Физика металлов и металловедение, 2021, T. 122, № 10, стр. 1083-1090
Влияние технологических параметров и упрочняющих элементов структуры на свойства гибридных алюминиевых композитных материалов, полученных методом порошковой металлургии
А. Парвеен a, *, Н. Р. Чаухан a, М. Сухаиб b
a Отделение автоматизации машиностроения, Делийский технический университет
для женщин им. Индиры Ганди
110006 Нью-Дели, Индия
b Инженерно-технический факультет, Университет Джамия Миллия Исламия
110025 Нью-Дели, Индия
* E-mail: aasiyaparveen346@gmail.com
Поступила в редакцию 07.02.2021
После доработки 05.05.2021
Принята к публикации 10.06.2021
Аннотация
В рамках данного исследования, методом порошковой металлургии были созданы алюминиевые гибридные композиты, в которых в качестве армирующего материала выступали частицы Si3N4 и ZrO2. Композитный порошок, синтезированный в соответствии с массовым процентом армирования, сначала подвергали измельчению в планетарной шаровой мельнице при 600 об/мин в течение 0.5 и 2.5 ч, а затем компактифицировали при 420 МПа. Компактированные композиты выдерживали в муфельной печи для спекания при температуре 550°C в контролируемой атмосфере в течение 30 минут. Изучено влияние времени обработки в шаровой мельнице, а также весового процента армирования, на микроструктуру, удельный вес (плотность) и твердость полученных композитов. Результаты РЭМ-микроскопии показали, что частицы Si3N4/ZrO2 после механо-синтеза композитов были распределены в объеме матрицы однородно, причем с увеличением продолжительности механообработки число кластеров убывало. Было также отмечено, что при больших временах помола и высоких весовых процентах (вес. %) армирующих частиц удельный вес синтезированных композитов возрастал с параллельным снижением пористости материала. Наконец, было обнаружено, что микротвердость композитов также улучшилась благодаря дисперсности и однородности пространственного распределения высокопрочных керамических элементов армирующей подсистемы, встроенной в матрицу.
ВВЕДЕНИЕ
Композиты с металлической матрицей (ММК) получили больший спрос в конструкционных приложениях из-за их превосходных свойств по сравнению с монолитными материалами [1]. В композитах с алюминиевой матрицей (AMК) высокопрочный металлический или неметаллический материал, или оба были усилено алюминиевой матрицей низкого удельного веса, благодаря чему свойства композитов улучшились [2]. Фактом стало то, что AMК композиты привлекли большое внимания в автомобильной и аэрокосмической промышленности из-за своего малого удельного веса и высокого отношения удельной прочности [3]. Армирование АМК керамическими включениями привело к превосходным свойствам [4–7]. В производстве АМК наиболее широко используют керамики SiC, Si3N4, Al2O3, B4C, ZrO2 [5, 8]. По сравнению с одинарно армироваными композитами, алюминиевые гибридные композиты демонстрируют значительно улучшенное поведение при испытаниях. Свойства композитов зависят от различных факторов, поэтому для получения оптимальных свойств очень важно выбрать подходящий способ армирования и изготовления. Усиленные армирующими частицами АМК могут быть получены широко используемыми твердотельными или жидкостными технологиями [9, 10]. Среди всех возможных технологий изготовления порошковая металлургия (ПМ) является наиболее перспективным и универсальным методом, поскольку она дает больше преимуществ, чем любой иной метод создания алюминиевых гибридных композитов [11]. Во-первых, реакция на межфазных границах исключается во время технологического ПМ-процесса “формования”, поскольку происходит в низкотемпературных условиях по сравнению с процессами литья. Во-вторых, ПМ-технология обеспечивает однородную дисперсность частиц порошка, что приводит к превосходным свойствам композитов [12–14]. Кроме того, с помощью этой (ПМ) методики также могут быть получены с высокой точностью “конструкционные” элементы сложной сетчатой формы [15]. Технологический процесс ПМ-“формования” состоит из трех этапов: смешивание/механическое сплавление алюминия и армирующих порошков, уплотнение и последующее спекание для достижения прочности [16]. Для улучшения свойств композитов важную роль играют такие параметры ПМ-процесса, как продолжительность измельчения, тип процесса компактирования, давление при компактировании, тип спекания, время, температура, окружающая среда и т.д. [17, 18]. Бенджамин впервые изобрел метод механической обработки порошка, т.е. метод механического легирования (МЛ) [19]. Смеси “элементарных” порошков измельчали в планетарной шаровой мельнице с мелющей средой для получения однородного порошкового сплава путем повторяющихся процессов деформации, сварки и механизмов разрушения [20–22]. Много исследований было проведено на композитах на основе алюминия, синтезированных механическим легированием [23–30]. В работе [31] авторы синтезировали композит Al6061/5% Si3N4 методом ПМ, причем они механически измельчали композитный порошок в течение различного времени помола: 1.5, 3, 4.5, 6, 8, и 10 ч в высокоэнергетической шаровой мельнице при 700 об/мин и исследовали равномерное диспергирование частиц Si3N4 с уменьшением их размера через 10 ч [32]. Авторы также заявили о высокой твердости композитов и ее росте с увеличением продолжительности механического помола [22]. После изучения доступной литературы было отмечено, что не было проведено никаких исследований по композитам Al, армированным частицами Si3N4/ZrO2 и синтезированным методами порошковой металлургии. Эта работа представляет собой попытку синтезировать композит Al–Si3N4/ZrO2 и исследовать влияние различных армирующих компонентов и продолжительности механосинтеза (МС) на морфологию, плотность и твердость означенных композитов.
МЕТОДИКА ЭКСПЕРИМЕНТА
В качестве исходного материала был использован чистый алюминиевый порошок, который был произведен компанией Otto Chemie India Ltd. Средний размер частиц порошка Al (чистотой 99.9%) составлял ≤44 мкм. В качестве армирующих материалов использовали нитрид кремния (α-Si3N4), закупленный у Sigma-Aldrich India Ltd, и двуокись и циркония (ZrO2) от фирмы Nano-Labs India Ltd. Оба армирующих материала представляли собой керамические частицы, обладающие высокой прочностью. В табл. 1 перечислены характеристики армирующих материалов. Микрофотографии армирующих порошков представлены на рис. 1, который показывает, что частицы Si3N4 имеют чешуйчатый тип, а частицы ZrO2 одинаково дисперсны.
Таблица 1.
Характеристики порошков α-Si3N4 и ZrO2
Свойство | α-Si3N4 | ZrO2 |
---|---|---|
Чистота | 97.50% | 99.9% |
Средний размер частиц | 10 мкм | 30–50 нм |
Структура | Тригональная | ГПУ |
Удельный вес | 3.44 г/см3 | 5.68 г/см3 |
Точка плавления | 2170°C | 2715°C |
Композиты были изготовлены по ПМ-технологии, и этапы, выполняемые при изготовлении, проиллюстрированы на рис. 2. Количества составляющих композита отмерены на электронных весах, что привело к составам, указанным ниже. После предварительных замеров, композитный порошок затем измельчали в планетарной шаровой мельнице (Fritsch, Германия) при 600 об/мин в течение 0.5 и 2.5 ч. Для получения однородной смеси и уменьшения скопления (кластеризации) частиц в качестве мелющей среды добавляли шарики из нержавеющей стали (диаметром 10 мм), а также 3-вес. % этанола в качестве агента управления технологическим процессом (АУП), причем весовое отношение (ВО) “шары/порошок” устанавливалось на уровне 10 : 1.
Были синтезированы композиции следующих элементных составов:
Чистый Al;
После синтеза композитных порошков полученные цилиндрические образцы высотой h = 8 мм и диаметром основания d = 13 мм были отформованы при 420 МПа одноосным гидравлическим прессом. Затем образцы для достижения прочности подвергали спеканию в муфельной печи при температуре 550°C в течение 30 мин в среде аргона. Микроструктуру спеченных образцов, полученных при двух различных временах измельчения, наблюдали методом РЭМ-микроскопии (на приборе марки JOEL-JSM 6510 LV SEM). Кроме того, нами были оценены плотность (уд. вес) и пористость этих композитов.
Теоретическая плотность (уд. вес) композитов измерена по правилу смеси [33]:
(1)
${{\rho }_{{{\text{th}}}}} = {{\rho }_{{{\text{Al}}}}}{{V}_{{{\text{Al}}}}} + {{\rho }_{{{\text{S}}{{{\text{i}}}_{3}}{{{\text{N}}}_{4}}}}}{{V}_{{{\text{S}}{{{\text{i}}}_{3}}{{{\text{N}}}_{4}}}}} + {{\rho }_{{{\text{Zr}}{{{\text{O}}}_{2}}}}}{{V}_{{{\text{Zr}}{{{\text{O}}}_{2}}}}},$Экспериментально плотность композитов измерялась по принципу Архимеда:
где ρe – уд. вес композита из эксперимента, а m и mw – вес исследуемого композита на воздухе и в воде, соответственно, ρ – уд. вес воды [г/см3].Для измерения твердости был использован твердомер Виккерса с нагрузкой 100 кгс и временем экспозиции 10 с. Показания были сняты на трех разных участках поверхности образцов, а затем рассматривали среднее значение.
РЕЗУЛЬТАТЫ И ОБСУЖДЕНИЕ
1. Микроструктура. Хорошо известно, что экстремальная пластическая деформация частиц в процессе измельчения создает значительные изменения в морфологии композитных порошков [34]. В процессе измельчения полученный алюминиевый порошок прошел указанную обработку в шаровой мельнице в течение 0.5 и 2.5 ч при 600 об/мин. Влияние процесса измельчения на морфологию алюминиевого порошка было исследовано по результатам РЭМ (FE-SEM) микроскопии с полевым эмиттером. Рисунок 3а показывает, что частицы алюминия имеют неправильную форму с острыми углами. После 0.5 ч процесса измельчения, как показано на рис. 3б, частицы порошка обнаруживают тенденцию к сглаживанию неровностей своей поверхности из-за пластичности алюминия. По мере увеличения времени измельчения (рис. 3в) размер частиц уменьшался и частицы приобретали округлую форму. Отмечено, что порошок по своему объему оказался однородно перемешан – без проявления видимых локальных неоднородностей – после 2.5‑часового измельчения. На рис. 4 показана рентгеновская дифрактограмма порошка чистого алюминия в состоянии поставки. На ней можно видеть пик 111, отличающийся от всех остальных самой большой интенсивностью. Из-за наличия ГЦК-структуры обнаруживаются четыре резких дифракционных пика. Как видно из рис. 4, дифракционные пики от алюминия испытывали уширение с увеличением временем измельчения порошковой смеси. Причиной этого, по-видимому, было измельчение кристаллитов и увеличение деформаций атомного уровня [35]. Из-за высокой термодинамической стабильности алюминия новые фазы не были обнаружены даже после измельчения в течение 2.5 ч. Уравнение Шеррера использовали для оценки размера зерна на основе данных, полученных из рентгеновских дифрактограмм. Установлено, что размер зерна составил 27.898 нм после 2.5 ч, 34.925 нм после 0.5 ч помола и 20.121 нм для немолотого порошка Al.
Рис. 3.
РЭМ-изображение с полевым эмиттером (FE) порошка Al (а) в состоянии поставки, (б) измельченного за 0.5 ч и (в) измельченного за 2.5 ч.
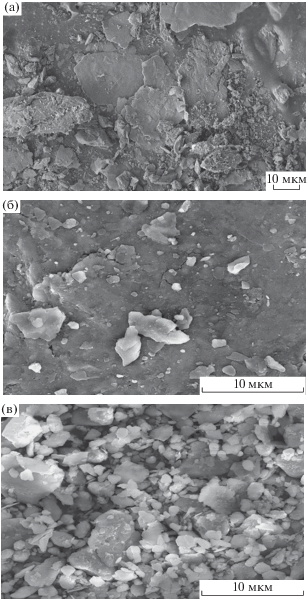
Рис. 4.
Сравнение рентгеновских дифрактограмм от порошка Al (I) в состоянии поставки, (II) измельченного за 0.5 ч и (III) измельченного за 2.5 ч.
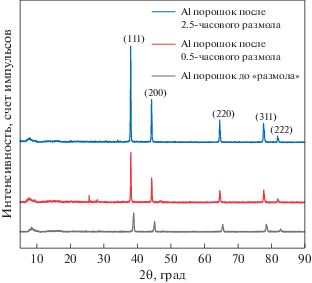
При времени помола 0.5 ч размер кристаллитов увеличивается, поскольку на начальном этапе механообработки в шаровой мельнице Al-матрица порошкового материала обладает высокой пластичностью, что усиливает эффект холодной сварки. На этой стадии холодная сварка доминирует над процессами размола–разрушения составляющих порошка, что приводит к увеличению размера кристаллитов. Но размер кристаллитов уже довольно мал после 2.5 ч механообработки в шаровой мельнице, и при дальнейшем размоле хрупкость составляющих порошкового материала увеличивается в результате процесса наклеп–деформационное упрочнение.
Изменение морфологии спеченных композитов исследовали методом РЭМ-микроскопии. На рис. 5 приведены РЭМ-микрофотографии пяти композитов после двух времен измельчения (0.5 и 2.5 ч). Отмечено, что продолжительность измельчения 0.5 ч, за исключением частичной деформации частиц алюминия, не оказывает существенного влияния на морфологию композита. Частицы алюминия сохранили свою первоначальную форму на этой стадии, когда можно наблюдать интенсивное скопление частиц армирования.
Рис. 5.
РЭМ-микрофотографии спеченных композитов (А–Е) при (а) 0.5 и (б) 2.5 ч предварительного измельчения порошковой смеси.
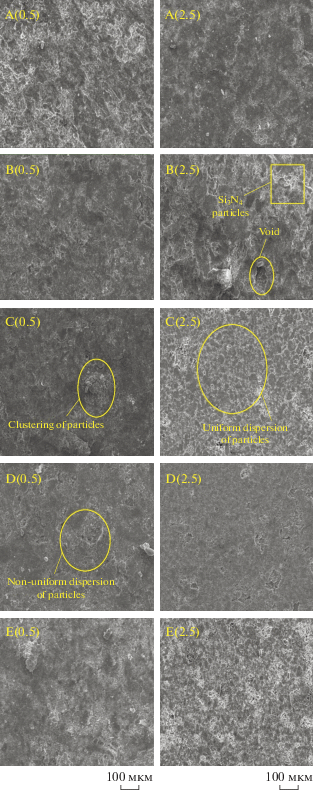
Холодная сварка частиц стала возможной, когда время измельчения достигло 2.5 ч, и частицы начали расплющиваться из-за столкновения мелющих шаров между собой с высокой энергией ударного воздействия. Вдобавок к продолжительности измельчения, природа частицы армирования также влияет на морфологию композитов. Это можно наблюдать на рис. 5. Частицы армирования (Si3N4/ZrO2) равномерно распределены в объеме композитов, предварительно механообработанных в течение 2.5 ч.
2. Удельный вес и пористость. Помимо процесса уплотнения и спекания морфология синтезированных композитных порошков после измельчения, размер частиц и равномерное распределение частиц армирования в матрице также влияют на плотность (уд. вес) спеченных композитов [34]. Экспериментальная плотность и пористость спеченных композитов (А–Е) при двух различных временах измельчения (0.5 и 2.5 ч) проиллюстрированы на рис. 6 и 7. Видно, что теоретическая плотность увеличивается с 2.7 для чистого Al до 2.834 г/см3 для композита Al–{3 вес. % Si3N4 + 4.5 вес. % ZrO2}. Увеличение теоретической плотности (удельного веса) наблюдали по мере добавления в матрицу частиц армирования высокого удельного веса. На начальной стадии измельчения экспериментальная плотность образца В низкая, что может быть связано с агломерацией и кластеризацией частиц Si3N4. Наличие агломератов и кластеров замедляет процесс диффузии, как это требуется при спекании. По мере увеличения времени измельчения частицы армирования равномерно распределяются внутри матрицы, что приводит к высокому удельному весу композита. С другой стороны, плотность также увеличивается по мере увеличения весовых процентов наночастиц ZrO2 в случае образцов C, D и E.
Рис. 6.
Сравнение “плотности” спеченных ПМ композитов при времени предварительного измельчения их порошковой смеси 0.5 и 2.5 ч.
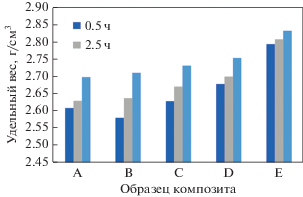
Рис. 7.
Сравнение пористости спеченных композитов при временах (предварительного) измельчения 0.5 и 2.5 ч.
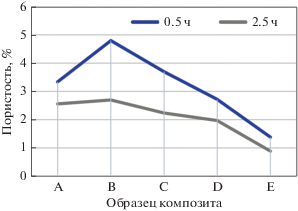
Также хорошо известно, что пористость обратно пропорциональна плотности. Разница в экспериментальной и теоретической плотности указывает на наличие некоторой пористости в композитах. На рис. 7 показано, что пористость композита уменьшается со временем измельчения. Как уже обсудили выше (п. 3.1), некоторые агломераты и кластеры образуются при непродолжительном (0.5 ч) времени измельчения, что влияет на свойства композитов. Частицы Si3N4 в композите B, прошедшие предварительное измельчение в течение 2.5 ч, были кластеризованы так, что возникли пустоты, как показано на рис. 5; это привело к высокой пористости композита. Но по мере добавления наночастиц ZrO2, эти частицы порошка равномерно “перемешивались” внутри матрицы. Более продолжительное время измельчения и равномерное пространственное распределение частиц армирования приводят к меньшей пористости.
3. Микротвердость. Изменение микротвердости алюминиевых гибридных композитов в зависимости от времени механосинтеза и степени армирования показано на рис. 8.
Рис. 8.
Сравнение микротвердости спеченных композитов при времени предварительного измельчения их порошковой смеси 0.5 и 2.5 ч.
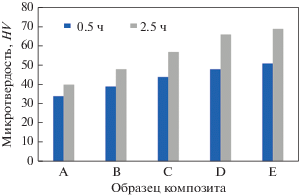
Было отмечено, что твердость повышается с увеличением времени механообработки в шаровой мельнице. Накопление обоих типов армирующей керамики в матрице повышает твердость композитов [1]. Вместе с тем нужно заметить, что время размола более существенно влияет на твердость композита, чем само армирование. Размер частиц порошка становился все меньше в процессе размола порошковой смеси, что приводило к увеличению взаимодействия частиц порошка между собой из-за увеличения площади поверхности измельчаемых порошков. Более того, постоянство деформирования является результатом совместного действия разрушения частиц и их холодной сварки [27]. Нами отмечено, что твердость алюминиевого гибридного композита, полученного за 2.5 ч механосинтеза, возросла на 43% по сравнению с образцом А и образцом Е.
ВЫВОДЫ
Синтез композита Al–Si3N4/ZrO2 был успешно выполнен. Настоящее исследование было проведено для определения влияния различных весовых процентов армирования керамикой и времени механообработки в шаровой мельнице на микроструктуру, физические и механические свойства композита. На основании полученных результатов сделан ряд выводов. А именно, увеличение времени измельчения и вес. % армирования наночастицами ZrO2 приводит к их равномерному распределению и уменьшению кластеров и агломератов внутри композитов. Размер частиц алюминиевого порошка также уменьшается со временем измельчения. Результаты по удельному весу (плотности) и пористости показали увеличение плотности и уменьшение пористости с увеличением времени механообработки в шаровой мельнице и вес. % содержания армирующих керамик. Аналогичную тенденцию наблюдали и для твердости композитов. Улучшенные физико-механические свойства композита Al–Si3N4/ZrO2 были обусловлены продолжительным временем механообработки и увеличением содержания наноструктурной ZrO2-фазы. Дальнейшее изучение влияния этих параметров на трибологические и другие свойства композита будет исследовано в ближайшем будущем.
Список литературы
Khorshid M.T., Jahromi S.A.J., Moshksar M.M. Mechanical properties of tri-modal Al matrix composites reinforced by nano- and submicron-sized Al2O3 particulates developed by wet attrition milling and hot extrusion // Mater. Des. 2010. V. 31. P. 3880–3884. https://doi.org/10.1016/j.matdes.2010.02.047
Singh J., Chauhan A. Characterization of hybrid aluminum matrix composites for advanced applications – A review // J. Mater. Res. Technol. 2016. V. 5. P. 159–169. https://doi.org/10.1016/j.jmrt.2015.05.004
Vani V.V., Chak S.K. The effect of process parameters in Aluminum Metal Matrix Composites with Powder Metallurgy // Manuf. Rev. 2018. V. 5. 7. https://doi.org/10.1051/mfreview/2018001
Surappa M.K. Aluminium Matrix Composites: Challenges and Opportunities // Sadhana. 2003. V. 28. P. 319–334. https://doi.org/10.1007/BF02717141
Sivakumar S., Thimmappa S.K., Golla B.R. Corrosion behavior of extremely hard Al–Cu/Mg–SiC light metal alloy composites // J. Alloys Compd. 2018. V. 767. P. 703–711. https://doi.org/10.1016/j.jallcom.2018.07.117
Panwar N., Chauhan A. Fabrication methods of particulate reinforced Aluminium metal matrix composite-A review // Mater. Today Proc. 2018. V. 5. P. 5933–5939. https://doi.org/10.1016/j.matpr.2017.12.194
Zebarjad S.M., Sajjadi S.A. Dependency of physical and mechanical properties of mechanical alloyed Al–Al2O3 composite on milling time // Mater. Des. 2007. V. 28. P. 2113–2120. https://doi.org/10.1016/j.matdes.2006.05.020
Parveen A., Chauhan N.R., Suhaib M. Study of Si3N4 reinforcement on the morphological and tribo-mechanical behaviour of aluminium matrix composites // Mater. Res. Express. 2019. V. 6. 42001. https://doi.org/10.1088/2053-1591/aaf8d8
C.V.V. V. Mahesh Kumar, A comprehensive review on material selection, processing, characterization and applications of aluminium metal matrix composites // Mater. Res. Express. 2019. V. 6. https://doi.org/10.1088/2053-1591/ab0ee3
Zhang G.P., Mei Q.S., Li C.L., Chen F., Mei X.M., Li J.Y., Ruan X.F. Fabrication and properties of Al–TiAl3–Al2O3 composites with high content of reinforcing particles by accumulative roll-bonding and spark plasma sintering // Mater. Today Commun. 2020. V. 24. https://doi.org/10.1016/j.mtcomm.2020.101060
Bains P.S., Sidhu S.S., Payal H.S. Fabrication and Machining of Metal Matrix Composites: A Review // Mater. Manuf. Process. 2016. V. 31. P. 553–573. https://doi.org/10.1080/10426914.2015.1025976
Bodunrin M.O., Alaneme K.K., Chown L.H. Aluminium matrix hybrid composites: A review of reinforcement philosophies; Mechanical, corrosion and tribological characteristics // J. Mater. Res. Technol. 2015. V. 4. P. 434–445. https://doi.org/10.1016/j.jmrt.2015.05.003
Torralba J.M., Da Costa C.E., Velasco F. P/M aluminum matrix composites: An overview // J. Mater. Process. Technol. 2003. V. 133. P. 203–206. https://doi.org/10.1016/S0924-0136(02)00234-0
Samal P., Vundavilli P.R., Meher A., Mahapatra M.M. Recent progress in aluminum metal matrix composites: A review on processing, mechanical and wear properties // J. Manuf. Process. 2020. V. 59. P. 131–152. https://doi.org/10.1016/j.jmapro.2020.09.010
Sharma P., Khanduja D., Sharma S. Tribological and mechanical behavior of particulate aluminum matrix composites // J. Reinf. Plast. Compos. 2014. V. 33. P. 2192–2202. https://doi.org/10.1177/0731684414556012
Umasankar V. Experimental evaluation of the influence of processing parameters on the mechanical properties of SiC particle reinforced AA6061 aluminium alloy matrix composite by powder processing // J. Alloys Compd. 2014. V. 582. P. 380–386. https://doi.org/10.1016/j.jallcom.2013.07.129
Afkham Y., Khosroshahi R.A., Kheirifard R., Mousavian R.T., Brabazon D. Microstructure and morphological study of ball-milled metal matrix nanocomposites//Phys. Met. Metallogr. 2017. V. 118. P. 749–758. https://doi.org/10.1134/S0031918X17080026
Eremina M.A., Lomaeva S.F., Paranin S.N., Demakov S.L., Elsukov E.P. Effect of compaction method on the structure and properties of bulk Cu + Cr3C2 composites // Phys. Met. Metallogr. 2016. V. 117. P. 510–517. https://doi.org/10.1134/S0031918X16050057
Benjamin J.S., Volin T.E. The Mechanism of Mechanical Alloying // Met. Trans. 1974. V. 5. 1929–1934. https://doi.org/10.1007/BF02644161
Suryanarayana C. Mechanical alloying and milling // Prog. Mater. Sci. 2001. V. 46. P. 1–184. https://doi.org/10.1016/S0079-6425(99)00010-9
Kaczmar J.W., Pietrzak K., Wlosinski W. The Production and Application of Metal Matrix Composite Materials // J. Mater. Process. Technol. 2000. V. 106. P. 58–67. https://doi.org/10.1016/S0924-0136(00)00639-7
Fogagnolo J., Velasco F., Robert M., Torralba J. Effect of mechanical alloying on the morphology, microstructure and properties of aluminium matrix composite powders, Mater. Sci. Eng. A. 2003. V. 342. P. 131–143. https://doi.org/10.1016/S0921-5093(02)00246-0
Arik H. Effect of mechanical alloying process on mechanical properties of a-Si3N4 reinforced aluminum-based composite materials // Mater. Des. 2008. V. 29. P. 1856–1861. https://doi.org/10.1016/j.matdes.2008.03.010
Fathy A., Wagih A., Abd El-Hamid M., Hassan A.A. Effect of mechanical milling on the morphology and structural evaluation of Al-Al2O3 nanocomposite powders // Int. J. Eng. Trans. A Basics. 2014. V. 27. P. 625–632. https://doi.org/10.5829/idosi.ije.2014.27.04a.14
Dagasan E., Gercekcioglu E., Unalan S. Characterization of Ball Milled Al-Al2O3 sub-micron Composites // IOP Conf. Ser. Mater. Sci. Eng. 2018. https://doi.org/10.1088/1757-899X/295/1/012045.
Goyal K., Marwaha K. Processing and Properties of Aluminium Matrix Composites : A Short Review // Eur. J. Adv. Eng. Technol. 2016. V. 3. P. 54–59.
Nayak D., Debata M. Effect of composition and milling time on mechanical and wear performance of copper-graphite composites processed by powder metallurgy route // Powder Metall. 2014. V. 57. P. 265–273. https://doi.org/10.1179/ 1743290113Y.0000000080
K. S, K. R, A. Ghosh, Investigation on microstructures, mechanical and wear properties of Al 390/ZrO2 composite materials fabricated by P/M method // Multidiscip. Model. Mater. Struct. 2020. https://doi.org/10.1108/MMMS-10-2019-0180
Udaya, P. Fernandes. Effect of fly ash and ball milling time on CNT-FA reinforced aluminium matrix hybrid composites // Mater. Res. Express. 2019. V. 6. https://doi.org/10.1088/2053-1591/ab1e20
Ekinci V.S., Baǧci C., Arik H. Effect of Al2O3 content and milling time on microstructure and mechanical properties of aluminum metal matrix composites // Exp. Tech. 2014. V. 38. P. 66–73. https://doi.org/10.1111/j.1747-1567.2011.00790.x
Fogagnolo J.B., Ruiz-Navas E.M., Robert M.H., Torralba J.M. 6061 Al reinforced with silicon nitride particles processed by mechanical milling // Scr. Mater. 2002. V. 47. P. 243–248. https://doi.org/10.1016/S1359-6462(02)00133-1
Fogagnolo J.B., Robert M.H., Torralba J.M. The effects of mechanical alloying on the extrusion process of AA 6061 alloy reinforced with Si3N4 // J. Brazilian Soc. Mech. Sci. Eng. 2003. P. 1–11.
Fathy A., Elkady O., Abu-Oqail A. Production and properties of Cu–ZrO2 nanocomposites // J. Compos. Mater. 2018. V. 52. P. 1519–1529. https://doi.org/10.1177/0021998317726148
Toozandehjani M., Matori K.A., Ostovan F., Aziz S.A., Mamat M.S. Effect of milling time on the microstructure, physical and mechanical properties of Al–Al2O3 nanocomposite synthesized by ball milling and powder metallurgy // Materials (Basel). 2017. V. 10. https://doi.org/10.3390/ma10111232
Amador D.R., Torralba J.M. Morphological and microstructural characterisation of low-alloying Fe powder obtained by mechanical attrition // J. Mater. Process. Technol. 2003. V. 143–144. P. 776–780. https://doi.org/10.1016/S0924-0136(03)00372-8
Дополнительные материалы отсутствуют.
Инструменты
Физика металлов и металловедение