Физика металлов и металловедение, 2019, T. 120, № 12, стр. 1257-1263
Влияние температуры изотермической осадки на структуру и свойства сплава Cu–14 мас. % Al–4 мас. % Ni с эффектом памяти формы
А. Э. Свирид a, **, А. В. Лукьянов b, c, В. Г. Пушин a, d, *, Е. С. Белослудцева a, Н. Н. Куранова a, d, А. В. Пушин a, d
a Институт физики металлов им. М.Н. Михеева УрО РАН
620108 Екатеринбург, ул. С. Ковалевской, 18, Россия
b Санкт-Петербургский государственный университет
198504 Петергоф, Санкт-Петербург, ул. Ульяновская, 3, Россия
c Уфимский государственный нефтяной технический университет
450062 Уфа, ул. Космонавтов, 1, Россия
d Уральский федеральный университет им. первого Президента России Б.Н. Ельцина
620002 Екатеринбург, ул. Мира, 19, Россия
** E-mail: svirid2491@rambler.ru
* E-mail: pushin@imp.uran.ru
Поступила в редакцию 13.04.2019
После доработки 15.05.2019
Принята к публикации 23.05.2019
Аннотация
Впервые изучены структурно-фазовые особенности и механические свойства в широком интервале температур сплава Сu–14 мас. % Al–4 мас. % Ni, испытывающего термоупругие мартенситные превращения и связанные с ними эффекты памяти формы. Исследования выполнены методами растровой и просвечивающей электронной микроскопии и рентгенофазового анализа. При измерении механических свойств в изотермических условиях была применена схема одноосной деформации сжатием.
ВВЕДЕНИЕ
Сплавы на основе систем Ti–Ni, Cu–Al и ряда других относятся к особому классу материалов c эффектом памяти формы (ЭПФ), обусловленными термоупругими мартенситными превращениями (ТМП) [1, 2]. Проблема повышения служебных характеристик устройств, изготовленных из сплавов с ЭПФ, всегда остается актуальной. Это особенно важно в медицине, авиации, космической технике, где необходима повышенная надежность изделий при эксплуатации в достаточно широком интервале температур подчас при их минимальных или, напротив, больших размерах и сечениях [1–4].
Однако, при всем разнообразии созданных к настоящему времени материалов с ЭПФ даже среди сплавов никелида титана с рекордным комплексом физико-механических свойств детально исследованы и широко используются только их бинарные композиции в узком диапазоне легирования никелем (от 49.5 до 50.5 ат. %) [3]. Вместе с тем, медные сплавы систем Cu–Al, Cu–Al–Ni, Cu–Zn–Al характеризуются лучшими тепло- и электропроводностью, технологичностью при изготовлении, меньшей стоимостью по сравнению с никелидом титана. Более того, в монокристаллическом состоянии они имеют превосходные характеристики ЭПФ [1–4]. Но, предназначенные для практического применения объемные сплавы с ЭПФ необходимы в традиционном поликристаллическом состоянии после достаточно простых термических или термомеханических обработок, которые, как правило, не могут обеспечить требуемые физико-механические и эксплуатационные параметры [4]. Так, большинство цветных сплавов с ЭПФ, включая и β-сплавы на основе меди, в поликристаллическом состоянии имеют в отличие от никелида титана низкие пластичность, циклическую прочность и долговечность, что не позволяет реализовать присущие им ЭПФ [1–4].
Одной из причин хрупкости медных сплавов является высокая анизотропия упругих модулей, которая в метастабильных по отношению к ТМП медных сплавах A = C44/C' близка 12–13 [2, 5], тогда как для упругоизотропных и пластичных сплавов никелида титана A составляет 1–2 [2–6]. К очевидным причинам охрупчивания сплавов на основе меди, в том числе и с ТМП, относятся также высокая локализация на границах зерен примесей и выделений избыточных фаз, и, как правило, их крупно- и разнозернистость [1, 7]. Если в сплавах при ТМП реализуются высокоанизотропные упругие объемные и сдвиговые напряжения, они концентрируются, прежде всего, на границах зерен, дополнительно ослабляя их.
Как известно, за счет измельчения зеренной структуры (и, соответственно, увеличения протяженности границ зерен) можно существенно повысить прочностные и пластические свойства сплавов никелида титана [8, 9]. Для измельчения зеренной структуры в медных сплавах пытались использовать различные способы обработки: термическую обработку и ковку [7, 10], термоциклирование под нагрузкой [11], непрерывную быструю разливку расплава [12]. Легирование сплавов Cu–Al–Ni, например, Ti или Mn, в оптимальных количествах также приводит к некоторому измельчению зерен [13].
Весьма эффективным способом измельчения зеренной структуры сплавов с ЭПФ на основе никелида титана до мелко- (МЗ) и ультрамелкозернистых (УМЗ) состояний является интенсивная пластическая деформация методами: кручения под высоким давлением (КВД) и равноканального углового прессования [14–21].
Контролируемая теплая деформация также может обеспечить накопление в сплавах высокой степени деформации и формирование МЗ и УМЗ структур. При этом основной задачей, особенно для медных сплавов, становится поиск и исследование режимов деформирования, обеспечивающих способность материала к пластическому течению без заметного роста размеров зерна, охрупчивания или разупрочнения при заданных температурно-скоростных условиях. В результате могут быть установлены оптимальные способы получения и обработки медных сплавов с ЭПФ, предназначенных для практического применения, с повышенными механическими и функциональными свойствами. В настоящей работе с данной целью был впервые использован для сплава Cu–Al–Ni с ТМП и ЭПФ метод теплой контролируемой осадки.
МАТЕРИАЛЫ И МЕТОДЫ ИССЛЕДОВАНИЯ
Трехкомпонентный сплав Cu–13.95 мас. % Al–3.98 мас. % Ni (Cu–14Al–4Ni) был получен из высокочистых Cu, Al, Ni (99.99%) компонентов. Слиток гомогенизировали при 900 ± 25°С, затем после нагрева до 950°С проковали в пруток сечением 20 × 20 мм. Закалку сплава проводили после повторного нагрева при 950°С, 10 мин, в воде при комнатной температуре.
Для пластической деформации сплава одноосным сжатием использовали электромеханическую измерительную систему Instron 8862, оснащенную электропечью для проведения измерений в изотермических условиях при температурах вплоть до 900°С в Центре коллективного пользования (ЦКП) Уфимского государственного авиационного технического университета. Испытания проводили на цилиндрических образцах сплава диаметром (d0) 7.5 мм и высотой (h0) 9.2 мм (согласно ГОСТ 25.503-80). Скорость испытаний v составляла 1 мм/мин.
На исходном крупнозернистом (с размерами зерен до 1 мм) и полученных в результате осадки образцах был аттестован химический состав с помощью спектрального анализа, фазовый состав определяли рентгенодифрактометрическим методом. Микроструктурные исследования выполняли методами оптической микроскопии, растровой электронной микроскопии (РЭМ) на микроскопе Quanta-200 при 30 кВ и просвечивающей электронной микроскопии (ПЭМ) на микроскопах Tecnai G2 30 и Philips CM 30 при ускоряющем напряжении 300 кВ, которыми оборудован отдел электронной микроскопии ЦКП ИФМ УрО РАН.
РЕЗУЛЬТАТЫ И ИХ ОБСУЖДЕНИЕ
По данным механических испытаний осадкой при комнатной температуре сплав Cu–14Al–4Ni в исходном состоянии способен испытывать достаточно большую пластическую деформацию до разрушения ε = 22% при высоких напряжениях предела текучести σ0.2 и временного сопротивления σВ, близких 400 и 1150 МПа, соответственно (рис. 1а). Кривая “напряжение–деформация” имела классический вид, на ней можно выделить четыре основные стадии деформации, различающиеся механизмами и коэффициентами деформационного упрочнения: 1 стадию упругой деформации; 2 и 3 стадии деформационного упрочнения, отличающиеся коэффициентами упрочнения; 4 стадию локализации деформации, завершающейся разрушением. На вставке к рис. 1 для сравнения приведена также кривая “напряжение–деформация”, полученная на данном сплаве при одноосном растяжении при комнатной температуре. Из сопоставления полученных результатов следует, что при близких значениях коэффициента деформационного упрочнения θ = dσ/dε (~3.5 и 4.5 ГПа, соответственно при сжатии и растяжении) относительное удлинение сплава до разрушения при растяжении равно 4%, что более чем в 5 раз меньше величины относительного сжатия до разрушения ε ≈ 22%.
Рис. 1.
Инженерные кривые “напряжение σ–деформация ε” сплава Cu–14Al–4Ni, полученные при механических испытаниях на сжатие, v = 1 мм/мин (на вставке – на одноосное растяжение): а – при комнатной температуре; б – при 400 (1); 500 (2); 600 (3); 700 (4); 800°C (5).
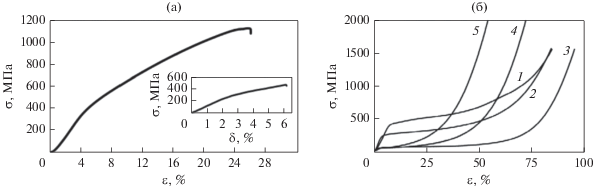
На рис. 2а, 2б представлены РЭМ-изображения микроструктуры сплава после испытаний при 20°С на растяжение и на сжатие. Видно, что сжатие обеспечивает изменение морфологии и существенное измельчение кристаллов мартенсита: на фоне доминирующей пакетной морфологии практически не наблюдаются фермообразные сочленения, а размеры как индивидуальных кристаллов мартенсита, так и их пакетов существенно уменьшаются.
Рис. 2.
РЭМ-изображения во вторичных электронах микроструктуры сплава Cu–14Al–4Ni после механических испытаний на одноосное растяжение (а) и сжатие (б) при 20°С.
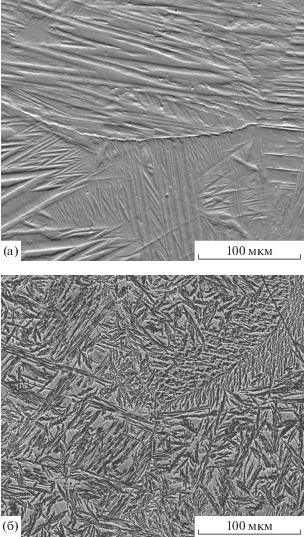
Типичные изображения поверхности разрушения, полученные при фрактографическом анализе образцов после растяжения или сжатия при 20°С, приведены на рис. 3а–3г. Из РЭМ-изображений следует, что хрупкое и вязко-хрупкое межзеренное и внутризеренное разрушение сплава в мартенситном состоянии при растяжении происходило преимущественно по границам пакетов двойниково ориентированных кристаллов мартенсита. При сжатии чаще формируются участки с мелкоямочным вязким изломом, свидетельствуя о повышенной деформируемости сплава с преобладанием вязкого механизма разрушения.
Рис. 3.
РЭМ-изображения поверхности разрушения образцов сплава Cu–14Al–4Ni после механических испытаний на одноосное растяжение (а, б) и сжатие (в, г).
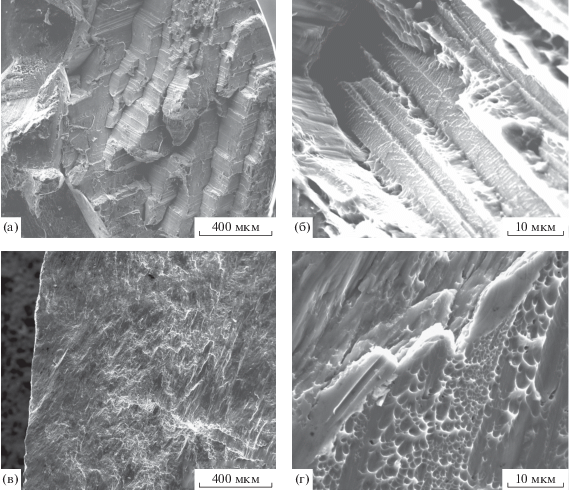
В дальнейшем выполняли механические испытания осадкой при температурах в интервале 400–800°С с шагом 100°С. Поскольку температуры начала и конца обратного мартенситного превращения в сплаве существенно ниже 400°С, теплой деформации подвергался сплав в аустенитном состоянии. Измерения показали, что рост температуры испытаний приводит, во-первых, к изменению стадийности пластической деформации по сравнению с испытаниями при комнатной температуре (рис. 1б). На всех измеренных инженерных кривых для атомно-упорядоченного аустенитного сплава можно наблюдать только три стадии деформации – упругой деформации (1), пластического течения с низким коэффициентом упрочнения (2) и стадию с резко возрастающим коэффициентом упрочнения (3). Во-вторых, повышение температуры деформации осадкой от комнатной температуры до 400°С при смене структуры сплава от мартенситной к аустенитной не привело к изменению величины σ0.2, сохранившейся на уровне 400 МПа при росте предела прочности σВ (см. табл. 1).
Таблица 1.
Механические свойства сплава Cu–14Al–4Ni при испытаниях на одноосное сжатие
T исп. | ε, % | σ0.2, МПа | σВ, МПа |
---|---|---|---|
20 | 22 | 400 | 1150 |
400 | 80 | 400 | 1560 |
500 | 79 | 230 | 1550 |
600 | 94 | 70 | 1540 |
700 | 72 | 50 | 2000 |
800 | 58 | 50 | 1980 |
Но дальнейшее увеличение температуры деформации от 400 до 600°С при той же скорости осадки вызвало прогрессирующее снижение σ0.2, по-видимому, в результате интенсификации возможных в сплаве динамических процессов возврата и рекристаллизации. Наиболее низкие значения σ0.2 наблюдались при высоких температурах деформации 700 и 800°С, σ0.2 = 50 МПа. Значения σВ, напротив, резко возросли вплоть до 2000 МПа. Достигаемая при сжатии величина деформации до разрушения при всех температурах испытаний была достаточно высокой, но максимум (94%) был получен при 600°С.
На рис. 4 приведена зависимость изменения величины σ0.2 от температуры осадки. Представленный график иллюстрирует, что величина σ0.2 с увеличением температуры сначала сохраняется на уровне 400 МПа (при температуре деформации 400°С), затем убывает в интервале 400–600°С и далее остается неизменной в интервале 600–800°С. Такое немонотонное поведение механических свойств может быть обусловлено наличием эвтектоидного распада в сплаве Cu–14Al–4Ni.
Рис. 4.
Зависимость изменения предела текучести σ0.2 от температуры деформации T при постоянной скорости осадки сплава Cu–14Al–4Ni.
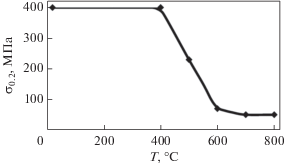
Согласно известным результатам [1–4, 7, 10], при деформации в интервале 400–600°С в данном сплаве может инициироваться эвтектоидный распад пересыщенного β-твердого раствора с формированием дисперсных избыточных фаз (β' + α + γ2), что, очевидно, будет обеспечивать упрочняющий эффект при деформации осадкой. Однако наблюдаемое при дальнейшем увеличении температуры деформации уже выше эвтектоидной температуры (в интервале 600–800°С) снижение σ0.2 и увеличение σВ сплава, по-видимому, связано только с деформационно-индуцированными процессами динамического возврата и рекристаллизации.
Для уточнения реальных изменений микроструктуры и фазового состава сплава в результате осадки были проведены РЭМ и ПЭМ-исследования и рентгенофазовый анализ. Оказалось, что после осадки при 400–600°С в сплаве сформировалась УМЗ-структура, по сравнению с исходной структурой на 2–3 порядка более дисперсная, с преобладающим размером зерен-кристаллитов 1–2 мкм (рис. 5, 6). Образование в процессе теплой осадки такой структуры, по-видимому, и обеспечило их высокую способность к развитой пластической деформации, предотвратив преждевременное разрушение.
Рис. 6.
ПЭМ (а – изображение УМЗ-структуры, на вставке – соответствующая картина микродифракции электронов) и РЭМ (б, в) – изображение УМЗ-структуры сплава после осадки при 600°С.
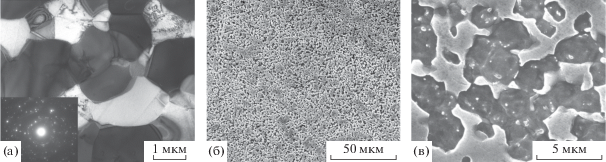
Деформация с постоянной скоростью при более высоких температурах (700–800°С), во-первых, интенсифицировала процесс динамической рекристаллизации в сплаве. На РЭМ-изображениях видны в несколько раз более дисперсные, чем в исходном крупнозернистом сплаве, равноосные мелкие зерна (МЗ) в основном размером 80–120 мкм (рис. 7), возникшие, очевидно, в результате динамической рекристаллизации. Деформация при 900°С, несколько ускорив рост зерен, привела, в целом, к аналогичным изменениям зеренной структуры (рис. 7в). Вместе с тем наблюдались и дисперсные выделения $\gamma _{{\text{2}}}^{'}$-фазы и ликвационная дендритная субструктура (рис. 7г).
Таким образом, в результате изотермической осадки при температурах, изменяющихся в широком диапазоне, в сплаве Cu–14Al–4Ni была сформирована УМЗ или МЗ структура с преобладающими размерами зерен вначале в пределах порядка единиц, затем ста микрометров. Наличие подобных ультра- и мелкозернистых структур, как известно, может привести к наблюдаемому необычному сочетанию умеренных или даже низких по величине σ0.2 и одновременно высоких σВ и пластичности.
ЗАКЛЮЧЕНИЕ
В настоящей работе были установлены основные закономерности структурно-фазовых превращений и формирования механических свойств сплава Cu–13.95 мас. % Al–3.98 мас. % Ni при контролируемой изотермической осадке в испытательной машине в интервале температур от комнатной до 900°С. Обнаружено, что в сплаве после термомеханической обработки, включающей гомогенизацию, горячую ковку и закалку, при последующем изотермическом одноосном сжатии происходит формирование мелко- или ультрамелкозернистой структуры аустенита, сопровождаемое высокой способностью к пластической деформации в процессе осадки при 400–800°С.
Холодная изотермическая осадка, не изменяя размеры зерен, приводит к образованию мелкокристаллической структуры пакетного мартенсита. Это также обеспечивает повышенные значения прочностных и одновременно пластических свойств сплава за счет эффективного перераспределения и адаптации по объему сплава в условиях сжатия упругих объемных и сдвиговых напряжений, обусловленных термоупругими мартенситными превращениями.
Разрушение крупнозернистого сплава в мартенситном состоянии при одноосном растяжении в основном происходит по границам дисперсных пакетов по квазихрупкому механизму. При сжатии, напротив, реализуется мелкоямочный вязкий внутризеренный механизм разрушения, что свидетельствует о повышенной пластичности сплава как в аустенитном, так и в мартенситном состояниях.
Работа выполнена по тематике госзадания № АААА-А18-118020190116-6 (“Структура”) и при поддержке проекта УрО РАН № 18-10-2-39.
Список литературы
Ооцука К., Симидзу К., Судзуки Ю., Сэкигути Ю., Тадаки Ц., Хомма Т., Миядзаки С. Сплавы с эффектом памяти формы. М.: Металлургия, 1990. 224 с.
Пушин В.Г., Кондратьев В.В., Хачин В.Н. Предпереходные явления и мартенситные превращения. Екатеринбург: УрО РАН, 1998. 368 с.
Otsuka K., Wayman C.M. Shape memory materials. Cambridge University Press, 1998. 284 p.
Материалы с эффектами памяти формы / Под ред. Лихачева В.А. в 4-х томах. СПб: НИИХ СПбГУ, 1997–1998.
Sedlak P., Seiner H., Landa M., Novák V., Šittner P., Manosa L.I. Elastic Constants of bcc Austenite and 2H Orthorhombic Martensite in CuAlNi Shape Memory Alloy // Acta Mater. 2005. V. 53. P. 3643–3661.
Хачин В.Н., Муслов С.А., Пушин В.Г., Чумляков Ю.И. Аномалии упругих свойств монокристаллов TiNi–TiFe // ДАН СССР. 1987. Т. 295. № 3. С. 606–609.
Лукьянов А.В., Пушин В.Г., Куранова Н.Н., Свирид А.Э., Уксусников А.Н., Устюгов Ю.М., Гундеров Д.В. Влияние термомеханической обработки на структурно-фазовые превращения в сплаве Cu–14Al–3Ni с эффектом памяти формы, подвергнутом кручению под высоким давлением // ФММ. 2018. Т. 119. № 4. С. 393–401.
Пушин В.Г., Лотков А.И., Колобов Ю.Р., Валиев Р.З., Дударев Е.Ф., Куранова Н.Н., Дюпин А.П., Гундеров Д.В., Бакач Г.П. О природе аномально высокой пластичности высокопрочных сплавов никелида титана с эффектами памяти формы. Исходная структура и механические свойства // ФММ. 2008. Т. 106. № 5. С. 537–547.
Дударев Е.Ф., Валиев Р.З., Колобов Ю.Р., Лотков А.И., Пушин В.Г., Бакач Г.П., Гундеров Д.В., Дюпин А.П., Куранова Н.Н. О природе аномально высокой пластичности высокопрочных сплавов никелида титана с эффектами памяти формы. Особенности механизмов пластической деформации при изотермическом нагружении // ФММ. 2009. Т. 107. № 3. С. 316–330.
Свирид А.Э., Куранова Н.Н., Лукьянов А.В., Макаров В.В., Николаева Н.В., Пушин В.Г., Уксусников А.Н. Влияние термомеханической обработки на структурно-фазовые превращения и механические свойства сплавов Cu–Al–Ni с памятью формы // Известия вузов. Физика. 2018. Т. 61. № 9. С. 114–119.
Matlakova L.A., Pereira E.C., Matlakov A.N., Monteiro S.N., Toledo R. Mechanical behavior and fracture characterization of a monocrystalline Cu–Al–Ni subjected to thermal cycling treatments under load // Mater. Characterization. 2008. V. 59. P. 1630–1637.
Wang Z., Liu X.F., Xie J.X. Effect of solidification parameters on microstructure and mechanical properties of continious columnar-grained Cu–Al–Ni alloy // Mater. Sci. Eng.: A. 2012. V. 532. P. 536–542.
Saud S.N., Hamzah E., Abubakar T., Bakhsheshirad H.R. Correlation of microstructural and corrosion characteristics of quaternary shape memory alloys Cu–Al–Ni–X (X = Mn or Ti) // Trans. Nonferrous Met. Soc. China. 2015. V. 25. P. 1158–1170.
Pushin V.G., Stolyarov V.V., Valiev R.Z., Kourov N.I., Kuranova N.N., Prokofiev E.A., Yurchenko L.I. Features of structure and phase transformations in shape memory TiNi-based alloys after severe plastic deformation // Ann. Chim. Sci. Mat. 2002. V. 27. № 3. P. 77–88.
Pushin V.G., Stolyarov V.V., Valiev R.Z., Kourov N.I., Kuranova N.N., Prokofiev E.A., Yurchenko L.I. Development of methods of severe plastic deformation for the production of high-strength alloys based on titanium nickelide with a shape memory effect // Phys. Met. Metallography. 2002. V. 94. Suppl 1. P. S54–S68.
Pushin V.G., Stolyarov V.V., Valiev R.Z., Lowe T.C., Zhu Y.T. Nanostructured TiNi-based shape memory alloys processed by severe plastic deformation // Materials Science and Engineering: A. 2005. V. 410. P. 386–389.
Valiev R., Gunderov D., Prokofiev E., Pushin V., Zhu Yu. Nanostructuring of TiNi alloy by SPD processing for advanced properties // Materials Transaction. 2008. V. 49. № 1. P. 97–101.
Гундеров Д.В., Куранова Н.Н., Лукьянов А.В., Уксусников А.Н., Прокофьев Е.А., Юрченко Л.И., Валиев Р.З., Пушин В.Г. Применение интенсивной пластической деформации кручением для формирования аморфного и нанокристаллического состояния в большеразмерных образцах сплава TiNi // ФММ. 2009. Т. 108. № 2. С. 139–146.
Куранова Н.Н., Гундеров Д.В., Уксусников А.Н., Лукьянов А.В., Юрченко Л.И., Прокофьев Е.А., Пушин В.Г., Валиев Р.З. Влияние термообработки на структурные и фазовые превращения и механические свойства сплава TiNi, подвергнутого интенсивной пластической деформации кручением // ФММ. 2009. Т. 108. № 6. С. 589–601.
Пушин В.Г., Валиев Р.З., Валиев Э.З., Коуров Н.И., Куранова Н.Н., Макаров В.В., Пушин А.В., Уксусников А.Н. Фазовые и структурные превращения в сплаве с эффектом памяти формы Ti49.5Ni50.5, подвергнутом кручению под высоким давлением // ФММ. 2012. Т. 113. № 3. С. 271–285.
Valiev R.Z., Gunderov D.V., Lukyanov A.V., Pushin V.G. Mechanical behavior of nanocrystalline TiNi alloy produced by SPD // J. Mater. Sci. 2012. V. 47. № 22. P. 7848–7853.
Дополнительные материалы отсутствуют.
Инструменты
Физика металлов и металловедение