванием в процессе обжига [16, 17].
Анализ элементного состава модифицированных АОП методом EDX показал (табл. 1), что сформированные АОП преимущественно состоят из алюминия, кислорода и серы. Значительное содержание серы в структуре покрытия обусловлено использованием сернокислого электролита анодирования. Содержание основного компонента модифицирующего раствора (металла) в структуре АОП составило от 0.30 до 13.4 мас. % в зависимости от состава электролита уплотнения. Проведение термической обработки при температуре 300°С приводит к увеличению содержания модифицирующего компонента в структуре покрытия на 0.30–0.50 мас. %.
Таблица 1.
Элементный состав поверхности сплава АД31 после анодирования и наполнения в растворах нитратов
Условия обработки | Элементный состав поверхности АОП, мас. % | ||||||||
---|---|---|---|---|---|---|---|---|---|
Al | S | O | Mg | Ca | Zn | Ni | Co | Cu | |
Mg(NO3)2 | 63.3 | 10.4 | 26.0 | 0.3 | – | – | – | – | – |
Ca(NO3)2 | 66.2 | 11.5 | 21.9 | – | 0.4 | – | – | – | – |
Zn(NO3)2 | 52.5 | 15.7 | 18.4 | – | – | 13.4 | – | – | – |
Ni(NO3)2 | 58.6 | 18.2 | 15.0 | – | – | – | 8.2 | – | – |
Co(NO3)2 | 56.6 | 17.3 | 16.0 | – | – | – | – | 10.1 | – |
Cu(NO3)2 | 57.7 | 17.1 | 19.1 | – | – | – | – | – | 6.1 |
Mg(NO3)2 + обжиг | 59.9 | 12.4 | 27.1 | 0.6 | – | – | – | – | – |
Ca(NO3)2 + обжиг | 63.5 | 12.8 | 23.0 | – | 0.7 | – | – | – | – |
Zn(NO3)2 + обжиг | 52.9 | 13.4 | 19.9 | – | – | 13.8 | – | – | – |
Ni(NO3)2 + обжиг | 54.2 | 20.6 | 16.4 | – | – | – | 8.8 | – | – |
Co(NO3)2 + обжиг | 51.9 | 18.7 | 18.8 | – | – | – | – | 10.6 | – |
Cu(NO3)2 + обжиг | 54.2 | 19.5 | 19.9 | – | – | – | – | – | 6.4 |
Коррозионную стойкость АОП изучали электрохимическими методами. Потенциодинамические поляризационные кривые полученных АОП представлены на рис. 3.
Рис. 3.
Потенциодинамические поляризационные кривые образцов АОП в 0.5 М растворе NaCl: составы 0.2 М растворов электролитов уплотнения АОП: 1 – Mg(NO3)2, 2 – Ca(NO3)2, 3 – Zn(NO3)2, 4 – Ni(NO3)2, 5 – Co(NO3)2, 6 – Cu(NO3)2, 7 – без уплотнения. (а) До обжига, (б) после обжига.
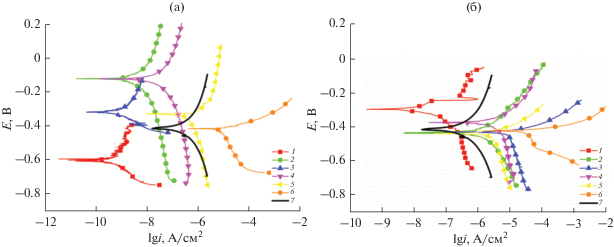
Уплотнение в растворах нитратов оказывает значительное влияние на значения бестокового потенциала образцов АОП в 0.5 M растворе NaCl. Для всех образцов АОП, за исключением покрытий, уплотненных в растворах Mg(NO3)2 и Cu(NO3)2, наблюдалось смещение бестокового потенциала в электроположительную область по сравнению с образцом без уплотнения. Это свидетельствует об эффективном внедрении модифицирующих компонентов в структуру АОП.
В случае уплотнения в растворе Cu(NO3)2 значение бестокового потенциала практически не изменилось, а в растворе Mg(NO3)2 – сместилось в электроотрицательную область на 150 ± 5 мВ. Для всех образцов АОП, за исключением уплотненных в растворе Cu(NO3)2, наблюдается уменьшение значений плотностей токов коррозии, а, следовательно, увеличение защитных свойств по сравнению с образцом без уплотнения (табл. 2). Это объясняется заполнением модифицирующим раствором пор АОП, образующихся в процессе сернокислого анодирования. Уплотнение обеспечивает закупоривание пор и герметизацию оксидного слоя поверхности образца. Наименьшие значения плотности тока коррозии были получены для образцов АОП, уплотненных в растворах нитратов магния, кальция и цинка (5.99 × 10−12, 7.39 × 10−11 и 1.18 × 10−10 А/см2 соответственно).
Таблица 2.
Электрохимические параметры, полученные из анализа потенциодинамических поляризационных кривых
Условия обработки | ak, В | |bk|, В | ba, В | aa, В | iкорр, А см–2 | Eкорр, В | EI, % |
---|---|---|---|---|---|---|---|
Mg(NO3)2 | −0.010 | 0.705 | 0.007 | −0.519 | 5.99 × 10−12 | –0.250 | 99.9 |
Ca(NO3)2 | −0.009 | 0.218 | 0.009 | −0.032 | 7.39 × 10−11 | –0.697 | 99.903 |
Zn(NO3)2 | −0.014 | 0.462 | 0.021 | −0.118 | 1.18 × 10−10 | –0.476 | 99.846 |
Ni(NO3)2 | −0.023 | 0.323 | 0.011 | −0.026 | 1.43 × 10−9 | –0.744 | 98.128 |
Co(NO3)2 | −0.016 | 0.452 | 0.009 | −0.268 | 4.12 × 10−8 | –0.457 | 46.073 |
Cu(NO3)2 | −0.011 | 0.483 | 0.022 | −0.303 | 2.95 × 10−6 | –0.378 | – |
Mg(NO3)2 + обжиг | −0.021 | 0.370 | 0.015 | −0.020 | 1.26 × 10−10 | –0.687 | 99.8 |
Ca(NO3)2 + обжиг | −0.005 | 0.481 | 0.014 | −0.332 | 2.65 × 10−8 | –0.364 | 65.314 |
Zn(NO3)2 + обжиг | −0.020 | 0.482 | 0.020 | −0.191 | 3.76 × 10−8 | –0.462 | 50.785 |
Ni(NO3)2 + обжиг | −0.005 | 0.481 | 0.014 | −0.332 | 2.65 × 10−8 | –0.364 | 65.314 |
Co(NO3)2 + обжиг | −0.021 | 0.511 | 0.017 | −0.261 | 2.82 × 10−7 | –0.423 | – |
Cu(NO3)2 + обжиг | −0.032 | 0.586 | 0.015 | −0.350 | 9.29 × 10−6 | –0.377 | – |
Без уплотнения | –0.927 | 0.072 | 0.0801 | –0.159 | 7.64 × 10‒8 | –0.408 | – |
Защитный эффект модифицирующих растворов уплотнения, вероятно, обусловлен гидролизом нитратов с образованием малорастворимых основных солей, закупоривающих поры АОП.
Проведение термической обработки модифицированных АОП значительно изменяет их коррозионное поведение (рис. 3б). В данном случае значения бестокового потенциала образцов в 0.5 M растворе NaCl отличаются не более чем на 50 ± 5 мВ по сравнению с образцом без уплотнения, за исключением образца, уплотненного в растворе Mg(NO3)2, для которого бестоковый потенциал смещается в электроположительную сторону на 280 ± 5 мВ. Анализ полученных поляризационных кривых показал, что термообработка приводит к увеличению значений плотностей токов коррозии по сравнению с образцами без термообработки и, соответственно, снижению защитной способности покрытий. Это может быть связано с растрескиванием поверхности в результате теплового воздействия. Появление дефектов приводит к облегчению проникновения хлорид-ионов в структуру АОП, что ускоряет его коррозионное разрушение.
Наибольшим значением плотности тока коррозии (табл. 2), а, следовательно, наименьшей коррозионной устойчивостью обладают образцы, уплотненные в растворах нитратов меди и кобальта, для которых плотности тока коррозии iкорр равны соответственно 2.95 × 10−6 и 4.12 × 10−8 А/см2. Это может быть связано с тем, что обработка в горячих растворах уплотнения приводит к усилению процессов гидролиза модифицирующих компонентов и образованию в порах их основных солей и гидроксидов. Длительное термическое воздействие приводит к разложению присутствующих в порах соединений и образованию соответствующих оксидов. Так как образующиеся частицы оксидов обладают низкой адгезионной способностью к поверхности АОП, а их размеры сопоставимы с размерами пор, то они не обеспечивают полного закрытия пор, что снижает коррозионную стойкость АОП.
Эффективность уплотнения АОП оценивали по значениям защитного эффекта, рассчитанного по формуле [17, 18]:
(1)
$EI,\% = \frac{{i_{{{\text{корр}}}}^{0} - i_{{{\text{корр}}}}^{{}}}}{{i_{{{\text{корр}}}}^{0}}} \times 100,$Как видно из данных табл. 2, для уплотненных в растворах Mg(NO3)2, Ca(NO3)2, Zn(NO3)2, Ni(NO3)2 образцов без последующей термообработки ингибирующий эффект составляет ≈99%. Для АОП, модифицированных в растворах Co(NO3)2, Cu(NO3)2, он значительно ниже и достигает отрицательных значений. Это свидетельствует о нецелесообразности применения финишной термообработки при формировании АОП на сплавах алюминия.
Результаты импедансной спектроскопии полученных образцов представлены на рис. 4 в виде диаграмм Найквиста. Для образцов АОП, модифицированных в исследуемых растворах уплотнения, можно выделить две временные константы (рис. 4а). Первая константа в области высоких и средних частот представляет собой полуокружность, что характерно для электрохимических процессов с лимитирующей стадией переноса заряда. В области низких частот на спектрах всех модифицированных образцов присутствует участок спектра, наклоненный к оси абсцисс под углом 45°, что характерно для процессов с лимитирующей стадией диффузии. В процессе анодирования и уплотнения пористый слой АОП заполняется водными электролитами, характеризующимися высокими значениями электрической проводимости [13, 14]. В связи с этим, верхней границы используемого диапазона частот может быть недостаточно для регистрации отклика внешнего пористого слоя АОП, а полученная зависимость реальной и мнимой частей импеданса от частоты описывает коррозионные процессы в глубине пор.
Рис. 4.
Результаты импедансной спектроскопии в виде диаграмм Найквиста. Составы 0.2 М растворов электролитов уплотнения АОП: 1 – Mg(NO3)2, 2 – Ca(NO3)2, 3 – Zn(NO3)2, 4 – Ni(NO3)2, 5 – Co(NO3)2, 6 – Cu(NO3)2, 7 – без уплотнения. (а) До обжига, (б) после обжига.
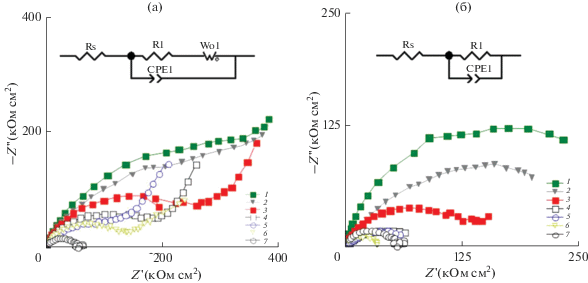
Термообработка образцов приводит к изменению характера спектров импеданса: на диаграммах Найквиста можно выделить одну временную константу в форме полуокружности (рис. 4б). Полученные спектры описывают сопротивление и емкостной отклик барьерного слоя АОП, что характерно для термообработанных покрытий [16, 17].
Экспериментальные данные описывали эквивалентными схемами, в которых: Rs – сопротивление электролита, Ом см2; R1 – сопротивление слоя АОП, Ом см2; СPE1 – элемент постоянной фазы, описывающий емкостной отклик слоя АОП; W – элемент Варбурга. Импеданс элемента постоянной фазы описывается двумя параметрами: константой Y1, Ом–1 см–2 cn, и математическим фактором n. Диффузионный элемент Варбурга включает в себя активную WR, Ом см2, и реактивную W, Ом–1 см–2 cn, части, а также математический фактор n = 0.5. Результаты подбора параметров эквивалентных схем представлены в табл. 3.
Таблица 3.
Параметры эквивалентных схем, полученные из анализа спектров импедансной спектроскопии
Вид обработки | R1, Ом см2 | Y1, Ом–1 см–2 cn | n1 | WR, Ом см2 | W, Ом–1 см–2 cn | EI, % |
---|---|---|---|---|---|---|
Mg(NO3)2 | 372 680 | 3.302 × 10–8 | 0.812 | 380 960 | 0.798 | 93.04 |
Ca(NO3)2 | 351 580 | 1.014 × 10–8 | 0.864 | 371 380 | 0.531 | 92.74 |
Zn(NO3)2 | 212 050 | 1.2232 × 10–8 | 0.832 | 340 960 | 0.407 | 90.51 |
Ni(NO3)2 | 158 690 | 3.553 × 10–8 | 0.822 | 277 770 | 0.880 | 87.98 |
Co(NO3)2 | 143 340 | 3.4438 × 10–8 | 0.787 | 238 700 | 0.314 | 86.27 |
Cu(NO3)2 | 83 017 | 1.515 × 10–8 | 0.780 | 213 970 | 0.710 | 82.34 |
Mg(NO3)2 + обжиг | 253 010 | 5.189 × 10–7 | 0.753 | – | – | 79.27 |
Ca(NO3)2 + обжиг | 233 010 | 1.4554 × 10–7 | 0.690 | – | – | 77.45 |
Zn(NO3)2 + обжиг | 135 050 | 2.6536 × 10–7 | 0.588 | – | – | 61.17 |
Ni(NO3)2 + обжиг | 59 457 | 8.1454 × 10–7 | 0.641 | – | – | 11.8 |
Co(NO3)2 + обжиг | 51 504 | 7.8932 × 10–7 | 0.644 | – | – | – |
Cu(NO3)2 + обжиг | 32 581 | 2.1329 × 10–7 | 0.865 | – | – | – |
Без уплотнения | 52 436 | 2.2688 × 10–7 | 0.871 | – | – | – |
Сравнение значений сопротивления пористого слоя АОП (R1) показало, что для образцов без обжига этот параметр значительно больше, чем для обработанных образцов, что свидетельствует о большем защитном эффекте и согласуется с данными поляризационных исследований.
Эффективность уплотнения АОП образцов оценивали по значениям защитного эффекта, рассчитанного по формуле:
где $({{R}_{1}} + {{W}_{R}})$, $R_{1}^{0}$– значения сопротивление слоя АОП модифицированного образца и образца сравнения (анодированный сплав алюминия без уплотнения) соответственно.Все полученные образцы также подвергались ресурсным испытаниям в камере соляного тумана в течение 510 ч. На рис. 5 представлены фотографии образцов сплава алюминия АД31 до и после испытаний. В результате уплотнения на поверхности формируется оксидная пленка с характерным матовым окрасом, интенсивность которого уменьшается с увеличением времени коррозионных испытаний в камере соляного тумана. Уплотненные термически не обработанные образцы показали высокую устойчивость в хлоридсодержащей среде. Даже после 510 ч испытаний структура их поверхности практически не изменилась, очагов коррозии не зафиксировано.
В свою очередь, для термически обработанных образцов уже после 48 ч коррозионных испытаний на поверхности присутствует большое количество очагов питтинговой коррозии, а через 510 ч – практически вся поверхность образцов покрыта большим количеством продуктов коррозии белого цвета.
На основании результатов проведенных исследований был предложен механизм уплотнения оксидного слоя, полученного на сплаве АД31 в ходе сернокислого анодирования (рис. 6а).
Использование серной кислоты при анодировании обусловливает наличие в структуре АОП значительного количества сульфат-ионов, которые в процессе уплотнения АОП нитратом кальция могут вступать в реакцию ионного обмена с ионами Ca2+ и закрывать поры образующимся малорастворимым сульфатом (рис. 6б):
(3)
${\text{C}}{{{\text{a}}}^{{{\text{2 + }}}}}\,\,{\text{ + }}\,\,{\text{SO}}_{{\text{4}}}^{{2 - }} \to CaS{{O}_{4}}.$Обжиг АОП, модифицированных солями кальция, приводит к формированию в порах “мертвого гипса”.
Нитраты и сульфаты двухвалентных металлов, образованные сильной кислотой и слабым основанием, активно подвергаются гидролизу с образованием соответствующего катиона MeOH+:
(4)
${\text{M}}{{{\text{e}}}^{{2 + }}} + \,\,{{{\text{H}}}_{{\text{2}}}}{\text{O}}\,\, \Leftrightarrow \,\,{\text{MeO}}{{{\text{H}}}^{ + }} + {{{\text{H}}}^{ + }}.$Так как значение константы электролитической диссоциации гидроксида меди по второй ступени составляет Kд = 10–7, что на 2–3 порядка меньше, чем для гидроксидов других рассматриваемых металлов, соли меди подвергаются гидролизу в большей степени. Нагрев растворов уплотнения приводит к усилению процессов гидролиза, а также способствует разложению образующихся малорастворимых оснований и основных солей с образованием соответствующих оксидов и средних солей.
(5)
${\text{Me(OH}}{{{\text{)}}}_{{{\text{2 }}}}}\xrightarrow{t}{\text{MeO}} + {{{\text{H}}}_{2}}{\text{O,}}$(6)
${{({\text{MeOH)}}}_{{\text{2}}}}{\text{S}}{{{\text{O}}}_{{\text{4}}}}\,\, \to \,\,{\text{MeS}}{{{\text{O}}}_{{\text{4}}}}\,\,{\text{ + }}\,\,{\text{MeO}}\,\,{\text{ + }}\,\,{{{\text{H}}}_{{\text{2}}}}{\text{O,}}$(7)
$2{\text{MeOHN}}{{{\text{O}}}_{{\text{3}}}}\,\, \to \,\,{\text{Me(N}}{{{\text{O}}}_{3}}{{{\text{)}}}_{2}}\,\,{\text{ + }}\,\,{\text{MeO}}\,\,{\text{ + }}\,\,{{{\text{H}}}_{{\text{2}}}}{\text{O}}{\text{.}}$Образующиеся соли меди, цинка, никеля и кобальта хорошо растворимы в воде, а их оксиды характеризуются низкой адсорбционной способностью по отношению к оксиду алюминия. В результате образующиеся соединения этих металлов могут переходить из пор в раствор с образованием дефектов в бемитной структуре оксидного слоя. При этом пора остается незакрытой, что объясняет процесс диффузии агрессивных хлорид-ионов к алюминиевой матрице (рис. 6в).
При использовании для уплотнения растворов нитрата магния в составе модифицированных АОП формируются малорастворимые гидроксиды и оксиды магния с достаточно высокой адсорбционной способностью к пористому слою оксида алюминия. Это приводит к формированию более плотных АОП, обеспечивающих надежную защиту алюминиевой подложки от агрессивного воздействия окружающий среды.
Последующая термическая обработка уплотненных АОП способствует разложению присутствующих в порах солей и образованию дополнительных количеств модифицирующих оксидов исследуемых металлов. Однако из-за существенной разности коэффициентов объемного расширения алюминиевой матрицы и сформированного покрытия термическая обработка приводит к растрескиванию АОП и образованию в их структуре локальных дефектов (рис. 6г), что в целом существенно снижает защитные свойства поверхности.
ВЫВОДЫ
1. Согласно данным СЭМ, в процессе уплотнения анодированных сплавов алюминия АД31 на поверхности образцов формируются покрытия с большим количеством микровключений. Проведение последующей термической обработки приводит к увеличению общей неоднородности поверхности покрытия, появлению локальных дефектов и увеличению количества микротрещин в структуре покрытия, что объясняется существенным различием значений коэффициентов теплового расширения алюминиевой матрицы и оксидного слоя.
2. Результаты EDX анализа показали, что основными компонентами сформированных покрытий являются алюминий, кислород и сера. Содержание модифицирующих металлов в структуре АОП составляло от 0.30 до 13.40 мас. % в зависимости от состава электролита уплотнения. Проведение термической обработки при температуре 300°С приводит к увеличению содержания модифицирующего компонента в структуре покрытия на 0.30–0.50 мас. %.
3. Поляризационные исследования показали, что для АОП, уплотненных в растворах Mg(NO3)2, Ca(NO3)2, Zn(NO3)2, Ni(NO3)2, ингибирующий эффект составляет ≈99%. Последующая термическая обработка негативно сказывается на коррозионной устойчивости образцов (защитный эффект не превышает 65%), что обусловлено растрескиванием АОП и образованием в их структуре локальных дефектов.
4. Испытания в камере соляного тумана в течение 510 ч показали, что для образцов АОП, модифицированных катионами кальция, магния и некоторых переходных 3d-элементов, в отсутствии последующей термической обработки очагов коррозии не обнаружено. Для модифицированных АОП, термически обработанных при температуре 300°С в течение 30 мин, уже через 48 ч испытаний на поверхности зафиксированы очаги точечной коррозии, а через 510 ч – практически вся поверхность образцов была покрыта большим количеством продуктов коррозии белого цвета.
Список литературы
Evertsson J., Bertram F., Rullik L., Harlow G., Lundgren E. Anodization of Al (100), Al (111) and Al Alloy 6063 studied in situ with X-ray reflectivity and electrochemical impedance spectroscopy // J. Electroanal. Chem. 2017. V. 799. P. 556–562.
Stojadinović S., Vasilić R., Kasalica B., Belča I., Zeković L. Luminescence During the Electrochemical Oxidation of Aluminum. In: Djokić S. (eds) Electrodeposition and Surface Finishing. Modern Aspects of Electrochemistry. 2014. V. 57. Springer, New York, NY. https://doi.org/10.1007/978-1-4939-0289-7_5.
Zhang F., Nilsson J., Pan J. In Situ and Operando AFM and EIS Studies of Anodization of Al 6060 : Influence of Intermetallic Particles // J. Electrochemical Society. 2016. V. 163. № 9. P. C609–C618.
Jeong C., Lee J., Sheppard K., Choi C. Air-Impregnated Nanoporous Anodic Aluminum Oxide Layers for Enhancing the Corrosion Resistance of Aluminum // Langmuir. 2015. V. 31. P. 11040−11050.
Hao L., Cheng R. Sealing processes of anodic coatings -Pa.t. Pre.ent. and Future // Metal Finishing, 2000. V. 98. P. 8–18, 2000.
Ofoegbu S.U., Fernandes F.A.O., Pereira A.B. The Sealing Step in Aluminum Anodizing : A Focus on Sustainable Strategies for Enhancing both Energy Efficiency and Corrosion Resistance // Coatings. 2020. V. 10. P. 226.
Chahboun N., Rocca E., Veys-Renaux D., Augros M., Boutoba M., Caldeira N. Sealing of Anodized Multiphase Aluminum Alloys with Cr(+III)/Zr(+IV) Salts: Characterization and Corrosion Behavior // J. Electrochem. Soc. 2016. V. 163. № 3. P. C69–C75.
Yu X., Cao C. Electrochemical study of the corrosion behavior of Ce sealing of anodized 2024 aluminum alloy // Thin Solid Films. 2003. V. 423. P. 252–256.
Osipenko M.A., Kharitonov D.S., Makarova I.V., Wrzesińska A., Kurilo I.I. // Prot. Met. Phys. Chem. Surf. 2020. V. 56. P. 990–997.
Kharitonov D.S. et al. Corrosion Inhibition of Aluminum Alloy AA6063-T5 by Vanadates : Microstructure Characterization and Corrosion Analysis // J. Electrochemical Society, 2018. V. 165. № 3. P. 116–126.
Kharitonov D.S. et al. Surface and corrosion properties of AA6063-T5 aluminum alloy in molybdate-containing sodium chloride solutions // Corros. Sci. 2020. V. 171. P. 108658.
Kharitonov D.S. et al. // Prot. Met. Phys. Chem. Surf. 2020. V. 56. P. 113–124.
Liu W., Zuo Y., Chen S., Zhao X., Zhao J. The effects of sealing on cracking tendency of anodic fi lms on 2024 aluminum alloy after heating up to 300°C // Surf. Coat. Technol., 2009. V. 203. № 9. P. 1244–1251.
Balaraju J.N., Srinivasan A., Yoganandan G., Grips V.K.W., Rajam K.S. Effect of Mn/Mo incorporated oxide layer on the corrosion behavior of AA 2024 alloy // Corros. Sci. 2011. V. 53. № 12. P. 4084–4092.
Runge J.M. Anodizing as an Industrial Process. In: The Metallurgy of Anodizing Aluminum. 2018. Springer, Cham. https://doi.org/10.1007/978-3-319-72177-4_3.
Donahue C.J., Exline J.A. Anodizing and Coloring Aluminum Alloys // J. Chem. Educ. 2014. V. 91. P. 711–715.
Chang J., Lin C., Liao C., Chen C. Effect of Heat-Treatment on Characteristics of Anodized Aluminum Oxide Formed in Ammonium Adipate Solution // J. Electrochemical Society. 2004. V. 151. P. B188.
Amin M.A., Ei-rehim S.S.A., El-sherbini E.E.F., Hazzazi O.A., Abbas M.N. Polyacrylic acid as a corrosion inhibitor for aluminium in weakly alkaline solutions . Part I : Weight loss, polarization, impedance EFM and EDX studies // Corros. Sci. 2009. V. 51. № 3. P. 658–667.
Дополнительные материалы отсутствуют.
Инструменты
Физикохимия поверхности и защита материалов