Журнал физической химии, 2021, T. 95, № 7, стр. 1068-1077
Газофазное окисление продуктов искрового плазменного спекания ковалентно сшитых углеродных нанотрубок
Е. В. Суслова a, *, В. В. Епишев a, С. В. Максимов a, К. И. Маслаков a, О. Я. Исайкина a, С. В. Савилов a
a Московский государственный университет имени М.В. Ломоносова,
Химический факультет
119991 Москва, Россия
* E-mail: suslova@kge.msu.ru
Поступила в редакцию 09.09.2020
После доработки 13.11.2020
Принята к публикации 17.11.2020
Аннотация
Ковалентно сшитые 3D-структуры углеродных нанотрубок (УНТ), а также УНТ с малослойными графеновыми фрагментами (МГФ) получены при гидролизе 3-аминопропилтриэтоксосилана в присутствии окисленных УНТ и/или МГФ. Полученные образцы консолидированы в нерассыпающиеся таблетки искровым плазменным спеканием при 1100°С и 30 МПа. При этом происходило элиминирование кислородсодержащих групп, а частицы МГФ превращались в смесь графеновых листов и луковичных углеродных наноструктур. Полученные консолидаты УНТ и смеси УНТ с МГФ имели плотности 0.85 и 0.81 г см–3, проводимость 42 и 57 См м–1 соответственно. Показано, что консолидированные образцы могут быть окислены парами азотной кислоты без нарушения их 3D-структуры. С увеличением времени окислительной обработки с 3 до 6 ч содержание кислорода возрастало с 8.4 до 15.3 ат. % для 3D-сшитых структур УНТ и с 14.0 до 16.1 ат. % для 3D-сшитых структур УНТ с МГФ.
Большое разнообразие свойств и структур углеродных наноматериалов (УНМ) открывает широкие возможности их применения в самых различных устройствах и приложениях. В настоящее время УНМ используют в качестве катализаторов, носителей катализаторов, адсорбентов, электродов устройств хранения и накопления энергии, сенсоров, лубрикантов и т.д. [1]. Для их применения часто требуется компактизация или гранулирование. Для этого к УНМ добавляют связующие агенты [2] или ковалентно “сшивают” отдельные частицы [3]. Консолидированные образцы УНМ без связующих могут быть получены методом искрового плазменного спекания (ИП-спекание) [4–22].
Консолидация методом искрового плазменного спекания описана для графита [4, 5], графена [6], малослойных графеновых фрагментов (МГФ) [7, 8], фуллеренов C60 [9, 10], одностенных углеродных нанотрубок (УНТ) [11], двустенных УНТ [12], многостенных УНТ [13, 14], окисленных УНТ [15], углеродных нановолокон [16], композита графита с углеродными волокнами [17]. В зависимости от условий ИП-спекания УНМ консолидируются с образованием жестких 3D-каркасов [13, 14, 18], либо происходит переход одной аллотропной модификации углерода в другую. Например, УНТ превращаются в графеновые листы при 2000–2400°С и 100 МПа [19, 20], в наноалмазы при 1500°С и 80 МПа [21], фуллерен С60 – в наноалмазы при 1150°С и 50 МПа [8], МГФ – в луковичные углеродные структуры (ЛУС) при 1100°С и 30 МПа [8]. В то же время наноалмазы превращаются в графит при 1200°C и 60 МПа [22].
Электропроводность ИП-спеченных УНТ, как правило, увеличивается [12, 23], а механические характеристики улучшаются [18, 24], что может быть связано с образованием новых C–C-связей между отдельными УНТ. Теоретические расчеты показали, что новые связи С–С могут образовываться при ИП-спекании, а гетероатомы в структуре УНТ способствуют этому [25]. Из прямой аналогии между процессами, происходящими при ИП-спекании, и воздействии облучения в колонне просвечивающего микроскопа, было сделано предположение, что две независимые УНТ объединяются за счет графеновых листов, формирующихся в процессе ИП-спекания [13, 19] и оплетающих трубки в общую структуру [13]. Однако позже было установлено, что эти процессы сильно зависят от условий ИП-спекания (T, P) и природы УНТ [15]. ИП-спекание ковалентно “сшитых” УНТ не описано в литературе. Однако такой подход может представлять интерес, так как является удобным методом получения компактизатов (монолитов) УНМ, в которых между отдельными частицами уже созданы ковалентные связи, что может способствовать улучшению проводимости [26, 27].
Часто для практического применения необходимо модифицировать поверхность УНМ кислородсодержащими группами, чтобы обеспечить ее гидрофильность [28]. Окисление УНМ осуществляют в растворах азотной кислоты, пероксида водорода или O3, либо же в газовой фазе парами азотной кислоты, CO2, обработкой в кислородной плазме [28–31]. Окисление в газовой фазе может рассматриваться как практически более удобный метод, так как в этом случае не требуется стадии фильтрации, промывания и высушивания продуктов.
Цель настоящей работы – получение нерассыпающихся консолидированных методом искрового плазменного спекания образцов ковалентно “сшитых” УНТ и углерод-углеродного композита УНТ и МГФ с последующей модификацией их поверхностей кислородсодержащими группами в газовой фазе и исследование их свойств.
ЭКСПЕРИМЕНТАЛЬНАЯ ЧАСТЬ
В работе использовали УНТ и МГФ производства ООО “Глобал СО” (Россия). УНТ с внешним диаметром ~10 нм состояли из 10–15 углеродных слоев (рис. 1а). Частицы МГФ, получение и физико-химические характеристики которых неоднократно описаны в [7, 32, 33], представляли собой графитоподобные частицы диаметром 50–100 нм, содержащие 10–15 графеновых слоев (рис. 1б).
Для получения ковалентно связанных УНТ использовали методику, приведенную в [3]. УНТ и МГФ предварительно окисляли раствором азотной кислоты (“х.ч.”, “Реахим”) при кипячении в течение 4 ч с последующим фильтрованием осадка и промыванием дистиллированной водой до нейтрального значения pH промывных вод. К 50 г окисленных УНТ в 250 мл спирта прибавляли 24 мл 3-аминопропилтриэтоксосилана H2NC3H6Si(OEt)3 (“х.ч.”) и 12 мл муравьиной кислоты для поддержания рН среды в интервале 4–4.5. Реакционную смесь перемешивали при 60°С в атмосфере Ar в течение 24 ч. Продукт промывали дистиллированной водой и сушили при 60°С в течение 8 ч. Образец обозначен УНТ_УНТ. Для получения ковалентно “сшитых” УНТ с МГФ к 50 г полученного продукта УНТ_УНТ, диспергированного в растворе N,N-диметилацетамида, добавляли 50 г окисленных МГФ в диметилформамиде. Смесь обрабатывали ультразвуком при охлаждении в течение 1 ч. Остатки дисперсионной среды удаляли фильтрованием полученного материала, который сушили при 135°С в течение 8 ч. Образец обозначен УНТ_МГФ.
ИП-спекание осуществляли в установке Labox-625 (Sinterland, Japan) в течение 5 мин при 1100°С и аксиальном давлении 30 МПа [8]. Спекание проводили в листах графлекса толщиной 15 мм, который потом отслаивали с поверхности образцов. Скорость нагрева составила 100 К мин–1. Спеченные образцы обозначены УНТ_УНТ_ИПС и УНТ_МГФ_ИПС.
Окисление ИП-спеченных образцов осуществляли парами азотной кислоты согласно методике [8, 31]. Для этого спеченные таблетки УНТ_УНТ_ИПС и УНТ_МГФ_ИПС в сухом открытом бюксе помещали внутрь круглодонной колбы. Колбу частично заполняли азотной кислотой (“Химмед”, ~70%, плотность 1.4 гсм–3, чистота 99.999%) таким образом, чтобы она не попадала в бюкс и кипятили с прямым холодильником. Окисляемые таблетки при этом оказывались в парах кипящей при 122°С кислоты, которые состояли из смеси HNO3, O2, H2O и оксидов азота [31]. В процессе окисления конденсат собирали в специальном приемнике. Окисление осуществляли в течение 3 и 6 ч. Условия получения всех образцов и их обозначения приведены в табл. 1.
Таблица 1.
Условия получения образцов (τ – продолжительность окисления в газовой фазе)
Образец | Методика получения | τ, ч |
---|---|---|
УНТ_УНТ | 1) окисление УНТ раствором HNO3, 2) окисленные УНТ+H2NC3H6Si(OEt)3 + HCO2H (Ar, 60°С, 24 ч) |
– |
УНТ_УНТ_ИПС | ИП-спекание (1100°C, 30 МПа) образца УНТ_УНТ | – |
УНТ_УНТ_ИПС_3 | окисление УНТ_УНТ_ИПС парами азотной кислоты | 3 |
УНТ_УНТ_ИПС_6 | » | 6 |
УНТ_МГФ | 1) окисление УНТ и МГФ раствором HNO3, 2) окисленные УНТ + H2NC3H6Si(OEt)3 + HCO2H (Ar, 60°С, 24 ч), 3) УНТ_УНТ в CH3CON(CH3)2 + окисленные МГФ в (CH3)2NCH. |
– |
УНТ_МГФ_ИПС | ИП-спекание (1100°C, 30 МПа) образца УНТ_МГФ | – |
УНТ_МГФ_ИПС_3 | окисление УНТ_МГФ_ИПС парами азотной кислоты | 3 |
УНТ_МГФ_ИПС_6 | » | 6 |
Морфологию УНМ определяли методом сканирующей (СЭМ) и просвечивающей (ПЭМ) электронной микроскопии на приборах “JEOL JSM-6390LA” при ускоряющем напряжении 20–25 кВ и “JEOL 2100F/Cs” (“JEOL Ltd”, Япония) с ускоряющим напряжением 200 кВ соответственно.
Рентгеновскую фотоэлектронную спектроскопию (РФЭС) использовали для определения состава поверхности образцов. Спектры регистрировали на спектрометре Axis Ultra DLD (“Kratos Analytical”, Великобритания) с использованием монохроматического AlKα-излучения (1486.7 эВ). Обзорные РФЭ-спектры получали при энергии пропускания анализатора, равной 160 эВ, и шаге 1 эВ, а спектры высокого разрешения – с энергией пропускания 40 эВ и шагом 0.1 эВ.
Спектры комбинационного рассеяния (КР) регистрировали на УФ-спектрометре “LabRamHR800 UV” (“HoribaJobinYvon”, Япония) с использованием возбуждения 5 МВт аргонового лазера с длиной волны 514.5 нм, и объектива 50x Olympus. Для каждого образца КР-спектр получали как минимум в пяти точках и усредняли.
ОБСУЖДЕНИЕ РЕЗУЛЬТАТОВ
Функционализацию поверхности УНТ различными группами, как правило, осуществляют после их окисления, так как в этом случае центрами химических реакций служат карбоксильные группы [34]. В настоящей работе ковалентные связи между отдельными УНТ формировались за счет взаимодействия поверхностных карбоксильных групп с продуктами гидролиза 3-аминопропилтриэтоксосилана (рис. 2). Гидролиз 3-аминопропилтриэтоксосилана катализирует кислая среда, в результате чего этоксогруппы превращаются в гидроксильные и мгновенно конденсируются с образованием поликремниевых производных [35] (рис. 2а). Параллельно карбоксильные группы на поверхности УНТ вступают в реакцию конденсации с ОН-группами поликремниевых производных, в результате чего отдельные УНТ оказываются ковалентно “сшиты” между собой связями (УНТ)С–O–Si–O–С(УНТ) (рис. 2б). Одновременно возможно электростатическое взаимодействие кислых карбоксильных групп с RNH$_{3}^{ + }$ [3, 34, 36].
Рис. 2.
Схема гидролиза и конденсации кремниевых производных (а) и одновременного образования ковалентных мостиков C-O-Si-O-C между окисленными УНТ и гидролизованным 3-аминопропилтриэтоксосиланом (б).
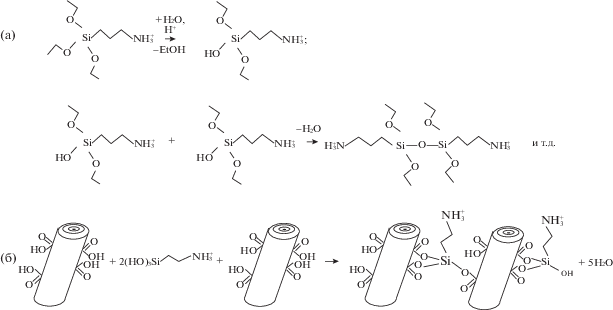
Изображения СЭМ и ПЭМ ковалентно “сшитых” материалов до и после ИП-спекания представлены на рис. 3. Отдельные УНТ ясно различимы на всех микрофотографиях СЭМ (рис. 3а, в, д, ж). Образцы УНТ_УНТ и УНТ_МГФ покрыты оболочками гидролизованного H2NC3H6Si(OEt)3 (рис. 3а–3г), которые исчезали после ИП-спекания (рис. 3д–3e). Все УНТ на всех стадиях сохраняли свою тубулярную структуру (рис. 3е). В случае ковалентных “сшивок” между УНТ и МГФ после ИП-спекания в образце УНТ_МГФ_ИПС появились графеновые листы (рис. 3з) и ЛУС (рис. 4).
Рис. 3.
Изображения СЭМ и ПЭМ УНТ_УНТ (a, б), УНТ_МГФ (в, г) и УНТ_УНТ_ИПС (д, е), УНТ_МГФ_ИПС (ж, з).
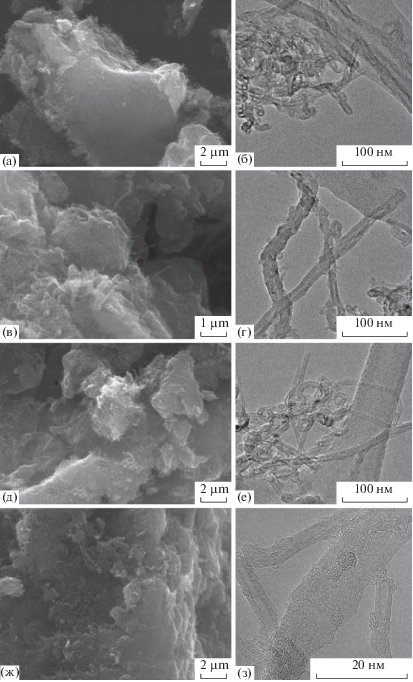
Вследствие формирования плазмы и высоких температур происходило элиминирование кислородсодержащих групп, что ранее неоднократно наблюдали при ИП-спекании различных УНМ: оксида графена [6], карбоксилированных УНТ [15] или электрохимически эксфолиированного графита [4]. Согласно данным РФЭС, кремний в составе образцов УНТ_УНТ_ИПС и УНТ_МГФ_ИПС находился в виде оксида SiO2, а связи C–O–Si исчезли (табл. 2).
Таблица 2.
Энергии связи (EB) и атомные доли (ат. %) компонентов в РФЭ-спектрах высокого разрешения ковалентно “сшитых” УНТ и УНТ с МГФ до и после ИП-спекания
Спектр | EB, эВ | Доли, ат. % | Тип связи | |||
---|---|---|---|---|---|---|
УНТ_УНТ | УНТ_УНТ_ИПС | УНТ_МГФ | УНТ_МГФ_ИПС | |||
O1s | 530.9–533.9 | 7.7 | 2.6 | 6.2 | 3.0 | O–, O=C, O–C=O OH–C, O–Si |
C1s | 284.4–284.4 | 78.9 | 94.3 | 85.8 | 93.3 | C–C (sp2) |
285.1–285.4 | 4.2 | – | 1.7 | – | C–C (sp3) | |
286.5–288.9 | 6.5 | 2.3 | 4.7 | 2.8 | C–O, C=O, O–C–O, O=C–O | |
N1s | 398.3–407.0 | 1.8 | 0.3 | 1.1 | 0.5 | C=N–C, NR3, N≡C, NOx |
Si2p | 102.6 | 0.9 | – | 0.5 | – | SiOxCyHz |
103.5 | – | 0.5 | – | 0.4 | SiO2 |
При ИП-спекании возрастает доля sp2-гибридизованных атомов углерода (табл. 2), что свидетельствует о совершенствовании графитовой структуры УНТ [13].
В КР-спектрах УНМ присутствуют, как правило, несколько линий. Линия D (1360 см–1) соответствует радиальной дыхательной моде Alg ароматического кольца C6 графеновой плоскости, в которой сопряжены sp2-гибридизованные атомы углерода. Эта мода резонансно возбуждается при оптических переходах π-электронов в соответствующих графеновых кластерах. Линия G (1581 см–1) соответствует E2g валентным колебаниям ароматического C6 кольца [37]. Увеличение отношения интенсивностей ID/IG, как правило, свидетельствует об увеличении дефектности и разупорядочении углеродной структуры [38]. Кроме линий D и G для УНМ характерна линия 2D (2700 см–1), являющаяся обертоном D-линии [39].
После ИП-спекания УНТ_УНТ отношение ID/IG уменьшилось до 0.23 по сравнению с исходными УНТ (ID/IG = 0.87), кроме того, появились обертоны D + G (2960 см–1) и 2G (~3200 см–1) (рис. 5а). Ширина линий D и G на полувысоте стала меньше, что свидетельствует о совершенствовании графитовой структуры и возможном “залечивании” дефектов, что ранее неоднократно наблюдали при ИП-спекании многостенных УНТ [12, 13]. Отношение ID/IG после ИП-спекания увеличилось от 0.56 для УНТ_МГФ до 0.95 для УНТ_МГФ_ИПС (рис. 5б). Вероятно, такой результат – следствие появления новой фазы ЛУС после ИП-спекания [8]. Отметим, что G-линия в спектрах наночастиц ЛУС смещается в область 1590–1600 см–1, характерную для нанокластеров углерода [40, 41] или для “сворачивания” углеродных слоев [42].
Рис. 5.
Спектры комбинационного рассеяния образцов ковалентно сшитых УНТ (а) и ковалентно сшитых УНТ и МГФ (б).
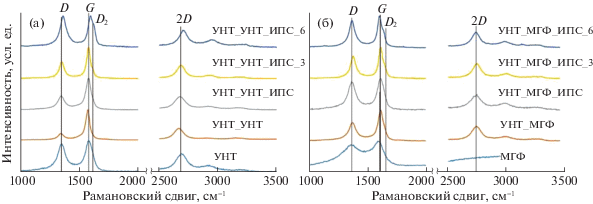
Несмотря на то, что метод ИП-спекания подразумевает формирование образцов, плотность которых приближена к теоретической, при спекании УНТ_УНТ и УНТ_МГФ не удалось получить высокоплотных образцов. Полученные значения 0.85 и 0.81 г см–3 намного меньше, чем значения для консолидированных при различных параметрах ИП-спекания трубок, но превосходят плотность ИП-спеченных МГФ [8] (табл. 3). При спекании (1100°С, 30 МПа) МГФ наблюдалось появление смеси фаз графена, ЛУС сферической и полигональной форм, что приводило к уменьшению объемной плотности образцов. При обработке УНТ плотность, как правило, возрастала с увеличением, как температуры, так и давления ИП-спекания. Образцы УНТ_УНТ_ИПС и УНТ_МГФ_ИПС имели промежуточное значение плотности между значениями для ИП-спеченных МГФ и УНТ.
Таблица 3.
Плотность (ρ) консолидированных образцов УНМ (Т и Р – условия ИП-спекания, МУНТ – Многостенные УНТ)
Образец | T, °C | P, МПа | ρ, г см–3 | Ссылка |
---|---|---|---|---|
УНТ_УНТ_ИПС | 1100 | 30 | 0.85 | Настоящая работа |
УНТ_МГФ_ИПС | 1100 | 30 | 0.81 | » |
УНТ (10–15 углеродных слоев) | 1000 | 22 | 0.97 | [13] |
» | 1300 | 22 | 1.39 | » |
» | 1500 | 10 | 1.10 | » |
» | 1500 | 16 | 1.37 | » |
» | 1500 | 22 | 1.46 | » |
» | 1800 | 22 | 1.60 | » |
МУНТ (20–30 нм диаметр) | 2000 | 100 | 1.56 | [20] |
МУНТ | 1100 | 40 | 1.95 | [43] |
МУНТ | 1100 | 100 | 0.85 | [44] |
МУНТ | 1700 | 50 | 2 | [45] |
МУНТ (30–40 нм диаметр) | 2000 | 25 | 1.1 | [23] |
Графитовые чешуйки | 1850 | 80 | 2.11 | [5] |
МГФ | 1100 | 30 | 0.42 | [8] |
После ИП-спекания электропроводность образцов УНМ достигает, как правило, высоких значений. Например, электропроводность двустенных УНТ (ИП-спекание при 1100°C, 100 МПа) составляет 1.65 × 105 См м–1 [12], а многостенных (ИП-спекание при 2000°С и 25 МПа) – (3.3–5) × × 104 См см–1 [23], при ИП-спекании (1200–1700, 30–100 МПа) УНТ с наночастицами Co удалось получить образцы с электропроводностями (0.5–4.5) × 103 См м–1 [44]. Авторы [12, 23] связывали увеличение электропроводности с возникновением новых С–С-связей между отдельными УНТ. Однако электропроводность УНМ увеличивается и вследствие термической обработки [46, 25 ], и при прессовании [47, 26 ], и с увеличением плотности [48], поэтому факт увеличения электропроводности УНМ после ИП-спекания не может рассматриваться как прямое доказательство возникновения новых С–С-связей. Следуя этой логике, можно предположить, что изначально созданные ковалентные связи между отдельными УНТ будут способствовать увеличению электропроводности материалов.
Электропроводность образцов определяли в соответствии с методикой [44]. Для этого спеченные таблетки УНТ_УНТ_ИПС и УНТ_МГФ_ИПС зажимали между двумя медными электродами диаметром 2.2 мм. Сопротивление измеряли с использованием вольтметра V7-78/1 (AKIP, Россия). Электропроводности вычисляли с использованием измеренных значений сопротивления по формуле:
где L –толщина образца, м; R – измеренное сопротивление, Ом; S – площадь контакта электродов с анализируемым образцом, м2. Для УНТ_УНТ_ИПС и УНТ_МГФ_ИПС значения электропроводности составили 42 и 57 См м–1 соответственно.Полученные значения существенно ниже 1.65 × 105 [12] и (3.3–5) × 104 См.см–1 [23], что обусловлено, вероятно, низкой плотностью образцов (табл. 3) и отсутствием связей между отдельными УНТ. Ковалентные связи С–O–Si–O–С были разрушены вследствие элиминирования кислорода при ИП-спекании (табл. 2), а предложенный подход оказался неэффективным.
Окисление спеченных таблеток УНТ_УНТ_ИПС и УНТ_МГФ_ИПС в газовой фазе не привело к растрескиванию или какому-либо другому разрушению этих таблеток, а сам метод может быть рекомендован для функционализации карбоксильными группами поверхности ИП-спеченных УНМ [8]. С увеличением времени окисления с 3 до 6 ч происходило увеличение содержания кислорода на поверхности УНТ_УНТ_ИПС с 8.4 до 15.3 ат. %, а на поверхности УНТ_МГФ_ИПС с 14.0 до 16.1 ат. %, что подтверждено методом РФЭС (табл. 4).
Таблица 4.
Энергии связи (EB) и атомные доли компонент в РФЭ-спектрах высокого разрешения окисленных в течение 3 и 6 ч образцов
Спектр | EB, эВ | Доля, ат. % | Тип связи | |||
---|---|---|---|---|---|---|
УНТ_УНТ_ ИПС_3 | УНТ_УНТ_ ИПС_6 | УНТ_МГФ_ИПС_3 | УНТ_МГФ_ИПС_6 | |||
O1s | 531.1 | 2.5 | 3.4 | 3.8 | 5.9 | O=C–O |
532.1 | 4.1 | 7.6 | 6.1 | 5.7 | C, H–O–C, O–Si, O–N | |
533.1 | 2.3 | 4.3 | 4.1 | 4.6 | O=C–O | |
C1s | 284.4–284.4 | 87.4 | 71.0 | 72.8 | 69.4 | C–C (sp2) |
285.1–285.4 | 0.4 | 6.5 | 6.3 | 6.8 | C–C (sp3) | |
286.5–288.9 | 3.8 | 7.2 | 6.9 | 7.7 | C–O, C=O, O–C–O, O=C–O |
При деконволюции O1s РФЭ-спектров окисленных образцов [33], выделены три основных линии с энергиями 531.1, 532.1 и 533.1 эВ, соответствующих кислороду с двойной связью O=C–O в карбоксильной группе, связям H–O–C, O–Si, O–N и кислороду с одинарной связью с углеродом O=C–O в карбоксильной группе соответственно (табл. 4). При окислении УНТ_УНТ_ ИПС происходит постепенное увеличение всех типов кислородсодержащих групп, в то время как при окислении УНТ_МГФ_ИПС увеличивается лишь концентрация карбоксильных групп (табл. 4). Одновременно с увеличением содержания кислорода в образце УНТ_УНТ_ИПС увеличивается доля sp3-гибридизованных атомов углерода, которым соответствует энергия связи 285.1–285.4 эВ в C1s РФЭ-спектрах (табл. 4). Это происходит за счет увеличения доли краевых атомов углерода при окислении. В образце УНТ_МГФ_ИПС при увеличении времени окисления с 3 до 6 ч количество sp3-атомов углерода возрастает существенно меньше, что, вероятно, связано с большим содержанием sp3-гибридизованных атомов С исходных МГФ.
Отметим, что установленные значения содержания кислорода превосходили ранее найденные значения при окислении УНТ различной морфологии растворами кислот-окислителей [28, 29] или же их в газовой фазе HNO3 [31] или O3 [29]. При окислении в газовой фазе ИП-спеченных образцов МГФ удавалось достичь существенно большего содержания кислорода на поверхности, которые составили 17.8 после 3 ч обработки и 28.8 ат. % после 6 ч [8].
При обработке УНТ и/или МГФ происходит окисление поверхности с формированием поверхностных групп – гидроксильных, карбоксильных, кето-, и др. При увеличении времени окисления с поверхности УНМ элиминируется CO2 – продукт полного окисления углерода. После ~3 ч окисления процессы фукционализации–дефункционализации с образованием CO2 приходят в равновесие, дальнейшая модификация поверхности приводит лишь к удалению углерода, но не к изменению концентрации кислородсодержащих групп [28, 29, 33].
Отношение интенсивностей линий ID/IG в КР-спектрах после окисления УНТ_УНТ_ИПС увеличивалось до 0.45 (образец УНТ_УНТ_ИПС_3) и 0.86 (образец УНТ_УНТ_ИПС_6) (рис. 5а). У G-линии после окисления появлялось плечо (~1620 см–1), что соответствует росту доли краевых атомов углерода [49]. Отношение ID/IG для образца УНТ_МГФ_ИПС уменьшилось до 0.63 (образец УНТ_МГФ_ИПС_3) и потом увеличилось до 0.87 (образец УНТ_МГФ_ИПС_6) (рис. 5б). Вероятно, подобная тенденция связана с удалением из состава УНТ_МГФ_ИПС_3 всех графеновых листов и частиц ЛУС и, как следствие, с увеличением его структурированности. После дальнейшего окисления увеличивалась степень дефектности УНТ_МГФ_ИПС_6, связанная с разрушением тубулярной структуры УНТ [49].
При ИП-спекании УНМ происходят параллельно, как минимум, шесть процессов: поверхностная, объемная, межзеренная диффузии, испарение атомов и ионов с поверхности с образованием плазмы между зернами, перекристаллизация поверхности и в ряде случаев формирование новых фаз [50, 51]. Доминирование какого-либо процесса определяется температурой и давлением ИП-спекания, а также природой УНМ [15]. Ранее мы предприняли попытку разделить вклад температуры и давления, используя первое начало термодинамики, и пришли к выводу, что вклад температуры – по сути выделяющееся джоулево тепло – имеет преимущественное значение [13].
Для образования новых углеродных фаз, как правило, необходимы экстремально высокие T и P [19, 21, 52]. Эффект от спекания, заключающийся в фазовом изменении, или существенное изменение физико-химических характеристик материала после спекания также в большей степени определяется температурой, так как для спекания необходим пробой, при котором будет формироваться плазма [15, 53]. Например, УНТ и фуллерены C60 при 1500°С и 80 МПа превращаются в наноалмазы [21, 54], а при 2400°С и 100 МПа – в графеновые листы [19]. Присутствие примесей металлов VIII группы катализирует превращение [54].
МГФ в представленных условиях ИП-спекания (1100°С, 30 МПа) превращались в новые фазы – графен и ЛУС. При более низком давлении 16 МПа и температуре 1600°С никаких трансформаций с МГФ не происходило [7]. Отметим, что графен не превращается в ЛУС при меньших температурах ИП-спекания 200, 250, 300 или 400°C [6]. Однако этот процесс осуществим при обработке лазером УНМ [54] или МГФ [55]. При ИП-спекании происходит испарение атомов углерода и кремния в газовую фазу. После перекристаллизации углерод формирует графеновые листы, а кремний остается в составе образцов в виде SiO2. Атомы углерода, вероятно, могут также испаряться с поверхности вновь сформировавшихся графеновых листов, при этом на месте “дырок” углеродные плоскости заворачиваются, уменьшая избыточную энергию нескомпенсированных атомов углерода, что приводит к формированию ЛУС [8].
ЗАКЛЮЧЕНИЕ
Ковалентно сшитые УНТ и УНТ с МГФ получены при кислом гидролизе 3-аминопропилтриэтоксосилана в присутствии окисленных УНТ или смеси УНТ с МГФ. При последующем ИП-спекании при 1100°С и 30 МПа получены консолидированные нерассыпающиеся таблетки соответствующих углеродных композитов. Методом РФЭС установлено, что во время ИП-спекания ковалентные связи между отдельными углеродными частицами не сохраняются, а кремний входит в состав консолидатов в виде SiO2. В образце ковалентно “сшитых” УНТ и МГФ происходит фазовый переход с образованием ЛУС и графеновых листов. При ИП-спекании атомы углерода испаряются с поверхности УНT и МГФ, после чего перекристаллизовываются с совершенствованием графитовой структуры УНТ и формированием новых фаз. Наиболее существенное влияние на данный процесс оказывает температура.
Плотность полученных консолидированных материалов равна 0.85 и 0.81 г.см–3, что ниже теоретически рассчитанного значения для консолидированных УНТ и графита. Значения проводимости консолидированных образцов, рассчитанных как соотношение толщины образца к сопротивлению и площади контактов, составили 42 и 57 См м–1 для УНТ и УНТ-МГФ спеченных образцов соответственно. Это свидетельствует о том, что описанный подход неэффективен для получения хорошо проводящих образцов УНТ или композитов УНТ с МГФ. Показано, что при увеличении времени обработки с 3 до 6 ч при газофазном окислении содержание кислорода на поверхности материалов увеличивалось от 8.4 до 15.3 ат. % для 3D-сшитых структур УНТ и от 14.0 до 16.1 ат. % для 3D-сшитых структур УНТ с МГФ.
Список литературы
Li Z., Wang L., Li Y., Feng Y., Feng W. // Compos. Sci. Technol. 2019. V. 179. P. 10. https://doi.org/10.1016/j.compscitech.2019.04.028
Крючков В.А., Крючков М.В., Выморков Н.В. и др. // Композиты и наноструктуры. 2015. Т. 7 (3). С. 183.
Cao M., Du C., Guo H. et al. // Composites A. 2018. V. 115. P. 331. https://doi.org/10.1016/j.compositesa.2018.09.024
Gong Y., Ping Y., Li D. et al. // Appl. Surf. Sci. 2017. V. 397. P. 213. https://doi.org/10.1016/j.apsusc.2016.11.153
Nieto A., Lahiri D., Agarwal A. // Carbon. 2012. V. 50. P. 4068.
Chakravarty D., Tiwary C.S., Woellner C.F. et al. // Adv. Mater. 2016. V. 28. P. 8959. https://doi.org/10.1002/adma.201603146
Strokova N., Savilov S., Xia H. et al. // Z. Phys. Chem. 2016. V. 230. P. 1719. 2016.https://doi.org/10.1515/zpch-2016
Suslova E.V., Epishev V.V., Maslakov R.I. et al. // Appl. Surf. Sci. 2020. V. 535. P. 147724. https://doi.org/10.1016/j.apsusc.2020.147724
Zhang F., Ahmed F., Holzhuter G., Burkel E. // J. Cryst. Growth. 2012. V. 340. P. 1.
Jun T.S., Park N.H., So D.S. et al. // J. Korean Cryst. Growth Cryst. Technol. 2013. V. 23. P. 27.
Yamamoto G., Sato Y., Takahashi T. et al. // J. Mater. Res. 2006. V. 21. P. 1537.
Laurent C., Chevallier G., Weibel A. et al. // Carbon. 2008. V. 46. P. 1812.
Suslova E., Savilov S., Egorov A. et al. // Micropor. Mesopor. Mat. 2020. V. 293. P. 109807. https://doi.org/10.1016/j.micromeso.2019.109807
Laurent C., Dinh T.M., Barthelemy M.C. et al. // J. Mater. Sci. 2018. V. 53. P. 3225.
Suslova E.V., Chernuak S.A., Maksimov S.V., Savilov S.V. // Carbon. 2020. V. 168. P. 597. https://doi.org/10.1016/j.carbon.2020.07.026
Borrell A., Fernández A., Merino C., Torrecillas R. // Int. J. Mat. Res. 2010. V. 101. P. 112.
Kanari M., Tanaka K., Baba S., Eto M. // Carbon. 1997. V. 35. № 10–11. P. 1429.
Uo M., Hasegawa T., Akasaka T. et al. // Bio Med. Mater. Eng. 2009. V. 19. P. 11.
Ham H., Park N.H., Kang I. et al. // Chem. Commun. (J. Chem. Soc. Sect. D). 2012. V. 48. P. 6672.
Zhang Z.H., Qi L., Shen X.B. et al. // Mat. Sci. Eng. A. 2013. V. 573. P. 12.
Zhang F., Shen J., Sun J. et al. // Carbon. 2005. V. 43. P. 1254.
Ukhina A.V., Dudina D., Anisimov A.G. et al. // Ceram. Int. 2015. V. 41. P. 12459.
Ma R.Z., Xu C.L., Wei B.Q. et al. // Mater. Res. Bull. 1999. V. 34. P. 741.
Li J.L., Bai G.Z., Feng J.W., Jiang W. // Carbon. 2005. V. 43. P. 2649.
Kis A., Csanyi G., Salvetat J.P. et al. // Nat. Mater. 2004. V. 3. P. 153.
Елецкий А.В., Книжник А.А., Потапкин Б.В., Кенни Х.М. // Успехи физ. наук. 2015. Т. 185 (3). С. 225.
Hooijdonk E.V., Bittencourt C., Snyders R., Colomer J.F. // Beilstein J. Nanotechnol. 2013. V. 4. P. 129. https://doi.org/10.3762/bjnano.4.14
Савилов С.В., Иванов А.С., Егоров А.В. и др. // Журн. физ. химии. 2016. Т. 90. № 2. С. 249.
Савилов С.В., Иванов А.С., Черняк С.А. и др. // Журн. физ. химии. 2015. Т. 89. № 11. С. 1723.
Chernyak S.A., Ivanov A.S., Strokova N.E. et al. // J. Phys. Chem. C. 2016. V. 120. P. 17465. https://doi.org/10.1021/acs.jpcc.6b05178
Xia W., Jin C., Kundu S., Muhler M. // Carbon. 2009. V. 47. P. 919.
Savilov S.V., Strokova N.E., Ivanov A.S. et al. // Mat. Res. Bull. 2015. V. 69. P. 13. https://doi.org/10.1016/j.materresbull.2015.01.001
Chernyak S.A., Ivanov A.S., Podgornova A.M. et al. // PCCP. 2018. V. 20. P. 24117. https://doi.org/10.1039/C8CP05149F
Vieira K.O., Panzera T.H., Ferrari J.L., Schiavon M.A. // Mat. Res. 2018. V. 21. № 6. P. e20180291. https://doi.org/10.1590/1980-5373-mr-2018-0291
Bechtold M.X., Vest R.D., Plambeck L. // J. Am. Chem. Soc. 1968. V. 90. № 17. P. 4590. https://doi.org/10.1021/ja01019a015
Ganguli S., Roy A.K., Anderson D.P. // Carbon. 2008. V. 46. P. 806. https://doi.org/10.1016/j.carbon.2008.02.008
Сморгонская Э.А., Звонарева Т.К., Иванова Е.И. и др. // Физика тв. тела. 2003. Т. 46. Вып. 9. С. 1579.
Biru E.I., Iovu H. Graphene Nanocomposites Studied by Raman Spectroscopy. 2017. https://doi.org/10.5772/intechopen.73487
Varga M., Izak T., Vretenar V. et al. // Carbon. 2017. V. 111. P. 54. https://doi.org/10.1016/j.carbon.2016.09.064
Bokova-Sirosh S.N., Pershina A.V., Kuznetsov V.L. et al. // J. Nanoelectr. Optoelectr. 2013. V. 8. P. 106.
Nemanich R.J., Solin S.A. // Phys. Rev. B. 1979. V. 20. P. 392.
Obraztsova E.D., Fujii M., Hayashi S. et al. // Carbon. 1998. V. 36. P. 821.
Wang W., Yokoyama A., Liao S. et al. // Mat. Sci. Engineer. C. 2008. V. 28. P. 1082.
Savilov S.V., Chernyak S.A., Paslova M.S. et al. // ACS Appl. Mat. Interfaces. 2018. V. 10. P. 20983.
Qin C., Shi X., Bai S.Q. et al. // Mat. Sci. Engineer. A. 2006. V. 420. P. 208.
Yamamoto G., Shirasu K., Nozaka Y. et al. // Carbon. 2014. V. 66. P. 219.
Marinho B., Ghislandi M., Tkalya E. et al. // Powder Technol. 2012. V. 221. P. 351.
Суслова Е.В., Архипова Е.А., Калашник А.В. и др. // Журн. физ. химии. 2019. Т. 93 (10). С. 1551. Suslova E.V., Arkhipova E.A., Kalashnik A.V. et al. // Russ. J. Phys. Chem. A. 2019. V. 93. P. 1960.
Chernyak S.A., Ivanov A.S., Maslakov K.I. et al. // PCCP. 2017. V. 19. P. 2276. https://doi.org/10.1039/c6cp04657f
Khoshghadam-Pireyousefan M., Mohammadzadeh A., Heidarzadeh A.A., Brabazon D. // Ref. Module Mat. Sci. Mat. Engineer. 2021. https://doi.org/10.1016/B978-0-12-803581-8.11907-1
Hu Z.Y., Zhang Z.H., Cheng X.W. et al. // Mat. Design. 2020. V. 191. P. 108662. https://doi.org/10.1016/j.matdes.2020.108662
Zhang F., Adam M., Ahmed F. et al. // Diamond Rel. Mat. 2011. V. 20. P. 853. https://doi.org/10.1016/j.diamond.2011.04.006
Сивков А.А., Герасимов Д.Ю., Евдокимов А.А. // Российские нанотехнол. 2015. № 10 (9–10).
Павлюченко П.Е., Серопян Г.М., Тренихян М.В., Дроздов В.А. // Журн. общ. химии. 2020. Т. 90. С. 559.https://doi.org/10.1134/S1070363220030317
Du J., Zhao R., Zhu Z. // Phys. Status Solidi. A. 2011. V. 208. P. 878. https://doi.org/10.1002/pssa.201026646
Дополнительные материалы отсутствуют.
Инструменты
Журнал физической химии