Физикохимия поверхности и защита материалов, 2022, T. 58, № 5, стр. 526-536
Влияние энергии разрядных импульсов при электроискровом осаждении аморфных покрытий
А. А. Бурков *
ФГБУН Институт материаловедения Хабаровского научного центра ДВО РАН
680042 Хабаровск, ул. Тихоокеанская, 153, Россия
* E-mail: burkovalex@mail.ru
Поступила в редакцию 20.07.2021
После доработки 30.05.2022
Принята к публикации 06.06.2022
- EDN: BYCXXM
- DOI: 10.31857/S0044185622050059
Аннотация
В работе представлены результаты исследования аморфного покрытия на подложке из стали 35, приготовленного электроискровым осаждением в смеси железных гранул с порошком CBCrSiMoW. С ростом длительности разрядов повышалось содержание железа в составе покрытий, что приводило к снижению доли аморфной фазы с 67 до 50 об. %. Аморфное покрытие имело в 23 раза более высокую стойкость к окислению при температуре 700°C по сравнению со сталью 35. Поляризационные испытания образцов в 3.5% растворе NaCl показали возрастание плотности тока коррозии с ростом длительности импульсов выше 200 мкс. Микротвердость покрытий находилась в диапазоне от 399 до 759 HV. Средние значения скорости износа покрытий в условиях сухого скольжения находились в диапазоне от 1.6 × 10–6 до 10.9 × 10–6 мм3/Нм, что от 4 до 22 раз ниже, чем у стали 35 без покрытия. Наибольший коэффициент трения и скорость изнашивания наблюдались для покрытия, полученного при наиболее длинных импульсах из-за наименьшей концентрации аморфной фазы. Результаты работы показали, что оптимальная длительность разрядных импульсов, для обеспечения достаточной толщины покрытий и приемлемого содержания аморфной фазы, находится в диапазоне от 50 до 200 мкс.
1. ВВЕДЕНИЕ
Металлические стекла (МС) – это аморфные металлические материалы, обладающие улучшенными магнитными, электрохимическими, трибологическими и каталитическими свойствами [1–4], а также радиационной-стойкостью, биосовместимостью и нецитотоксичностью [5–7]. Покрытия из МС на основе железа привлекают внимание исследователей и инженеров, поскольку они улучшают твердость, жаростойкость и коррозионную устойчивость стальных изделий [8, 9]. Для получения МС покрытий используются различные технологии, такие как магнетронное напыление, лазерная наплавка, плазменное распыление, гальванику и электроискровое легирование (ЭИЛ) [10–15]. Технология ЭИЛ основана на переносе материала анода на поверхность катода при воздействии множества коротких (~10–4 с) электрических разрядов. Среди вышеперечисленных методов ЭИЛ характеризуется минимальным тепловым воздействием на материал подложки, не требует дорогостоящего оборудования и поддержания вакуума, а полученные покрытия выгодно отличаются высокой адгезией к подложке за счет металлургической связи покрытия с подложкой [15–18].
Обычно процесс ЭИЛ выполняется на установках, оснащенных ручным держателем электрода. Ранее нами была показана возможность автоматизированного ЭИЛ с использования смеси порошков металлов (W, Mo, Cr) и неметаллов (Si, C, SiB4) для осаждения аморфных покрытий с анодом их железных гранул [19]. Железные гранулы и стальная подложка выступали в качестве источника железа для МС. При прохождении разряда между гранулой и подложкой, порошок электростатически зафиксированный на их поверхности вводится в микрованну расплава. Это сопровождается конвективным и диффузионным перемешиванием элементов до гомогенного состояния. Из-за высокой скорости охлаждения материала после прекращения разряда до 105–106 К/с происходит фиксация аморфной структуры из многокомпонентного расплава с высокой стеклообразующей способностью. Известно, что энергия разрядов может оказывать влияние на условия охлаждения материала при ЭИЛ [17]. Поэтому целью данной работы является исследование влияния длительности разрядных импульсов на структуру и свойства аморфных покрытий, полученных электроискровой обработкой стали 35 в смеси железных гранул с многокомпонентным порошком.
2. МЕТОДИКА
Покрытия наносились на подложку из стали 35 в виде цилиндра диаметром 12 мм и высотой 10 мм. В качестве осаждаемого материала использовали порошковую смесь (табл. 1) и гранулы низколегированной стали Ст. 3.
Таблица 1.
Состав порошковой смеси
Порошок | ат. % | Элемент | ат. % |
---|---|---|---|
Si | 5.91 | Si | 15.27 |
C | 3.49 | C | 24.03 |
Mo | 20.02 | Mo | 10.00 |
Cr | 21.7 | Cr | 19.99 |
SiB4 | 7.66 | B | 20.60 |
WС | 41.23 | W | 10.09 |
Гранулы получали путем разрезания проволоки диаметром 4 ± 0.2 мм на цилиндры высотой 4 ± 0.2 мм. Исходные порошки имели чистоту не менее 99.5 мас. %. Порошковая смесь была приготовлена путем смешивания порошков в планетарной шаровой мельнице PM-400 в течение 90 мин в аргоне при скорости вращения 250 об./мин в течение 2 ч. По данным сорбтометра Sorbi-М, после смешивания порошок имел удельную поверхность 3.1 м2/г. К железным гранулам добавляли высушенный порошок в концентрации 9 об. %, и все это загружали в стальной контейнер. Схема установки для нанесения покрытий представлена на рис. 1а. Подложка размещалась в центре контейнера. Контейнер устанавливался под углом 45° и соединялся с приводом.
Рис. 1.
Схема ЭИЛ в гранулах с добавлением порошка (а) и прирост массы подложки в зависимости от длительности импульсов после 6 мин ЭИЛ (б).
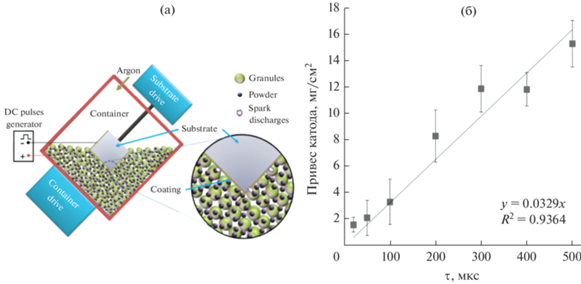
Скорость вращения контейнера составляла 60 об./мин. Подложка была закреплена на стальном стержне, подключенном к отрицательной клемме генератора импульсов, и соединена с приводом, вращающем ее в направлении, противоположном контейнеру, со скоростью 60 об./мин. Положительный вывод генератора был подключен к контейнеру через медные щетки. Генератор импульсов IMES-40 выдавал прямоугольные импульсы тока амплитудой 110 ± 10 А при напряжении 30 ± 5 В, длительностью (τ) в диапазоне 20‒500 мкс с частотой 1000 Гц (табл. 2). Аргон подавали в контейнер со скоростью 10 Л мин–1 для предотвращения процессов окисления на поверхности образцов. Время нанесения каждого покрытия составляло 360 с.
Таблица 2.
Электрические параметры ЭГД, обозначение покрытий и их толщина
Обозначение покрытий | Длительность импульса, мкс | Энергия, Дж | Толщина, мкм |
---|---|---|---|
C20 | 20 | 0.066 | 22 ± 9 |
C50 | 50 | 0.165 | 29 ± 5 |
C100 | 100 | 0.33 | 38 ± 9 |
C200 | 200 | 0.66 | 39 ± 7 |
C300 | 300 | 0.99 | 47 ± 17 |
C400 | 400 | 1.32 | 54 ± 9 |
C500 | 500 | 1.65 | 56 ± 17 |
Фазовый состав образцов исследовали на рентгеновском дифрактометре ДРОН-7 в CuKα-излучении. Состав покрытий исследовали с помощью растрового электронного микроскопа (СЭМ) Sigma 300 VP, оснащенного спектральным анализатором INCA Energy. Рамановскую микроспектрометрию проводили на приборе InVia Reflex (Renishow, Великобритания). Параметры зонда: лазер 532 нм, выходная мощность 5 мВт при 500 повторах. Электрохимические поляризационные испытания проводили в 3.5% растворе NaCl в стандартной трехэлектродной ячейке с использованием потенциостата P-2X. В качестве электрода сравнения использовался стандартный хлорсеребряный электрод. Контр-электродом служила платиновая фольга, а в качестве рабочего электрода использовались образцы с покрытием и сталь 35. Площадь контакта образцов с электролитом составляла 1 см2. Сканирование проводилось со скоростью 3 мВ/с в диапазоне –1.5‒0.5 В. Для обеспечения воспроизводимости результатов было выполнено 5 измерений для каждого образца. Испытания на стойкость к высокотемпературному окислению проводились в муфельной печи при температуре 700°C на воздухе. Общее время тестирования составило 100 ч. Твердость покрытий измеряли на микротвердомере ПМТ-3М при нагрузках 0.5 Н по методу Виккерса. Износостойкость покрытий исследовали согласно ASTM G99-17 при сухом трении скольжения со скоростью 0.47 м/с при нагрузках 10 и 25 Н с использованием диска из быстрорежущей стали М45 твердостью 60 HRC в качестве контртела. Изменение массы образцов контролировали с помощью весов с чувствительностью 0.1 мг.
3. РЕЗУЛЬТАТЫ И ИХ ОБСУЖДЕНИЕ
В процессе электроискрового осаждения покрытий в смеси стальных гранул и порошка CrMoWCBSi наблюдалось увеличение массы подложек в результате осаждения материала гранул и порошка на катод (рис. 1б). С увеличением длительности импульсов, посылаемых генератором, средний привес катода монотонно увеличивался почти в десять раз с 1.6 до 15.4 мг/см2 за 6 мин осаждения. Привес катода Δmc во время ЭИЛ в гранулах может быть выражен как сумма масс материала гранул Δma и порошка Δmp, перешедшего в микрованну расплава (MB) на поверхности катода, за вычетом эрозии катода εc:
Как известно, Δma увеличивается с увеличением энергии разряда при ЭИЛ [20]. В этом случае, повышение привеса катода происходит за счет увеличения эрозии анода Δma и фиксации порошка Δmp. Величина Δmp ‒ это масса порошка, закрепленная силами электростатического притяжения на поверхности электродов, равной площади MB.
СЭМ-изображения в режиме обратно отраженных электронов и распределение элементов в поперечном сечении покрытий показаны на рис. 2. Средняя толщина покрытий увеличивалась с 22 до 56 мкм при увеличении длительности разрядных импульсов (табл. 2). В микроструктуре покрытий наблюдалось небольшое количество пор и поперечных трещин. Возникновение поперечных трещин принято объяснять разницей коэффициентов теплового расширения покрытия и подложки [21, 22]. Светлые включения в покрытиях диаметром менее 15 мкм представляют собой карбид вольфрама и металлический молибден, которые не успевают раствориться в металлическом расплаве из-за высокой температуры плавления (рис. 3а, 3б). В слоях подложки, прилегающих к покрытию, видны световые пятна, являющиеся зоной термического воздействия. По данным СЭМ изображений толщина зоны термического влияния не превышала 30 мкм. Таким образом, можно сделать вывод о слабом тепловом воздействии ЭИЛ на подложку.
Рис. 2.
СЭМ-изображения (а, в, д) и результаты ЭДС сканирования (б, г, е) поперечного сечения покрытий С20 (а, б); C100 (в, г) и C500 (д, е). Пунктирная линия указывает область сканирования.
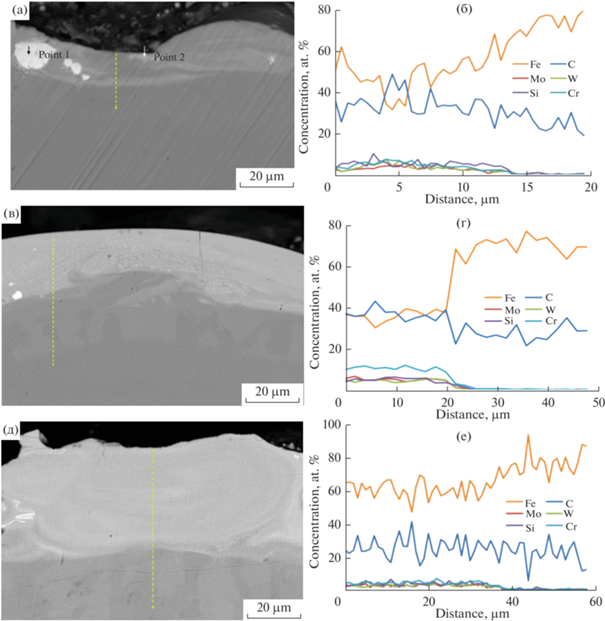
Рис. 3.
ЭДС спектры участков покрытия точка 1 (а) и точка 2 (б) на рис. 3а, а также концентрации металлов и кремния, согласно ЭДС-анализу поверхности покрытия в зависимости от τ (в).
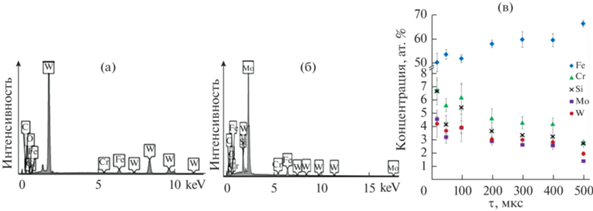
EDS-анализ покрытий показал равномерное распределение элементов в поперечном сечении покрытий (рис. 2б, 2г, 2е). По данным EDS-анализа поверхности покрытий, с увеличением τ в диапазоне от 20 до 500 мкс содержание железа в покрытиях увеличивалось с 50 до 67 ат. % на фоне снижения концентрации элементов CrMoWCBSi порошка (рис. 3в). Это объясняется увеличением времени разряда, в течение которого большее количество железа вовлекается в микрованну разряда из гранул и подложки. В момент прохождения разряда, порошок, закрепленный на поверхности электрода, равной МВ, плавился и смешался с электродным материалом, образуя покрытие. Таким образом, количество порошка, перенесенного в покрытие в результате одного разряда, зависит от диаметра MB. Зависимость диаметра МБ на катоде от τ в диапазоне от 20 до 500 мкс хорошо описывается логарифмической зависимостью: при малых τ от 20 до 100 мкс диаметр области плавления увеличивался сильно, а выше 100 мкс – незначительно [23]. Соответственно, при τ более 100 мкс количество порошка в МВ практически не увеличивалось. В то же время при увеличении τ от 100 до 500 мкс глубина проплавления подложки в зоне действия разряда увеличивалась и, соответственно, увеличивалась концентрация железа в МВ. Этим объясняется наблюдаемое снижение концентрация элементов порошка в покрытии при увеличении τ выше 100 мкс.
Результаты рентгенофазового анализа исходной порошковой смеси и покрытия С100 показаны на рис. 5. Рефлексы карбида вольфрама, молибдена, хрома, кремния и графита наблюдались в рентгеновском спектре CrMoWCBSi порошка (рис. 4а).
Рис. 4.
Рентгеновские дифрактограммы многокомпонентного порошка и покрытия С100 (а), а также фазовый состав нанесенных покрытий по данным РФА (б).

Рис. 5.
Поляризационные кривые стали 35 и аморфных покрытий в 3.5% растворе NaCl (а) и спектр комбинационного рассеяния поверхности образца С100 после испытаний (б).
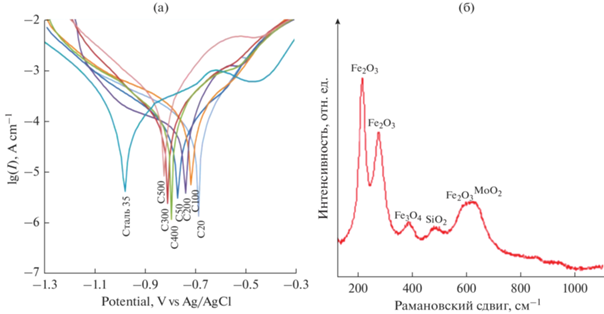
На дифрактограмме покрытия видно характерное гало в диапазоне углов 2θ = 35°–55°, что означает наличие аморфной фазы. Кроме того, в спектрах покрытий наблюдались узкие Брэгговские рефлексы, соответствующие αFe от подложки, а также карбиду вольфрама и молибдену. Наличие фаз WC и Mo в покрытиях согласуется с данными СЭМ и ЭДС-анализа (рис. 2а; 3а, 3б) и объясняется их высокими точками плавления. Доля аморфной фазы по данным рентгеноструктурного анализа обычно рассчитывается как отношение суммы площадей гало к сумме площадей гало и острых Брэгговских рефлексов [24, 25]:
Потенциодинамические поляризационные испытания проводились в 3.5% водном растворе NaCl для изучения коррозионной стойкости стали 35 с МС покрытиями (рис. 5а). Плотность тока коррозии (Icorr), потенциал коррозии (Ecorr) и сопротивление поляризации (Rp) были рассчитаны путем экстраполяции катодных и анодных наклонов Тафеля с использованием метода Штерна-Гири (табл. 3). Результаты испытания покрытий показали снижение потенциала коррозии на 19–43% и плотности тока до 2.17 раз и повышение сопротивления поляризации до 6.9 раз по сравнению со сталью 35. Это можно объяснить аморфной структурой покрытий [26, 27]. Кроме того, хром, кремний и вольфрам, входящие в состав аморфных покрытий, могут улучшить их коррозионные свойства в 3.5% растворе NaCl [28]. Это связано с барьерными свойствами оксидных пленок, образующихся на поверхности покрытия при взаимодействии с электролитом. При увеличении τ от 200 до 500 мкс Ecorr уменьшался, а Icorr увеличивался. Покрытие C500 показало самый высокий ток коррозии и самые низкие значения Ecorr и Rp. Это объясняется увеличением концентрации железа в покрытиях с увеличением τ, поскольку известно, что с уменьшением концентрации аморфной фазы коррозионная стойкость аморфно-нанокристаллических композитов ухудшается [29].
Таблица 3.
Коррозионные параметры образцов
Параметр | сталь 35 | С20 | С50 | С100 | С200 | С300 | С400 | С500 |
---|---|---|---|---|---|---|---|---|
Ecorr, V | –0.98 | –0.68 | –0.77 | –0.71 | –0.74 | –0.81 | –0.79 | –0.82 |
Icorr, µА cm–2 | 121.8 | 85.0 | 56.1 | 76.1 | 60.6 | 98.5 | 111.1 | 171.7 |
Rp, kOhm | 14.8 | 38.7 | 89.8 | 49.2 | 46.9 | 76.9 | 101.9 | 31.2 |
Рамановская спектроскопия поверхности покрытия C100 после поляризационного тестирования показала присутствие Fe2O3 (217, 279 и 597 см–1) вместе с небольшим количеством Fe3O4 (390 см–1), SiO2 (479 см–1) и MoO2 (660 см–1), которые являются нерастворимыми продуктами коррозии аморфной фазы во время испытаний в 3.5% растворе NaCl (рис. 5б).
На рис. 6а показана кинетика изменения массы образца С100 и стали 35 при температуре 700°С на воздухе. За 100 ч испытаний образец с покрытием подвергся окислению в 23 раза меньше, чем сталь 35, из-за ограничения контакта кислорода с подложкой. На рис. 6б показан участок рентгеновского спектра покрытия C100 после испытания на жаростойкость. В соответствии с ним, прирост образца обусловлен фиксацией кислорода на поверхности образца в виде оксида железа(III) в модификации гематита. Помимо гематита, на дифракционной картине наблюдались рефлексы αFe, что указывает на небольшую толщину оксидного слоя, через который проникает рентгеновское излучение. Рамановская спектроскопия оксидного слоя также показала присутствие Fe2O3 (216, 279 и 592 см–1) (рис. 6в). Кроме того, магнетит Fe3O4 (390 см–1) наблюдается вместе с небольшим количеством SiO2 (485 см–1). SiO2 указывает на коррозию аморфной фазы в процессе высокотемпературного окисления. Известно, что существенную роль в высокой жаростойкости МС покрытий играет кремний, оксид которого обладает высокими барьерными свойствами [30, 31].
Рис. 6.
Циклическая жаростойкость покрытия C100 по сравнению со сталью 35 при температуре 700°C (a), рентгеновская дифрактограмма (б) и спектры комбинационного рассеяния поверхности покрытия после испытания на жаростойкость (в).
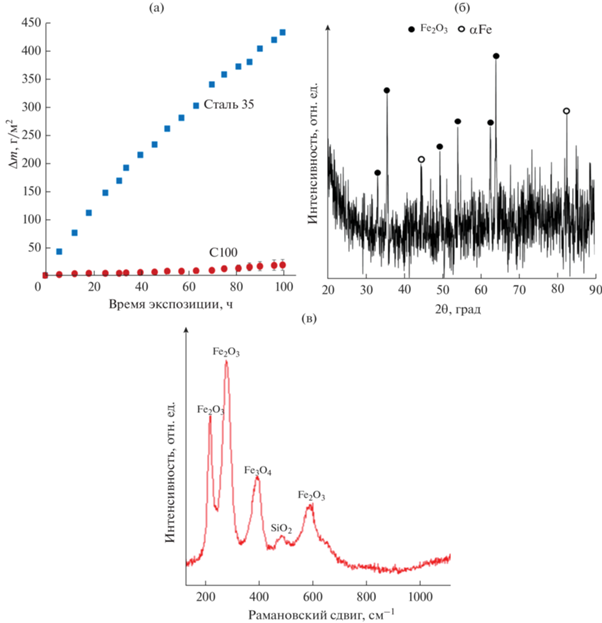
Изображение поперечного сечения покрытия С100 после испытания на жаростойкость показывает, что оксидный слой формируется на стальной подложке фрагментарно в самых тонких местах покрытия (рис. 7а). На микрофотографии фрагмента покрытия (рис. 7б) видно, что оксидный слой продолжает расти под покрытием и в наиболее богатых железом местах покрытия.
Рис. 7.
СЭМ-изображение поперечного сечения покрытия С100 после испытания на циклическое окисление при увеличении: 250× (а), 2500× (б); 1200× (г); и ЭДС спектр точки 3 (в).
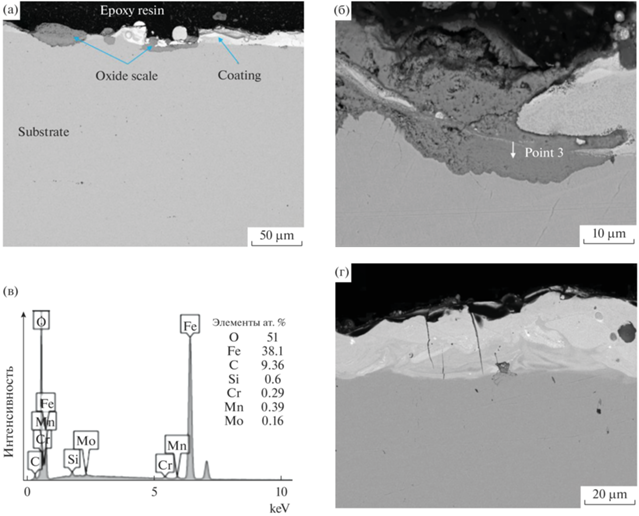
Примечательно, что оксидный слой практически не образуется поверх покрытия, что подтверждает высокую стойкость к окислению сформированного аморфного слоя. Данные ЭДС анализа показывают значительно более низкую концентрацию Cr, Mo и Si по сравнению с железом в оксидном слое (рис. 7г). Это означает слабое участие материала покрытия в образовании окалины. Важно отметить, что тонкие поперечные трещины в покрытии не вызывают очагов окисления, как показано на рис. 7в.
Испытания покрытий на микротвердость показали, что для большинства образцов средние значения твердости находились в диапазоне от 617 до 759 HV (рис. 8а). В целом наблюдалась тенденция к снижению твердости покрытия с увеличением τ. Так, средняя твердость покрытия C500 составила 399 HV. Согласно литературным данным, твердость большинства МС на основе Fe находится в диапазоне от 430 до 1200 HV [32–44]. Таким образом, твердость разработанных покрытий соответствует МС близкого состава.
Рис. 8.
Зависимость микротвердости покрытий от длительности импульса (а), коэффициент трения покрытий при нагрузках 25 (б) и 70 Н (в), износ покрытий по сравнению со сталью 35 (г).
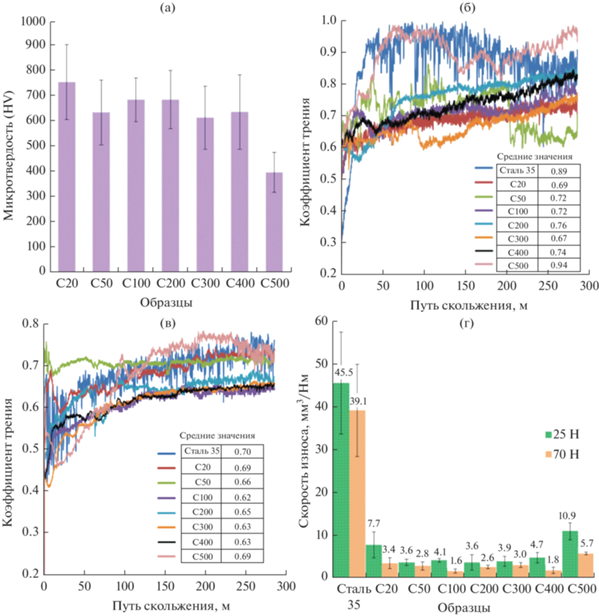
Средние значения коэффициента трения покрытий составляли от 0.67 до 0.94 при нагрузке 25 Н и от 0.62 до 0.69 при 70 Н (рис. 8б, 8в). Полученные значения укладываются в диапазон коэффициентов трения для большинства МС покрытий на стальной подложке. Для большинства покрытий коэффициент трения был на 15–25% ниже, чем для стали 35. При обеих нагрузках наибольший коэффициент трения наблюдался для покрытия С500 мкс. Это можно объяснить низкой твердостью данного покрытия из-за высокого содержания железа.
Результаты испытаний покрытий на износ при нагрузках 25 и 70 Н представлены на рис. 8г. Средние значения скорости износа покрытий находились в диапазоне от 1.6 × 10–6 до 10.9 × 10–6 мм3/Нм. Покрытие C20, нанесенное при самой низкой τ, показало относительно высокую скорость износа, что может быть объяснено его малой толщиной, вследствие чего оно быстро изнашивалось. Наибольшая скорость износа наблюдалась у покрытия C500 при обеих нагрузках. Это связано с высоким содержанием железа в его составе и низкой твердостью. Скорость износа покрытий С50–С400 имела близкие значения в диапазоне от 1.6 × 10–6 до 3 × 10–6 мм3/Нм при нагрузке 25 Н и от 3.6 × 10–6 до 4.7 × 10–6 мм3/Нм при 70 Н. Защитный эффект покрытий определяется как отношение скорости износа материала подложки к скорости износа покрытия. Как показано на рис. 8г, защитный эффект приготовленных ЭИЛ покрытий находился в диапазоне от 4 до 22. Исходя из данных за последние годы [32–44], скорость износа при сухом скольжении представленных МС покрытий находилась в широком диапазоне 2.7 × 10–6‒373 × 10–6 мм3/Нм, а защитный эффект от 0.54 до 6. Таким образом, данные по износостойкости полученных аморфных покрытий являются одними из лучших среди ранее опубликованных результатов.
ВЫВОДЫ
Приготовлено аморфное покрытие на стали 35 новым методом электроискрового осаждения в смеси железных гранул с порошком CBCrSiMoW. Установлено, что в структуре покрытия преобладает аморфная фаза. При увеличении длительности импульса разряда доля аморфной фазы в составе покрытий уменьшалась с 67 до 50 об. %. Это связано как с ухудшением стеклообразующей способности материала покрытия из-за обогащения железом, так и с уменьшением скорости охлаждения материала из-за объемного нагрева подложки. Осажденное покрытие характеризуется высокой стойкостью к окислению при температуре 700°С. Оксидная окалина образовывалась фрагментарно на стальной подложке в наиболее богатых железом местах покрытия и не обнаруживалась на поверхности покрытия. Микротвердость покрытий находилась в диапазоне от 399 до 759 HV. Средние значения коэффициента трения покрытий находились в диапазоне от 0.62 до 0.94. Средние значения скорости изнашивания покрытий находились в диапазоне от 1.6 × 10–6 до 10.9 × 10–6 мм3/Нм, что в 4‒22 раза ниже, чем у стали 35. Покрытие, полученное при наиболее длинных импульсах, имело наименьшую твердость и износостойкость, а также самый высокий коэффициент трения за счет малой концентрации аморфной фазы.
Список литературы
Masood A., Belova L., Ström V. // J. Magnetism and Magnetic Materials. 2020. V. 504. P. 166667.
Cherkezova-Zheleva Z. et al. // Hyperfine Interactions. 2020. V. 241. № 1. P. 1–12.
Ji L. et al. // J. Physics and Chemistry of Solids. 2020. V. 145. P. 109546.
Zhang Q. et al. // J. Materials Science & Technology. 2021. V. 61. P. 159–168.
Suo Y. et al. // Fusion Engineering and Design. 2020. V. 157. P. 111635.
Schroers J. et al. // Jom. 2009. V. 61. № 9. P. 21–29.
Wang Y.B. et al. // Materials Science and Engineering: C. 2012. V. 32. № 3. P. 599–606.
Ibrahim M.Z. et al. // Surface and Coatings Technology. 2020. V. 392. P. 125755.
Wang H. et al. // Materials Chemistry and Physics. 2020. V. 250. P. 123091.
Lee J., Liou M. L., Duh J. G. // Surface and Coatings Technology. 2017. V. 310. P. 214–222.
Koga Y. et al. // Materials Transactions. 2017. V. 58. № 10. P. 1444–1450.
Chen W. Y. et al. // Surface and Coatings Technology. 2020. V. 389. P. 125636.
Бурков А.А., Зайцев А.В., Сюй А.В., Зайкова Е.Р., Каминский О.И. // Физикохимия поверхности и защита материалов. 2019. Т. 55. № 1. С. 72–78.
Бурков А.А., Кулик М.А. // Физикохимия поверхности и защита материалов. 2020. Т. 56. № 6. С. 667–672.
Cadney S., Brochu M. // Intermetallics. 2008. V. 16. № 4. P. 518–523.
Николенко С.В., Сюй Н.А. // Физикохимия поверхности и защита материалов. 2017. Т. 53. № 5. С. 543–549.
Felix L.M., Kwan C.C.F., Zhou N.Y. // Metallurgical and Materials Transactions A. 2019. V. 50. № 9. P. 4223–4231.
Kayali Y., Talas S. // Protection of Metals and Physical Chemistry of Surfaces. 2021. V. 57. P. 106–112.
Бурков А.А. // Обработка металлов: технология, оборудование, инструменты. 2019. V. 21. № 4. P. 19–30.
Ribalko A.V., Sahin O. // Surface and coatings technology. 2006. V. 201. № 3–4. P. 1724–1730.
Zhang J. et al. // Transactions of the China Welding Institution. 2009. V. 30. № 12. P. 17–20.
Salmaliyan M., Ghaeni F.M. // Surface and Coatings Technology. 2017. V. 321. P. 81–89.
Pyachin S.A. et al. // Russian Physics Journal. 2019. V. 61. № 12. P. 2236–2243.
Shkodich N.F. et al. // J. Alloys and Compounds. 2018. V. 741. P. 575–579.
Cheng J. et al. // J. Alloys and Compounds. 2017. V. 716. P. 88–95.
Guo R. Q. et al. // Corrosion Science. 2011. V. 53. № 7. P. 2351–2356.
Li S. et al. // Materials Science and Engineering: C. 2015. V. 52. P. 235–241.
Sagasti A., Lopes A.C., Lasheras A. et al. // AIP Advances. 2018. V. 8. P. 047702.
Coimbrão D.D., Zepon G., Koga G.Y. et al. // Alloys Compd. 2020. V. 826. P. 154123.
Garip Y., Ozdemir O. // Alloys Compd. 2019. V. 780. P. 364–377.
Matsushita J.-I., Satsukawa T., Iwamoto N., Wang X., J. et al. // Mater. Sci. Forum 2016. V. 868. P. 38–42.
Wang G. et al. // J. Iron and Steel Research International. 2016. V. 23. № 7. P. 699–704.
Hong W. U. et al. // Transactions of Nonferrous Metals Society of China. 2016. V. 26. № 6. P. 1629–1637.
Paul T. et al. // Lasers in Manufacturing and Materials Processing. 2015. V. 2. № 4. P. 231–241.
Zhang H. et al. // J. non-crystalline solids. 2014. V. 406. P. 37–44.
Liu L., Zhang C. // Thin Solid Films. 2014. V. 561. P. 70–86.
An Y. et al. // Vacuum. 2014. V. 107. P. 132–140.
Yugeswaran S. et al. // J. alloys and compounds. 2013. V. 551. P. 168–175.
Zhang C. et al. // Intermetallics. 2012. V. 29. P. 80–85.
Guo R. Q. et al. // Intermetallics. 2012. V. 30. P. 94–99.
Li X. et al. // J. Non-Crystalline Solids. 2020. V. 537. P. 120018.
Nayak S. K. et al. // J. Alloys and Compounds. 2020. V. 825. P. 154120.
Liang D. et al. // Surface and Coatings Technology. 2020. V. 387. P. 125535.
Ji X. et al. // Wear. 2019. V. 438. P. 203113.
Дополнительные материалы отсутствуют.
Инструменты
Физикохимия поверхности и защита материалов