Нефтехимия, 2020, T. 60, № 6, стр. 810-826
Дегидрирование кумола в α-метилстирол на пористых керамических каталитических конвертерах состава [Re,W]/γ-Al2O3(K,Ce)/α-Al2O3 и [Fe,Cr]/γ-Al2O3(K,Ce)/α-Al2O3
А. С. Федотов 1, *, В. И. Уваров 2, М. В. Цодиков 1, S. Paul 3, P. Simon 3, M. Marinova 4, F. Dumeignil 3
1 Институт нефтехимического синтеза им. А. В. Топчиева РАН
119991 Москва, Россия
2 Институт структурной макрокинетики и проблем материаловедения РАН
142432 Черноголовка, Россия
3 Univ. Lille, CNRS, Centrale Lille, ENSCL, Univ. Artois, UMR 8181
F-59000 Lille, France
4 Institut Chevreul, Université Lille
F-59655 Lille, France
* E-mail: alexey.fedotov@ips.ac.ru
Поступила в редакцию 30.06.2020
После доработки 09.07.2020
Принята к публикации 10.07.2020
Аннотация
Изучены особенности протекания процесса дегидрирования кумола в α-метилстирол на оригинальных пористых керамических каталитических конвертерах состава [Re,W]/γ-Al2O3(K,Ce)/α-Al2O3 и [Fe,Cr]/γ-Al2O3(K,Ce)/α-Al2O3, полученных с применением самораспространяющегося высокотемпературного синтеза и золь−гель метода. Установлено, что при оптимальной температуре 625°С рений–вольфрам-содержащая система обладает, в ~ 1.5 раза большей каталитической активностью, чем железохромовая. На Re–W-содержащем каталитическом конвертере при оптимальной температуре конверсия кумола составляет ~71 мол. %, выход α-метилстирола от теоретически возможного ~77 мол. %, содержание α-метилстирола в продуктах реакции ~35 мол. %, при производительности по целевому продукту ~7.4 г/(ч гакт.комп). Степень зауглероженности катализатора за 6 ч эксперимента не превышала 5 мас. %.
Альфа-метилстирол (далее α-метилстирол) является незаменимым мономером при получении бутадиен-стирольных каучуков и акрилонитрил-бутадиен-стирольных (АБС) пластиков, обладающих повышенной термостойкостью и механической прочностью [1, 2]. Кроме того, α-метилстирол широко используется при изготовлении клеев, смазочных масел, парфюмерии и другой многотоннажной продукции органического синтеза. В настоящее время, объемы годового производства α-метилстирола превышают 220 тыс. т/г [3]. Согласно маркетинговым исследованиям, в период с 2017 по 2024 гг. среднегодовой темп наращивания отраслевых мощностей по выпуску α-метилстирола глобально составит 4.5–6%, главным образом, благодаря росту резиновой промышленности, стимулируемой спросом на автомобили, потребляющей до одной трети получаемого α-метилстирола [1]. Ведущими мировыми производителями α-метилстирола являются такие крупные компании как Solvay S.A. (Бельгия), INEOS (Великобритания), United Petrochemical Company (Россия), Honeywell International Inc. (США), SI Group (США) и Mitsui Chemicals (Япония) [4, 5].
На сегодняшний день основные промышленные способы производства α-метилстирола – окислительный “кумольный” метод и каталитическое дегидрирование кумола в адиабатических контактных реакторах [4]. При этом главные проблемы перечисленных решений заключаются, во-первых, в недостаточной чистоте получаемого α-метилстирола в виду повышенного содержания побочных продуктов автоокисления и сополимеризации с другими компонентами дегидрогенизата, что требует применения дополнительных стадий очистки и многокомпонентных ингибиторов, а, во-вторых, – в необходимости частой регенерации используемого железо–хром-содержащего катализатора [6].
Перспективным способом повышения эффективности существующих процессов дегидрирования является разработка малогабаритных реакторов кассетного типа на основе пористых керамических каталитических конвертеров [7]. Этот подход может позволить интенсифицировать протекание реакции дегидрирования и повысить селективность процесса по целевому продукту, главным образом, путем уменьшения общей энергетики химического превращения (по сравнению с традиционными реакторами со стационарным слоем гранулированного катализатора) за счет улучшенного тепломассопереноса в высокопористой среде каталитического конвертера, в которой благодаря принудительной диффузии молекул субстрата в пространственно-ограниченном объеме пор и высокому соотношению площади каталитической поверхности к объему внутренних пор, увеличивается такой важный в катализе фактор, как частота стохастических соударений молекул субстрата со стенками пор, модифицированных каталитически активными компонентами [7, 8].
Эффективность заявленного метода подтверждена ранее проведенными исследованиями по высокоскоростному получению водородсодержащего газа в процессах углекислотного, парового и смешанного риформинга сырья ископаемого, синтетического и биологического происхождения, такого как метан, диметиловый эфир и продукты ферментации [9, 10], а также по получению пропилена дегидрированием пропана, 1,3-бутадиена и изопрена из 1-бутанола и изоамилового спирта, соответственно, в совмещенных процессах дегидратации–дегидрирования [11].
Другим важным фактором, позволяющим усовершенствовать промышленные технологии основного органического синтеза, является перспектива использования каталитического конвертера в качестве тиражируемого элемента кассетных реакторов нового типа, что существенным образом упрощает стадии загрузки и выгрузки больших объемов катализаторов, а увеличивает безопасность работы.
ЭКСПЕРИМЕНТАЛЬНАЯ ЧАСТЬ
Синтез пористого каталитического конвертера для процесса дегидрирования кумола в α-метилстирол
Получение трубчатой пористой керамической подложки на основе α-Al2O3. На первой стадии приготовления каталитического конвертера с применением самораспространяющегося высокотемпературного синтеза получали трубчатую пористую керамическую подложку на основе α-Al2O3, у которой один конец заглушен для обеспечения “принудительной” диффузии газов через рабочую поверхность цилиндра от наружной стенки к внутренней, а на другом находится прижимная гайка для герметичной стыковки подложки с реактором через графитовую прокладку (рис. 1).
Геометрические размеры трубчатой подложки: общая длина – 137 мм; длина рабочей зоны – 120 мм; внешний диаметр трубки – 25 мм; толщина стенки – 7 мм.
Размер открытых пор трубчатой пористой керамической подложки оценивали по модели капиллярного вытеснения на основе формулы Лапласа для “модели цилиндрических пор” с использованием ртутного порометра и методом “пузырька” [12]. Диаметр открытых пор подложки 1–3 мкм. Пористость, измеренная методом гидростатического взвешивания, составила более 50%.
В качестве сырья для синтеза подложки использовали порошок α-Al2O3 крупной фракции “Электрокорунд белый” с размером частиц 100 мкм (ООО “Литпром”).
С целью повышения механической прочности подложки и ее устойчивости к высокой температуре, в исходный порошок α-Al2O3 вводили порошкообразные добавки эвтектического состава, а именно: оксид магния (ГОСТ 4526-75) производства завода “Красный химик” и карбид кремния в соотношении (мас. %): α-Al2O3 – 90; MgO – 3; SiС – 7. Данные соединения в ходе СВС-синтеза образуют активный SiO2, который связывает между собой частицы α-Al2O3 за счет их превращения в муллиты, индиалит (Mg2Al4Si5O18) и шпинель (MgAl2O4) [13].
Указанные порошки смешивали в шаровой мельнице в течение 1 ч, после чего проводили одностороннее прессование готовой смеси под давлением 30–90 МПа и ее спекание при температуре 1300–1450°C в атмосфере воздуха в течение 1 ч, а затем охлаждали до комнатной температуры в течение 2 ч.
При температурах спекания порошков в области 1300–1450°C образуется жидкая фаза эвтектического состава, содержащая оксид магния и карбид кремния в виде клиноэнстатита, которая смачивает частицы Al2O3, образуя прочный пористый каркас подложки. Далее по тексту для простоты написания состава катализаторов обозначение трубчатой керамической подложки будет “α-Al2O3” (или же просто “подложка”), без упоминания добавок.
Модификация синтезированных подложек Re–W- и Fe–Cr-содержащими каталитическими системами
На основании литературных данных, в качестве объектов исследования процесса дегидрирования кумола в α-метилстирол, для сравнения основных показателей каталитической активности, были выбраны две полиметаллические системы, содержащие как оригинальные рений-вольфрамовые активные компоненты (первая) [14], так и железо-хромовые аналоги традиционных промышленных катализаторов (вторая) [15–19]. В настоящей работе, в каждом случае их наносили на внутреннюю поверхность каналов конвертера. Каталитические системы формировали на внутренней поверхности стенок пор методом молекулярного наслаивания коллоидного раствора предшественников. Предварительно, с целью увеличения внутренней поверхности пор, формировали промежуточный слой γ-Al2O3. Для этого на первой стадии путем прокачки через поры подложки наносили коллоидный раствор золя, состоящего из 0.03 мол. % H2O, 1.5 моль/л Al(OPri)3 (98%, “Acros Organics”), 1.5 моль ацетилацетона (98%, “Fluka”) в толуоле (“Экос-1”, ГОСТ 5789-78). После нанесения золя модифицированную пористую керамическую подложку сушили в токе воздуха в сушильном шкафу при 120°С в течение 1 ч, а затем проводили термообработку в режиме теплового удара при 500°С в течение 30 мин. Количество осажденного γ-Al2O3 оценивали по увеличению веса образца. Стадию пропитки повторяли 4 раза, пока прирост веса не достигал 4–5 мас. %. Затем, с целью подавления побочных реакций полимеризации α-метилстирола, наносили K2O и CeO2 раздельной пропиткой конвертера водным раствором K2CO3 и нитрата церия.
Далее на первой подложке проводили раздельное нанесение активных рений–вольфрам-содержащих компонентов из водно-спиртовых растворов соответствующих комплексов NBu4ReO4 и (NH4)6W12O39 · H2O. Формирование оксидов Re(7+) и W(6+) осуществляли путем прокаливания пропитанного образца в муфельной печи в токе воздуха при различных температурах: 500°C – 2 ч, 600°C – 2 ч, 800°C – 1 ч. Количество нанесенных компонентов определяли по привесу образца п-осле стадий термической обработки (мас. %):
Раздельное нанесение активных железо–хромсодержащих компонентов на вторую подготовленную подложку осуществляли из толуольных растворов, соответствующих ацетилацетонатных комплексов, содержащих 7.2 мас. % Fe(acac)3 и 7.4 мас. % Cr(acac)3. Для формирования оксидов Fe(3+) и Cr(3+) пропитанный образец прокаливали в муфельной печи в токе воздуха при различных температурах: 500°C – 2 ч, 600°C – 2 ч, 800°C – 1 ч. Количество нанесенных компонентов определяли по привесу образца после стадий термической обработки (мас. %):
Далее по тексту, для простоты написания, модифицированная каталитическими покрытиями подложка состава будет обозначаться словом “конвертер”.
Схема лабораторной установки и проточного каталитического реактора
Дегидрирование кумола в α-метилстирол на разработанных каталитических конвертерах изучали с использованием оригинальной лабораторной установки и проточного реактора, устройства которых представлены на рис. 2 и 3.
Рис. 2.
Схема лабораторной установки дегидрирования кумола в α-метилстирол: 1 – газовый баллон с аргоном; 2 – емкость с кумолом; 3 – eмкость с дистиллированной водой; 4 – газовый редуктор; 5 – регулятор расхода газа; 6 –задающее устройство регулятора расхода газа; 7 – жидкостной насос; 8 – задающее устройство жидкостного насоса; 9 – фитинг смешения газо-жидкостных потоков; 10 – испаритель; 11 – температурный процессор; 12 – датчик давления; 13 – обогреваемый проточный каталитический реактор; 14 – жидкостной сепаратор; 15 – запорный вентиль; 16 – жидкостной приемник; 17 – индикатор расхода газа; 18 – газовый хроматограф; 19 – хромато-масс-спектрометр; 20 – газо-жидкостной хроматограф; 21 – вычислительная рабочая станция для обработки полученных данных.
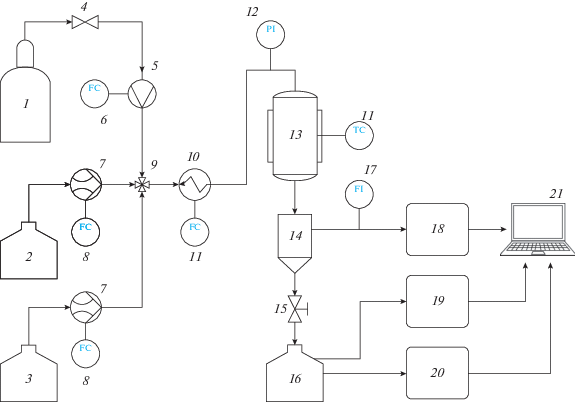
Методика проведения эксперимента
Перед началом эксперимента по дегидрированию кумола в α-метилстирол, на описанном выше лабораторном стенде проводили подготовительные работы по установке каталитического конвертера в проточный реактор (позиция 13 на рис. 2), сборке и уплотнению самого реактора, его монтированию на установку в регламентированное схемой место и опрессовке всей системы аргоном в течение 15 мин. С целью предотвращения нежелательного окисления нанесенных каталитически активных компонентов конвертера кислородом воздуха, нагрев реактора с установленным образцом до температуры начала процесса (и далее до каждой контрольной точки в диапазоне 500–650°С с шагом 25°С) осуществляли в токе аргона (99.998% ГОСТ 10157-79), подаваемом из газового баллона (1) через редуктор (4). Скорость потока аргона задавали равной 2.5 л/ч и контролировали при помощи электронного регулятора РРГ “Элточприбор БУИП-1” (5). По достижении требуемой температуры подачу аргона прекращали и начинали раздельную подачу сырья (кумол, 98%, “Sigma-Aldrich”) и разбавителя (дистиллированной воды) из встроенных емкостей (2) и (3) жидкостных дозаторов “High Pressure Pump 5001” (7). Объемные скорости подачи субстратов задавали равными 0.1 и 0.2 мл/мин, соответственно, для обеспечения мольного соотношения H2O : кумол = 14 и парциального давления кумола ~0.01 МПа. Смешение потоков жидкостей происходило в фитинге (9). С целью гомогенизации общего жидкостного потока, направляемого в реактор, его предварительно испаряли в змеевиковом испарителе (10) при температуре 200°С. Нагревом испарителя управляли при помощи температурного измерителя-регулятора “ОВЕН ТРМ-210” (11). Далее, поток парогазовой водно-органической смеси поступал в каталитический мембранный реактор (13). Нагрев и поддержание температуры реакторной печи задавали при помощи температурного процессора “ОВЕН ТРМ251” (Термопара ТП-0198, Хромель-алюмель (К)) (11). Давление в реакторе контролировали при помощи измерителя давления “ОВЕН IP65” и индикатора давления “ОВЕН 2ТРМ0” (12). Подачу сырья в реактор на каждой температурной точке осуществляли в течение 1 ч для установления стационарного режима процесса дегидрирования и обеспечения накопления в газовых и жидкостных приемниках установки продуктов реакции в количествах, необходимых для проведения ГХ-, ГЖХ- и ГХ-МС-анализов. Перед отбором газовой пробы выходные трубопроводы, присоединенные к приемнику, продували продуктовым газом в течение 15 мин. Скорость отбираемого в приемник продуктового газового потока измеряли при помощи газовых часов “Sinagawa DC2CM” (17). Отобранную газовую пробу анализировали методом газовой хроматографии для определения содержания неорганических (Н2, СО, СО2) и углеводородных (С1–С5) газов на хроматографах “Кристаллюкс-4000М” (18), снабженных детекторами ПИД и ДТП. Жидкую пробу концентрировали в охлаждаемом водопроводной водой жидкостном сепараторе (14) на протяжении всего времени каждой температурной точки, а затем, по средствам открытия запорного вентиля (15) сливали в пробоотборник (16). Далее измеряли объем отобранной пробы, отделяли водный слой от органического, а затем анализировали органическую фазу методом хромато-масс-спектрометрии (качественно) (19) и ГЖХ (количественно) (20). Полученные данные обрабатывали при помощи специализированного программного обеспечения NetChrom v2.1 на вычислительной рабочей станции (21). По завершении опыта, каталитический реактор охлаждали до комнатной температуры в атмосфере аргона аналогично с целью предотвращения нежелательного окисления катализатора.
Методика анализа продуктов реакции
Содержание водорода, оксидов углерода и метана в продуктах реакции определяли методом ГХ на хроматографе “КристалЛюкс-4000М” (“Мета-хром”, Россия), детектор – катарометр, газ-носитель – аргон высокой чистоты (99.998% ГОСТ 10157-79) с расходом 10 мл/мин, адсорбционная насадочная колонка 1 м × 3 мм. Наполнитель колонки – активированный уголь марки СКТ, размер частиц – 0.2–0.3 мм. Температура колонки, детектора и испарителя – 120°С. Концентрации газов находили по калибровочным кривым с использованием специализированного программного обеспечения NetChrom v2.1.
Углеводородные газы С1–С5 идентифицировали на хроматографе “КристалЛюкс 4000М” (“Мета-хром”, Россия) с применением пламенно-ионизационного детектора (ПИД), газ-носитель – гелий (ТУ 0271-001-45905715-02). Были установлены следующие расходы газов: гелий – 30 мл/мин; водород – 35 мл/мин; воздух – 300 мл/мин. Для анализа использовали хроматографическую колонку “HP-PLOT/Al2O3” (“Agilent Technologies”, США), 50 м × 0.32 мм, толщина пленки 8.0 мкм. Температура колонки составляла 120, детектора – 230, испарителя – 250°C. Концентрации продуктов определяли по калибровочным кривым с помощью специализированного программного обеспечения NetChrom v2.1.
Жидкие органические продукты реакции идентифицировали методами ГХ-МС и ГЖХ. Анализ ГХ-МС проводили с использованием хромато-масс-спектрометра “Thermo Focus DSQ II” с квадрупольным масс-анализатором, энергия электронов 70 эВ. Напряжение на электронном умножителе составляло 1244 В. Температура источников ионов 280°С. Температура интерфейса – 280°С. Детектирование проводилось в режиме регистрации полного ионного тока SIM (Selected Ion Monitoring).
Анализ ГЖХ осуществляли на хроматографе “Varian 3600” (“Varian Chromatography System”, США), ПИД, капиллярная колонка “Хромтэк SE-30”, 25 м × 0.25 мм, Df = 0.33 мкм. Температурный режим: 50°С (5 мин), 10°C/мин, 280°С, Тинж = = 250°С, Ринж = 1 бар, деление потока 1/200, газ-носитель – гелий (ТУ 0271-001-45905715–02).
Методика структурного анализа
Структура материала каталитических конвертеров и распределение элементов на их поверхности были изучены с использованием просвечивающей электронной микроскопии на приборе “TEM TITAN Themis 300” (“FEI”, США).
Анализ поверхности при помощи рентгеновской фотоэлектронной спектроскопии осуществляли на приборе “Axis Ultra DLD” (“Kratos Analytical Ltd.”, Великобритания) с монохроматическим рентгеновским излучением AlKα (15 кВ, 15 мА, 1486.6 эВ). Все спектры были откалиброваны по энергии с использованием положения пика C1s, соответствующего связям C–C, C–H при 284.8 эВ.
Методика расчетов
Расчет константы химического равновесия. Для реакции, записанной в общем виде, как:
(1)
${{\nu }_{1}}{{B}_{1}} + {{\nu }_{2}}{{B}_{2}} + ... = \nu _{1}^{'}B_{1}^{'} + \nu _{2}^{'}B_{2}^{'} + ...$Справочные данные для расчета энергии Гиббса брали из [19].
Расчет равновесных параметров реакции
Кумол | + | водяной пар (инерт) | = | α-метилстирол | + | водород | |
Стехиометрические коэффициенты химического уравнения (νi) | |||||||
1 | 0 | 1 | 1 | ||||
Мольные доли компонентов реакционной системы в начальный момент времени (xi) | |||||||
1 – z | z | 0 | 0 | $\sum {{{x}_{i}}} = 1$ | |||
Равновесная степень превращения компонентов реакционной системы (${{\bar {n}}_{i}}$) | |||||||
(1 – z)(1 –$\bar {y}$) | z | (1 – z)$\bar {y}$ | (1 – z)$\bar {y}$ | $\sum {{{{\bar {n}}}_{i}} = 1 + \bar {y}\left( {1 - z} \right)} $ | |||
Равновесные мольные доли компонентов реакционной системы (${{\bar {x}}_{i}}$) | |||||||
$\frac{{\left( {1 - z} \right)\left( {1 - \bar {y}} \right)}}{{1 + \bar {y}\left( {1 - z} \right)}}$ | $\frac{z}{{1 + \bar {y}\left( {1 - z} \right)}}$ | $\frac{{\left( {1 - z} \right)\bar {y}}}{{1 + \bar {y}\left( {1 - z} \right)}}$ | $\frac{{\left( {1 - z} \right)\bar {y}}}{{1 + \bar {y}\left( {1 - z} \right)}}$ | $\sum {{{{\bar {x}}}_{i}}} = 1$ |
Константа равновесия равна:
(4)
$\begin{gathered} {{K}_{x}} = \frac{{\bar {x}_{{B_{1}^{'}}}^{{\nu _{1}^{'}}}\bar {x}_{{B_{2}^{'}}}^{{\nu _{2}^{'}}} \times ...}}{{\bar {x}_{{{{B}_{1}}}}^{{{{\nu }_{1}}}}\bar {x}_{{{{B}_{2}}}}^{{{{\nu }_{2}}}} \times ...}} = \prod {\bar {x}_{{{{A}_{i}}}}^{{{{\nu }_{i}}}}} = \\ = \frac{{{{{\left[ {\alpha {\text{ - метилстирол}}} \right]}}^{1}}{{{\left[ {{\text{водород}}} \right]}}^{1}}}}{{{{{\left[ {{\text{кумол}}} \right]}}^{1}}}} = \\ = \frac{{\left( {1 - z} \right){{{\bar {y}}}^{2}}}}{{\left( {1 + \bar {y}} \right)\left[ {1 + \left( {1 - z} \right)\bar {y}} \right]}}; \\ \end{gathered} $(5)
$\bar {y} = \frac{{ - \left( {{{K}_{x}} - \frac{{{{K}_{x}}}}{{1 - z}}} \right) - \sqrt {{{{\left( {{{K}_{x}} - \frac{{{{K}_{x}}}}{{1 - z}}} \right)}}^{2}} = - 4\left( { - {{K}_{x}} - 1} \right)\frac{{{{K}_{x}}}}{{1 - z}}} }}{{2\left( { - {{K}_{x}} - 1} \right)}},$(6)
${{\bar {x}}_{{\alpha {\text{ - }}{{{\text{метилстирол}}} \mathord{\left/ {\vphantom {{{\text{метилстирол}}} {{\text{водород}}}}} \right. \kern-0em} {{\text{водород}}}}}}} = \frac{{\left( {1 - z} \right)\frac{{ - \left( {{{K}_{x}} - \frac{{{{K}_{x}}}}{{1 - z}}} \right) - \sqrt {{{{\left( {{{K}_{x}} - \frac{{{{K}_{x}}}}{{1 - z}}} \right)}}^{2}} - 4\left( { - {{K}_{x}} - 1} \right)\frac{{{{K}_{x}}}}{{1 - z}}} }}{{2\left( { - {{K}_{x}} - 1} \right)}}}}{{1 + \left( {1 - z} \right)\frac{{ - \left( {{{K}_{x}} - \frac{{{{K}_{x}}}}{{1 - z}}} \right) - \sqrt {{{{\left( {{{K}_{x}} - \frac{{{{K}_{x}}}}{{1 - z}}} \right)}}^{2}} - 4\left( { - {{K}_{x}} - 1} \right)\frac{{{{K}_{x}}}}{{1 - z}}} }}{{2\left( { - {{K}_{x}} - 1} \right)}}}}.$Содержание водяного пара по отношению к кумолу, мол. доля:
(7)
$z = \frac{{{{n}_{{{{{\text{H}}}_{{\text{2}}}}{\text{O}}}}}}}{{1 + {{n}_{{{{{\text{H}}}_{{\text{2}}}}{\text{O}}}}}}}.$Мольные содержания компонентов равновесной реакционной смеси пропорциональны их мольным долям, поэтому за вычетом инерта их сумма равна, моль:
(8)
$\sum {\bar {x}} = {{\bar {x}}_{{\alpha {\text{ - метилстирол}}}}} + {{\bar {x}}_{{{\text{водород}}}}} + {{\bar {x}}_{{{\text{кумол}}}}}.$Тогда равновесный выход α-метилстирола (для упрощения восприятия данных, на рис. 4 обозначен, как “равновесное расчетное содержание α-метилстирола в продуктах реакции”) за вычетом инерта равен, мол. %:
(9)
${{\bar {\eta }}_{{\alpha {\text{ - метилстирол}}}}} = \frac{{{{{\bar {x}}}_{{\alpha {\text{ - метилстирол}}}}}}}{{\sum {\bar {x}} }} \times 100\% .$Рис. 4.
Сравнение расчетных равновесных и опытных температурных зависимостей основных параметров процесса дегидрирования кумола в α-метилстирол на каталитическом конвертере состава [Re,W]/γ-Al2O3(K,Ce)/α-Al2O3.
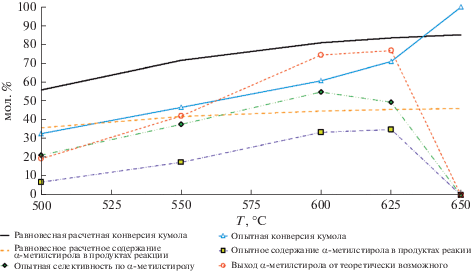
Расчет выходных параметров эксперимента. Конверсия кумола, мол. %:
(10)
${{y}_{{{\text{кумол}}}}} = \frac{{{{n}_{{\alpha {\text{ - метилстирол}}}}}}}{{{{n}_{{{\text{кумол\;}}}}}}} \times 100{\text{\% }},$Выход α-метилстирола от теоретически возможного, мол. %:
(11)
${{\chi }_{{\alpha {\text{ - метилстирол}}}}} = \frac{{{{n}_{{\alpha {\text{ - метилстирол}}}}}}}{{{{{\bar {n}}}_{{\alpha {\text{ - метилстирол}}}}}}} \times 100{\text{\% }},$Выход α-метилстирола на пропущенный кумол (на рис. 4 обозначен, как “опытное содержание α-метилстирола в продуктах реакции”), мол. %:
(12)
${{\eta }_{{\alpha {\text{ - метилстирол}}}}} = \frac{{{{n}_{{\alpha {\text{ - метилстирол}}}}}}}{{{{n}_{{{\text{кумол}}}}}}} \times 100{\text{\% }}.$Выход α-метилстирола на превращенный кумол (селективность процесса по α-метилстиролу), мол. %:
(13)
${{S}_{{\alpha {\text{ - метилстирол}}}}} = \frac{{{{n}_{{{\text{кумол}}}}}}}{{{{n}_{{\alpha {\text{ - метилстирол}}}}}}} \times 100{\text{\% }},$Производительность по α-метилстиролу на грамм активного компонента, л/(ч гакт.комп):
где Vα-метилстирол – объемный поток образующегося α-метилстирола, л/ч, а mакт.комп – общая масса нанесенных активных компонентов (активными компонентами считали Re2О7, WO3 и Fe2O3, Cr2O3), г.РЕЗУЛЬТАТЫ И ИХ ОБСУЖДЕНИЕ
Дегидрирование кумола в α-метилстирол на разработанных каталитических Re–W- и Fe–Cr-содержащих конвертерах
На основании результатов по исследованию влияния температуры на дегидрирование кумола на каталитических конвертерах состава [Re,W]/γ-Al2O3(K,Ce)/α-Al2O3 и [Fe,Cr]/γ-Al2O3(K,Ce)/α-Al2O3 в присутствии паров воды, взятых в мольном соотношении H2O : кумол = 14, и объемной скорости подачи сырья ~1.4 ч–1, установлено, что оптимальной температурой получения α-метилстирола является 625°С (рис. 4, 5). При оптимальной температуре рений−вольфрам-содержащая система обладает примерно в 1.5 раза большей каталитической активностью, чем железо-хромовая, что, очевидно, связано с фундаментальными различиями в природе этих металлов. Как видно на рис. 4 при этой температуре на Re–W-содержащем каталитическом конвертере конверсия кумола составляет ~71 мол. %, выход α-метилстирола от теоретически возможного ~77 мол. %, содержание α-метилстирола в продуктах реакции ~35 мол. %, селективность по α-метилстиролу ~0 мол. %, производительность по α-метилстиролу ~ 7.4 г/(ч гакт.комп) (рис. 6). Важно отметить, что в диапазоне температур 500–625°С, образующиеся побочные жидкие продукты, такие как бензол, толуол, этилбензол и стирол присутствуют в конденсированной продуктовой смеси в следовых количествах, что указывает на высокую селективность разработанного Re–W-содержащего каталитического конвертера по стиролу. Степень зауглероженности катализатора за 6 ч эксперимента, определенная весовым методом, не превышала 5 мас. %.
Рис. 5.
Сравнение расчетных равновесных и опытных температурных зависимостей основных параметров процесса дегидрирования кумола в α-метилстирол на каталитическом конвертере состава [Fe,Cr]/γ-Al2O3(K,Ce)/α-Al2O3.
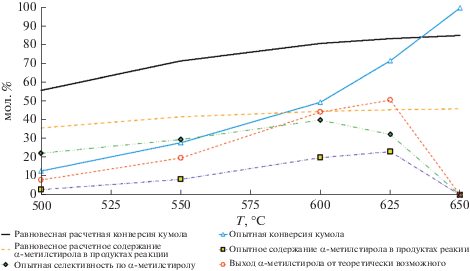
Рис. 6.
Производительность по α-метилстиролу на каталитических конвертерах состава [Re,W]/γ-Al2O3(K,Ce)/α-Al2O3 и [Fe,Cr]/γ-Al2O3(K,Ce)/α-Al2O3 в температурном диапазоне 500–650°С.
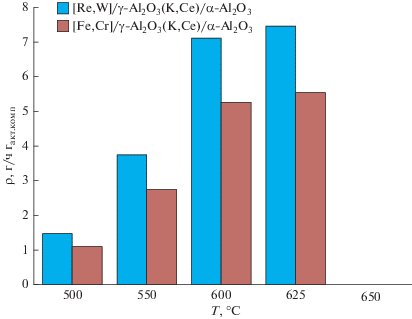
Показано, что при температурах ниже 600°С скорость реакции дегидрирования кумола недостаточно высокая, что не позволяет получать максимально возможное в данных условиях для данного конвертера количество α-метилстирола, а при температурах выше 600°С, интенсификация побочных превращений приводит к увеличению содержания продуктов крекинга и парового риформинга углеводородов в продуктовых газах (табл. 1, 2). Как следствие, это приводит к снижению выхода и селективности по α-метилстиролу, а также к ускоренному закоксовыванию катализатора. При 650°C доля побочных неравновесных превращений кумола возрастает до 100%.
Таблица 1.
Состав продуктовых газов процесса дегидрирования кумола в α-метилстирол на каталитическом конвертере состава [Re,W]/γ-Al2O3(K,Ce)/α-Al2O3 в температурном диапазоне 500–650°С, мол. %
Т, °С | H2 | CO | CO2 | CH4 | C2H6 | C2H4 | C3H8 | C3H6 |
---|---|---|---|---|---|---|---|---|
500 | 98.82 | 0.00 | 0.30 | 0.88 | 0.00 | 0.00 | 0.00 | 0.00 |
550 | 91.88 | 0.00 | 0.65 | 6.77 | 0.10 | 0.31 | 0.05 | 0.24 |
600 | 74.82 | 0.27 | 1.50 | 18.14 | 0.39 | 1.76 | 1.85 | 1.27 |
625 | 66.37 | 1.40 | 3.60 | 22.98 | 0.81 | 3.29 | 0.13 | 1.42 |
650 | 57.49 | 2.20 | 5.00 | 26.00 | 1.51 | 5.50 | 0.00 | 2.30 |
Таблица 2.
Состав продуктовых газов процесса дегидрирования кумола в α-метилстирол на каталитическом конвертере состава [Fe,Cr]/γ-Al2O3(K,Ce)/α-Al2O3 в температурном диапазоне 500–650°С, мол. %
Т, °С | H2 | CO | CO2 | CH4 | C2H6 | C2H4 | C3H8 | C3H6 |
---|---|---|---|---|---|---|---|---|
500 | 90.12 | 0.00 | 4.19 | 5.69 | 0.00 | 0.00 | 0.00 | 0.00 |
550 | 82.98 | 0.00 | 8.34 | 8.68 | 0.00 | 0.00 | 0.00 | 0.00 |
600 | 67.04 | 0.48 | 6.37 | 26.08 | 0.00 | 0.02 | 0.00 | 0.01 |
625 | 54.52 | 1.85 | 12.52 | 31.09 | 0.00 | 0.01 | 0.00 | 0.01 |
650 | 34.88 | 13.65 | 13.35 | 38.12 | 0.00 | 0.00 | 0.00 | 0.00 |
Согласно данным литературных источников, традиционные промышленные процессы дегидрирования кумола в α-метилстирол осуществляют в двухсекционных адиабатических реакторах на больших загрузках (до 100 т) железнооксидных катализаторов, содержащих до 80 мас. % Fe2O3, при температурах 550–580°С, объемной скорости подачи сырья 0.5–1 ч–1, мольном соотношении H2O : кумол = 20 и парциальном давлении кумола 0.08 МПа. Степень превращения кумола при этом составляет ~70 мол. %, селективность по α-метилстиролу ~90 мол. %, выход α-метилстирола на пропущенный кумол ~ 0 мол. %, производительность по α-метилстиролу ~0.3 г/(ч гакт.комп) [15–19, 21, 22].
Более высокие значения некоторых параметров процесса, достигнутые на промышленных катализаторах, по сравнению с результатами, полученными на разработанных нами системах, вероятно, связаны с существенно более низким содержанием активных компонентов, сформированных во внутреннем объеме открытых пор конвертера.
На основании полученных данных можно заключить, что разработанные каталитические конвертеры, содержащие на поверхности стенок каналов пористого керамического носителя малые количества наноразмерных активных частиц рения и вольфрама (менее 0.5 мас. %), уже на стадии опытных разработок составляют значительную конкуренцию существующим промышленным решениям, обеспечивая в ~25 раз бóльшую производительность по α-метилстиролу при меньших затратах на объемы подаваемой воды и загрузку используемого катализатора. Такое заметное преимущество каталитических конвертеров по сравнению с традиционными реакторами с насыпным слоем гранулированного катализатора, по-видимому, связано с улучшенным тепло- и массопереносом реагента в пространственно ограниченном объеме пор конвертера, представляющего собой ансамбль нанореакторов. Возрастание поперечной диффузии молекул субстрата в узких извилистых каналах конвертера приводит к повышению вероятности их контакта с активной поверхностью катализатора, что может служить объяснением интенсификации каталитических превращений и повышению устойчивости конвертера к коксообразованию [23].
По аналогии с ранее проведенными нами работами [24], отдельный интерес может представлять использование интегрированной в отводящий канал конвертера палладий-содержащей мембраны для одновременного извлечения ультрачистого водорода из зоны реакции.
Таким образом, применение каталитических конвертеров в составе гибридных реакторов кассетного типа может стать толчком для создания малогабаритных химических производств, что открывает новые пути развития современных процессов нефтехимии.
Изучение эволюции структуры разработанных каталитических Re–W- и Fe–Cr-содержащих конвертеров в процессе дегидрирования кумола
Структурные исследования исходного и отработанного каталитического конвертера состава [Re,W]/γ-Al2O3(K,Ce)/α-Al2O3. В результате ПЭМ- ЭДС-анализа исходного образца каталитического конвертера состава [Re,W]/γ-Al2O3(K,Ce)/α-Al2O3 обнаружено большое количество индивидуальных атомов и групп атомов рения и вольфрама, гомогенно распределенных по поверхности α‑Al2O3, при этом агломераций атомов в нанокластеры обнаружено не было (рис. 7а, 7б). Этот факт говорит в пользу золь–гель метода как эффективного способа равномерного осаждения небольших количеств высокодисперсных катализаторов атомарного размера.
Рис. 7.
Фотомикрография распределения частиц рения и вольфрама (светлые пятна) по поверхности α-Al2O3 в исходном конвертере состава [Re,W]/γ-Al2O3(K,Ce)/α-Al2O3 (а) и ПЭМ-ЭДС-спектр распределения элементов по его поверхности (б).
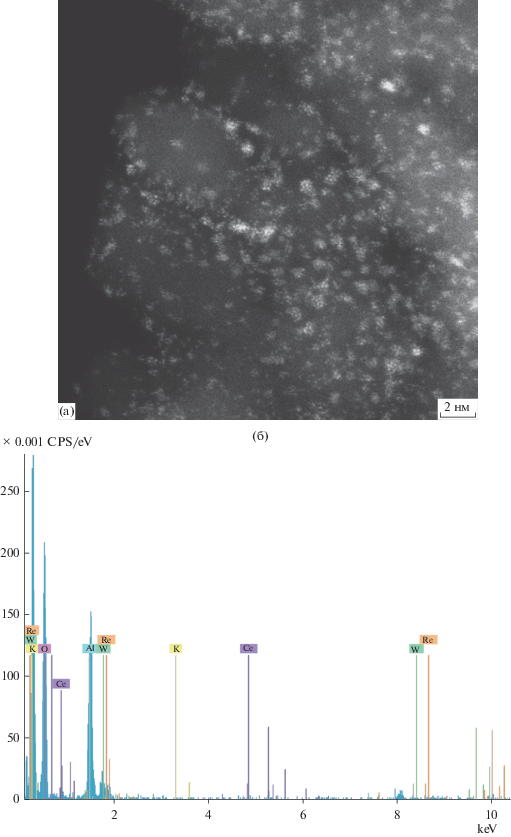
В свою очередь, на отработанном конвертере четко видна агломерация рениевых атомов в нанокластеры, в то время как частицы вольфрама заметной трансформации не подвергаются (рис. 8а, 8б). Это обстоятельство, вероятно, указывает на то, что в ходе дегидрирования кумола происходит восстановление оксидов рения высвобождающимся водородом, что приводит к последующему спеканию образующихся металлических частиц рения.
Рис. 8.
Агломерация частиц рения и отсутствие агломерации вольфрама на поверхности отработанного конвертера состава [Re,W]/γ-Al2O3(K,Ce)/α-Al2O3: а) масштаб изображения 20 нм; б) масштаб изображения 2 нм.
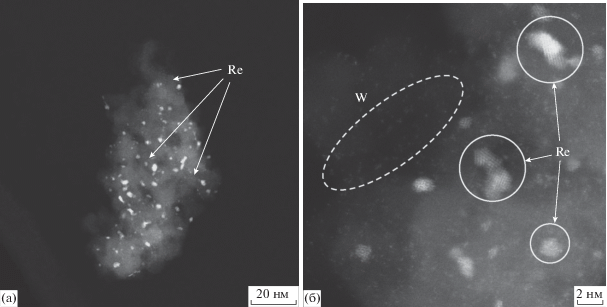
Согласно справочным данным, нанесенный оксид вольфрама(VI) восстанавливается при более высоких температурах (800–900°C) [25], чем температура изучаемого процесса дегидрирования, что, вероятно, и объясняет видимую неизменяемость фракционного состава частиц оксида вольфрама.
К важным наблюдениям относится также и то, что на отснятой поверхности конвертера следов углеродных отложений обнаружено не было, что согласуется с приведенными выше выводами о низкой степени коксования катализатора в ходе процесса дегидрирования.
Таким образом, на основании полученных данных, можно предположить, что одной из функций оксида вольфрама в разработанной системе является препятствие интенсивному зауглероживанию конвертера ввиду пространственного затруднения формирования зародышевых углеродных частиц на каталитически активной поверхности. Однако, этот аспект подлежит более детальному изучению в наших последующих работах.
Данные РФЭС показали, что на поверхности как исходного, так и отработанного конвертера вольфрам неизменно присутствует в степени окисления (6+), что соответствует нанесенному оксиду состава WO3 (рис. 9).
Рис. 9.
РФЭС-спектры (по интенсивности) исходного (верхний) и отработанного (нижний) конвертера состава [Re,W]/γ-Al2O3(K,Ce)/α-Al2O3.
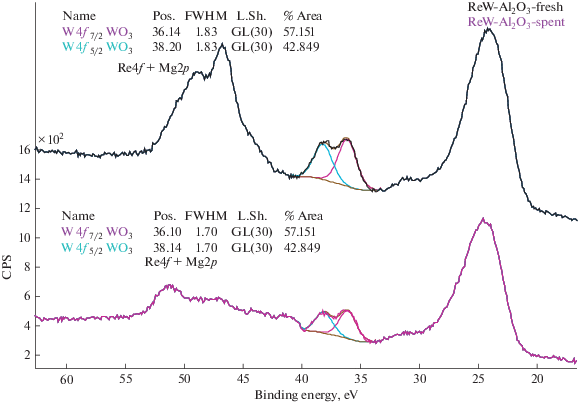
Рений в исходном образце идентифицирован в степени окисления (7+), что соответствует нанесенному оксиду Re2O7. В отработанном образце оксид рения в значительной степени восстановлен до металлического.
В виду того, что пик вольфрама не смещен относительно эталонного, надо полагать, что химического взаимодействия между рением и вольфрамом в системе не происходит. Этот факт может объясняться раздельным нанесением активных компонентов на подложку.
Структурные исследования исходного и отработанного каталитического конвертера состава [Fe,Cr]/γ-Al2O3(K,Ce)/α-Al2O3. Согласно данным ПЭМ-ЭДС-анализа, на поверхности исходного конвертера состава [Fe,Cr]/γ-Al2O3(K,Ce)/α-Al2O3 присутствуют равномерно распределенные индивидуальные атомы железа и хрома, а также наблюдается их небольшие агломерации (рис. 10а, 10б).
Рис. 10.
Фотомикрография распределения частиц железа и хрома по поверхности подложки в исходном конвертере состава [Fe,Cr]/γ-Al2O3(K,Ce)/α-Al2O3 (а) и ПЭМ-ЭДС-спектр распределения элементов по его поверхности (б).
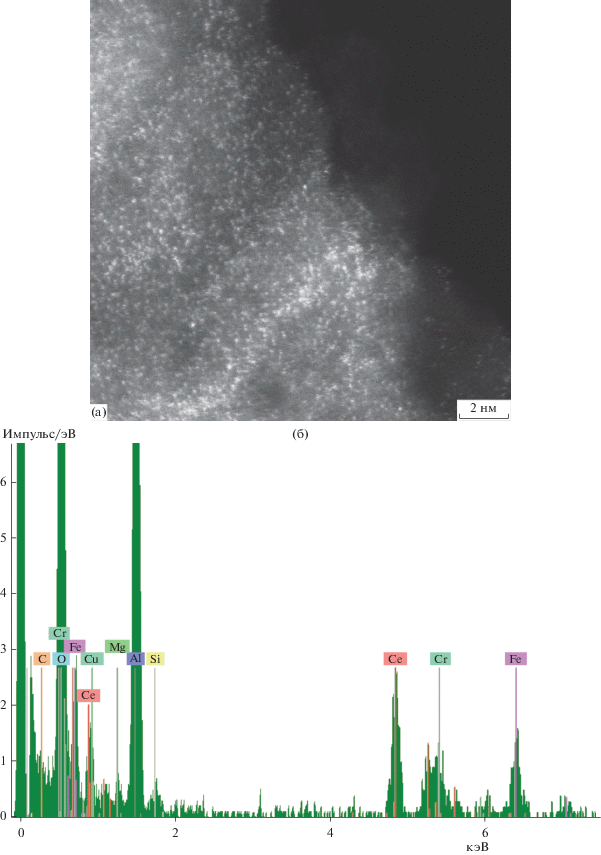
Наряду с этим, на поверхности отработанного конвертера радикального изменения структуры материала, по сравнению с исходным образцом, обнаружено не было. Аналогично идентифицировано равномерное распределение частиц железа и хрома по поверхности подложки в виде, как индивидуальных атомов, так и их небольших агломераций, при этом присутствие углеродных отложений, как и в случае рений–вольфрам-содержащей системой, отмечено в следовых количествах, что свидетельствует о высокой устойчивости рассматриваемой системы к коксообразованию в процессе дегидрирования кумола (рис. 11).
Рис. 11.
Данные ПЭМ-ЭДС-анализа поверхности отработанного конвертера состава [Fe,Cr]/γ-Al2O3(K,Ce)/α-Al2O3.
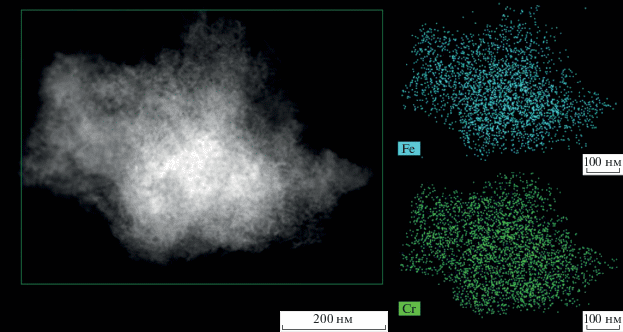
На рис. 12а, 12б представлены РФЭС-спектры Fe2p и Cr2р исходного конвертера [Fe,Cr]/γ-Al2O3(K,Ce)/ α-Al2O3. Для обоих металлов (железа и хрома) только часть спектра 2p3/2 была обработана после вычитания фоновой составляющей по методу Ширли. Спектры идентифицированы на основании базы данных [26].
Установлено, что в соответствии с результатами разложения спектра Fe2p железо присутствует в степени окисления +3, при этом энергия связи основного пика составляет 710.2 эВ, а сателлитного выше на 9.3 эВ.
В спектре Cr2p имеется основной пик с энергией связи 576.0 эВ и четыре мультиплетных пика, наличие которых свидетельствует, что на исходном конвертере помимо оксидов железа содержатся частицы оксида хрома Cr2О3.
Результаты изучения методом РФЭС отработанного конвертера предполагают наличие в нем как компонентов Fe3+, так и Fe2+, пик которого локализован в области энергии 708.5 эВ. Было установлено, что содержание Fe2+ составляет ~25% общего количества железа в образце; это говорит о частичном восстановлении железа водородом во время каталитического процесса (рис. 13а). Изменений же в спектре Cr2p после катализа отмечено не было; это означает, что хром в ходе протекания процесса дегидрирования не меняет своей степени окисления и находится, как и в исходном образце, в зарядовом состоянии Cr+3 (рис. 13б).
ЗАКЛЮЧЕНИЕ
Разработаны пористые керамические каталитические конвертеры состава [Re,W]/γ-Al2O3(K,Ce)/ α-Al2O3 и [Fe,Cr]/γ-Al2O3(K,Ce)/α-Al2O3, полученные с применением самораспространяющегося высокотемпературного синтеза и золь–гель метода, для эффективного дегидрирования кумола в α-метилстирол.
Показано, что рений–вольфрам-содержащая система обладает заметно большей каталитической активностью в изучаемом процессе, по сравнению с железо-хромовой, что, очевидно, связано с фундаментальными различиями в природе этих металлов.
Установлено, что производительность по стиролу на каталитическом конвертере состава [Re,W]/γ‑Al2O3(K,Ce)/α-Al2O3, при его ~100%-ной селективности по жидким продуктам, в ~25 раз больше, чем на традиционных насыпных катализаторах; при этом за 6 ч эксперимента степень зауглероженности конвертера не превышала 5 мас. %.
Преимущество разработанного подхода перед традиционными реакторами с насыпным слоем катализатора заключается в улучшенном тепло- и массопереносе реагентов в пространственно-ограниченном объеме пор конвертера, стенки которых модифицированы небольшим количеством равномерно распределенных высокоактивных наноразмерных каталитических компонентов. Этой особенностью можно объяснить интенсификацию протекания каталитических реакций, в частности, реакции дегидрирования, и повышение устойчивости системы к коксообразованию.
Список литературы
https://www.gminsights.com/industry-analysis/alpha-methyl-styrene-market.
https://www.persistencemarketresearch.com/market-research/alpha-methyl-styrene-market.asp.
https://www.icis.com/explore/resources/news/2000/ 05/22/115657/alpha-methylstyrene/.
Литвин О.Б. Основы технологии синтеза каучуков. 2-е изд., перераб. и доп. М.: Химия, 1964. 648 с.
https://www.mitsuichem.com/en/release/2019/ 2019_0115.htm.
Синтетический каучук. Под ред. Гармонова И.В. Л.: Химия, 1976. 752 с.
Lavrenov A.V., Saifulina L.F., Buluchevskii E.A., Bogdanets E.N. // Catalysis in Industry. 2015. V. 7. № 3. P. 175. https://doi.org/10.1134/S2070050415030083
Kurchatov I.M., Laguntsov N.I., Tsodikov M.V., Fedotov A.S., Moiseev I.I. // Kinetics and Catalysis. 2008. V. 49. № 1. P. 121. https://doi.org/10.1134/S0023158408010151
Tsodikov M.V., Fedotov A.S., Antonov D.O., Uvarov V.I., Bychkov V.Y., Luck F.C. // Intern. J. of Hydrogen Energy. 2016. V. 41. № 4. P. 2424. https://doi.org/10.1016/j.ijhydene.2015.11.113
Fedotov A.S., Antonov D.O., Bukhtenko O.V., Uvarov V.I., Kriventsov V.V., Tsodikov M.V. // Intern. J. of Hydrogen Energy. 2017. V. 42. № 38. P. 24 131. https://doi.org/10.1016/j.ijhydene.2017.07.095
Fedotov A.S., Antonov D.O., Uvarov V.I., Tsodikov M.V., Paul S., Heyte S., Dumeignil F. // Petrol. Chemistry. 2019. V. 59. № 4. P. 401. https://doi.org/10.1134/S0965544119040066
Кантаев А.С., Брус И.Д. Определение размера пор фильтрующего элемента. Издательство Томского политехнического университета, 2014. С. 16.
Uvarov V.I., Alymov M.I., Loryan V.E., Kapustin R.D., Fedotov A.S., Tsodikov M.V. // Novye Ogneupory (New Refractories). 2019. V. 8. P. 59. (In Russ.) https://doi.org/10.17073/1683-4518-2019-8-59-62
Ряшенцева М.А., Миначев Х.М. Рений и его соединения в гетерогенном катализе, М.: Наука, 1983. 247 с.
Корыстов В.А., Жирнов Б.С., Сыркин А.М., Хабибуллин Р.Р., Егоров В.И., Исхаков Ф.Ф. Производство мономера стирола в ОАО “САЛАВАТНЕФТЕОРГСИНТЕЗ”. Учебн. пособие. Уфа: Уфимская государственная академия экономики и сервиса, 2009. 104 с.
Платэ Н.А., Сливинский Е.В. Основы химии и технологии мономеров: Учебн. пособие. М.: Наука, МАИК “Наука/Интерпериодика”, 2002. 696 с.
Адельсон С.В., Вишнякова Т.П., Паушкин Я.М. Технология нефтехимического синтеза. Учебн. пособие для вузов. 2-е изд., перераб. М.: Химия, 1985. 608 с.
Тимофеев В.М., Серафимов Л.А., Тимошенко А.В. Принципы технологии основного органического и нефтехимического синтеза. Учебн. пособие для вузов. 3-е изд. перераб. и доп. М.: Высш. школа, 2010. 408 с.
Соколов Р.С. Химическая технология. Учебн. пособие для вузов. В 2. Т. 2: Металлургические процессы. Переработка химического топлива. Производство органических веществ и полимерных материалов. М.: Гуманит. изд. центр ВЛАДОС, 2000. 448 с.
Carl L. Yaws. Yaws’ Handbook of Thermodynamic and Physical Properties of Chemical Compounds, Knovel: McGraw-Hill, 2003. P. 2078.
Гутник С.П., Кадоркина Г.Л., Сосонко В.Е. Примеры и задачи по технологии органического синтеза. М.: Химия, 1984. 190 с.
Вагапов А. В., Клементьев А.Н., Журавлева М.В., Климентова Г.Ю. // Южно-Сибирский научный вестник. 2019. Т. 26. №. 2. С. 33.
Teplyakov V.V., Tsodikov M.V. In Simulation of Membrane Reactors. Ed. Basile A.and Gallucci F. New York: Nova Science Publishers, 2009. 123 p.
Fedotov A.S., Antonov D.O., Uvarov V.I., Tsodikov M.V. // Intern. J. of Hydrogen Energy. 2018. V. 43. № 14. P. 7046. https://doi.org/10.1016/j.ijhydene.2018.02.060
Wilken T.R., Morcom W.R., Wert C.A., Woodhouse J.B. // Metallurgical Transactions B. 1976. V. 7. № 4. P. 589. https://doi.org/10.1007/BF02698592
Biesinger M.C., Payne B.P., Grosvenor A.P., Lau L.W., Gerson A.R., Smart R.S.C. // Applied Surface Science. 2011. V. 257. № 7. P. 2717. https://doi.org/10.1016/j.apsusc.2010.10.051
Дополнительные материалы отсутствуют.