Физика металлов и металловедение, 2021, T. 122, № 1, стр. 8-30
Лазерная аддитивная 3D-печать титановых сплавов: современное состояние, проблемы, тенденции
Н. В. Казанцева a, *, П. В. Крахмалев b, И. А. Ядройцева c, И. А. Ядройцев c
a Институт физики металлов УрО РАН
620108 Екатеринбург, ул. С. Ковалевской, 18, Россия
b Университет Карлстада
SE–651 88 Карлстад, Университетгатан 2, Швеция
c Центральный университет технологии, Свободный Штат, Отделение механической инженерии
и мехатроники
9300 Блюмфонтейн, Частный почтовый ящик X20539, ЮАР
* E-mail: kazantseva@imp.uran.ru
Поступила в редакцию 30.07.2020
После доработки 18.08.2020
Принята к публикации 25.08.2020
Аннотация
Рассмотрены особенности метода 3D-печати, использующего лазерное сплавление металлических порошков, влияние режима работы лазера на структуру, остаточные напряжения и свойства получаемых металлов. Предложенная авторами данного обзора методика подбора параметров процесса с помощью единичных треков может рассматриваться как универсальная для всех видов металлических 3D-принтеров, использующих лазерную печать. Приведены структурные характеристики и медицинские требования к биосовместимым материалам. Обзор включает как российские, так и зарубежные публикации. В качестве объекта исследования рассмотрен биосовместимый сплав Ti–6Al–4V, однако обнаруженные общие закономерности изменения структуры и свойств этого титанового сплава, связанные с методикой его получения при селективном лазерном сплавлении, могут быть интересны также специалистам, разрабатывающим авиационные материалы.
1. ВВЕДЕНИЕ
В настоящее время человечество вступает в эпоху четвертой промышленной революции, которая характеризуется внедрением кибер-физических систем в производственные процессы. Интеграция физических, цифровых и биологических технологий ведет к новым достижениям в таких областях как искусственный интеллект, робототехника, нано- и биотехнологии, энергетика, материаловедение и т.д. Новая индустриальная парадигма “аддитивное производство” (англ. Additive Manufacturing, AM) объединяет класс технологий, позволяющих создавать трехмерные объекты, последовательно добавляя материал, обычно слой за слоем, в противоположность субтрактивным (вычитающим) технологиям и традиционным формообразующим производствам (литье, штамповка) [1]. Аддитивные технологии уникальны и радикально меняют всю цепочку производства и потребления – от дизайна изделий до реализации готового продукта. Сложность и разнообразие форм деталей, сокращение времени от разработки прототипа до конечного изделия, потенциальная возможность использования разных материалов в одном цикле производства, оперативное изготовление “продукта по запросу” (product on demand), являются основными преимуществами аддитивного производства.
Важной частью AM является использование компьютерных технологий для преобразования трехмерной модели в физический объект. Технологии, представленные AM, являются некоторым аналогом широко распространённых компьютерных принтеров. Сходство AM с 2D-печатью привело к появлению альтернативного общего названия – 3D-печать. За последние 30 лет современного развития AM, если брать за точку отсчета изобретение SLS (англ. Selective Laser Sintering) Карлом Декардом (Deckard, Carl Robert 1961–2019) использовали множество наименований этой технологии (англ. free formed fabrication, rapid tooling, rapid prototyping, rapid manufacturing, additive fabrication, additive processes, additive techniques, layer manufacturing, additive layer manufacturing, solid free formed fabrication и т.д.). Термин “additive manufacturing” был официально принят 14 января 2009 г. на первом заседании технического комитета ASTM F42, который в настоящее время является комитетом по разработке стандартов для технологий аддитивного производства, и его цель – это продвижение знаний, стимулирование исследований и внедрение АМ технологий. Вскоре после этого термин AM был принят техническим комитетом ISO TC261, который способствовал его широкому международному распространению. В настоящее время в мире используют оба термина, как AM, так и 3D-печать. Первый термин больше используется в научном сообществе, в то время как средства массовой информации в основном используют термин “3D-печать”.
Системы AM можно классифицировать по типу используемого материала: жидкостные, твердотельные и порошковые. ISO/ASTM стандарт по терминологии распределяет все AM процессы на семь подклассов (рис. 1):
1) Прямой подвод энергии и материала (directed energy deposition, DED) – процесс, в котором сфокусированная тепловая энергия (например, лазерного/ электронного луча, или энергия плазменной дуги) плавит материал непосредственно в процессе нанесения. Материалом может быть порошок, динамически подаваемый c помощью газовой струи в заданную область (powder DED) или проволока (wire DED).
2) Плавление порошкового слоя (powder bed fusion, PBF) – процесс, в котором тепловая энергия сфокусированного луча избирательно плавит области предварительно нанесенного порошкового слоя. Российский стандарт ГОСТ Р 57558–2017 рекомендует использовать термин “синтез на подложке”, акцентируя внимание на предварительном нанесении порошкового слоя на субстрат [2].
3) Струйное нанесение связующего (binder jetting) – селективное струйное нанесение (впрыскивание) связующего агента на порошковый слой.
4) Струйная печать, или струйное нанесение материала (material jetting) – процесс, в котором изделие формируется непосредственно из капель материала. Примером таких материалов являются фотополимеры, воски, смеси металлических или керамических порошков и связующего жидкого агента.
5) Экструзия материала (material extrusion) – процесс, при котором материал селективно выдавливается через сопло или специальную насадку.
6) Листовая ламинация (sheet lamination) –изделие формируется послойным соединением листового материала.
7) Фотополимеризация в ванне (vat photopolymerization) – процесс, в котором жидкий фотополимер выборочно полимеризуется в емкости световым лучом.
Из этих семи категорий только четыре напрямую связаны с изготовлением металлических компонентов – DED, PBF, material jetting и binder jetting, и только первые две используются для работы с титаном и его сплавами.
В данной работе будет рассмотрен только один АМ процесс – лазерный синтез на подложке (laser-based powder bed fusion L-PBF, селективное лазерное сплавление СЛС).
2. ТЕХНОЛОГИЯ ПОЛУЧЕНИЯ 3-D ИЗДЕЛИЯ ЛАЗЕРНОЙ ПЕЧАТЬЮ
2.1. Лазерный синтез на подложке. Лазерный синтез на подложке (L-PBF, лазерное сплавление или селективное лазерное сплавление) – это технология плавления порошкового слоя с помощью сфокусированного лазерного луча.
Металлический порошок предварительно наносится на рабочую платформу (подложку). Лазерный луч сканирует поверхность порошка, селективно плавя определенные области порошкового слоя и одновременно переплавляя предыдущий затвердевший слой, тем самым достигая прочного металлургического контакта между слоями. Затем наносится новый слой порошка, и цикл повторяется до тех пор, пока цифровая трехмерная модель детали не преобразуется в физический объект (рис. 2).
В большинстве современных машин изделие формируется не непосредственно на платформе построения, а сначала строится система так называемых “поддержек” или суппортов.
Высокая степень свободы, предлагаемая технологией L-PBF, позволяет создавать объекты с уникальной геометрией и сложными внутренними структурами, применять топологическую оптимизацию и консолидацию деталей, объединяя множество компонентов в одну функциональную деталь, возможно создание градиентных структур, как в плане объемных структур, так и материалов. Следует отметить, что в зарубежной литературе используют разные названия данного процесса, наиболее известные из них – выборочное лазерное плавление или селективное лазерное сплавление (selective laser melting, SLM), прямой лазерный синтез металла (direct metal laser sintering, DMLS), LaserCusing, прямое лазерное плавление металла (direct metal laser melting, DMLM), лазерное плавление металла (laser metal fusion, LMF). Однако надо четко понимать, что это коммерческие названия одного и того же процесса. В настоящее время ГОСТ/ISO/ASTM стандарты рекомендуют называть этот процесс “синтез на подложке”, или в английском варианте laser-based “powder bed fusion” (L-PBF). Однако в российской литературе для этого процесса принят также термин: лазерное сплавление или селективное лазерное сплавление.
Мировые производители все чаще осознают преимущества производства металлических деталей путем аддитивного производства, поэтому каждый год продажи таких систем растут. Основными и самыми крупными производителями L‑PBF систем являются: EOS (Германия) [3]; Concept Laser (GE Additive, Германия) [4]; SLM Solutions (Германия) [5]; 3D Systems (США) [6]; Renishaw (Великобритания) [7]. Несколько лет назад истек срок действия основных патентов на L‑PBF, поэтому с каждым годом все больше компаний (особенно из Китая) предлагают свои решения в этой области (рис. 3).
Наиболее исчерпывающую информацию о всех компаниях, производящих оборудование для лазерного сплавления (L-PBF), о ценах на данное оборудование, об используемых материалах, областях применения, новых тенденциях и направлениях исследований, можно узнать из Wohlers Report [8]. Это ежегодное международное издание сообщает о развитии и перспективах AM в мире и отдельно по странам, о новых материалах, приложениях, системах, услугах, дизайне, программном обеспечении, а также о патентах, стандартах, инвестициях.
Аддитивное производство особенно бурно развивается в автомобильной, аэрокосмической, медицинской и других высокотехнологичных областях промышленности.
Хотя технология лазерного сплавления (L-PBF) пока не является массовой, она достаточно широко тестируется в ряде высокотехнологичных отраслей с низким и средним объемом производства. Например, Bugatti разработала самые мощные в мире тормоза для нового Chiron [10]. Тормозные суппорты были спроектированы с использованием бионических принципов и изготовлены из Ti‒6AI–4V в Laser Zentrum Nord (Гамбург) на L‒PBF системе SLM® 500 (SLM Solutions). Новая архитектура сочетает в себе минимальный вес (2.9 кг) с максимальной жесткостью. Суппорт имеет длину 41 см, ширину 21 см и высоту 13.6 см. По сравнению с используемым в настоящее время алюминиевым компонентом, который весит 4.9 кг, Bugatti снизил вес тормозного суппорта примерно на 40%, одновременно обеспечивая еще более высокую прочность благодаря использованию материала из Ti–6AI–4V и новой L-PBF технологии. До настоящего времени такой подход был неосуществим, потому что чрезвычайно трудно или даже невозможно фрезеровать или выковывать компоненты такой сложности из Ti‒6AI–4V, как это обычно делают с алюминиевым сплавом, из–за высокой прочности материала.
Эта проблема теперь решена с появлением высокопроизводительных систем для лазерного сплавления (L-PBF) нового поколения. Это также открывает возможность создания деталей относительно большого размера с еще более сложной структурой, которые значительно более жесткие, прочные и функциональные, чем это было бы возможно достичь при любом обычном производственном процессе (табл. 1).
Таблица 1.
L-PBF системы, имеющие наибольшее количество лазерных источников и наибольшие рабочие объемы
Производитель | Система для лазерного сплавления L-PBF | Лазерный источник: волоконный лазер, Вт | Рабочий объем (X, Y, Z), мм3 |
---|---|---|---|
EOS [3] | EOS M 300-4 | 4 × 400 | 300 × 300 × 400 |
EOS M 400-4 | 4 × 400 | 400 × 400 × 400 | |
Concept Laser (GE Additive) [4] | M Line Factory | 4 × 400/4 × 1000 | 500 × 500 × 400 |
X Line 2000R | 2 × 1000 | 800 × 400 × 500 | |
SLM Solutions [5] | SLM® 500 | 4 × 400/4 × 700 | 500 × 280 × 365 |
SLM® 800 | 4 × 400/4 × 700 | 500 × 280 × 850 | |
3D Systems [6] | DMP Factory 500 Solution | 3 × 500 | 500 × 500 × 500 |
Renishaw [7] | RenAM 500Q | 4 × 500 | 250 × 250 × 350 |
Другим примером, где преимущества функциональной интеграции, объединяющей элементы изделия особенно важно, является изготовление с помощью АМ системы EOS M 400-4 критически важного компонента двигателя нового ракетного ускорителя Ariane-6. Традиционный дизайн ракетного инжектора состоит из 248 компонентов, которые изготавливают и собирают с помощью литья, пайки, сварки, сверления. Обычное производство требует просверлить более 8000 поперечных отверстий в медных гильзах, которые затем прецизионно привинчивают к 122 инжекторным элементам, чтобы смешивать водород, протекающий через них, с кислородом. Это трудоемкий и сложный процесс, который может привести к появлению “слабых” мест и представлять риск при экстремальных нагрузках. Благодаря технологии лазерного сплавления (L-PBF), Ariane Group удалось кардинально упростить инжектор ракетного двигателя до конструкции “все в одном” (AiO) и вывести его функциональность на совершенно новый уровень [11]. Существует множество индустриальных приложений, в которых особенно важен компактный, пространственно–эффективный дизайн с той же функциональностью.
2.2 Факторы, влияющие на качество изделий, полученных лазерным сплавлением. На первый взгляд, лазерное сплавление (L-PBF) – это красивая и простая концепция, но она достаточно сложна в воплощении. В физические основы лазерного сплавления (L-PBF) заложены: лазерная физика, оптика, точная механика, физика твердого тела, газодинамика, и др. Процесс лазерного сплавления можно интерпретировать как результат наложения и взаимодействия множества подпроцессов, включающих поглощение и отражение лазерного излучения дисперсной средой, тепло- и массоперенос, фазовые превращения, подвижную границу раздела между твердой и жидкой фазой, газо– и гидродинамику, химические реакции и т.д. [12–15].
Основные параметры, влияющие на процесс лазерного сплавления (L-PBF), и, в конечном итоге, на качество изготавливаемых деталей, можно представить в виде Ishikawa диаграмм [16–19]. В работе [17] сообщается о более чем 130 входных параметрах, влияющих в целом на процесс лазерного сплавления. Кроме того, 49 параметров были описаны в работе [18]. Среди этих параметров можно выделить группу заранее предопределенных, к которым можно отнести, например, свойства используемого материала – плотность, температуру плавления и кипения, теплопроводность, удельную теплоемкость, коэффициент поверхностного натяжения, коэффициент поглощения на длине волны используемого лазерного источника и т.д. В группу изменяемых или контролируемых параметров входят мощность лазерного излучения, диаметр фокального пятна, скорость сканирования, толщина порошкового слоя, уровень кислорода в окружающей атмосфере, скорость потока защитного газа, и др. В целом параметры, оказывающие наибольшее влияние на процесс лазерного сплавления (L-PBF), можно разделить на три большие группы: “оборудование”, “материал”, “процесс изготовления”. Нередко изменение одного из параметров приводит к изменению нескольких других параметров, что может привести к появлению дефектов.
2.2.1. Исходный материал для процесса лазерного сплавления
Одной из наиболее важных групп параметров является “материал”. Свойства материала влияют на дальнейший выбор всех остальных параметров процесса. Химический состав, теплофизические, оптические, металлургические, механические и реологические характеристики материала играют ключевую роль в лазерном сплавлении (L-PBF). Обычно в лазерном сплавлении (L-PBF) используют металлические порошки размером до 60 микрон. Грануломорфометрические свойства, такие как форма и размер частиц, шероховатость, удельная площадь поверхности, распределение (доля) частиц порошка по размерам, влияют на процесс нанесение слоя, его гомогенность, коэффициент поглощения лазерного излучения.
В работе [20] представлен анализ связи свойств порошка, формирования слоя, влияние параметров на процесс и на качество L-PBF–детали. Наиболее подходящими для лазерного сплавления (L-PBF) являются порошки со сферическими частицами, которые имеют высокую плотность упаковки, хорошую текучесть, и равномерно наносятся на подложку. Порошки, содержащие фракции мелких частиц (1–2 микрон и менее), легко агломерируются и не могут быть нанесены на рабочую платформу должным образом. Крупные порошки, с размером частиц более 60 микрон, не используют в L-PBF, так как для их применения потребуется наносить достаточно толстые слои, что приведет к потере точности изготовления и значительно увеличивает риск повышения пористости, с последующим ухудшением механических свойств деталей.
2.2.2. Выбор стратегии сканирования при изготовлении изделий в процессе лазерного сплавления
Стратегия лазерного сканирования – это шаблон, по которому движется лазерный луч в процессе плавления порошкового материала. Существует множество возможных стратегий сканирования: однозонные, многозонные, сканирование в одном направлении или зигзагообразное (вперед–назад), стратегия сканирования полосами или островками, спиральное сканирование, изменение направления сканирования для каждого последующего слоя и т.д., и каждая из них может применяться для достижения определенных целей [22–24].
Оптимальный выбор стратегии лазерного сканирования определяет морфологию поверхности переплавленного слоя и помогает достичь равномерной толщины при нанесении последующих слоев порошка или улучшает шероховатость поверхности и точность изготовления. Специальные стратегии применяют для достижения минимально возможных остаточных напряжений. Так наилучшее качество поверхности достигается при применении стратегии с повторным сканированием, а для минимизации остаточных напряжений используют “островную” стратегию со сканированием областей (“островков”) в шахматном порядке [23].
В современных системах лазерного сплавления (L-PBF) для изготовления сложных объектов используют различные стратегии сканирования и параметры процесса для определенных областей детали, например, для первых и последних слоев, для основной части и контура, преконтурной и постконтурной обработки, для навесных частей детали, и т.д. Все это делается с целью улучшения металлургического контакта между слоями, качества поверхности, или даже для специальной термической обработки с целью изменения микроструктуры, а значит, и свойств материала в определенных областях изготавливаемой детали. Современные многолучевые лазерные (L-PBF) системы (табл. 1) могут значительно расширить спектр применяемых стратегий сканирования и тем самым улучшить механические свойства деталей, добиться уникальной микроструктуры, а также уменьшить остаточные напряжения.
2.2.3. Выбор оптимальных параметров системы лазерного сплавления с помощью технологии одиночных треков
Свойства детали, изготовленной по технологии лазерного сплавления (L-PBF), сильно зависят от свойств каждого отдельного трека и каждого отдельного слоя, формируемого в слое порошка. Углубленное изучение механизмов образования одиночных лазерно–расплавленных треков и нестабильности расплавленной ванны, предложенное в работе [25], позволяет не только успешно подбирать оптимальные параметры работы системы лазерного сплавления (L-PBF), но и экономно использовать весь спектр коммерчески доступных металлических порошков для аддитивных технологий. В результате взаимодействия лазерного излучения с предварительно нанесенным слоем металлического порошка формируется единичный трек, который является фундаментальной единицей трехмерных L-PBF-объектов. Единичные треки формируют отдельные слои, а слои формируют объемное изделие. И это уже своего рода конструкция, состоящая из огромного количества единичных треков, от качества которых в конечном итоге зависит качество всей детали, так как невозможно построить высококачественную конструкцию из некачественных конструктивных элементов. Технология подбора параметров системы лазерного сплавления методом одиночных треков заключается в следующем: 1) получение одиночных треков при различных параметрах процесса; 2) проведение последующего анализа целостности, регулярности и 3) анализ геометрических характеристик треков с помощью микроскопии. В случае слишком высокой мощности лазера, достаточной для кипения и испарения расплавленного материала, можно наблюдать эффект “замочной скважины” (keyhole effect), хампинг-эффект, образование сателлитов и множественных брызг, которые ведут к пористости в 3D изделии. При недостаточной мощности лазера глубина ванны расплава уменьшается, и треки превращаются в последовательность отдельных капель (balling effect) [25], что также ведет к пористости изделия. Таким образом, при формировании единичного трека всегда очень важно соблюдать баланс между параметрами процесса. Также надо помнить, что существует несколько оптимальных наборов параметров для мощности лазерного излучения, толщины порошкового слоя и скорости сканирования, которые обеспечивают высокое качество единичных треков и, наконец, 3D-изделия.
2.2.4. Контроль качества изделий, полученных лазерным сплавлением
Изготовление детали сложной формы и относительно большого размера может продолжаться достаточно длительное время: от нескольких дней и более. Поэтому для предотвращения непредвиденных ситуаций информация о ходе процесса построения, оперативный мониторинг и контроль качества являются одними из актуальнейших задач. Для L-PBF-технологии очень важен непрерывный контроль, измерение и документирование основных параметров процесса обработки (например, мощности лазера, размера фокального пятна, распределения интенсивности излучения, скорость сканирования), порошкового слоя (наблюдение за слоем оптическими методами) и свойств порошка (контроль текучести, распределение частиц по размерам, оценка морфологии).
Хотя L-PBF-процесс достаточно стабилен, отклонение параметров процесса за определенные границы значений приводит к нестабильности процесса и ухудшению качества изготавливаемой детали (шероховатость, пористость, плохие механические свойства). Методы онлайн мониторинга в процессе L-PBF являются важным аспектом внедрения аддитивных технологий в индустрию. Необходимо разработать дополнительные решения для мониторинга, чтобы осуществлять контроль не только параметров процесса, но и оценивать качество консолидированного материала в каждом слое. Предлагаемая система должна создавать отчеты в режиме реального времени и на выходе представлять “сертификат качества” произведенных L-PBF-объектов с указанием местоположения возможных дефектов.
Онлайн мониторинг также является источником для разработки систем управления с обратной связью для оптимизации качества изготавливаемой продукции, чтобы не только регистрировать дефекты, но и динамически исправлять проблемные места во время процесса L-PBF. Результаты мониторинга должны быть соотнесены с данными неразрушающего контроля, такими, например, как компьютерная томография (КТ), и разрушающего контроля, например, механическими испытаниями. Корреляция мониторинга и качества изделий служит базой для разработки рекомендаций построения деталей, а также допустимых размеров и типов дефектов.
В настоящее время отдельные виды мониторинга начинают успешно внедрять в программные комплексы L-PBF-систем всеми ведущими изготовителями данного оборудования. Так фирма EOS использует EOSTATE – модульное решение, состоящее из четырех блоков, и предназначенное для мониторинга всей производственной цепочки L-PBF-процесса и контроля качества изготавливаемых деталей [26]. Похожий по функциональности мониторинг Additive.Quality разработала и внедряет в свои системы фирма SLM Solutions [27]. Кроме того, используя современные программные комплексы для компьютерного моделирования аддитивных процессов (MSC Software Simufact Additive, Ansys Additive Print, Siemens NX, Autodesk Netfabb и многие другие), можно анализировать процесс при различных параметрах, прогнозировать отклонения формы детали от цифровой модели, остаточные напряжения, процесс нанесения порошкового слоя и т.д. Таким образом, современные оборудование и программные комплексы позволяют не только изготавливать L-PBF-детали высочайшего качества, но и контролировать процесс, и получить сертификат гарантии качества. Надежность и повторяемость являются жизненно важными задачами для этой инновационной технологии.
3. СПЛАВ Ti–6Al–4V
Для того чтобы понять специфику L-PBF-процесса, в рамках данного обзора мы рассмотрим особенности структуры и механических свойств образцов титанового сплава Ti–6Al–4V, полученных с помощью лазерного 3D-принтера. Для начала приведем краткие характеристики этого сплава, получаемого традиционными методами.
3.1. Промышленное получение сплава Ti–6Al–4V. Деформируемый сплав Ti–6Al–4V (Grade 5, российский аналог ВТ6) относится к классу титановых сплавов с двухфазной α-(ГПУ) + β-(ОЦК)-структурой, подвергающейся упрочнению при термической обработке [28]. Основными легирующими элементами для этого сплава являются алюминий и ванадий. Легирование алюминием повышает прочность и жаропрочность, а дополнительное легирование ванадием повышает не только значения механической прочности, но также приводит к увеличению пластичности [29]. Ti–6Al–4V – самый используемый титановый сплав класса α + β и наиболее распространенный из всех титановых сплавов (занимает более 50% мирового титанового производства) благодаря своим уникальным физическим и механическим свойствам. В связи с этим область применения сплава велика: от медицины до аэрокосмической промышленности. Этот коммерчески важный сплав активно используют в судостроении, поскольку он обладает низкой склонностью к солевой коррозии и высокой степенью технологичности, сплав хорошо сваривается всеми промышленными видами сварки, а также и диффузионной. Прочность и пластичность сварного шва сплава Ti–6Al–4V практически не отличается от основного металла [30]. Рабочая температура сплава Ti–6Al–4V (ВТ6) авиационного назначения ∼350°С [31]. Низкий удельный вес наряду с высокой механической и усталостной прочностью и высокой коррозионной и эрозионной стойкостью обуславливает его использование в авиационных газотурбинных двигателях [32].
Сверхчистый сплав Ti–6Al–4V ELI (Grade 23) медицинского назначения обладает хорошей биохимической совместимостью, коррозионной стойкостью, он немагнитен и имеет низкий удельный вес по сравнению со сталями [33]. В отличие от Grade 5, Grade 23 медицинского назначения имеет ограниченный набор химических элементов, используемых для микролегирования, и меньшее содержание кислорода и азота [34, 35]. Сплав Ti–6Al–4V (Grade 5) содержит менее 0.2 мас. % кислорода, в то время как в сплаве медицинского назначения Ti–6Al–4V ELI (Extra Low Interstitial) содержание кислорода составляет менее 0.13 мас. %. Прочность сплава Ti–6Al–4V ELI при комнатной температуре ниже, чем конструкционного Grade 5, а пластичность и усталостные свойства выше [36]. В медицине сплав Ti–6Al–4V используют для производства ортопедических постоянных и временных протезов, а также в стоматологии для зубных имплантатов [33].
Сплав Ti–6Al–4V имеет хорошую высокотемпературную пластичность и легко деформируется в разогретом состоянии. Термическая обработка титановых сплавов не позволяет провести нормализацию структуры, поэтому для получения требуемого структурного состояния необходимо проведение термомеханической обработки (ТМО). Этапы термической обработки включают: гомогенизацию (1050°С – 30 мин) с последующей закалкой, отжиг в двухфазной α + β-области с последующим охлаждением, а также может быть произведена упрочняющая термообработка – старение (600°С – 1 ч). Титан активно взаимодействует с атмосферными газами и водородом при повышенных температурах, поэтому все термические обработки титановых слитков проводят в вакууме. Высокотемпературную деформацию слитков Ti–6Al–4V, позволяющую снизить размер исходного зерна, проводят как в β-, так и в α + β-области. Формирование мелкозернистой (размер зерен α-фазы 0.2–10 мкм) микроструктуры в сплаве было обнаружено после многоходовой всесторонней изотермической ковки в двухфазной α + β-области [37, 38]). В промышленном варианте нагрев заготовок проводят в защитной атмосфере, а деформацию и последующее охлаждение слитка производят на воздухе. После чего удаляют поверхностный окисленный слой путем дробеструйной обработки и травления, затем проводят релаксационный неполный отжиг в вакууме для снятия остаточных внутренних напряжений после механообработки и удаления водорода, образовавшегося после травления заготовки [30, 39].
Рекристаллизационный (полный) отжиг сплава приводит к разупрочнению или устранению остаточных внутренних напряжений, что сопровождается изменением механических свойств. В зависимости от температуры, отжиг может быть без полного фазового перехода (ниже температуры α → β-превращения) или сопровождаться полным фазовым переходом (отжиг с фазовой перекристаллизацией в области выше температуры α → β-превращения).
Морфология структуры сплава Ti–6Al–4V зависит от температуры термической выдержки и скорости охлаждения. Полностью равноосную (глобулярную) α + β-структуру можно получить после гомогенизации и последующего рекристаллизационного отжига (800°С), если скорость охлаждения от температуры рекристаллизации будет достаточно низкая [40]. Глобулярно–пластинчатая (бимодальная) структура, в которой α‑составляющая состоит из первичных равноосных α-зерен и вторичных областей α-фазы пластинчатой (Видманштеттовой) морфологии, формируется при ступенчатой термомеханической обработке, включающей: гомогенизацию (I), деформацию в α + β-области (II), рекристаллизацию в α + β-области (III) и старение (IV) [40]. Формирование такой структуры способствует повышению вязкости разрушения и ударной вязкости при сохранении высоких пластических свойств [30]. Объемная фракция ОЦК–β-фазы после гомогенизации и закалки составляет 5–6%, после полного рекристаллизационного отжига объемная фракция ОЦК-фазы увеличивается до 14–15% [29].
В России титановый прокат ВТ6 выпускают согласно ГОСТ 19807–91 и поставляют в отожженном состоянии либо в технически упрочненном состоянии после закалки и старения [28]. По требованиям, предъявляемым к медицинским материалам, сплав Ti–6Al–4V должен иметь двухфазное α + β-состояние и глобулярную равновесную структуру [34]. Листы, полосы (σb = 860 МПа, δ = 8%) и прутки (σb = 860 МПа, δ = 10%) сплава Ti–6Al–4V медицинского назначения поставляются в отожженном состоянии и не должны иметь трещин на поверхности. Отжиг листов, тонкостенных труб, профилей и деталей из них обычно проводят при 750–800°С – 3.5 ч с последующим охлаждением вместе с печью, что позволяет предотвратить их коробление.
Как известно, титан обладает высокой химической активностью по отношению к атмосферным газам и водороду. Титан коррозионно устойчив до температур 500–550°С [41]. При нагреве до 600°C титан активно поглощает кислород, а при нагреве до 700°C и выше – азот. При высоком содержании этих химических элементов в сплаве возможно формирование фаз внедрения – оксидов и нитридов, в значительной мере повышающих твердость и снижающих пластичность материала [30].
Активное газонасыщение поверхностного слоя титановых полуфабрикатов происходит при температурах свыше 500°C во время технологических операций, связанных с высокотемпературным нагревом без защитной атмосферы (горячей деформации, термообработки) [41]. На поверхности слитка в этом случае образуется окалина, а также происходит диффузия кислорода вглубь металла. Под окалиной формируется газонасыщенный слой, толщина которого может достигать 2 мм. Кислород и азот стабилизируют в титановых сплавах альфа-фазу, в связи с чем этот насыщенный кислородом и азотом слой называют альфированным (alpha case layer) [42, 43]. Механические и физические свойства альфированного поверхностного слоя резко отличаются от свойств основного металла. Температура полиморфного превращения в этом слое значительно выше, объемный эффект превращения меньше, а коэффициент линейного расширения больше, чем у основного металла. Это приводит к образованию трещин во время остывания слитка.
В отличие от водорода, кислород и азот невозможно удалить из титана вакуумным отжигом, поэтому при проведении каждой последующей технологической операции требуется тщательная механическая (пескоструйная, гидропескоструйная [41]) и химическая очистка поверхности титанового слитка от окалины и альфированного слоя, поскольку окисленные и газонасыщенные слои резко снижают механические и эксплуатационные свойства сплава. При завершении технологического процесса получения титанового полуфабриката отходы составляют до 70% от массы исходной шихты. При этом в отличие от большинства металлов, при производстве титановых сплавов титановые отходы используются ограниченно [44]. Все это в значительной мере увеличивает себестоимость производства с одной стороны, и влияет на экологию, с другой, обуславливает поиск альтернативных способов производства титановых изделий.
3.2. Фазовые превращения в сплаве Ti–6Al–4V. Сплав Ti–6Al–4V имеет широкое промышленное применение, поэтому сегодня свойства, микроструктура и фазовые превращения в нем хорошо изучены. На рис. 4 приведен изотермический разрез равновесной диаграммы состояния Ti–Al–V при 1000°С, построенный с помощью программного пакета CALPHAD [45].
Как показано на рис. 4, в системе Ti–Al–V образуются как твердые растворы на основе титана, ванадия и алюминия, так и интерметаллидные фазы. Образование интерметаллидных фаз связано с высокой химической активностью алюминия.
Квазибинарный разрез для сплава Ti–6Al–4V приведен на рис. 5. В равновесном состоянии при комнатной температуре сплав Ti–6Al–4V состоит из двух фаз – β (ОЦК, пространственная группа Im–3m, a = 0.332 нм) и α (ГПУ, пространственная группа P63/mmc, а = 0.295 нм, с = 0.468 нм, с/а = = 1.586). Растворимость ванадия, который является β-стабилизатором, в α-фазе в сплаве Ti–6Al–4V составляет ∼2 мас. % [47]. Между фазами выполняются ориентационные соотношения Бюргерса [48]:
Кроме равновесных фаз, в сплаве Ti–6Al–4V возможно образование метастабильных мартенситных фаз и интерметаллидной фазы Ti3Al (α2, D019, ГПУ, a = 0.574 нм, c = 0.498 нм, пространственная группа P63/mmc, прототип Mg3Cd). Кристаллическая решетка этой интерметаллидной фазы когерентно связана с кристаллической решеткой α-фазы. Фаза α2 гомогенно зарождается внутри α-областей в результате длительного (300–576 ч) старения в диапазоне температур 500–600°С [49]. Температура полиморфного β → α-превращения в сплаве Ti–6Al–4V находится в диапазоне температур 980–1000°С (978°С для Grade 23) и зависит от содержания микролегирующих добавок. Например, при увеличении содержания кислорода, который является альфа-стабилизатором, температура полиморфного превращения увеличивается, а при увеличении содержания железа (бета-стабилизатора), она понижается [36]. Типичная равновесная структура промышленного сплава Ti–6Al–4V приведена на рис. 6.
Рис. 6.
Микроструктура промышленного сплава Ti‒6Al–4V ELI, ПЭМ: (а) светлопольное изображение; (б) микроэлектронограмма.
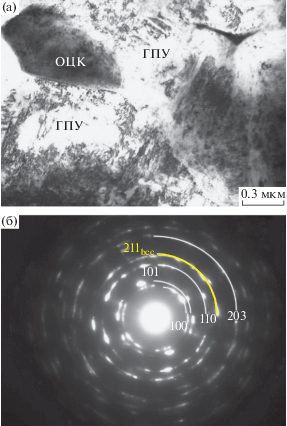
Две мартенситные фазы: α' (ГПУ, пространственная группа P63/mmc, a = 0.293 нм, c = 0.467 нм) и α" (базоцентрированная орторомбическая решетка, пространственная группа Cmcm, a = 0.3152 нм, b = 0.4854 нм, c = 0.4642 нм) [50, 51] могут образовываться при быстрой закалке сплава из различных температурных областей. Мартенситная α'‑фаза образуется при закалке из высокотемпературной β-области (выше температуры α → β-полиморфного превращения), α"-фаза образуется при закалке из промежуточной α + β области (750–850°C) [52, 53]. Ориентационные соотношения между кристаллическими решетками мартенситных фаз и кристаллической решеткой ОЦК β-фазы удовлетворяют следующим выражениям:
α'-Мартенсит образуется, когда концентрация ванадия в β-фазе составляет менее 4.27 ат. % (4.65 мас. %). В пересыщенной ванадием мартенситной α"-фазе (5.45–8.0 мас. % V) параметры решетки зависят от состава сплава [55]. В сплаве Ti–6Al–4V эта фаза образуется в локализованных областях с повышенной концентрацией ванадия 9–13 мас. % [52].
Морфологически области с орторомбическим α"-мартенситом обычно характеризуются наличием микродвойников, образующихся внутри пластин [52, 55]. Появление α'-мартенсита приводит к повышению прочности и снижению пластичности сплава, α"-мартенсита – к снижению прочности и повышению пластичности [51, 52, 56]. При старении обе мартенситные фазы (α'- и α"‑фаза) распадаются с образованием равновесных α- и β-фаз [49].
4. СТРУКТУРА И ФАЗОВЫЕ ПРЕВРАЩЕНИЯ В СПЛАВЕ Ti–6Al–4V, ПОЛУЧЕННОМ ЛАЗЕРНЫМ СПЛАВЛЕНИЕМ
4.1. Порошок для лазерного сплавления и способы его получения
Сегодня изделия, получаемые в процессе лазерной 3D-печати достаточно дорогие, поскольку в их стоимость входит стоимость порошка (например, титанового $200–$400 за килограмм). Получение высококачественных металлических порошков для 3D-печати и снижение стоимости их производства являются самыми важными задачами для быстрого развития аддитивных 3D‑технологий.
На рис. 7 приведено изображение порошка Ti–6Al–4V (ELI), используемого в L-PBF-процессе. Это типичная морфология порошка, полученного методом индукционной вакуумной плавки вращающегося электрода с распылением падающих с него капель инертным газом (EIGA, Electrode Induction Melting Inert Gas Atomization). Этот метод используют для получения порошков реактивных металлов – Ti, Zr, Hf, V, Pt, Ir, Nb, Mo, и т.д., для которых плавка в керамических тиглях затруднена даже в условиях вакуума. Суть этого метода получения порошков заключается в следующем: прутки после предварительной выплавки в форме электродов проходят индукционную вакуумную плавку и распыляются инертным газом без использования плавильного тигля через систему форсунок. Диаметр сферических металлических частиц регулируется расположением форсунок и давлением инертного газа [57]. Особенностью этого метода является возможность получать мелкодисперсные порошки сферической формы, что обеспечивает максимальную плотность металлического изделия при последующем его изготовлении в 3D-принтере. Недостатком метода является высокая стоимость получаемого материала за счет многочисленных технологических переделов, невысокая скорость распыливания – около 0.5 кг/с [57], образование в порошинках внутренних пор, заполненных газом, а также химическая неоднородность за счет образования дендритной структуры и формирование конгломератов из крупных и мелких частиц.
Лучшее качество порошка (в частности, Ti‒6Al–4V) может быть получено с помощью центробежной плазменной обработки (PREP – Plasma Rotating Electrode Process), в которой плавление металлического прутка производят посредством высокоскоростного потока ионизированного инертного газа [57]. Плазменная обработка (сфероидизация) также может быть использована для улучшения качества уже готового низкосферичного порошка. Известно, что плазменная обработка снижает геометрические недостатки поверхности порошинок, способствует снижению производственных затрат процесса получения качественного порошка, обеспечивает однородность и сыпучесть порошка, устраняет внутренние дефекты порошинок, повышает его чистоту за счет высокой температуры плазмы [58].
Чистота исходного порошка для лазерного сплавления является существенным моментом [59, 60]. Низкое качество исходного порошка при лазерной 3D-печати, даже при выборе оптимальных параметров работы L-PBF-системы, приводит к формированию внутренних дефектов (каверн и пор), нарушению химической однородности, которые не всегда удается минимизировать последующими термическими или термомеханическими (горячее изостатическое прессование, ГИП) обработками. Как было обнаружено в работах [61, 62], при проведении термического отжига после горячего изостатического прессования происходит восстановление внутренней пористости СЛС-материала. Все это ведет к снижению эксплуатационных свойств полученного 3D-изделия. Также некоторые авторы рекомендуют использовать высококачественный порошок после плазменной сфероидизации для исключения последующего горячего изостатического прессования, которое применяют для устранения газовых пор и повышения плотности полученного изделия [63].
В работе [64] была проведена оценка возможности вторичного использования титанового порошка (re-usage). Авторы показали, что при соблюдении условий работы в защитной среде никаких существенных изменений в химическом составе и в структуре порошка после 11 циклов не обнаружено.
4.2. Структура сплава Ti–6Al–4V, полученного лазерным сплавлением
Учитывая послойный характер построения, материалы, полученные лазерным сплавлением, фактически можно рассматривать как слоистые композиционные материалы с направлением слоев, расположенных перпендикулярно направлению построения изделия в 3D-принтере. На рис. 8 приведены фотографии микроструктуры сплава Ti–6Al–4V, полученные в различных сечениях образца. Структура сплава состоит из пластин α′ мартенсита, образовавшегося в объеме зерен первичной β-фазы, вытянутых вдоль направления построения. В поперечном сечении размер зерен составляет ∼100–200 мкм (рис. 8а). Внутри зерен хорошо видны мартенситные пластинки α'-фазы. Как показали исследования [62], направление роста зерен совпадает с направлением [100] кубической β-фазы.
Рис. 8.
Микроструктура различных сечений образца Ti–6Al–4V: (а) – в направлении перпендикулярном построению; (б) вдоль направления построения, (оптическая микроскопия).
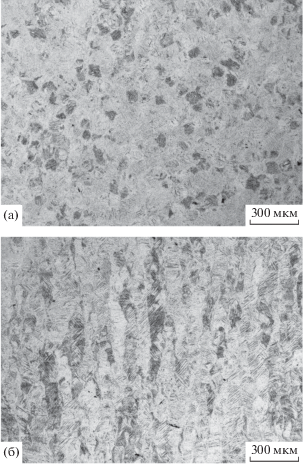
Появление ростовой текстуры в металлах, полученных лазерным сплавлением, связано непосредственно с технологическими особенностями послойного изготовления. Это является существенным моментом в формировании структуры, поскольку оказывает влияние на физические и механические свойства 3D-изделия. Наличие текстуры в Ti–6Al–4V–образцах, полученных лазерным сплавлением, было исследовано в работах [62, 65–67]. Образующаяся в образцах кубическая ❬100❭ (001) текстура ОЦК–бета-фазы сходна с ОЦК-текстурой, наблюдаемой в ОЦК-металлах при плоской прокатке, когда ось текстуры лежит в направлении проката, а плоскость текстуры совпадает с плоскостью проката. Таким образом, образование ГПУ-текстуры в СЛС-титановых образцах можно рассматривать как текстурно–фазовый переход с образованием (11–20) – (НН), [1–100 ] – (НП), [0001] – (ПН) текстуры в α'-фазе. Где НН – нормаль к плоскости прокатки, НП – направление прокатки, ПН – поперечное направление [66, 67]. Слабая ГПУ текстура сохраняется в образце и после неполного релаксационного отжига при 650°С в течение 3 ч (рис. 9).
Рис. 9.
Результаты текстурного анализа образца Ti–6Al–4V ELI, полученного лазерным сплавлением, EBSD: (а) исходное состояние (as-build); (б) после релаксационного отжига 650°C в течение 3 ч.
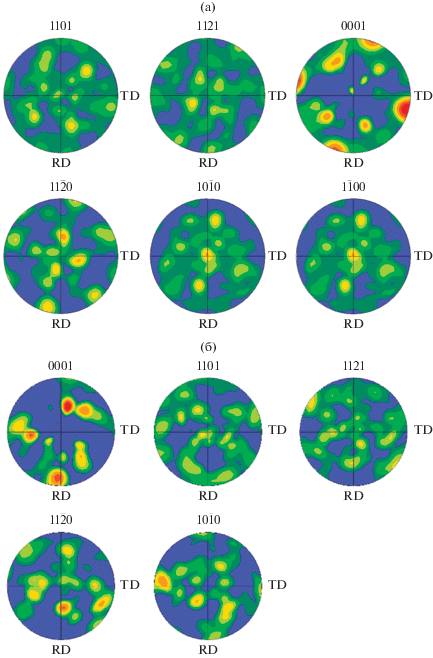
Благодаря высокой скорости процесса лазерного сплавления (L-PBF) в образцах Ti–6Al–4V формируется α'-мартенситная структура. Кроме того, на рентгенограммах образцов не наблюдаются дифракционные линии ОЦК β-фазы [65, 67–70]. Таким образом, учитывая фазовую чувствительность рентгеновских аппаратов, можно сказать, что присутствие бета фазы в Ti–6Al–4V образцах, полученных лазерным сплавлением, составляет менее 5%. Иногда слабые дифракционные линии бета фазы могут быть обнаружены на дифрактограммах в больших углах, что также свидетельствует о присутствии текстуры и малом количестве этой фазы в СЛС–образцах. По данным просвечивающей электронной микроскопии после релаксационного отжига 650°C – 3 ч (область α + β на равновесной диаграмме состояния) в структуре сплава Ti–6Al–4V ELI обнаружено присутствие бета-фазы в виде дисперсных нано выделений [62].
В ряде работ были предприняты попытки получения двухфазной α + β-структуры в Ti–6Al–4V образцах непосредственно сразу после их изготовления в лазерном 3D-принтере [71–73]. Путем варьирования режимов работы лазерного принтера авторам этих работ удалось получить образцы Ti–6Al–4V ELI с различной морфологией фаз и фазовым составом: от полностью мартенситной α'-структуры до пластинчатой (не мартенситной) α + β. Присутствие β-фазы в сплаве в работе [71] было определено с помощью сканирующей электронной микроскопии по контрастности на снимках, а также по изменению механических свойств полученных образцов. Интересно, что прочность образцов с разной структурой и фазовым составом практически одинаковая (980 МПа), а пластичность различная. В образце с двухфазной α + β-пластинчатой структурой она составила 11% [71].
Снижение пластичности в сплаве с мартенситной структурой авторы [71] также объясняют присутствием нерасплавленных порошинок и большим размером пор. В работе [72] авторы также получили пластинчатую α + β-структуру, при этом кроме варьирования параметров процесса L-PBF был использован предварительный нагрев подложки до 170°С (200°C [73]). Присутствие β‑фазы в сплаве подтверждено данными рентгеноструктурного анализа, сканирующей и просвечивающей электронной микроскопии. В отличие от результатов механических испытаний, полученных в работе [71], образцы с однофазной мартенситной α' структурой показали выше прочность (1150 МПа) и более высокую пластичность (15%), по сравнению с образцами с пластинчатой α + β структурой, для которых прочность составила 1105 МПа, а пластичность 12% [72]. Очень медленное сканирование в лазерном 3D-принтере способствует не только образованию пластинчатой α + β-структуры, но и формированию интерметаллидной Ti3Al-фазы [73].
Тщательное исследование структуры с помощью просвечивающей электронной микроскопии, проведенное в [53, 69, 74–76], показало, что структура сплава Ti–6Al–4V, полученного лазерным сплавлением, неоднородна и состоит из областей мартенситных фаз α' и α". Особенностью α'–мартенсита в структуре сплава Ti–6Al–4V, полученного лазерным сплавлением, является присутствие двойников с плоскостями двойникования системы {10–12}❬–1011❭. Внутри двойниковых пластин были обнаружены дефекты упаковки [62]. Двойники сохраняются в структуре сплава и после релаксационного отжига [62].
Двойники системы {10–12} являются двойниками растяжения, они активируются только при растяжении вдоль оси с матрицы. Система двойникования {10$\bar {1}$2}ГПУ в титане имеет самое низкое критическое скалывающее напряжение сдвига для двойникования и приводит к деформации 16.7% в направлении (1.00) в ГПУ структуре [76]. Присутствие двойников растяжения в структуре означает наличие высокого уровня предшествующих сжимающих напряжений (рис. 10).
α"-Мартенсит с орторомбической кристаллической решеткой в сплаве Ti–6Al–4V, полученном лазерным сплавлением, имеет типичную пластинчатую морфологию с внутренними поперечными двойниками [69]. Ширина внутренних двойников составляет от 10 до 20 нм. Такие мартенситные области были обнаружены в локальных областях, обогащенных ванадием (рис. 11).
Появление орторомбического α"-мартенсита в сплаве Ti–6Al–4V связано с циклическим нагревом слоев материала во время изготовления образца в 3D-принтере. Это еще одна особенность процесса лазерного сплавления, которая оказывает влияние на химическую однородность формирующегося образца и которую необходимо учитывать при изготовлении деталей этим методом. Особенно это существенно для материалов, испытывающих фазовые переходы в неравновесном состоянии при промежуточных температурах. Благодаря послойному способу изготовления, предыдущие слои образца несколько раз нагреваются и охлаждаются, таким образом, происходит процесс многократного термоциклирования [69, 78]. Температурный диапазон термоциклирования может быть широк, так как он связан с технологическими параметрами работы 3D-принтера. А также температуры и скорости охлаждения в процессе лазерного сплавления зависят от параметров и геометрии изделия.
5. МЕХАНИЧЕСКИЕ СВОЙСТВА СПЛАВА Ti–6Al–4V, ПОЛУЧЕННОГО ЛАЗЕРНЫМ СПЛАВЛЕНИЕМ
5.1. Структурные параметры, влияющие на механические свойства L-PBF Ti–6Al–4V
L-PBF-материалы характеризуются мелко-кристаллической структурой с присутствием химической негомогенности и неравновесных фаз. В случае высокой пористости, механические характеристики полученного материала также обычно низкие, и в значительной степени определяются не микроструктурой, а пористостью [79].
Дополнительным фактором, влияющим на прочностные характеристики материалов, изготовленных аддитивными технологиями, является содержание примесей внедрения, которые повышают прочностные характеристики, но негативно влияют на пластичность титановых сплавов [80]. В образцах, свойства которых приведены в табл. 2, содержание примесей внедрения не измеряли, поэтому оценить количественно их влияние на свойства затруднительно. Можно предполагать некоторое повышение содержания кислорода и водорода из-за адсорбирования поверхностью порошинок молекул воды. Формирование оксидов и других примесей может происходить при изготовлении, транспортировке и хранении порошка, а также при его многократном использовании. Исследования, проведенные в работе [60], показали, что содержание кислорода и азота в полученных методом лазерного сплавления Ti–6Al–4V образцах при использовании свежего порошка и оптимальных параметров процесса в соответствующей защитной атмосфере находится в пределах нормы.
Таблица 2.
Механические характеристики сплава Ti–6Al–4V, изготовленного с помощью аддитивных технологий без термообработки (as-built)
Технология | σ0.2, MПa | σВ, MПa | δ, % | Микроструктура | Ссылка |
---|---|---|---|---|---|
Лазерное сплавление | 990–1333 | 1095–1407 | 2–8.5 | α'-мартенсит | [74, 80] |
980–1130 | 1050–1165 | 11–12 | α + β | [70, 71, 81, 82] | |
1098–1150 | 1100–1265 | 9.6– 15 | α'-мартенсит | [62, 81–83] | |
1060–1070 | 1200–1230 | 10–11 | α'-мартенсит | [26] | |
Электронно-лучевое сплавление | 883–1150 | 953–1200 | 12–25 | α + β | [84–87] |
Таблица 2 содержит механические характеристики сплава Ti–6Al–4V, изготовленного методами лазерного сплавления с плотностью 99.5% и выше. Из таблицы видно, что сплав Ti–6Al–4V, изготовленный методом лазерного сплавления, имеет более высокие прочностные характеристики, чем материал, полученный при помощи электронно-лучевого сплавления. В случае электронно-лучевого сплавления вследствие предварительного нагрева, а также медленного охлаждения материала в вакуумной камере, образуется структура, содержащая равновесные α + β-фазы. Прочность этих материалов определяется дисперсностью (lamellar or platelet thickness) α-фазы, а пластичность достигает 25% [85–88]. Из-за разных условий охлаждения различных частей изделия в камере в изделиях, изготовленных электронно-лучевым спеканием, наблюдается градиент микроструктуры и свойств по сечению [86–89]. Механические свойства сплава Ti–6Al–4V, изготовленного методами аддитивных технологий, определяются в первую очередь микроструктурой и дефектами материала, которые, в свою очередь, зависят от метода и параметров изготовления (мощности лазера, диаметра пятна, скорости сканирования лазера, толщины порошкового слоя, стратегии сканирования и др.).
При лазерном сплавлении в отсутствие предварительного нагрева платформы, скорости охлаждения высоки, что ведет к образованию α'-мартенсита [75, 81, 89–91]; как было описано раньше, β-фаза обычно не обнаруживается или образуется в незначительных количествах. Мартенситная гексагональная α'-фаза в сплаве Ti–6Al–4V имеет кристаллографическое ориентационное соотношение с высокотемпературной β-фазой и незначительно упрочняет материал. Принято считать, что образование αʹ-мартенсита в сплаве Ti‒6Al–4V, изготовленного методами лазерного сплавления, негативно влияет на пластичность материала. Для улучшения пластичности сплава Ti–6Al–4V, изготовленного методом лазерного сплавления, были предложены альтернативные стратегии сканирования лазерного луча. Подстройкой параметров изготовления материала: мощности лазера, скорости сканирования лазера и расстояния между единичными треками, было достигнуто медленное охлаждение изготовленного компонента. Более низкие скорости охлаждения приводят к образованию равновесных α + β-фаз без дополнительной термообработки [71, 72, 82, 83]. Однако, как было показано некоторыми авторами [71, 82, 83], высокие значения пластичности 10–15% могут быть достигнуты и в материале со структурой α'-мартенсита.
Морфология поверхностей излома сплава Ti‒6Al–4V, изготовленного методами аддитивных технологий, определяется микроструктурой. В том случае, когда материал изготовлен лазерным сплавлением, на поверхности обнаруживаются фасетки квазискола, часто ориентированные вдоль направления роста мартенситной колонии [62]. На микроскопическом уровне поверхность имеет выраженные особенности чашечного/ямочного вязкого излома (рис. 12), что показывает наличие пластической деформации. Излом сплава Ti–6Al–4V, изготовленного методом электроннолучевого сплавления, обычно имеет признаки типичного вязкого разрушения [92].
Рис. 12.
Поверхность разрушения L-PBF Ti–6A–l4V образцов без термообработки после испытаний на растяжение: (а) чашечный/ямочный вязкий излом, (б) и (в) фасетки квазискола, (г) ямки.
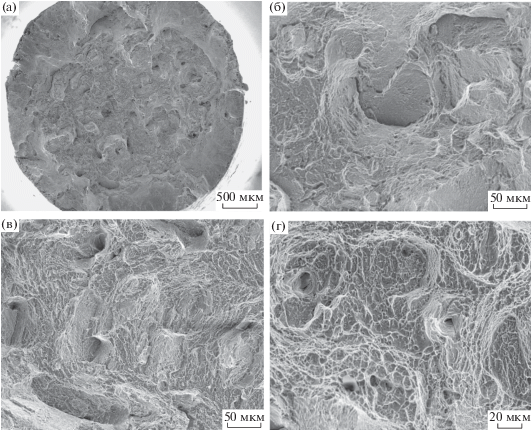
Другим методом, приводящим к формированию равновесной микроструктуры и повышению пластичности, является применение термообработки к компонентам, изготовленным методами аддитивных технологий. В объектах, изготовленных методом лазерного сплавления, обычно наблюдается высокий уровень остаточных напряжений [15, 93]. Поэтому их подвергают термообработке до того, как изделие отрезают от платформы. Поскольку микроструктура исходных СЛС-образцов в значительной степени не идентична микроструктурам образцов, полученных традиционными методами, то стандартные режимы термообработки часто не дают требуемый результат. Для термообработки СЛС-образцов сплава Ti–6Al–4V опробованы различные режимы, например, 2–4 часа при 630–680°С для снятия напряжений с последующим отжигом в вакууме [15, 94], или отжиг при 800°С в течение нескольких часов в защитной атмосфере аргона [26]. В работе [95] было проанализировано влияние режимов термообработки на фазовый состав и микроструктуру образцов Ti–6Al–4V ELI, полученных лазерным сплавлением. После двухстадийного отжига сначала 1050°С – 30 мин (охлаждение с печью) и последующего отжига 700°С – 2 ч (охлаждение с печью) микроструктура образца была бимодальная α (ГПУ) + β (ОЦК) с размером зерен ∼80 мкм. В результате первого отжига произошел распад мартенситной структуры, а второй отжиг был использован как релаксационный для снятия внутренних напряжений. Границы исходных столбчатых бета-зерен после такой обработки становятся размытыми. Снижение температуры отжига на каждой ступени (950°С – 1 ч + 650°С – 2 ч) приводит к сохранению столбчатых зерен и α′-мартенсита, размер зерен увеличивается до 100 мкм. Не очень эффективной оказалась и термоводородная обработка, в результате которой в сплаве образовалась бимодальная α-(ГПУ) + β-(ОЦК)-структура с крупной игольчатой α-фазой и вытянутыми бета зернами размером ∼200 мкм [95]. Сохранение границ исходных столбчатых зерен и формирование игольчатой α- с прослойками β-фаз после отжига образцов Ti–6Al–4V, полученных лазерным сплавлением, в области температур ниже β → α-перехода (β-transus) подтверждено и в работе [96].
Для залечивания пор эффективно используется горячее изостатическое прессование. Использование дополнительной обработки позволяет контролировать свойства в широком диапазоне и получать структуры схожие с горячекатанными изделиями [97–99], однако это ведет и к удорожанию процесса.
5.2. Влияние качества поверхности на механические свойства сплава Ti–6Al–4V, полученного лазерным сплавлением
Сопротивление усталости сплава Ti–6Al–4V, изготовленного методами аддитивных технологий, определяется шероховатостью поверхности, дефектами, остаточными напряжениями в материале и микроструктурой. Шероховатость поверхности может являться решающим фактором, влияющим на сопротивление усталости, особенно в тех частях изделия, где поверхностная обработка затруднена или невозможна (внутренние поверхности, каналы, полости). Обычно горизонтальные верхние части изделия менее шероховаты, чем вертикальные или горизонтальные нижние. Шероховатость можно интерпретировать как поверхностный дефект, вызывающий концентрацию напряжений и являющийся местом более легкого зарождения усталостной трещины на поверхности. Известно, что образцы, изготовленные методом электронно-лучевого сплавления, обычно имеют более шероховатую поверхность по сравнению с поверхностью изделий, изготовленных при помощи лазера. Это приводит к тому, что в случае испытания образцов с шероховатой поверхностью, при заданном циклическом напряжении и амплитуде образцы материала, изготовленного электронно–лучевым методом, разрушаются первыми [100, 101].
В материалах, изготовленных методом лазерного сплавления, поверхность имеет меньшую шероховатость и также зависит от направления изготовления образца. При усталостных испытаниях на изгиб образцов сплава Ti–6Al–4V, изготовленного методом лазерного сплавления, большее количество циклов до разрушения наблюдали, когда максимальные напряжения были на горизонтальной, менее шероховатой поверхности [101–103]. Микроструктура, текстура и внутренние дефекты также влияют на рост усталостной трещины. Было показано, что скорость роста трещины в сплаве Ti–6Al–4V, изготовленного методами аддитивных технологий, зависит от направления изготовления образцов (building direction) и контролируется как границами слоев, так и границами первичной высокотемпературной фазы [94, 103]. Наличие дефектов, в частности, пор, оказывает негативное влияние на сопротивление усталости сплава Ti–6Al–4V, изготовленного методами аддитивных технологий.
Механическая обработка поверхности, а также термическая обработка и горячее изостатическое прессование значительно увеличивает количество циклов до разрушения сплава Ti–6Al–4V, изготовленного методами аддитивных технологий [101]. На рис. 13 приведены сводные результаты усталостных испытаний сплава Ti–6Al–4V, полученного аддитивными технологиями. Необходимо отметить, что проведение термообработки позволяет лишь некоторым образом улучшить усталостные характеристики сплава Ti–6Al–4V, изготовленного как лазерным, так и электронно–лучевым сплавлением. В то время как после проведения поверхностной обработки в комбинации с термообработкой усталостные свойства сплава Ti–6Al–4V, полученного как электронно–лучевым, так и лазерным сплавлением, не уступают типичным свойствам для промышленного горячекатанного сплава Ti–6Al–4V (рис. 13).
Рис. 13.
Усталостная долговечность сплава Ti–6Al–4V в зависимости от способа получения и постобработки, адаптировано из [99].
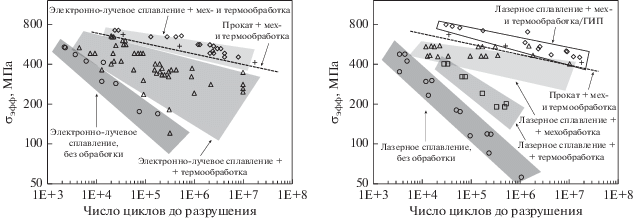
5.3. Остаточные напряжения в сплаве Ti–6Al–4V, полученном лазерным сплавлением
Как известно, неконтролируемые остаточные упругие напряжения могут приводить к ухудшению эксплуатационных свойств металла [104]. Многие исследователи указывают на образование микротрещин в полученном СЛС–образце или коробление металлических образцов, полученных лазерным сплавлением, при отрезании их от подложки [105]. В обычных материалах коробление связано с нарушением баланса между внутренними растягивающими и поверхностными сжимающими напряжениями [104]. В промышленном производстве неконтролируемые упругие растягивающие остаточные напряжения в объеме материала обычно стараются скомпенсировать контролируемыми поверхностными сжимающими напряжениями с помощью различных поверхностных обработок, таких как ультразвуковая, дробеструйная обработка или азотирование [106].
Как было показано в работе [107], упругие остаточные напряжения возникают в образце во время процесса лазерного производства в 3D принтере за счет высоких термических напряжений. При охлаждении расплавляемого лазером участка порошкового слоя возникает температурный градиент. При этом в зоне воздействия лазера возникают растягивающие напряжения, а в охлажденной зоне – сжимающие. Присутствие высокого уровня остаточных растягивающих напряжений в сплаве Ti–6Al–4V, полученном лазерным сплавлением, отмечено в нескольких работах [62, 93, 105, 108, 109]. В работе [108] в образцах Ti–6Al–4V, полученных лазерным сплавлением, были обнаружены растягивающие остаточные напряжения первого рода (макронапряжения), связанные с неоднородным накоплением дефектов в объеме материала, и микронапряжения второго рода (структурные), возникающие в пределах одного или нескольких зерен и связанные со структурными превращениями или неоднородным нагревом и охлаждением образца.
Уровень остаточных напряжений зависит от ориентации Ti–6AL–4V образца в 3D-принтере. Самые низкие остаточные напряжения обнаружены в образце, расположенном вертикально, а самые высокие – горизонтально. Эти результаты свидетельствуют о влиянии формы образца на ширину температурного диапазона, в который попадает строящийся в 3D-принтере образец при термоциклировании.
В целом, можно сказать, что физические процессы, протекающие при селективном лазерном сплавлении порошка Ti–6Al–4V и формировании образца в процессе лазерного сплавления, отличаются от процессов, которые протекают при высокотемпературной пластической деформации литого промышленного сплава. В деформированном литом образце наблюдается высокий уровень остаточных сжимающих напряжений, который возникает за счет неоднородной объемной пластической деформации, в то время как в образце, полученном с помощью лазерного сплавления, присутствуют упругие остаточные растягивающие напряжения, связанные с фазовым (мартенситным) превращением и термическими искажениями [108].
6. ТЕНДЕНЦИИ В ИСПОЛЬЗОВАНИИ L-PBF Ti–6Al–4V В МЕДИЦИНЕ
Сплавы на основе титана широко применяют для биомедицинских приложений, в частности, для производства имплантатов, так как являются биосовместимыми, легкими, немагнитными, имеют высокие прочностные и усталостные характеристики [110]. Золотым стандартом при замене костной ткани все еще является аутотрансплантат (удаление кости из другого участка у того же пациента для восстановления участка дефекта кости) [111], однако при наличии больших дефектов используются металлические имплантаты. Начиная с середины прошлого века, титан и его сплавы начали применять в ортопедии для производства пластин и винтов. В настоящее время титановые сплавы применяют для зубного протезирования, для замены тазобедренного и коленного суставов, локтевого и плечевого суставов, а также производства имплантатов позвонков. Винты, пластины, скобы, сетки и проволока из титана и его сплавов применяют для фиксации костей.
Пассивная оксидная пленка на поверхности титана обеспечивает хорошие коррозионные свойства, титановые имплантаты могут служить более 20 лет. Предполагается, что способность титана к остеоинтеграции обусловлена высокой диэлектрической проницаемостью его поверхностного оксида TiO2, который не денатурирует белки [112].
Одной из серьезных проблем, возникающих при использовании металлических имплантатов, является их высокий модуль упругости по сравнению с модулем упругости кости. Было замечено, что высокий модуль упругости материалов имплантатов, в частности, из сплава Ti–6Al–4V, приводит к эффекту “экранирования напряжений” и резорбции здоровой костной ткани [113]. Так среднее значение и 95%-ный доверительный интервал для прочности на растяжение кортикальной кости в продольном направлении составляет около 135 (104; 166) МПа и 205 (170; 239) МПа при сжатии, а модуль упругости составляет 17.9 (10.1–25.7) ГПа [114]. В поперечном направлении кортикальная кость имеет прочность и модуль упругости на 30–70% ниже. Механические свойства губчатой кости варьируются как в продольном направлении, так и от одной кости к другой, а средние значения прочности на сжатие варьируются от 2 до 5 МПа [115].
Однако L-PBF Ti–6Al–4V ELI в отожженном состоянии имеет предел прочности при растяжении 900–1000 МПа и, как и для полученного традиционным способом, высокий модуль упругости 110–120 ГПа [94], а соответствующие значения костной ткани почти в 10 раз ниже. Это обуславливает активный поиск L-PBF титановых сплавов с низкими модулями упругости.
Перспективным направлением в аддитивном производстве является изготовление ячеистых/решетчатых структур с особыми механическими характеристиками и специфической поверхностью. На рис. 14 представлено изображение ячеистых спинальных имплантатов, изготовленных в Центре быстрого прототипирования и аддитивного производства (CRPM) Центрального технологического университета (Фри-Стейт) в сотрудничестве с SASPINE Pty (ЮАР).
Подобные ячеистые периодические структуры могут быть изготовлены только методами аддитивных технологий. Эти структуры могут найти широкое применение как пористые материалы в медицинской промышленности для изготовления имплантатов [116, 117]. С помощью аддитивных технологий могут быть получены ячеистые структуры с широким диапазоном механических характеристик, в том числе с модулем упругости, близким к костным тканям.
Особенности послойного изготовления изделий из металлических порошков приводят к высокой шероховатости имплантатов, что повышает удельную площадь и вероятность прикрепления клеток к поверхности имплантатов. Но при этом важно учитывать реакцию не только костных, но и мягких тканей, а также коррозию материала. Изучение коррозионных свойств пористых L-PBF-материалов, поверхностная обработка и эвакуация порошка, а также усталостные свойства требуют отдельного анализа и являются актуальной научной проблемой [117, 118].
Таким образом, с помощью аддитивных технологий возможно создание не только индивидуальных имплантатов, у которых адаптирована форма для идеального соответствия участку дефекта кости у конкретного пациента, но и выполнена адаптация свойств самого материала, используя ячеистые структуры [114].
Ячеистые/решетчатые структуры могут найти широкое применение не только в медицине, но и в автомобильной, авиационной и аэрокосмической индустрии для изготовления облегченных изделий с высокой удельной прочностью. Моделирование периодических ячеистых структур, топологическая оптимизация размера и геометрии ячейки, а также возможность градиентно изменять параметры по сечению изделия [114, 119] открывает широкие перспективы для производства легких конструкций сложной формы с высокой удельной прочностью. Вариативность свойств достигается контролем направления структуры в изделии, изменением типа ячейки, толщины стенок и оптимизацией макропористости [120–122].
ЗАКЛЮЧЕНИЕ
Данный обзор представляет основные аспекты развития аддитивных технологий и общую информацию о большой научно-поисковой работе, которая ведется учеными всего мира по аттестации селективного лазерного сплавления для получения сложных высококачественных металлических компонентов из титанового сплава Ti–6Al–4V. Цифровая 3D-лазерная печать металлов успешно внедряется в современное промышленное производство. В настоящее время она стремительно занимает нишу в мелкосерийном производстве сложно-профильных изделий, которые очень дорого или невозможно изготовить традиционными методами.
Сегодня экспериментально подтверждено многочисленными научными работами, что as-built сплав Ti–6Al–4V, полученный методом лазерного сплавления в 3D-принтере, имеет мелкокристаллическую структуру, находится в неравновесном состоянии с высоким уровнем остаточных упругих напряжений. Однако по статическим механическим свойствам и усталостной долговечности, СЛС-сплав Ti–6Al4V после термических обработок сравним, и даже превышает, его литейный аналог.
Уникальность цифрового 3D-производства заключается в синергетике возможностей компьютерного дизайна и прямой 3D-печати изделий. Например, изготовление изделий с внутренними конформными каналами или стенками сложной формы, или с внутренними подвижными деталями без сборки. Цифровая 3D-печать способствует развитию “гибкого”, персонализированного производства с учетом пожеланий заказчика (flexible manufacturing, custom design, manufacturing by demand), которое позволит быстро перестраивать производство с одной детали на другую.
Также можно сказать, что цифровая 3D лазерная печать металлов требует подготовки новых специалистов, обладающих знаниями, сочетающими в себе инженерные и информационные технологии, материаловедение и лазерные технологии.
Работа выполнена в рамках государственного задания Минобрнауки РФ по теме “Диагностика” № АААА-А18-118020690196-3, при поддержке РФФИ (грант № 17-03-000-84), в рамках соглашения о научном сотрудничестве между ИФМ и Карлстадским университетом, Швеция, от 16.10.2015, а также при содействии международного совместного исследовательского проекта между Центральным технологическим университетом, Южная Африка, и Карлстадским университетом, Швеция, при поддержке Департамента науки и техники и Национального исследовательского фонда Южной Африки (South African Research Chairs Initiative, Grant № 97994).
Список литературы
ISO/ASTM 52900:2015(en) Additive manufacturing. General principles. Terminology [Электронный ресурс]. https://www.iso.org/ru/standard/69669.html.
ГОСТ Р 57558–2017/ISO/ASTM 52900:2015 Аддитивные технологические процессы. Базовые принципы. Часть 1. Термины и определения. [Электронный ресурс]. http://docs.cntd.ru/document/1200146332.
Сайт компании ЭОС, Германия. [Электронный ресурс]. https://www.eos.info/en.
Сайт компании Лазер, Франция. [Электронный ресурс]. https://www.ge.com/ad-ditive/who-we-are/concept-laser.
Сайт компании SLM Solution, Германия. [Электронный ресурс]. https://www.slm-solutions.com.
Сайт компании 3D System, США. [Электронный ресурс]. https://www.3dsystems.com/3d-printers/metal.
Сайт компании Renishaw, США. [Электронный ресурс]. https://www.renishaw.com/en/metal-3d-printing-32084.
Сайт компании Wohlers Associates, США. [Электронный ресурс]. https://wohlersassociates.com.
[Электронный ресурс]. https://amfg.ai/whitepaper-the-additive-manufacturing-landscape-2019.
Сайт компании Bugatti, Франция. [Электронный ресурс]. https://www.bugatti.com/media/news/2018/ world-premiere-brake-caliper-from-3-d-printer.
Сайт компании ЭОС, Германия. [Электронный ресурс]. https://www.eos.info/en/3d-printing-examples-applications/innovation-stories/aerospace-additive-manufacturing-for-ariane-injection-nozzles.
Yadroitsev I. Selective laser melting: Direct manufacturing of 3D-objects by selective laser melting of metal powders. Lap Lambert Acad. Publ., 2009. 280 p.
Meier C., Penny R., Zoua Y., Gibbs J.S., Hart A.J. Thermophysical phenomena in metal additive manufacturing by selective laser melting: fundamentals, modeling, simulation and experimentation // Annual Review of Heat Transf. 2017. V. 20. P. 241–316.
Rubenchik A., King W., Wu S. Scaling laws for the additive manufacturing // Journal of Materials Processing Technology. 2018. V. 257. P. 234–243.
DebRoy T., Wei H.L., Zuback J.S., Mukherjee T., Elmer J.W., Milewski J.O., Beese A.M., Wilson–Heid A., De A., Zhang W. Additive manufacturing of metallic components – Process, structure and properties // Progress in Mater. Sci. 2018. V. 92. P. 112–224.
Schmidt M., Merklein M., Bourell D., Dimitrov D., Hausotte T., Wegener K., Overmeyer L., Vollertsen F., Levy G. N. Laser based additive manufacturing in industry and academia // CIRP Annals. V. 66(2). 2017. P. 561–583.
Rehme O., Emmelmann C. Reproducibility for Properties of Selective Laser Melting Products. in Beyer E, (Ed.) Lasers in Manufacturing 2005: Proceedings of the Third International WLT Conference Lasers in Manufacturing, LIM 2005, Munich, Germany, June 13th–16th, 2005, AT–Fachverl. Stuttgart.
O’Regan P., Prickett P., Setchi R., Hankins G., Jones N. Metal Based Additive Layer Manufacturing: Variations, Correlations and Process Control // Procedia Computer Science. 2016. V. 96. P. 216–224.
Moges T., Ameta G., Witherell P. A review of model inaccuracy and parameter uncertainty in laser powder bed fusion models and simulations // J. Manuf. Sci. Eng. 2019. V. 141(4). P. 040801.
Vock S., Klöden B., Kirchner A., Weißgärber T. & Kieback B. Powders for powder bed fusion: a review // Prog. Additive Manuf. 2019. V. 4. P. 383–397.
Yadroitsev I., Krakhmalev P., Yadroitsava I. Hierarchical design principles of selective laser melting for high quality metallic objects // Additive Manuf. 2015. V. 7. P. 45–56.
Valente E.H., Gundlach C., Christiansen T.L., Somer M.A.J. Effect of scanning strategy during selective laser melting on surface topography, porosity, and microstructure of additively manufactured Ti–6Al–4V // Appl. Sci. 2019. V. 9. P. 5554
Parry L., Ashcroft I.A., Wildman R.D. Understanding the effect of laser scan strategy on residual stress in selective laser melting through thermo–mechanical simulation // Additive Manuf. 2016. V. 12. Part A. P. 1–15.
ugwagwa L., Dimitrov D., Matope S., Yadroitsev I. Evaluation of the impact of scanning strategies on residual stresses in selective laser melting // The International J. Advanced Manufacturing Technology. 2019. V. 102(5–8). P. 2441–2450
Yadroitsev I., Smurov I. Selective laser melting technology: from the single laser melted track stability to 3D parts of complex shape // Physics Procedia. 2010. V. 5. P. 551–560.
Сайт компании ЭОС, Германия. [Электронный ресурс]. https://www.eos.info/en/additive-manufacturing/software-3d-printing/monitoring-software.
Сайт компании SLM Solution, Германия. [Электронный ресурс]. https://www.slm-solutions.com/en/products/software/additivequality.
Титан и сплавы титановые деформируемые. Марки ГОСТ 19807–911. [Электронный ресурс]. http://docs.cntd.ru/document/1200006390l.
Цвикер У. Титан и его сплавы. Москва: Металлургия. 1979. 511 с.
Илларионов А.Г., Попов А.А. Технологические и эксплуатационные свойства титановых сплавов: учебное пособие. Екатеринбург: Изд-во Урал. ун‑та. 2014. 137 с.
Колачев Б.А., Полькин И.С., Талалаев В.Д. Титановые сплавы разных стран. М.: ВИЛС. 2000. 316 с.
Гецов Л.Б. Материалы и прочность деталей газовых турбин. М.: Недра. 1996. 591 с.
Колобов Ю.Р. Технологии формирования структуры и свойств титановых сплавов для медицинских имплантатов с биоактивными покрытиями // Российские нанотехнологии. 2009. Т. 4. № 11–12. С. 69–81.
ГОСТ Р ИСО 5832-3–2014 Национальный стандарт российской федерацииимплантаты для хирургии металлические материалы. Часть 3. Деформируемый сплав на основе титана, 6-алюминия и 4-ванадия. [Электронный ресурс]. http://docs.cntd.ru/document/1200116339.
Implants for surgery. Metallic materials. Part 3: Wrought titanium 6-aluminium 4-vanadium alloy, ISO 2016, Published in Switzerland. 1–7 p.
Prasad Y.V.R.K., Seshacharyulu T., Medeiros S.C., Frazier W.G. A study of beta processing of Ti–6Al–4V: Is it trivial? // J. Engineering Materials and Technology. 2001. V. 123(3). P. 355–360.
Зарипова Р. Г., Шундалов В.А., Шарафутдинов А.В., Ситдиков В.Д., Кандаров И.В., Латыш В.В., Зарипов Н.Г., Александров И.В. Влияние интенсивной пластической деформации и режимов обработки на структуру и механические свойства титанового сплава ВТ6 // Вестник УГТУ. 2012. Т. 16. № 7(52). С. 17–24.
Salishev G.A., Galeev R.M., Valiahmetov O.R., Zherebtsov S.V., Gigliotti, Salishev G.A., Galeev R.M., Valiahmetov O.R., Zherebtsov S.V., Gigliotti M.F.X., Bewlay B.P. Fine Grain Processing of Titanium Alloys / In: Titanium”99: Science and Technology. 1999. V. 1. P. 1563–1568.
Peters M., Lutjering G., Ziegler G. Control of microstructures of (α + β)-titanium alloys // Zeitschrift für Metallkunde. 1983. V. 74. № 5. P. 274–282.
Lutjering G., Williams J.C., Gysler A. Titanium. 2nd Edition. Springer. 2007. 442 p.
Константинова М.В., Гусева Е.А., Шведков Л.В. Подготовка поверхности заготовок титановых сплавов для последующих технологических операций // Системы. Методы. Технологии. 2013. № 2(18). С. 119–123.
Gaddam R, Sefer B., Pederson R., Antti M–L. Study of alpha–case depth in Ti–6Al–2Sn–4Zr–2Mo and Ti–6Al–4V // IOP Conf. Series: Materials Science and Engineering. 2013. V. 48. P. 012002.
Bauristhene A.M., Mutombo K., Stump W.E. Alpha case formation mechanism in Ti–6Al–4V alloy investment castings using YFSZ shell moulds // The J. Southern African Institute of Mining and Metallurgy. 2013. V. 113. P. 357–361.
Андреев А.Л., Аношкин Н.Ф. Борзецовская К.М., Бочвар Г.А. Плавка и литье титановых сплавов. М.: Металлургия, 1994. С. 128–135.
Saunders N. Modelling of phase equilibria in Ti-alloys / Proc. “Titanium’95: Science and Technology”, Eds. Bleckinsop P., Evans W.J., and Flower H.M., Institute of Materials, London. 1996. 2167 p.
Babu B. Physically based model for plasticity and creep of Ti–6Al–4V. 2008, Luleå University of Technology Department of Applied Physics and Mechanical Engineering Division of Material Mechanics, Sweden. 55 p.
Sahoo R., Jha B.B., Sahoo T.K. Effect of primary alpha phase variation on mechanical behaviour of Ti–6Al–4V alloy // Mater. Sci. Technol. 2015. V. 31(12). P. 1486–1494.
Burgers W.G. On the process of transition of cubic body–centered modification into the hexagonal–close packed modification of zirconium // Physica. 1934. V. 1. № 7. P. 561–586.
Carreon H., Ruiz A., Santoveña B. Study of Aging Effects in a Ti–6Al–4V Alloy with Widmanstätten and Equiaxed Microstructures by Non–Destructive Means // AIP Conference Proceedings. 2014. V. 1581. P. 739.
Froes F.H. (Eds), Titanium: Physical Metallurgy, Processing, and Applications, ASM International, Materials Park, Ohio, 2015.
Колачев Б.А., Елагин В.И., Ливанов В.А., Металловедение и термообработка цветных металлов и сплавов. М.: МИСИС, 2005. 416 с.
Boyer R., Welsch G., Collings E.W., Materials Properties Handbook: Titanium Alloys, ASM International. Metals Park, Ohio. 1994. P. 1079–1082.
Wielewski E., Siviour C.R., Petrinic N. On the correlation between macrozones and twinning in Ti–6Al–4V at very high strain rates // Scripta Mater. 2012. V. 67. P. 229–232.
Li C., Li G., Yang Yi, Varlioglu M., Yang Ke. α" martensitic twinning in alpha + beta Ti–3.5Al–4.5Mo titanium alloy // J. Metall. 2011. P. 1–5.
Moffat D.L., Larbeliestier D.C. The competition between martensite and omega in quenched Ti–Nb alloys // Metall. Trans. 1988. V. 19. P. 1677–1686.
Ivasishin O.M., Flower H.M., Lutjering G. Mechanisms of martensite formation and tempering in titanium alloys and their relationship to mechanical property development / Proc. titanium’99, Sci. Technol. 1999. P. 77–84.
Довбыш В.М., Забеднов П.В., Зленко М.А. Аддитивные технологии и изделия из металла // Библиотечка литейщика. 2014. № 9. С. 1–57.
Дудихин Д.В., Сапрыкин А.А. Применение плазменной обработки для производства Специализированного металлического порошка // Технологии и материалы. 2017. С. 1–5.
Kazantseva N. Main factors affecting the structure and properties of Titanium and cobalt alloys manufactured by the 3D printing // IOP Conf. Series: J. Physics: Conf. Series 1115. 2018. P. 042008.
Kazantseva N., Krakhmalev P., Fefelov A., Merkushev A., Ilyinikh M., Vinogradova N., Ezhov I., Kurennykh T. Oxygen and nitrogen concentrations in the Ti–6Al–4V Alloy manufactured by direct metal laser sintering (DMLS) process // Materials Letters. 2017. V. 209. P. 311–314.
Cunningham R. Analyzing the effects of powder and post–processing on porosity and properties of electron beam melted Ti–6Al–4V // Mater. Res. Lett. 2017. V. 5. № 7. P. 516–525.
Krakhmalev P., Fredriksson G., Yadroitsava I., Kazantseva N., Du Plessis A., Yadroitsev I. Deformation behavior and microstructure of Ti6Al4V manufactured by SLM // Physics Procedia. 2016. V. 83. P. 778–788.
Bi Zhang, Yongtao Li, Qian Bai. Defect Formation Mechanisms in Selective Laser Melting: A Review // Chin. J. Mech. Eng. 2017. V. 30. P. 515–527.
Cordova L., Campos M., Tinga T. Revealing the Effects of Powder Reuse for Selective Laser Melting by Powder Characterization // JOM. 2019. V. 71. P. 1062–1070.
Simonelli M., Tse Y.Y., Tuck C. Effect of the build orientation on the mechanical properties and fracture modes of SLM Ti–6Al–4V // Mater. Sci. Eng. 2014. A616. P. 1–11.
Казанцева Н.В., Крахмалев П.В., Фредрикссон Г., Виноградова Н.И., Ядройцев И.А., Ежов И.В. Двойники в сплаве Ti–6Al–4V после селективного лазерного сплавления // Титан. 2017. № 2. С. 8–15.
Kazantseva N., Krakhmalev P., Yadroitsev I., Fefelov A., Vinogradova N., Ezhov I., Kurennykh T. Texture and Twinning in Selective Laser Melting Ti–6Al–4V Alloys // Intern. J. Mater. Metal. Eng. 2017. V. 11(11). P. 723–726.
Thijs L., Verhaeghe F., Craeghs T., Van Humbeeck J., Kruth J.–P. A study of the microstructural evolution during selective laser melting of Ti–6Al–4V // Acta Mater. 2010. V. 58. P. 3303–3312.
Kazantseva N., Krakhmalev P., Thuvander M., Yadroitsev I., Vinogradova N., Ezhov I. Martensitic transformations in Ti–6Al–4V (ELI) alloy manufactured by 3D Printing // Mater. Characteriz. 2018. V. 146. P. 101–112.
Ming Yan, Peng Yu. An overview of densification, microstructure and mechanical property of additively manufactured Ti–6Al–4V – comparison among selective laser melting, electron beam melting, laser metal deposition and selective laser sintering, and with conventional powder, in A. Lakshmana (Eds): Sintering techniques of materials, InTech, 2015. Ch. 5. P. 77–106.
Lui E.W., Xu W., Pateras A., Qian M., Brandt M. New development in selective laser melting of Ti–6Al–4V: a wider processing window for the achievement of fully lamellar α + β microstructures // JOM. 2017. V. 69(12).P. 2679–2683.
Zafari A., Barati M.R., Xia K. Controlling martensitic decomposition during selective laser melting to achieve best ductility in high strength Ti–6Al–4V // Mater. Sci. Eng.: A. 2019. V. 744. P. 445–455.
Barriobero–Vila P., Gussone J., Haubrich J., Sandlöbes S., Da Silva J. C., Cloetens P., Schell N., Requena G. Inducing Stable α + β Microstructures during Selective Laser Melting of Ti–6Al–4V Using Intensified Intrinsic Heat Treatments // Materials. 2017. V. 10. P. 268 1–14.
Tan X., Kok Yi., Toh W.Q., Tan Y. J., Descoins M., Mangelinck D., Tor S. B., Leong K. F., Chua Ch. K. Revealing martensitic transformation and α/β interface evolution in electron beam melting three-dimensional-printed Ti–6Al–4V // Sci. Reports. 2016. V. 6(26039). P. 1–10.
Murr L.E., Quinones S.A., Gaytan S.M. Lopez, M.I., Rodela A., Martinez E.Y., Hernandez D.H., Martinez E., Medina F., Vicker R.B. Microstructure and mechanical behavior of Ti–6Al–4V produced by rapid-layer manufacturing, for biomedical applications // J. Mechan. Behavior Biomedical Materials. 2009. V. 2. P. 20–32.
Moletsane M.G., Krakhmalev P., Kazantseva N., Du Plessis A., Yadroitsava I. Yadroitsev I. Tensile properties and microstructure of direct metal laser sintered Ti6Al4V (ELI) alloy // South African J. Industrial Engineering. 2016. V. 27(3). Special Edition. P. 110–121.
Partridge P.G. Cyclic twinning in fatigued close–packed hexagonal metals / P.G. Partridge // Philosoph. Magazine: A J. Theor. Experim. Appl. Phys. 1965. V. 12(119). P. 1043–1054.
Beese A.M., Carroll B.E. Review of mechanical properties of Ti–6Al–4V made by laser-based additive manufacturing using powder feedstock // JOM. 2016. V. 68. P. 724–734.
Du Plessis A., Yadroitsava I. Yadroitsev I. Effects of defects on mechanical properties in metal additive manufacturing: A review focusing on X-ray tomography insights // Mater. Design, 2019. V. 187. P. 108385.
Donachie M.J. Titanium: A Technical Guide, Materials Park (OH): ASM international. 2000. 369 p.
Rafi H., Karthik N.V., Gong H., Starr Th.L., Stucker B.E. Microstructures and mechanical properties of Ti6Al4V parts fabricated by selective laser melting and electron beam melting // J. Mater. Eng. Performance. 2013. V. 22. P. 3873–3883.
Xu W., Brandt M., Sun S., Elambasseril J., Liu Q., Latham K., Xia K., Qian M. Additive manufacturing of strong and ductile Ti–6Al–4V by selective laser melting via in situ martensite decomposition // Acta Mater. 2015. V. 85. P. 74–84.
Xu W., Lui EW., Pateras A., Qian M., Brandt M. In situ tailoring microstructure in additively manufactured Ti–6Al–4V for superior mechanical performance // Acta Mater. 2017. V. 125. P. 390–400.
Zafari A., Xia K. High ductility in a fully martensitic microstructure: a paradox in a Ti alloy produced by selective laser melting // Mater. Research Letters. 2018. V. 6(11). P. 627–633.
Scharowsky T., Jüchter V., Singer R.F., Körner C. Influence of the scanning strategy on the microstructure and mechanical prop-erties in selective electron beam melting of Ti–6Al–4V // Adv. Eng. Mat. 2015. V. 17. P. 11.
Murr L.E., Exquivel E.V., Quinones S.A., Gaytan S., Lopes M.I., Martinez E.Y., Medina F., Hernandez D.H., Martinez J.L., Stafford S.W., Brown D.K., Hoppe T., Meyers W., Lindhe U., Wicker R.B. Microstructures and mechanical properties of electron beam rapid manufactured Ti–6Al–4V biomedical prototypes compared to wrought Ti–6Al–4V // Mater. Charact. 2009. V. 60(2) P. 96–105.
Hrabe N. and Quinn T. Effects of processing on microstructure and mechanical properties of a titanium alloy (Ti–6Al–4V) fabricated using electron beam melting (EBM). Part 1: distance from build plate and part size // Mater. Sci. Eng. A. 2013. V. 573(20). P. 264–270.
Lu S.L., Tang H.P., Ning Y.P. Liu N, StJohn D.H., Qian M. Microstructure and Mechanical Properties of Long Ti–6Al–4V Rods Additively Manufactured by Selective Electron Beam Melting Out of a Deep Powder Bed and the Effect of Subsequent Hot Isostatic Pressing // Metal and Mat Trans A. 2015. V. 46. P. 3824–3834.
Vilaro T., Colin C., Bartout J.D. As-fabricated and heat-treated microstructures of the Ti–6Al–4V alloy processed by selective laser melting // Metallurgical and Materials Transactions A. 2011. V. 42(10). P. 3190–3199.
Mertens A., Reginster S., Paydas H., Contrepois Q., Dormal T., Lemaire O., Lecomte–Beckers J. Mechanical properties of alloy Ti–6Al–4V and of stainless steel 316L processed by selective laser melting: influence of out-of-equilibrium microstructures // Powder Metallurgy. 2014. V. 57(3). P.184–189.
Facchini L., Magalini E., Robotti P., Molinari A., Hoges S., Wissenbach K. Ductility of a Ti–6Al–4V alloy produced by selective laser melting of prealloyed powders // Rapid Prototyping J. 2010. V. 16/6. P.450–459.
Mohammadhosseini A., Fraser D., Masood S.H. and Jahedi M. Microstructure and mechanical properties of Ti–6Al–4V manufactured by electron beam melting process // Materials Research Innovations. 2013. V. 17(sup2). P. s106–s112.
Yadroitsev I., Yadroitsava I. Evaluation of residual stress in stainless steel 316L and Ti6Al4V samples produced by selective laser melting // Virtual and Physical Prototyping. 2015. V. 10(2). P. 67–76.
Yadroitsev I., Krakhmalev P., Yadroitsava I., Du Plessis A. Qualification of Ti6Al4V ELI Alloy Produced by Laser Powder Bed Fusion for Biomedical Applications // JOM. 2018. V. 70. P. 372–377.
Becker T., Van Rooyen M., Dimitrov D. Heat treatment of Ti–6Al–4V produced by lasercusing // South African J. Industrial Engineering. 2015. V. 26(2). P. 93–103.
Vrancken B., Thijs L., Kruth J.–P., Van Humbeeck J. Heat treatment of Ti6Al4V produced by Selective Laser Melting: Microstructure and mechanical properties // J. Alloys Compounds. 2012. V. 541. P. 177–185.
Wu M.W., Lai P.H. The positive effect of hot isostatic pressing on improving the anisotropies of bending and impact properties in selective laser melted Ti–6Al–4V alloy // Mater. Sci. Eng.: A, 2016. V. 658. P. 429–438.
Tammas-Williams S., Withers P.J., Todd I., Prangnell P.B. The effectiveness of hot isostatic pressing for closing porosity in titanium parts manufactured by selective electron beam melting. Metal. Mater. Trans. A // 2016. V. 47(5). P. 1939–1946.
Hernández-Nava E., Mahoney P., Smith C.J., Donoghue J., Todd I., Tammas-Williams S. Additive manufacturing titanium components with isotropic or graded properties by hybrid electron beam melting/hot isostatic pressing powder processing // Sci. Rep. 2019. V. 9. P. 4070.
Chan K.-S. Characterization and analysis of surface notches on Ti–alloy plates fabricated by additive manufacturing techniques // Surface Topography: Metrology and Properties. 2015. V. 3(4). P.044006.
Greitemeier D., Dalle Donne C., Syassen F., Eufinger J., Melz T. Effect of surface roughness on fatigue performance of additive manufactured Ti–6Al–4V // Mater. Sci. Techn. 2016. V. 32(7). P. 629–634.
Vilardell A.M., Krakhmalev P., Fredriksson G., Cabanettes F., Sova A., Valentin D., Bertrand P. Influence of surface topography on fatigue behavior of Ti6Al4V alloy by laser powder bed fusion // Procedia CIRP. 2018. V. 74. P. 49–52.
Leuders S., Thöne M., Riemer A., Niendorf T., Tröster T., Richard H.A., Maier H.J. On the mechanical behaviour of titanium alloy TiAl6V4 manufactured by selective laser melting: Fatigue resistance and crack growth performance // International J. Fatigue. 2013. V. 48. P. 300–307.
Буркин С.П., Шимов Г.В., Андрюкова Е.А. Остаточные напряжения в металлопродукции, Екатеринбург: Изд. Урал. ун-та, 2015. 248 с.
Van Zyl I., Yadroitsava I., Yadroitsev I. Residual stress in Ti6Al4V objects produced by direct metal laser sintering // South African Journal of Industrial Engineering. 2016. V. 27(4). P. 134–141.
овиков И.И. Теория термической обработки. М.: Металлургия, 1978. 392 с
Knowles C.R., Becker T.H., Tait R.B. Residual stress measurements and structural integrity implications for selective laser melted Ti–6Al–4V // South African J. Industrial Engineering. 2012. V. 23(3). P. 119–129.
Kazantseva N., Ezhov I., Vinogradova N., Davidov D., Fefelov A., Merkushev A., Ilyinikh M., Volkov A. Comparative analysis of the structure and internal stress in TI–6AL–4V alloys manufactured by 3D printing and processing with screw extrusion // IOP Conf. Series: J. Physics: Conf. Series. 2018. V. 1115. № 042007. P. 1–7.
Kazantseva N.V., Ezhov I.V., Vinogradova N.I., Il’inykh M.V., Fefelov A.S., Davydov D.I., Oleneva O.A., Karabanalov M.S. Effect of Built Geometry on the Microstructure and Strength Characteristics of the Ti–6Al–4V Alloy Prepared by the Selective Laser Melting // Phys. Met. Metal. 2018. V. 119(11). P. 1079–1086.
Williams D.F. On the mechanisms of biocompatibility // Biomaterials. 2008. V. 29. P. 2941–2953.
Dimitriou R., Jones E., McGonagle D., Giannoudis V P. Bone regeneration: current concepts and future directions // BMC Medicine. 2011. V. 9(66). P. 1–10.
Silva–Bermudez P., Rodil S.E. An Overview on Protein Adsorption on Metal Oxide Coatings for Biomedical Implants // Surface Coatings Technology. 2013. V. 233. P. 147–158.
Hollister S.J. Porous scaffold design for tissue engineering // Nature Mater. 2005. V. 4(7). P. 518–524.
Wang X., Xu S., Zhou S., Xu W., Leary M., Choong P., Qian M., Brandt M., Xie Y.M. Topological design and additive manufacturing of porous metals for bone scaffolds and orthopaedic implants: a review // Biomaterials. 2016. V. 83. P. 127–141.
Nouri A., Hodgson P.D., Wen S.U. Effect of process control agent on the porous structure and mechanical properties of biomedical Ti–Sn–Nb alloy produced by powder metallurgy // Acta Biomater. 2010. V. 6. P. 1630–1639.
Du Plessis A., Yadroitsava I., Yadroitsev I., Ti6Al4V lightweight lattice structures manufactured by laser powder bed fusion for load-bearing applications // Optics and Laser Technology. 2018. V. 108. P. 521–528.
Yadroitsava I., du Plessis A., Yadroitsev I. Bone regeneration on implants of titanium alloys produced by laser powder bed fusion: a review / a book chapter in: Froes F., Qian M., Niinomi M. (Eds.) “Titanium for Consumer Applications. Real World Use of Titanium”. Elsevier. 2019. P. 197–233.
Eliaz N. Corrosion of Metallic Biomaterials: A Review // Materials (Basel). 2019. V. 12(3). P. 407.
Mahmoud D., Elbestawi M.A. Lattice structures and functionally graded materials applications in additive manufacturing of orthopedic implants: a review // J. Manufacturing Mater. Proces. 2017. V. 1(2). P. 1–19.
Epasto G., Palomba G., D’Andrea D., Guglielmino E., Di Bella S. and Traina F. Ti–6Al–4V ELI microlattice structures manufactured by electron beam melting: Effect of unit cell dimensions and morphology on mechanical behavior // Mater. Sci. Eng.: A. 2019. V. 753. P. 31–41.
Choy S.Y., Sun C.N., Leong K.F., Wei J. Compressive properties of Ti–6Al–4V lattice structures fabricated by selective laser melting: Design, orientation and density // Additive Manufacturing. 2017. V. 16. P. 213–224.
Zhao S., Li S.J., Hou W.T., Hao Y.L., Yang R., Misra R.D.K. The influence of cell morphology on the compressive fatigue behavior of Ti–6Al–4V meshes fabricated by electron beam melting // J. Mechan. Behavior Biomedical Mater. 2016. V. 59. P. 251–264.
Дополнительные материалы отсутствуют.
Инструменты
Физика металлов и металловедение