Доклады Российской академии наук. Химия, науки о материалах , 2021, T. 498, № 1, стр. 69-75
Масштабирование получения оксидов железа в реакциях горения из растворов с добавлением инактивного компонента FeOx
Ш. М. Халиуллин 1, *, **, А. М. Мурзакаев 2, В. Д. Журавлев 1, ***, ****, О. В. Русских 3, член-корреспондент РАН В. Г. Бамбуров 1
1 Институт химии твердого тела
Уральского отделения Российской академии наук
620990 Екатеринбург, Россия
2 Институт электрофизики
Уральского отделения Российской академии наук
620016 Екатеринбург, Россия
3 Уральский федеральный университет
имени первого Президента России Б.Н. Ельцина
620002 Екатеринбург, Россия
* E-mail: shamil58@rambler.ru
** E-mail: khaliullin@ihim.uran.ru
*** E-mail: zhuravlev47@bk.ru
**** E-mail: zhvd@ihim.uran.ru
Поступила в редакцию 30.03.2021
После доработки 19.05.2021
Принята к публикации 04.06.2021
Аннотация
Исследованы процессы получения оксидов железа горением из нитратных растворов с двойным топливом, состоящим из мочевины и лимонной кислоты, на предварительно приготовленном порошке FeOx. Впервые продемонстрирована возможность синтеза в лабораторных условиях до 100 г целевого продукта в относительно небольшом реакторе объемом 4 дм3. Полученные нанодисперсные материалы представляют собой хорошо закристаллизованную смесь оксидов Fe3O4 и α-Fe2O3. Последовательное увеличение массы порошка FeOx приводит к увеличению массовой доли фазы α-Fe2O3 до 91% на заключительной стадии синтеза.
ВВЕДЕНИЕ
Синтез горением из растворов, который в англоязычной литературе называется SCS (Solution Combustion Synthesis), является простым и доступным методом для получения оксидов и неорганических соединений [1]. Горением из растворов были успешно синтезированы композиты различного состава [2–9]. В работе [3] описано получение катализатора Co3O4/γ-Al2O3 методом горения в матрице γ-Al2O3, пропитанной раствором Co(NO3)2 с мочевиной. Данный вариант получил название синтез горением с пропиткой, или Impregnation Combustion Synthesis (ICS) [2]. Оксиды α-Al2O3 [4–6, 9] и SiO2 [6, 8], вследствие их стабильности, часто используются в качестве матриц для пропитки. Применяются матрицы и из других оксидов, например ZnO [7]. В исследованиях [3, 6] отмечено, что в этом варианте горение является, в основном, беспламенным и распространяется в виде волны. Во фронте горения развиваются относительно невысокие температуры – максимальная температура составляла 573°C [6]. Все это указывает на то, что введение инактивного (инертного) для реакционной среды компонента снижает скорость и увеличивает продолжительность реакций SCS.
Влияние различных способов внесения инертной добавки диоксида циркония, стабилизированного иттрием (YSZ, yttrium stabilized zirconium), в реакционный раствор в количестве 0–60 масс. % от массы получаемых нанокомпозитов mAl2O3–nYSZ исследованы в работе [2]. Было обнаружено, что частицы порошка YSZ покрыты слоем α-Al2O3. J. Shin и соавт. [10] изучали низкотемпературную трансформацию гибридного нанокомпозита Fe2O3, состоящего из наночастиц и нитроцеллюлозы, в Fe3O4@C структуру “ядро–оболочка”. Утверждается, что за несколько секунд происходит фазовый переход гематит–магнетит при максимальной температуре 520°C.
С увеличением массы получаемых материалов в процессах SCS возрастают количество и скорость выделения газовых продуктов, температура может повышаться вплоть до 1000°C. Поэтому обычно получают небольшое количество (2–5 г) целевых продуктов. Поскольку добавление инертного компонента в реакционную среду снижает температуру и скорость реакций SCS, то представляют научный интерес фундаментальный и прикладной аспекты реакций горения на предварительно полученном продукте того же состава.
В работе [11] приведены многочисленные области применения наноструктурированных оксидов железа. Одной из наиболее многообещающих является использование как Fe3O4, так и α-Fe2O3 в качестве анодов Li-ионных батарей. Из смешанных оксидов железа всегда можно получить монофазные Fe3O4 или α-Fe2O3. Поэтому модельной системой выбраны смешанные оксиды железа.
Целью настоящей работы является масштабирование процесса получения целевого продукта – смешанного оксида железа FeOx – с увеличенной до 100 г массой в одном цикле. Тип топлива, соотношение топливо/окислитель оказывают влияние как на максимальную температуру синтеза, так и на фазовый состав оксидов железа, получаемых в реакциях горения из растворов [11]. Непосредственно после синтеза с глицином, мочевиной и лимонной кислотой целевые продукты представляют собой смесь оксидов α-Fe2O3 и Fe3O4 в различных массовых соотношениях. Поэтому отдельной задачей было исследование фазообразования при ICS в системе Fe(NO3)3–топливо (глицин, мочевина, лимонная кислота)–H2O–FeOx непосредственно после синтеза.
ЭКСПЕРИМЕНТАЛЬНАЯ ЧАСТЬ
В качестве исходных материалов использовали нитрат железа девятиводный Fe(NO3)3 · 9H2O (х. ч.), глицин NH2CH2COOH (х. ч.), мочевину (NH2)2CO (х. ч.) и моногидрат лимонной кислоты C6H8O7 · H2O (х. ч.). Fe(NO3)3 · 9H2O растворяли в дистиллированной воде. Концентрация раствора в пересчете на [Fe2O3] составила 69.4 г л–1.
Для подбора оптимального типа и количества топлива проводили предварительные эксперименты с монотопливом (NH2CH2COOH, (NH2)2CO и C6H8O7 · H2O) в алюминиевом цилиндрическом реакторе с диаметром основания 11.5 см и объ-емом 1 дм3 на получение 5 г Fe2O3 в единичном опыте. Для этого в 72 мл раствора Fe(NO3)3 · 9H2O растворяли требуемое количество топлива в соответствии с реакциями (1)–(3) при соотношении топливо/окислитель φ = 1.0. Смесь наливали в реактор, который оставляли открытым и помещали на электрическую нагревательную панель мощностью 1 кВт. Параметр φ принимается за единицу, если реакция не сопровождается выделением кислорода и не потребляет его из атмосферы. Реакции (1)–(3), используемые для расчета топлива, приведены на получение Fe2O3.
(1)
$\begin{gathered} {\text{Fe}}{{\left( {{\text{N}}{{{\text{O}}}_{{\text{3}}}}} \right)}_{3}} + 1.667\varphi {\text{N}}{{{\text{H}}}_{2}}{\text{C}}{{{\text{H}}}_{2}}{\text{COOH}} + \hfill \\ + \,3.75(\varphi --1){{{\text{O}}}_{2}} \to 0.5{\text{F}}{{{\text{e}}}_{{\text{2}}}}{{{\text{O}}}_{3}} + (1.5 + 0.833\varphi ){{{\text{N}}}_{2}} + \hfill \\ + \,4.167\varphi {{{\text{H}}}_{{\text{2}}}}{\text{O}} + 3.333\varphi {\text{C}}{{{\text{O}}}_{2}} \hfill \\ \end{gathered} $(2)
$\begin{gathered} {\text{Fe}}{{\left( {{\text{N}}{{{\text{O}}}_{{\text{3}}}}} \right)}_{3}} + 2.5\varphi {{\left( {{\text{N}}{{{\text{H}}}_{{\text{2}}}}} \right)}_{2}}{\text{CO}} + 3.75(\varphi --1){{{\text{O}}}_{2}} \to \hfill \\ \to 0.5{\text{F}}{{{\text{e}}}_{{\text{2}}}}{{{\text{O}}}_{3}} + (1.5 + 2.5\varphi ){{{\text{N}}}_{2}} + 5\varphi {{{\text{H}}}_{{\text{2}}}}{\text{O}} + 2.5\varphi {\text{C}}{{{\text{O}}}_{2}} \hfill \\ \end{gathered} $(3)
$\begin{gathered} {\text{Fe}}{{\left( {{\text{N}}{{{\text{O}}}_{{\text{3}}}}} \right)}_{{\text{3}}}} + 0.833\varphi {{{\text{C}}}_{{\text{6}}}}{{{\text{H}}}_{{\text{8}}}}{{{\text{O}}}_{7}} + 3.75(\varphi --1){{{\text{O}}}_{2}} \to \hfill \\ \to 0.5{\text{F}}{{{\text{e}}}_{{\text{2}}}}{{{\text{O}}}_{3}} + 1.5{{{\text{N}}}_{2}} + 3.333\varphi {{{\text{H}}}_{{\text{2}}}}{\text{O}} + 5\varphi {\text{C}}{{{\text{O}}}_{2}} \hfill \\ \end{gathered} $При упаривании воды из реакционного раствора образовывался гель, который затем превращался в ксерогель. В некоторый момент времени при реакции с глицином или мочевиной происходило возгорание, и через несколько секунд на дне реактора оставался ажурный слой порошка красно-коричневого и сиренево-коричневого оттенков соответственно. При нагревании реакционной смеси с лимонной кислотой видимого возгорания не наблюдалось. Окислительно-восстановительная реакция проходила в виде медленно распространяющейся волны обугливания ксерогеля.
Масштабирование процесса SCS оксидов железа проводили в цилиндрическом алюминиевом реакторе с диаметром основания 21 см и объемом 4 дм3. Технологический прием заключался в дозагрузке рабочего раствора в реактор после очередного синтеза порции материала, в результате чего накапливался инертный (готовый) оксид в серии из нескольких опытов.
Температуры горения в реакторе измеряли с помощью трех термопар типа ТПП и фиксировали регистратором видеографическим Ш932.9А 29.015/1 (ООО “Сенсорика”, Россия) с периодом измерений 0.3 с. Одна из термопар располагалась на оси реактора около самого дна, не касаясь его. Две другие располагались на расстоянии 20 и 40 мм от дна реактора по обе стороны от оси на расстоянии 20 мм.
Рентгенофазовый анализ (РФА) выполняли на дифрактометре Shimadzu XRD-7000 (Япония) в Cu–Kα излучении с длиной волны λ = 1.54056 нм в диапазоне углов 2θ = 20–80°, с дискретностью 0.05° и экспозицией 3 с на точку. Фазовый состав образцов идентифицировали с помощью программы PowderCell (Version 2.4) с использованием базы данных PDF2. Определение дисперсности полученных порошков проводили на лазерном анализаторе размеров частиц HORIBA модели Partica LA-950 (Япония). Пробоподготовку проводили путем измельчения порошков в агатовой ступке.
Микроструктуру частиц полученных порошков исследовали в просвечивающем электронном микроскопе (ПЭМ) JEM-2100 (Япония) с LaB6 катодом при ускоряющем напряжении 200 кВ с разрешением по точкам 0.19 нм и по линиям 0.14 нм.
РЕЗУЛЬТАТЫ И ИХ ОБСУЖДЕНИЕ
Для получения только стабильных форм оксидов железа α-Fe2O3 и Fe3O4 и предотвращения образования вюстита Fe0.947O, который при температурах ниже 400°С диспропорционирует с образованием Fe и Fe3O4 [12], необходимо, чтобы реакции SCS протекали при температурах ниже точки Шардона (575°C) [12]. При использовании в качестве монотоплива глицина или мочевины максимальные температуры 880 и 612°C соответственно, превышают температуру точки Шардона (рис. 1a). Реакция взаимодействия нитрата железа с лимонной кислотой с максимальной температурой 482°C не относится к типу реакций SCS [11], но лимонная кислота служит ингибитором в реакциях горения из растворов [13].
Рис. 1.
(a) Температурные профили горения из растворов Fe(NO3)3 с органическим топливом: 1 – φгл. = 1.0; 2 – φмоч. = 1.0; 3 – φлим. = 1.0; 4 – (φмоч. = 0.8) + (φлим. = 0.3); 5 – (φмоч. = 0.5) + (φлим. = 0.5); 6 – (φмоч. = 0.3) + (φлим. = 0.7) (кривые 1–6 соответственно); (б) Температурные профили горения из растворов с органическим топливом: I – синтез первых 25 г FeOx, II – синтез 25 г FeOx на 25 г предварительно полученного продукта, III – синтез 25 г FeOx на 50 г предварительно полученного продукта, IV – синтез 25 г FeOx на 75 г предварительно полученного продукта (кривые I–IV соответственно).
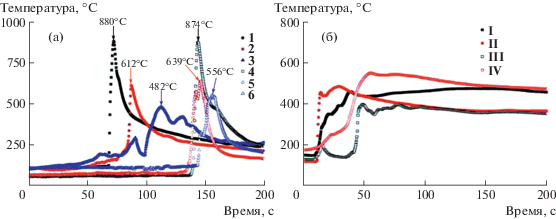
Окисление поверхности зерен магнетита до маггемита начинается при 200°C и заканчивается при достижении 400°C [14]. Образование упорядоченной структуры гематита начинается с температур выше 550°C [15]. Поэтому для масштабирования процесса получения FeOx методом SCS с элементами ICS необходимо для каждого конкретного реактора подбирать состав топлива, чтобы температуры горения не превышали 575°C. На основании полученных температурных профилей (рис. 1a) было определено, что для синтеза исходного FeOx предпочтительным является двойное топливо, состоящее из мочевины и лимонной кислоты в количестве φмоч. = 0.3, φлим. = 0.7 для первоначального опыта (рис. 1a), так как его фазовый состав представлен оксидами α-Fe2O3 и Fe3O4 (рис. 2), а максимальная температура горения равна 556°C.
Рис. 2.
РФА образцов 1–6 (кривые 1–6 соответственно) после SCS: G – рефлексы гематита, M – рефлексы магнетита.
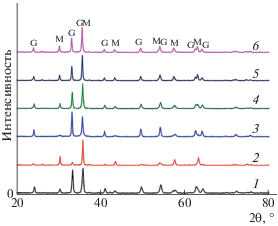
По данным РФА непосредственно после SCS образуется смесь оксидов Fe3O4 и α-Fe2O3 (рис. 2, табл. 1). Наибольшее содержание Fe3O4 зафиксировано при синтезе с мочевиной в образце 2, а наименьшее – в образце 3 с лимонной кислотой (рис. 2). Использование двойного топлива дает содержание Fe3O4 от 33.6 до 42% (табл. 1). Расчеты по формуле Шеррера показывают, что средний размер первичных кристаллитов в образцах 2–6 варьируется от 26 до 35 нм (табл. 1).
Таблица 1.
Содержание фаз оксидов железа после SCS c разными видами топлива
№ образца | φ | Fe3O4 | α-Fe2O3 | Tmax, °C | ||
---|---|---|---|---|---|---|
Содержание, % | Средний размер кристаллитов, нм | Содержание, % | Средний размер кристаллитов, нм | |||
1 | φгл. = 1.0 | 25.1 | 19 | 74.9 | 37 | 880 |
2 | φмоч. = 1.0 | 79.4 | 31 | 20.6 | 29 | 612 |
3 | φлим. = 1.0 | 11.7 | – | 88.3 | 31 | 482 |
4 | φмоч. = 0.8 | 33.6 | 26 | 66.4 | 27 | 874 |
φлим. = 0.3 | ||||||
5 | φмоч. = 0.5 | 42.0 | 30 | 58.0 | 34 | 639 |
φлим. = 0.5 | ||||||
6 | φмоч. = 0.3 | 40.8 | 30 | 59.2 | 35 | 556 |
φлим. = 0.7 |
Масштабирование SCS c элементами ICS проводили в реакторе объемом 4 дм3, который накрывали крышкой с отверстиями для термопар и выхода исходящих газов. В реакторе последовательно проводили эксперименты по увеличению массы получаемого продукта: 5, 12.5 и 25 г. Вследствие ограничений по параметрам вытяжной вентиляции максимальная масса получаемого продукта в единичном опыте не должна была превышать 25 г. Это эквивалентно 360 мл раствора Fe(NO3)3 ⋅ 9H2O, в котором были растворены соответственно уравнению (4) количества мочевины и лимонной кислоты, φмоч. = 0.3 и φлим. = 0.7.
(4)
$\begin{gathered} {\text{Fe(N}}{{{\text{O}}}_{{\text{3}}}}{{{\text{)}}}_{3}} + 0.75{{({\text{N}}{{{\text{H}}}_{{\text{2}}}}{\text{)}}}_{{\text{2}}}}{\text{CO}} + 0.58{{{\text{C}}}_{{\text{6}}}}{{{\text{H}}}_{{\text{8}}}}{{{\text{O}}}_{7}} \to \\ \to 0.5{\text{F}}{{{\text{e}}}_{{\text{2}}}}{{{\text{O}}}_{3}} + 2.25{{{\text{N}}}_{2}} + 4.23{\text{C}}{{{\text{O}}}_{2}} + 3.82{{{\text{H}}}_{{\text{2}}}}{\text{O}} \\ \end{gathered} $Согласно уравнению (4') окислительно-восстановительной реакции по синтезу образца I, записанному согласно полученным массовым долям фаз (табл. 2), выделяется небольшое количество кислорода:
Таблица 2.
Характеристики порошков FeOx, полученных методом SCS c элементами ICS
Образец (масса в г) | Содержание фаз, % | Средний размер кристаллитов непосредственно после синтеза, нм | Средний размер кристаллитов после отжига при 900°C, нм | Средний размер агломератов непосред-ственно после синтеза, мкм | Tmax, °C | ||
---|---|---|---|---|---|---|---|
Fe3O4 | α-Fe2O3 | Fe3O4 | α-Fe2O3 | α-Fe2O3 | FeOx | ||
I (25) | 88 | 12 | 73 | 21 | 48 | 7.58 | 460 |
II (50) | 60 | 40 | 30 | 32 | 49 | 5.28 | 485 |
III (75) | 21 | 79 | 24 | 33 | 48 | 4.10 | 399 |
IV (100) | 9 | 91 | 22 | 33 | 46 | 6.59 | 550 |
После достижения температуры примерно 150°C исходящие газы окрасились в бурый цвет, указывающий на присутствие NO2. Через 2–3 с произошло возгорание. После окончания горения на дне реактора остался слой ажурного порошка сиренево-коричневого оттенка толщиной 1–1.5 см (образец I).
Через небольшой промежуток времени, необходимый для остывания реактора ниже температуры кипения воды, в него помещали следующую порцию реакционного раствора, содержащего 360 мл раствора Fe(NO3)3 · 9H2O, мочевину и лимонную кислоту в соотношениях φмоч. = 0.5, φлим. = 0.5. Раствор полностью пропитывал находящуюся в реакторе массу порошка. Соотношения между мочевиной и лимонной кислотой изменили, чтобы компенсировать снижение максимальной температуры под влиянием инертной добавки. После окончания синтеза в реакторе было накоплено 50 г FeOx (образец II). Проведя эту процедуру еще 2 раза, получили 100 г продукта. Количества мочевины и лимонной кислоты составляли: в 3-м синтезе φмоч. = 0.7, φлим. = 0.3 (образец III), в 4-м синтезе φмоч. = 1.0, φлим. = 0.0 (образец IV).
Синтез образцов I, II, III сопровождался возникновением открытого пламени, а синтез образца IV проходил в виде распространяющейся волны без открытого пламени. Во всех опытах перед возгоранием из реактора в течение нескольких секунд выделялся бурый газ. Максимальные температуры горения не превышали 550°C (рис. 1б). После окончания горения на дне реактора оставался слой порошка толщиной 1.5–2 см. С каждым последующим опытом происходило его уплотнение. Максимальная плотность сформировавшегося синтезированного продукта в реакторе была меньше 0.15 г см‒3.
На основании результатов опытов 4–6 (рис. 2, табл. 1) ожидали, что содержание фазы Fe3O4 в образцах I–III будет составлять 35–42%. Однако изменение условий горения (закрытый реактор большего размера вместо открытого малого реактора) повлияло на фазообразование оксидов железа. Уже при первом акте синтеза (φмоч. = 0.3, φлим. = 0.7) образовалось 88% фазы Fe3O4 (рис. 3, табл. 2). Увеличение количества инертной массы FeOx, пропитываемой реакционным раствором, привело к дальнейшему снижению доли фазы Fe3O4 и увеличению доли α-Fe2O3 (рис. 3), которая в образце IV достигла 91% (табл. 2). Этот результат невозможно объяснить окислением поверхности зерен магнетита вследствие малой толщины этого слоя [12]. Одной из вероятных причин окисления Fe3O4 является присутствие раствора азотнокислого железа с pH 3. Магнетит гораздо легче растворяется в кислотах по сравнению с гематитом [16]. При переходе в раствор ионы Fe2+ окисляются до Fe3+. В результате уменьшается доля фазы магнетита и увеличивается доля гематита. Другой причиной может быть турбулентный тип горения в реакторе, при котором в некоторых локальных областях реактора создаются разрежения, способствующие затягиванию в реактор воздуха из атмосферы.
Рис. 3.
РФА образцов FeOxI–IV (кривые I–IV соответственно), полученных методом SCS с элементами ICS: G – рефлексы гематита, M – рефлексы магнетита.
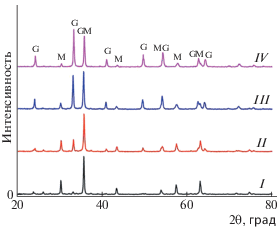
Средний размер кристаллитов фазы Fe3O4 уменьшался от опыта I к опыту IV c 73 до 22 нм (табл. 2), что указывает на окисление зерен при проведении последовательных синтезов SCS с элементами ICS с увеличением массы пропитываемого порошка. Средний размер кристаллитов фазы α-Fe2O3 в опытах II–IV составил 32–33 нм. Исключением является первоначальный синтез, который выполнялся только в режиме SCS. Следовательно, отсутствовал эпитаксиальный рост размера первичных кристаллитов при последовательных синтезах в пропитанном продукте.
После отжига при 900°C во всех образцах осталась только фаза гематита, а средний размер кристаллитов α-Fe2O3 выровнялся до 46–49 нм. Уменьшение среднего размера агломератов с 7.58 до 4.10 мкм в опытах I–III (табл. 2) объясняется процессами первичной рекристаллизации, которые запускаются при каждом горении. Более высокая температура в опыте IV (рис. 1б) запустила процесс собирательной рекристаллизации, которая привела к росту среднего размера агломератов до 6.59 мкм.
На снимках, сделанных на просвечивающем электронном микроскопе (ПЭМ) (рис. 4), видно, что порошок FeOx состоит из бесформенных наночастиц, объединенных в агломераты. Фазовый состав и межплоскостные расстояния в синтезированных оксидах определили с помощью программной обработки снимков ПЭМ ВР (высокого разрешения) (рис. 4). Расшифровка картины прямого разрешения с помощью функции быстрого преобразования Фурье показала, что частицы имеют структуру достаточно хорошо закристаллизованных Fe3O4 и α-Fe2O3. Вследствие малой доли фазы Fe3O4 в образце IV на снимке выбранного фрагмента порошка она не присутствует.
ЗАКЛЮЧЕНИЕ
Впервые продемонстрировано масштабирование получения оксидов железа массой до 100 г реакцией горения из растворов. Процесс масштабирования выполняли путем последовательного добавления новых порций раствора в реактор, содержащий продукт предыдущего сжигания. Получены наноструктурированные прекурсоры смешанных оксидов железа. Выявлено последовательное увеличение доли фазы α-Fe2O3 с 12% при первом сжигании порции 25 г до 91% после четвертого сжигания.
Полученные наноструктурированные оксиды железа после отжига на воздухе превращаются в монофазный α-Fe2O3, а после прокаливания в атмосфере аргона преобразуются в монофазный Fe3O4. Несложная трансформация из одной фазы в другую обеспечивает перспективы их применения как в качестве пигментов, так и основы анодов литий-ионных батарей, а также в медицине и др. областях.
Список литературы
Varma A., Mukasyan A.S., Rogachev A.S., Manu-kyan Kh.V. // Chem. Rev. 2016. V. 116. P. 14493− 14586. https://doi.org/10.1021/acs.chemrev.6b00279
Khaliullin Sh.M., Nefedova K.V., Zhuravlev V.D. // Int. J. Self-Propag. High-Temp. Synth. 2019. V. 28. № 1. P. 1–9. https://doi.org/10.3103/S1061386219010072
Wang Q., Peng Y., Fu J., Kyzas G.Z., Billah S.M.R., An S. // Appl. Catal., B. 2015. V. 168–169. P. 42–50. https://doi.org/10.1016/j.apcatb.2014.12.016
Rezaee L., Haghighi M. // RSC Adv. 2016. V. 6. № 40. P. 34055–34065. https://doi.org/10.1039/c6ra02973f
Barros B.S., Melo D.M.A., Libs S., Kiennemann A. // Appl. Catal., A. 2010. V. 378. № 1. P. 69–75. https://doi.org/10.1016/j.apcata.2010.02.001
Kumar A., Mukasyan A.S., Wolf E.E. // Appl. Catal., A. 2010. V. 372. № 2. P. 175–183. https://doi.org/10.1016/j.apcata.2009.10.032
Habibi M.H., Karimi B. // J. Ind. Eng. Chem. 2014. V. 20. № 4. P. 1566–1570. https://doi.org/10.1016/j.jiec.2013.07.048
Shi L., Yang R., Tao K., Yoneyama Y., Tan Y., Tsu-baki N. // Catal. Today. 2012. V. 185. № 1. P. 54– 60. https://doi.org/10.1016/j.cattod.2011.10.015
Baneshi J., Haghighi M., Jodeiri N., Abdollahifar M., Ajamein H. // Ceram. Int. 2014. V. 40. № 9. Part A. P. 14177–14184. https://doi.org/10.1016/j.ceramint.2014.06.005
Shin J., Lee K.Y., Yeo T., Choi W. // Sci. Rep. 2016. V. 6. P. 21792. https://doi.org/10.1038/srep21792
Khaliullin Sh.M., Koshkina A.A. // Ceram. Int. 2021. V. 47. № 9. P. 11942–11950. https://doi.org/10.1016/j.ceramint.2021.01.035
Рябухин А.Г., Тепляков Ю.Н., Гусева С.В. // Изв. ЧНЦ УрО РАН. 2003. № 1(18). С. 33–36. https://www.csc.ac.ru/news/2003_1/2003_1_4_2.pdf
Khaliullin Sh.M., Zhuravlev V.D., Ermakova L.V., Buldakova L.Yu., Yanchenko M.Yu., Porotnikova N.M. // Int. J. Self-Propag. High-Temp. Synth. 2019. V. 28. № 4. P. 226–232. https://doi.org/10.3103/S1061386219040058
Ламберов А.А., Дементьева Е.В., Кузьмина О.В., Хазеев Б.Р. // Вестн. Казан. технол. ун-та. 2013. Т. 16. № 1. С. 37–41. https://elibrary.ru/download/elibrary_18725973_50330483.pdf
Юрьев Б.П., Гольцев В.А. // Изв. вуз. Черная металлургия. 2016. Т. 59. № 10. С. 735–739. https://doi.org/10.17073/0368-0797-2016-10-735-739
Тодт Ф. Коррозия и защита от коррозии. Коррозия металлов и сплавов. Методы защиты от коррозии. Л.: Химия, 1966. С. 124. 848 с.
Дополнительные материалы отсутствуют.
Инструменты
Доклады Российской академии наук. Химия, науки о материалах