Физика металлов и металловедение, 2019, T. 120, № 10, стр. 1022-1029
Влияние легирующей микродобавки ванадия на характер изотермического превращения в эвтектоидной стали
Цай Чжень a, c, Мао Синь-пин a, c, Бао Сы-цянь a, b, *, Чжао Ган a, b, Ху Сяо a, b
a Ведущая государственная лаборатория огнеупоров и металлургии тугоплавких материалов,
Уханьский университет науки и технологии
430081 Хубэй, Ухань, Китай
b Ведущая лаборатория черной металлургии и использования минеральных ресурсов подчинения
Министерства Высшего и среднего образования, Уханьский университет науки и технологии
430081 Хубэй, Ухань, Китай
c Уханьский филиал центрального научно-исследовательского института
сталелитейной промышленности корпорации Бао-Сталь (Шанхай)
430080 Ухань, Китай
* E-mail: caizhen198804@126.com
Поступила в редакцию 10.09.2018
После доработки 20.11.2018
Принята к публикации 15.04.2019
Аннотация
Влияние ванадия как микролегирующей добавки на характер распада аустенита и превращений микроструктуры эвтектоидной стали изучено при изотермическом охлаждении. Растворенный в γ матрице ванадий оказал отрицательный эффект на распад аустенита с образованием перлитной микроструктуры и привел к уменьшению межламельного расстояния. Более того, полученные результаты показали, что растворенный ванадий сегрегировал на границах зерна аустенита, что привело к подавлению формирования зернограничного феррита. Вместе с тем выделение ванадия при изотермическом процессе привело к снижению растворенного в матрице ванадия, что косвенно способствовало превращению в перлит. Возникавшие выделения могли выступать в качестве зародышей для формирования перлита, что также ускоряло указанное превращение. Межламельное расстояние перлита возросло в результате ухода углерода в выделения. Добавление азота заметно ускорило это превращение вследствие того, что химическая движущая сила образования нитрида ванадия была значительно выше в сравнении с отмеченным перераспределением углерода.
ВВЕДЕНИЕ
Использование микродобавок ванадия является одним из наиболее общих способов обеспечения дисперсионного твердения [1–3]. Упрочнение феррита выделениями ванадия продолжают широко изучать как уже используемое в низко- и среднеуглеродистых сталях [4, 5], так и перспективное в применении к высокоуглеродистым сталям [6–9]. Исследования эффекта легирующей микродобавки ванадия в случае высокоуглеродистых сталей до сих пор в основном были сфокусированы на изучении процессов выделения. Вместе с тем характер распада аустенита в высокоуглеродистых сталях и эволюцию микроструктуры в этом процессе практически не освещали в литературе.
В высокоуглеродистых сталях одной из главных черт является их перлитная микроструктура. Что касается влияния ванадия на межламельные расстояния в перлите, ряд исследователей склоняются к мнению, что добавка ванадия приводит к их уменьшению [10, 11]. Однако существуют и противоположные мнения, согласно которым ванадий в действительности не только не приводит к уменьшению, но и способствует увеличению межламельных расстояний в перлите [12]. Тем самым вопрос влияния растворенного ванадия на характер трансформации феррита в высокоуглеродистых сталях становится предметом активной дискуссии. Авторы публикаций [13, 14] отмечали присутствие феррита в областях γ-матрицы, прилегающих к границам зерен, и относили это на счет одной из функций ванадия; вместе с тем некоторые исследователи убеждены, что сегрегирование атомов ванадия на границы аустенитных зерен делает их менее эффективными в качестве центров зарождения феррита [15, 16].
В данной работе влияние легирующих микродобавок ванадия на характер распада аустенита и трансформации микроструктуры в процессе изотермического охлаждения было изучено на примере эвтектоидной стали. В частности, основное внимание авторов было сосредоточено на выяснении влияния микродобавок ванадия на кинетику превращения и морфологию трансформированной микроструктуры.
МЕТОДИКА ЭКСПЕРИМЕНТА
Состав исследованных сталей приведен в табл. 1. Стали были выплавлены в вакуумной среднечастотной индукционной печи. После двухчасовой выдержки при 1100°C слитки были прокатаны в пластины толщиной 20 мм. Для проведения пилотных термомеханических обработок из них на токарном станке были выточены цилиндрические образцы диаметром 8 мм и высотой 12 мм.
Таблица 1.
Химический состав исследованных сталей
Образец | C | Si | Mn | P | S | V | N |
---|---|---|---|---|---|---|---|
A | 0.798 | 0.21 | 0.33 | <0.015 | <0.01 | ||
B | 0.80 | 0.21 | 0.32 | <0.015 | <0.01 | 0.094 | |
C | 0.78 | 0.22 | 0.33 | <0.015 | <0.01 | 0.27 | |
D | 0.79 | 0.22 | 0.35 | <0.015 | <0.01 | 0.098 | 0.02 |
Сначала методом дилатометрии при скорости охлаждения 20 К/с была установлена температура начала превращения, Aс1. Далее образцы нагревали до 1150°C и выдерживали в течение 5 мин. Затем охлаждали со скоростью 20 К/с до 640°C и выдерживали 5 мин. И наконец охлаждали со скоростью 50 К/с до комнатной температуры, чтобы зафиксировать микроструктуру, испытавшую превращение.
Микроструктуру в центральной части объема образцов изучали методами оптической (ОМ) и растровой электронной (РЭМ) микроскопии. Межламелярное расстояние в перлите было установлено из анализа изображений микроструктуры. Выделения ванадия визуализировали методами просвечивающей электронной микроскопии (ПЭМ).
РЕЗУЛЬТАТЫ
Температуры начала превращения Aс1 при скорости охлаждения 20 К/с образцов стали A, B и C составляли 610, 600 и 598°C, соответственно. Термическое расширение образца стали D в промежутках между температурными областями перлитного превращения не было отмечено, а микроструктура, испытавшая превращение после охлаждения, была мартенситной. Перлитное превращение при содержании ванадия 0.1 и 0.27 вес. % оказалось отложенным и ограниченным. Влияние содержания азота на температуру Aс1 является незначительным.
Кинетика изотермического превращения
На рис. 1 представлены дилатометрические кривые распада аустенита в образцах стали A, B, C и D, выдержанных при температуре 640°C в течение 5 мин, а точки начала и конца превращения (распада) аустенита сведены в табл. 2. Для стали A точки начала и конца превращения соответствовали 4 и 29 с, тогда как продолжительность превращения составляла 25 с. Для стали В точки начала и конца превращения были сдвинуты в сторону (как бы “отложены”) больших времен – 46 и 77 с, соответственно, а продолжительность превращения увеличилась до 31 с. Для стали С превращение также было “отложено” в сравнении со случаем стали А. Вместе с тем в случае стали С инкубационный период был короче, чем в случае стали В, а точки начала и конца превращения соответствовали 11 и 44 с, при скорости превращения такой же, как и в случае стали В. Сталь D продемонстрировала самый короткий инкубационный период и самую быструю трансформацию среди всех изученных четырех образцов; точки начала и конца превращения соответствовали 2 и 22 с, а продолжительность превращения составила 20 с. Из-за высокой скорости превращения высвободившаяся теплота в стали D привела к увеличению в значениях температуры и дилатации. Появление пика на дилатометрической кривой для стали D как раз и объясняется таким увеличением в значениях температуры и дилатации.
Микроструктура
На рис. 2 показана микроструктура четырех исследованных сталей после выдержки их образцов при 640°C в течение 5 мин. В каждом случае микроструктура состояла из перлита и небольшого количества феррита, расположенного у некоторых границ γ-зерен. Сталь B продемонстрировала самые тонкие пленочные образования феррита с наименьшим количеством феррита среди всех изученных. Сталь C содержала максимальное количество феррита, с границами γ зерен, вблизи которых были локализованы ферритные пленочные образования (как можно видеть на рис. 3).
Рис. 2.
Доэвтектоидный избыточный феррит в исследованных сталях после выдержки образ-цов при 640°C в течение 5 мин: сталь A (a), B (б), C (в), D (г).
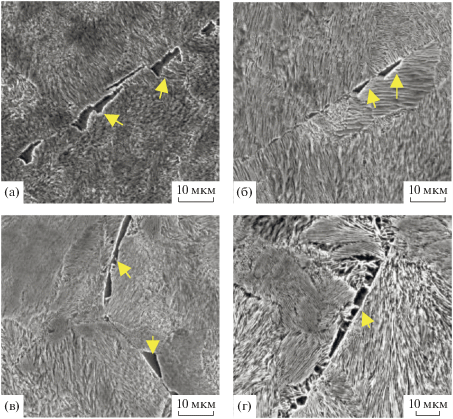
На рис. 4 показана морфология перлита в сталях А, B, C и D после выдержки их образцов при 640°C в течение 5 мин. Видно, что соответствующие карбиды имели пластинчатую форму. Межламелярные расстояния представлены в табл. 3. Для стали A межламелярное расстояние (МР) составило 0.223 ± 0.082 мкм. При содержании ванадия в количестве 0.1 вес. % МР уменьшается до 0.175 ± 0.092 мкм. Вместе с тем, когда содержание ванадия возросло до 0.27 вес. %, МР составило 0.218 ± 0.077 мкм. В стали D, микролегированной ванадием и азотом, был получен самый огрубленный перлит, с МР 0.243 ± 0.085 мкм.
Выделения второй фазы
На ПЭМ-изображениях рис. 5–7 представлена морфология микроструктуры сталей B, C и D после выдержки при 640°C в течение 5 мин. В случае стали B частиц фазы выделения не было обнаружено после завершения изотермического процесса. Вместе с тем в стали C и особенно стали D вдоль границ зерен, а также между цементитными пластинами перлита, отмечено присутствие выделившихся в феррите карбидов VC или V(C, N), по форме напоминающих раскрывшиеся коробочки хлопка. Также наблюдали карбиды железа с “подмешанным” ванадием. При этом пространственная плотность распределения выделений вторых фаз в стали D была более высокая, как можно видеть на рис. 6, 7.
ОБСУЖДЕНИЕ
Выделение ванадия
Растворимость микродобавки ванадия в аустените можно описать следующими формулами [17]:
(1)
${\text{lg[V][C}}{{{\text{]}}}_{\gamma }} = {{{\text{6}}{\text{.72}} - {\text{9500}}} \mathord{\left/ {\vphantom {{{\text{6}}{\text{.72}} - {\text{9500}}} T}} \right. \kern-0em} T}{\text{;}}$(2)
${\text{lg[V][N}}{{{\text{]}}}_{\gamma }} = {{3.63 - {\text{8700}}} \mathord{\left/ {\vphantom {{3.63 - {\text{8700}}} T}} \right. \kern-0em} T}{\text{.}}$Согласно формулам (1) и (2), было положено, что весь “объем” ванадия и азота в сталях B, C и D испытал растворение в γ-матрице при аустенитизации их образцов при 1150°C в течение 5 мин. Выделение ванадия могло происходить при охлаждении образцов вследствие изменения термодинамических условий, а также при изотермическом процессе. Выделение контролировалось диффузией; поэтому не было достаточно времени, чтобы весь растворенный ванадий испытал выделение во время процесса охлаждения со скоростью 20 К/с. Во время изотермического процесса сталь B не обнаружила процессов выделения – время выдержки было слишком мало для этого. В реакциях, описывающих процессы выделения, химическая движущая сила их инициации может быть увеличена за счет увеличения содержания ванадия и, особенно, азота. Именно это обеспечило реализацию выделения ванадия в сталях C и D. Хорошо установлено, что VN имеет значительно меньшую растворимость в сравнении с VC, причем как в феррите, так и аустените. Таким образом, для формирования частиц VN требуется значительно большая движущая (химическая) сила. Именно это делает выделение богатых азотом частиц V(C, N) предпочтительным, пока в матрице сохраняется достаточное количество азота.
Влияние ванадия на перлитное превращение
При охлаждении образца от 1150°C со скоростью 20 К/с установлен факт распада аустенита и определена температура Aс1. Показано, что присутствие растворенного ванадия было способно затормозить реализацию перлитного превращения [18], и этот “тормозной” эффект еще мог возрасти с увеличением содержания ванадия. Вместе с тем влияние растворенного азота на перлитное превращение оказалось незначительным вследствие малой разности в температурах Aс1 сталей B и D.
В результате выдержки при 640°C в сталях C и D выделялись как VC, так и V(C, N), которые могли выступить в качестве центров зарождения перлита. При изучении литературы по среднеуглеродистым сталям выяснилось, что внутригранулярное зарождение феррита обеспечивают как ванадий, так и азот [19, 20]. Далее, выделение карбидов ванадия и V(C, N) могло снизить количество C и V, растворенных в γ-матрице. Оба этих химических элемента косвенно ускоряют перлитное превращение. Увеличение доли выделения ванадия посредством параллельной добавки N привело к возникновению “ускоряющего” воздействия на перлитное превращение.
Растворенный в γ-матрице ванадий привел к увеличению энергии активации диффузии углерода и снижению скорости диффузии углерода в аустените [21]. Как результат, межламелярное расстояние для стали B оказалось меньше в сравнении со сталью A [22]. В начале процесса выделения ванадия количество растворенного в γ-матрице ванадия начало убывать; поэтому уменьшение скорости диффузии углерода в аустените замедлилось [23]. Более того, частицы VC, V(C, N) и микролегированный ванадием цементит оказались способны к захвату атомов углерода, что было необходимо для сформирования цементитных ламелей перлита. Как следствие, соответствующее межламелярное расстояние увеличилось по достижении содержания ванадия отметки 0.27 вес. %, а процессы выделения в стали C начали протекать легче. Благодаря выделению значительной доли V(C,N), межламелярное расстояние для стали D возросло до такой степени, что превысило МР, характерное для стали A.
Влияние ванадия на формирование феррита
Микроструктура эвтектоидной стали, испытавшей превращение при 640°C, была перлитной, но без доэвтектоидного избыточного феррита. Это относят на тот счет, что возникновение избыточного доэвтектоидного феррита, формирующегося вблизи границ γ зерен, как правило, инициируется присутствием кремния. Тенденция сегрегирования ванадия в направлении границ зерен аустенита в нашем случае подтверждается [24], как можно видеть на рис. 8. Можно было бы допустить, что сегрегирование ванадия в направлении границ зерен аустенита приводит к повышению его поверхностной энергии и подавляет формирование зернограничного феррита, как имело место в стали B. Тем не менее, выделение по границам γ-зерен карбонитридов ванадия могло способствовать формированию феррита посредством поглощения им углерода, что объясняет рост количества феррита по границам зерен γ матрицы, особенно в стали C.
ВЫВОДЫ
Влияние ванадия как микролегирующей добавки на характер распада аустенита и трансформацию микроструктуры эвтектоидной стали было исследовано в процессе ее охлаждения и изотермической выдержки. Получены следующие результаты:
1. Ванадий выделяется при изотермическом процессе как в стали C с 0.27 вес. % V, так и в стали D с 0.1 вес. % V и N, но не в стали B с 0.1 вес. % V. Повышенную пространственную плотность выделений наблюдали в стали D, т.к. химическая движущая сила к формированию VN в ней была значительно больше в сравнении с другими образцами.
2. Растворенный в γ-матрице ванадий продемонстрировал эффект подавления распада аустенита в перлит. Выделение ванадия в изотермическом процессе привело к снижению содержания растворенного ванадия в матрице, что косвенно способствовало инициации перлитного превращения. Частицы фазы выделения при этом могли уже выступать в качестве центров зарождения перлита, также ускоряя протекание указанного превращения, в особенности, в стали D с характерными для нее минимальным инкубационным периодом и наибольшей скоростью превращения.
3. Межламельное расстояние в перлите могло быть уменьшено посредством растворения (введения) ванадия, но и увеличено формированием выделений VC, V(C, N) и карбидов железа с “подмешанным” ванадием.
4. Сегрегирование растворенного ванадия в сторону границ зерен аустенита подавляет формирование зернограничного феррита, но такое формирование обычно бывает инициировано поглощением углерода, когда начинают развиваться процессы выделения вторых фаз с участием ванадия.
Список литературы
Han K., Mottishaw T.D., Smith G.D., Edmonds D.V., Stacey A.G. Effects of vanadium additions on microstructure and hardness of hypereutectoid pearlitic steels // Mater. Sci. Eng. A. 1995. V. A190. P. 207.
Jaiswal S., McIvor I.D. Metallurgy of vanadium-microalloyed, high-carbon steel rod // Mater. Sci. Technol. 1985. V. 1. P. 276.
Izotov B.I. Precipitation of disperse vanadium carbides at the interphase boundary upon the pearlitic transformation of a steel // Phys. Met. Met. 2011. V. 111(6). P. 592–597.
Pao T., Chai X.Y., Wang J.G., Su H., Yang C.F. Precipitation Behavior of V–N Microalloyed Steels during Normalizing // J. Iron Steel Res. Int. 2015. V. 22(11). P. 1037–1042.
Yang G.W., Sun X.J., Yong Q.L., Li Z.D., Li X.X. Austenite Grain Refinement and Isothermal Growth Behavior in a Low Carbon Vanadium Microalloyed Steel // J. Iron Steel Res. Int. 2014. V. 21(8). P. 757–764.
Parusov V.V., Sychkov A.B., Derevyanchenko I.V. High-carbon wire rod made of steel microalloyed with vanadium // Metallurgist. 2004. V. 48. P. 618.
Parsons D.E., Malis T.F., Boyd J.D. Microalloying and precipitation in Cr-V rail steels // J. Heat Treating. 1984. V. 3. P. 213.
Piekering F.B., Garbarz B. Strengthening in pearlite formed from thermomechanically processed austenite in vanadium steels and implications for toughness // Mater. Sci. Technol. 1989. V. 5. P. 227.
Wang Q.L., Li F., Zhang G.Y. Effect of Vanadium on the Microstructure and Properties of High Carbon SteelWires // Iron Steel. 2005. V. 40(Suppl). P. 576.
Li Y., Yang Z.M. The effects of V on phase transformation of high carbon steel during continuous cooling // Acta Metallurgica Sinica. 2010. V. 46(12). P. 1502–1510.
Hu X.J., Zhao Y.F., Wang L. Effect of Vanadium on the Microstructure and Properties of High Carbon Steel Wires // Iron&Steel. 2014. V. 49(12). P. 71–75.
Zhao B.C., Zhao T., Li G.Y., Liu Q. Effect of Thermal Deformation on Continuous Cooling Transformation Behaviors of V–N Microalloyed Steel // Iron Steel vanadium titanium. 2014. V. 35(2). P. 113–117.
Mottishaw T.D., Smith G.D.W. HSLA Steels-Technology and Appliacations / In: Korchynsky Med, Proc Conf HSLA Steels-Technology and Appliacations, OH:Metals Park press, 1984. P. 163.
Han K., Smith G.D.W., Edmonds D.V. Pearlite phase transformation in Si and V steel // Metall. Mater. Trans. 1995. V. 26A. P. 1617.
Kaspar R. et al. Effect of deformation conditions on the transformation of micro-alloyed medium-carbon forging steels // Steel Research. 1992. V. 63. P. 324.
Zajac S., Lagneborg R., Siwecki T. The Role of Nitrogen in Microalloyed Steels // Proc. of Int. Conf. Microalloying ’95, ISS, Warrendale, PA, (1995), 321.
Sharma R.C., Lakshmanan V.K., Kirkaldy J.S. Solubility of Niobium Carbide and Niobium Carbonitride in Alloyed Austenite and Ferrite // J. Metal. Trans. A. 1984. V. 15A(3). P. 545–553.
Enomoto M., Nojiri N., Sato Y. Effects of Vanadium and Niobium on the Nucleation Kinetics of Proeutectoid Ferrite at Austenite Grain Boundaries in Fe–C and Fe–C–Mn Alloys // Mater. Trans.JIM. 1994. V. 35(12). P. 859.
Ishikawa F., Takahashi T., Ochi T. Intragranular ferrite nucleation in medium-carbon vanadium steel // Metall. Trans. A. 1994. V. 25A. P. 929.
Ochi T, Takahashi T, Takada H. Iron and steelmaker, Improvement of the Toughness of Hot Forged Products through Intragranular Ferrite Formation // Iron and steelmaker. 1989. Feb. 21.
Van L.Y., Sietsma J. and Van D.Z.S. The Influence of Carbon Diffusion on the Character of the γ-α Phase Transformation in Steel // ISIJ Int. 2003. V. 43(5). P. 767.
Dobuzhskaya A.B., Kolosova E.L., Syreyshchikova V.I. influence of microalloying with carbonitride-forming elements on the structure and properties of rail steel // Phys. Met. 1990. T. 70. № 3. C. 121–128.
Wang K., Wang L.J., Cui W.F. Effect of cerium sulphide particle dispersions on acicular ferrite microstructure development in steels // J. Mater. Sci. Technol. 2006. V. 22(2). P. 159–163.
He K. and Edmonds D.V. Formation of acicular ferrite and influence of vanadium alloying // Mater. Sci. Technol. 2002. V. 18. P. 289.
Дополнительные материалы отсутствуют.
Инструменты
Физика металлов и металловедение