Физика металлов и металловедение, 2020, T. 121, № 12, стр. 1315-1323
Обоснование концентрации меди в термостойких деформируемых алюминиевых сплавах, содержащих 2 мас. % Mn
Н. А. Белов a, Н. О. Короткова a, *, П. К. Шуркин a, А. А. Аксенов a
a НИТУ “МИСиС”
119049 Москва, Ленинский просп., 4, Россия
* E-mail: kruglova.natalie@gmail.com
Поступила в редакцию 10.07.2020
После доработки 28.07.2020
Принята к публикации 04.08.2020
Аннотация
С использованием экспериментальных и расчетных методов изучено влияние температуры отжига на удельное электросопротивление, твердость и структуру сплавов системы Al–Cu–Mn, содержащих 2 мас. % Mn и до 3 мас. % Cu, в литом и холоднокатаном состоянии. Показано, что наилучшей комплекс механических свойств достигается в холоднокатаных листах, содержащих 2–3 мас. % Cu и отожженных при 400°С, что обусловлено формированием в их структуре дисперсоидов фазы Al20Cu2Mn3 в количестве более 9 об. % со средним размером менее 100 нм. Такая структура обеспечивает более высокую термостойкость по сравнению с марочным сплавом 1201 (аналогичной системы легирования 0.32 Mn, 5.86 Cu, 0.07 Fe, 0.08 Si, 0.08 Zr мас. %), упрочняемым за счет закалки и старения.
ВВЕДЕНИЕ
В настоящее время имеется острая потребность в алюминиевых сплавах с повышенной прочностью и термостойкостью [1, 2]. Среди стандартных деформируемых сплавов наиболее сбалансированными прочностными свойствами при комнатной и повышенных температурах обладают алюминиевые сплавы 2xxx серии, легированные медью, в частности типа 1201 (АА2219) [3]. Однако рабочие температуры деформированных полуфабрикатов из этих сплавов не превышают ~250°С, и значительно повысить этот уровень в рамках традиционного легирования вряд ли возможно. Это обусловлено процессами перестаривания (в частности, укрупнением вторичных выделений фазы θ-Al2Cu) при нагреве выше данной температуры [4, 5]. Особо следует отметить, что достижение оптимального уровня свойств марочных алюминиевых сплавов сопряжено с необходимостью проведения операций гомогенизации для слитков и закалки для деформированных полуфабрикатов. Это приводит к снижению производительности, повышенному энергопотреблению, а также к необходимости иметь специализированное оборудование. Радикальным способом устранения выше рассмотренных недостатков марочных сплавов 2ххх серии является разработка принципиально новых по составу деформированных термостойких алюминиевых сплавов, технология получения которых не требует операций гомогенизации и закалки.
В работах [6–8] на примере сплавов системы Al–Mn–Cu (Zr,Sc), содержащих около 1.5 мас. % Mn показано, что при добавлении меди в количестве до 2 мас. % большая ее часть растворяется в твердом растворе (Al). Это позволяет подвергать деформационной обработке слитки таких сплавов без использования гомогенизации, которая необходима для промышленных алюминиево-медных сплавов [4]. Для формирования Mn-содержащих дисперсоидов (Al6Mn, Al20Cu2Mn3 и Al15Mn2Si3) размером не более 100 нм требуется отжиг при температуре не выше 450°С, что существенно ниже температуры гомогенизации сплавов 2ххх серии [6, 9]. В работах [10, 11] на примере сплавов системы Al–Mn–Cu–Be было показано, что снижение температуры отжига позволяет получить вторичные выделения квазикристаллов размером менее 50 нм.
Mn-содержащие дисперсоиды, обладающие повышенной термостабильностью по сравнению с основными фазами упрочнителями в сплавах 2ххх серии (в частности, θ' и θ"), позволяют сохранить в деформированных полуфабрикатах нерекристаллизованную структуру при нагревах вплоть до 400°С [8, 12, 13].
В работе [8] на примере холоднокатаных листов показано, что добавка к сплаву Al–1.5 мас. % Mn такого же количества меди приводит к одновременному повышению электропроводности-и твердости. Такой эффект обусловлен ускорением распада (Al) и формированием вторичных дисперсоидов Al20Cu2Mn3 вместо фазы Al6Mn, имеющей более крупные размеры. Дальнейшее повышение прочности по сравнению с характеристикой сплава Al–1.5% Mn–1.5% Cu требует увеличения в структуре количества дисперсоидов Al20Cu2Mn3, что может быть достигнуто за счет увеличения концентраций меди и марганца в сплаве. При этом есть необходимость сохранения деформационной технологичности литых слитков. Именно на это и была направлена данная работа, объектом исследования которой были модельные сплавы системы Al–Cu–Mn, содержащие 2 мас. % Mn и до 3 мас. % Cu.
МЕТОДИКА ЭКСПЕРИМЕНТА
Объектами исследования были слитки и холоднокатаные листы 6-ти модельных сплавов системы Al–Cu–Mn, содержащих 2 мас. % Mn (по шихте) и различное количество меди (до 3 мас. %). Объектом сравнения был сплав, имеющий средний состав марочного сплава 1201/АА2219 (ГОСТ4784–2019).
Модельные сплавы готовили на основе алюминия марки А99 (ГОСТ 11069–2001). Медь марки М1 (ГОСТ 859–2001) вводили в чистом виде, а марганец в виде лигатуры Al–10% Mn (ГОСТ 53777–2010). Плавку проводили в электрической печи сопротивления (GRAFICARBO) в графитном тигле при 740–760°С. Плоские слитки с размерами 10 × 40 × 180 мм получали литьем в графитовую изложницу (скорость охлаждения составляла около 15 К/с). Фактический химический состав экспериментальных сплавов приведен в табл. 1. Нижние половины слитков подвергали холодной прокатке на вальцах ВЭМ 3 М до толщины 2 мм (степень обжатия – 80%). Для оценки технологичности и возможности дальнейшего упрочнения 2-х мм листы докатывали до толщины 0.5 мм (суммарная степень обжатия – 95%).
Таблица 1.
Химический состав экспериментальных сплавов по данным спектрального анализа
Обозначение сплава | Концентрация, мас. % | |||||
---|---|---|---|---|---|---|
Mn | Cu | Fe | Si | Zr | Al | |
0Cu | 1.72 ± 0.04 | 0.03 ± 0.04 | 0.04 ± 0.03 | 0.00 ± 0.03 | – | Основа |
0.5Cu | 1.73 ± 0.04 | 0.61 ± 0.05 | 0.05 ± 0.04 | 0.01 ± 0.03 | – | |
1Cu | 1.84 ± 0.04 | 1.15 ± 0.05 | 0.04 ± 0.03 | 0.01 ± 0.03 | – | |
1.5 Cu | 1.79 ± 0.03 | 1.66 ± 0.06 | 0.03 ± 0.03 | 0.00 ± 0.02 | – | |
2Cu | 1.75 ± 0.03 | 1.97 ± 0.06 | 0.02 ± 0.03 | 0.00 ± 0.02 | – | |
3Cu | 1.73 ± 0.03 | 2.82 ± 0.06 | 0.02 ± 0.03 | 0.00 ± 0.02 | – | |
1201 | 0.32 ± 0.03 | 5.86 ± 0.08 | 0.07 ± 0.03 | 0.08 ± 0.03 | 0.08 ± 0.02 |
Отжиг литых и холоднокатаных образцов проводили по многоступенчатым режимам в муфельной печи SNOL 8.2/1100 в интервале температур от 200 до 600°С с 3-часовой выдержкой на каждой ступени (табл. 2). После каждого режима отжига на литых и деформированных (толщиной 2 мм) образцах измеряли удельную электрическую проводимость (УЭП) и твердость (НV). Значения УЭП определяли методом вихревых токов на приборе ВЭ-26НП, в качестве эталона выступал чистый алюминий (А99). Значения удельного электросопротивления (УЭС) рассчитывали, как величину обратную УЭП. Твердость по Виккерсу определяли на твердомере DUROLINE MH-6 при нагрузке 1 кгс, и времени выдержки 10 с. Механические свойства экспериментальных сплавов оценивали методом испытаний на растяжение образцов из тонких листов (0.5 мм) на универсальной машине Zwick/Z 250 по методике ГОСТ 11701–84.
Таблица 2.
Режимы отжига модельных сплавов
Обозначение режима отжига слитков (F) и холоднокатаных листов (СR) | Режим отжига |
---|---|
F200/CR200 | 200°C, 3 ч |
F250/CR250 | F200/CR200 + 250°C, 3 ч |
F300/CR300 | F250/CR250 + 300°C, 3 ч |
F350/CR350 | F300/CR300 + 350°C, 3 ч |
F400/CR400 | F350/CR350 + 400°C, 3 ч |
F450/CR450 | F400/CR400 + 450°C, 3 ч |
F500/CR500 | F450/CR450 + 500°C, 3 ч |
F550/CR550 | F500/CR500 + 550°C, 3 ч |
F600/CR600 | F550/CR550 + 600°C, 3 ч |
Микроструктуру литых и деформированных сплавов изучали на световом (СМ) микроскопе Axio Observer MAT и электронном сканирующем (СЭМ) микроскопе TESCAN VEGA 3, укомплектованном энергодисперсионной приставкой-микроанализатором OXFORD Instruments (МРСА). Изучение структуры методом просвечивающей электронной микроскопии (ПЭМ) проводили на приборе JEM2100, используя в качестве образцов фольги.
Анализ фазового состава расчетными методами проводили с помощью программы “Thermo-Calc” (термодинамическая база TTAL5).
ЭКСПЕРИМЕНТАЛЬНЫЕ РЕЗУЛЬТАТЫ И ИХ ОБСУЖДЕНИЕ
Состав экспериментальных сплавов выбран из условия вхождения всего количества марганца при кристаллизации в состав алюминиевого раствора (далее – (Al)). Это условие для литого сплава, содержащего 2% Mn, обеспечивалось технологическими параметрами получения заготовок [6–8]. Медь в отличие от марганца не может быть полностью растворена в (Al) в литом состоянии – при неравновесной кристаллизации неизбежно образование эвтектических частиц фазы Al2Cu [13, 14]. В связи с этим задача состояла в обеспечении достаточной концентрации меди в (Al) для формирования при отжиге дисперсоидов Al20Cu2Mn3 и компактной морфологии частиц Al2Cu. Последнее требование позволяет обеспечить достаточно высокую пластичность литых сплавов при холодной прокатке. При содержании меди более 3% эвтектические включения имеют вид прожилок (неблагоприятная морфология) [6, 7], поэтому верхний предел для экспериментальных сплавов был ограничен именно этой концентрацией.
Из изотермического разреза диаграммы состояния системы Al–Cu–Mn при 400°С (рис. 1а) видно, что составы модельных сплавов попадают в различные фазовые области. Если двойной сплав содержит кроме (Al) только фазу Al6Mn, то сплавы с 0.5, 1 и 1.5% Cu содержат кроме этой фазы тройное соединение. Сплав с 2% Cu попадает в двухфазную область (Al) + Al20Cu2Mn3, а сплав с 3% Cu в трехфазную: (Al) + Al20Cu2Mn3 + Al2Cu. При 500 и 600°С наличие фазы Al2Cu в экспериментальных сплавах невозможно (рис. 1б, 1в). Рост содержания меди в сплаве (рис. 1) изменяет также и состав (Al): концентрация Cu увеличивается, а Mn, наоборот, снижается.
Рис. 1.
Изотермические сечения системы Al–Cu–Mn и составы экспериментальных сплавов: (а) при 400°С, (б) при 500°С, (в) при 600°С; где Al6–Al6Mn, Al20–Al2Cu2Mn3, остальные наименования фаз приведены без сокращений.
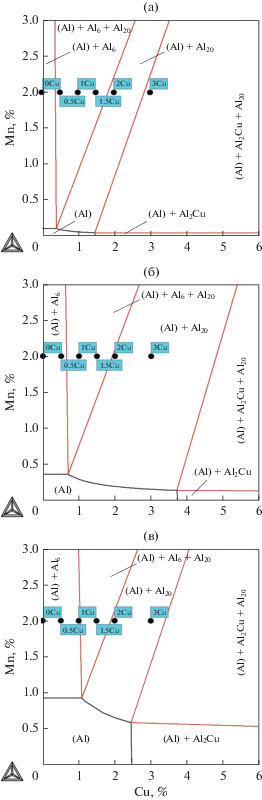
Поскольку для формирования максимального количества дисперсоидов Al20Cu2Mn3 концентрация Mn в (Al) должна быть минимальной, то концентрация 3% Cu и температура отжига 400°С представляются наилучшим сочетанием. Расчетные параметры фазового состава сплавов системы Al–Cu–Mn, содержащих 2% Mn, при различных температурах (табл. 3) показывают, что данное сочетание состава и температуры позволяет сформировать около 10 об. % фазы Al20Cu2Mn3. С ростом температуры равновесные концентрации марганца и меди в (Al) увеличиваются, а количество Mn-содержащих фаз уменьшается.
Таблица 3.
Расчетные параметры фазового состава сплавов системы Al–Cu–Mn, содержащих 2% Mn, при различных температурах
T, °C | Сплав | Доли фаз, об. % | Концентрации в (Al), мас. % | |||
---|---|---|---|---|---|---|
Al6Mn | Al20Cu2Mn3 | Al2Cu | Mn | Cu | ||
400 | 0Cu | 7.50 | – | – | 0.11 | – |
0.5Cu | 6.87 | 0.83 | – | 0.11 | 0.40 | |
1Cu | 4.29 | 4.13 | – | 0.11 | 0.40 | |
1.5Cu | 1.71 | 7.42 | – | 0.11 | 0.40 | |
2Cu | – | 9.71 | – | 0.08 | 0.57 | |
3Cu | – | 9.88 | 0.32 | 0.05 | 1.47 | |
500 | 0Cu | 6.55 | – | – | 0.36 | – |
0.5Cu | 6.57 | – | – | 0.36 | 0.53 | |
1Cu | 4.83 | 2.24 | – | 0.36 | 0.70 | |
1.5Cu | 2.24 | 5.56 | – | 0.36 | 0.70 | |
2Cu | – | 8.59 | – | 0.34 | 0.77 | |
3Cu | – | 9.13 | – | 0.21 | 1.77 | |
600 | 0Cu | 4.40 | – | – | 0.93 | – |
0.5Cu | 4.41 | – | – | 0.92 | 0.52 | |
1Cu | 4.43 | – | – | 0.92 | 1.04 | |
1.5Cu | 2.05 | 3.06 | – | 0.92 | 1.09 | |
2Cu | – | 5.90 | – | 0.88 | 1.17 | |
3Cu | – | 7.09 | – | 0.64 | 2.06 |
Анализ микроструктуры показал, что сплав 0Cu, имеет однофазную структуру. Согласно данным МРСА (табл. 4), марганец практически полностью вошел в состав (Al) во всех 6-ти модельных сплавах. В тройных сплавах выявляются равномерно распределенные частицы фазы Al2Cu, количество которых увеличивается с ростом содержания меди (рис. 2). При содержании последней до 1.5% эти частицы имеют глобулярную форму (рис. 2а, 2б), что наиболее благоприятно для деформационной обработки.
Таблица 4.
Состав алюминиевого твердого раствора экспериментальных сплавов в литом состоянии
Сплав | Mn, мас. % | Cu, мас. % |
---|---|---|
0Cu | 1.65 ± 0.12 | 0.05 ± 0.13 |
0.5Cu | 1.62 ± 0.12 | 0.31 ± 0.15 |
1Cu | 1.63 ± 0.12 | 0.38 ± 0.14 |
1.5Cu | 1.67 ± 0.12 | 0.62 ± 0.15 |
2Cu | 1.54 ± 0.12 | 0.61 ± 0.15 |
3Cu | 1.59 ± 0.12 | 0.88 ± 0.16 |
Литая структура сплава 2Cu характеризуется прожилками длиной до 20 мкм (рис. 2в), часть из которых представляет собой двухфазные эвтектические колонии. Сплав 3Cu имеет качественно аналогичную структуру с большим количеством прожилок (рис. 2г). Следует отметить, что и в этих наиболее легированных сплавах большинство эвтектических частиц имеет компактную форму.
Наибольшее содержание меди в (Al) по данным МРСА (табл. 4) достигается в сплаве 3Cu – около 1%. Ликвация марганца в литой структуре невелика, а меди значительна – ее концентрация повышена на границах дендритных ячеек.
Холодная прокатка слитков показала высокую технологичность при обработке давлением всех модельных сплавов. Сплавы, содержащие до 1.5% Cu, с исходной глобулярной морфологией частиц фазы Al2Cu сохранили такую форму частиц и после прокатки (рис. 3а). В более легированных сплавах морфология этих включений существенно улучшилась (рис. 3б, 3в) за счет фрагментации прожилок (рис. 2в, 2г).
Литая структура, имеющая сильно пересыщенный (Al), является неравновесной, и фазовый состав модельных сплавов закономерно отличается от расчетного.
Формирование равновесного фазового состава требует достаточной диффузии марганца и меди, зависящей от температуры [14]. Также отжиг, особенно при температурах до ~400°С, предполагает достаточно сложные структурные изменения. Это связано с протеканием процессов распада пересыщенного (Al) с образованием Mn-содержащих диспероидов, растворения эвтектических частиц фазы Al2Cu, уменьшения внутридендритной ликвации. Согласно данным [10] при 400°С диффузионный путь (“The root-mean-square (RMS) diffusion distances”) меди за 24 ч равен 25 мкм, что можно считать достаточным для растворения неравновесных частиц фазы Al2Cu, размер которых не превышает данную величину (рис. 2). Диффузионный путь марганца при этой температуре существенно ниже (0.42 мкм), но и он превышает средний размер дисперсоидов [15, 16]. При 500°С и, тем более, при 600°С, диффузия Cu и Mn резко ускоряется, что должно уменьшать время, необходимое для формирования равновесного фазового состава в экспериментальных сплавах согласно рис. 1.
Максимальная твердость (~130 HV) достигается в листах толщиной 0.5 мм сплава 3Cu, что более, чем в 2 раза превосходит твердость исходного литого сплава. УЭС всех модельных сплавов достаточно велико, что также подтверждает наличие Mn в (Al). При этом УЭС и литых, и прокатанных сплавов, с ростом содержания меди растет незначительно (рис. 4а), вследствие ее меньшего количества в составе (Al), чем Mn [17]. Отжиг влияет на структуру, фазовый состав литых и прокатанных сплавов, а также на их свойства, в частности на электросопротивление, чувствительное к изменению состава (Al). [17–19]. До 300°С отжиг практически не меняет УЭС как литых (рис. 4а), так и холоднокатаных сплавов (рис. 4б), что означает незначительный распад (Al). Дальнейшее повышение температуры вызывает сильное снижение УЭС, более заметное в сплавах с медью. В слитках минимальное значение УЭС для сплава 0Cu достигается при 550°С (состояние F550), а для сплавов с медью при 500°С (F500), в листах – при 450°С (CR450) и 400°С (CR400), соответственно. В деформированных сплавах минимальные значения УЭС заметно ниже, чем в литых, что обусловлено ускоренным распадом (Al) и формированием Mn-содержащих дисперсоидов (рис. 5) в условиях сильной деформации (т.е. высокой плотности дислокаций) [17, 20]. Разница значений УЭС между сплавами уменьшается с ростом температуры и при 600°С она практически исчезает. Это можно объяснить почти одинаковым содержанием Mn в (Al) (табл. 3).
Рис. 4.
Влияние температуры отжига на удельное электросопротивление (а, б) и твердость (в) экспериментальных сплавов: (а) слитки (F), (б, в) холоднокатаные листы 2 мм (CR).
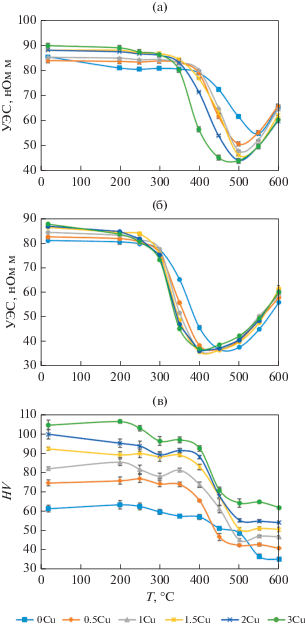
Рис. 5.
Дисперсоиды фаз Al6Mn (а) и Al20Cu2Mn3 (б–г) в холоднокатаных листах сплавов 0Cu (а), 2Cu (б, г) и 3Cu (в) после отжига при 500°С (а–в) и 400°С (г): (а–в) СЭМ; (г) ПЭМ.
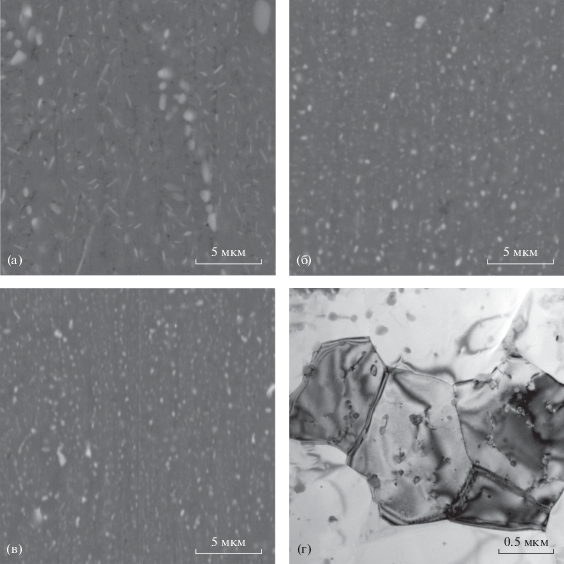
Влияние режимов отжига на твердость литых сплавов незначительно, несмотря на распад (Al). Это означает примерное равенство упрочняющих эффектов от твердорастворного легирования и дисперсоидов. Температурные зависимости твердости холоднокатаных сплавов (рис. 4в) выявляют начало разупрочнения, что связано, в первую очередь, с процессом рекристаллизации. Заметное снижение HV в Cu-содержащих сплавах наблюдается при температурах выше 350–400°С. В сплаве 0Cu разупрочнение выражено в меньшей степени.
После отжига при высоких температурах Mn-содержащие дисперсоиды выявляются методом СЭМ (рис. 5а, 5в). В сплаве 0Cu частицы Al6Mn имеют форму игл, с преимущественным размером не более 1 мкм (рис. 5а). В сплавах 2Cu и 3Cu, в которых марганец должен быть полностью связан в фазу Al20Cu2Mn3 (рис. 1б, табл. 3), дисперсоиды имеют глобулярную морфологию и меньший размер (рис. 5б). В состоянии CR400 средний размер дисперсоидов составляет менее 100 нм (рис. 5г), что делает их эффективными антирекристаллизаторами. Именно это состояние с точки зрения термостойкости является наиболее показательным, поскольку оно характеризуется достаточно высокой твердостью (рис. 4в) и стабильностью к нагревам до 400°С.
Состояние CR400 (рис. 6) показывает не только существенный рост HV с ростом содержания Cu, но и снижение УЭС. Это говорит о более низкой концентрации Mn в (Al), что согласуется с результатами расчета (табл. 3).
Рис. 6.
Зависимости твердости и удельного электросопротивления холоднокатаных листов в состоянии CR400 (см. табл. 2) от содержания меди.
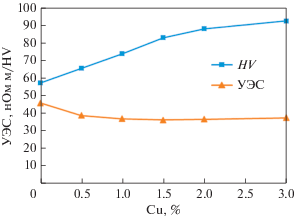
Оценку механических свойств проводили на листах сплавов 2Cu и 3Cu в сравнении со сплавом 1201. При этом пластичность гомогенизированного литого марочного сплава оказалась недостаточной для прокатки: при деформации менее 50% произошло разрушение слитков при обработке. Поэтому из сплава 1201 был сначала получен горячекатаный лист, толщиной 3 мм, а из него после промежуточного отжига – холоднокатаный лист, толщиной 0.5 мм. Последний испытывали после термообработки на максимальную прочность (Т6), а также после отжига при 400°С в течение 3 ч (т.е. в состоянии, аналогичном состоянию сплавов 2Cu и 3Cu). Как видно из табл. 5, модельные сплавы демонстрируют существенно более высокий уровень прочности по сравнению с сплавом 1201, что обусловлено термической стабильностью их структуры.
Таким образом, на примере сплавов, содержащих ~2% Mn и 2–3% Cu, показана принципиальная возможность создания деформируемых алюминиевых сплавов, обладающих высокой термостойкостью и технологичностью.
ВЫВОДЫ
1. Расчетными и экспериментальными методами изучено влияние температуры отжига на удельное электросопротивление, твердость и структуру сплавов системы Al–Cu–Mn, содержащих 2% Mn и до 3% Cu, в литом и холоднокатаном состоянии.
2. Показано, что в литом состоянии практически весь марганец находится в твердом растворе (Al), а медь распределена между (Al) и эвтектическими частицами фазы Al2Cu. Благоприятная морфология данных включений способствует высокой технологичности литых сплавов при холодной прокатке.
3. Установлены сложные зависимости твердости и удельного электросопротивления литых и деформированных сплавов от температуры отжига, что обусловлено протеканием нескольких процессов, в частности растворением в (Al) эвтектических частиц Al2Cu и выделением из него Mn-содержащих дисперсоидов.
4. Наилучший комплекс механических свойств достигается в сплавах, содержащих 2–3% Cu, что обусловлено наличием в их структуре дисперсоидов фазы Al20Cu2Mn3 в количестве более 9 об. % со средним размером менее 100 нм. Такая структура обеспечивает более высокую термостойкость модельных сплавов по сравнению со сплавом 1201, упрочняемым метастабильными выделениями за счет закалки и старения.
Работа выполнена при поддержке гранта РНФ № 20-19-00249.
Список литературы
ASTM B941-16, Standard specification for heat resistant aluminum-zirconium alloy wire for electrical purposes. West Conshohocken, PA. ASTM International, 2016.
International Alloy Designations and Chemical Composition Limits for Wrought Aluminum and Wrought Aluminum Alloys. Arlington. The Aluminum Association Publications, 2015.
Polmear I.J. Light Alloys. From Traditional Alloys to Nanocrystals, 4th ed. UK, Oxford: Butterworth-Heinemann, 2006. 416 p.
Aluminum: Properties and Physical Metallurgy / By ed. Hatch J.E. USA, Ohio: ASM Metals. Park, 1984. 424 p.
Goreslavets N.N., Rodin A.O. Diffusion formation of intermediate phases and supersaturated solid solutions in the aluminum-copper system // Phys. Met. Metal. 2017. V. 118. № 11. P. 1120–1126. https://doi.org/10.1134/S0031918X17100064
Belov N.A., Alabin A.N., Matveeva I.A. Optimization of phase composition of Al–Cu–Mn–Zr–Sc alloys for rolled products without requirement for solution treatment and quenching // J. Alloys Compd. 2014. V. 583. P. 206–213. https://doi.org/10.1016/j.jallcom.2013.08.202
Белов Н.А., Алабин А.Н., Яковлев А.А. Влияние меди на формирование литой микроструктуры алюминиевых сплавов, содержащих 1% (мас.) Mn // Цветные металлы. 2014. № 7. С. 66–72.
Belov N., Korotkova N., Akopyan T., Tsydenov K. Simultaneous Increase of Electrical Conductivity and Hardness of Al–1.5 wt % Mn Alloy by Addition of 1.5 wt % Cu and 0.5 wt % Zr // Metals. 2019. № 9. P. 1246. https://doi.org/10.3390/met9121246
Li Zh., Zhang Zh., Chen X. Improvement in the mechanical properties and creep resistance of Al–Mn–Mg 3004 alloy with Sc and Zr addition // Mat. Sci. Eng. A. 2018. V. 729. P. 196–207. https://doi.org/10.1016/j.msea.2018.05.055
Zupanič F., Wang D., Gspan C., Bončin T. Precipitates in a quasicrystal-strengthened Al–Mn–Be–Cu alloy // Mater. Charact. 2015. V. 106. P. 93–99. https://doi.org/10.1016/j.matchar.2015.05.013
Zupanič F., Gspanb Ch., Burjac J., Bončinaa T. Quasicrystalline and L12 precipitates in a microalloyed Al–Mn–Cu alloy // Mater. Today Commun. 2020. V. 22. P. 100809. https://doi.org/10.1016/j.mtcomm.2019.100809
Mansurov Yu.N., Buravlev I.Yu., Belov N.A., Sannikov A.V. Optimization of composition and properties of heatresistant complex-alloyed aluminum alloy castings // Non-Ferrous Met. 2015. V. 39. № 2. P. 48–55. https://doi.org/10.17580/nfm.2015.02.09
Muddassir Dar S., Liao H. Creep behavior of heat resistant Al–Cu–Mn alloys strengthened by fine (θ') and coarse (Al20Cu2Mn3) second phase particle // Mat. Sci. Eng. A. 2019. V. 763. P. 138062. https://doi.org/10.1016/j.msea.2019.138062
Belov N.A., Eskin D.G., Aksenov A.A. Multicomponent phase diagrams: applications for commercial aluminum alloys. NL. Amsterdam: Elsevier, 2005. 414 p.
Zoeller T.L., Sanders Jr. T.H. The rate of solidification and the effects of local composition on the subsequent nucleation of Al20Cu2Mn3 dispersoid phase in Al–4Cu–0.3Fe–0.4Mn–0.2Si alloys // J. Phys. IV Fr. 2004. V. 120. P. 61–68. https://doi.org/10.1051/jp4:2004120006
Feng Z.Q., Yang Y.Q., Huang B., Li M.H. Chen Y.X., Ru J.G. Crystal substructures of the rotation-twinned T(Al20Cu2Mn3) phase in 2024 aluminum alloy // J. Alloys Compd. 2014. V. 583. P. 445−451. https://doi.org/10.1016/j.jallcom.2013.08.200
Воронцова Л.А. Алюминий и алюминиевые сплавы в электротехнических изделиях. М.: Энергия, 1971. 224 с.
Valiev R.Z., Murashkin M.Yu., Sabirov I. A nanostructural design to produce high-strength Al alloys with enhanced electrical conductivity // Scripta Mater. 2014. № 76. P. 13–16. https://doi.org/10.1016/j.scriptamat.2013.12.002
Zuiko I.S., Gazizov M.R., Kaibyshev R.O. Effect of thermomechanical treatment on the microstructure, phase composition, and mechanical properties of Al–Cu–Mn–Mg–Zr alloy // Physics of Metals and Metallography. 2016. V. 117. № 9. P. 906–919. https://doi.org/10.1134/S0031918X16090088
Robson J.D., Hill T., Kamp N. The effect of hot deformation on dispersoid evolution in a model 3xxx alloy // Mater. Sci. Forum. 2014. V. 794–796. P. 697–703. https://doi.org/10.4028/www.scientific.net/MSF.794-796.697
Дополнительные материалы отсутствуют.
Инструменты
Физика металлов и металловедение