Доклады Российской академии наук. Химия, науки о материалах , 2021, T. 498, № 1, стр. 55-58
Реосинтез изделий и СВС-штамповка
А. М. Столин 1, П. М. Бажин 1, *, П. А. Столин 1, член-корреспондент РАН М. И. Алымов 1
1 Институт структурной макрокинетики
и проблем материаловедения им. А.Г. Мержанова Российской академии наук
142432 Черноголовка, Московская обл., Россия
* E-mail: bazhin@ism.ac.ru
Поступила в редакцию 08.12.2020
После доработки 12.03.2021
Принята к публикации 17.03.2021
Аннотация
Предложен новый метод – СВС-штамповка, ‒ основанный на использовании реологического эффекта тиксотропии. Обсуждаются перспективные возможности этого метода для прямого получения компактных металлокерамических и керамических изделий заданных формы и размера из продуктов синтеза на одной установке в одну технологическую стадию. На примере материала на основе МАХ-фазы Ti3AlC2 представлена эволюция структуры продуктов синтеза в ходе химического превращения в условиях высокотемпературного сдвигового деформирования.
ВВЕДЕНИЕ
В настоящее время в металлургии бурно развивается новое направление ‒ металлургия тиксотропных материалов, находящихся в твердожидком состоянии, с использованием жидкофазных процессов [1–3]. Совершенствованию этих технологий уделяется большое внимание в ведущих научных центрах и промышленных фирмах Западной Европы, США, Японии и других стран [4, 5].
Одновременно в технологии самораспространяющегося высокотемпературного синтеза (СВС) интенсивно развиваются методы твердофазного прямого получения изделий из современных металлокерамических и керамических материалов, сочетающие процессы горения и высокотемпературного сдвигового деформирования при воздействии на продукты горения внешним давлением. Начиная с 1984 г. были разработаны методы СВС-экструзии, СВС-измельчения и свободного СВС-сжатия [6]. Эти новые технологические процессы объединяет использование пришедшего из технологии полимеров, но ранее не используемого отечественными металлургами, реологического эффекта «тиксотропии» ‒ снижения вязкости структурированных твердых или твердожидких продуктов синтеза во времени [7, 8]. В 1992 г. совмещение СВС с процессами сдвигового деформирования назвали реосинтезом (от греческого “rheo” ‒ течь) [9].
Специфика реосинтеза состоит в том, что формование изделий происходит в твердой фазе. Даже в случаях, когда температура горения ниже температур плавления исходных компонентов и продуктов химической реакции, материал обладает способностью к формованию [10]. Разработанные новые технологические процессы формования изделий являются разновидностью процессов in situ, поскольку на основе тугоплавких неорганических соединений они позволяют получать компактные композиционные материалы и изделия из этих материалов в одну технологическую стадию в одной установке, не разделяя эти процессы в пространстве и времени.
Представление о возможных способах управления твердофазными процессами реосинтеза подсказало идею разработки нового метода получения изделий из современных металлокерамических и керамических материалов, который можно назвать СВС-штамповкой.
Цель исследования – представить общую характеристику нового метода СВС-штамповки, изучить эволюцию структуры материала в ходе химического превращения и последующего формования.
ЭКСПЕРИМЕНТ И ОБСУЖДЕНИЕ РЕЗУЛЬТАТОВ
В качестве объекта исследования выбраны металлокерамические материалы на основе МАХ-фазы из расчета на образование стехиометрического состава Ti3AlC2. Исходную шихту перемешивали в следующем соотношении компонентов, масс. %: 73 (Ti)‒15 (Al)‒12 (C) и прессовали заготовку в холодном состоянии до относительной плотности 0.7. Затем заготовку размещали в предварительно изготовленную Г-образную оснастку заданной формы и размера. Волну горения инициировали локальным нагревом вольфрамовой спирали и через заданное время прессовали продукты горения под давлением 20 МПа. После уплотнения горячих продуктов синтеза и формования материала были получены компактные пластины с угловым вырезом (рис. 1). Такая форма пластин диктовалась практической задачей изготовления электродов для электролиза цветных металлов. Ранее вырезка Г-образного профиля из керамических пластин приводила к образованию в них трещин, что и подсказало идею применения процесса штамповки для формирования изделий заданной формы.
Для разработки научных принципов управления процессом СВС-штамповки необходимо установить закономерности эволюции структуры продуктов синтеза в ходе химического превращения в условиях высокотемпературного сдвигового деформирования. В волне горения исходные реагенты претерпевают ряд физических и химических превращений. Вначале материал представляет собой суспензию, состоящую из жидкого алюминия, в которой присутствуют твердые частицы титана и сажи (рис. 2).
Рис. 2.
Эволюция структуры в процессе горения и последующего формования и изменение температуры горения во времени (зеленая кривая).
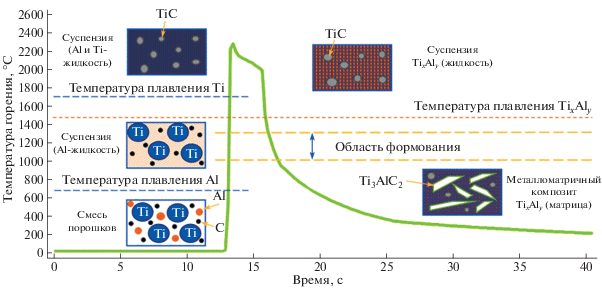
Далее, менее чем за 1 с, при повышении температуры происходит плавление титана и его взаимодействие с алюминием и сажей. Формируется второй тип суспензии, состоящей из кристаллов карбида титана, распределенных в матрице из расплавленных титана, алюминия и начинающего формирование из них интерметаллида Ti‒Al. Постепенно кристаллы карбида титана укрупняются, а расплавленные алюминий и титан образуют жидкость из алюминида титана различной стехиометрии (третий вид суспензии при горении), за счет чего вязкость материала снижается. При остывании синтезированного материала происходит взаимодействие жидкого алюминида с кристаллами карбида титана с образованием зерен тройного соединения МАХ-фазы Ti3AlC2, которые постепенно увеличиваются в размерах и формируется металломатричный композит. Образование МАХ-фазы происходит в интервале температур 1350‒1500°С [11]. Анализируя термограмму, можно сказать, что такое образование начинается при переходе интерметаллида из жидкого состояния в твердое, что повышает вязкость материала. Заканчивается образование МАХ-фазы уже в твердофазном состоянии. Как установлено ранее [11], если температурно-временной интервал образования этой фазы мал, то в конечном продукте синтеза остаются промежуточные продукты в виде карбида титана и интерметаллидов. В настоящей работе конечный фазовый состав материала составил (масс. %): 80 (Ti3AlC2)–5 (TiC)‒15 (TixAly).
Методы, сочетающие процессы горения и последующее высокотемпературное деформирование, позволяют варьированием технологическими и конструктивными параметрами процесса увеличивать температурно-временной интервал, и тем самым способствовать получению материала с максимальным содержанием МАХ-фазы [12]. В результате за несколько секунд формируется металломатричный композит ‒ материал, содержащий в матрице интерметаллида TixAly частицы карбида титана и зерен Ti3AlC2. Способность к формуемости СВС-материалы проявляют лишь в определенном температурно-временном интервале при нагрузках, когда внутренняя структура материала разрушается и, как следствие, происходит уменьшение вязкости структурированных твердых или твердожидких продуктов синтеза со временем. Следует отметить, что такая возможность обеспечивается самой химической реакцией в условиях сдвигового деформирования. Благодаря этому эффекту становится технически возможным (путем создания соответствующих температурных условий) обеспечивать контролируемый перевод материалов в твердожидкое состояние и их стабильное пребывание в этом состоянии в течение достаточно длительного промежутка времени и, как следствие, обеспечить возможность формования изделий из тугоплавких неорганических соединений непосредственно в процессах СВС в условиях высокотемпературного сдвигового деформирования. Формование композитов возможно лишь тогда, когда матрица находится в вязко-пластичном состоянии. На основании литературных данных [13] и проведенных экспериментов мы установили, что этот температурно-временной интервал находится в диапазоне 0.7‒0.9 от температуры плавления интерметаллида. При дальнейшем снижении температуры образуется твердообразная масса, не обладающая способностью к макроскопическому течению, вязкость резко снижается и материал затвердевает. При приложении внешних нагрузок происходит его разрушение. Для каждого металлокерамического и керамического материала существует свой температурно-временной интервал, в котором он обладает способностью к сдвиговому деформированию. Для определения этого интервала была разработана специальная методика [14].
ЗАКЛЮЧЕНИЕ
Впервые предложен новый экспериментальный и технологический метод – СВС-штамповка, основанный на использовании реологического эффекта тиксотропии. Представлены экспериментальные результаты применения этого метода для получения крупногабаритных пластин из материалов на основе МАХ-фазы системы Ti3AlC2.
На примере материала на основе МАХ-фазы Ti3AlC2 представлена эволюция структуры продуктов синтеза в ходе химического превращения в условиях высокотемпературного сдвигового деформирования.
Полученные экспериментальные результаты подтверждают способность металлокерамических композитов к формованию и получению компактных изделий с заданными структурой и габаритными размерами.
Список литературы
Kapranos P. // Metals. 2019. V. 9. № 12. № 1301. https://doi.org/10.3390/met9121301
Борисов В.Г. // Технология легких сплавов. 2016. № 2. С. 71‒79.
Аксененко А.Ю., Бычков С.А., Климов В.Н., Коробо-ва Н.В., Тарасов Ф.Е., Фризен В.Э., Шевченко С.Ю. // Металлургия машиностроения. 2013. № 2. С. 17‒20.
Decker R., LeBeau S., Wilson B., Reagan J., Mosko- vich N., Bronfin B. // Solid State Phenom. 2016. V. 256. P. 3–8. https://doi.org/10.4028/www.scientific.net/SSP.256.3
Semenov A.B., Ngo T.B., Semenov B.I. // Solid State Phenom. 2019. V. 285. P. 446–452. https://doi.org/10.4028/www.scientific.net/SSP.285.446
Бажин П.М., Столин А.М. Современные направления практического использования высокотемпературного сдвигового деформирования порошковых материалов в технологии СВС / Алдошин С.М., Алымов М.И. (ред.) Технологическое горение. М.: Российская академия наук, 2018 г. С. 372‒394.
Li D.Q., Zhang F., Midson S.P., Liang X.K., Yao H. // Solid State Phenom. 2019. V. 285. P. 417–422. https://doi.org/10.4028/www.scientific.net/SSP.285.417
Толочко Н.К., Шиенок Ю.А., Мяльдун А.З., Мозжаров С.Е. // Литье и металлургия. 2003. № 2. С. 39‒46.
Бучацкий Л.М., Столин А.М. // Инженерно-физический журнал. 1992. Т. 63. № 5. С. 593‒611.
Чижиков А.П., Столин А.М., Бажин П.М., Алы-мов М.И. // ДАН. 2019. Т. 484. № 6. С. 709‒711. https://doi.org/10.31857/S0869-56524846709-711
Pazniak A., Bazhin P., Shchetininc I., Kolesnikov E., Prokopets A., Shplis N., Stolin A., Kuznetsov D. // Ceram. Int. 2019. V. 45. № 2. P. 2020‒2027. https://doi.org/10.1016/j.ceramint.2018.10.101
Бажин П.М., Столин А.М. // ДАН. 2011. Т. 439. № 5. С. 630‒632.
Шарапова В.А., Филиппов М.А. (ред.) Композиционные материалы специального назначения: учебное пособие. Екатеринбург: Изд-во Урал. ун-та, 2020. 147 с.
Столин А.М., Бажин П.М., Алымов М.И. // Неорганические материалы. 2016. Т. 52. № 6. С. 672–678. https://doi.org/10.7868/S0002337X16060166
Дополнительные материалы отсутствуют.
Инструменты
Доклады Российской академии наук. Химия, науки о материалах