Журнал физической химии, 2020, T. 94, № 7, стр. 1105-1113
Адсорбенты СО2, нанесенные на карбид кремния
И. С. Портякова a, А. В. Антипов b, И. В. Мишин a, *, Л. М. Кустов a, c, **
a Российская академия наук, Институт органической химии им. Н.Д. Зелинского
119991 Москва, Россия
b ООО “ИнХимСинтез”
119991 Москва, Россия
c Московский государственный университет им. М.В. Ломоносова, Химический факультет
119992 Москва, Россия
* E-mail: igo@ioc.ac.ru
** E-mail: lmk@ioc.ac.ru
Поступила в редакцию 20.07.2019
После доработки 20.07.2019
Принята к публикации 03.09.2019
Аннотация
Синтезированы нанесенные на карбид кремния адсорбенты для поглощения СО2 (Li2ZrO3, Li4SiO4, CaSiO3, MgO, Li2O). Адсорбенты эффективны в области средних (300–400°С) или высоких (450–750°С) температур, обладают большой динамической адсорбционной емкостью по СО2 и повышенной скоростью адсорбции.
В связи с угрозой глобального потепления особую актуальность приобретает проблема улавливания углекислого газа из промышленных газообразных выбросов. В настоящее время наиболее перспективными методами очистки газовых потоков от СО2 в промышленности считаются адсорбция твердыми адсорбентами [1–13] или поглощение диоксида углерода жидкими растворами аминов [14–16]. Поскольку отходящие газы обычно нагреты, в качестве адсорбентов используют системы, такие как цирконаты, силикаты и оксиды Са, Mg, Li, способные адсорбировать СО2 в области средних (–400°С) или высоких (450–750°С) температур.
Однако степень поглощения и скорость поглощения СО2 массивными адсорбентами невелика, а их регенерация сопряжена с высокими затратами. Поэтому представляет интерес приготовление адсорбентов путем нанесения сорбирующего материала Li2ZrO3, Li4SiO4, CaSiO3, MgO и Li2O на различные носители. Это позволяет сформировать на поверхности носителя тонкий слой мелкодисперсного равномерно распределенного адсорбента, благодаря чему можно добиться увеличения удельной поверхности и, следовательно, адсорбционной емкости по СО2 и снизить содержание сорбирующего материала.
Ранее [17] нами были получены эффективные нанесенные адсорбенты на карбид кремния, который практически не взаимодействует с адсорбционным слоем при температурах до 600–800°С. Карбид кремния не имеет поверхностных функциональных групп типа гидроксильных или льюисовских центров, что создает предпосылки к формированию на поверхности карбидов высокоэффективных в адсорбции фаз стабильных цирконатов или силикатов лития и кальция, а также окислов магния и лития.
Целью данной работы было изучение структурных и адсорбционных свойств керамических адсорбентов, нанесенных на карбид кремния, который отличается высокой термической и механической стабильностью.
ЭКСПЕРИМЕНТАЛЬНАЯ ЧАСТЬ
Использованные реактивы. В качестве исходных носителей для получения сорбентов СО2 для высоких рабочих температур использовали:
1. Карбид кремния (SiC) марки F120 и F180 производства “Лит.Пром.Абразив” (Украина) с размером частиц 10–60 мкм, содержание SiC не менее 97%.
2. Пенокерамический материал из карбида кремния (ПК МКК), производства фирмы “Русский катализатор” (Россия) был изготовлен из ретикулированного пенополиуретана пористостью 10–20 ppi. Образующийся пенокерамический материал содержит более 95% SiC и имеет темно-серый цвет, плотность 0.3–0.5 г/см3 и пористость 80–90%. ПКМКК измельчали и для приготовления сорбентов СО2 использовали гранулы носителя (фракцию 0.25–0.5 мм).
3. Наноразмерный карбид кремния (ООО “ИнХимСинтез”, нано-SiC 10–120 нм, площадь поверхности 59.3 м2/г) получен вакуумной термообработкой высокодисперсного состава “C + + SiO2” с использованием силикагеля, приготовленного золь-гель-методом. Исходными веществами для получения геля-полупродукта служили водорастворимые органические вещества и эфиры кремниевой кислоты.
6. Газы СО2 квалификации по ГОСТ 8050-85 и N2 по ГОСТ 9293-74.
7. Активную фазу, наносимую на носители, синтезировали из нитратов, ацетатов и гидроксидов Li, Zr, Mg, Ca и SiO2 (Aerosil), а также использовали карбонаты К и Nа фирмы “Acros organics”.
Кислотное травление поверхности карбида кремния. Образцы исходных карбидных носителей помещали в раствор, содержащий дистиллированную воду, этиловый спирт и 40% плавиковую кислоту в соотношении 5 : 1 : 1, и перемешивали в течение 1 ч при комнатной температуре. Далее протравленные кислотой образцы фильтровали, промывали дистиллированной водой до рН 7.0 и сушили 2 ч при 110°С. Такая процедура позволяет удалить с поверхности карбида кремния тонкую пленку оксида кремния, которая образуется при высокотемпературном (1900–2000°С) синтезе карбида кремния в атмосфере воздуха. Для приготовления адсорбентов СО2 использовали протравленные кислотой образцы карбидов кремния.
Нанесение сорбирующих агентов. Сорбирующие агенты Li2ZrO3 и Li4SiO4 осаждали на носители по аналогии с традиционными методиками, в частности, цитратным методом [18], цитратным золь-гель-методом [19].
а) Синтез нанесенного 30%Li2ZrO3/SiC. В раствор Zr(NO3)4, приготовленный взаимодействием ZrO(NO3)2 · H2O и стехиометрического количества 65%-ной азотной кислоты, при интенсивном перемешивании и 20°С загрузили карбид кремния и добавили по каплям раствор LiNO3 из расчета Zr : Li = 1 : (0.8–2), нагрели до 80°С и упарили смесь наполовину. Далее при интенсивном перемешивании в реакционную смесь малыми порциями внесли безводную лимонную кислоту из расчета Zr : C6H8О7 = 1 : (2–3) и упарили до сухого твердого остатка горчичного цвета. После сушки предшественника адсорбента при 110°С 3 ч и прокаливания 6 ч при 650° был получен адсорбент Li2ZrO3/SiC белого цвета.
б) Синтез нанесенного 30%Li4SiO4/SiC. Для приготовления цитратного комплекса лития (мольное отношение C6H8O7 : Li = 1.4–3.0) навеску LiOH · H2O растворили в воде и добавили безводную лимонную кислоту (C6H8O7). В полученный раствор внесли носитель – SiC и перемешивали 1 ч при 20°С. Затем в реактор прилили стехиометрическое количество раствора Аэросила-380 в воде (содержание SiO2 в воде 20 мас. %) и при интенсивном перемешивании нагрели полученную суспензию до 80°С. Реакционную смесь упарили до сухого остатка горчичного цвета. После сушки предшественника при 110°С 3 ч и прокаливания 4 ч при 650 или 850°С был получен адсорбент Li4SiO4/SiC белого цвета.
Аналогичным образом из СаО и SiO2 получали адсорбент 30%CaSiO3/SiC.
в) Синтез нанесенных металлоксидных сорбентов на основе MgO или Li2O цитратным способом. К суспензии носителя – SiC, прилили раствор нитрата Li (Mg) и перемешивали при нагревании от 20 до 80°С, упаривали реакционную смесь наполовину. Далее при интенсивном перемешивании в течение 20 мин в реакционную смесь маленькими порциями вносили безводную лимонную кислоту и упаривали содержимое до сухого остатка горчичного цвета. После сушки предшественника при 110°С 3 ч и прокаливании 5 ч при 400 или 650°С был получен адсорбент MgO (или Li2O)/SiC.
Допирование полученных адсорбентов. Адсорбенты допировали двумя способами:
- допирование карбонатами калия или натрия (20% от массы адсорбирующего материала) проводили в процессе синтеза совместно с нанесением прекурсоров на носитель, сушили и прокаливали при соответствующих температурах,
- готовый прокаленный адсорбент пропитывали раствором карбоната калия или натрия (20% от массы адсорбирующего материала), влажную массу встряхивали 1 ч на вибраторе ВП 30 с частотой 1500 колебаний/мин, сушили при 110°С 2 ч и повторно прокаливали при 400°С 4 ч.
МЕТОДЫ ИССЛЕДОВАНИЙ
Сканирующая электронная микроскопия. Морфологию образцов изучали методом электронной микроскопии (FE-SEM) на электронном микроскопе Hitachi SU8000. Съемку изображений вели в режиме регистрации вторичных электронов при ускоряющем напряжении 2 кВ и рабочем расстоянии 4–5 мм. Образцы исследовались с учетом поправки на поверхностные эффекты напыления проводящего слоя. При изучении образцов методом рентгеновского микроанализа (EDS-SEM) использовали энергодисперсионный рентгеновский спектрометр Oxford Instruments X-max 80 при ускоряющем напряжении 10 кВ и рабочем расстоянии 15 мм [20].
Рентгенофазовый анализ. Рентгенофазовый анализ проводили на дифрактометре ДРОН-2 в следующем режиме: CuKa-излучение (30 кВ, 30 мА), Ni-фильтр, сканирование в области 10–60° (2θ) со скоростью 1 град(2θ)/мин.
ИК-спектроскопия. ИК-спектры образцов нанесенных адсорбентов измеряли на ИК-фурье-спектрометре Nicolet iS50 с приставкой НПВО (кристалл–алмаз). Условия измерения спектров − разрешение 4 см–1, число сканирований 128.
Измерение адсорбционной емкости полученных адсорбентов по СО2. Экспериментальное измерение адсорбционной емкости адсорбентов включало следующие этапы:
− прокаливание образцов сорбентов в муфельной печи в атмосфере воздуха при соответствующих температурах,
− декарбоксилирование образцов адсорбентов при температурах, близких к температурам разложения их карбонатов в проточном кварцевом реакторе с внутренним диаметром 7 мм. Реактор помещали в печь с электрообогревом и нагревали адсорбент 2 часа в токе азота (40 мл/мин.),
− через образец адсорбента, нагретого до соответствующей температуры, в течение 1 ч со скоростью 40 мл/мин. пропускали СО2.
Адсорбционную емкость образцов в пересчете на массу адсорбирующего материала определяли по разнице веса реактора с загруженным образцом адсорбента до и после пропускания СО2.
ОБСУЖДЕНИЕ РЕЗУЛЬТАТОВ
Принцип действия и морфологические особенности нанесенных адсорбентов
В основе процесса поглощения углекислого газа адсорбентами лежат обратимые реакции образования карбонатов соответствующих металлов, которые обычно протекают в тонком слое адсорбента, нанесенного на носитель, по следующим схемам:
(1)
${\text{L}}{{{\text{i}}}_{{\text{2}}}}{\text{Zr}}{{{\text{O}}}_{3}} + {\text{C}}{{{\text{O}}}_{2}} \leftrightarrow {\text{L}}{{{\text{i}}}_{{\text{2}}}}{\text{C}}{{{\text{O}}}_{{\text{3}}}} + {\text{Zr}}{{{\text{O}}}_{2}},$(2)
${\text{L}}{{{\text{i}}}_{{\text{4}}}}{\text{Si}}{{{\text{O}}}_{4}} + {\text{C}}{{{\text{O}}}_{{\text{2}}}} \leftrightarrow {\text{L}}{{{\text{i}}}_{{\text{2}}}}{\text{C}}{{{\text{O}}}_{3}} + {\text{L}}{{{\text{i}}}_{{\text{2}}}}{\text{Si}}{{{\text{O}}}_{3}},$(3)
${\text{CaSi}}{{{\text{O}}}_{3}} + {\text{C}}{{{\text{O}}}_{2}} \leftrightarrow {\text{CaC}}{{{\text{O}}}_{3}} + {\text{Si}}{{{\text{O}}}_{2}},$(5)
${\text{L}}{{{\text{i}}}_{{\text{2}}}}{\text{O}} + {\text{C}}{{{\text{O}}}_{2}} \leftrightarrow {\text{L}}{{{\text{i}}}_{{\text{2}}}}{\text{C}}{{{\text{O}}}_{3}}.$Несмотря на близость этих схем, степень поглощения оксида углерода зависит от доступности катионов металла в процессе сорбции, которая определяется не только реакционной способностью катионов, но и особенностями диффузии на поверхности адсорбента. Поглощение углекислого газа адсорбирующим материалом происходит благодаря диффузии ионов металла на поверхность частицы, где при высоких температурах образуется твердый непроницаемый слой карбоната металла, диффузия СО2 в массу частицы становится затруднительной, и реакция характеризуется чрезвычайно медленной кинетикой поглощения. В результате значительная часть адсорбента в ядре частицы не вовлекается в процесс адсорбции.
На рис. 1 приведены изображения карбида кремния и адсорбента 30% Li2ZrO3/SiC, зарегистрированные на электронном микроскопе. Видно, что карбид кремния образован игольчатыми кристаллами различной длины с преобладающей толщиной игл 0.1–0.2 мкм, а нанесенный адсорбент 30%Li2ZrO3/SiС представлен частицами цирконата лития со средним размером 0.05–0.1 мкм.
Рис. 1.
Изображения микроструктуры образцов а) SiС-F180, б) 30%Li2ZrO3/SiС-F180, полученные на электронном микроскопе.
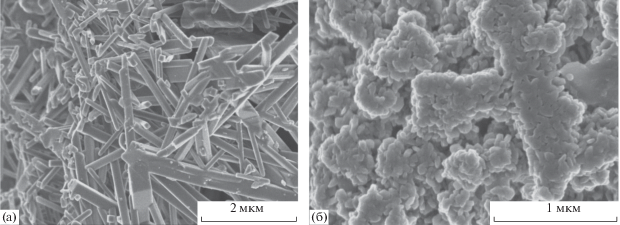
Полученные адсорбенты представляют собой гранулы, построенные по типу ядро-оболочка, где ядром являются нано- и микроразмерные частицы карбидов металлов, а оболочкой − активная фаза поглотителя СО2, равномерно распределенная по поверхности носителя.
ФАЗОВЫЙ СОСТАВ НАНЕСЕННЫХ АДСОРБЕНТОВ
Адсорбционный слой, закрепленный на носителе, при комнатной температуре находится в рентгеноаморфном состоянии. Однако перед адсорбционными измерениями образцы адсорбентов проходят высокотемпературную обработку. Поэтому данные рентгенографического анализа образцов, предварительно прогретых при высоких температурах, могут указать на особенности формирования и фазовый состав нанесенных систем, участвующих в процессе адсорбции. Соответствующие данные приведены на рис. 2 и в табл. 1.
Рис. 2.
Рентгенограммы адсорбентов: CaSiO3/SiC (1), Li2ZrO3/SiC (2), Li4SiO4/SiC (3), Li2O/SiC (4) и MgO/SiC (5).
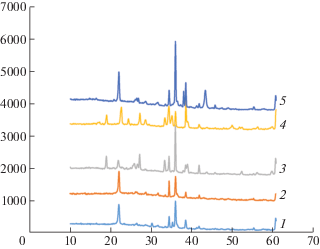
Таблица 1.
Состав адсорбционного слоя, нанесенного в количестве 30 мас. % на карбид кремния
Состав адсорбентов | Т, °С | Состав |
---|---|---|
CaSiO3/SiC | 650 820 |
Волластонит (CaSiO3) |
Li2ZrO3/SiC | 650 820 |
Следы ZrO2 |
Li4SiO4/SiC | 820 | Li2SiO3 |
Li2O/SiC | 820 | Li4SiO4, Li2SiO3 |
MgO/SiC | 650 | MgO, |
На рентгенограмме образца 30% CaSiO3/SiC, прогретого при 650°С, наблюдаются интенсивные дифракционные максимумы при 2Θ = 34.06, 35.63 и 38.16°, характерные для карбида кремния. Дифрактограмма содержит также отражения при 25.35, 26.90 и 29.96°, указывающие на присутствие волластонита (триклинной модификации CaSiO3). Прогревание системы при 820°С не влияет на положение и интенсивность дифракционных максимумов, что указывает на стабильность адсорбционной фазы. Максимум при 21.76° вместе с небольшим пиком при 36.4° можно отнести к кристобалиту, кубической модификации SiO2. Присутствие кристобалита можно объяснить разрушением небольшой части карбида кремния или CaSiO3. Таким образом, адсорбционная фаза этого образца представляет собой кристаллический силикат кальция.
На дифрактограмме образца 30% Li2ZrO3/SiC, прогретого при 650°С, видны максимумы, связанные с присутствием носителя, и несколько слабых отражений, которые можно отнести к нестехиометрическим оксидам циркония. Можно предположить, что активная фаза в этом образце представлена рентгеноаморфным цирконатом лития. Прогревание системы при 820°С не изменяет дифракционную картину.
Дифрактограмма образца 30% Li4SiO4/SiC, прогретого при 820°С, содержит отражения, характерные для карбида кремния, а также максимумы при 2Θ = 18.84, 26.92, 33.00 и 38.6°, указывающие на присутствие ромбической модификации Li2SiO3. В небольших количествах присутствует также кристобалит (21.73°). Очевидно, активная адсорбционная фаза этой системы ассоциирована с кристаллическим силикатом лития.
В образце 30% Li2O/SiC после прокаливания при 820°С появляются отражения, соответствующие присутствию двух фаз силиката лития. Ромбическую фазу Li2SiO3 можно идентифицировать по отражениям при 2Θ = 18.91, 27.00, 33.05 и 38.52°, а моноклинную модификацию Li4SiO4 – по отражениям при 22.47, 24.20, 34.78 и 49.38°(2Θ). Очевидно, кристаллические фазы силиката лития являются активными компонентами адсорбционной системы.
На рентгенограмме образца MgO/SiC, прогретого при 670°С, наблюдаются максимумы, связанные с присутствием носителя SiC, и двух фаз оксида кремния – кристобалита (21.91°) и кварца (26.61°), а также кубической модификации оксида магния (42.86° 2Θ). Можно предположить, что при высокотемпературной обработке часть носителя разрушается, но оксиды кремния не взаимодействуют с оксидом магния и образуют самостоятельные фазы. Оксиды кремния являются в данной системе балластными компонентами, а активность в сорбции проявляет оксид магния.
СОРБЦИОННЫЕ СВОЙСТВА АДСОРБЕНТОВ
Система Li2ZrO3/SiC является одним из эффективных и перспективных адсорбирующих соединений, способным поглощать СО2 в температурном интервале (450–550°С) и выдерживать много циклов сорбции/десорбции СО2 [3, 4, 21–23]. Согласно рентгенографическим данным, цирконат лития скорее всего присутствует на поверхности носителя в виде рентгеноаморфных соединений, благодаря которым ионы лития обладают большой подвижностью. Поглощение углекислого газа цирконатом лития с образованием Li2СO3 происходит благодаря диффузии подвижных ионов лития на поверхность частицы, где при высоких температурах образуется твердый непроницаемый слой Li2СO3, диффузия СО2 в массу частицы становится затруднительной, и реакция характеризуется чрезвычайно медленной скоростью поглощения. В результате, значительная часть адсорбента не вовлекается в процесс адсорбции [1, 22–24]. Аналогичное явление характерно для всех применяемых массивных сорбирующих материалов.
В табл. 2 собраны данные по адсорбции СО2 цирконатом лития, нанесенным на карбид кремния. Полученные нами адсорбенты 30% Li2ZrO3/SiC демонстрирует сорбционную активность на уровне лучших известных из литературы образцов сорбентов – 23.5–27.0%. Так, при теоретической емкости 28 мас. % наблюдаемое поглощение составляет, как правило, 11–13% при 500–700°С за 1 ч [1]. Лучший результат достигает 27% для нанодиспергированного образца Li2ZrO3/SiC [3, 24, 25]. В настоящей работе высокую эффективность поглощения СО2 цирконатом лития можно объяснить тем, что адсорбирующий материал равномерно распределен на большой поверхности носителя и в высокотемпературных условиях не поддается значительному спеканию.
Таблица 2.
Сорбционные свойства цирконата лития, нанесенного на носители (прокаливание – 650°С, 6 ч, десорбция СО2 – 550°С, 2 ч)
Адсорбент | Тсорбц, °С | ${{\tau }_{{{\text{С}}{{{\text{О}}}_{{\text{2}}}}}}}$, ч | ${{Е}_{{{\text{С}}{{{\text{О}}}_{{\text{2}}}}}}}$, % |
---|---|---|---|
30%Li2ZrO3/SiC F120 | 550 | 1 | 23.5 |
400 | 0.5 | 7.2 | |
400 | 1 | 9.4 | |
400 | 1.5 | 12.4 | |
30% Li2ZrO3/SiC- наноразмерный | 550 | 1 | 24.6 |
400 | 1 | 9.2 | |
30%Li2ZrO3/SiC- пористый | 550 | 1 | 24.6 |
550 | 1 | 26.1* | |
550 | 1 | 27.0** | |
550 | 0.5 | 11.6 | |
400 | 0.5 | 7.8 | |
300 | 0.5 | 5.4 |
Для уменьшения экранирующего влияния непроницаемого слоя карбоната лития на процесс адсорбции предложено вводить в адсорбенты легирующие добавки окислов или карбонатов металлов [2, 4, 26–31]. Литературные данные указывают на значительное увеличение сорбции СО2 при допировании цирконата лития, например, карбонатами калия, натрия, иттрия, но механизм допирующего действия остается до конца невыясненным. Предполагается, что в процессе сорбции при температуре 500°С Li2СO3 и K2СО3 образуют эвтектическую смесь (расплав солей), которая облегчает диффузию СО2 к глубинным слоям сорбента [1, 23, 30]. Кроме того, если сорбция СО2 осуществляется в присутствии водяного пара, то из карбоната натрия может образовываться бикарбонат натрия, который поглощает в 2 раза больше СО2 по сравнению с Na2CO3 [2]. Но и в этом случае в адсорбции СО2 участвует только поверхность частицы сорбента, а внутренние слои адсорбционной фазы остаются недоступными для реагентов.
Li4SiO4 – эффективный высокотемпературный адсорбент, работающий в интервале температур 450–700°С, но высокая температура, необходимая для его регенерации (>800°С), способствует спеканию адсорбирующего материала в наружном слое. Теоретическая емкость (36.7 мас. %) и наблюдаемая способность к поглощению СО2 этого сорбента (27–28 мас. % [1]) достаточно велики. Работы по улучшению сорбционного поведения силиката лития направлены на синтез нанодисперсных частиц Li4SiO4 [7, 8, 32–35], а также легированию адсорбента натрием, калием, алюминием и железом [36, 37]. Нам удалось приблизить поглотительную эффективность сорбента 30% Li4SiO4/SiC к лучшим нанодисперсным образцам (23.5–26.7 мас. %), известным из литературы.
В табл. 3 приведены данные, позволяющие проследить, как температура прокаливания и условия десорбции влияют на эффективность адсорбции СО2. Повышение температуры десорбции от 550 до 750°С увеличивает сорбционную емкость благодаря более полному освобождению адсорбционных центров. Температура прокаливания 675°С оказалась достаточной для формирования оптимальной морфологии поверхности.
Таблица 3.
Сорбционные свойства силиката лития, нанесенного на карбид кремния (время прокаливания – 6 ч, время десорбции СО2 – 2 ч, сорбция СО2 – 550°С, 1 ч)
Адсорбент | Т, °С | Тдесорбц, °С | ${{Е}_{{{\text{С}}{{{\text{О}}}_{{\text{2}}}}}}}$, % |
---|---|---|---|
30%Li4SiO4/SiC-пористый | 675 | 550 | 23.2 |
26.6* | |||
850 | 550 | 20.4 | |
21.6* | |||
850 | 750 | 28.4 | |
30%Li4SiO4/SiC-наноразмерный | 21.8 | ||
675 | 550 | 24.5* | |
26.7** |
Не очень высокая сорбционная емкость CaSiO3 (табл. 4) значительно возрастает при увеличении температуры прокаливания. Известно, что полное разложение СаСО3 возможно только при температурах около 1000°С и, очевидно, использование более низких температур десорбции (800°С) недостаточно для полного разложения карбоната кальция. Согласно данным, приведенным в табл. 4, сорбционная емкость образцов 30%CaSiO3/SiC, регенерируемых при 850°С, падает от 22.9 до 13.3% к пятому циклу. Аналогичная зависимость, связанная со снижением сорбционной емкости при увеличении числа циклов при проведении сорбции из потока газа, состоящего из 15% СО2 и 85% N2, описана в литературе [38]. К достоинствам силиката кальция можно отнести небольшую стоимость и высокую эффективность сорбции при температурах от 400 до 800°С. Потеря поглотительной способности, вероятно, связана с процессами спекания и не полным разложением карбоната кальция.
Таблица 4.
Сорбционные свойства силиката кальция, нанесенного на карбид кремния (время прокаливания – 6 ч, время десорбции СО2 – 2 ч, сорбция СО2 – 400°С, 1 ч)
Адсорбент | Т, °С | Тдесорбц, °С | ${{Е}_{{{\text{С}}{{{\text{О}}}_{{\text{2}}}}}}}$, % |
---|---|---|---|
30%CaSiO3/SiC-пористый | 700 850 900 |
550 | 12.4 15.5 17.3 |
850 | 850 | 22.9 – первый цикл, 20.9 – второй 18.7 – третий 16.2 – четвертый 13.3 – пятый |
|
24.8* 26.4** |
Данные табл. 5 показывают, что Li2O/SiC, прокаленный при 820°С, имеет высокую емкость адсорбции СО2 (65–66%). На его поверхности наблюдается образование двух модификаций силиката лития Li4SiO4 и Li2SiO3, которые сами являются хорошими адсорбентами.
Таблица 5.
Сорбционные свойства Li2O, нанесенного карбид кремния (время прокаливания – 5 ч, температура прокаливания — 820°С, время десорбции – 2 ч, время сорбции – 1 ч)
Адсорбент | Тдесорбц, °С | Тсорбц, °С | ${{Е}_{{{\text{С}}{{{\text{О}}}_{{\text{2}}}}}}}$, % |
---|---|---|---|
30%Li2O/SiC-наноразмерный | 40.8 | ||
400 | 400 | 49.4* | |
53.6** | |||
720 | 720 | 65.8 | |
0%Li2O/SiC-пористый | 550 | 400 (0.5 ч) | 28.6 |
550 | 400 | 39.8 | |
650 | 650 | 40.2 | |
66.1* | |||
720 | 720 | 69.4* | |
73.3** | |||
20%Li2O/SiC-пористый | 650 | 650 | 39.4 |
10%Li2O/SiC-пористый | 650 | 650 | 41.1 |
Температура сорбции 720°С обеспечивает максимальную степень поглощения углекислого газа. Это согласуется с данными термогравиметрического исследования поглощения СО2 массивным коммерческим оксидом лития [39], которое показало, что в интервале температур 190–400°С поглощение СО2 массивными частицами Li2O составляет около 14 мас. %, а начиная с 600°С оно резко возрастает до 109 мас.% за 2 ч. Скачок адсорбционного поглощения СО2 объясняется мощным ускорением при 530–700°С миграции лития на поверхность частицы с образованием карбоната лития. Поверхностный слой значительно разрыхляется и образует глубокие трещины на поверхности частицы, меняя ее морфологию, благодаря чему также увеличиваются возможности для физической сорбции СО2 и его доступа к более глубоким слоям частицы.
Допирование K2СО3 и парами воды существенно повышает сорбционные мощности оксида лития (табл. 5).
В табл. 6 представлены данные, полученные при адсорбции СО2 на MgO, нанесенном на пористый и наноразмерный образцы карбида кремния. Адсорбция CO2 проведенная при 150 и 400°С, показала, что этот адсорбент поглощает СО2, в количествах до 65 мас. %. Согласно рентгенографическим данным, на поверхности карбида кремния, прокаленного при 650°С, присутствуют тонко диспергированные оксиды магния с размером кристаллитов около 150 Å.
Таблица 6.
Сорбционные свойства MgO, нанесенного на SiC (время прокаливания – 5 ч, время десорбции – 2 ч, время сорбции – 1 ч)
Адсорбент | Т, °С | Тдесорбц, °С | Тсорбц, °С | ${{Е}_{{{\text{С}}{{{\text{О}}}_{{\text{2}}}}}}}$, % |
---|---|---|---|---|
0%MgO/SiC-пористый | 670 | 700 | 150 | 57.9* |
670 | 650 | 150 | 36.1 | |
670 | 400 | 400 | 65.8 | |
30%MgO/SiC-F120 | ||||
650 | 400 | 400 | 48.9* | |
51.4** | ||||
400 | 400 | 400 | 29.8 | |
30%MgO/SiC-наноразмерный | 670 | 400 | 400 | 65.8 – 1-й цикл ……… 60.5 – 6-й цикл |
Образцы 30%MgO/SiC показали высокую сорбционную емкость (до ∼66%) и стабильность, поскольку при циклическом использовании образца снижение сорбционной емкости к 5–6 циклу составило около 5% (табл. 6.). Допирование MgO/SiC карбонатом калия и парами воды повышает его сорбционную способность.
Наиболее близкий к нашим исследованиям вариант — нанесенный адсорбент 31.7 и 33.8% MgO/Al2O3 [40] имеет крайне низкую сорбционную емкость (0.5 ммоль СО2/г Al2O3), а массивный коммерческий пористый MgO [12] с размером частиц <44 мкм при 300°С и давлении СО2 20–40 бар в присутствии паров воды прореагировал до MgСO3 на 70–80%. Авторы [12, 41] считают, что регулированием парциального давления воды можно даже контролировать процесс карбонизации MgO. В отсутствие водяного пара [40] образуется структура MgO · 2MgСO3, снижающая поглощение СО2, но при >350°С в присутствии паров воды она разлагается до MgO.
Поверхностные свойства MgO (площадь поверхности, пористость) также играют важную роль в процессе адсорбции СО2. Так, мезопористый MgO, полученный гидротермальным синтезом [42] с использованием мочевины и NaNO3/NaNO2 в качестве промотора, имел адсорбционную емкость по СО2 60–88 мас. % при 325°С. Его удельная поверхность составляла 180–230 м2/г, объем пор 0.39–0.49 см3/г и размер мезопор 5–7 нм. Эффективное поглощение таким адсорбентом достигается, очевидно, за счет развития системы мезопор в текстуре оксида магния, тогда как в наших нанесенных адсорбентах высокая емкость по СО2 (до ≈66 мас. %) получена благодаря тонкослойному распределению микроразмерного MgO на поверхности карбида кремния.
Представленные в табл. 1–6 результаты свидетельствуют о получении нового класса эффективных нанесенных на карбид кремния высокотемпературных адсорбентов СО2. Высокая адсорбционная емкость образцов является косвенным подтверждением формирования на поверхности носителей высокоэффективных в хемосорбции СО2 фаз сорбирующих материалов.
Формирование карбонатов при адсорбции СО2 подтверждается ИК-спектроскопическими наблюдениями за процессом адсорбции СО2.
Важным вопросом практического использования адсорбентов является их способность выдерживать несколько циклов адсорбции, чередующейся с регенерацией. В ИК-спектре образца 30% Li2ZrO3 (рис. 3, кривая 1) наблюдаются интенсивные полосы поглощения при 1493 и 1434 см–1, характерные для карбонат-иона. Интенсивности этих полос поглощения существенно уменьшаются после обработки в токе азота при 650°С в течение 0.5 ч (кривая 2). Это свидетельствует о быстрой частичной регенерации адсорбента уже при 650°С, температуре, которая всего на 100°С выше температуры адсорбции СО2. Если дополнительно выдержать образец в токе азота при 700°С в течение еще 0.5 ч, то эти полосы поглощения исчезают из спектра. Повторная адсорбция СО2 приводит к практически полному воспроизведению результатов.
Рис. 3.
ИК-спектры образца 30%Li2ZrO3/SiC адсорбента: после адсорбции СО2 при 550°С в течение 1 ч (1); после регенерации в токе азота при 650°С в течение 0.5 ч (2).
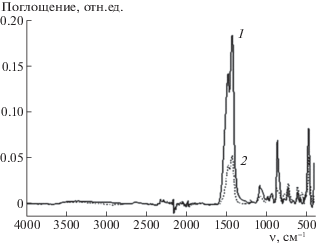
Таким образом, впервые синтезированы адсорбенты СО2 (Li2ZrO3, Li4SiO4, CaSiO3, MgO, Li2O), нанесенные на карбид кремния (нано-, микроразмерный и гранулированный пористый). Адсорбенты обладают высокой динамической адсорбционной емкостью по СО2, повышенной скоростью адсорбции. Адсорбенты представляют собой гранулы, построенные по типу ядро-оболочка, где ядром являются частицы карбида кремния, а оболочкой микроразмерная активная фаза поглотителя СО2, равномерно распределенная по поверхности носителя.
Преимуществом полученных в настоящей работе нанесенных на карбид кремния высоко- (450–750°С) и среднетемпературных (300–400°С) адсорбентов, по сравнению с традиционными массивными цирконатами и силикатами лития и кальция, а также оксидами лития и магния, является экономическая целесообразность и возможность их полной регенерации в токе инертного газа при температурах, превышающих температуру адсорбции на 100–150°С.
Список литературы
Kumar S., Saxena S.K. // Mater. Renew. Sustain. Energy. 2014. V. 3. P. 30. https://doi.org/10.1007/s40243-014-0030-9
Ramírez-Moreno M.J., Romero-Ibarra I.C., Ortiz-Landeros J., Pfeiffer H. // Alkaline and Alkaline-Earth Ceramic Oxides for CO2 Capture, Separation and Subsequent Catalytic Chemical Conversion. Additional information is available at the end of the chapter 14. https://doi.org/10.5772/574446
Ochoa-Fernández E., Ronning M., Grande T., Chen D. // Chem. Mater. 2006. V. 18 (6). P. 1383. https://doi.org/10.1021/cm052075d
Xiao Q., Tang X., Liu Y. et al. // Front. Chem. Sci. Eng. 2013. V. 7 (3). P. 297. https://doi.org/10.1007/s11705-013-1346-1
Radfarnia H.R. // High-Temperature CO2 Sorbents and Application in the Sorption Enhanced Steam Reforming for Hydrogen Production. Universite LAVAL, Quebec, Canada, 2013. P. 70.
Yi K.B., Eriksen D.O. // Separ. Sci.Technol., 2006. V. 41. № 2. P. 283.https://doi.org/10.1080/01496390500496884
Xiao Q, Liu Y., Zhong Y., Zhu W. // J. Mater. Chem. 2011. V. 41. № 21. P. 3838–3842. https://doi.org/10.1039/C0JM03243C
Venegas M.J., Fregoso-Israel E., Eskamilla R., Pfeiffer H. // Ing. Eng. Chem. Res. 2007. V. 41. 46 (8). P. 2407–2412. https://doi.org/10.1021/ie061259e
Kato M., Nakagawa K., Essaki K. et al. // Int. J. Appl. Ceram. Technol. 2005. V. 2. P.467. https://doi.org/10.1111/j.1744-7402.2005.02047.x
Kishor B.K., Reshma Y.R., Vilash H.R., Abaji G.G. // Adsorption Sci.Technol. 2012. V. 30. № 10. P. 817.
Hassanzadeh A., Abbasian J. // Fuel. 2010. V. 89. P. 1287–1297. https://doi.org/10.1016/j.fuel.2009.11.017
Fagerlund J., Highfield J., Zevenhoven R. // RSC Adv. 2012. V. 2. P. 10380–10393. https://doi.org/10.1039/C2RA21428H
Duan Y., Sorescu D.C. // Phys. Rev. B. 2009. V. 79. № 1. 014301. https://doi.org/10.1103/PhysRevB.79.014301
Лавренченко Г.К., Копытин А.В., Пятничко А.И., Иванов Ю.В. // Технические газы. 2011. № 1. С. 31.
Xiao M., Liu H.,Gao H., Liang Z. // J. Chem. Thermodyn. 2018. V. 122. P. 170. https://doi.org/10.1016/j.jct.2018.03.020
Lang P., Denes F., Hegely L. // Chem. Eng. Transaction. 2017. V. 61. P. 1105. https://doi.org/10.3303/CET1761182
Игнатов А.В., Тарасов А.Л., Кустов Л.М., Портякова И.С. Способ получения высокотемпературных адсорбентов СО2, патент РФ № 2659256// Б.И. 2018. № 16.
Денисова Е.A., Бакланова Я.Б., Максимова Л.Г. Способ получения порошка цирконата лития, патент РФ № 2440298 // Б.И. 2012. № 2.
Xiao Q., Liu Y., Zhong Y., Zhu W. // J. Mater. Chem. 2011. V. 21. P. 3838. https://doi.org/10.1039/C0JM03243C
Качала В.В., Хемчян Л.Л., Кашин А.С. и др. // Успехи химии. 2013. Вып. 82. С. 648. https://doi.org/10.1070/RC2013v082n07ABEH004413
Nakagawa K., Ohashi T. // J. Electrochem. Soc. 1998. 145. V. 4. P. 1344. https://doi.org/10.1149/1.1838462
Nakagawa K., Ohashi T. // Electrochemistry. 1999. V. 67 (6). P. 618.
Ida J., Xiong R, Lin Y.S. // Sep. Purif. Technol. 2004. V. 36. P. 41–51. https://doi.org/10.1016/S1383-5866(03)00151-5
Nair B.N., Yamaguchi T., Kawamura H. et al. // J. Amer. Ceram. Soc. 2008. V. 87 (1). P. 68–74. https://doi.org/10.1111/j.1551-2916.2004.00068.x
Ochoa-Fernandes E., Ronning M., Grande T., Chen D. // Chem. Mater. 2006. V. 18. P. 6037. https://doi.org/10.1021/cm061515d
Xiao Q., Tang X., Liu Y. et al. // Chem. Eng. Journal. 2011. V. 174. № 1. P. 231.
Wang C., Dou B, Song Y. et al. // Ind. Eng. Chem. Res. 2014. V. 53 (32). P. 12744.https://doi.org/10.1021/ie502042p
Pannocchia G., Puccini M., Seggiani M., Vitolo S. // Ind. Eng. Chem. Res. 2007. V. 46 (21). P. 6696. https://doi.org/10.1021/ie0616949
Veliz-Enriquez M.Y., Gonzalez G., Pfeiffer H. // J. Solid. State Chem. 2007. V. 180 (9). P. 2485. https://doi.org/10.1016/j.jssc.2007.06.023
Ida, J., Lin, Y.S. // Environ. Sci. Technol. 2003. V. 37. № 9. P. 1999. https://doi.org/10.1021/es0259032
Khokhani M., Khomane R., Kulkarni B.D. // J. Sol-Gel Sci. Technol. 2012. V. 61 (2). P. 316. https://doi.org/10.1007/s10971-011-2629-y
Khomane R.B., Sharma B.K., Saha S., Kulkarni B.D. // Chem. Eng. Sci. 2006. V. 61. P. 3415–3418.
Wu X.,Wen Z., Xu X., Wang X., Lin J. // J. Nucl. Mater. 2009. V. 392. № 3. P. 471–475. https://doi.org/10.1016/j.jnucmat.2009.04.010
Venegas M.J., Fregoso-Israel E., Escamilla R., Pfeiffer H. // Ind. Eng. Chem. Res. 2007. V. 46. P. 2407–2412. https://doi.org/10.1021/ie061259e
Xu H., Cheng W., Jin X. et al. // Ind. Eng. Chem. Res. 2013. V. 52. P. 1886. https://doi.org/10.1021/ie301178p
Gauer C., Heschel W. // J. Mater. Sci. 2006. V. 41. P. 2405.
Korake P.V., Gaikwad A.G. // Front. Chem. Sci. Eng. 2011. V. 5. № 2. P. 215. https://doi.org/10.1007/s11705-010-1012-9
Wang M., Lee C.G. // Energy Convers. Manage. 2009. V. 50. № 3. P. 636.https://doi.org/10.1016/j.enconman.2008.10.006
Mosqueda H.A., Vazquez C., Bosch P., Pfeiffer H. // Chem. Mater. 2006. V. 18. № 9. P. 2307. https://doi.org/10.1021/cm060122b
Lee S.C., Choi B.Y., Lee T.J., Ryu C.K. // Catal. Today. 2006. V. 111 (3). P. 385–390. https://doi.org/10.1016/j.cattod.2005.10.051
Churakov S.V., Ianuzzi M., Parrinello M. // J. Phys. Chem. B. 2004. V. 108. P. 31. P. 11567. https://doi.org/10.1021/jp037935x
Zhao X., Ji G., Liu W. et al. // Chem. Eng. J. 2018. V. 332. P. 216. https://doi.org/10.1016/j.cej.2017.09.068
Дополнительные материалы отсутствуют.
Инструменты
Журнал физической химии