Физика металлов и металловедение, 2020, T. 121, № 12, стр. 1307-1314
Особенности эрозионного изнашивания покрытий со структурообразующей парой “Ti1 – xCx–алмазоподобный углерод” (х = 0.2, 0.8)
А. П. Рубштейн a, *, А. Б. Владимиров a, С. А. Плотников a
a Институт физики металлов УрО РАН
620108 Екатеринбург, ул. С. Ковалевской, 18, Россия
* E-mail: rubshtein@imp.uran.ru
Поступила в редакцию 06.04.2020
После доработки 04.08.2020
Принята к публикации 17.08.2020
Аннотация
Исследованы износостойкие покрытия, полученные совместным осаждением титана и углерода вакуумным ионно-плазменным способом. Однослойные и многослойные покрытия с систематическим повторением пары [(Ti1– xCx/a-C] были осаждены на подложки из стали Р6М5 и 18ХН10Т. Наибольшей эрозионной стойкостью в потоке твердых частиц обладает многослойное покрытие состава [Ti0.2C0.8/a-C]40 с толщиной слоев 25 нм. Скорость эрозионного изнашивания этого покрытия в 1.6–1.8 раза ниже скорости изнашивания однослойных а-С и Ti0.2C0.8 покрытий. Износ [Ti0.2C0.8/a-C]40 происходит послойно, без выкрашивания отдельных участков, что повышает срок его службы. Межфазные границы в Ti0.2C0.8 композитном слое наряду с интерфейсными границами Ti1 –xCx → а-С служат барьером для распространения микротрещин, снижая вероятность образования макротрещин, нарушающих целостность покрытия.
ВВЕДЕНИЕ
Твердые покрытия являются технологически перспективными материалами для снижения изнашивания поверхности различных изделий. В течение последних лет интенсивно развиваются технологии осаждения покрытий, свойства которых определяются структурными элементами наноразмерного масштаба [1–5]. Разрушение материала, структура которого включает зерна микронного размера, происходит вследствие распространения трещин, возникающих в местах концентрации дислокаций у различных дефектов [6, 7]. В наноструктурированных материалах с размерами зерна менее ста нанометров реализуется другой механизм разрушения [8]. Особенность таких материалов состоит в наличии большого количества межзеренных границ с количеством атомов, сравнимым с их количеством в зернах. Такие границы тормозят движение и генерацию дислокаций, препятствуя зарождению, ветвлению и распространению трещин, что позволяет создавать уникальные свойства наноматериалов [9].
Интенсивное развитие технологий привело к созданию нанокомпозитных пленочных структур, включающих аморфную матрицу и кристаллические включения карбидов, нитридов, карбонитридов переходных металлов. Исследуется физическая природа образования таких структур, влияние матрицы, легирующих элементов и размеров кристаллитов на их уникальные физико-механические и трибологические свойства [1–5].
Конструирование многослойных систем путем комбинации слоев и межфазной архитектуры в отдельных слоях позволяет создавать покрытия с низкими коэффициентами трения, высокой твердостью, трещиностойкостью и износостойкостью [10–16]. Границы раздела между слоями, как и межзеренные границы в композитных структурах, препятствуют распространению трещин [14]. Механические и трибологические характеристики многослойных покрытий могут превосходить характеристики отдельно взятых слоев, из которых они сформированы. В литературе имеются работы, посвященные получению и исследованию многослойных покрытий, в состав которых входят нитриды переходных металлов Mo2N/CrN [12], Ti/TiN [17], ZrN–(Zr,Al,Si)N [18], а также карбиды и нитриды переходных металлов в сочетании с алмазоподобным углеродом (diamond-kike carbon DLC) CrN/DLC/Cr–DLC [19], a-C/a-C:Ti [10], TaN/a-CNx [11].
В работе [19] исследованы покрытия, DLC слои в которых осаждались PECVD (physical enhanced chemical vapor deposition) способом. Их твердость не превышает 15 ГПа из-за большого содержания sp2-связанного углерода. Скорость изнашивания CrN/DLC/Cr–DLC уменьшается по сравнению с CrN и DLC. Улучшение трибологических характеристик авторы связывают с использованием твердой CrN компоненты, введением DLC как лабриканта, и ингибированием распространения трещин. Авторы [10] исследовали многослойное покрытие из а-С и а-С:Ti-слоев, осаждаемых магнетронным способом. Трибологические и механические свойства а-С/а-С:Ti превосходят свойства а-С. Многослойная а-С/а-С:Ti-пленка имеет высокую твердость, прочность сцепления с подложкой, обладает низким коэффициентом трения (0.08). В обеих работах исследована износостойкость фрикционной пары покрытие–контртело (сталь AISI 440C [19], керамика Si3N4 [10]).
В настоящей работе получены однослойные Ti1– xCx и многослойные [(Ti1 –xCx/a-C]n покрытия. Состав Ti1– xCx варьировали условиями осаждения. В многослойных покрытиях использованы а-С слои с высоким содержанием sp3-связей. Основная цель работы – исследование влияния структуры и состава покрытий на механизм эрозионного изнашивания.
МАТЕРИАЛЫ И МЕТОДЫ
Осаждение покрытий на пластины из нержавеющей стали 18ХН10Т размером 10 × 10 × 2 мм, инструментальной стали Р6М5 размером 20 × 20 × × 3 мм, карбида вольфрама (WC–Co) и медной фольги проводили в установке УВНИПА-1-001. Пластины промывали в ультразвуковой ванне в смеси дистиллированной воды и спирта. Окончательную очистку проводили травлением ионами аргона в вакууме (Е = 4 кэВ, P = 4.2 × 10−2 Па, 30 мин).
Для осаждения а-С-покрытий и аналогичных слоев в многослойных покрытиях использовали импульсно-дуговой источник с графитовым катодом, для Ti1– xCx – импульсно-дуговой с графитовым катодом совместно с дуговым с титановым катодом. Изменением частоты импульсов варьировали соотношение ${{N_{{\text{C}}}^{ + }} \mathord{\left/ {\vphantom {{N_{{\text{C}}}^{ + }} {N_{{{\text{Ti}}}}^{ + }}}} \right. \kern-0em} {N_{{{\text{Ti}}}}^{ + }}}$ в плазме (N – количество ионов). Многослойные покрытия [(Ti1 – xCx/a-C]n получали чередованием слоев а‑С и Ti1 – xCx. Первым наносили адгезивный слой толщиной 0.1–0.2 мкм c градиентом концентрации титана от 100 до 0%.
Состав однослойных покрытий, осажденных на пластины из медной фольги, определяли методом рентгеновской энергодисперсионной спектроскопии (сканирующий электронный микроскоп QUANTA 200 с EDAX анализатором). Толщину покрытий определяли по электронно-микроскопическим снимкам поперечного сечения системы покрытие–подложка. Для этого использовали покрытия, осажденные на тонкую WC–Co-пластину.
Для качественной оценки наличия в покрытиях sp3- и sp2-связанного углерода использовали соотношение интегральных интенсивностей D и G пиков рамановских спектров ID/IG. Спектры возбуждали лазерной линией 532 нм (2.33 эВ) мощностью до 0.5 мВт, сфокусированной в пятно на покрытии диаметром ~2 мкм. Рассеянный свет регистрировали спектрометром RM 1000 фирмы Renishaw. Спектральное разрешение составляло ~3 см–1.
Механические характеристики покрытий, осажденных на пластины из нержавеющей стали 18ХН10Т, определяли методом индентирования на приборе NanoTest 600 с использованием алмазной пирамиды Берковича (индентор) при нагрузках от 1 до 256 мН. При каждой нагрузке делали от 6 (большие нагрузки) до 8 (малые нагрузки) индентаций на расстоянии от 20 до 50 мкм. Твердость определяли по максимуму на зависимости f = H(d), где Н – твердость, d – глубина внедрения индентора. Корректность определения твердости контролировали соблюдением следующих условий. Глубина внедрения индентора должна быть в 10 раз ниже толщины покрытия для минимизации влияния подложки; в 20 раз превышать среднеквадратичное отклонение профиля (Rq) покрытия, во избежание погрешности измерения глубины индентирования; в 2 раза превышать толщину повторяющейся структурной единицы многослойной системы для достоверности результата [20].
Метод индентирования использован также для качественной оценки трещиностойкости покрытий. Авторами [15, 21] было обнаружено, что появление трещин в покрытии при индентировании приводит к нарушению гладкости (появлению горизонтальных “плато”) кривой нагружения P–d диаграммы, где Р – нагрузка на индентор, d – глубина внедрения. Нагрузка, при которой на диаграммах появляется первое “плато”, использована для оценки устойчивости покрытия к образованию трещин.
Для испытаний на эрозионную стойкость использовали покрытия, осажденные на инструментальную сталь Р6М5. Тестирование проводили в струе частиц карбида кремния SiC размером 120–150 мкм, при скорости 20 м/с и угле падения 90°, создаваемой центробежным ускорителем. Образцы устанавливали в держатели с диафрагмой диаметром 15 мм. Это исключало вероятность скалывания покрытия на краях образца. Для равномерного изнашивания струю сканировали по поверхности покрытия. Одновременно испытывали 10 образцов, включая пластины из Р6М5 без покрытия. После определенной дозы частиц образцы вынимали, очищали и взвешивали на аналитических весах. Относительную интенсивность изнашивания покрытий рассчитывали из соотношения I/I0 = (Δm/mc + 1)–1, где I, I0 – интенсивность изнашивания материала покрытия и подложки, соответственно, Δm – разность между потерей веса материала подложки и потерей веса образца с полностью изношенным покрытием при одной и той же дозе абразива, mc – вес изношенного покрытия.
РЕЗУЛЬТАТЫ И ОБСУЖДЕНИЕ
Для исследования были получены однослойные и многослойные покрытия, состав и толщина которых приведены в табл. 1. Однослойные покрытия осаждали из углеродной (покрытие № 1) или титан-углеродной плазмы с соотношением ионов ${{N_{{\text{C}}}^{ + }} \mathord{\left/ {\vphantom {{N_{{\text{C}}}^{ + }} {N_{{{\text{Ti}}}}^{ + }}}} \right. \kern-0em} {N_{{{\text{Ti}}}}^{ + }}}$ > 1 (№ 2) и ${{N_{{\text{C}}}^{ + }} \mathord{\left/ {\vphantom {{N_{{\text{C}}}^{ + }} {N_{{{\text{Ti}}}}^{ + }}}} \right. \kern-0em} {N_{{{\text{Ti}}}}^{ + }}}$ < 1 (№ 3). При ${{N_{{\text{C}}}^{ + }} \mathord{\left/ {\vphantom {{N_{{\text{C}}}^{ + }} {N_{{{\text{Ti}}}}^{ + }}}} \right. \kern-0em} {N_{{{\text{Ti}}}}^{ + }}}$ > 1 формируется покрытие из аморфного углерода с включениями карбида титана, при ${{N_{{\text{C}}}^{ + }} \mathord{\left/ {\vphantom {{N_{{\text{C}}}^{ + }} {N_{{{\text{Ti}}}}^{ + }}}} \right. \kern-0em} {N_{{{\text{Ti}}}}^{ + }}}$ < 1 – из аморфного титана с включениями карбида титана [2]. Слои в Ti1 – xCx многослойных покрытиях № 4–8 осаждали в таких же условиях, что и соответствующие однослойные покрытия.
Таблица 1.
Характеристики покрытий
№ | Состав покрытия | h, нм | N* | h*, нм | ID/IG |
---|---|---|---|---|---|
1 | a-C | 2000 | 1 | – | 0.26 |
2 | Ti0.2C0.8 | 1600 | 1 | – | 2.06 |
3 | Ti0.8C0.2 | 1700 | 1 | – | – |
4 | [Ti0.8C0.2/a-C]2 | 4000 | 4 | 1000 | – |
5 | [Ti0.8C0.2/a-C]10 | 2000 | 20 | 100 | – |
6 | [Ti0.2C0.8/a-C]10 | 2000 | 20 | 100 | – |
7 | [Ti0.2C0.8/a-C]40 | 2000 | 80 | 25 | 1.03 |
8 | [Ti0.8C0.2/a-C]40 | 2000 | 80 | 25 | 0.77 |
Последовательность осаждения слоев влияет на формирование межслоевых границ. На рис. 1 представлены СЭМ (сканирующая электронная микроскопия) изображения поперечных сечений покрытий № 4–6, отличающихся толщиной слоев и составом Ti1– xCx (см. табл. 1). В покрытии № 4 наблюдается хорошее сцепление между слоями Ti0.8C0.2 и а-С (граница 1, рис. 1а). Напротив, при осаждении Ti0.8C0.2 на а-С видна четкая граница раздела (граница 2). Аналогичную картину мы наблюдаем в покрытии № 5 с меньшей толщиной слоев и покрытии № 6 с меньшей концентрацией титана в Ti1 – xCx (рис. 1б, 1в). При образовании пары Ti1 – xCx ← а-С ускоренные ионы углерода проникают вглубь Ti1 – xCx, вступают в химическую связь с титаном, формируя тонкий адгезивный слой без образования видимой межслоевой границы раздела. При последовательности осаждения а-С ← Ti1– xCx инертная поверхность сверхтвердого алмазоподобного углерода не способствует континуальному переходу от а-С к Ti1– xCx. Бомбардировка ионами Ti+ при последовательности осаждения а-С ← Ti1 – xCx приводит к графитизации поверхностных слоев а-С [22], создавая особую межслоевую прослойку. Графитизация а-С была подтверждена рамановской спектроскопией.
Рис. 1.
Поперечное сечение покрытие-подложка: (а) покрытие № 4, (б) № 5, (в) № 6. Сканирующая электронная микроскопия.
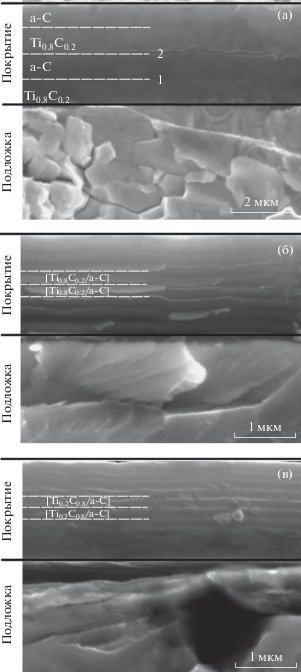
Углеродные аллотропные структуры обладают уникальными характеристическими пиками. Для алмаза характерен пик на 1332 см–1 (D-пик), для кристаллического графита – на 1580 см–1 (G-пик), аморфный алмазоподобный углерод имеет широкую полосу в интервале 1300–1600 см–1. Положение, ширина и интенсивность D и G пиков определяются плотностью, размером и структурой кластеров с sp2-связями между атомами углерода. В свою очередь свойства sp2 кластеров тесно связаны с наличием sp3 связей в алмазоподобной структуре, что дает возможность оценивать их содержание по соотношению интегральных интенсивностей ID/IG. Отношение ID/IG уменьшается с увеличением содержания sp3 и достигает значения, близкого к нулю, для DLC с содержанием sp3-связей около 80% [23]. На рис. 2 представлены спектры покрытий а-С (№ 1), Ti0.8C0.2 (№ 3) и [Ti0.8C0.2/a-C]40 (№ 8). Покрытие а-С имеет характерную для алмазоподобного углерода асимметричную полосу с максимумом на 1550 см–1. Отсутствие пиков в интервале 1300–1600 см–1 у Ti0.8C0.2 (№ 3) свидетельствует о том, что в покрытии не сформирован сплошной углеродный кластер. Пики на 300 и 630 см–1 свойственны карбидам титана. Спектр покрытия № 8 имеет характерную для аморфного углерода асимметричную полосу с двумя максимумами (вклад от а-С-слоев) и пики на 300 и 630 см–1 (вклад от Ti0.8C0.2 слоев). В табл. 1 приведены расчетные значения ID/IG. Более высокое значение ID/IG в многослойной структуре № 8 по сравнению с покрытием № 1 свидетельствует о снижении соотношения sp3/sp2 в а-С-слоях, так как в Ti0.8C0.2 не обнаружены непрерывные углеродные кластеры. Бомбардировка а-С ионами Ti+ при осаждении на их поверхность титансодержащих слоев приводит к их графитизации, и, соответственно, снижению твердости. В случае покрытия № 7 [Ti0.2C0.8/a-C]40 Рамановская спектроскопия не может быть использована для характеризации структурных изменений а-С, так как оба структурообразующих слоя в этом покрытии содержат непрерывный кластер углерода, дающий свой вклад в усредненное значение ID/IG (см. табл. 1). Можно только предположить, что графитизация а-С слоев в этом покрытии идет менее интенсивно, т.к. количество ионов титана в плазме при осаждении Ti0.2C0.8 существенно ниже по сравнению с плазмой, используемой для осаждения Ti0.8C0.2.
На рис. 3 представлены зависимости твердости от глубины внедрения индентора для многослойных покрытий № 7 и 8. Твердость покрытия № 7 достигает максимума при d = 150 нм, № 8 – 100 нм, что менее 0.1 толщины покрытия, в 15–20 раз превышает Rq а-С-покрытия [4] и 4–6 раз толщину слоя. Значения твердости приведены в табл. 2. Твердость покрытий № 7 и 8 существенно ниже твердости а-С, что также подтверждает графитизацию а-С-слоев.
Качественная оценка начала разрушения покрытий была сделана по кривым нагружения P‒d-диаграммы. При распространении трещин, нарушающих структурную целостность покрытий, или образовании макроскопической полосы сдвига при индентации, на кривых нагружения появляется “плато” [15, 21]. На рис. 4 представлены P–d-диаграммы покрытий № 7 и 8, полученные при одинаковой глубине индентации (~1800 нм). При глубине вдавливания 1000 нм в покрытии [Ti0.2C0.8/a-C]40 (№ 7) наблюдается более высокий уровень разрушения (протяженное плато) по сравнению с покрытием [Ti0.8C0.2/a-C]40. Наличие пластичных слоев Ti0.8C0.2 (их диаграмма при такой же глубине индентации была гладкой) оказывает положительное влияние на стойкость покрытия к распространению трещин. С другой стороны, “плато” на кривой нагружения покрытия № 7 появляется при более высокой нагрузке. Наибольшей устойчивостью (высокими значениями Ртр) обладают а–С и [Ti0.2C0.8/a-C]40-покрытия (см. табл. 2).
Относительная интенсивность изнашивания (I/I0) всех покрытий меньше единицы (табл. 2), т.е. их износостойкость выше износостойкости стали Р6М5. Многослойные покрытия более стойкие к эрозионному изнашиванию по сравнению с однослойными.
Среди однослойных покрытий небольшим преимуществом обладает покрытие № 2, твердость которого и Ртр меньше, чем у а-С (№ 1) (табл. 2, рис. 5а). Покрытие состава Ti0.2C0.8 состоит из аморфной углеродной матрицы с включениями карбида титана с большой объемной долей границ, что было установлено ранее для покрытий с концентрацией титана ~80 ат. % [4]. Границы служат барьером для распространения сети субмикронных трещин, снижая вероятность разрушения материала покрытия.
Рис. 5.
Зависимости потери веса образца от веса изнашивающих частиц: (а) однослойные покрытия; (б) многослойные.
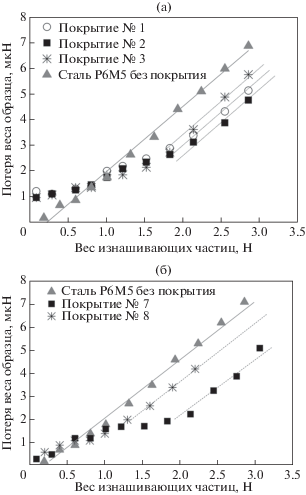
Высокой износостойкостью обладает и многослойное покрытие, в состав которого входят слои такого же состава (№ 7). Оно изнашивается послойно (ступени на кривой изнашивания), с изменением толщины, но без нарушения сплошности (рис. 5б).
Отслоения, скорее всего, происходят вследствие сдвига слоев по графитизированным границам раздела между парами слоев [Ti1 –xCx/a-C] ← ← [Ti1 – xCx/а-С]. Для покрытий № 2 и 7 основной причиной эрозионного изнашивания является распространение трещин, так как равномерного износа материала покрытия не происходит (рис. 6а, 6в). Зародышевые трещины возникают на структурных несовершенствах покрытия и в зонах повышенной деформации. При возрастании количества ударов частиц трещины распространяются вглубь, достигая плоскости покрытие–подложка в однослойных покрытиях или межслоевых, или интерфейсных границ в многослойных структурах. В первом случае фрагменты покрытия отслаиваются от подложки, во втором – от интерфейсных границ.
Рис. 6.
Поверхность покрытий после эрозионного изнашивания (доза 1 Н): (а) покрытие № 2; (б) покрытие № 3; (в) покрытие № 7; (г) покрытие № 8.
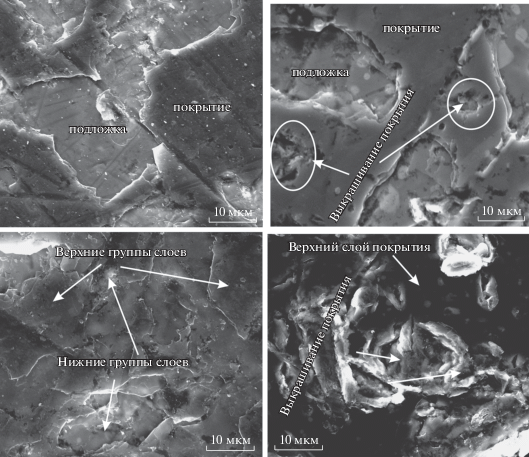
Покрытия Ti0.8C0.2 (№ 3) и [Ti0.8C0.2/а-С]40 (№ 8) менее износостойкие в сравнении с покрытиями № 2 и 7. Для них характерно равномерное, не ступенчатое, изнашивание (рис. 5а, 5б). На поверхности покрытия № 3, в отличие от покрытия № 2, образуются эрозионные пятна из-за выкрашивания материала покрытия (рис. 6б). В местах фрагментарного отслаивания верхнего сверхтвердого а-С слоя покрытия № 8 также образуются характерные эрозионные пятна (рис. 6г). Менее твердые и более пластичные титансодержащие Ti0.8C0.2 слои (твердость 12.6 ГПа), а также графитизированные а-С слои разрушаются под действием потока твердых частиц, приводя к выкрашиванию отдельных участков.
ЗАКЛЮЧЕНИЕ
Исследованы однослойные а-С, Ti1 – xCx и многослойные [Ti1 – xCx/а-С]n покрытия, полученные совместным осаждением титана и углерода вакуумным ионно-плазменным способом. Слои Ti1 –xCx в многослойных покрытиях осаждали в тех же условиях, что и однослойные покрытия аналогичного состава.
Установлено, что многослойные покрытия более стойкие к эрозионному изнашиванию по сравнению с однослойными. Скорость их изнашивания в 1.6–1.8 раза ниже скорости изнашивания однослойных покрытий. Повышенная стойкость многослойных покрытий связана с наличием межслоевых границ, тормозящих распространение трещин при эрозионном воздействии.
При эрозионном воздействии наибольшим преимуществом обладает покрытие [Ti0.2C0.8/a-C]40. Скорость его изнашивания в 1.4 раза ниже скорости изнашивания многослойного [Ti0.8C0.2/a-C]40. Износ [Ti0.2C0.8/a-C]40 происходит послойно, без выкрашивания отдельных участков, что повышает срок его службы. Межфазные границы в Ti0.2C0.8 слое наряду с интерфейсными границами Ti1 ‒ xCx → а-С служат барьером для распространения микротрещин, снижая вероятность образования макротрещин, нарушающих целостность покрытия.
Покрытие [Ti0.8C0.2/а-С]40 менее износостойкое, так как содержит менее твердые и более пластичные титансодержащие слои. Кроме того, при формировании покрытия происходит графитизация а-С-слоев. Под действием потока твердых частиц покрытие разрушается равномерно выкрашиванием отдельных участков.
Работа выполнена в рамках государственного задания Минобрнауки России (тема “Функция”, № АААА-А19-119012990095-0), при частичной поддержке РФФИ (проект № 20-48-660065).
Список литературы
Kumar N., Natarajan G., Pandian R., Bahuguna A., Srivastava S.K., Ravindran T.R., Rajagopalan S., Dash S., Tyagi A.K., Dumpala R., Ramachandra Rao M.S. Microstructure and phase composition dependent tribological properties of TiC/a–C nanocomposite thin films // Surf. Coat. Technol. 2014. V. 258. P. 557–565.
Vladimirov A.B., Plotnikov S.A., Trakhtenberg I.Sh. Rubshtein A.P., Volkova E.G. Nanocomposite Films Prepared by Arc-Plasma Deposition of Titanium and Carbon // Prot. Met. Phys. Chem. Surf. 2015. V. 51. P. 230–233.
Trakhtenberg I.Sh., N. V. Gavrilov N.V., Emlin D.R., Plotnikov S.A., Vladimirov A.B., Volkova E.G., Rubshtein A.P. Nanocomposite vacuum-Arc TiC/a–C:H coatings prepared using an additional ionization of acetylene // Phys. Met. Metal. 2014. V. 115. P. 723–729.
Rubshtein A.P., Vladimirov A.B., Korkh Yu.V. Ponosov Y.S., Plotnikov S.A. The composition, structure and surface properties of the titanium-carbon coatings prepared by PVD technique // Surf. Coat. Technol. 2017. V. 309. P. 680–686.
Jansson U., Lewin E. Sputter deposition of transition-metal carbide films—a critical review from a chemical perspective // Thin Solid Films. 2013. V. 536. P. 1–24.
Финкель В.М. Физические основы торможения разрушения. М.: Металлургия. 1977. 348 с.
Panckow A.N., Steffenhagen J., Wegener B., Dübner L., Lierath F. Application of novel vacuum-arc ion-plating technologies for the design of advanced wear resistant coatings // Surf. Coat. Technol. 2001. V. 138. P. 71–76.
Gleiter H. Nanostructured materials: basic concepts and microstructure // Acta Mater. 2000. V. 48. P. 1–29.
Верещака А.С., Верещака А.А. Повышение эффективности инструмента путем управления составом, структурой и свойствами покрытий // Упрочняющие технологии и покрытия. 2005. № 9. С. 9–18.
Cai J.B., Wang X.L., Bai W.Q. Wang D.H., Gu C.D., Tu J.P. Microstructure, mechanical and tribological properties of a–C/a–C:Ti nanomultilayer film // Surf. Coat. Technol. 2013. V. 232. P. 403–411.
Chen R., Tu J.P., Liu D.G., Yu Y.L., Qu S.X., Gu C.D. Structural and mechanical properties of TaN/a-CNx multilayer films // Surf. Coat. Technol. 2012. V. 206. P. 2242–2248.
Bouaouina B., Besnard A., Abaidia S.E., Haid F. Residual stress, mechanical and microstructure properties of multilayer Mo2N/CrN coating produced by R.F Magnetron discharge // Appl. Surf. Sci. 2017 V. 395. P. 117–121.
Teles V.C., Mello J.D.B., Silva W.M. Abrasive wear of multilayered/gradient CrAlSiN PVD coatings: Effect of interface roughness and of superficial flaws // Wear. 2017. V. 376–377(B). P. 1691–1701.
Bai W.Q., Li L.L., Wang X.L., He F.F., Liu D.G., Jin G., Tu J.P. Effects of Ti content on microstructure, mechanical and tribological properties of Ti-doped amorphous carbon multilayer films // Surf. Coat. Technol. 2015. V. 266. P. 70–78.
Wiecinski P., Smolik J., Garbacz H., Bonarski J., Mazurkiewicz A., Kurzydłowski K.J. Microstructure and properties of metal/ceramic and ceramic/ceramic multilayer coatings on titanium alloy Ti6Al4V // Surf. Coat. Technol. 2017. V. 309. P. 709–718.
Kumar D., Kumar N., Kalaiselvam S., Dash S., Jayave R. Wear resistant super-hard multilayer transition metal-nitride coatings // Surf. Interfaces. 2017. V. 7. P. 74–82.
Ghasemi S., Shanaghi A., Chu P.K. Nano mechanical and wear properties of multi-layer Ti/TiN coatings deposited on Al 7075 by high-vacuum magnetron sputtering // Thin Solid Films. 2017. V. 638. P. 96–104.
Vereschaka A., Tabakov V., Grigoriev S., Aksenenko A., Sitnikov N., Oganyan G., Seleznev A., Shevchenko S.l. Effect of adhesion and the wear-resistant layer thickness ratio on mechanical and performance properties of ZrN–(Zr,Al,Si)n coatings // Surf. Coat. Technol. 2019. V. 357. P. 218–234.
Sui X., Liu J., Zhang S., Yang J., Hao J. Microstructure, mechanical and tribological characterization of CrN/DLC/Cr-DLC multilayer coating with improved adhesive wear resistance // Appl. Surf. Sci. 2018. V. 439. P. 24–32.
ISO 14577-1:2002, Metallic materials – Instrumented indentation test for hardness and materials parameters – Part 1: Test method.
Martinez E., Andujar J.L., Polo M.C., Esteve J., Robertson J., Milne W.I. Study of the mechanical properties of tetrahedral amorphous carbon films by nanoindentation and nanowear measurements // Diam. Relat. Mater. 2001. V. 10. P. 145–152.
Rubshtein A.P., Trakhtenberg I.Sh., Yugov V.A., Vladimirov A.B., Plotnikov S.A., Ponosov Yu.S. Temperature effect on the formation of a relief of diamond-like carbon coatings and its modification by ion bombardment // Phys. Met. Metallogr. 2006. V. 102. P. 626–631.
Cui W.G., Lai Q.B., Zhang L., Wang F.M. Quantitative measurements of sp3 content in DLC films with Raman spectroscopy // Surf. Coat. Technol. 2010. V. 205. P. 1995–2002.
Дополнительные материалы отсутствуют.
Инструменты
Физика металлов и металловедение